Page 233 of 396
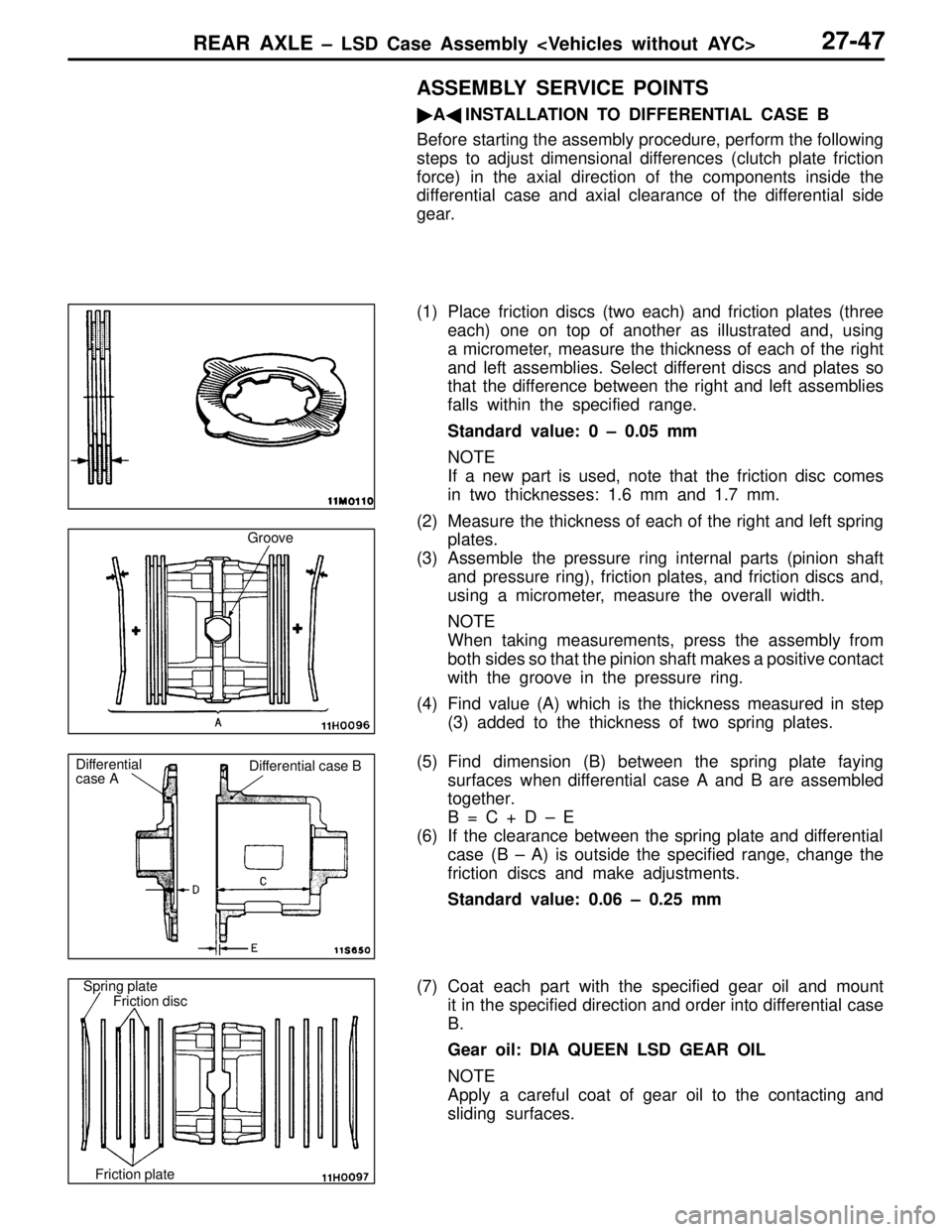
REAR AXLE – LSD Case Assembly 27-47
ASSEMBLY SERVICE POINTS
AINSTALLATION TO DIFFERENTIAL CASE B
Before starting the assembly procedure, perform the following
steps to adjust dimensional differences (clutch plate friction
force) in the axial direction of the components inside the
differential case and axial clearance of the differential side
gear.
(1) Place friction discs (two each) and friction plates (three
each) one on top of another as illustrated and, using
a micrometer, measure the thickness of each of the right
and left assemblies. Select different discs and plates so
that the difference between the right and left assemblies
falls within the specified range.
Standard value: 0 – 0.05 mm
NOTE
If a new part is used, note that the friction disc comes
in two thicknesses: 1.6 mm and 1.7 mm.
(2) Measure the thickness of each of the right and left spring
plates.
(3) Assemble the pressure ring internal parts (pinion shaft
and pressure ring), friction plates, and friction discs and,
using a micrometer, measure the overall width.
NOTE
When taking measurements, press the assembly from
both sides so that the pinion shaft makes a positive contact
with the groove in the pressure ring.
(4) Find value (A) which is the thickness measured in step
(3) added to the thickness of two spring plates.
(5) Find dimension (B) between the spring plate faying
surfaces when differential case A and B are assembled
together.
B = C + D – E
(6) If the clearance between the spring plate and differential
case (B – A) is outside the specified range, change the
friction discs and make adjustments.
Standard value: 0.06 – 0.25 mm
(7) Coat each part with the specified gear oil and mount
it in the specified direction and order into differential case
B.
Gear oil: DIA QUEEN LSD GEAR OIL
NOTE
Apply a careful coat of gear oil to the contacting and
sliding surfaces.
Groove
Differential
case ADifferential case B
Spring plate
Friction disc
Friction plate
Page 234 of 396
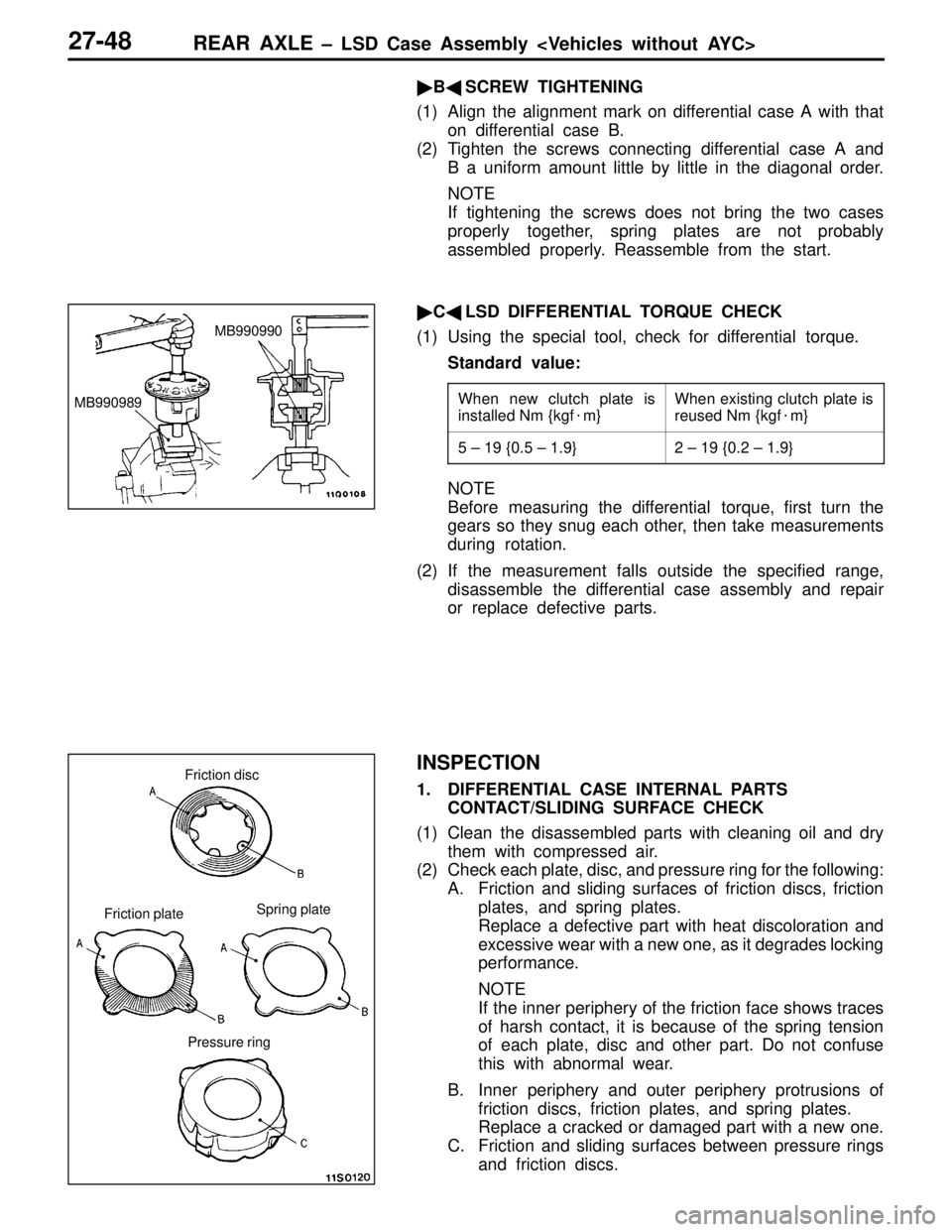
REAR AXLE – LSD Case Assembly 27-48
BSCREW TIGHTENING
(1) Align the alignment mark on differential case A with that
on differential case B.
(2) Tighten the screws connecting differential case A and
B a uniform amount little by little in the diagonal order.
NOTE
If tightening the screws does not bring the two cases
properly together, spring plates are not probably
assembled properly. Reassemble from the start.
CLSD DIFFERENTIAL TORQUE CHECK
(1) Using the special tool, check for differential torque.
Standard value:
When new clutch plate is
installed Nm {kgfm}When existing clutch plate is
reused Nm {kgfm}
5 – 19 {0.5 – 1.9}2 – 19 {0.2 – 1.9}
NOTE
Before measuring the differential torque, first turn the
gears so they snug each other, then take measurements
during rotation.
(2) If the measurement falls outside the specified range,
disassemble the differential case assembly and repair
or replace defective parts.
INSPECTION
1. DIFFERENTIAL CASE INTERNAL PARTS
CONTACT/SLIDING SURFACE CHECK
(1) Clean the disassembled parts with cleaning oil and dry
them with compressed air.
(2) Check each plate, disc, and pressure ring for the following:
A. Friction and sliding surfaces of friction discs, friction
plates, and spring plates.
Replace a defective part with heat discoloration and
excessive wear with a new one, as it degrades locking
performance.
NOTE
If the inner periphery of the friction face shows traces
of harsh contact, it is because of the spring tension
of each plate, disc and other part. Do not confuse
this with abnormal wear.
B. Inner periphery and outer periphery protrusions of
friction discs, friction plates, and spring plates.
Replace a cracked or damaged part with a new one.
C. Friction and sliding surfaces between pressure rings
and friction discs.
MB990989MB990990
Friction disc
Friction plateSpring plate
Pressure ring
Page 235 of 396
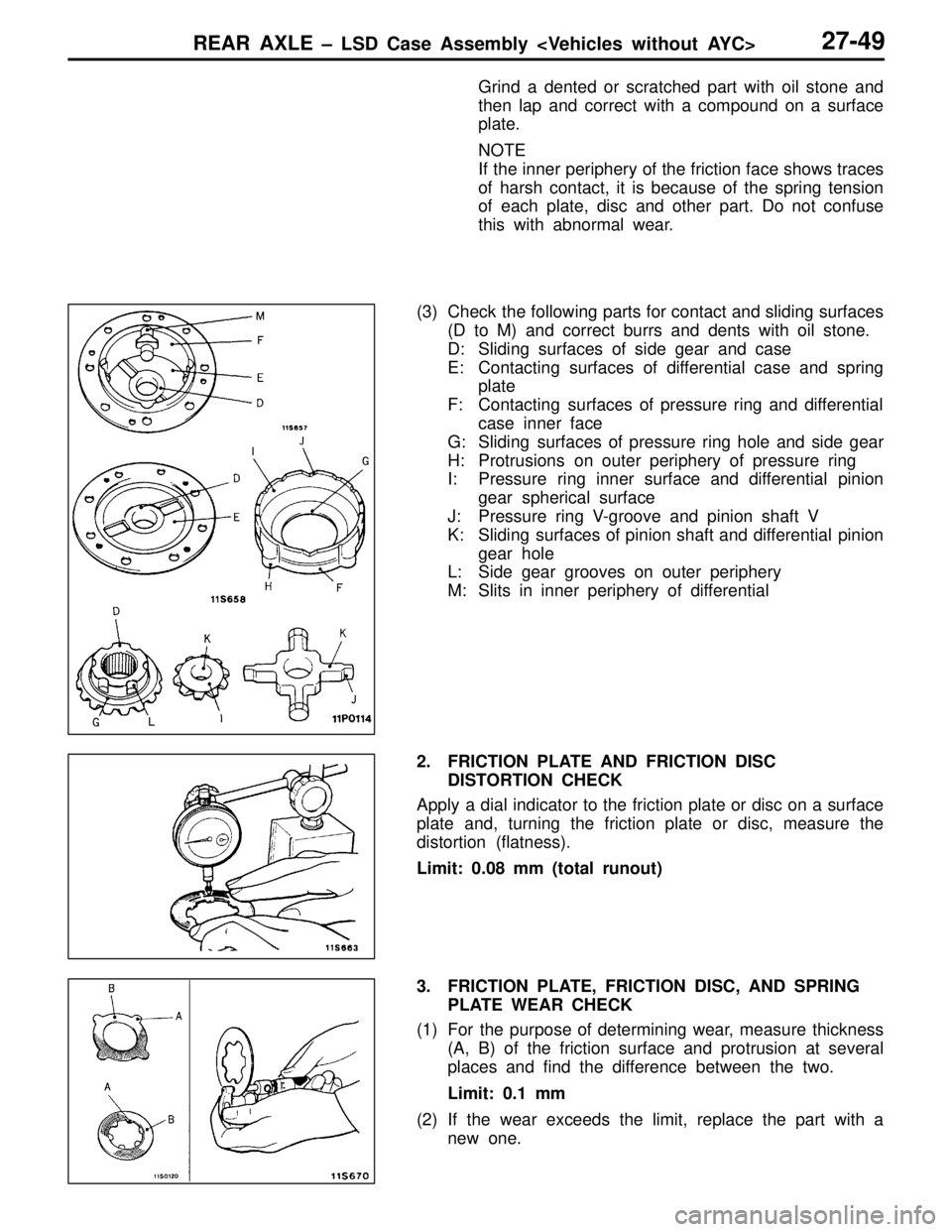
REAR AXLE – LSD Case Assembly 27-49
Grind a dented or scratched part with oil stone and
then lap and correct with a compound on a surface
plate.
NOTE
If the inner periphery of the friction face shows traces
of harsh contact, it is because of the spring tension
of each plate, disc and other part. Do not confuse
this with abnormal wear.
(3) Check the following parts for contact and sliding surfaces
(D to M) and correct burrs and dents with oil stone.
D: Sliding surfaces of side gear and case
E: Contacting surfaces of differential case and spring
plate
F: Contacting surfaces of pressure ring and differential
case inner face
G: Sliding surfaces of pressure ring hole and side gear
H: Protrusions on outer periphery of pressure ring
I: Pressure ring inner surface and differential pinion
gear spherical surface
J: Pressure ring V-groove and pinion shaft V
K: Sliding surfaces of pinion shaft and differential pinion
gear hole
L: Side gear grooves on outer periphery
M: Slits in inner periphery of differential
2. FRICTION PLATE AND FRICTION DISC
DISTORTION CHECK
Apply a dial indicator to the friction plate or disc on a surface
plate and, turning the friction plate or disc, measure the
distortion (flatness).
Limit: 0.08 mm (total runout)
3. FRICTION PLATE, FRICTION DISC, AND SPRING
PLATE WEAR CHECK
(1) For the purpose of determining wear, measure thickness
(A, B) of the friction surface and protrusion at several
places and find the difference between the two.
Limit: 0.1 mm
(2) If the wear exceeds the limit, replace the part with a
new one.
Page 236 of 396
REAR AXLE – Hydraulic Unit 27-50
HYDRAULIC UNIT
REMOVAL AND INSTALLATION
Pre-removal Operation
(1) Trunk Side Trim Removal
(2) Hydraulic Piping Fluid DrainingPost-installation Operation
(1) Hydraulic Piping Fluid Filling and Bleeding
(Refer to P.27-29.)
(2) Trunk Side Trim Installation
1 23 45
6
7 8 9
10 11 12
1314
Unit: Nm {kgfm}
12 {1.2}
4
12 {1.2}
18 {1.8}
12 {1.2}
12 {1.2} 18 {1.8}
34 {3.5}
34 {3.5}
Removal steps
1. Dust guard
2. Suction hose and return hose con-
nection
3. Hydraulic unit hose assembly con-
nection
4. Hydraulic unit and bracket assem-
bly mounting bolt
C5. Hydraulic unit and bracket assem-
bly
6. Hydraulic unit
7. Hydraulic unit bracket
8. AYC harness9. Hydraulic unit bracket
10. Hydraulic unit hose assembly
B11. Return hose
B12. Suction hose
A13. Grommet
14. Oil reservoir
Caution
(1) When connecting the return hose and suction
hose, do not apply lubricant.
(2) No foreign matter should be allowed in the
hydraulic piping and joints.
Page 237 of 396
REAR AXLE – Hydraulic Unit 27-51
INSTALLATION SERVICE POINTS
AGROMMET INSTALLATION
On the vehicle mounted with a sun roof, mount the drain
pipe to the grommet as illustrated.
BSUCTION HOSE / RETURN HOSE INSTALLATION
Fit the suction hose and return hose to the nipple of hydraulic
unit as illustrated.
CHYDRAULIC UNIT AND BRACKET ASSEMBLY
INSTALLATION
Hook the hydraulic unit bracket hook to the rear floor side
member and install the hydraulic unit and bracket assembly
mounting bolt.Grommet
Drain pipe
25 ± 5 mm
Nipple
Suction hose and
return hose15 mm
Hook
Rear floor side member
Page 238 of 396
REAR AXLE – Sensor Relay 27-52
SENSOR RELAY
REMOVAL AND INSTALLATION
12
3
4
Steer sensor removal steps
Steering wheel and column cover
(Refer to GROUP 37 – Steering Wheel
and Shaft.)
A1. Steer sensorAcceleration sensor and AYC relay
removal
2. Longitudinal acceleration sensor
3. Lateral acceleration sensor
4. AYC relay
NOTE
For the wheel speed sensor, refer to GROUP 35B.
REMOVAL SERVICE POINT
ASTEER SENSOR REMOVAL
Remove the steer sensor from the column switch.
Caution
(1) A photocoupler is used as the steer sensor. Use care
not to allow dust or grease to be on the sensor.
(2) Do not bend or dirty with grease the slit plate on
the column switch side.Slit plate
Steer sensor
Page 239 of 396
REAR AXLE – Sensor Relay / AYC-ECU27-53
INSPECTION
1. LONGITUDINAL AND LATERAL ACCELERATION
SENSOR CHECK
Refer to GROUP 35B – Acceleration Sensor.
2. AYC RELAY CONTINUITY CHECK
Battery voltageTerminal No.
1345
When not energized
When energized
AYC-ECU
REMOVAL AND INSTALLATION
Pre-removal and Post-installation Operation
Front Floor Console Removal and Installation
Unit: Nm {kgfm}
5 {0.5}
AYC-ECU
5 {0.5}
Page 240 of 396
ROLL STOPPER AND CENTERMEMBER 2. . . . . . . . . . . . . . . . . . . . . .
32-1
POWER PLANT
MOUNT
CONTENTS