Page 225 of 715
03-212210-01
1. OVERVIEW
The components in fuel system supply the fuel and generate the high pressure to inject the fuel to
each injector. They are controlled by the engine ECU.
The common rail fuel injection system consists of fuel tank, fuel line, low pressure line which
supplies low pressure fuel to the low pressure pump (including high pressure pump), common rail
which distributes and accumulates the high pressurized fuel from the fuel pump, high pressure
line which connected to the injector, and the engine control unit (ECU) which calculates the
accelerator pedal position and controls the overall performance of vehicle based on the input
signals from various sensors.
1) Fuel Flow Diagram
Page 226 of 715
03-22
Camshaft position sensor
Determining injection orderFuel tank
Fuel metering by sender
2. SYSTEM LAYOUT AND OPERATION
1) Layout
For sensor and actuator control logic, refer to Chapter "Engine Control".
Engine ECU (D20DTR)
Engine control by various
signalsInjector (C3I)
Pre-injection, main injection,
after-injection by signals from
ECU
HFM sensor
Measuring intake air mass
and temperature
Crankshaft position sensor
Measuring engine rpm
Page 227 of 715
03-232210-01
T-MAP sensor
Measuring booster pressure
and temperatureFuel rail assembly
Relieving the pulsation.
Measuring the fuel pressure.
Distributing the fuel to injectors.
High pressure pump
Generating high pressurized fuel
and supplying it according to
engine rpm, required volume,
required pressure
Plunger type HP pump (1,800 bar)
Vane type LP pump (6 bar)
Accelerator pedal position
sensor
Detecting driver's intention for
speed up/down
Fuel filter assembly
Supplying clean fuel/fuel
heating/water separation by
priming pump
Page 228 of 715
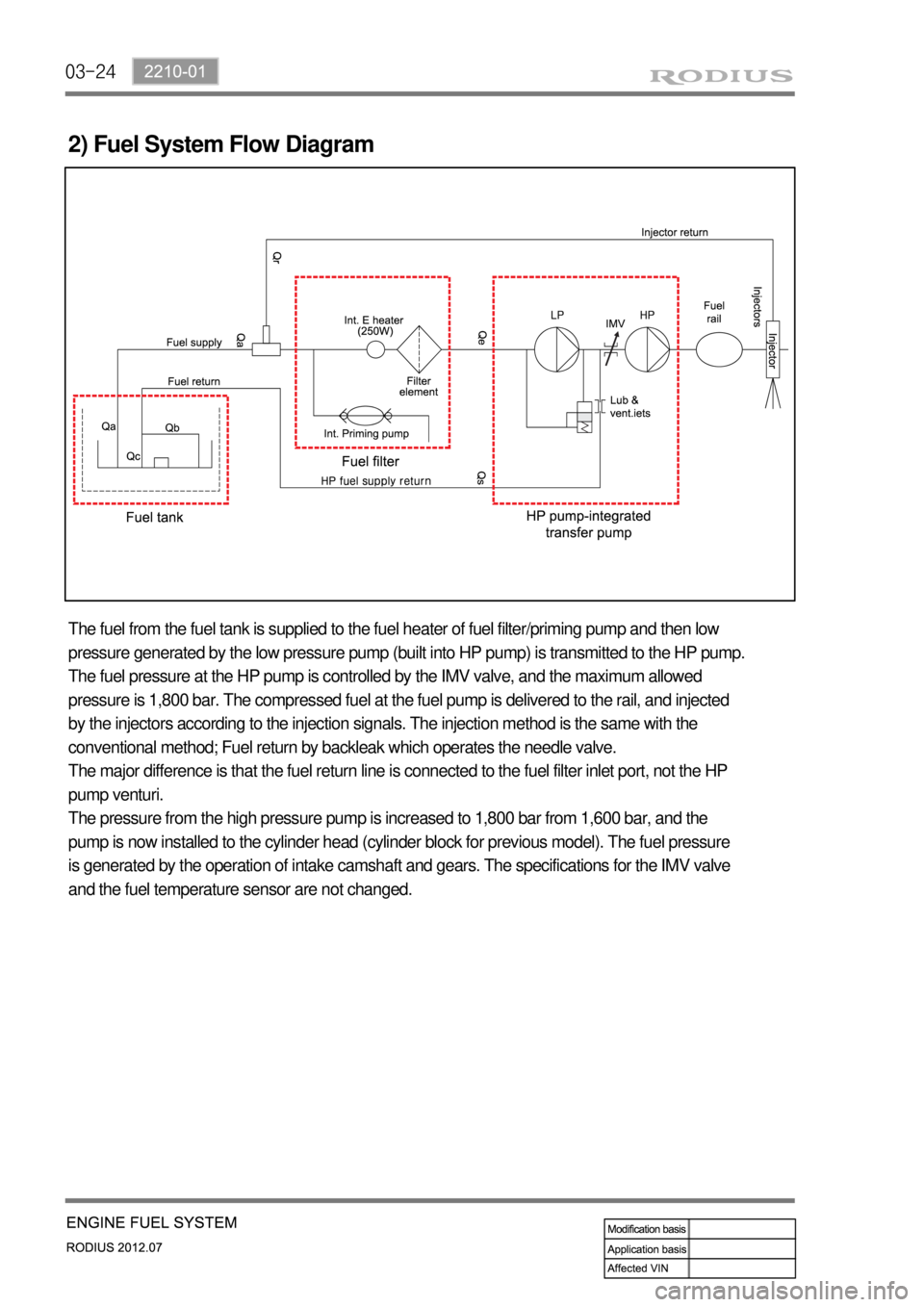
03-24
2) Fuel System Flow Diagram
The fuel from the fuel tank is supplied to the fuel heater of fuel filter/priming pump and then low
pressure generated by the low pressure pump (built into HP pump) is transmitted to the HP pump.
The fuel pressure at the HP pump is controlled by the IMV valve, and the maximum allowed
pressure is 1,800 bar. The compressed fuel at the fuel pump is delivered to the rail, and injected
by the injectors according to the injection signals. The injection method is the same with the
conventional method; Fuel return by backleak which operates the needle valve.
The major difference is that the fuel return line is connected to the fuel filter inlet port, not the HP
pump venturi.
The pressure from the high pressure pump is increased to 1,800 bar from 1,600 bar, and the
pump is now installed to the cylinder head (cylinder block for previous model). The fuel pressure
is generated by the operation of intake camshaft and gears. The specifications for the IMV valve
and the fuel temperature sensor are not changed.
Page 229 of 715
03-252210-01
3) Input/Output devices
Refer to Chapter "Engine Control". *
Page 230 of 715
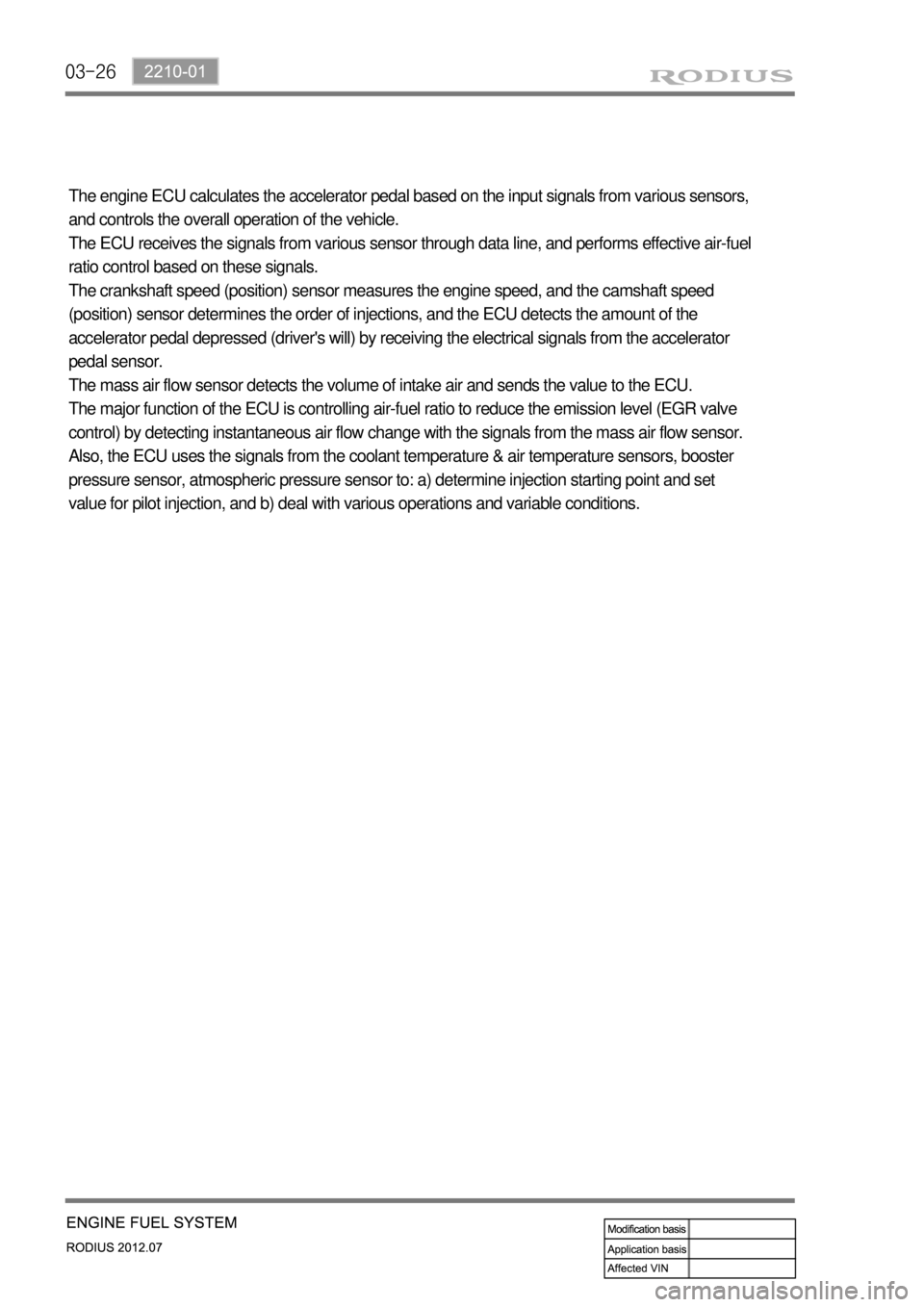
03-26
The engine ECU calculates the accelerator pedal based on the input signals from various sensors,
and controls the overall operation of the vehicle.
The ECU receives the signals from various sensor through data line, and performs effective air-fuel
ratio control based on these signals.
The crankshaft speed (position) sensor measures the engine speed, and the camshaft speed
(position) sensor determines the order of injections, and the ECU detects the amount of the
accelerator pedal depressed (driver's will) by receiving the electrical signals from the accelerator
pedal sensor.
The mass air flow sensor detects the volume of intake air and sends the value to the ECU.
The major function of the ECU is controlling air-fuel ratio to reduce the emission level (EGR valve
control) by detecting instantaneous air flow change with the signals from the mass air flow sensor.
Also, the ECU uses the signals from the coolant temperature & air temperature sensors, booster
pressure sensor, atmospheric pressure sensor to: a) determine injection starting point and set
value for pilot injection, and b) deal with various operations and variable conditions.
Page 231 of 715
04-31719-00
1. SPECIFICATIONS
Shorten the service interval under severe conditions such as driving on a dusty road or off-
road. *
Unit Description Specification
Air cleaner elementFilter type Dry, filter element
Initial resistance Max. 300 mmAq
Service interval EU: Change every 20,000 km
GEN: Change every 15,000 km
Air cleaner assemblyWeight 2.36kg
Operating temperature-30 ~ 100℃
IntercoolerRadiation over 13,000 Kcal
Pressure loss at turbocharger below 90 mmHg
Cooling type Air cooled type
Core size 450W*130H*70T
Core type C/FIN
Page 232 of 715
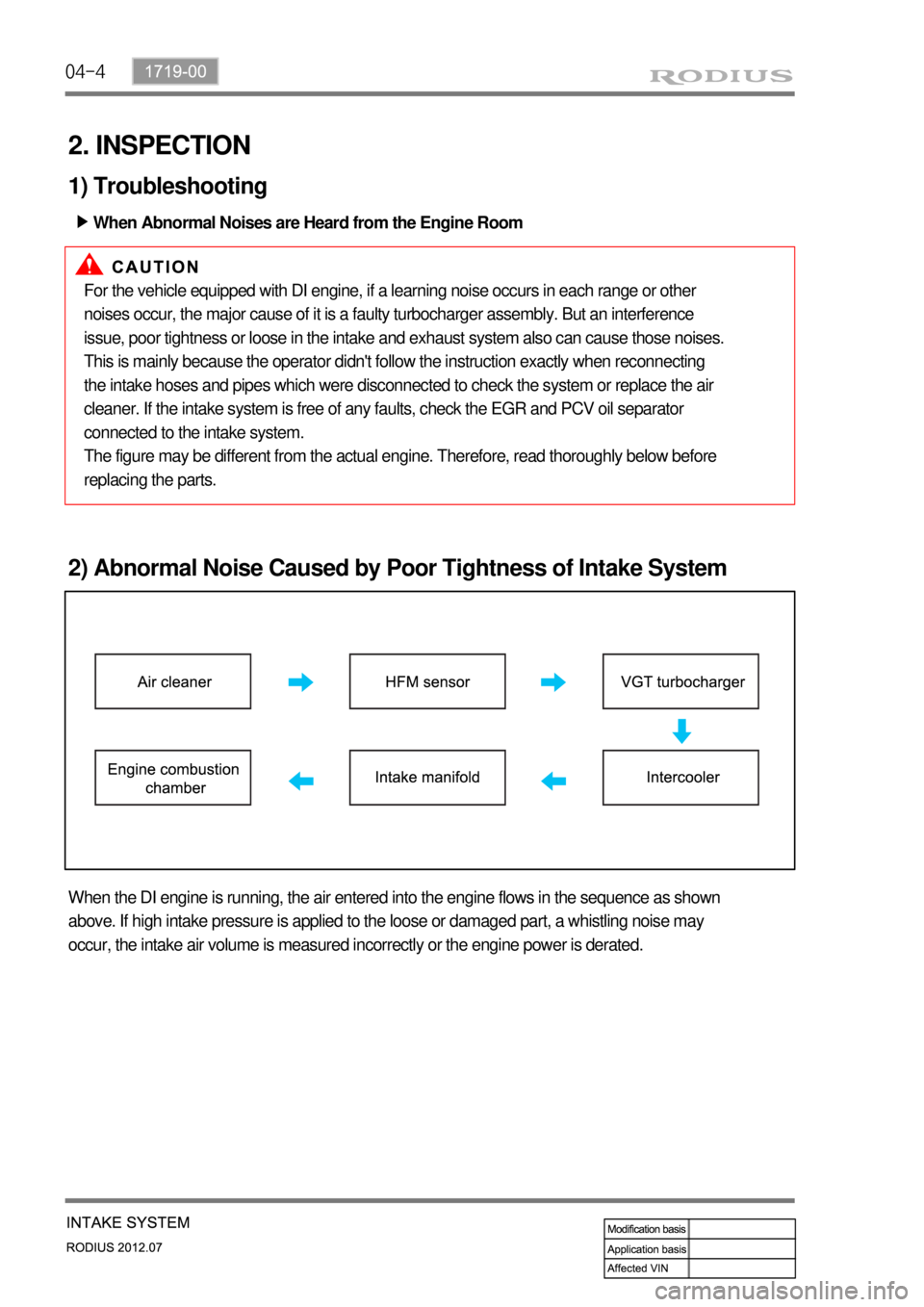
04-4
2. INSPECTION
1) Troubleshooting
When Abnormal Noises are Heard from the Engine Room ▶
For the vehicle equipped with DI engine, if a learning noise occurs in each range or other
noises occur, the major cause of it is a faulty turbocharger assembly. But an interference
issue, poor tightness or loose in the intake and exhaust system also can cause those noises.
This is mainly because the operator didn't follow the instruction exactly when reconnecting
the intake hoses and pipes which were disconnected to check the system or replace the air
cleaner. If the intake system is free of any faults, check the EGR and PCV oil separator
connected to the intake system.
The figure may be different from the actual engine. Therefore, read thoroughly below before
replacing the parts.
2) Abnormal Noise Caused by Poor Tightness of Intake System
When the DI engine is running, the air entered into the engine flows in the sequence as shown
above. If high intake pressure is applied to the loose or damaged part, a whistling noise may
occur, the intake air volume is measured incorrectly or the engine power is derated.