Page 97 of 396
INTAKE AND EXHAUST – Air Control Valve15-8
AIR CONTROL VALVE
REMOVAL AND INSTALLATION
1
Unit: Nm {kgfm}
22 {2.2}
35 {3.6}49 {5.0}
24 {2.4}4 {0.4}10 – 12 {1.0 – 1.2}
4 {0.4}10 – 12
{1.0 – 1.2}
24 {2.4}
22 {2.2}
2
3
8 7 64 5
12 – 15 {1.2 – 1.5}
Removal steps
1. Control harness connection
2. Vacuum pipe hose assembly
3. Air pipe assembly
A4. Gasket5. Air hose
6. Air control valve
7. Engine hanger
8. Air control valve bracket
INSTALLATION SERVICE POINT
AGASKET INSTALLATION
Install the gasket so that its protrusion is located as shown.Protrusion
Page 98 of 396
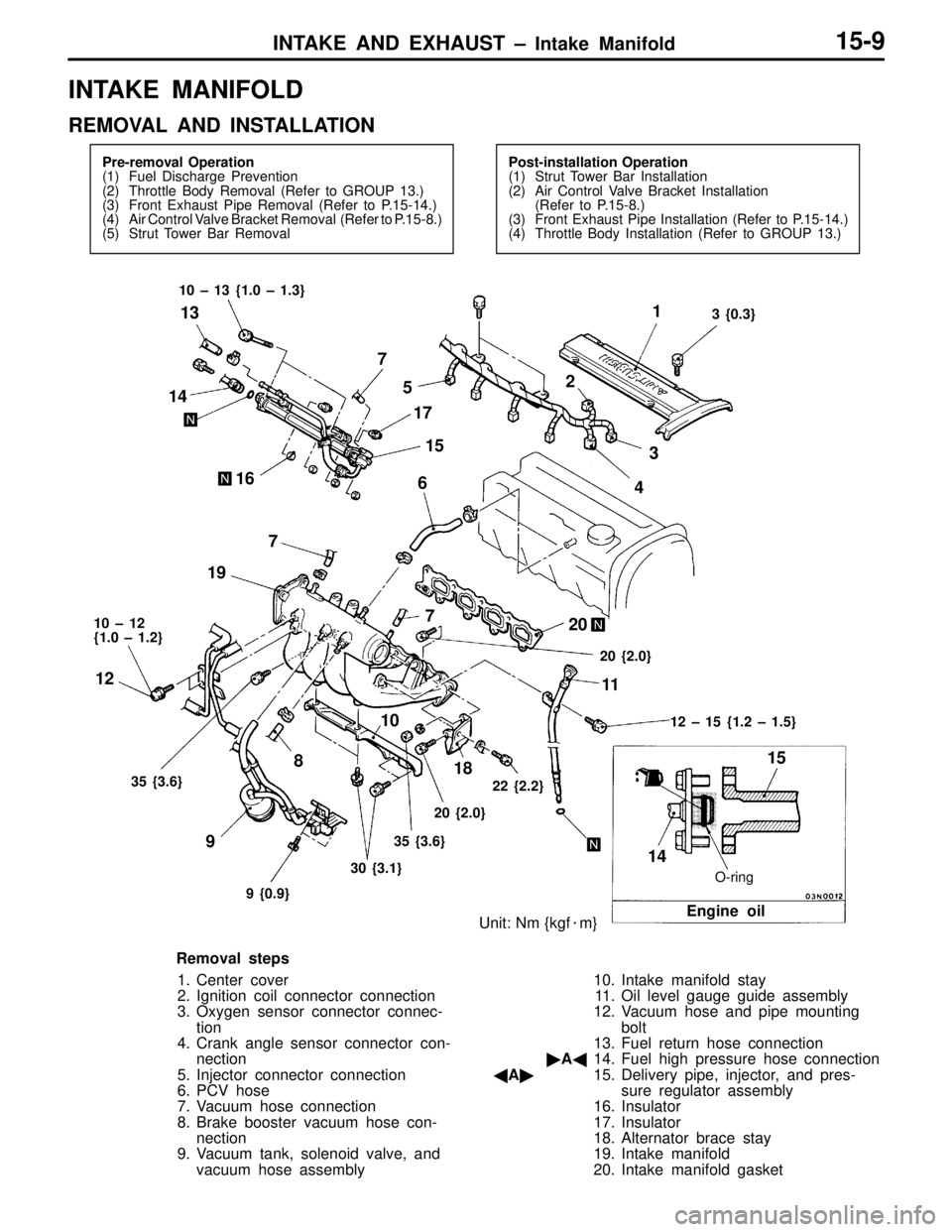
INTAKE AND EXHAUST – Intake Manifold15-9
INTAKE MANIFOLD
REMOVAL AND INSTALLATION
Pre-removal Operation
(1) Fuel Discharge Prevention
(2) Throttle Body Removal (Refer to GROUP 13.)
(3) Front Exhaust Pipe Removal (Refer to P.15-14.)
(4) Air Control Valve Bracket Removal (Refer to P.15-8.)
(5) Strut Tower Bar RemovalPost-installation Operation
(1) Strut Tower Bar Installation
(2) Air Control Valve Bracket Installation
(Refer to P.15-8.)
(3) Front Exhaust Pipe Installation (Refer to P.15-14.)
(4) Throttle Body Installation (Refer to GROUP 13.)
O-ring
Unit: Nm {kgfm}
15
Engine oil
3 {0.3} 10 – 13 {1.0 – 1.3}
10 – 12
{1.0 – 1.2}
12 – 15 {1.2 – 1.5}
35 {3.6}
9 {0.9}30 {3.1}35 {3.6}20 {2.0}22 {2.2}20 {2.0}
14 14
167
5
17
1521
3
4 6
7 7
19
20
18 8
9 12
1011
13
Removal steps
1. Center cover
2. Ignition coil connector connection
3. Oxygen sensor connector connec-
tion
4. Crank angle sensor connector con-
nection
5. Injector connector connection
6. PCV hose
7. Vacuum hose connection
8. Brake booster vacuum hose con-
nection
9. Vacuum tank, solenoid valve, and
vacuum hose assembly10. Intake manifold stay
11. Oil level gauge guide assembly
12. Vacuum hose and pipe mounting
bolt
13. Fuel return hose connection
A14. Fuel high pressure hose connection
A15. Delivery pipe, injector, and pres-
sure regulator assembly
16. Insulator
17. Insulator
18. Alternator brace stay
19. Intake manifold
20. Intake manifold gasket
Page 99 of 396
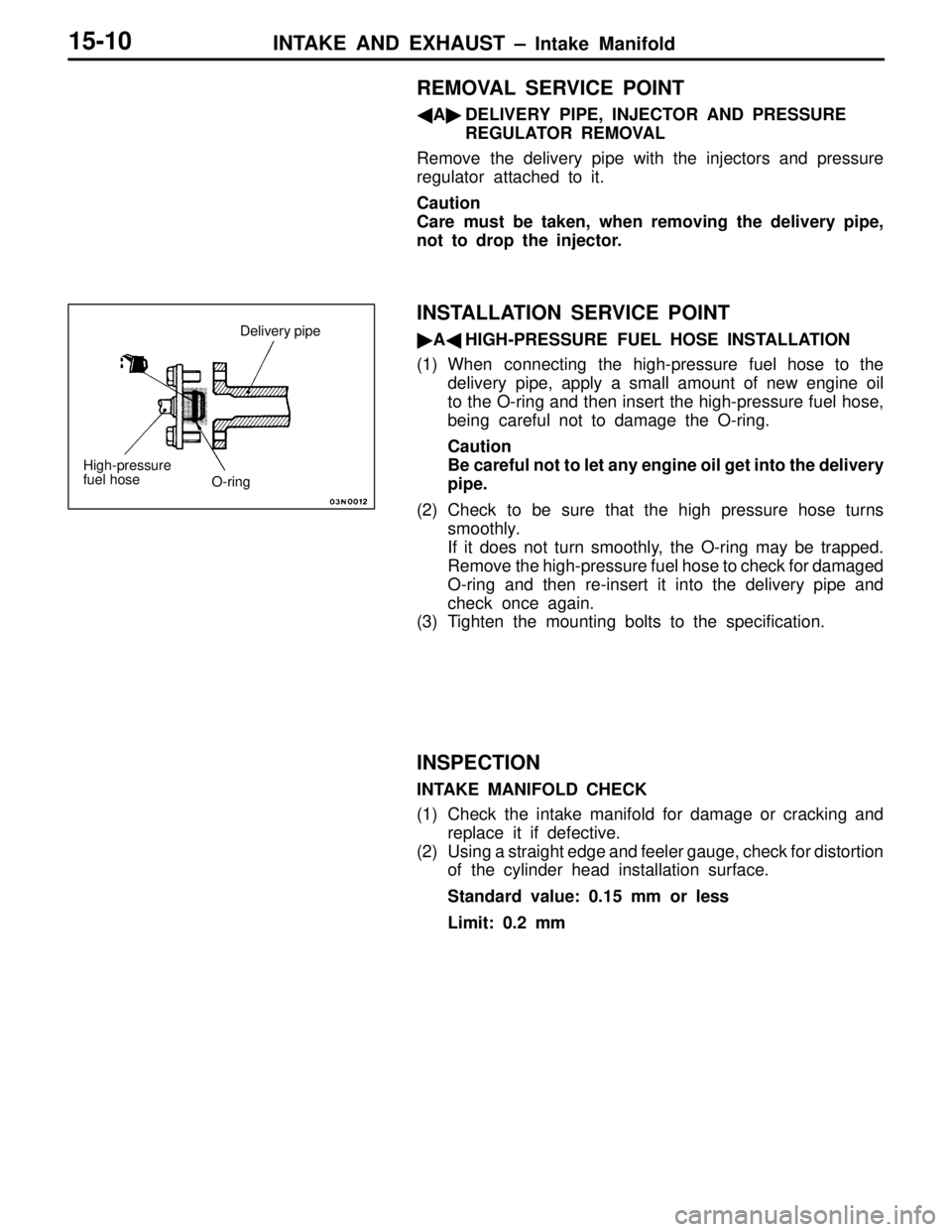
INTAKE AND EXHAUST – Intake Manifold15-10
REMOVAL SERVICE POINT
ADELIVERY PIPE, INJECTOR AND PRESSURE
REGULATOR REMOVAL
Remove the delivery pipe with the injectors and pressure
regulator attached to it.
Caution
Care must be taken, when removing the delivery pipe,
not to drop the injector.
INSTALLATION SERVICE POINT
AHIGH-PRESSURE FUEL HOSE INSTALLATION
(1) When connecting the high-pressure fuel hose to the
delivery pipe, apply a small amount of new engine oil
to the O-ring and then insert the high-pressure fuel hose,
being careful not to damage the O-ring.
Caution
Be careful not to let any engine oil get into the delivery
pipe.
(2) Check to be sure that the high pressure hose turns
smoothly.
If it does not turn smoothly, the O-ring may be trapped.
Remove the high-pressure fuel hose to check for damaged
O-ring and then re-insert it into the delivery pipe and
check once again.
(3) Tighten the mounting bolts to the specification.
INSPECTION
INTAKE MANIFOLD CHECK
(1) Check the intake manifold for damage or cracking and
replace it if defective.
(2) Using a straight edge and feeler gauge, check for distortion
of the cylinder head installation surface.
Standard value: 0.15 mm or less
Limit: 0.2 mm
High-pressure
fuel hoseDelivery pipe
O-ring
Page 100 of 396
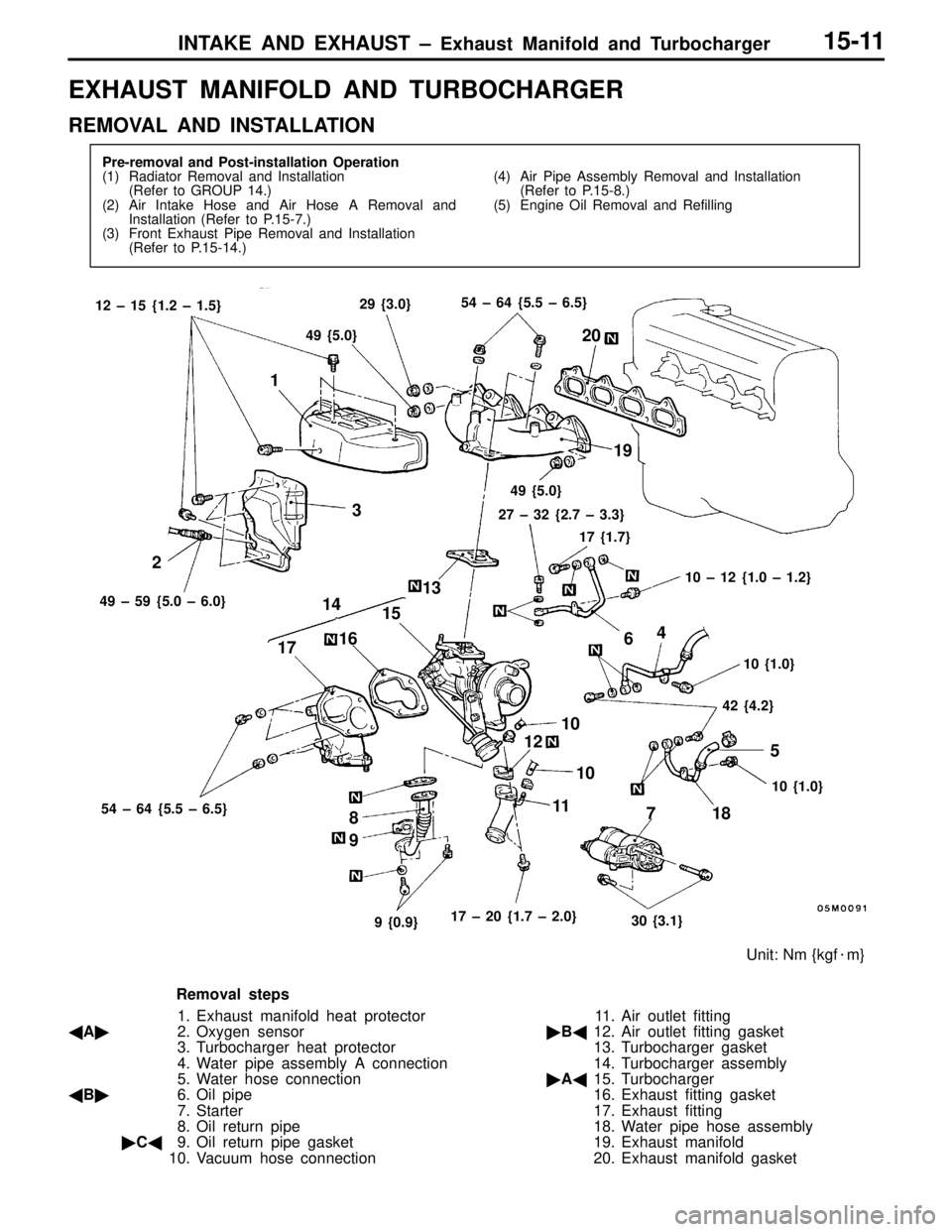
INTAKE AND EXHAUST – Exhaust Manifold and Turbocharger15-11
EXHAUST MANIFOLD AND TURBOCHARGER
REMOVAL AND INSTALLATION
Pre-removal and Post-installation Operation
(1) Radiator Removal and Installation
(Refer to GROUP 14.)
(2) Air Intake Hose and Air Hose A Removal and
Installation (Refer to P.15-7.)
(3) Front Exhaust Pipe Removal and Installation
(Refer to P.15-14.)(4) Air Pipe Assembly Removal and Installation
(Refer to P.15-8.)
(5) Engine Oil Removal and Refilling
1
Unit: Nm {kgfm}
49 {5.0}54 – 64 {5.5 – 6.5}
9 {0.9} 12 – 15 {1.2 – 1.5}
23
4
29 {3.0}
20
49 – 59 {5.0 – 6.0}
54 – 64 {5.5 – 6.5}
30 {3.1} 17 – 20 {1.7 – 2.0}10 {1.0} 42 {4.2}10 {1.0} 10 – 12 {1.0 – 1.2} 17 {1.7} 49 {5.0}
27 – 32 {2.7 – 3.3}
19
6
10
12
10
11
18 7
8
9 171615 1413
5
Removal steps
1. Exhaust manifold heat protector
A2. Oxygen sensor
3. Turbocharger heat protector
4. Water pipe assembly A connection
5. Water hose connection
B6. Oil pipe
7. Starter
8. Oil return pipe
C9. Oil return pipe gasket
10. Vacuum hose connection11. Air outlet fitting
B12. Air outlet fitting gasket
13. Turbocharger gasket
14. Turbocharger assembly
A15. Turbocharger
16. Exhaust fitting gasket
17. Exhaust fitting
18. Water pipe hose assembly
19. Exhaust manifold
20. Exhaust manifold gasket
Page 101 of 396
INTAKE AND EXHAUST – Exhaust Manifold and Turbocharger15-12
REMOVAL SERVICE POINTS
AOXYGEN SENSOR REMOVAL
BOIL PIPE REMOVAL
Caution
After the oil pipe has been removed, ensure that no foreign
matter will get into the oil passage holes in turbocharger.
INSTALLATION SERVICE POINTS
ATURBOCHARGER INSTALLATION
(1) Clean the connections between oil pipe, oil return pipe,
and water pipe.
Caution
Ensure that no foreign matter will get into the
turbocharger.
(2) Through the oil pipe mounting hole in the turbocharger,
add fresh engine oil.
BAIR OUTLET FITTING GASKET INSTALLATION
Install the gasket so that its tab is located as shown.
MB998770
Turbocharger
Ta b
Page 102 of 396
INTAKE AND EXHAUST – Exhaust Manifold and Turbocharger15-13
COIL RETURN PIPE GASKET INSTALLATION
Install the gasket so that its print part is on the oil pan side.
INSPECTION
1. TURBOCHARGER CHECK
(1) Visually check the turbine wheel and compressor wheel
for damage and cracking.
(2) Check that the turbine wheel and compressor wheel can
be turned manually with a light force.
(3) Check that there is no oil leak from the turbocharger.
(4) Check to see if the wastegate valve remains open. If
any of these faulty symptoms is evident, disassemble
the turbocharger and replace the defective part.
NOTE
For the disassembly procedure, refer to ENGINE
WORKSHOP MANUAL.
2. EXHAUST MANIFOLD CHECK
(1) Check the exhaust manifold for damage and cracking
and replace it as necessary.
(2) Using a straightedge and feeler gauge, check the cylinder
head mounting surface for distortion and replace as
necessary.
Standard value: Within 0.15 mm
Limit: 0.2 mm
Print
Gasket
Compressor wheel
Page 103 of 396
INTAKE AND EXHAUST – Exhaust Pipe and Muffler15-14
EXHAUST PIPE AND MUFFLER
REMOVAL AND INSTALLATION
Unit: Nm {kgfm}
15
44 {4.5}
49 {5.0}
34 {3.5}
5 {0.5}13 {1.3}
14
16
7 5 13
172 1
3
46 18
8
9 12
10 11
34 {3.5}
19 {1.9}49 {5.0}
Hanger mounting bolt tightening
torque
13 {1.3}
3, 9, 18
93 3 9
Main muffler removal steps
1. Bolt
2. Main muffler
3. Hanger
Center exhaust pipe removal steps
1. Bolt
4. Spring
5. Heat protector
6. Self-locking nut
7. Hanger bracket
8. Center exhaust pipe
9. Hanger
10. Protector11. High-temperature sensor
12. Bolt
13. Catalytic converter
14. Front floor heat protector panel
Front exhaust pipe removal steps
4. Spring
5. Heat protector
12. Bolt
15. Self-locking nut
16. Front exhaust pipe
17. Front exhaust pipe bracket
18. Hanger
Page 104 of 396
16-1
ENGINE
ELECTRICAL
CONTENTS
CHARGING SYSTEM 2. . . . . . . . . . . . . . . .
ALTERNATOR 2. . . . . . . . . . . . . . . . . . . . . . . . . . .
IGNITION SYSTEM 4. . . . . . . . . . . . . . . . . .
ON-VEHICLE SERVICE 4. . . . . . . . . . . . . . . . . . .
1. Ignition Coil with Built-in Power Transistor
Check 4. . . . . . . . . . . . . . . . . . . . . . . . . . . . . . . .
2. Spark Plug Check, Cleaning, and
Replacement 4. . . . . . . . . . . . . . . . . . . . . . . . . .
CAMSHAFT POSITION SENSOR AND
CRANK ANGLE SENSOR
5 . . . . . . . . . . . . .