Page 33 of 396
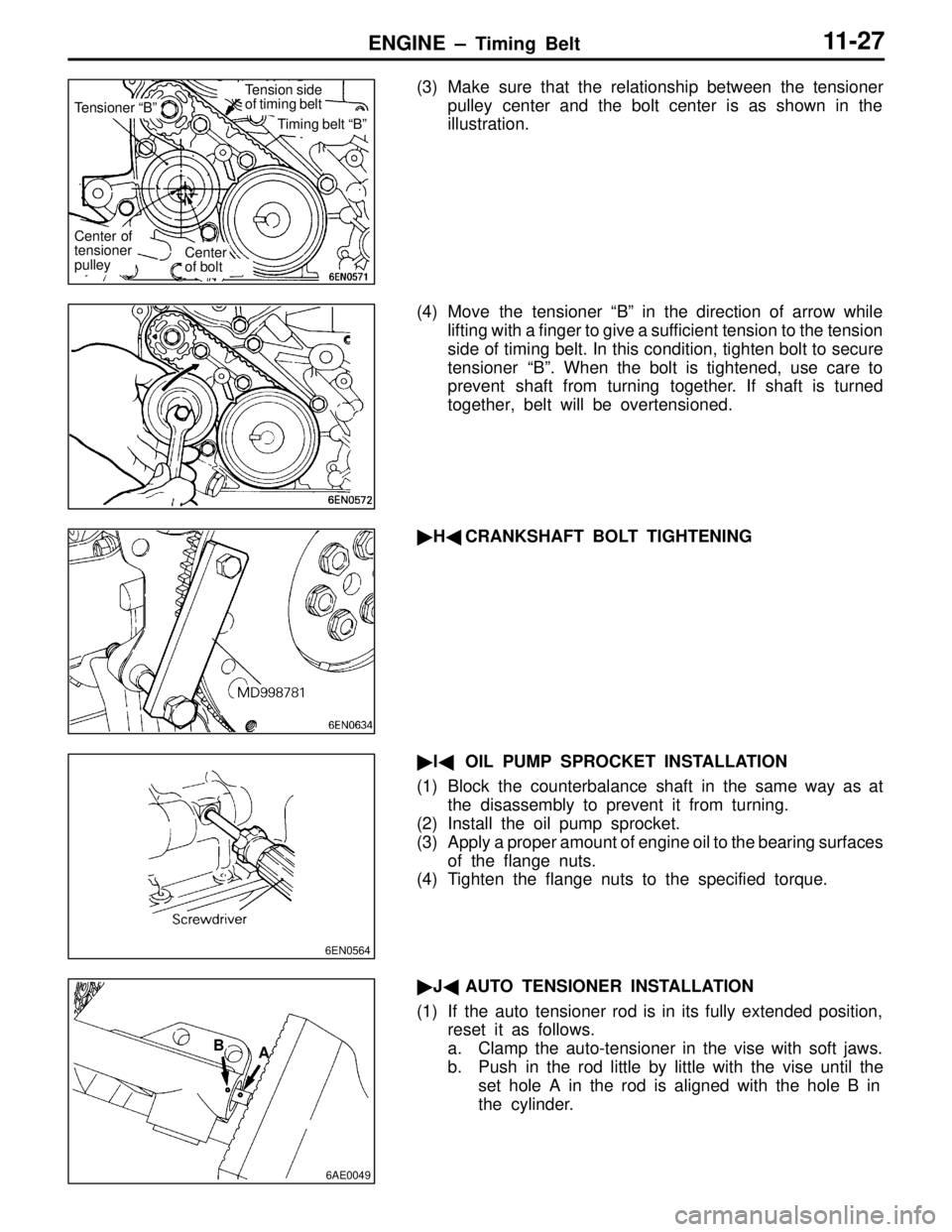
ENGINE – T iming Belt 11-27
(3) Make sure that the relationship between the tensioner
pulley center and the bolt center is as shown in the
illustration.
(4) Move the tensioner “B” in the direction of arrow while
lifting with a finger to give a sufficient tension to the tension
side of timing belt. In this condition, tighten bolt to secure
tensioner “B” . When the bolt is tightened, use care to
prevent shaft from turning together. If shaft is turned
together, belt will be overtensioned.
H CRANKSHAFT BOLT TIGHTENING
I OIL PUMP SPROCKET INSTALLATION
(1) Block the counterbalance shaft in the same way as at the disassembly to prevent it from turning.
(2) Install the oil pump sprocket.
(3) Apply a proper amount of engine oil to the bearing surfaces
of the flange nuts.
(4) Tighten the flange nuts to the specified torque.
J AUTO TENSIONER INSTALLATION
(1) If the auto tensioner rod is in its fully extended position, reset it as follows.
a. Clamp the auto-tensioner in the vise with soft jaws.
b. Push in the rod little by little with the vise until the
set hole A in the rod is aligned with the hole B in
the cylinder.
Tensioner “B”
Timing belt “B”
Tension side
of timing belt
Center of
tensioner
pulley
Center
of bolt
6EN0564
6AE0049
A
B
Page 34 of 396
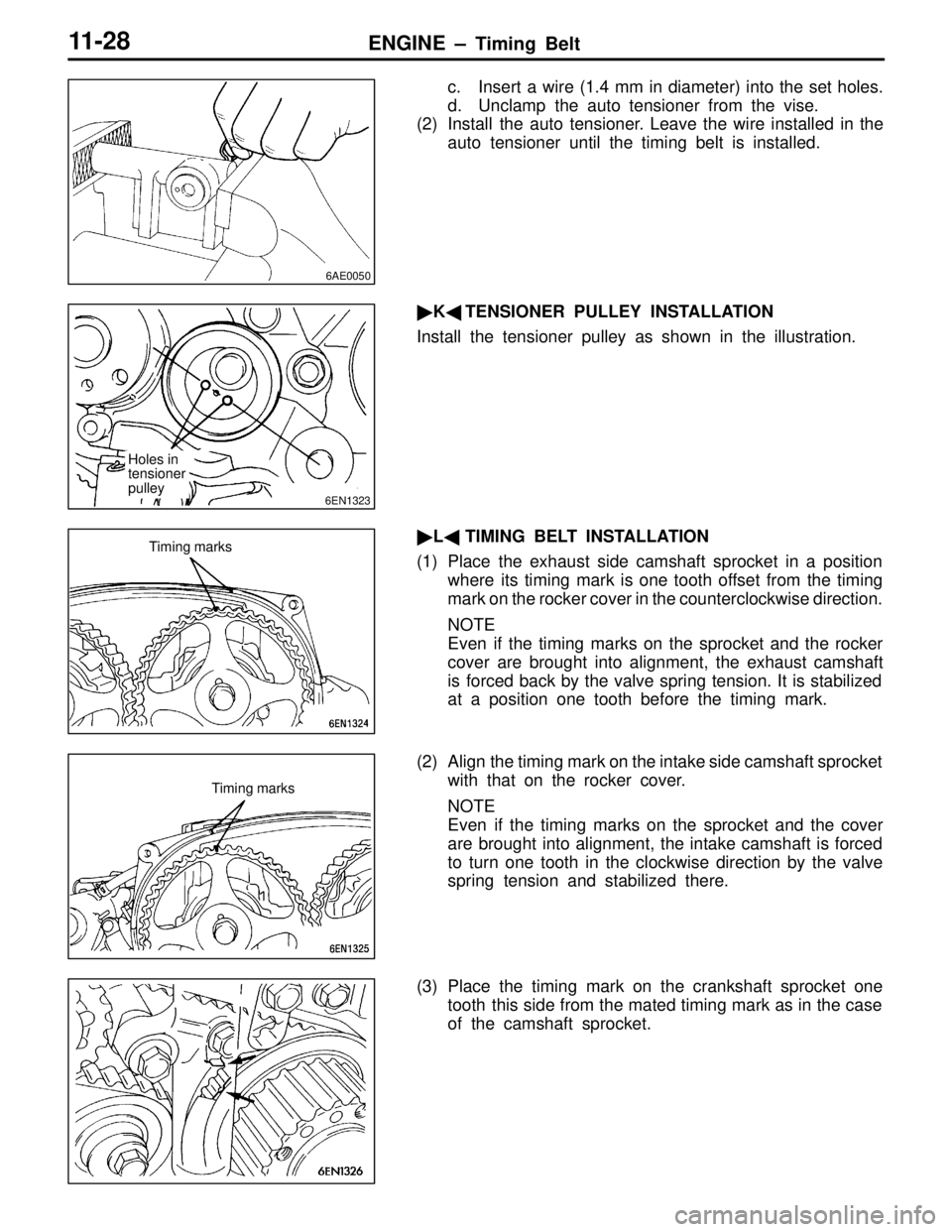
ENGINE – Timing Belt11-28
c. Insert a wire (1.4 mm in diameter) into the set holes.
d. Unclamp the auto tensioner from the vise.
(2) Install the auto tensioner. Leave the wire installed in the
auto tensioner until the timing belt is installed.
K TENSIONER PULLEY INSTALLATION
Install the tensioner pulley as shown in the illustration.
L TIMING BELT INSTALLATION
(1) Place the exhaust side camshaft sprocket in a position where its timing mark is one tooth offset from the timing
mark on the rocker cover in the counterclockwise direction.
NOTE
Even if the timing marks on the sprocket and the rocker
cover are brought into alignment, the exhaust camshaft
is forced back by the valve spring tension. It is stabilized
at a position one tooth before the timing mark.
(2) Align the timing mark on the intake side camshaft sprocket with that on the rocker cover.
NOTE
Even if the timing marks on the sprocket and the cover
are brought into alignment, the intake camshaft is forced
to turn one tooth in the clockwise direction by the valve
spring tension and stabilized there.
(3) Place the timing mark on the crankshaft sprocket one tooth this side from the mated timing mark as in the case
of the camshaft sprocket.
6AE0050
6EN1323
Holes in
tensioner
pulley
Timing marks
Timing marks
Page 35 of 396
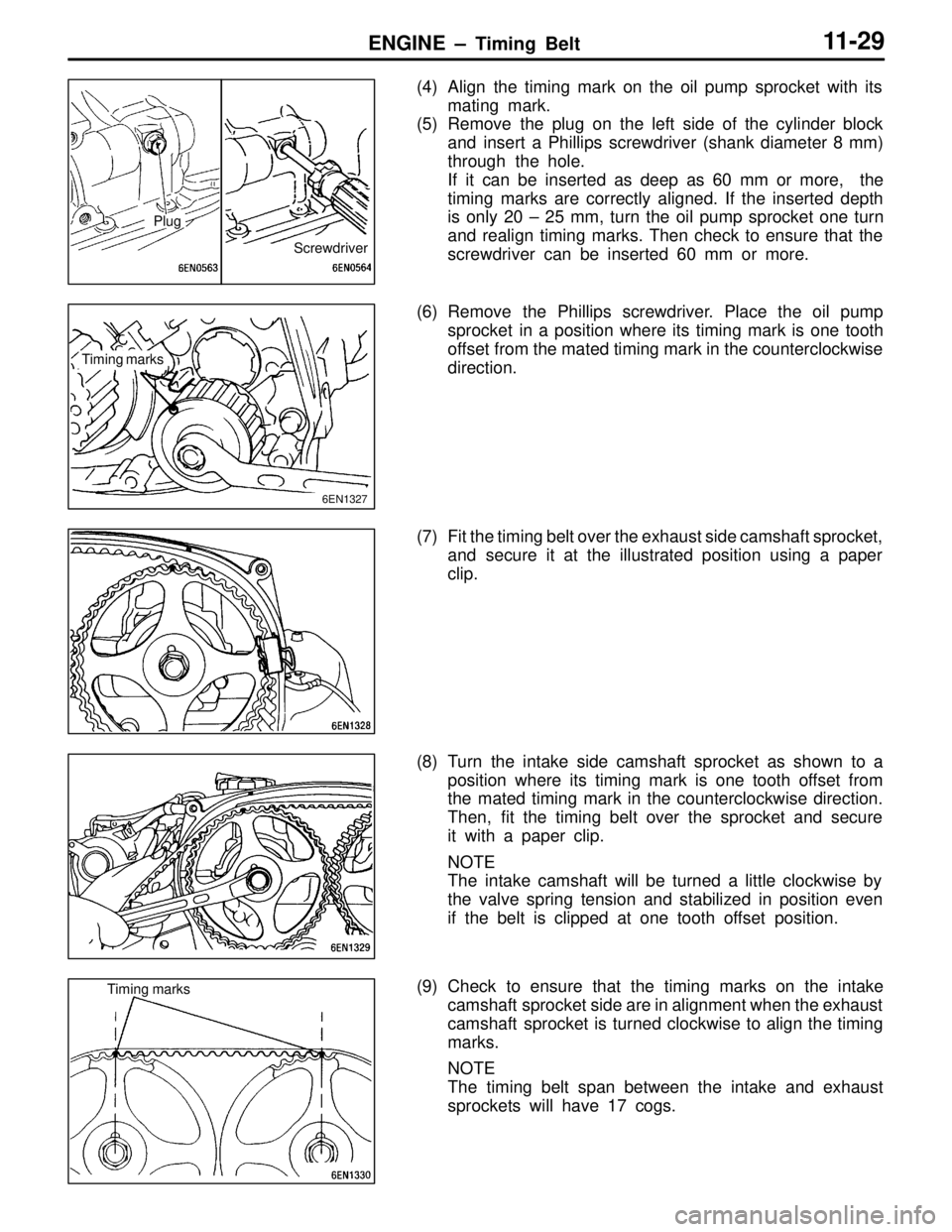
ENGINE – T iming Belt 11-29
(4) Align the timing mark on the oil pump sprocket with its
mating mark.
(5) Remove the plug on the left side of the cylinder block
and insert a Phillips screwdriver (shank diameter 8 mm)
through the hole.
If it can be inserted as deep as 60 mm or more, the
timing marks are correctly aligned. If the inserted depth
is only 20 – 25 mm, turn the oil pump sprocket one turn
and realign timing marks. Then check to ensure that the
screwdriver can be inserted 60 mm or more.
(6) Remove the Phillips screwdriver. Place the oil pump sprocket in a position where its timing mark is one tooth
offset from the mated timing mark in the counterclockwise
direction.
(7) Fit the timing belt over the exhaust side camshaft sprocket, and secure it at the illustrated position using a paper
clip.
(8) Turn the intake side camshaft sprocket as shown to a position where its timing mark is one tooth offset from
the mated timing mark in the counterclockwise direction.
Then, fit the timing belt over the sprocket and secure
it with a paper clip.
NOTE
The intake camshaft will be turned a little clockwise by
the valve spring tension and stabilized in position even
if the belt is clipped at one tooth offset position.
(9) Check to ensure that the timing marks on the intake camshaft sprocket side are in alignment when the exhaust
camshaft sprocket is turned clockwise to align the timing
marks.
NOTE
The timing belt span between the intake and exhaust
sprockets will have 17 cogs.
Screwdriver
Plug
Timing marks
6EN1327
Timing marks
Page 36 of 396
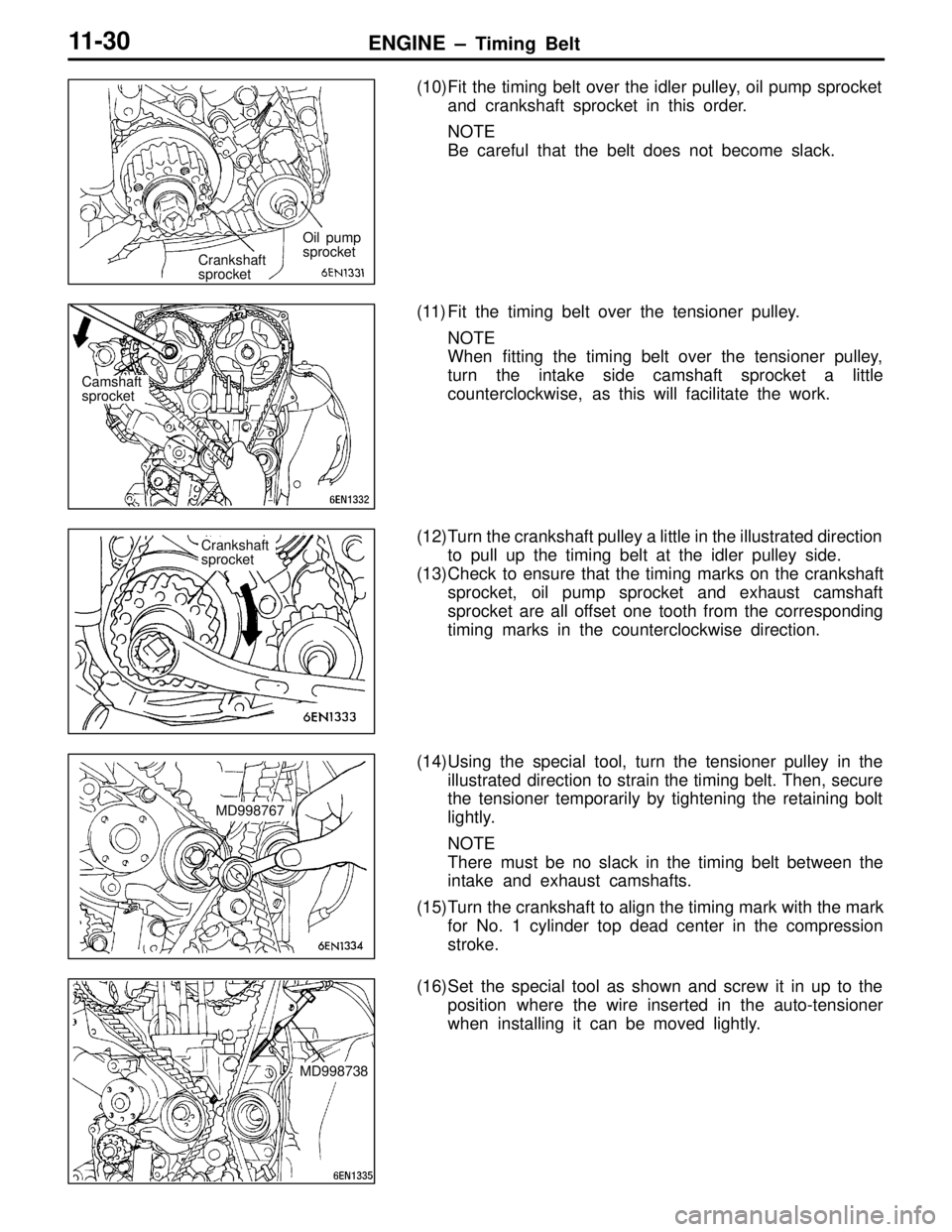
ENGINE – Timing Belt11-30
(10)Fit the timing belt over the idler pulley, oil pump sprocket
and crankshaft sprocket in this order.
NOTE
Be careful that the belt does not become slack.
(11) Fit the timing belt over the tensioner pulley. NOTE
When fitting the timing belt over the tensioner pulley,
turn the intake side camshaft sprocket a little
counterclockwise, as this will facilitate the work.
(12)Turn the crankshaft pulley a little in the illustrated direction to pull up the timing belt at the idler pulley side.
(13)Check to ensure that the timing marks on the crankshaft sprocket, oil pump sprocket and exhaust camshaft
sprocket are all offset one tooth from the corresponding
timing marks in the counterclockwise direction.
(14)Using the special tool, turn the tensioner pulley in the illustrated direction to strain the timing belt. Then, secure
the tensioner temporarily by tightening the retaining bolt
lightly.
NOTE
There must be no slack in the timing belt between the
intake and exhaust camshafts.
(15)Turn the crankshaft to align the timing mark with the mark for No. 1 cylinder top dead center in the compression
stroke.
(16)Set the special tool as shown and screw it in up to the position where the wire inserted in the auto-tensioner
when installing it can be moved lightly.
Crankshaft
sprocket Oil pump
sprocket
Camshaft
sprocket
Crankshaft
sprocket
MD998767
MD998738
Page 37 of 396
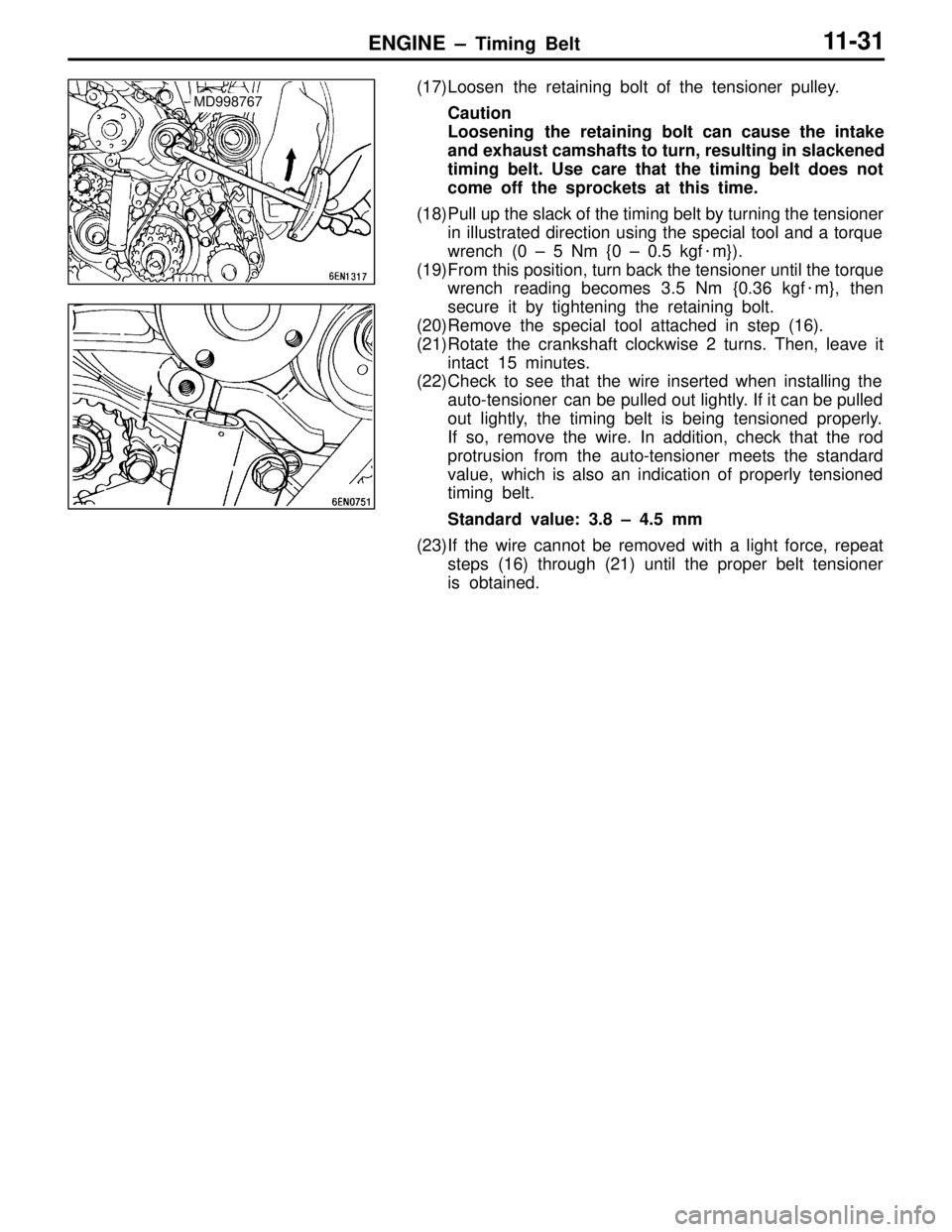
ENGINE – T iming Belt 11-31
(17)Loosen the retaining bolt of the tensioner pulley.
Caution
Loosening the retaining bolt can cause the intake
and exhaust camshafts to turn, resulting in slackened
timing belt. Use care that the timing belt does not
come off the sprockets at this time.
(18)Pull up the slack of the timing belt by turning the tensioner in illustrated direction using the special tool and a torque
wrench (0 – 5 Nm {0 – 0.5 kgf m}).
(19)From this position, turn back the tensioner until the torque wrench reading becomes 3.5 Nm {0.36 kgf m}, then
secure it by tightening the retaining bolt.
(20)Remove the special tool attached in step (16).
(21)Rotate the crankshaft clockwise 2 turns. Then, leave it intact 15 minutes.
(22)Check to see that the wire inserted when installing the
auto-tensioner can be pulled out lightly. If it can be pulled
out lightly, the timing belt is being tensioned properly.
If so, remove the wire. In addition, check that the rod
protrusion from the auto-tensioner meets the standard
value, which is also an indication of properly tensioned
timing belt.
Standard value: 3.8 – 4.5 mm
(23)If the wire cannot be removed with a light force, repeat steps (16) through (21) until the proper belt tensioner
is obtained.MD998767
Page 38 of 396
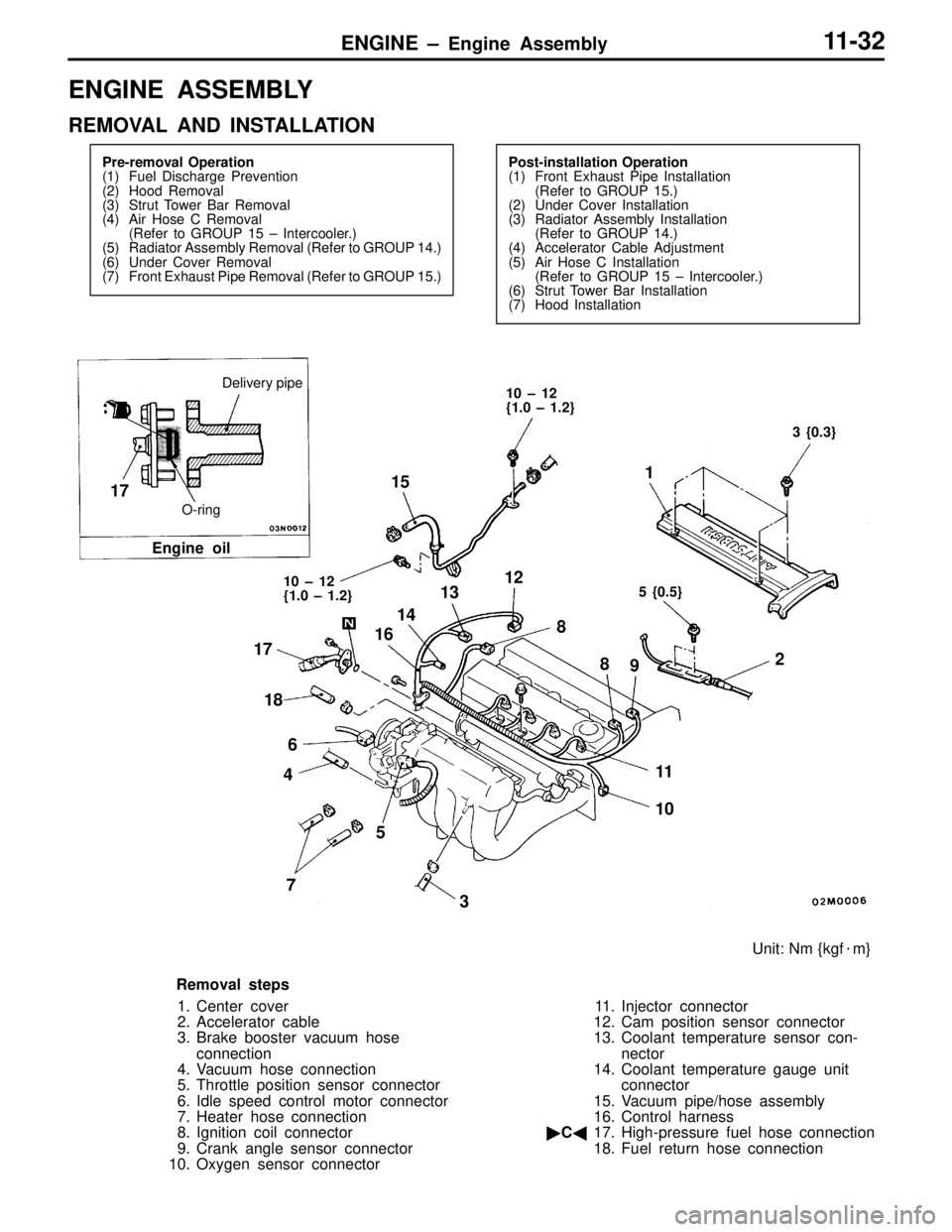
ENGINE – Engine Assembly 11- 32
ENGINE ASSEMBLY
REMOVAL AND INSTALLATION
Pre-removal Operation
(1) Fuel Discharge Prevention
(2) Hood Removal
(3) Strut Tower Bar Removal
(4) Air Hose C Removal
(Refer to GROUP 15 – Intercooler.)
(5) Radiator Assembly Removal (Refer to GROUP 14.)
(6) Under Cover Removal
(7) Front Exhaust Pipe Removal (Refer to GROUP 15.)Post-installation Operation
(1) Front Exhaust Pipe Installation
(Refer to GROUP 15.)
(2) Under Cover Installation
(3) Radiator Assembly Installation (Refer to GROUP 14.)
(4) Accelerator Cable Adjustment
(5) Air Hose C Installation (Refer to GROUP 15 – Intercooler.)
(6) Strut Tower Bar Installation
(7) Hood Installation
O-ring Delivery pipe
1
2
3
4
5
6
7 8
9
10
11
18 12
Engine oil
5 {0.5}
Unit: Nm {kgf
m}
10 – 12
{1.0 – 1.2}
17 1614 13
10
– 12
{1.0 – 1.2}
15
3 {0.3}
17
8
Removal steps1. Center cover
2. Accelerator cable
3. Brake booster vacuum hose connection
4. Vacuum hose connection
5. Throttle position sensor connector
6. Idle speed control motor connector
7. Heater hose connection
8. Ignition coil connector
9. Crank angle sensor connector
10. Oxygen sensor connector 11. Injector connector
12. Cam position sensor connector
13. Coolant temperature sensor con-
nector
14. Coolant temperature gauge unit connector
15. Vacuum pipe/hose assembly
16. Control harness
C 17. High-pressure fuel hose connection
18. Fuel return hose connection
Page 39 of 396
ENGINE – Engine Assembly11- 33
25
27 2819
20 21
22 23
24
26
Unit: Nm {kgf m}
98 {10.0}*
29
57 {5.8}
22
12 {1.2} 39 {4.0}
9 {0.9}
19. Solenoid valve connector
20. Vacuum tank/solenoid valve/vacuum hose assembly
21. Oil pressure switch connector
22. Alternator connector Drive belt tension inspection
(Refer to P.11-4.)
A 23. Drive belt
B 24. A/C compressor
C 25. Power steering oil pump
Transmission assembly 26. A/C relay box
27. A/C receiver bracket mounting bolt
28. Oil pressure hose mounting bolt
C B 29. Engine mount bracket
E A 30. Engine assembly
Caution
Mounting locations marked by * should be
provisionally tightened, and then fully tightened after
placing the vehicle horizontally and loading the full
weight of the engine on the vehicle body.
Page 40 of 396
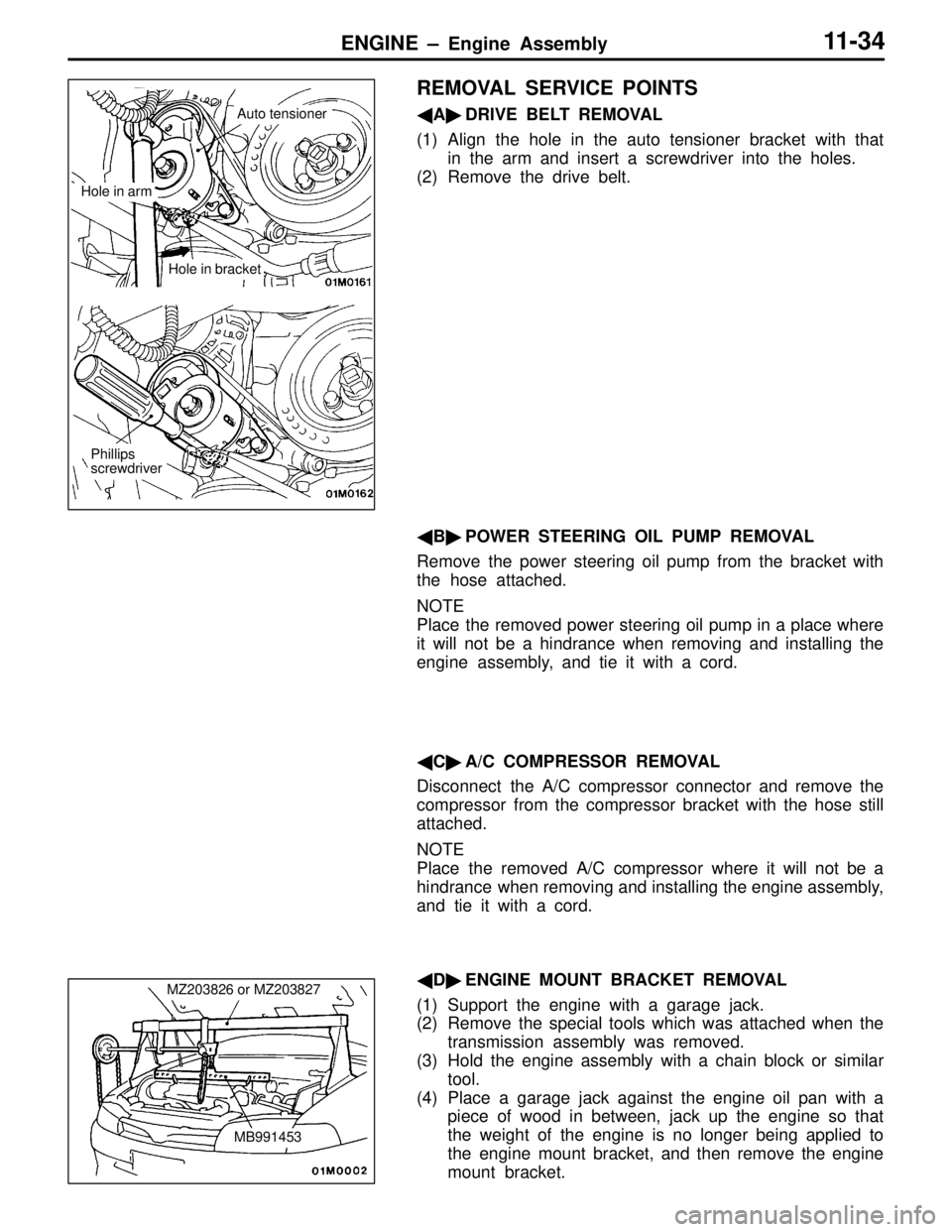
ENGINE – Engine Assembly 11- 34
REMOVAL SERVICE POINTS
A DRIVE BELT REMOVAL
(1) Align the hole in the auto tensioner bracket with that in the arm and insert a screwdriver into the holes.
(2) Remove the drive belt.
B POWER STEERING OIL PUMP REMOVAL
Remove the power steering oil pump from the bracket with
the hose attached.
NOTE
Place the removed power steering oil pump in a place where
it will not be a hindrance when removing and installing the
engine assembly, and tie it with a cord.
C A/C COMPRESSOR REMOVAL
Disconnect the A/C compressor connector and remove the
compressor from the compressor bracket with the hose still
attached.
NOTE
Place the removed A/C compressor where it will not be a
hindrance when removing and installing the engine assembly,
and tie it with a cord.
D ENGINE MOUNT BRACKET REMOVAL
(1) Support the engine with a garage jack.
(2) Remove the special tools which was attached when the transmission assembly was removed.
(3) Hold the engine assembly with a chain block or similar tool.
(4) Place a garage jack against the engine oil pan with a piece of wood in between, jack up the engine so that
the weight of the engine is no longer being applied to
the engine mount bracket, and then remove the engine
mount bracket.
Phillips
screwdriver
Hole in arm
Auto tensioner
Hole in bracket
MZ203826 or MZ203827
MB991453