Page 49 of 392
42Section 2 Fuel Pump Inspection1. Fuel pump
(a) Check fuel pump resistance, 0.2~3.0 at 20°. Replace fuel pump if the resistance is not as specified.
See (Figure 93)
(b) Fuel pump running:
Check fuel pump by connecting with battery. Replace fuel pump or wire if the running is not as specified.
See (Figure 94).
The test should be conducted within 10s to prevent coil from damage.
2. Fuel injector assembly
Injection Volume: 40~50cm3/s
Error between each injector: less than 10 cm3Replace injector if the injection volume is not as specified.
(a) Check for leakage: Disconnect the cable from the battery. The fuel drop/min is no more than 1 drop.
Figure 93 Figure 94 Ohmmeter
Battery Ω
Page 50 of 392
43Section 3 Fuel Injector Replacement1. Check fuel for ejection.
2. Remove PCV ventilation hoses. See (Figure 95). Remove fuel pipe clamp.
3. Detach fuel hose sub-assembly
4. Detach fuel delivery pipe sub-assembly. See (Figure 96)
(a) Press the connector to lock the spring and pull the connector from the injector.
(b) Remove 2 screws and detach fuel delivery pipe with injector.
5. Remove fuel injector assembly
6. Install injector assembly
(a) Smear a light layer of oil on two O-rings and install them to injector. See (Figure 97).
(b) Install 4 injectors to feul delivery pipe by rotating them left and right. See (Figure 98).
(c) Install retain frame to each injector.
Figure 95 Figure 96
Figure 97 Figure 98New O-ringUpward
Ratain Frame
PushRotate
Page 51 of 392
447. Install fuel delivery pipe sub-assembly
(a) Install two washers in intake manifold. See (Figure 99).
(b) Install 4 injectors and fuel delivery pipe assembly into intake manifold .
(c) Temperarily install 2 bolts to attach the fuel delivery pipe to intake
manifold .
(d) Check injector for smooth rotation. See (Figure 100).
Hint: If injector doesn't rotate smoothly, replace O-ring with the injector
connector upward.
(e) Tighten the 2 bolts and attach the fuel delivery pipe to intake manifold
See (Figure 101).
Torque: 15N. m
Figure 100 Figure 101Figure 99 Washer
Rotate
Upward
Page 52 of 392
45Section 4 Fuel Pump ReplacementFigure 102
Page 53 of 392
461. Avoid fuel ejection
2. Disconnect fuel tank hose
3. Disconnect fuel tank return hose
4. Disconnect fuel tank gas exhaust hose
5. Detach fuel pump assembly with filter screen. See (Figure 103)
Using special tool, loose fuel tank cap. Be careful not to bend the fuel
level sensor arm when pulling out fuel pump.
6. Install fuel pump assembly. See (Figure 104). Replace ring seal .
Align the tab on the fuel pump to the notch on the fuel tank port. Tighten
the fuel tank cap with special tool.
Torque: 40N. m
7. Install fuel gas exhaust hose
(a) Install return hose;
(b) Install fuel hose;
(c) Check fuel for leakage.Figure 103
Figure 104New Washer
Page 54 of 392
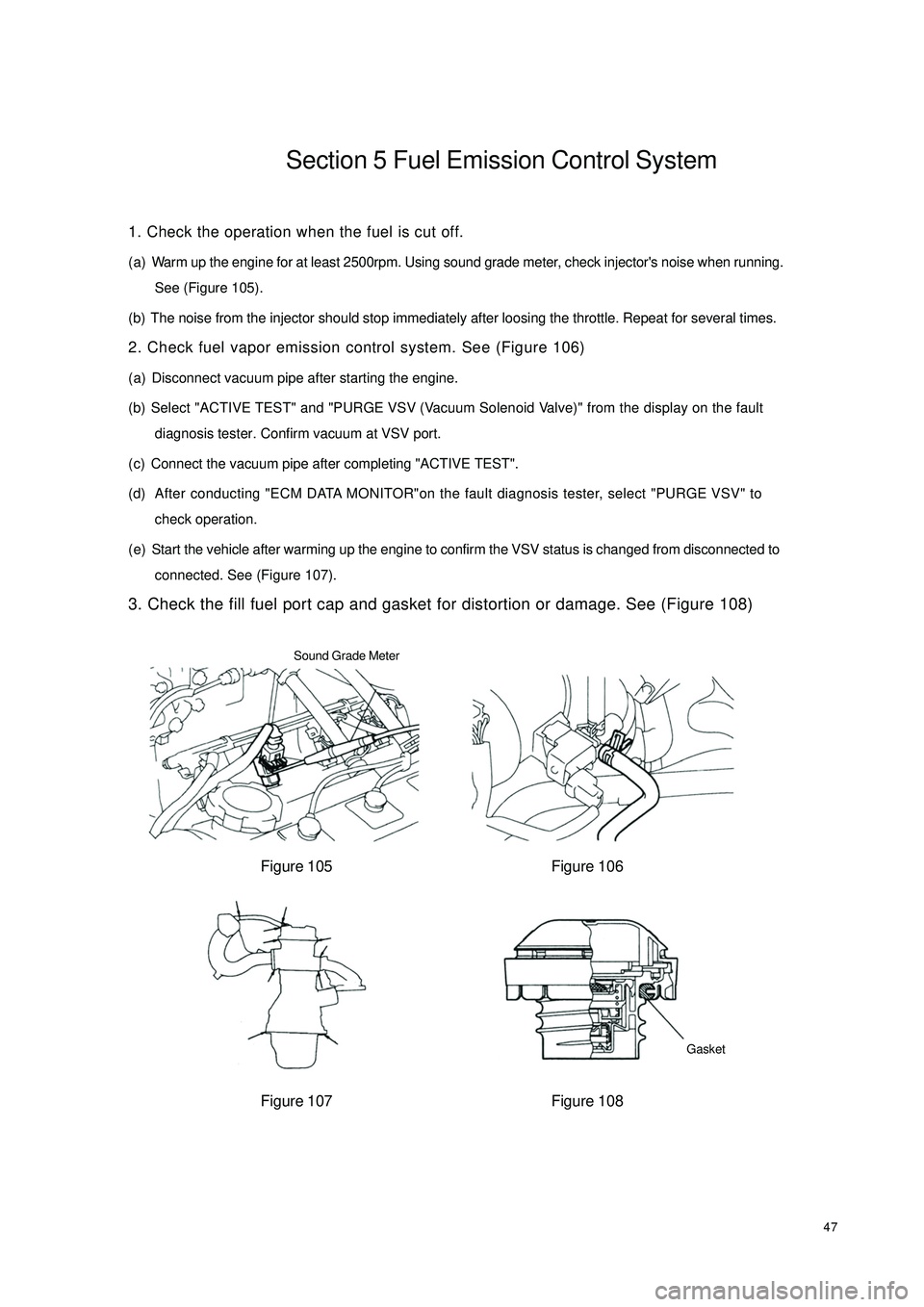
47Section 5 Fuel Emission Control System1. Check the operation when the fuel is cut off.
(a) Warm up the engine for at least 2500rpm. Using sound grade meter, check injector's noise when running.
See (Figure 105).
(b) The noise from the injector should stop immediately after loosing the throttle. Repeat for several times.
2. Check fuel vapor emission control system. See (Figure 106)
(a) Disconnect vacuum pipe after starting the engine.
(b) Select "ACTIVE TEST" and "PURGE VSV (Vacuum Solenoid Valve)" from the display on the fault
diagnosis tester. Confirm vacuum at VSV port.
(c) Connect the vacuum pipe after completing "ACTIVE TEST".
(d) After conducting "ECM DATA MONITOR"on the fault diagnosis tester, select "PURGE VSV" to
check operation.
(e) Start the vehicle after warming up the engine to confirm the VSV status is changed from disconnected to
connected. See (Figure 107).
3. Check the fill fuel port cap and gasket for distortion or damage. See (Figure 108)
Figure 105 Figure 106
Figure 107 Figure 108Sound Grade Meter
Gasket
Page 55 of 392
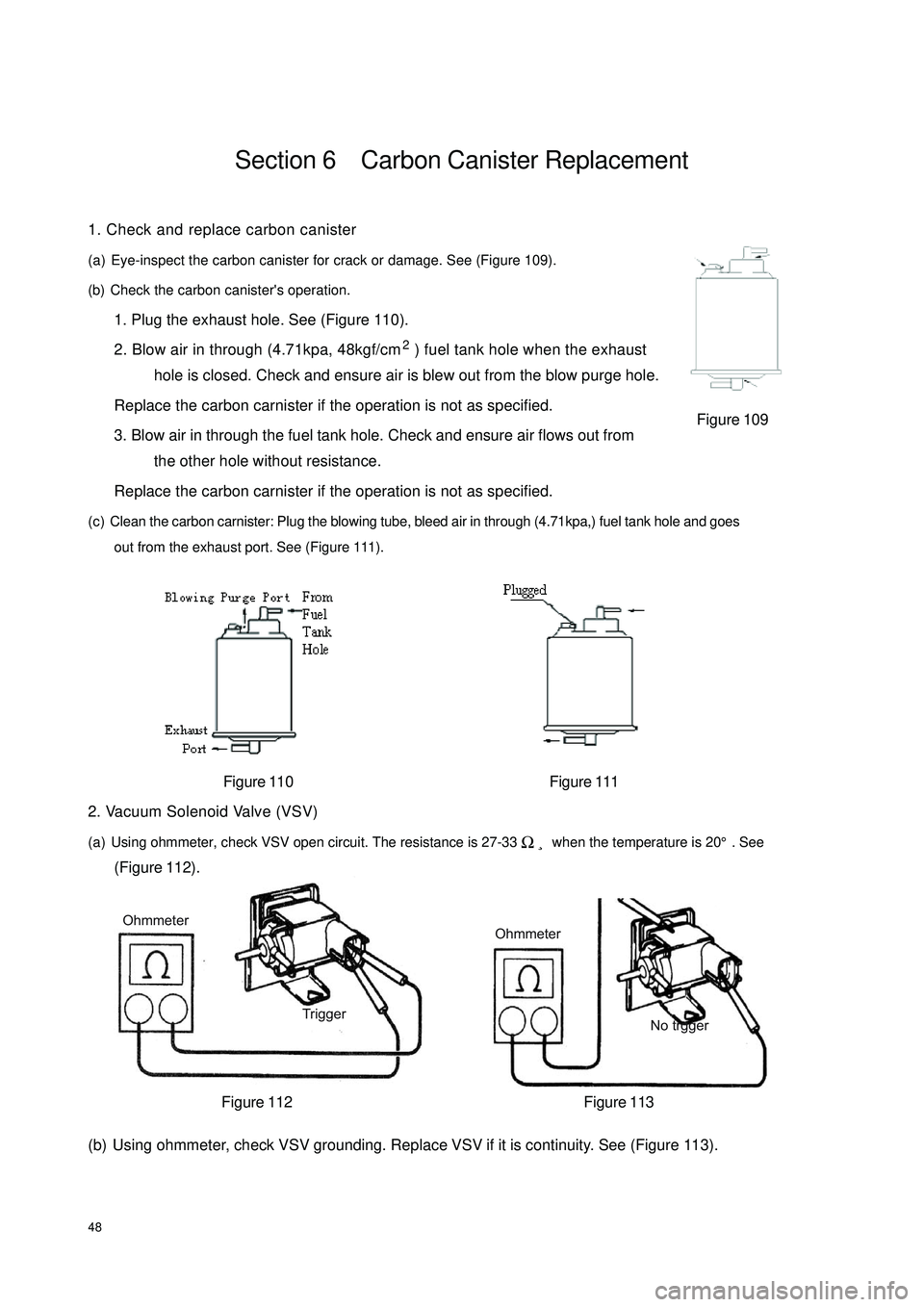
Ohmmeter
No trggerOhmmeter
Trigger48Section 6 Carbon Canister Replacement1. Check and replace carbon canister
(a) Eye-inspect the carbon canister for crack or damage. See (Figure 109).
(b) Check the carbon canister's operation.
1. Plug the exhaust hole. See (Figure 110).
2. Blow air in through (4.71kpa, 48kgf/cm2) fuel tank hole when the exhaust
hole is closed. Check and ensure air is blew out from the blow purge hole.
Replace the carbon carnister if the operation is not as specified.
3. Blow air in through the fuel tank hole. Check and ensure air flows out from
the other hole without resistance.
Replace the carbon carnister if the operation is not as specified.
(c) Clean the carbon carnister: Plug the blowing tube, bleed air in through (4.71kpa,) fuel tank hole and goes
out from the exhaust port. See (Figure 111).
Figure 110 Figure 111
2. Vacuum Solenoid Valve (VSV)
(a) Using ohmmeter, check VSV open circuit. The resistance is 27-33¸ when the temperature is 20°. See
(Figure 112).
(b) Using ohmmeter, check VSV grounding. Replace VSV if it is continuity. See (Figure 113).Figure 112 Figure 113Figure 109Ω
Page 56 of 392
Near cylinder head
Cleaning pipeNear the intake manifold49(3) Check VSV operation from hole E to F and that the air flow should be difficult. See (Figure 114).
3. PCV sub-assembly
It should be easy for air to pass through the cylinder head.
Notice:
zDo not suck air through valve.
zNever put any object into the valve. Replace PCV if the operation is
not as specified.
zBlow air in from the intake manifold side. Check that the air flow
should be difficult. Replace PCV if the operation is not as specified. See
(Figure 115).
Figure 115AirFigure 114