Page 209 of 447
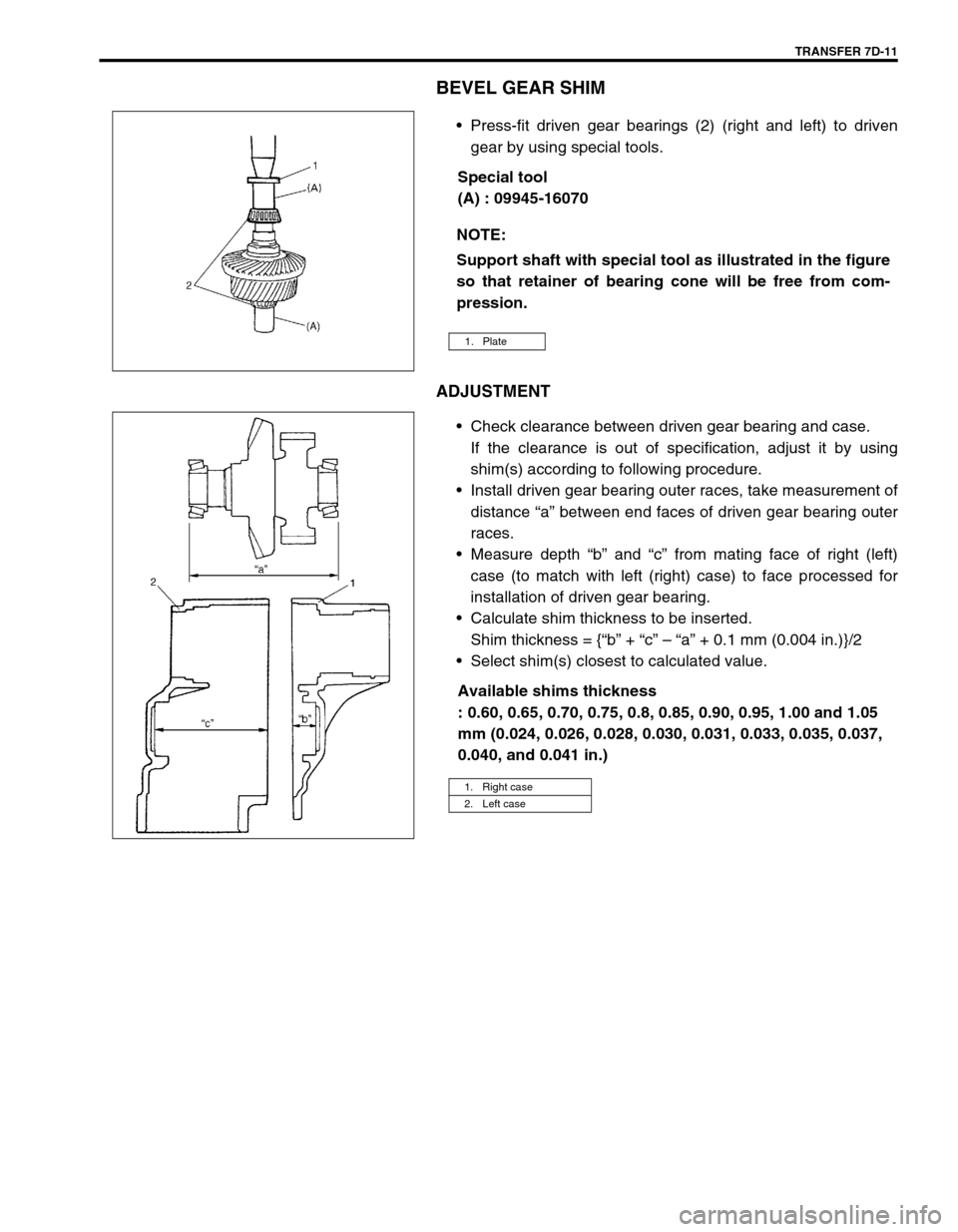
TRANSFER 7D-11
BEVEL GEAR SHIM
Press-fit driven gear bearings (2) (right and left) to driven
gear by using special tools.
Special tool
(A) : 09945-16070
ADJUSTMENT
Check clearance between driven gear bearing and case.
If the clearance is out of specification, adjust it by using
shim(s) according to following procedure.
Install driven gear bearing outer races, take measurement of
distance “a” between end faces of driven gear bearing outer
races.
Measure depth “b” and “c” from mating face of right (left)
case (to match with left (right) case) to face processed for
installation of driven gear bearing.
Calculate shim thickness to be inserted.
Shim thickness = {“b” + “c” – “a” + 0.1 mm (0.004 in.)}/2
Select shim(s) closest to calculated value.
Available shims thickness
: 0.60, 0.65, 0.70, 0.75, 0.8, 0.85, 0.90, 0.95, 1.00 and 1.05
mm (0.024, 0.026, 0.028, 0.030, 0.031, 0.033, 0.035, 0.037,
0.040, and 0.041 in.) NOTE:
Support shaft with special tool as illustrated in the figure
so that retainer of bearing cone will be free from com-
pression.
1. Plate
1. Right case
2. Left case
Page 210 of 447
7D-12 TRANSFER
TRANSFER OUTPUT RETAINER
ADJUSTMENT
Special tool
(A) : 09922-76140
(B) : 09922-76150
(C) : 09922-76340
(D) : 09922-76430
“a”: Pinion dummy (special tool) height 1. Transfer output retainer
“b”: Height from retainer installation face to pinion dummy 2. Left case
“c”: Distance from retainer installation face to end face of bearing race (“b” – “a”) 3. Pinion shaft bearing
“d”: Distance from end face of left case to cylinder section of reduction driven gear 4. Reduction driven gear
“e”: Outer diameter of cylinder section of reduction driven gear (29.7 mm/1.1693 in.) 5. Bevel pinion shaft
“f”: Distance from end face of left case to center shaft of reduction driven gear (“d” + “e”/2)
“g”: Dimension marked on bevel pinion shaft (Marked in shaft in mm)
“h”: Shim size for mounting distance adjustment (“g” + “c” – “f”)
Page 211 of 447
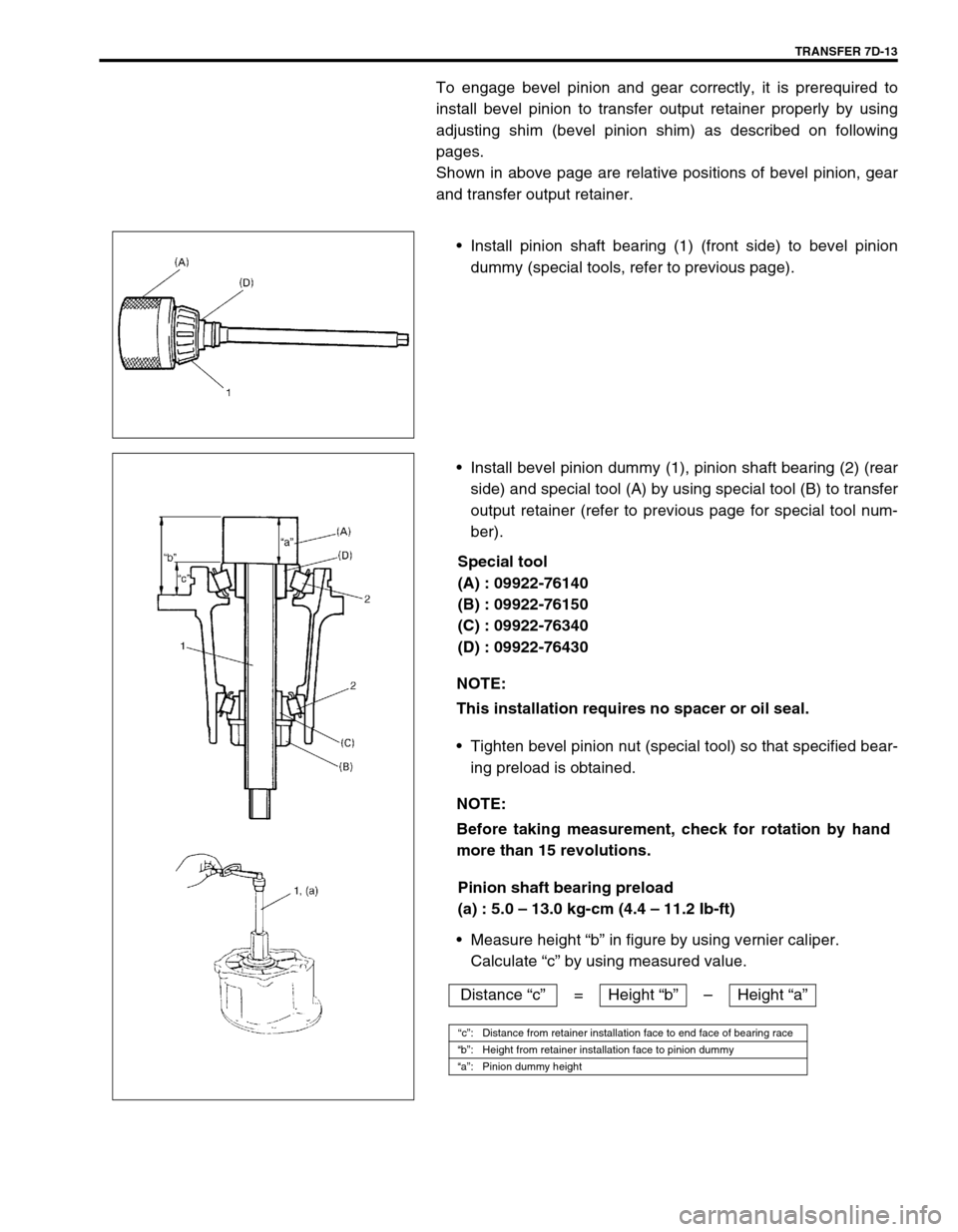
TRANSFER 7D-13
To engage bevel pinion and gear correctly, it is prerequired to
install bevel pinion to transfer output retainer properly by using
adjusting shim (bevel pinion shim) as described on following
pages.
Shown in above page are relative positions of bevel pinion, gear
and transfer output retainer.
Install pinion shaft bearing (1) (front side) to bevel pinion
dummy (special tools, refer to previous page).
Install bevel pinion dummy (1), pinion shaft bearing (2) (rear
side) and special tool (A) by using special tool (B) to transfer
output retainer (refer to previous page for special tool num-
ber).
Special tool
(A) : 09922-76140
(B) : 09922-76150
(C) : 09922-76340
(D) : 09922-76430
Tighten bevel pinion nut (special tool) so that specified bear-
ing preload is obtained.
Pinion shaft bearing preload
(a) : 5.0 – 13.0 kg-cm (4.4 – 11.2 Ib-ft)
Measure height “b” in figure by using vernier caliper.
Calculate “c” by using measured value.
NOTE:
This installation requires no spacer or oil seal.
NOTE:
Before taking measurement, check for rotation by hand
more than 15 revolutions.
Distance “c”= Height “b”–Height “a”
“c”: Distance from retainer installation face to end face of bearing race
“b”: Height from retainer installation face to pinion dummy
“a”: Pinion dummy height
Page 212 of 447
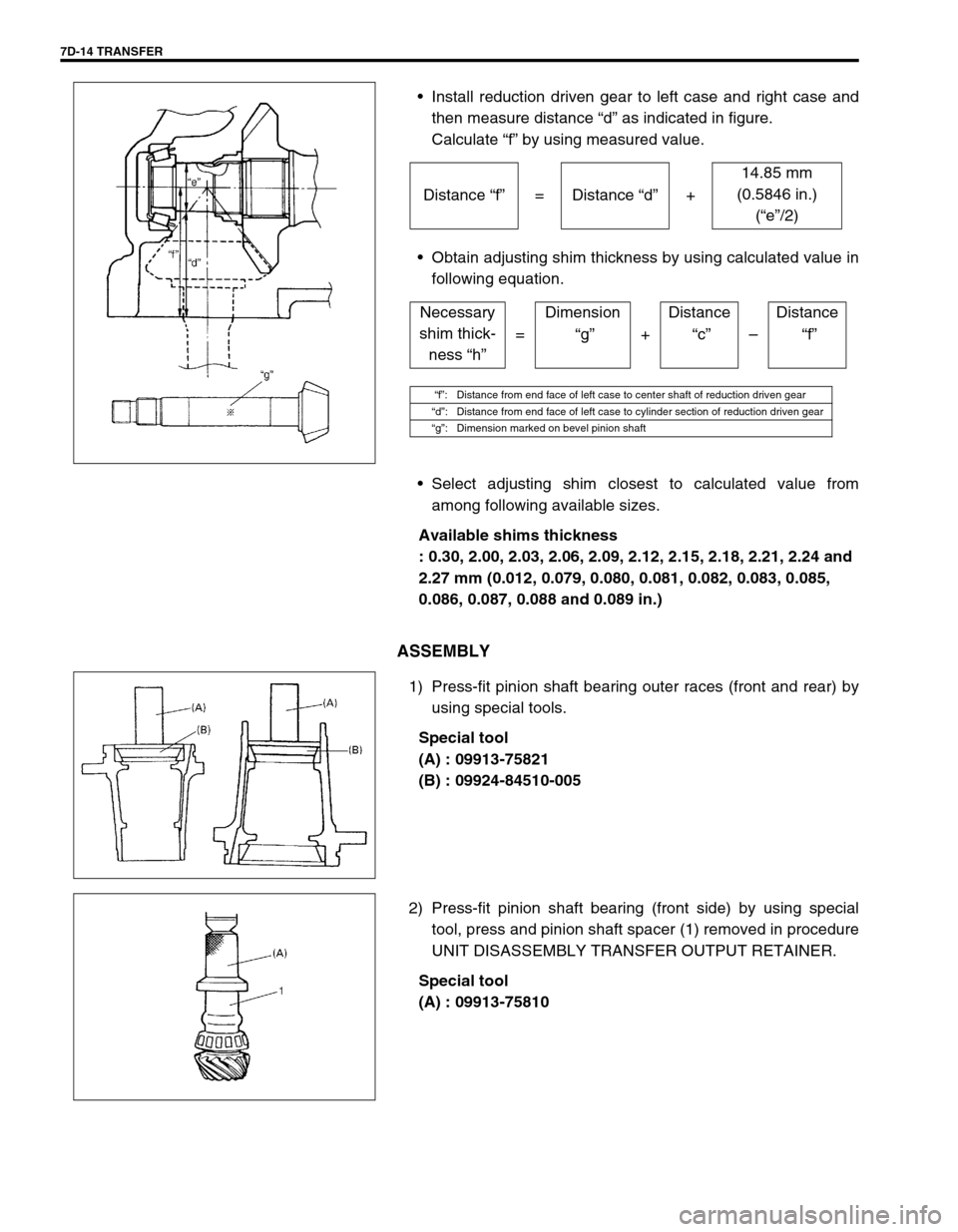
7D-14 TRANSFER
Install reduction driven gear to left case and right case and
then measure distance “d” as indicated in figure.
Calculate “f” by using measured value.
Obtain adjusting shim thickness by using calculated value in
following equation.
Select adjusting shim closest to calculated value from
among following available sizes.
Available shims thickness
: 0.30, 2.00, 2.03, 2.06, 2.09, 2.12, 2.15, 2.18, 2.21, 2.24 and
2.27 mm (0.012, 0.079, 0.080, 0.081, 0.082, 0.083, 0.085,
0.086, 0.087, 0.088 and 0.089 in.)
ASSEMBLY
1) Press-fit pinion shaft bearing outer races (front and rear) by
using special tools.
Special tool
(A) : 09913-75821
(B) : 09924-84510-005
2) Press-fit pinion shaft bearing (front side) by using special
tool, press and pinion shaft spacer (1) removed in procedure
UNIT DISASSEMBLY TRANSFER OUTPUT RETAINER.
Special tool
(A) : 09913-7581014.85 mm
(0.5846 in.)
(“e”/2) Distance “f”= Distance “d”+
Necessary
shim thick-
ness “h”Dimension Distance Distance
= “g”+ “c”– “f”
“f”: Distance from end face of left case to center shaft of reduction driven gear
“d”: Distance from end face of left case to cylinder section of reduction driven gear
“g”: Dimension marked on bevel pinion shaft
Page 213 of 447
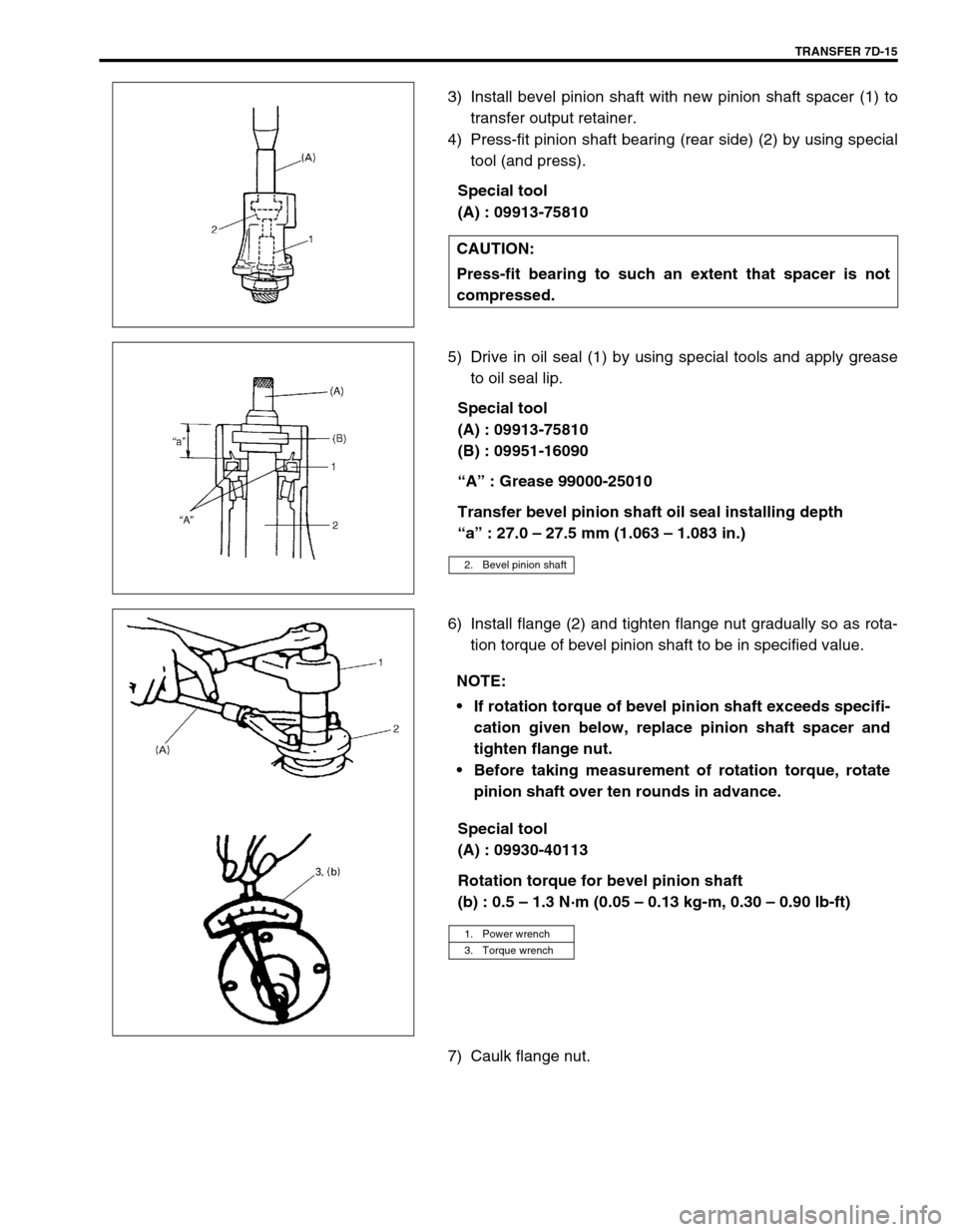
TRANSFER 7D-15
3) Install bevel pinion shaft with new pinion shaft spacer (1) to
transfer output retainer.
4) Press-fit pinion shaft bearing (rear side) (2) by using special
tool (and press).
Special tool
(A) : 09913-75810
5) Drive in oil seal (1) by using special tools and apply grease
to oil seal lip.
Special tool
(A) : 09913-75810
(B) : 09951-16090
“A” : Grease 99000-25010
Transfer bevel pinion shaft oil seal installing depth
“a” : 27.0 – 27.5 mm (1.063 – 1.083 in.)
6) Install flange (2) and tighten flange nut gradually so as rota-
tion torque of bevel pinion shaft to be in specified value.
Special tool
(A) : 09930-40113
Rotation torque for bevel pinion shaft
(b) : 0.5 – 1.3 N·m (0.05 – 0.13 kg-m, 0.30 – 0.90 lb-ft)
7) Caulk flange nut.CAUTION:
Press-fit bearing to such an extent that spacer is not
compressed.
2. Bevel pinion shaft
NOTE:
If rotation torque of bevel pinion shaft exceeds specifi-
cation given below, replace pinion shaft spacer and
tighten flange nut.
Before taking measurement of rotation torque, rotate
pinion shaft over ten rounds in advance.
1. Power wrench
3. Torque wrench
Page 214 of 447
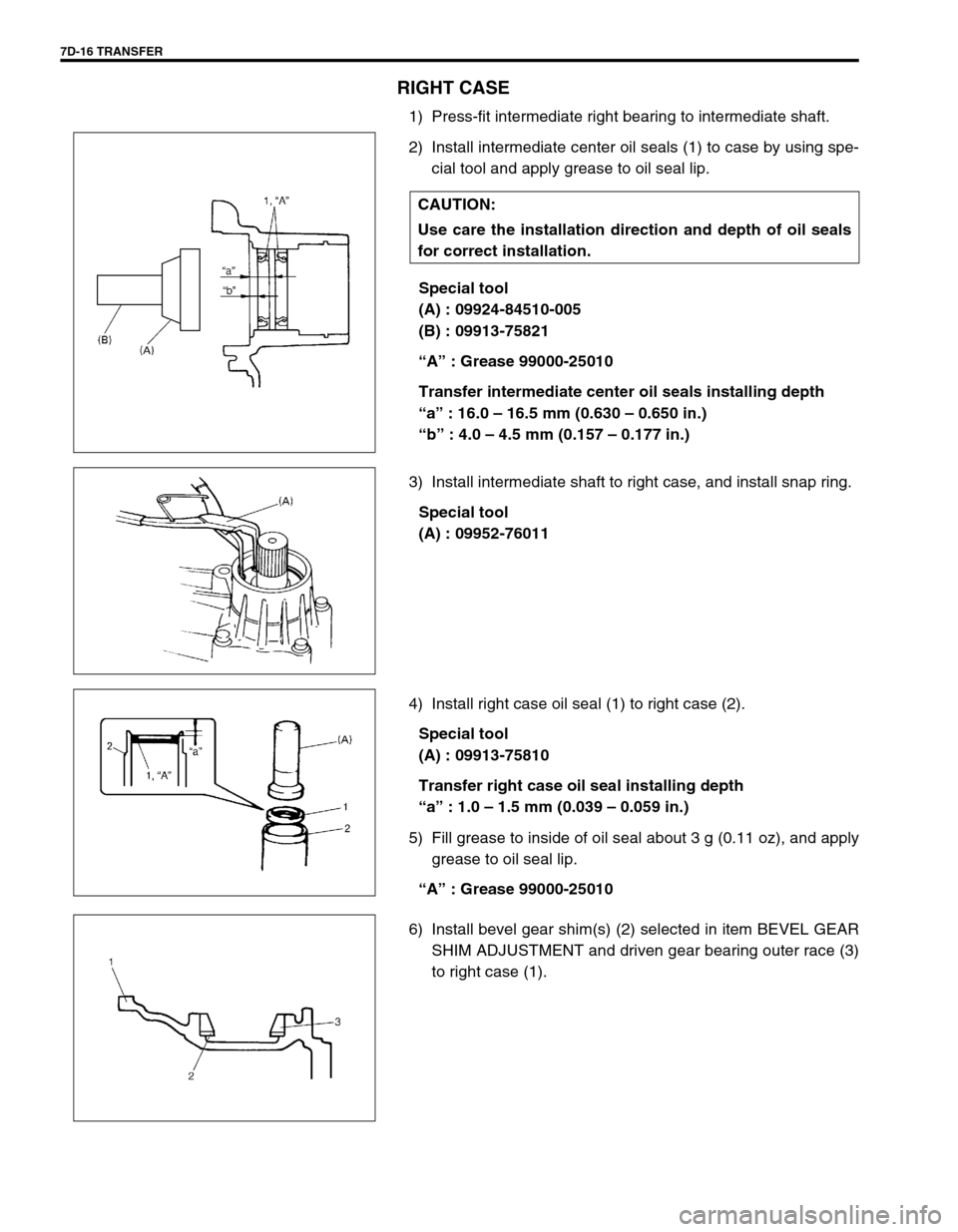
7D-16 TRANSFER
RIGHT CASE
1) Press-fit intermediate right bearing to intermediate shaft.
2) Install intermediate center oil seals (1) to case by using spe-
cial tool and apply grease to oil seal lip.
Special tool
(A) : 09924-84510-005
(B) : 09913-75821
“A” : Grease 99000-25010
Transfer intermediate center oil seals installing depth
“a” : 16.0 – 16.5 mm (0.630 – 0.650 in.)
“b” : 4.0 – 4.5 mm (0.157 – 0.177 in.)
3) Install intermediate shaft to right case, and install snap ring.
Special tool
(A) : 09952-76011
4) Install right case oil seal (1) to right case (2).
Special tool
(A) : 09913-75810
Transfer right case oil seal installing depth
“a” : 1.0 – 1.5 mm (0.039 – 0.059 in.)
5) Fill grease to inside of oil seal about 3 g (0.11 oz), and apply
grease to oil seal lip.
“A” : Grease 99000-25010
6) Install bevel gear shim(s) (2) selected in item BEVEL GEAR
SHIM ADJUSTMENT and driven gear bearing outer race (3)
to right case (1). CAUTION:
Use care the installation direction and depth of oil seals
for correct installation.
Page 215 of 447
TRANSFER 7D-17
LEFT CASE
1) Install the bevel gear shim(s) selected in item BEVEL GEAR
SHIM ADJUSTMENT and driven gear bearing outer race to
left case.
2) Install reduction drive gear oil seal (1) to left case (2) by
using special tool.
Special tool
(A) : 09913-75810
Transfer reduction drive gear oil seal installing depth
“a” : 1.5 – 2.0 mm (0.059 – 0.078 in.)
3) Fill grease to inside of oil seal about 3 g (0.11 oz), and apply
grease to oil seal lip.
“A” : Grease 99000-25010
4) Press-fit drive gear bearings (right (2) and left (3)) to reduc-
tion drive gear (1).
Apply gear oil to ball part of bearing.
5) Install reduction drive gear (2) and reduction driven gear (3)
to left case (1).
TRANSFER ASSEMBLY
1) Clean mating surface of right case and left case (1), and
apply sealant to left case (1) by using a nozzle as shown in
figure by such amount that its section is 1.5mm (0.059 in) in
diameter.
“A” : Sealant 99000-31230
Page 216 of 447
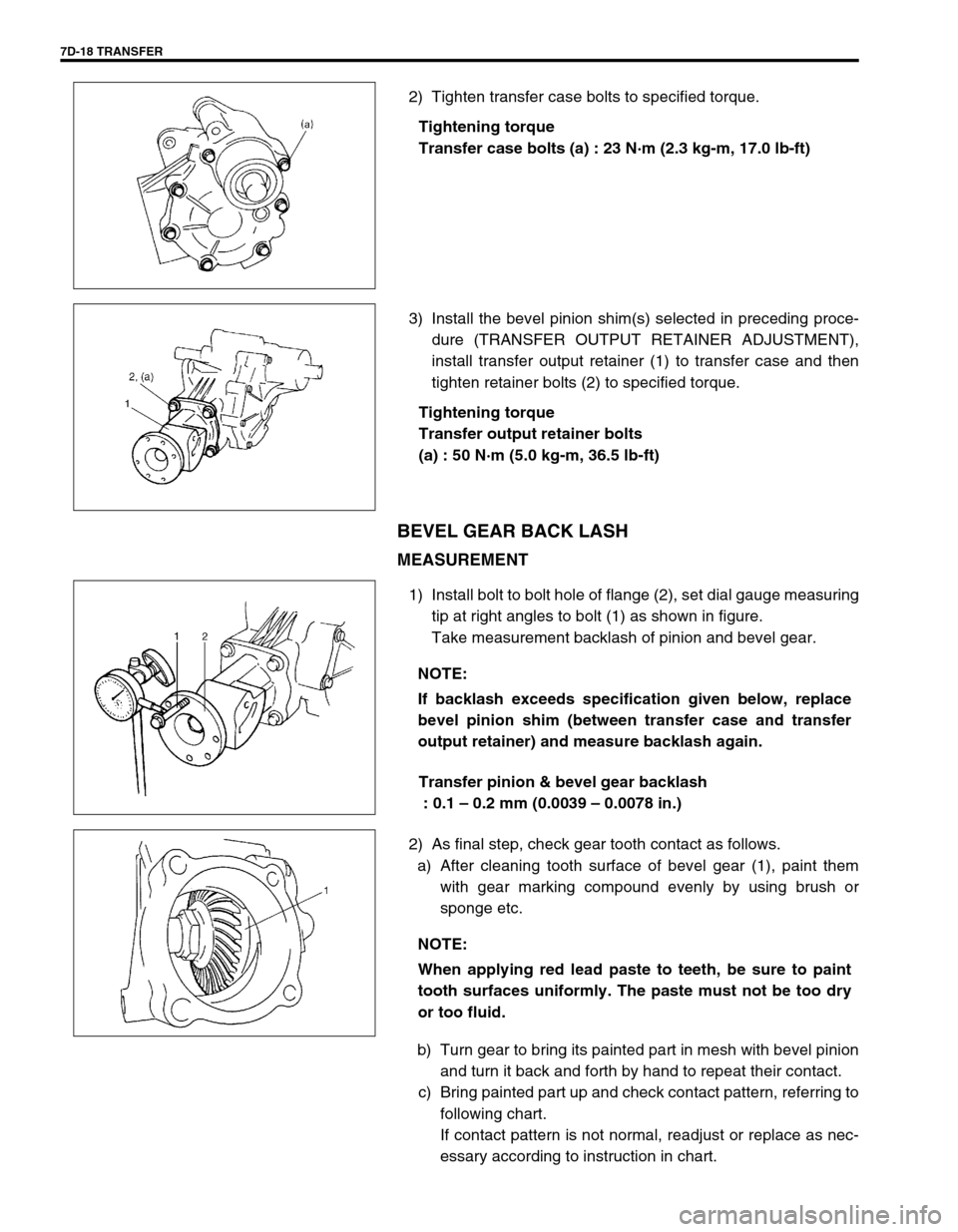
7D-18 TRANSFER
2) Tighten transfer case bolts to specified torque.
Tightening torque
Transfer case bolts (a) : 23 N·m (2.3 kg-m, 17.0 lb-ft)
3) Install the bevel pinion shim(s) selected in preceding proce-
dure (TRANSFER OUTPUT RETAINER ADJUSTMENT),
install transfer output retainer (1) to transfer case and then
tighten retainer bolts (2) to specified torque.
Tightening torque
Transfer output retainer bolts
(a) : 50 N·m (5.0 kg-m, 36.5 lb-ft)
BEVEL GEAR BACK LASH
MEASUREMENT
1) Install bolt to bolt hole of flange (2), set dial gauge measuring
tip at right angles to bolt (1) as shown in figure.
Take measurement backlash of pinion and bevel gear.
Transfer pinion & bevel gear backlash
: 0.1 – 0.2 mm (0.0039 – 0.0078 in.)
2) As final step, check gear tooth contact as follows.
a) After cleaning tooth surface of bevel gear (1), paint them
with gear marking compound evenly by using brush or
sponge etc.
b) Turn gear to bring its painted part in mesh with bevel pinion
and turn it back and forth by hand to repeat their contact.
c) Bring painted part up and check contact pattern, referring to
following chart.
If contact pattern is not normal, readjust or replace as nec-
essary according to instruction in chart.
NOTE:
If backlash exceeds specification given below, replace
bevel pinion shim (between transfer case and transfer
output retainer) and measure backlash again.
NOTE:
When applying red lead paste to teeth, be sure to paint
tooth surfaces uniformly. The paste must not be too dry
or too fluid.