Page 249 of 396
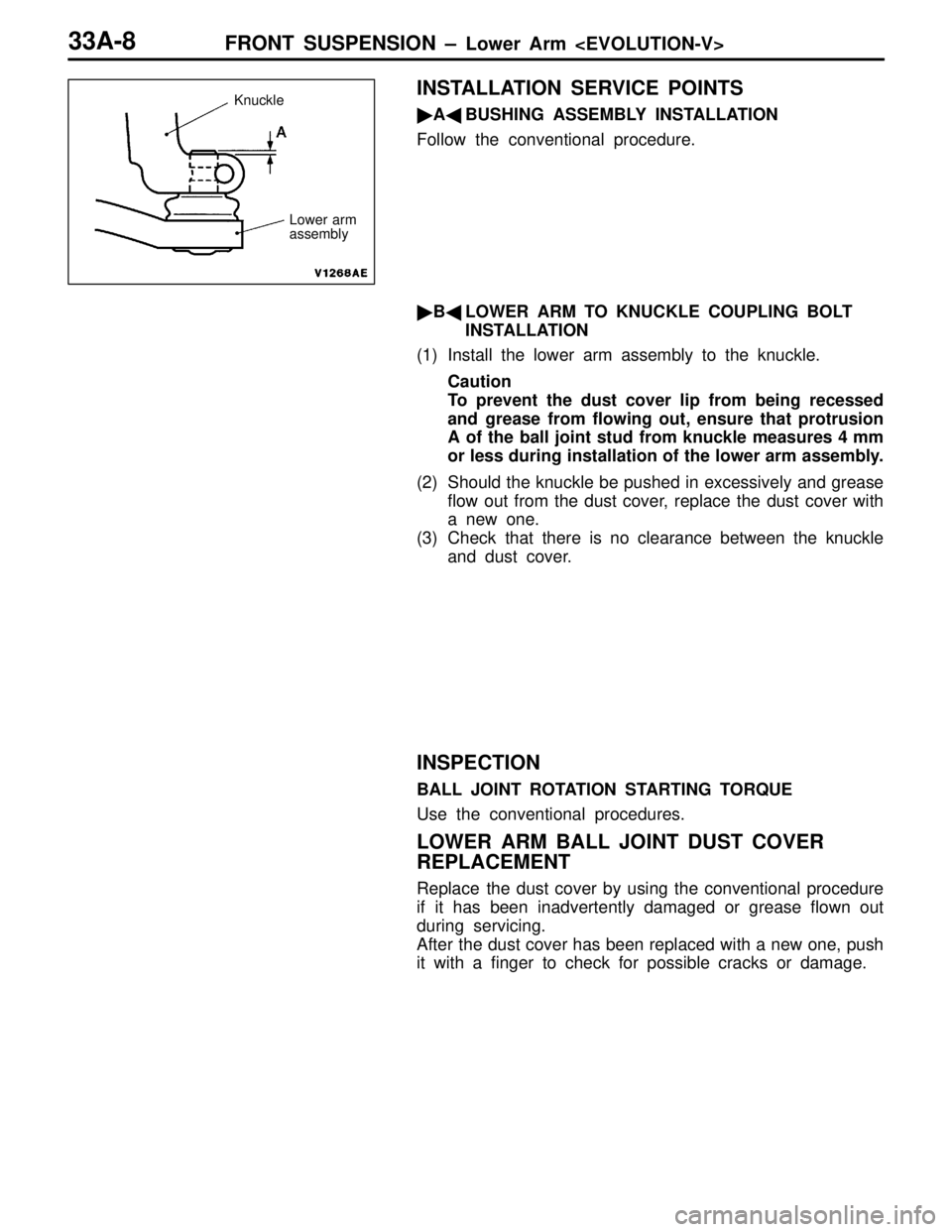
FRONT SUSPENSION – Lower Arm 33A-8
INSTALLATION SERVICE POINTS
ABUSHING ASSEMBLY INSTALLATION
Follow the conventional procedure.
BLOWER ARM TO KNUCKLE COUPLING BOLT
INSTALLATION
(1) Install the lower arm assembly to the knuckle.
Caution
To prevent the dust cover lip from being recessed
and grease from flowing out, ensure that protrusion
A of the ball joint stud from knuckle measures 4 mm
or less during installation of the lower arm assembly.
(2) Should the knuckle be pushed in excessively and grease
flow out from the dust cover, replace the dust cover with
a new one.
(3) Check that there is no clearance between the knuckle
and dust cover.
INSPECTION
BALL JOINT ROTATION STARTING TORQUE
Use the conventional procedures.
LOWER ARM BALL JOINT DUST COVER
REPLACEMENT
Replace the dust cover by using the conventional procedure
if it has been inadvertently damaged or grease flown out
during servicing.
After the dust cover has been replaced with a new one, push
it with a finger to check for possible cracks or damage.
Knuckle
Lower arm
assembly
Page 250 of 396
FRONT SUSPENSION – Stabilizer Bar33A-9
STABILIZER BAR
REMOVAL AND INSTALLATION
Pre-removal Operation
Crossmember RemovalPost-installation Operation
(1) Crossmember Installation
(2) Check the Stabilizer Link Ball Joint Dust Cover for
Cracks or Damage by Pushing it with Finger.
1
23
4
5
Unit: Nm {kgfm}
22 {2.2}
SHOWA SHELL SEKIYU
VARIANT R-2 or equivalent
39 {4.0}
39 {4.0}
1
Removal steps
1. Stabilizer link
2. Stabilizer bar bracket
A3. Fixture
A4. Bushing
5. Stabilizer bar
INSTALLATION SERVICE POINT
AFIXTURE / BUSHING INSTALLATION
Install the stabilizer bar so that the identification mark is
positioned at left. Fit the bushing so that the mark may protrude
about 10 mm from the inner end of the bushing, then secure
it with the fixture.Approx. 10 mm
Page 251 of 396
FRONT SUSPENSION – Stabilizer Bar33A-10
INSPECTION
STABILIZER LINK BALL JOINT ROTATION STARTING
TORQUE
Follow the conventional procedures.
STABILIZER LINK DUST COVER
REPLACEMENT
Replace the dust cover by using the conventional procedure
only if it has been inadvertently damaged during servicing.
After the dust cover has been replaced with a new one, push
it with a finger to check for possible cracks or damage.
Page 252 of 396
34-1
REAR
SUSPENSION
CONTENTS
SERVICE SPECIFICATIONS 2. . . . . . . . . . . . . .
LUBRICANT 2. . . . . . . . . . . . . . . . . . . . . . . . . . . . .
SPECIAL TOOLS 2. . . . . . . . . . . . . . . . . . . . . . . .
ON-VEHICLE SERVICE 3. . . . . . . . . . . . . . . . . .
1. Rear Wheel Alignment Check and
Adjustment 3. . . . . . . . . . . . . . . . . . . . . . . . . . .
2. Ball Joint Dust Cover Check 3. . . . . . . . . . .
REAR SUSPENSION ASSEMBLY 4. . . . . . . . . UPPER ARM ASSEMBLY 6. . . . . . . . . . . . . . . .
TRAILING ARM ASSEMBLY 8. . . . . . . . . . . . . .
LOWER ARM AND TOE CONTROL
ARM ASSEMBLIES 10. . . . . . . . . . . . . . . . . . . .
SHOCK ABSORBER ASSEMBLY 13. . . . . . .
STABILIZER BAR 14. . . . . . . . . . . . . . . . . . . . . .
Page 253 of 396
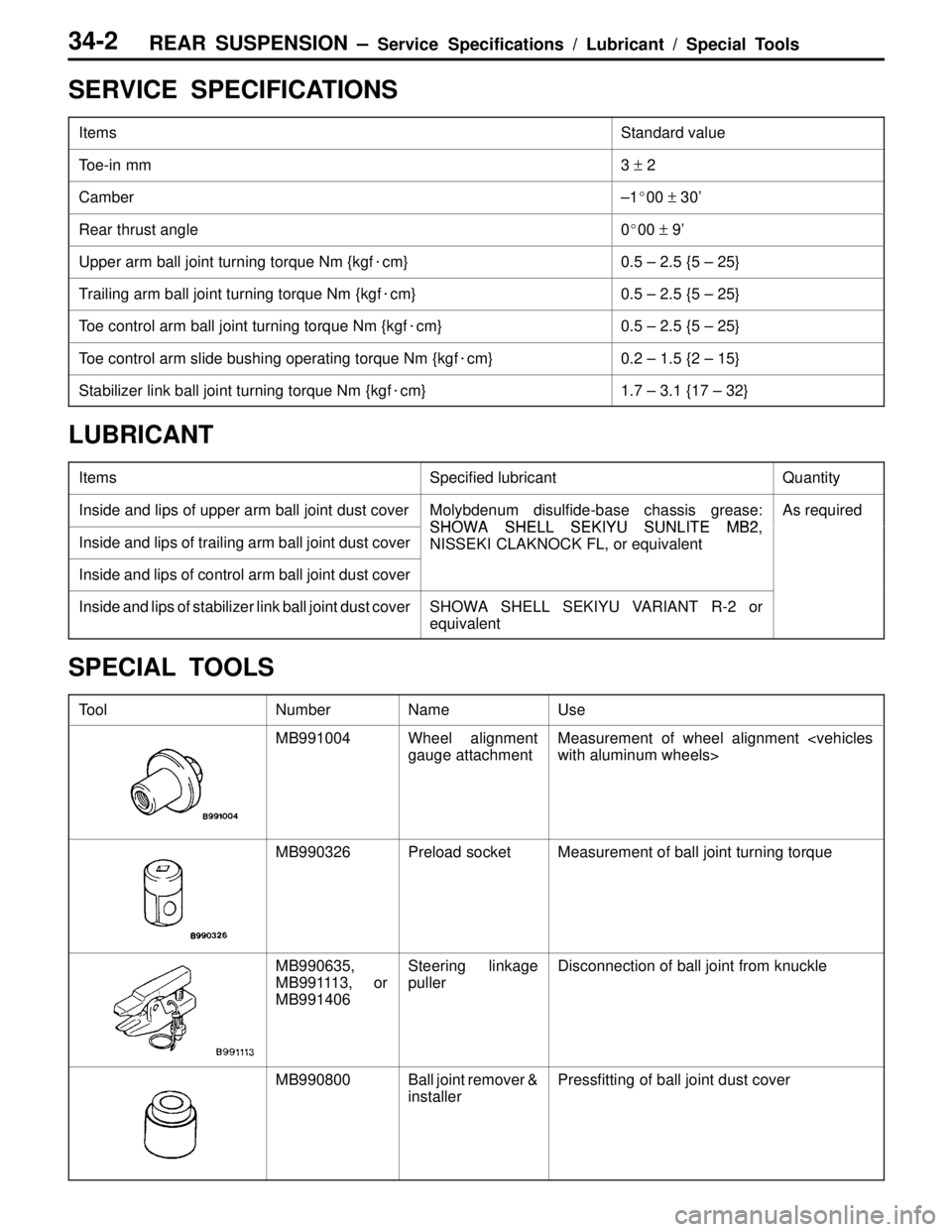
REAR SUSPENSION – Service Specifications / Lubricant / Special Tools34-2
SERVICE SPECIFICATIONS
ItemsStandard value
Toe-in mm3 ± 2
Camber–100 ± 30’
Rear thrust angle000 ± 9’
Upper arm ball joint turning torque Nm {kgfcm}0.5 – 2.5 {5 – 25}
Trailing arm ball joint turning torque Nm {kgfcm}0.5 – 2.5 {5 – 25}
Toe control arm ball joint turning torque Nm {kgfcm}0.5 – 2.5 {5 – 25}
Toe control arm slide bushing operating torque Nm {kgfcm}0.2 – 1.5 {2 – 15}
Stabilizer link ball joint turning torque Nm {kgfcm}1.7 – 3.1 {17 – 32}
LUBRICANT
ItemsSpecified lubricantQuantity
Inside and lips of upper arm ball joint dust coverMolybdenum disulfide-base chassis grease:
SHOWA SHELL SEKIYU SUNLITE MB2
As required
Inside and lips of trailing arm ball joint dust coverSHOWA SHELL SEKIYU SUNLITE MB2,
NISSEKI CLAKNOCK FL, or equivalent
Inside and lips of control arm ball joint dust cover
Inside and lips of stabilizer link ball joint dust coverSHOWA SHELL SEKIYU VARIANT R-2 or
equivalent
SPECIAL TOOLS
ToolNumberNameUse
MB991004Wheel alignment
gauge attachmentMeasurement of wheel alignment
with aluminum wheels>
MB990326Preload socketMeasurement of ball joint turning torque
MB990635,
MB991113, or
MB991406Steering linkage
pullerDisconnection of ball joint from knuckle
MB990800Ball joint remover &
installerPressfitting of ball joint dust cover
Page 254 of 396
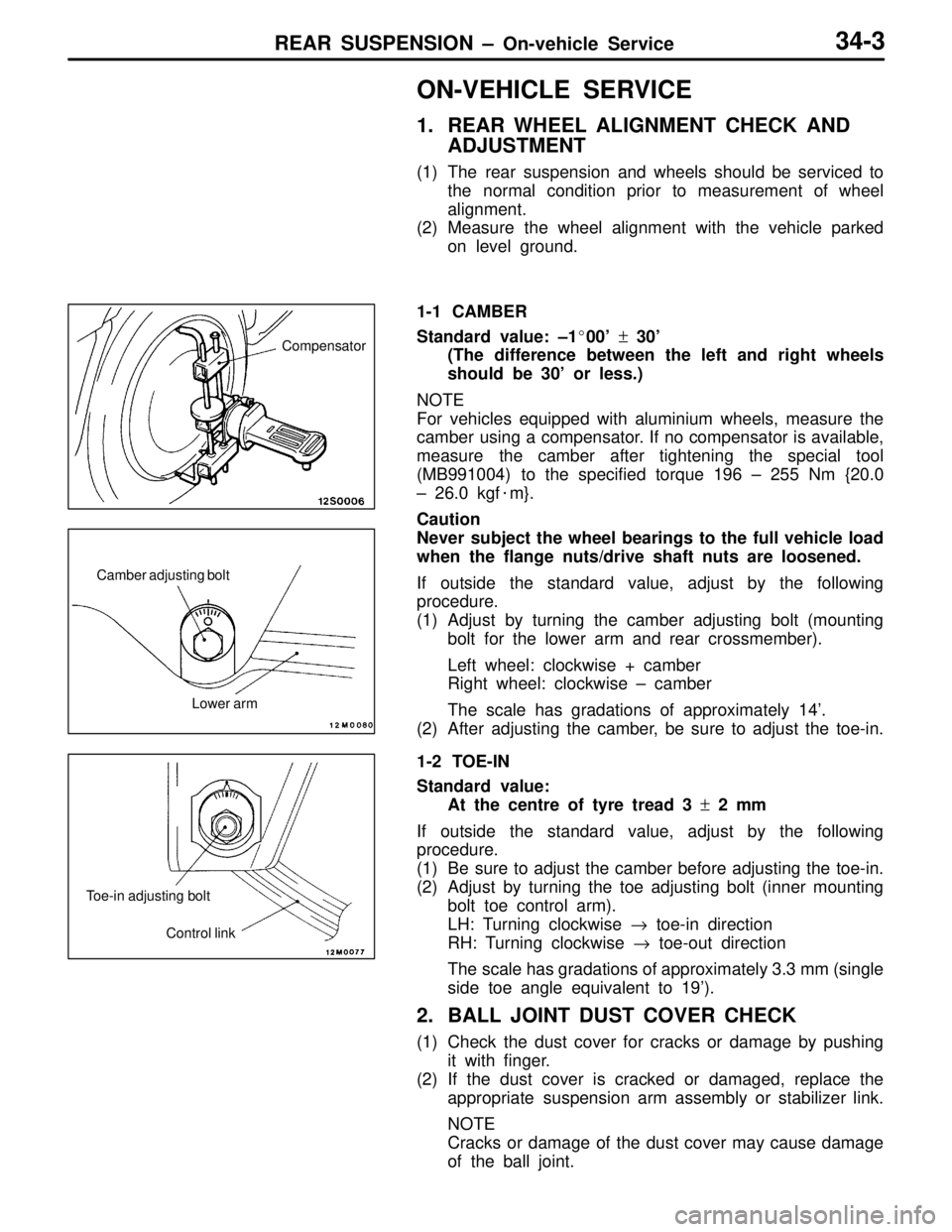
REAR SUSPENSION – On-vehicle Service34-3
ON-VEHICLE SERVICE
1. REAR WHEEL ALIGNMENT CHECK AND
ADJUSTMENT
(1) The rear suspension and wheels should be serviced to
the normal condition prior to measurement of wheel
alignment.
(2) Measure the wheel alignment with the vehicle parked
on level ground.
1-1 CAMBER
Standard value: –100’ ± 30’
(The difference between the left and right wheels
should be 30’ or less.)
NOTE
For vehicles equipped with aluminium wheels, measure the
camber using a compensator. If no compensator is available,
measure the camber after tightening the special tool
(MB991004) to the specified torque 196 – 255 Nm {20.0
– 26.0 kgfm}.
Caution
Never subject the wheel bearings to the full vehicle load
when the flange nuts/drive shaft nuts are loosened.
If outside the standard value, adjust by the following
procedure.
(1) Adjust by turning the camber adjusting bolt (mounting
bolt for the lower arm and rear crossmember).
Left wheel: clockwise + camber
Right wheel: clockwise – camber
The scale has gradations of approximately 14’.
(2) After adjusting the camber, be sure to adjust the toe-in.
1-2 TOE-IN
Standard value:
At the centre of tyre tread 3 ± 2 mm
If outside the standard value, adjust by the following
procedure.
(1) Be sure to adjust the camber before adjusting the toe-in.
(2) Adjust by turning the toe adjusting bolt (inner mounting
bolt toe control arm).
LH: Turning clockwise → toe-in direction
RH: Turning clockwise → toe-out direction
The scale has gradations of approximately 3.3 mm (single
side toe angle equivalent to 19’).
2. BALL JOINT DUST COVER CHECK
(1) Check the dust cover for cracks or damage by pushing
it with finger.
(2) If the dust cover is cracked or damaged, replace the
appropriate suspension arm assembly or stabilizer link.
NOTE
Cracks or damage of the dust cover may cause damage
of the ball joint.
Compensator
Camber adjusting bolt
Lower arm
Toe-in adjusting bolt
Control link
Page 255 of 396
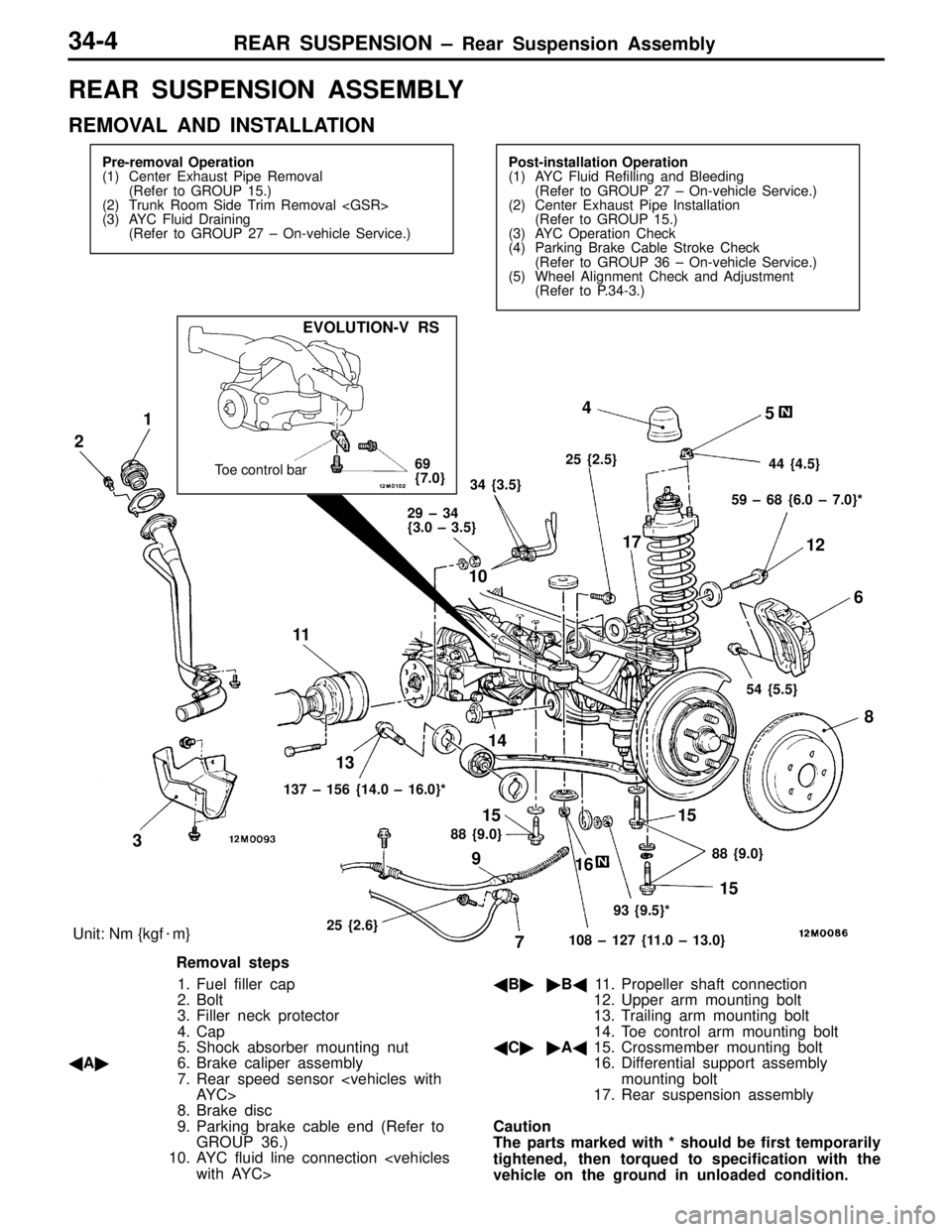
REAR SUSPENSION – Rear Suspension Assembly34-4
REAR SUSPENSION ASSEMBLY
REMOVAL AND INSTALLATION
Pre-removal Operation
(1) Center Exhaust Pipe Removal
(Refer to GROUP 15.)
(2) Trunk Room Side Trim Removal
(3) AYC Fluid Draining
(Refer to GROUP 27 – On-vehicle Service.)Post-installation Operation
(1) AYC Fluid Refilling and Bleeding
(Refer to GROUP 27 – On-vehicle Service.)
(2) Center Exhaust Pipe Installation
(Refer to GROUP 15.)
(3) AYC Operation Check
(4) Parking Brake Cable Stroke Check
(Refer to GROUP 36 – On-vehicle Service.)
(5) Wheel Alignment Check and Adjustment
(Refer to P.34-3.)
1
34
5
6
7 9 10
1112
1314
15 1617
Unit: Nm {kgfm}
44 {4.5}
108 – 127 {11.0 – 13.0}
54 {5.5}
88 {9.0}
93 {9.5}*88 {9.0}
158 2
15
29 – 34
{3.0 – 3.5}
25 {2.6}34 {3.5}25 {2.5}
69
{7.0} Toe control bar
EVOLUTION-V RS
137 – 156 {14.0 – 16.0}*59 – 68 {6.0 – 7.0}*
Removal steps
1. Fuel filler cap
2. Bolt
3. Filler neck protector
4. Cap
5. Shock absorber mounting nut
A6. Brake caliper assembly
7. Rear speed sensor
AYC>
8. Brake disc
9. Parking brake cable end (Refer to
GROUP 36.)
10. AYC fluid line connection
with AYC>BB11. Propeller shaft connection
12. Upper arm mounting bolt
13. Trailing arm mounting bolt
14. Toe control arm mounting bolt
CA15. Crossmember mounting bolt
16. Differential support assembly
mounting bolt
17. Rear suspension assembly
Caution
The parts marked with * should be first temporarily
tightened, then torqued to specification with the
vehicle on the ground in unloaded condition.
Page 256 of 396
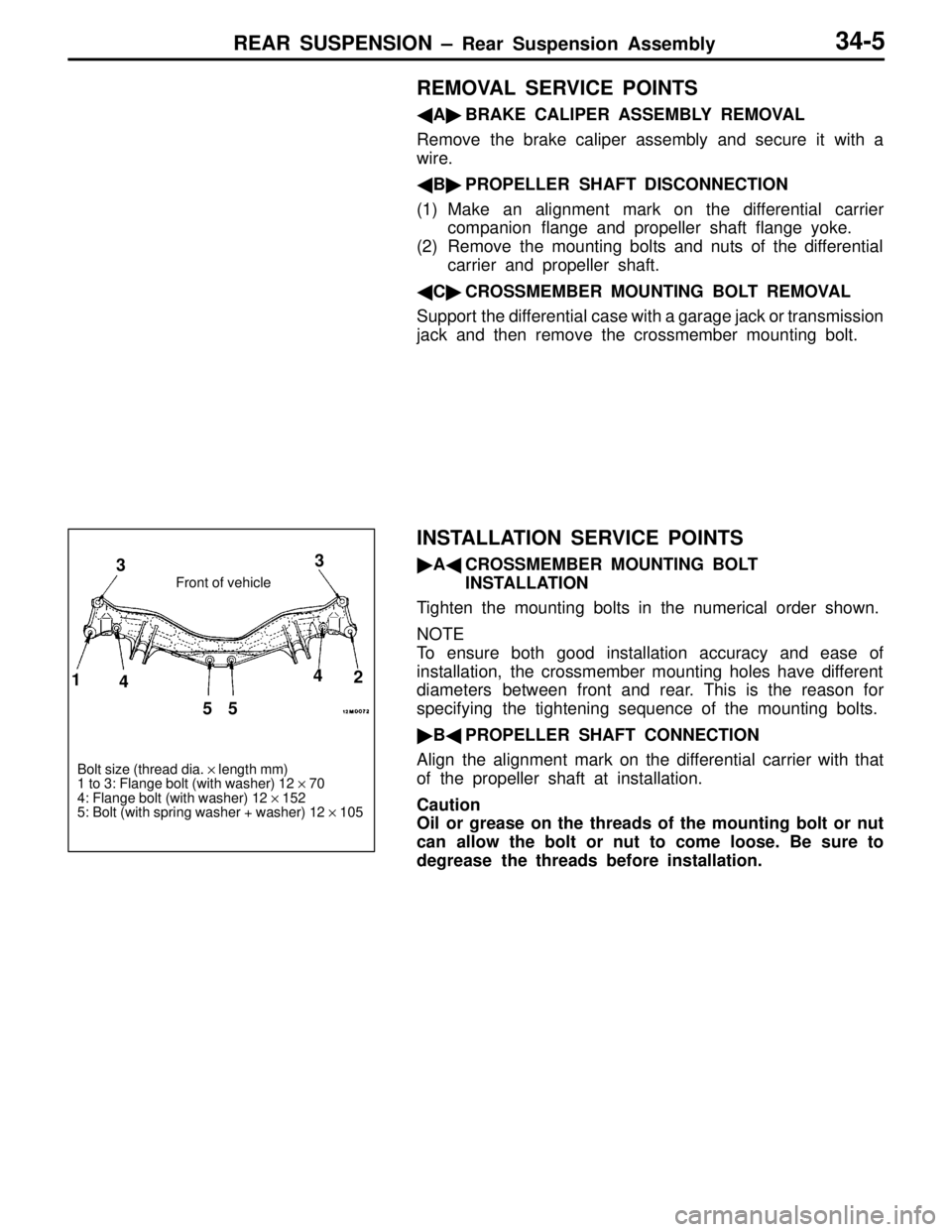
REAR SUSPENSION – Rear Suspension Assembly34-5
REMOVAL SERVICE POINTS
ABRAKE CALIPER ASSEMBLY REMOVAL
Remove the brake caliper assembly and secure it with a
wire.
BPROPELLER SHAFT DISCONNECTION
(1) Make an alignment mark on the differential carrier
companion flange and propeller shaft flange yoke.
(2) Remove the mounting bolts and nuts of the differential
carrier and propeller shaft.
CCROSSMEMBER MOUNTING BOLT REMOVAL
Support the differential case with a garage jack or transmission
jack and then remove the crossmember mounting bolt.
INSTALLATION SERVICE POINTS
ACROSSMEMBER MOUNTING BOLT
INSTALLATION
Tighten the mounting bolts in the numerical order shown.
NOTE
To ensure both good installation accuracy and ease of
installation, the crossmember mounting holes have different
diameters between front and rear. This is the reason for
specifying the tightening sequence of the mounting bolts.
BPROPELLER SHAFT CONNECTION
Align the alignment mark on the differential carrier with that
of the propeller shaft at installation.
Caution
Oil or grease on the threads of the mounting bolt or nut
can allow the bolt or nut to come loose. Be sure to
degrease the threads before installation.
Bolt size (thread dia. × length mm)
1 to 3: Flange bolt (with washer) 12 × 70
4: Flange bolt (with washer) 12 × 152
5: Bolt (with spring washer + washer) 12 × 105 Front of vehicle
13
3
44
2
55