Page 209 of 715
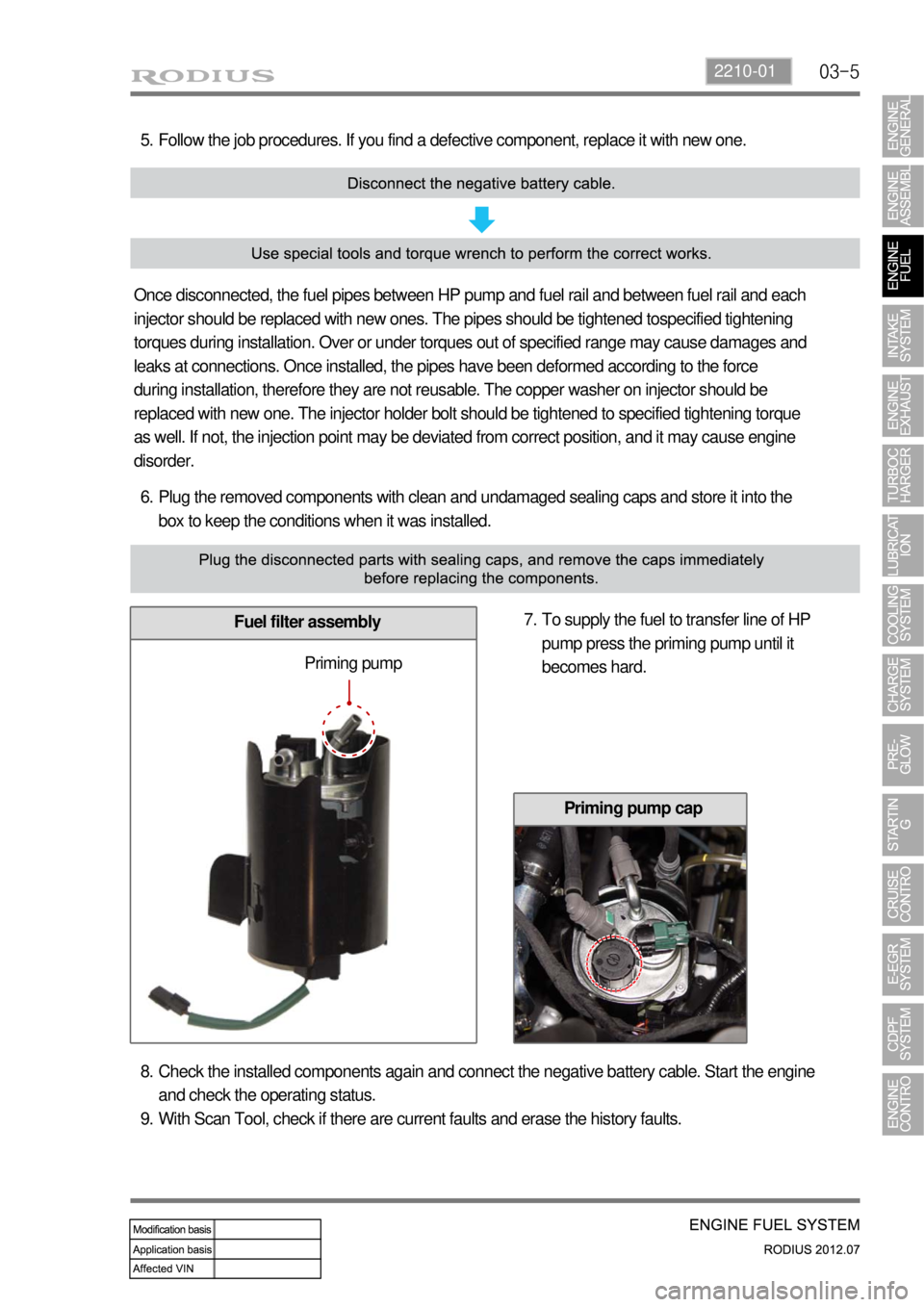
03-52210-01
Plug the removed components with clean and undamaged sealing caps and store it into the
box to keep the conditions when it was installed. 6.
Fuel filter assembly
Follow the job procedures. If you find a defective component, replace it with new one. 5.
Once disconnected, the fuel pipes between HP pump and fuel rail and between fuel rail and each
injector should be replaced with new ones. The pipes should be tightened tospecified tightening
torques during installation. Over or under torques out of specified range may cause damages and
leaks at connections. Once installed, the pipes have been deformed according to the force
during installation, therefore they are not reusable. The copper washer on injector should be
replaced with new one. The injector holder bolt should be tightened to specified tightening torque
as well. If not, the injection point may be deviated from correct position, and it may cause engine
disorder.
To supply the fuel to transfer line of HP
pump press the priming pump until it
becomes hard. 7.
Priming pump
Check the installed components again and connect the negative battery cable. Start the engine
and check the operating status.
With Scan Tool, check if there are current faults and erase the history faults. 8.
9.
Priming pump cap
Page 210 of 715
03-6
2) Diagnostic Test for Engine Fuel System
(1) Overview
If a DTC is displayed on the diagnostic device, check the low pressure- and high pressure fuel
systems before removing the components.
To run the system properly, the electric system must be intact but for the DI engine, the fuel
pressure should be measured also when there is a malfunction even after the diagnostic test with
a diagnostic device.
(2) Hydraulic system
Page 211 of 715
03-72210-01
(3) Excessive backleak of injector
Excessive injector backlea ▶
Occurs when the injector control valve is not sealed due to the entry of the foreign materials.
Example: ▶
Entry of foreign materials
Burned out and worn HP pump
Mechanical damage inside the injector -
-
-
Page 212 of 715
03-8
(4) Loss of pump pressure/flow
Loss of HP pump pressure/flow ▶
Faulty fuel supply line, or damaged or worn pump causes the lack of flow pressure and flow
volume
Example: ▶
Air in fuel supply line
Excessive load on fuel supply line (←400 mBar)
Burned out and mechanical worn pump
High temperature of fuel supply (> 85℃) -
-
-
-
Page 213 of 715
03-92210-01
Device for high pressure
Device for low pressure
3) DI Engine Fuel System Pressure Test
(1) Test device (Tool kit)
(2) Pre-check
Check-tighten fuel supply line
Check fuel level in fuel tank
Check air in fuel supply line (bubble in fuel supply line or fuel)
Check fuel supply line for leaks (low pressure and high pressure)
Check that specified fuel is used
Check fuel filter for contamination -
-
-
-
-
-
Page 214 of 715
03-10
(3) DI Engine Fuel System Check Procedure
If several DTCs are output simultaneously, check the electric wiring for open or short circuit.
Check the low pressure fuel system and fuel filter and confirm that there are no abnormalities.
Carry out the high pressure fuel system check.
Page 215 of 715
03-112210-01
(4) Fuel System Check Procedure
Page 216 of 715
03-12
(5) High Pressure System Pressure Test
Fuel rail pressure test ▶
Disconnect the pressure sensor connector
(A) and IMV connector (B) from the fuel
rail. 1.
Connect the pressure tester to the fuel rail
pressure sensor connector. 2.
Crank the engine 2 times for 5 seconds. 3.
Read the highest pressure value
displayed on the tester display.
If the highest pressure value is 1,050 bar
or less, refer to the section "Fuel System
Check Process". -
-