Page 225 of 260
BODY REPAIR
BL-225
C
D
E
F
G
H
J
K
L
MA
B
BL
Revision: 2006 November2007 350Z
The spot weld on HSS panels is harder than that of an ordi-
nary steel panel.
Therefore, when cutting spot welds on a HSS panel, use a
low speed high torque drill (1,000 to 1,200 rpm) to increase
drill bit durability and facilitate the operation.
2. Precautions in spot welding HSS
This work should be performed under standard working condi-
tions. Always note the following when spot welding HSS:
The electrode tip diameter must be sized properly according
to the metal thickness.
The panel surfaces must fit flush to each other, leaving no
gaps.
Follow the specifications for the proper welding pitch.
Unit:mm
PIIA0145E
PIIA0146E
PIIA0147E
Thickness (t) Minimum pitch (l)
0.6 (0.024)
0.8 (0.031)
1.0 (0.039)
1.2 (0.047)
1.6 (0.063)
1.8 (0.071)10 (0.39) or over
12 (0.47) or over
18 (0.71) or over
20 (0.79) or over
27 (1.06) or over
31 (1.22) or over
PIIA0148E
Page 226 of 260
BL-226
BODY REPAIR
Revision: 2006 November2007 350Z
Replacement Operations (Coupe)NIS00047
DESCRIPTION
This section is prepared for technicians who have attained a high level of skill and experience in repairing col-
lision-damaged vehicles and also use modern service tools and equipment. Persons unfamiliar with body
repair techniques should not attempt to repair collision-damaged vehicles by using this section.
Technicians are also encouraged to read Body Repair Manual (Fundamentals) in order to ensure that the orig-
inal functions and quality of the vehicle can be maintained. The Body Repair Manual (Fundamentals) contains
additional information, including cautions and warning, that are not including in this manual. Technicians
should refer to both manuals to ensure proper repairs.
Please note that these information are prepared for worldwide usage, and as such, certain procedures might
not apply in some regions or countries.
Page 227 of 260
BODY REPAIR
BL-227
C
D
E
F
G
H
J
K
L
MA
B
BL
Revision: 2006 November2007 350Z
The symbols used in this section for cutting and welding / brazing operations are shown below.
PIIA0149E
Page 228 of 260
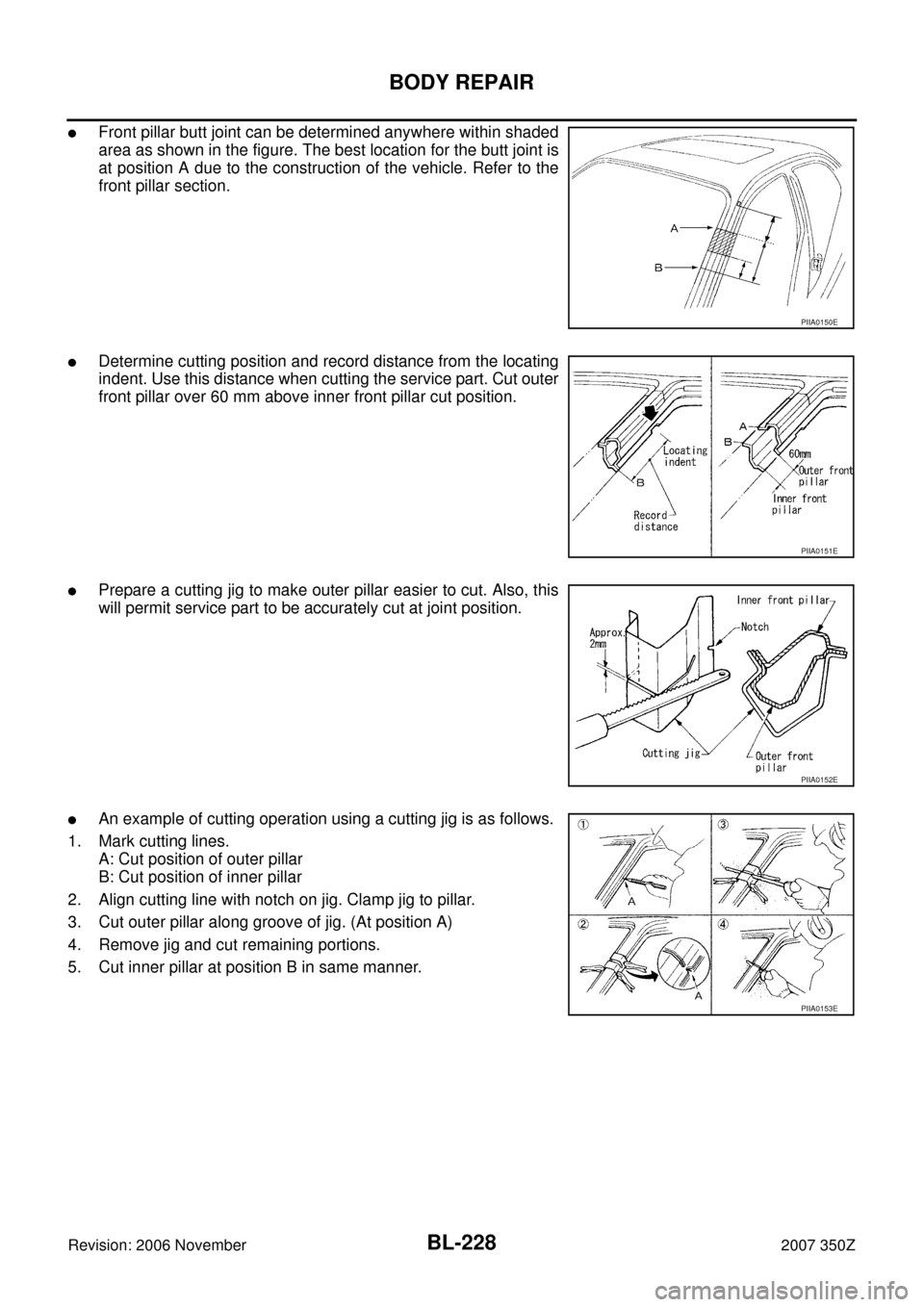
BL-228
BODY REPAIR
Revision: 2006 November2007 350Z
Front pillar butt joint can be determined anywhere within shaded
area as shown in the figure. The best location for the butt joint is
at position A due to the construction of the vehicle. Refer to the
front pillar section.
Determine cutting position and record distance from the locating
indent. Use this distance when cutting the service part. Cut outer
front pillar over 60 mm above inner front pillar cut position.
Prepare a cutting jig to make outer pillar easier to cut. Also, this
will permit service part to be accurately cut at joint position.
An example of cutting operation using a cutting jig is as follows.
1. Mark cutting lines.
A: Cut position of outer pillar
B: Cut position of inner pillar
2. Align cutting line with notch on jig. Clamp jig to pillar.
3. Cut outer pillar along groove of jig. (At position A)
4. Remove jig and cut remaining portions.
5. Cut inner pillar at position B in same manner.
PIIA0150E
PIIA0151E
PIIA0152E
PIIA0153E
Page 229 of 260
BODY REPAIR
BL-229
C
D
E
F
G
H
J
K
L
MA
B
BL
Revision: 2006 November2007 350Z
HOODLEDGE (COUPE)
Change parts
Front strut housing (LH)Upper front hoodledge (LH)Hoodledge reinforcement (LH)
SIIA1992E
Page 230 of 260
BL-230
BODY REPAIR
Revision: 2006 November2007 350Z
FRONT SIDE MEMBER (COUPE)
Work after hoodledge has been removed.
SIIA1993E
Page 231 of 260
BODY REPAIR
BL-231
C
D
E
F
G
H
J
K
L
MA
B
BL
Revision: 2006 November2007 350Z
Change parts
Front side member assembly (LH)Front side member closing plate assembly (LH)
Front side member outrigger assembly (LH)Front side member rear reinforcement (LH)
Page 232 of 260
BL-232
BODY REPAIR
Revision: 2006 November2007 350Z
FRONT SIDE MEMBER (PARTIAL REPLACEMENT) (COUPE)
Change parts
Front side member assembly (RH)Front side member front closing plate (RH)Outer front towing hook bracket (RH)
SIIA1994E