Page 65 of 396
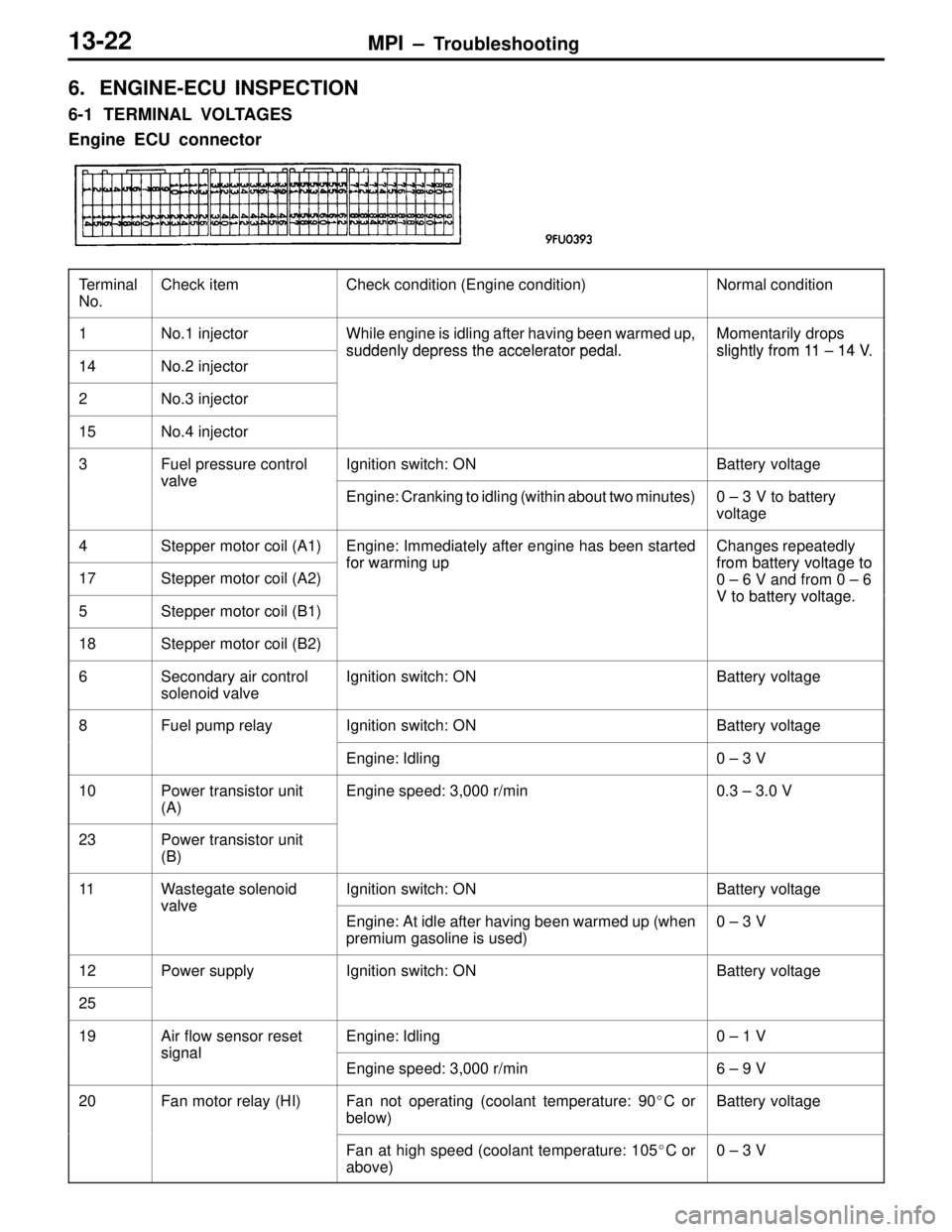
MPI – Troubleshooting13-22
6. ENGINE-ECU INSPECTION
6-1 TERMINAL VOLTAGES
Engine ECU connector
Terminal
No.Check itemCheck condition (Engine condition)Normal condition
1No.1 injectorWhile engine is idling after having been warmed up,
suddenly depress the accelerator pedal
Momentarily drops
slightlyfrom 1114V
14No.2 injector
suddenly depress the accelerator pedal.slightly from 11 – 14 V.
2No.3 injector
15No.4 injector
3Fuel pressure control
valve
Ignition switch: ONBattery voltage
valve
Engine: Cranking to idling (within about two minutes)0 – 3 V to battery
voltage
4Stepper motor coil (A1)Engine: Immediately after engine has been started
f
or warming up
Changes repeatedly
f
rom battery voltage to
17Stepper motor coil (A2)
for warming upfrom battery voltage to
0 – 6 V and from 0 – 6
V to battery voltage5Stepper motor coil (B1)V to battery voltage.
18Stepper motor coil (B2)
6Secondary air control
solenoid valveIgnition switch: ONBattery voltage
8Fuel pump relayIgnition switch: ONBattery voltage
Engine: Idling0 – 3 V
10Power transistor unit
(A)Engine speed: 3,000 r/min0.3 – 3.0 V
23Power transistor unit
(B)
11Wastegate solenoid
valve
Ignition switch: ONBattery voltage
valve
Engine: At idle after having been warmed up (when
premium gasoline is used)0 – 3 V
12Power supplyIgnition switch: ONBattery voltage
25
19Air flow sensor reset
signal
Engine: Idling0 – 1 V
signal
Engine speed: 3,000 r/min6 – 9 V
20Fan motor relay (HI)Fan not operating (coolant temperature: 90C or
below)Battery voltage
Fan at high speed (coolant temperature: 105C or
above)0 – 3 V
Page 66 of 396
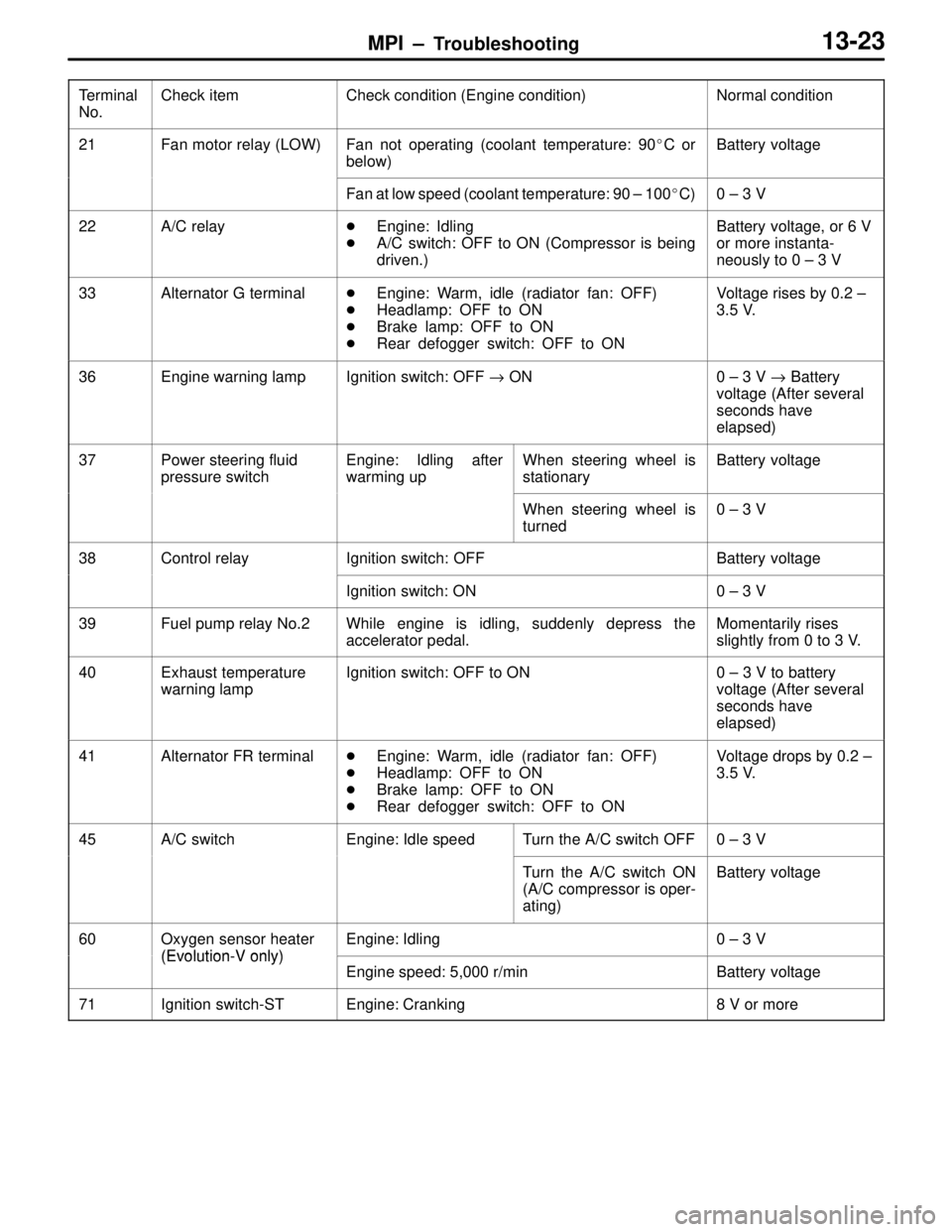
MPI – Troubleshooting13-23
Terminal
No.Normal condition Check condition (Engine condition) Check item
21Fan motor relay (LOW)Fan not operating (coolant temperature: 90C or
below)Battery voltage
Fan at low speed (coolant temperature: 90 – 100C)0 – 3 V
22A/C relayEngine: Idling
A/C switch: OFF to ON (Compressor is being
driven.)Battery voltage, or 6 V
or more instanta-
neously to 0 – 3 V
33Alternator G terminalEngine: Warm, idle (radiator fan: OFF)
Headlamp: OFF to ON
Brake lamp: OFF to ON
Rear defogger switch: OFF to ONVoltage rises by 0.2 –
3.5 V.
36Engine warning lampIgnition switch: OFF → ON0 – 3 V → Battery
voltage (After several
seconds have
elapsed)
37Power steering fluid
pressure switchEngine: Idling after
warming upWhen steering wheel is
stationaryBattery voltage
When steering wheel is
turned0 – 3 V
38Control relayIgnition switch: OFFBattery voltage
Ignition switch: ON0 – 3 V
39Fuel pump relay No.2While engine is idling, suddenly depress the
accelerator pedal.Momentarily rises
slightly from 0 to 3 V.
40Exhaust temperature
warning lampIgnition switch: OFF to ON0 – 3 V to battery
voltage (After several
seconds have
elapsed)
41Alternator FR terminalEngine: Warm, idle (radiator fan: OFF)
Headlamp: OFF to ON
Brake lamp: OFF to ON
Rear defogger switch: OFF to ONVoltage drops by 0.2 –
3.5 V.
45A/C switchEngine: Idle speedTurn the A/C switch OFF0 – 3 V
Turn the A/C switch ON
(A/C compressor is oper-
ating)Battery voltage
60Oxygen sensor heater
(Evolution V only)
Engine: Idling0 – 3 V
(Evolution-V only)
Engine speed: 5,000 r/minBattery voltage
71Ignition switch-STEngine: Cranking8 V or more
Page 67 of 396
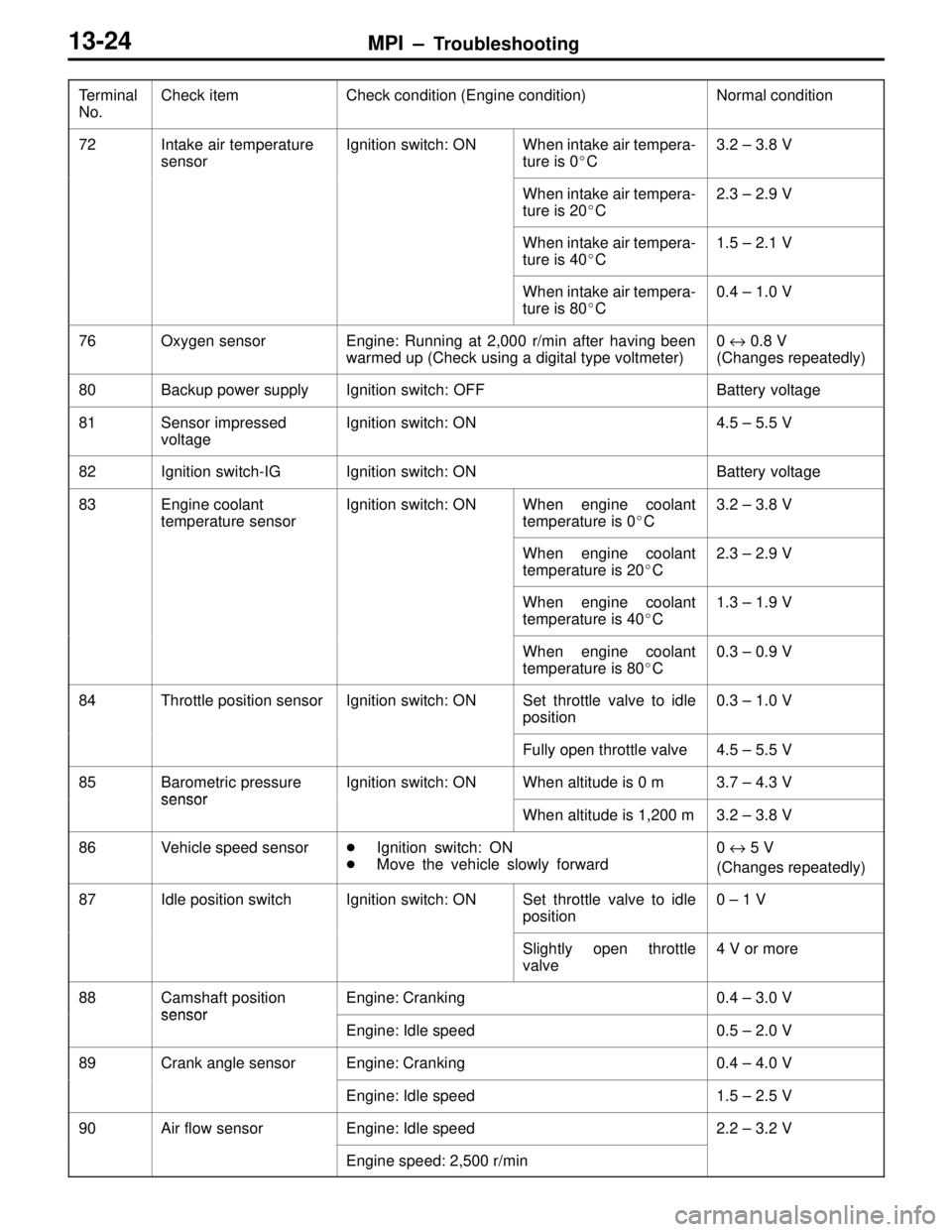
MPI – Troubleshooting13-24
Terminal
No.Normal condition Check condition (Engine condition) Check item
72Intake air temperature
sensorIgnition switch: ONWhen intake air tempera-
ture is 0C3.2 – 3.8 V
When intake air tempera-
ture is 20C2.3 – 2.9 V
When intake air tempera-
ture is 40C1.5 – 2.1 V
When intake air tempera-
ture is 80C0.4 – 1.0 V
76Oxygen sensorEngine: Running at 2,000 r/min after having been
warmed up (Check using a digital type voltmeter)0 ↔ 0.8 V
(Changes repeatedly)
80Backup power supplyIgnition switch: OFFBattery voltage
81Sensor impressed
voltageIgnition switch: ON4.5 – 5.5 V
82Ignition switch-IGIgnition switch: ONBattery voltage
83Engine coolant
temperature sensorIgnition switch: ONWhen engine coolant
temperature is 0C3.2 – 3.8 V
When engine coolant
temperature is 20C2.3 – 2.9 V
When engine coolant
temperature is 40C1.3 – 1.9 V
When engine coolant
temperature is 80C0.3 – 0.9 V
84Throttle position sensorIgnition switch: ONSet throttle valve to idle
position0.3 – 1.0 V
Fully open throttle valve4.5 – 5.5 V
85Barometric pressure
sensor
Ignition switch: ONWhen altitude is 0 m3.7 – 4.3 V
sensor
When altitude is 1,200 m3.2 – 3.8 V
86Vehicle speed sensorIgnition switch: ON
Move the vehicle slowly forward0 ↔ 5 V
(Changes repeatedly)
87Idle position switchIgnition switch: ONSet throttle valve to idle
position0 – 1 V
Slightly open throttle
valve4 V or more
88Camshaft position
sensor
Engine: Cranking0.4 – 3.0 V
sensor
Engine: Idle speed0.5 – 2.0 V
89Crank angle sensorEngine: Cranking0.4 – 4.0 V
Engine: Idle speed1.5 – 2.5 V
90Air flow sensorEngine: Idle speed2.2 – 3.2 V
Engine speed: 2,500 r/min
Page 68 of 396
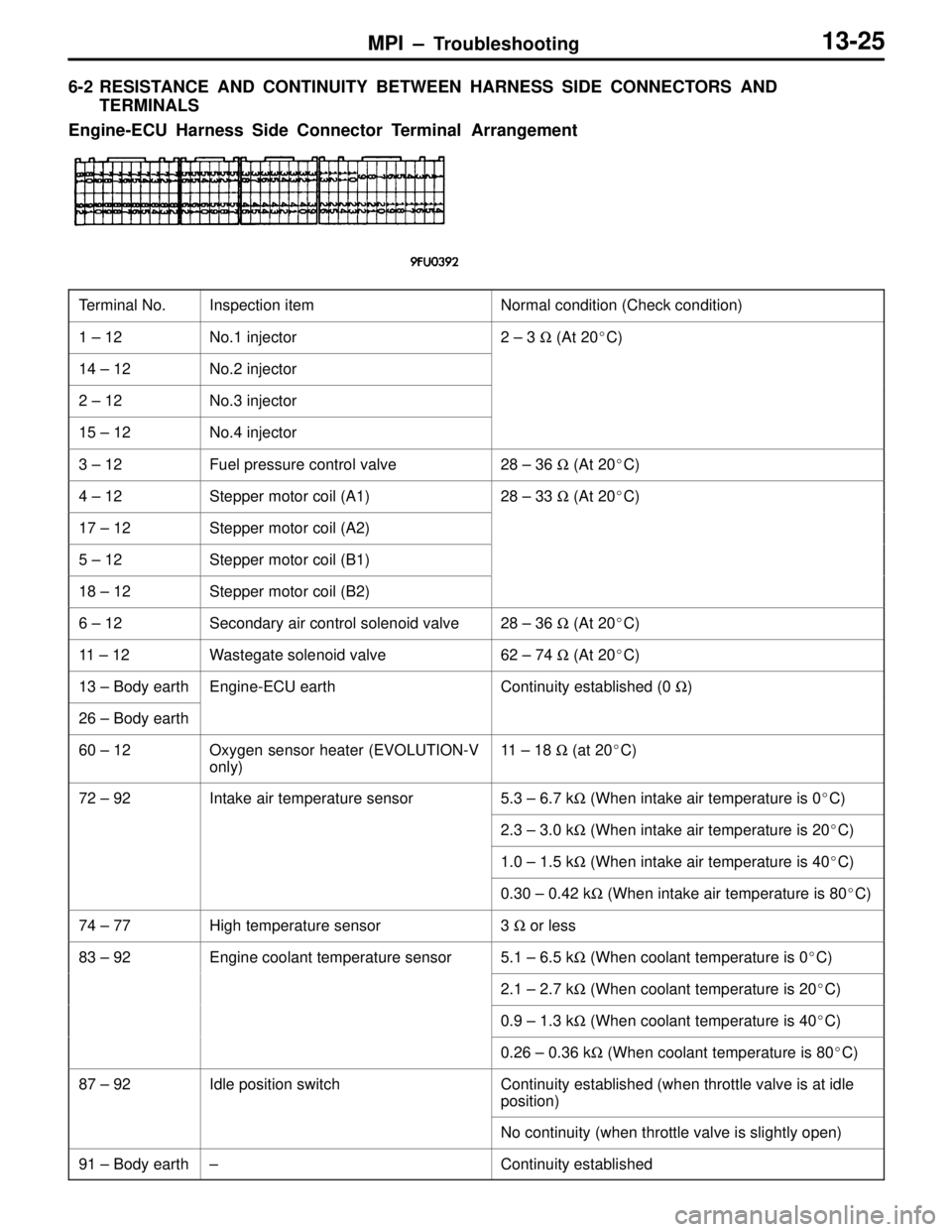
MPI – Troubleshooting13-25
6-2 RESISTANCE AND CONTINUITY BETWEEN HARNESS SIDE CONNECTORS AND
TERMINALS
Engine-ECU Harness Side Connector Terminal Arrangement
Terminal No.Inspection itemNormal condition (Check condition)
1 – 12No.1 injector2 – 3 Ω (At 20C)
14 – 12No.2 injector
2 – 12No.3 injector
15 – 12No.4 injector
3 – 12Fuel pressure control valve28 – 36 Ω (At 20C)
4 – 12Stepper motor coil (A1)28 – 33 Ω (At 20C)
17 – 12Stepper motor coil (A2)
5 – 12Stepper motor coil (B1)
18 – 12Stepper motor coil (B2)
6 – 12Secondary air control solenoid valve28 – 36 Ω (At 20C)
11 – 12Wastegate solenoid valve62 – 74 Ω (At 20C)
13 – Body earthEngine-ECU earthContinuity established (0 Ω)
26 – Body earth
60 – 12Oxygen sensor heater (EVOLUTION-V
only)11 – 18 Ω (at 20C)
72 – 92Intake air temperature sensor5.3 – 6.7 kΩ (When intake air temperature is 0C)
2.3 – 3.0 kΩ (When intake air temperature is 20C)
1.0 – 1.5 kΩ (When intake air temperature is 40C)
0.30 – 0.42 kΩ (When intake air temperature is 80C)
74 – 77High temperature sensor3 Ω or less
83 – 92Engine coolant temperature sensor5.1 – 6.5 kΩ (When coolant temperature is 0C)
2.1 – 2.7 kΩ (When coolant temperature is 20C)
0.9 – 1.3 kΩ (When coolant temperature is 40C)
0.26 – 0.36 kΩ (When coolant temperature is 80C)
87 – 92Idle position switchContinuity established (when throttle valve is at idle
position)
No continuity (when throttle valve is slightly open)
91 – Body earth–Continuity established
Page 69 of 396
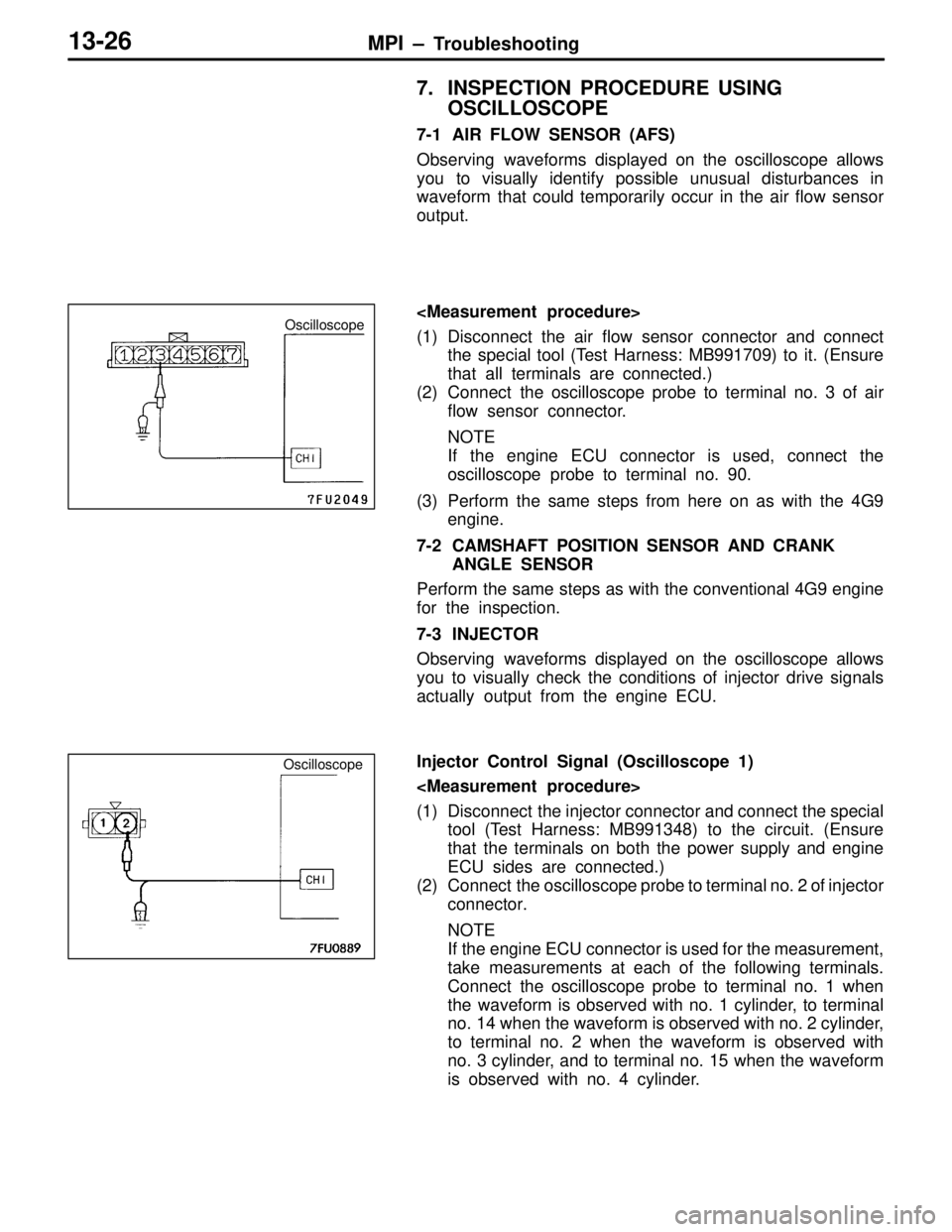
MPI – Troubleshooting13-26
7. INSPECTION PROCEDURE USING
OSCILLOSCOPE
7-1 AIR FLOW SENSOR (AFS)
Observing waveforms displayed on the oscilloscope allows
you to visually identify possible unusual disturbances in
waveform that could temporarily occur in the air flow sensor
output.
(1) Disconnect the air flow sensor connector and connect
the special tool (Test Harness: MB991709) to it. (Ensure
that all terminals are connected.)
(2) Connect the oscilloscope probe to terminal no. 3 of air
flow sensor connector.
NOTE
If the engine ECU connector is used, connect the
oscilloscope probe to terminal no. 90.
(3) Perform the same steps from here on as with the 4G9
engine.
7-2 CAMSHAFT POSITION SENSOR AND CRANK
ANGLE SENSOR
Perform the same steps as with the conventional 4G9 engine
for the inspection.
7-3 INJECTOR
Observing waveforms displayed on the oscilloscope allows
you to visually check the conditions of injector drive signals
actually output from the engine ECU.
Injector Control Signal (Oscilloscope 1)
(1) Disconnect the injector connector and connect the special
tool (Test Harness: MB991348) to the circuit. (Ensure
that the terminals on both the power supply and engine
ECU sides are connected.)
(2) Connect the oscilloscope probe to terminal no. 2 of injector
connector.
NOTE
If the engine ECU connector is used for the measurement,
take measurements at each of the following terminals.
Connect the oscilloscope probe to terminal no. 1 when
the waveform is observed with no. 1 cylinder, to terminal
no. 14 when the waveform is observed with no. 2 cylinder,
to terminal no. 2 when the waveform is observed with
no. 3 cylinder, and to terminal no. 15 when the waveform
is observed with no. 4 cylinder.
Oscilloscope
Oscilloscope
Page 70 of 396
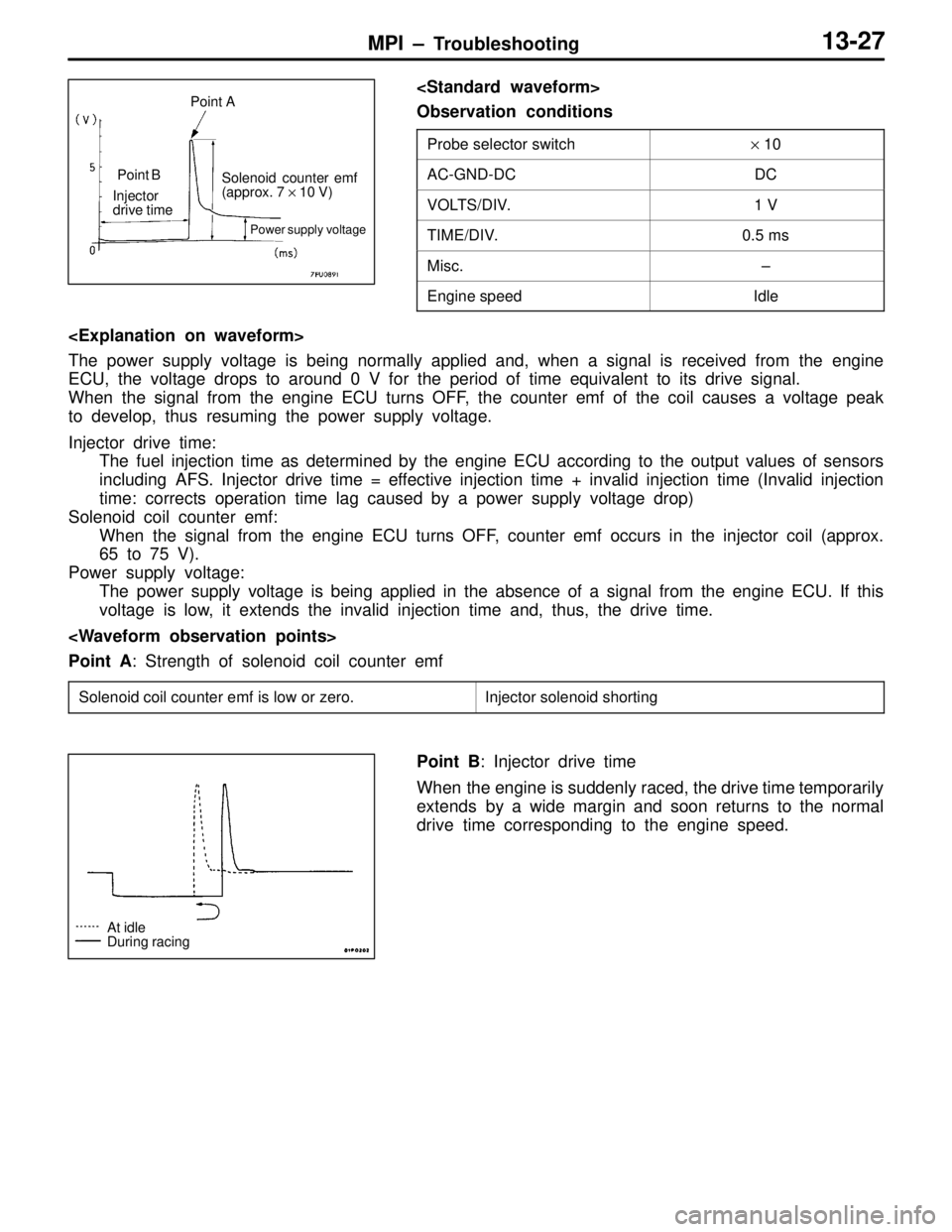
MPI – Troubleshooting13-27
Observation conditions
Probe selector switch× 10
AC-GND-DCDC
VOLTS/DIV.1 V
TIME/DIV.0.5 ms
Misc.–
Engine speedIdle
The power supply voltage is being normally applied and, when a signal is received from the engine
ECU, the voltage drops to around 0 V for the period of time equivalent to its drive signal.
When the signal from the engine ECU turns OFF, the counter emf of the coil causes a voltage peak
to develop, thus resuming the power supply voltage.
Injector drive time:
The fuel injection time as determined by the engine ECU according to the output values of sensors
including AFS. Injector drive time = effective injection time + invalid injection time (Invalid injection
time: corrects operation time lag caused by a power supply voltage drop)
Solenoid coil counter emf:
When the signal from the engine ECU turns OFF, counter emf occurs in the injector coil (approx.
65 to 75 V).
Power supply voltage:
The power supply voltage is being applied in the absence of a signal from the engine ECU. If this
voltage is low, it extends the invalid injection time and, thus, the drive time.
Point A: Strength of solenoid coil counter emf
Solenoid coil counter emf is low or zero.Injector solenoid shorting
Point B: Injector drive time
When the engine is suddenly raced, the drive time temporarily
extends by a wide margin and soon returns to the normal
drive time corresponding to the engine speed.
Point A
Point B
Injector
drive timeSolenoid counter emf
(approx. 7 × 10 V)
Power supply voltage
At idle
During racing
Page 71 of 396
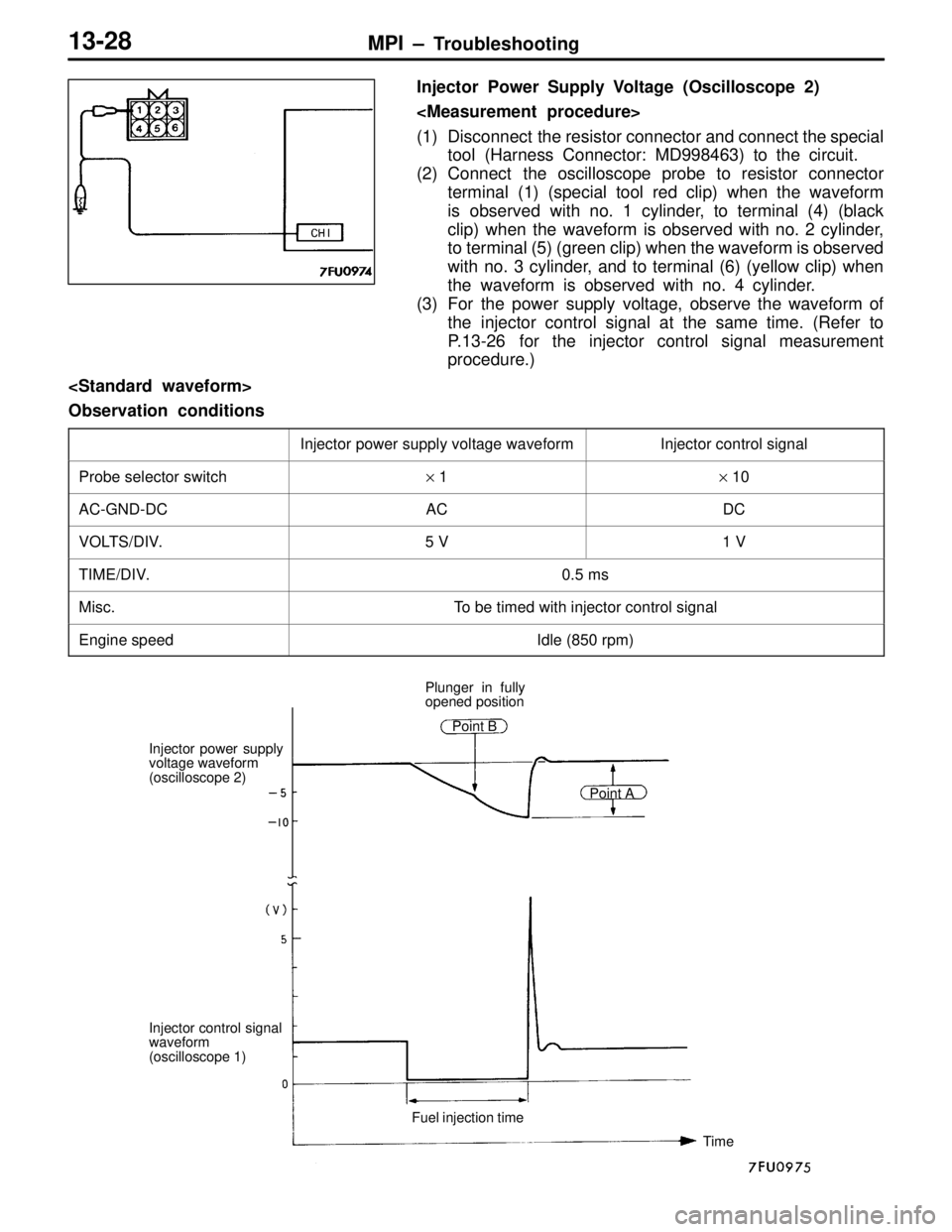
MPI – Troubleshooting13-28
Injector Power Supply Voltage (Oscilloscope 2)
(1) Disconnect the resistor connector and connect the special
tool (Harness Connector: MD998463) to the circuit.
(2) Connect the oscilloscope probe to resistor connector
terminal (1) (special tool red clip) when the waveform
is observed with no. 1 cylinder, to terminal (4) (black
clip) when the waveform is observed with no. 2 cylinder,
to terminal (5) (green clip) when the waveform is observed
with no. 3 cylinder, and to terminal (6) (yellow clip) when
the waveform is observed with no. 4 cylinder.
(3) For the power supply voltage, observe the waveform of
the injector control signal at the same time. (Refer to
P.13-26 for the injector control signal measurement
procedure.)
Observation conditions
Injector power supply voltage waveformInjector control signal
Probe selector switch× 1× 10
AC-GND-DCACDC
VOLTS/DIV.5 V1 V
TIME/DIV.0.5 ms
Misc.To be timed with injector control signal
Engine speedIdle (850 rpm)
Injector power supply
voltage waveform
(oscilloscope 2)
Injector control signal
waveform
(oscilloscope 1)Plunger in fully
opened position
Point B
Point A
Fuel injection time
Time
Page 72 of 396
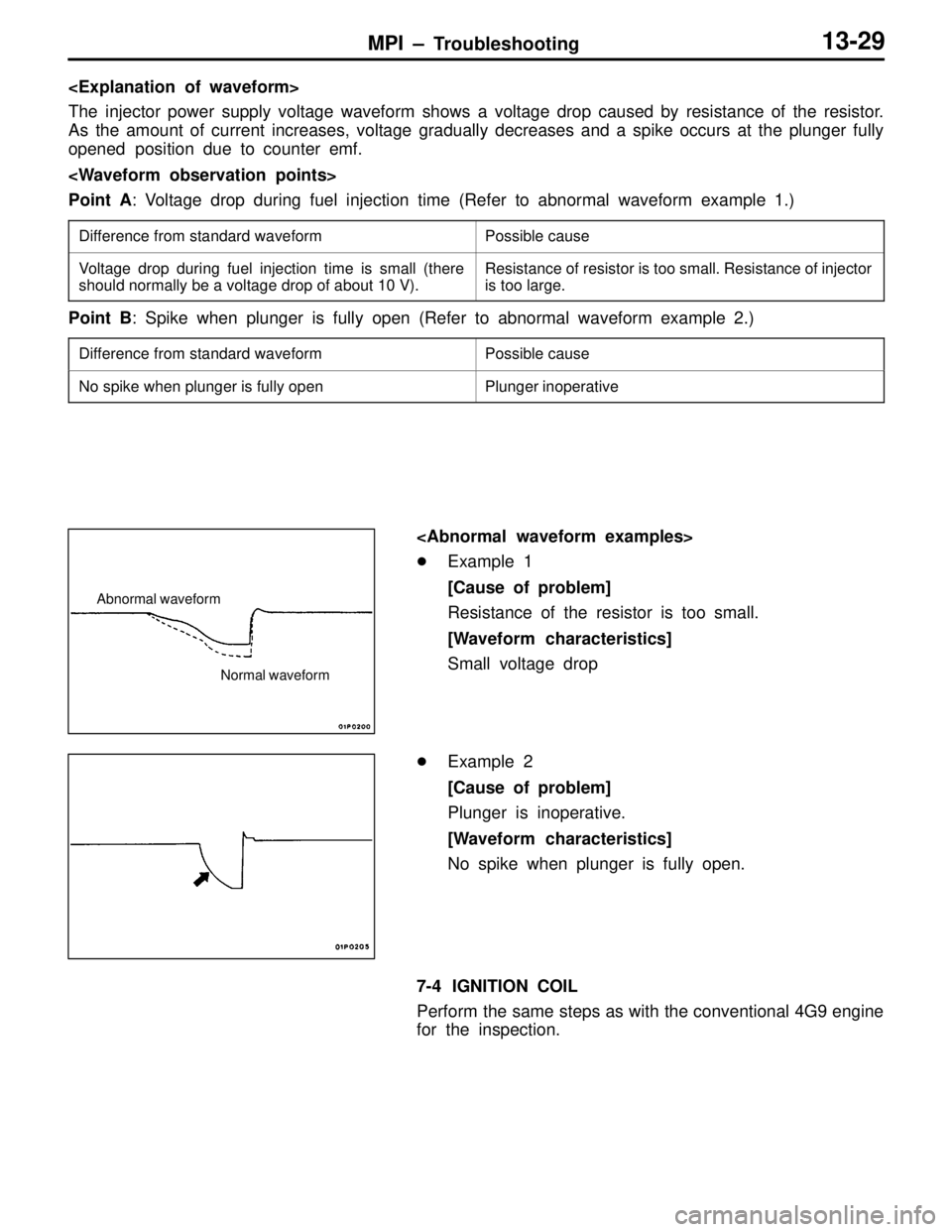
MPI – Troubleshooting13-29
The injector power supply voltage waveform shows a voltage drop caused by resistance of the resistor.
As the amount of current increases, voltage gradually decreases and a spike occurs at the plunger fully
opened position due to counter emf.
Point A: Voltage drop during fuel injection time (Refer to abnormal waveform example 1.)
Difference from standard waveformPossible cause
Voltage drop during fuel injection time is small (there
should normally be a voltage drop of about 10 V).Resistance of resistor is too small. Resistance of injector
is too large.
Point B: Spike when plunger is fully open (Refer to abnormal waveform example 2.)
Difference from standard waveformPossible cause
No spike when plunger is fully openPlunger inoperative
Example 1
[Cause of problem]
Resistance of the resistor is too small.
[Waveform characteristics]
Small voltage drop
Example 2
[Cause of problem]
Plunger is inoperative.
[Waveform characteristics]
No spike when plunger is fully open.
7-4 IGNITION COIL
Perform the same steps as with the conventional 4G9 engine
for the inspection.
Abnormal waveform
Normal waveform