Page 41 of 396
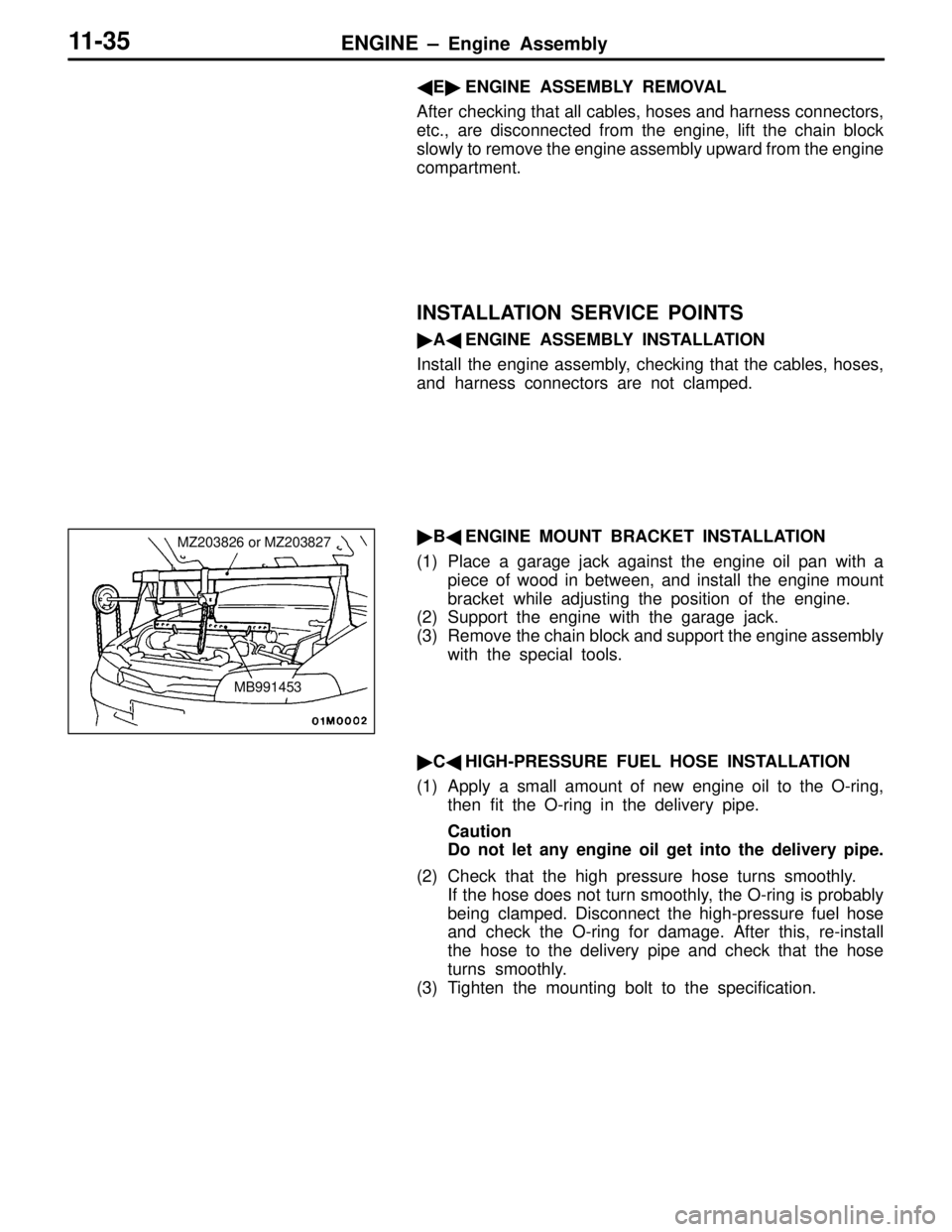
ENGINE – Engine Assembly11-3 5
E ENGINE ASSEMBLY REMOVAL
After checking that all cables, hoses and harness connectors,
etc., are disconnected from the engine, lift the chain block
slowly to remove the engine assembly upward from the engine
compartment.
INSTALLATION SERVICE POINTS
A ENGINE ASSEMBLY INSTALLATION
Install the engine assembly, checking that the cables, hoses,
and harness connectors are not clamped.
B ENGINE MOUNT BRACKET INSTALLATION
(1) Place a garage jack against the engine oil pan with a piece of wood in between, and install the engine mount
bracket while adjusting the position of the engine.
(2) Support the engine with the garage jack.
(3) Remove the chain block and support the engine assembly
with the special tools.
C HIGH-PRESSURE FUEL HOSE INSTALLATION
(1) Apply a small amount of new engine oil to the O-ring, then fit the O-ring in the delivery pipe.
Caution
Do not let any engine oil get into the delivery pipe.
(2) Check that the high pressure hose turns smoothly. If the hose does not turn smoothly, the O-ring is probably
being clamped. Disconnect the high-pressure fuel hose
and check the O-ring for damage. After this, re-install
the hose to the delivery pipe and check that the hose
turns smoothly.
(3) Tighten the mounting bolt to the specification.
MZ203826 or MZ203827
MB991453
Page 42 of 396
LUBRICANTS 2. . . . . . . . . . . . . . . . . . . . . . . . . . . . . . . . . . . . . . . . . . . . . . .
ENGINE OIL COOLER 2. . . . . . . . . . . . . . . . . . . . . . . . . . . . . . . . . . . . . . .
12-1
ENGINE
LUBRICATION
CONTENTS
Page 43 of 396
ENGINE LUBRICATION – Lubricants / Engine Oil Cooler12-2
TSB Revision
LUBRICANTS
ItemsCapacity dm3 {}
Engine oilQuantity in oil filter0.3 {0.3}
Quantity in oil cooler0.16 {0.16}
Total quantity5.1 {5.1}
BrandDIA QUEEN MOTOR OIL (Grade SG or higher); or engine oil in
a can marked with ILSAC certification.
ENGINE OIL COOLER
REMOVAL AND INSTALLATION
Pre-removal and Post-installation Operation
(1) Engine Oil Removal and Refilling
(2) Front Bumper Removal and Installation
(Refer to GROUP 51.)
3
Unit: Nm {kgfm}
12 {1.2}
39 – 44
{4.0 – 4.5} 29 – 34
{3.0 – 3.5}
2 1
39 – 44
{4.0 – 4.5} 12 {1.2}
12 {1.2}
Removal steps
1. Engine oil cooler
A2. Feed hose assembly
A3. Return hose assembly
INSTALLATION SERVICE POINT
AFEED HOSE ASSEMBLY / RETURN HOSE
ASSEMBLY INSTALLATION
Fit the hose joint positioning tab into the hole in oil cooler
to secure the hose assembly in position.
Page 44 of 396
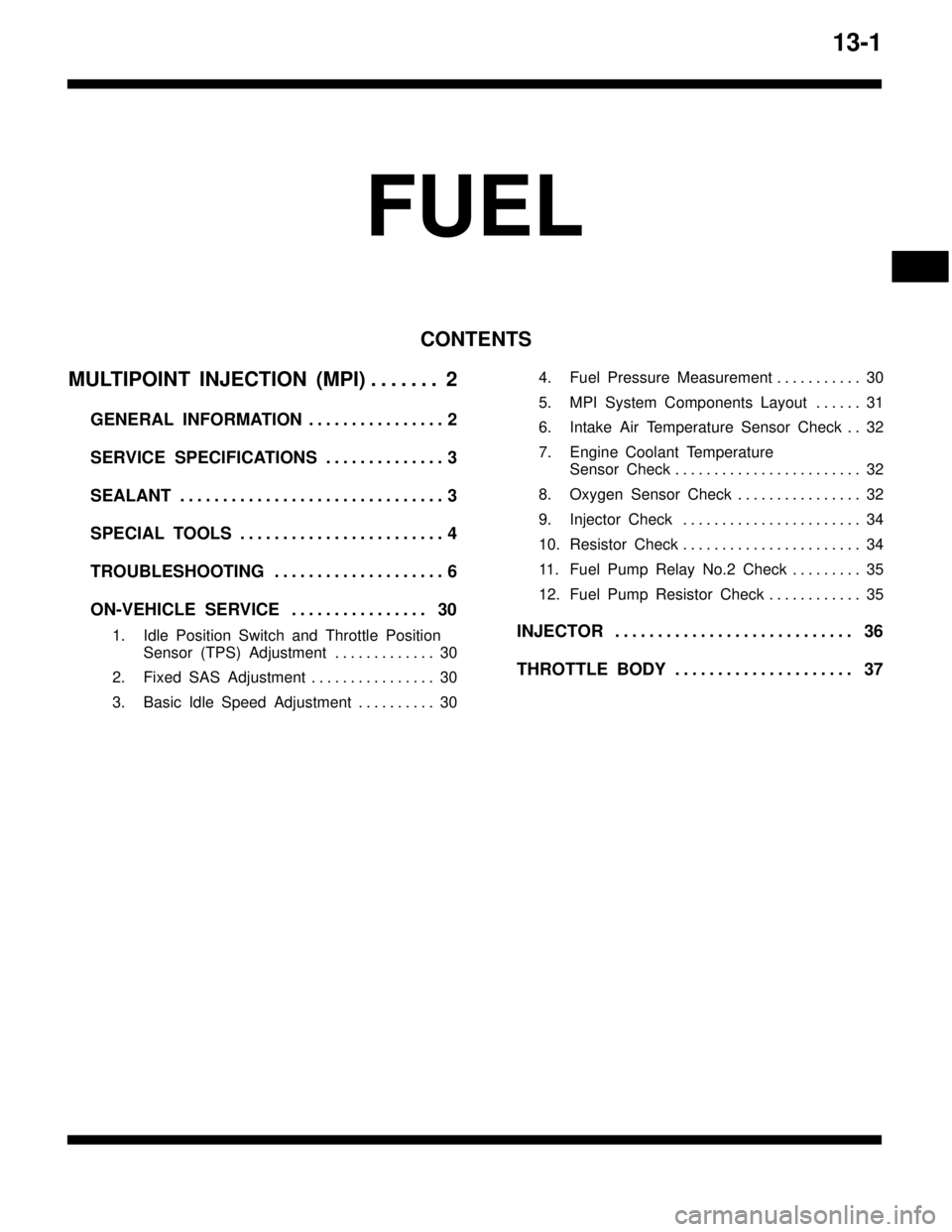
13-1
FUEL
CONTENTS
MULTIPOINT INJECTION (MPI) 2. . . . . . .
GENERAL INFORMATION 2. . . . . . . . . . . . . . . .
SERVICE SPECIFICATIONS 3. . . . . . . . . . . . . .
SEALANT 3. . . . . . . . . . . . . . . . . . . . . . . . . . . . . . .
SPECIAL TOOLS 4. . . . . . . . . . . . . . . . . . . . . . . .
TROUBLESHOOTING 6. . . . . . . . . . . . . . . . . . . .
ON-VEHICLE SERVICE 30. . . . . . . . . . . . . . . .
1. Idle Position Switch and Throttle Position
Sensor (TPS) Adjustment 30. . . . . . . . . . . . .
2. Fixed SAS Adjustment 30. . . . . . . . . . . . . . . .
3. Basic Idle Speed Adjustment 30. . . . . . . . . . 4. Fuel Pressure Measurement 30. . . . . . . . . . .
5. MPI System Components Layout 31. . . . . .
6. Intake Air Temperature Sensor Check 32. .
7. Engine Coolant Temperature
Sensor Check 32. . . . . . . . . . . . . . . . . . . . . . . .
8. Oxygen Sensor Check 32. . . . . . . . . . . . . . . .
9. Injector Check 34. . . . . . . . . . . . . . . . . . . . . . .
10. Resistor Check 34. . . . . . . . . . . . . . . . . . . . . . .
11. Fuel Pump Relay No.2 Check 35. . . . . . . . .
12. Fuel Pump Resistor Check 35. . . . . . . . . . . . INJECTOR 36. . . . . . . . . . . . . . . . . . . . . . . . . . . .
THROTTLE BODY 37. . . . . . . . . . . . . . . . . . . . .
Page 45 of 396
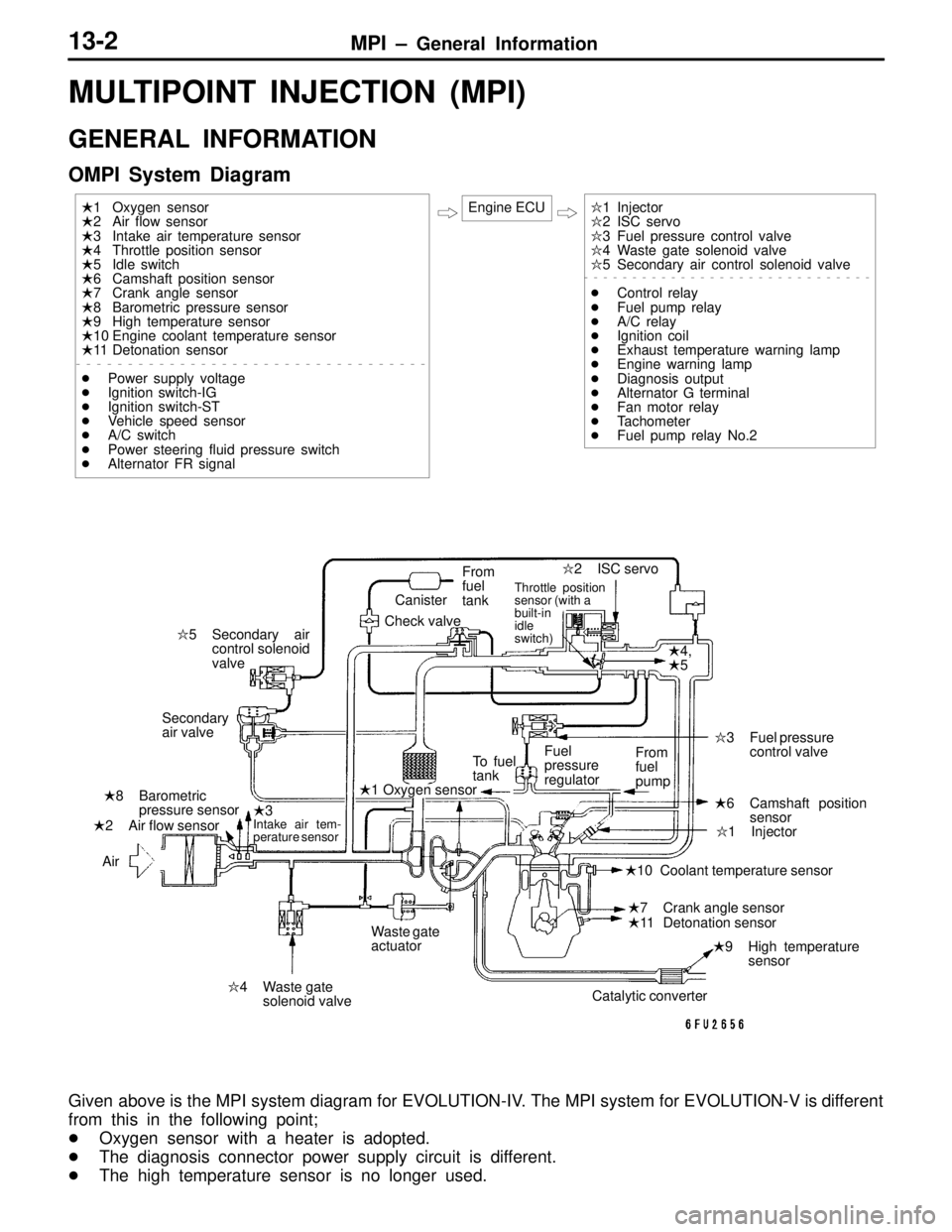
MPI – General Information13-2
MULTIPOINT INJECTION (MPI)
GENERAL INFORMATION
OMPI System Diagram
1 Injector
2 ISC servo
3 Fuel pressure control valve
4 Waste gate solenoid valve
5 Secondary air control solenoid valve
Control relay
Fuel pump relay
A/C relay
Ignition coil
Exhaust temperature warning lamp
Engine warning lamp
Diagnosis output
Alternator G terminal
Fan motor relay
Tachometer
Fuel pump relay No.2 1 Oxygen sensor
2 Air flow sensor
3 Intake air temperature sensor
4 Throttle position sensor
5 Idle switch
6 Camshaft position sensor
7 Crank angle sensor
8 Barometric pressure sensor
9 High temperature sensor
10 Engine coolant temperature sensor
11 Detonation sensor
Power supply voltage
Ignition switch-IG
Ignition switch-ST
Vehicle speed sensor
A/C switch
Power steering fluid pressure switch
Alternator FR signalEngine ECU
1 Oxygen sensor
2 Air flow sensor3
Intake air tem-
perature sensor
4,
5
6 Camshaft position
sensor
7 Crank angle sensor 8 Barometric
pressure sensor
9 High temperature
sensor 10 Coolant temperature sensor
11 Detonation sensor1 Injector 2 ISC servo
3 Fuel pressure
control valve
4 Waste gate
solenoid valve 5 Secondary air
control solenoid
valveCanister
Check valveFrom
fuel
tank
Throttle position
sensor (with a
built-in
idle
switch)
Secondary
air valve
AirTo fuel
tankFuel
pressure
regulatorFrom
fuel
pump
Waste gate
actuator
Catalytic converter
Given above is the MPI system diagram for EVOLUTION-IV. The MPI system for EVOLUTION-V is different
from this in the following point;
Oxygen sensor with a heater is adopted.
The diagnosis connector power supply circuit is different.
The high temperature sensor is no longer used.
Page 46 of 396
MPI – Service Specifications / Sealant13-3
SERVICE SPECIFICATIONS
ItemsSpecifications
Basic ignition timing BTDC5 ± 3
Basic idle speed rpm850 ± 50
Throttle position sensor adjusting voltage mV400 – 1,000
Throttle position sensor resistance kΩ3.5 – 6.5
ISC servo coil resistance (at 20C) Ω28 – 33
Intake air temperature sensor resistance kΩAt 20C2.3 – 3.0
At 80C0.30 – 0.42
Coolant temperature sensor resistance kΩAt 20C2.1 – 2.7
At 80C0.26 – 0.36
Fuel pressure
kPa {kgf/cm2}
When vacuum hose is connected230 {2.35}
kPa {kgf/cm2}
When vacuum hose is disconnected289 – 309 {2.95 – 3.15}
Injector coil resistance Ω2 – 3
Amount of injector fuel leak drop/min1 or less
Oxygen sensor output voltage0.6 – 1.0
Fuel pressure control valve coil resistance (at 20C) Ω28 – 36
SEALANT
ItemSpecified sealant
Coolant temperature sensorDrying sealant: HELMESEAL H-1M [0110513]
NOTE:
Given in [ ] are MITSUBISHI GENUINE PART numbers.
Page 47 of 396
MPI – Special Tools13-4
SPECIAL TOOLS
ToolNumberNameUse
MB991348Test harness setMeasurement of voltage during trouble-
shooting
Inspection using an oscilloscope
MB991519Alternator harness
connectorMeasurement of voltage during
troubleshooting
MB991536TPS check
harnessAdjustment of idle switch and throttle position
sensor (TPS)
MD998464Test harness
(4-pin, square)Inspection of oxygen sensor
MD998463Test harness
(6-pin, square)Inspection of idle speed control servo
Inspection using an oscilloscope
MD998478Test harness
(3-pin, triangle)Measurement of voltage during trouble-
shooting
Inspection using an oscilloscope
MD998706Injector test setChecking the spray condition of injectors
MD998741Injector test
adaptor
MB991607Injector test
harness
Page 48 of 396
MPI – Special Tools13-5
Tool UseName Number
MD998746ClipChecking the spray condition of injectors
MD998709Adaptor hoseMeasurement of fuel pressure
MD998742Hose adaptor
MB991637Fuel pressure
gauge set
Red harness
White harness
MB991223Inspection test
herness set
Pin contact
pressure
inspection
harness
Market tester
contact probe
(for general
connectors)Measurement of terminal voltage
MB991529Diagnostic trouble
code check har-
nessReading of diagnosis codes
MB991709Test harnessMeasurement of voltage during trouble-
shooting
Inspection using an oscilloscope