Page 25 of 396
ENGINE – Cylinder Head Gasket11-19
REMOVAL SERVICE POINT
ACYLINDER HEAD BOLT REMOVAL
Loosen the bolts in 2 or 3 steps in order of the numbers
shown in the illustration, and remove the cylinder head
assembly.
INSTALLATION SERVICE POINTS
ACYLINDER HEAD GASKET INSTALLATION
(1) Wipe off all oil and grease from the gasket mounting
surface.
(2) Install so that the shapes of the cylinder head holes match
the shapes of the respective cylinder head gasket holes.
BCYLINDER HEAD BOLT INSTALLATION
(1) When installing the cylinder head bolts, the length below
the head of the bolts should be within the limit.
If it is outside the limit, replace the bolts.
Limit (A): 99.4 mm
(2) Apply a small amount of engine oil to the thread section
and the washer of the cylinder head bolt.
Intake sideMB991654
Exhaust sideFront of engine
Cylinder head bolt
Washer
(Engine
oil)
Cylinder
head A
Page 26 of 396
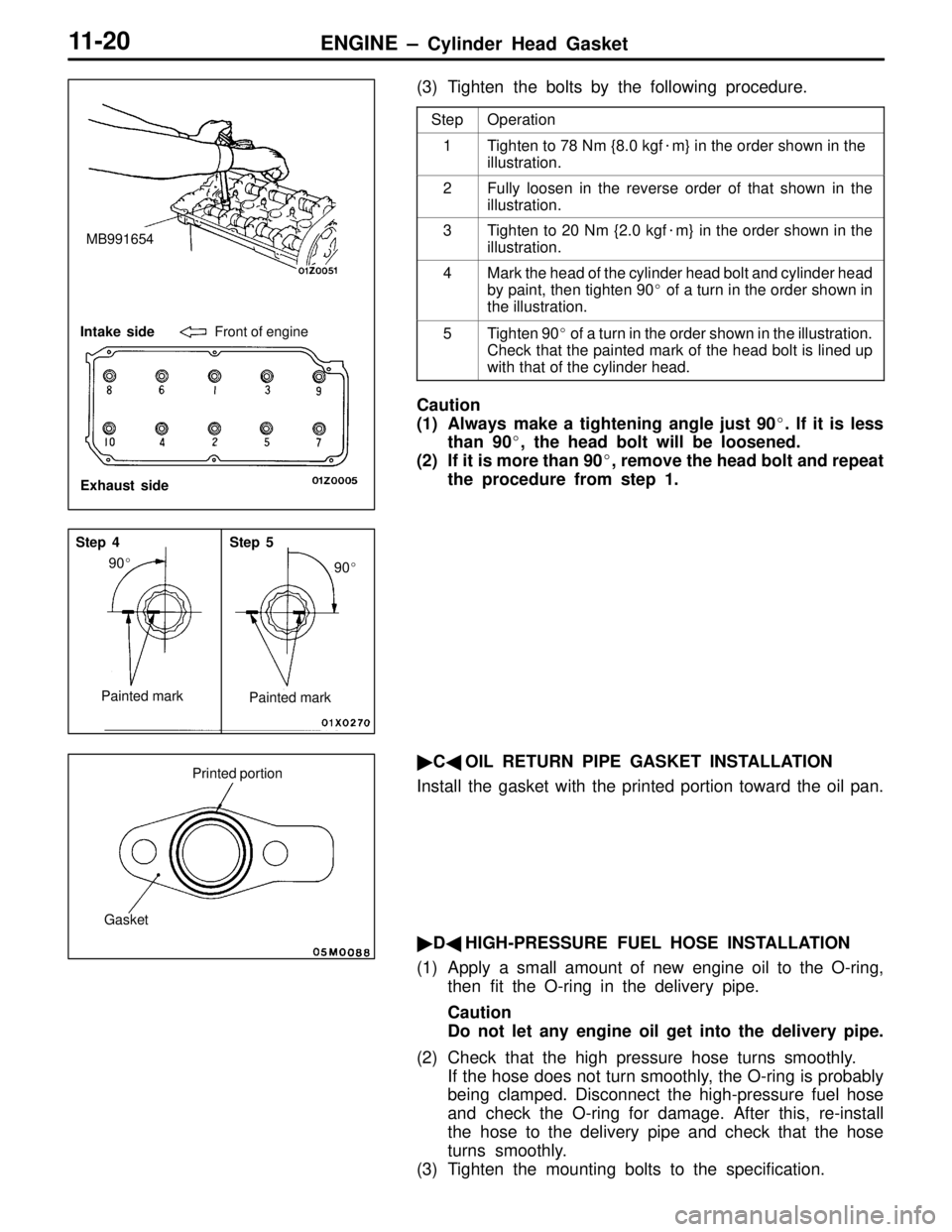
ENGINE – Cylinder Head Gasket11-20
(3) Tighten the bolts by the following procedure.
StepOperation
1Tighten to 78 Nm {8.0 kgfm} in the order shown in the
illustration.
2Fully loosen in the reverse order of that shown in the
illustration.
3Tighten to 20 Nm {2.0 kgfm} in the order shown in the
illustration.
4Mark the head of the cylinder head bolt and cylinder head
by paint, then tighten 90 of a turn in the order shown in
the illustration.
5Tighten 90 of a turn in the order shown in the illustration.
Check that the painted mark of the head bolt is lined up
with that of the cylinder head.
Caution
(1) Always make a tightening angle just 90. If it is less
than 90, the head bolt will be loosened.
(2) If it is more than 90, remove the head bolt and repeat
the procedure from step 1.
COIL RETURN PIPE GASKET INSTALLATION
Install the gasket with the printed portion toward the oil pan.
DHIGH-PRESSURE FUEL HOSE INSTALLATION
(1) Apply a small amount of new engine oil to the O-ring,
then fit the O-ring in the delivery pipe.
Caution
Do not let any engine oil get into the delivery pipe.
(2) Check that the high pressure hose turns smoothly.
If the hose does not turn smoothly, the O-ring is probably
being clamped. Disconnect the high-pressure fuel hose
and check the O-ring for damage. After this, re-install
the hose to the delivery pipe and check that the hose
turns smoothly.
(3) Tighten the mounting bolts to the specification.
Intake sideMB991654
Exhaust sideFront of engine
Step 4
90
Painted markStep 5
90
Painted mark
GasketPrinted portion
Page 27 of 396
ENGINE – Timing Belt11-21
TIMING BELT
REMOVAL AND INSTALLATION
1
2
3
4 56
7
8
910
11 1213
14 15
16 171821
22
23
242526
27
28
20
19
11 {1.1}
11 {1.1} 11 {1.1}
88 {9.0}
49 {5.0}
9 {0.9}
48 {4.9}54 {5.5}49 {5.0} 118 {12.0}
9 {0.9}3.5 {0.35}
49 {5.0}
45 {4.6}
19 {1.9}30 {3.1} 24 {2.4}24 {2.4}
Unit: Nm {kgfm}
Removal steps
1. Front upper cover
2. Front center cover
3. Front lower cover
4. Bracket
AL5. Timing belt
K6. Tensioner pulley
7. Tensioner arm
J8. Auto tensioner
9. Idle pulley
10. Crankshaft position sensor
BI11. Oil pump sprocket
CH12. Crankshaft bolt
D13. Crankshaft sprocket
14. Sensing blade15. Tensioner B
EG16. Timing belt B
FF17. Counterbalance shaft sprocket
E18. Spacer
G19. Crankshaft sprocket B
20. Crankshaft key
D21. Rocker cover
C22. Semi-circular packing
B23. Engine support bracket
HA24. Camshaft sprocket bolt
25. Camshaft sprocket
26. Timing belt rear right cover
27. Timing belt rear left upper cover
28. Timing belt rear left lower cover
Page 28 of 396
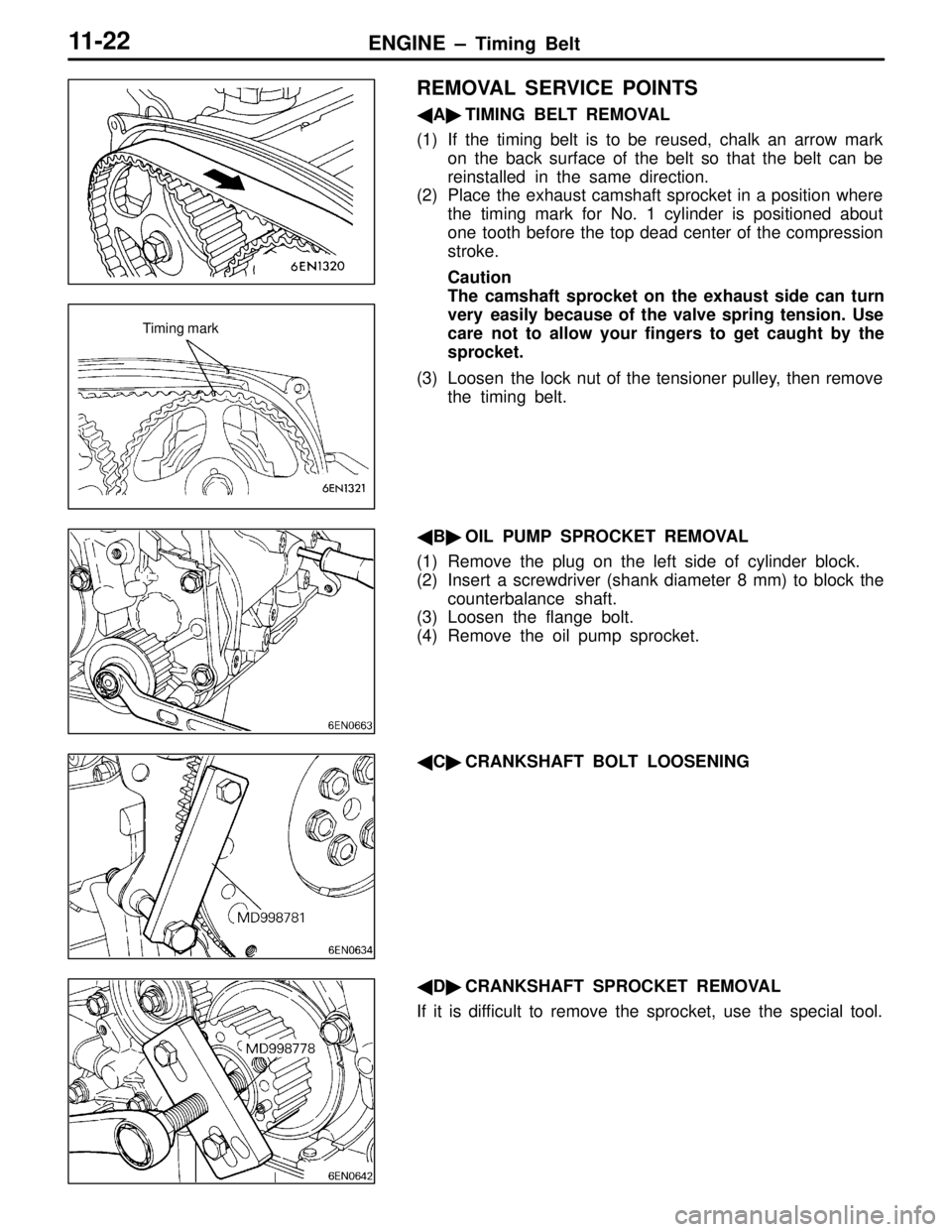
ENGINE – Timing Belt11-22
REMOVAL SERVICE POINTS
ATIMING BELT REMOVAL
(1) If the timing belt is to be reused, chalk an arrow mark
on the back surface of the belt so that the belt can be
reinstalled in the same direction.
(2) Place the exhaust camshaft sprocket in a position where
the timing mark for No. 1 cylinder is positioned about
one tooth before the top dead center of the compression
stroke.
Caution
The camshaft sprocket on the exhaust side can turn
very easily because of the valve spring tension. Use
care not to allow your fingers to get caught by the
sprocket.
(3) Loosen the lock nut of the tensioner pulley, then remove
the timing belt.
BOIL PUMP SPROCKET REMOVAL
(1) Remove the plug on the left side of cylinder block.
(2) Insert a screwdriver (shank diameter 8 mm) to block the
counterbalance shaft.
(3) Loosen the flange bolt.
(4) Remove the oil pump sprocket.
CCRANKSHAFT BOLT LOOSENING
DCRANKSHAFT SPROCKET REMOVAL
If it is difficult to remove the sprocket, use the special tool.
Timing mark
Page 29 of 396
ENGINE – Timing Belt11-23
ETIMING BELT “B” REMOVAL
Make an arrow mark on the back of the timing belt indicating
the direction of rotation so it may be reassembled in the
same direction if it is to be reused.
FCOUNTERBALANCE SHAFT SPROCKET
REMOVAL
GCRANKSHAFT SPROCKET “B” REMOVAL
If it is difficult to remove the sprocket, use the special tool.
HCAMSHAFT SPROCKET BOLT LOOSENING
Use a wrench to hold the hexagonal part of the camshaft,
and then remove the camshaft sprocket mounting bolt.
INSPECTION
TIMING BELT
Replace belt if any of the following conditions exist.
(1) Hardening of back rubber.
Back side is glossy without resilience and leaves no indent
when pressed with fingernail.
6EN1322
Page 30 of 396
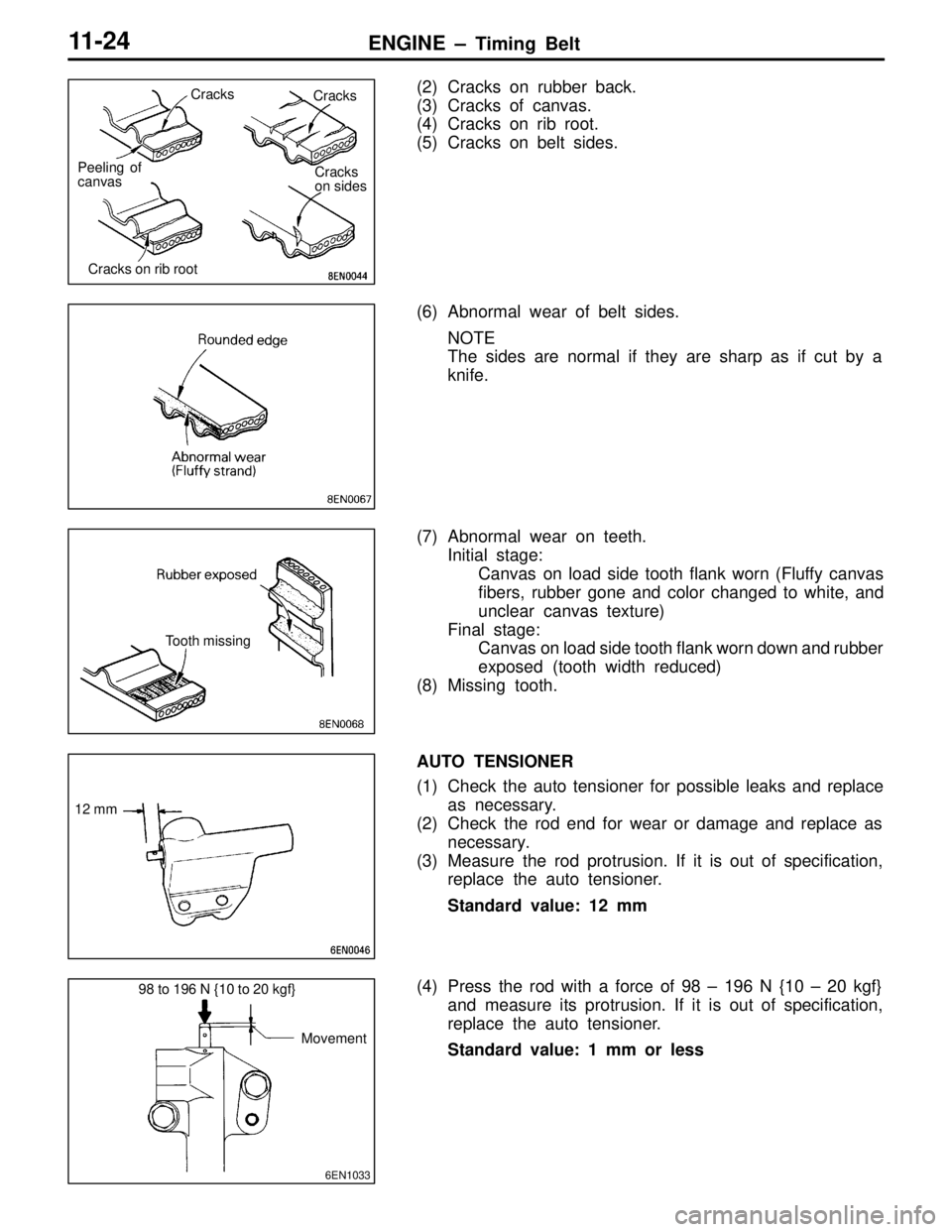
ENGINE – Timing Belt11-24
(2) Cracks on rubber back.
(3) Cracks of canvas.
(4) Cracks on rib root.
(5) Cracks on belt sides.
(6) Abnormal wear of belt sides.
NOTE
The sides are normal if they are sharp as if cut by a
knife.
(7) Abnormal wear on teeth.
Initial stage:
Canvas on load side tooth flank worn (Fluffy canvas
fibers, rubber gone and color changed to white, and
unclear canvas texture)
Final stage:
Canvas on load side tooth flank worn down and rubber
exposed (tooth width reduced)
(8) Missing tooth.
AUTO TENSIONER
(1) Check the auto tensioner for possible leaks and replace
as necessary.
(2) Check the rod end for wear or damage and replace as
necessary.
(3) Measure the rod protrusion. If it is out of specification,
replace the auto tensioner.
Standard value: 12 mm
(4) Press the rod with a force of 98 – 196 N {10 – 20 kgf}
and measure its protrusion. If it is out of specification,
replace the auto tensioner.
Standard value: 1 mm or lessCracks
Cracks
on sides Cracks
Cracks on rib root Peeling of
canvas
Tooth missing
12 mm
6EN1033
98 to 196 N {10 to 20 kgf}
Movement
Page 31 of 396
ENGINE – Timing Belt11-25
INSTALLATION SERVICE POINTS
ACAMSHAFT SPROCKET BOLT TIGHTENING
Using a wrench, hold the camshaft at its hexagon and tighten
the bolt to the specification.
Caution
Locking the camshaft sprocket with a tool damages the
sprocket.
BENGINE SUPPORT BRACKET LEFT
INSTALLATION
Coat the bolts illustrated with sealant before tightening.
Specified sealant: THREEBOND 1207F or equivalent
CSEALANT APPLICATION ON SEMI-CIRCULAR
PACKING
Apply sealant to the areas indicated in the illustration.
Specified sealant: THREEBOND 1212D or equivalent
Apply sealant
Apply
sealant 10 mm
10 mm
Cylinder head Semi-circular
packing
Page 32 of 396
ENGINE – Timing Belt11-26
DSEALANT APPLICATION ON ROCKER COVER
Apply sealant to the areas indicated in the illustration.
Specified sealant: THREEBOND 1212D or equivalent
Apply sealant
10 mm
10 mm 10 mm
10 mm
Apply sealant
Apply sealant
ESPACER INSTALLATION
(1) Apply very thin coat of oil to the outer periphery of the
spacer (oil seal contacting surface).
(2) Install the spacer with the chamfered end toward the
oil seal. Mounting in the reverse direction can damage
the oil seal lip.
FCOUNTERBALANCE SHAFT SPROCKET
INSTALLATION
GTIMING BELT “B” INSTALLATION
(1) Align timing marks on the crankshaft sprocket “B” and
counterbalance shaft sprocket with the marks on the front
case respectively.
(2) Install the timing belt “B” on the crankshaft sprocket “B”
and counterbalance shaft sprocket. There should be no
slack on the tension side.
SpacerOil seal
Chamfer
Timing
marks Timing
marks