Page 161 of 715
02-4
2. TIGHTENING TORQUE
Component SizeBolt
QuantitySpecified torque
(Nm)Remark
(Total torque)
Main bearing capM12×82 10 55±5Nm,
180˚ Not re-usable
Connecting rod capM9×52 8 40±5Nm,
90˚+10˚ 50 to 80 Nm
Crankshaft rear sealM6×20 6 10±1Nm -
Oil pump M8x35 3 25±2.5Nm -
Drive plateM10×22 8 45±5Nm,
90˚+10˚ 60 to 100 Nm
Isolation damper center
boltM18x50 1 200±20Nm,
180˚+20˚660 to 720 Nm
Not re-usable
Oil panM6×20 18 10±1Nm -
M6×35 2 10±1Nm -
M6×85 2 10±1Nm -
M6×120 2 10±1Nm -
M8×40 2 25±2.5Nm -
HP pump main nutM14×1.5-8-1 1 65±5Nm -
HP pump bolt M8x30 3 25±2.5Nm -
Cylinder headM13×150 12 85Nm
270°±10° -
Camshaft capM6×30 16 10±1Nm -
M8×60 4 25±2.5Nm -
Exhaust stud bolt 10 15±1.5Nm -
Exhaust sprocket boltM11×40 1 30±3Nm -
Chain tensioner screw
plugM38×1.5 1 25±2.5Nm -
Coolant temperature
sensor1 20±2.0Nm
-
Auto tensionerM8×30(LOW) 1 25±2.5Nm -
M10×75(Upper)1 55±5.5Nm -
Coolant pumpM6×50 7 10±1.0Nm -
Page 162 of 715
02-50000-00
Component SizeBolt
QuantitySpecified torque
(Nm)Remark
(Total torque)
Hot water inlet pipeM6×12210±1Nm-
AlternatorM10×901(lower) 25±2.5Nm-
M10×1161(upper) 46±4.6Nm-
A/C compressorM8×85425±2.5Nm-
A/C bracketM6×25410±1Nm-
Intake manifoldM8×35225±2.5Nm-
M8×110625±2.5Nm-
Oil filter moduleM8×40625±2.5Nm-
M8×20125±2.5Nm-
M8×140225±2.5Nm-
Knock sensorM8×28220±5Nm-
Cam position sensorM8×141 10~14Nm -
T-MAP pressure
sensorM6×20110±1Nm-
Exhaust manifold M8 1040±4Nm-
Turbocharger M8 325±2.5Nm-
T/C support bolt 125±2.5Nm-
T/C support nut M8 125±2.5Nm-
T/C oil supply pipe M6(block side) 110±1.0Nm-
M6(turbo side) 117±2.0Nm-
T/C oil return pipeM6×16
(turbo side)210±1Nm-
M6×16
(block side)210±1Nm-
EGR valveM8×22325±2.5Nm-
EGR pipe bolt
(Intake side)M8×16210±1.0Nm-
EGR pipe bolt
(EGR cooler side)M8×16225±2.5Nm-
Idle pulley/Tensioner
pulley145±4.5Nm -
Page 163 of 715
02-6
Cylinder head coverM6×352110±1Nm-
Oil gauge tubeM6×16110±1Nm-
Oil filter cap 125±2.5Nm-
Fuel railM8×25225±2.5Nm-
Injector clamp boltM6×4429±1.0Nm
130˚±10˚-
High pressure pipe
(between HP pump and
fuel rail)M17 130±3Nm-
High pressure pipe
(between fuel rail and
injector)M17 430±3Nm-
Crank position sensorM5×1418±0.4Nm-
Main wiringM6×16510±1Nm-
Intake ductM8×25325±2.5Nm-
Power steering pumpM8×100325±2.5Nm-
Cylinder head front
coverM6×10510±1Nm-
Ladder frame M8x16 530±3Nm-
Component SizeBolt
QuantitySpecified torque
(Nm)Remark
(Total torque)
Glow plug M5 420±2Nm-
Vacuum pumpM8×25310±1Nm-
Timing gear case coverM6×40710±1Nm-
M6×45110±1Nm-
M6×50310±1Nm-
Page 164 of 715
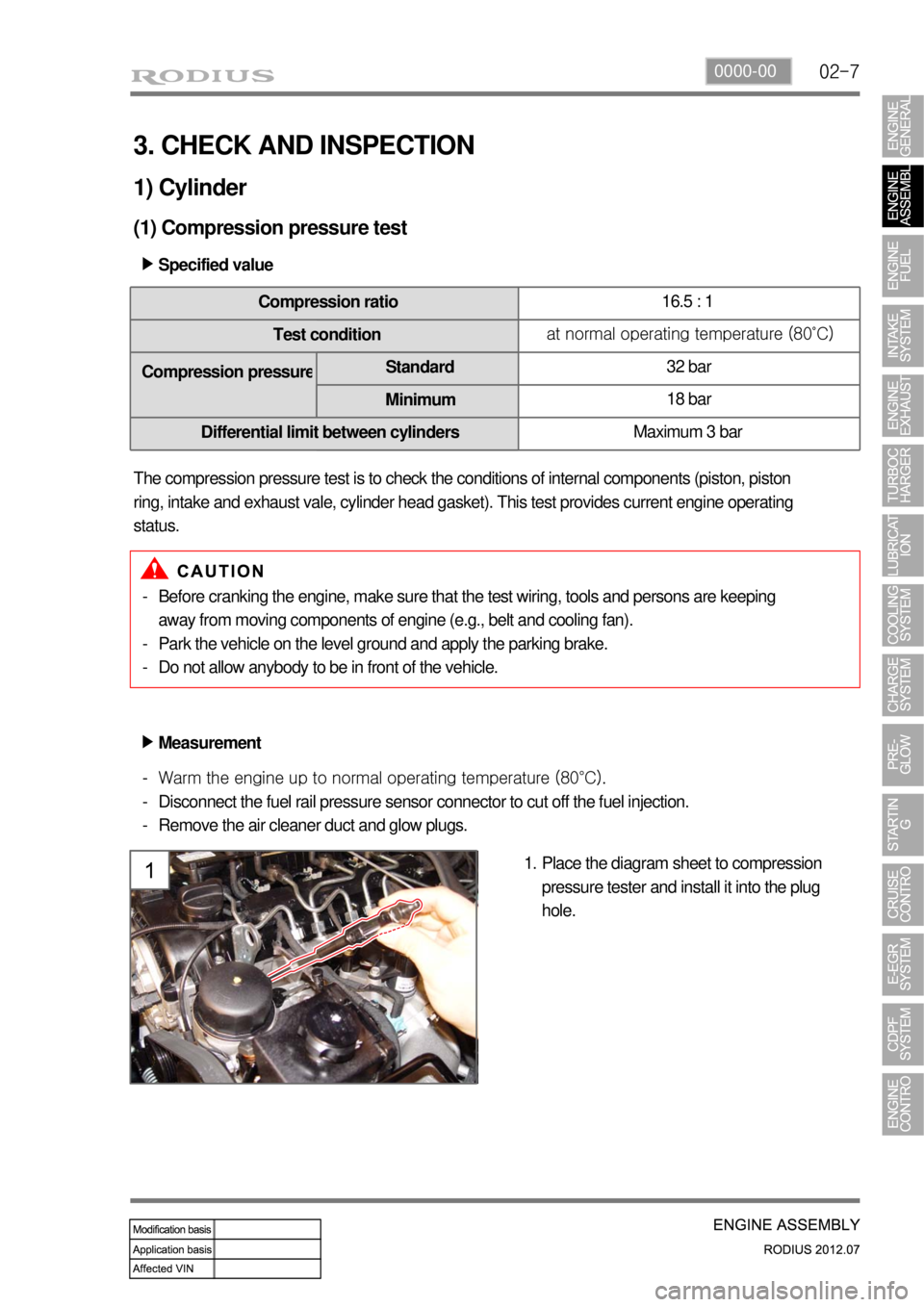
02-70000-00
3. CHECK AND INSPECTION
1) Cylinder
(1) Compression pressure test
Specified value ▶
Compression ratio16.5 : 1
Test conditionat normal operating temperature (80˚C)
Compression pressur
eStandard32 bar
Minimum18 bar
Differential limit between cylindersMaximum 3 bar
The compression pressure test is to check the conditions of internal components (piston, piston
ring, intake and exhaust vale, cylinder head gasket). This test provides current engine operating
status.
Measurement ▶
<007e0088009900940047009b008f008c0047008c0095008e00900095008c0047009c00970047009b00960047009500960099009400880093004700960097008c00990088009b00900095008e0047009b008c00940097008c00990088009b009c0099008c00
47004f005f005700b6006a00500055>
Disconnect the fuel rail pressure sensor connector to cut off the fuel injection.
Remove the air cleaner duct and glow plugs. -
-
-
Place the diagram sheet to compression
pressure tester and install it into the plug
hole. 1. Before cranking the engine, make sure that the test wiring, tools and persons are keeping
away from moving components of engine (e.g., belt and cooling fan).
Park the vehicle on the level ground and apply the parking brake.
Do not allow anybody to be in front of the vehicle. -
-
-
Page 165 of 715
02-8
(2) Cylinder pressure leakage test
If the measured value of the compression pressure test is not within the specifications, perform
the cylinder pressure leakage test.Specified value ▶
Perform this test in the sequence of firing order.
Do not test the cylinder pressure leakage with wet type test procedure. (do not inject the
engine oil into the combustion chamber) -
-
Test condition: normal engine operating
temperature (80˚C)Specified value
Whole engine below 25%
at valve and cylinder head gasket below 10%
at piston ring below 20%
Crank the engine for approx. 10 seconds
by using the start motor. 2.
Record the test result and measure the
compression pressure of other cylinders
with same manner. 3.
If the measured value is out of specified
value, perform the cylinder pressure
leakage test. 4.
Page 166 of 715
02-90000-00
Position the piston at TDC and measure the
piston protrusion from crank case mating
surface.
(3) Piston protrusion check
Specified value 0.475~0.745mm
Measure it at both ends of crankshaft. -
Page 167 of 715
02-10
2) Cylinder Head
(1) Cylinder head mating surface check
Specified value ▶
Measure the cylinder head height "A". 1.
Insert the valves into the valve guides and
measure the recesses. 2.
Valve recess “a”0.6 to 1.0mm
(2) Cylinder head pressure Leak test
Immerse the cylinder head with the pressure plate into warm water (approx. 60°C) and pressurize
with compressed air to 2 bar.If the height is less than the limit, the
cylinder head must be replaced. -
If the measured value is out of the
specified range, machine the valve seat
as much as necessary until the specified
value is achieved. -
Total height "A"131.9 to 132.1 mm
Minimum height after machining131.9 mm
Flatness Longitudinal direction0.1 / 150
Transverse direction0.15
Parallel deviation of cylinder headbelow 0.1 mm
Peak-to valley of surfaceRmax 7 Rz 6.3
valve recess "a" Intake valve0.6 to 1.0 mm
Exhaust valve0.6 to 1.0 mm
Page 168 of 715
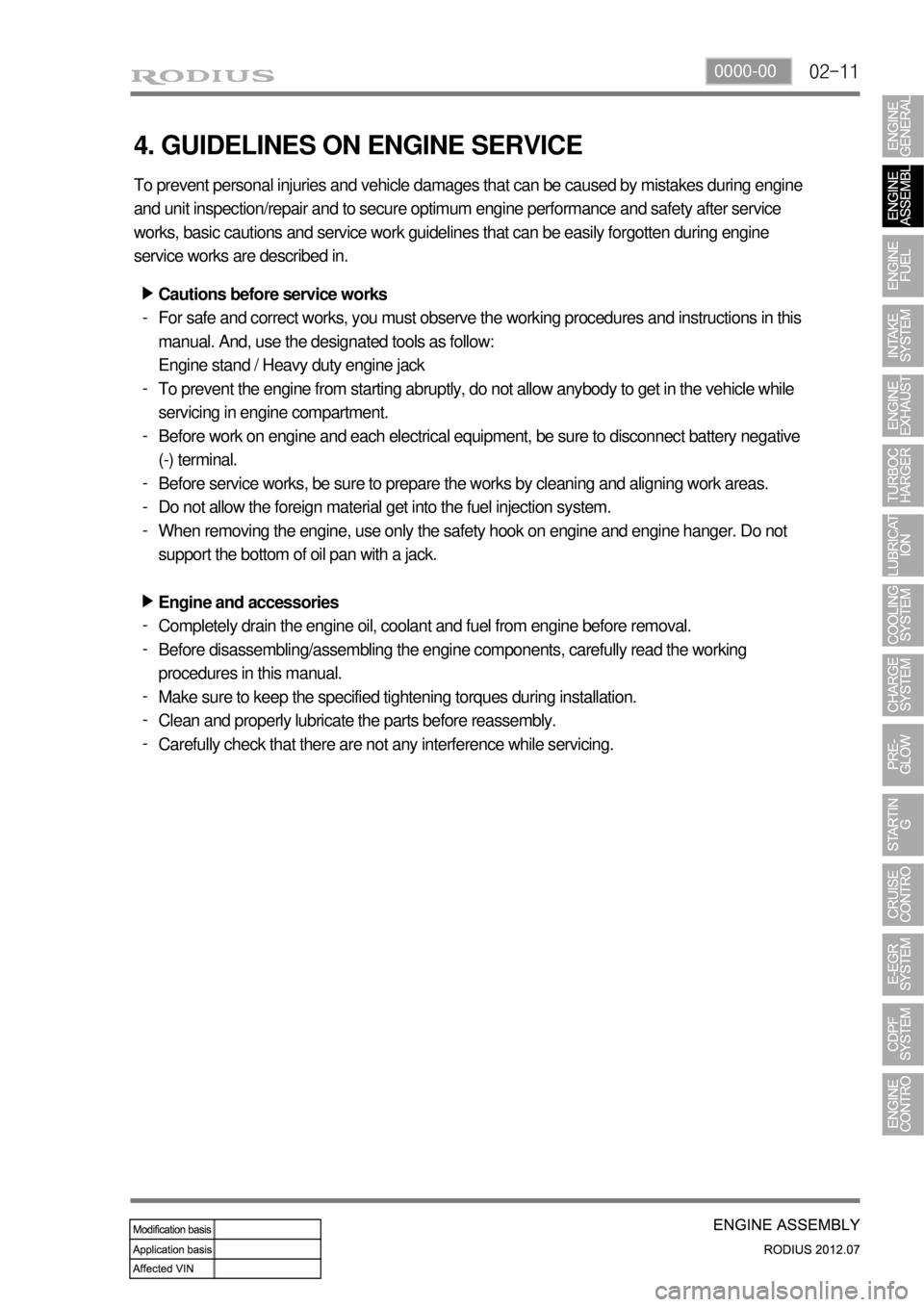
02-110000-00
4. GUIDELINES ON ENGINE SERVICE
To prevent personal injuries and vehicle damages that can be caused by mistakes during engine
and unit inspection/repair and to secure optimum engine performance and safety after service
works, basic cautions and service work guidelines that can be easily forgotten during engine
service works are described in.
Cautions before service works
For safe and correct works, you must observe the working procedures and instructions in this
manual. And, use the designated tools as follow:
Engine stand / Heavy duty engine jack
To prevent the engine from starting abruptly, do not allow anybody to get in the vehicle while
servicing in engine compartment.
Before work on engine and each electrical equipment, be sure to disconnect battery negative
(-) terminal.
Before service works, be sure to prepare the works by cleaning and aligning work areas.
Do not allow the foreign material get into the fuel injection system.
When removing the engine, use only the safety hook on engine and engine hanger. Do not
support the bottom of oil pan with a jack.
Engine and accessories
Completely drain the engine oil, coolant and fuel from engine before removal.
Before disassembling/assembling the engine components, carefully read the working
procedures in this manual.
Make sure to keep the specified tightening torques during installation.
Clean and properly lubricate the parts before reassembly.
Carefully check that there are not any interference while servicing. ▶
-
-
-
-
-
-
▶
-
-
-
-
-