Page 409 of 652
13B-48
DIESEL INJECTION
Rail pressure sensor: Removal - Refitting
K9K
13B
aThe pressure sensor (1) cannot be removed from
the spherical injector rail.
If the pressure sensor is faulty, replace the
« pressure sensor - high pressure pipes and rail »
assembly (see 13B, Diesel injection, Injector rail:
Removal - Refitting, page 13B-43) .
102086
Page 410 of 652
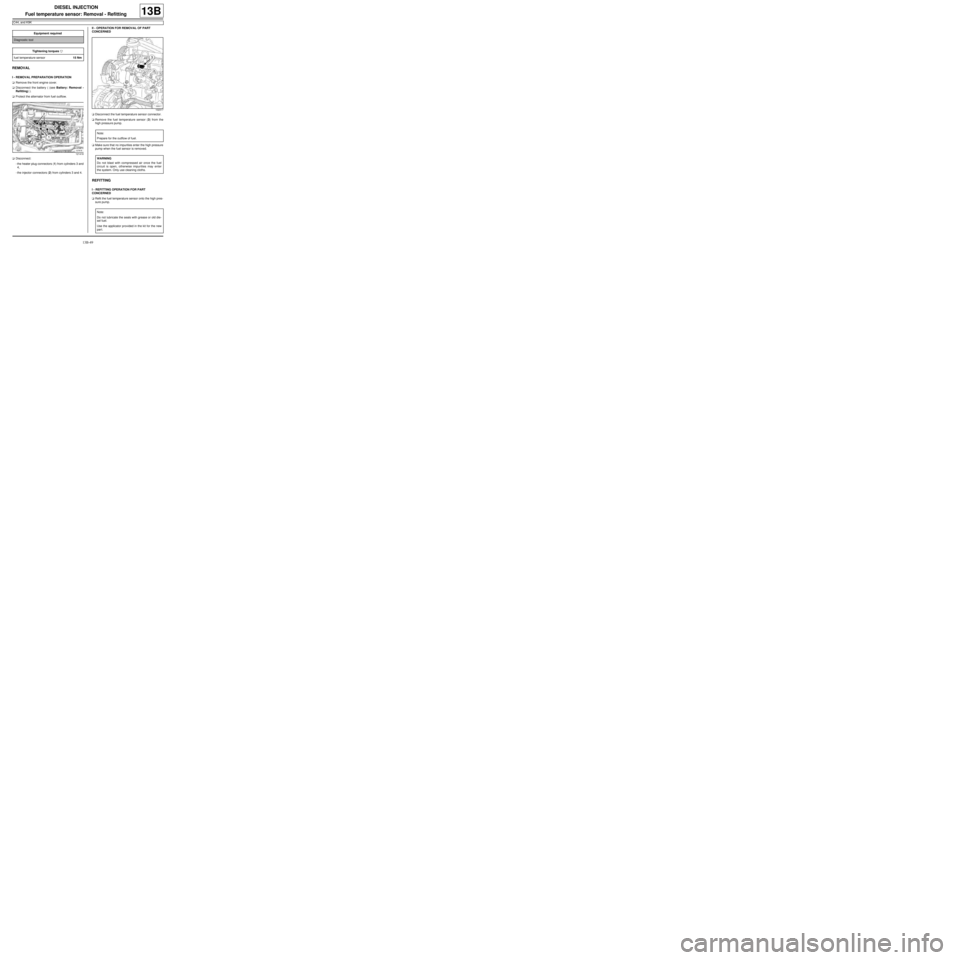
13B-49
DIESEL INJECTION
Fuel temperature sensor: Removal - Refitting
C44, and K9K
13B
REMOVAL
I - REMOVAL PREPARATION OPERATION
aRemove the front engine cover.
aDisconnect the battery ( (see Battery: Removal -
Refitting) ).
aProtect the alternator from fuel outflow.
aDisconnect:
-the heater plug connectors (1) from cylinders 3 and
4,
-the injector connectors (2) from cylinders 3 and 4.II - OPERATION FOR REMOVAL OF PART
CONCERNED
aDisconnect the fuel temperature sensor connector.
aRemove the fuel temperature sensor (3) from the
high pressure pump.
aMake sure that no impurities enter the high pressure
pump when the fuel sensor is removed.
REFITTING
I - REFITTING OPERATION FOR PART
CONCERNED
aRefit the fuel temperature sensor onto the high pres-
sure pump. Equipment required
Diagnostic tool
Tightening torquesm
fuel temperature sensor15 Nm
121418
102317
Note:
Prepare for the outflow of fuel.
WARNING
Do not blast with compressed air once the fuel
circuit is open, otherwise impurities may enter
the system. Only use cleaning cloths.
Note:
Do not lubricate the seals with grease or old die-
sel fuel.
Use the applicator provided in the kit for the new
par t.
Page 411 of 652
13B-50
DIESEL INJECTION
Fuel temperature sensor: Removal - Refitting
C44, and K9K
13B
aTorque tighten the fuel temperature sensor (15
Nm).
aConnect the fuel temperature sensor connector.
II - FINAL OPERATION.
aConnect:
-the injector connectors for cylinders 3 and 4,
-the heater plug connectors for cylinders 3 and 4.
aRemove the protection on the alternator to prevent
fuel flowing out.
aConnect the battery ( (see Battery: Removal - Re-
fitting) ).
aStart the engine and check that there are no leaks.
aRefit the engine cover.
aUse the Diagnostic tool to check for an absence of
stored faults; deal with these and clear them as nec-
essary.
Page 412 of 652
13B-51
DIESEL INJECTION
Injector leak flow: Check
K9K
13B
PIECES ET INGREDIENTS POUR LA REPARATION
Ingrédients :
-cleaning cloths,
-set of K9K blanking plugs (DELPHI injection).
CHECK
aRemove the front engine cover.aDisconnect:
-the diesel return pipes (1) on the injectors,
-the diesel return pipe (2) on the Venturi fitted on the
high pressure pump.
aFit the correct blanking plug on the Venturi. Special tooling required
Mot. 1711Kit for measuring the injector
fuel flow rate.
Equipment required
Diagnostic tool
IMPORTANT
Consult the safety and cleanliness advice and oper-
ation recommendations before carrying out any
repair (see 13B, Diesel injection, Diesel injec-
tion: Precautions for the repair, page 13B-1) .
121418
WARNING
To avoid any corrosion or damage, protect the
areas on which fuel is likely to r un.
Note:
It is essential to fi t an appropriate blanking plug
to the Venturi to avoid depriming the diesel return
circuit.
Page 413 of 652
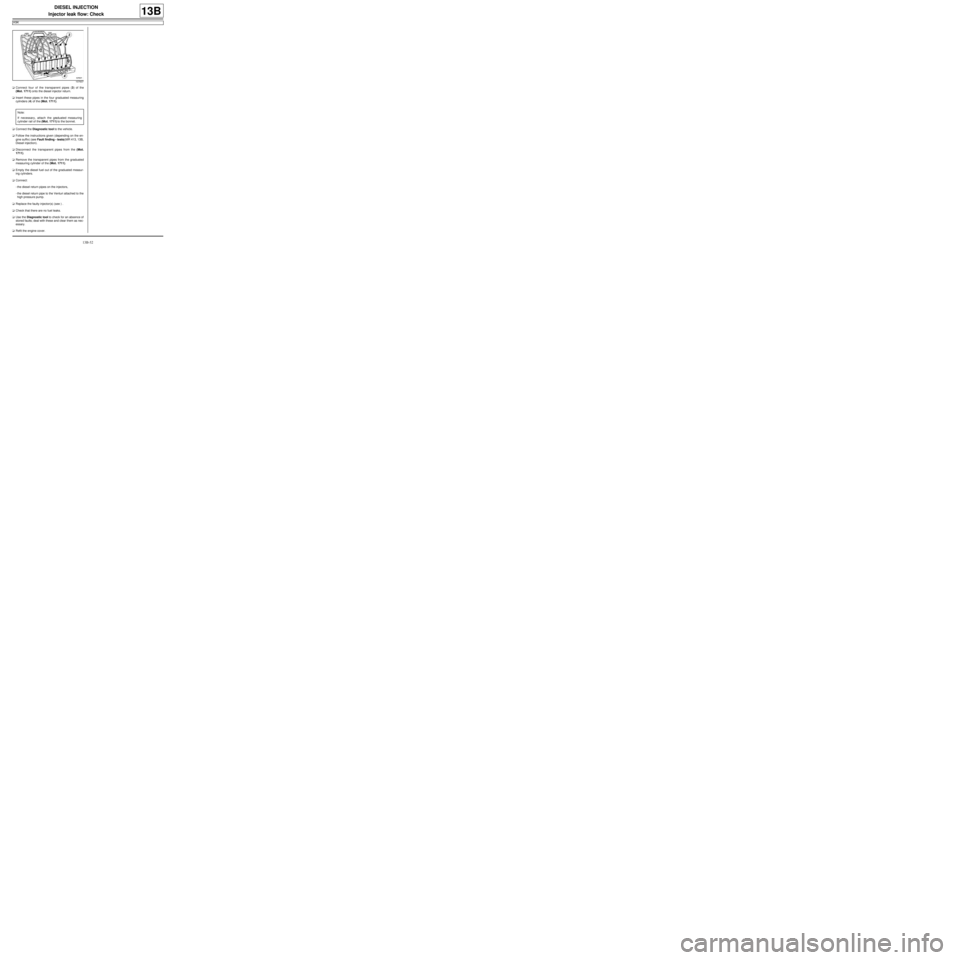
13B-52
DIESEL INJECTION
Injector leak flow: Check
K9K
13B
aConnect four of the transparent pipes (3) of the
(Mot. 1711) onto the diesel injector return.
aInsert these pipes in the four graduated measuring
cylinders (4) of the (Mot. 1711).
aConnect the Diagnostic tool to the vehicle.
aFollow the instructions given (depending on the en-
gine suffix) (see Fault finding - tests)(MR 413, 13B,
Diesel injection).
aDisconnect the transparent pipes from the (Mot.
1711).
aRemove the transparent pipes from the graduated
measuring cylinder of the (Mot. 1711).
aEmpty the diesel fuel out of the graduated measur-
ing cylinders.
aConnect:
-the diesel return pipes on the injectors,
-the diesel return pipe to the Venturi attached to the
high pressure pump.
aReplace the faulty injector(s) (see ) .
aCheck that there are no fuel leaks.
aUse the Diagnostic tool to check for an absence of
stored faults; deal with these and clear them as nec-
essary.
aRefit the engine cover.
107637
Note:
If necessary, attach the graduated measuring
cylinder rail of the (Mot. 1711) to the bonnet.
Page 414 of 652
13B-53
DIESEL INJECTION
Accelerometer: Removal - Refitting
K9K
13B
REMOVAL
I - REMOVAL PREPARATION OPERATION
aRemove the front engine cover.
aRemove:
-the dipstick,
-the oil level dipstick nut (1) ,
-the oil level dipstick guide.
aPlug the oil level dipstick guide inlet opening on the
cylinder block.
aDisconnect the following connectors :
-the heater plugs,
-the injectors,
-the flow actuator,-the diesel temperature sensor.
aDetach the channel at (2) .
aMove the wiring away from the channel.
aRemove:
-the nut (3) from the channel,
-the neck. Special tooling required
Emb. 1797Socket (24 mm) for removal -
refitting of the clutch master
cylinder
Equipment required
Diagnostic tool
Tightening torquesm
accelerometer20 N.m
114527
121419
Page 415 of 652
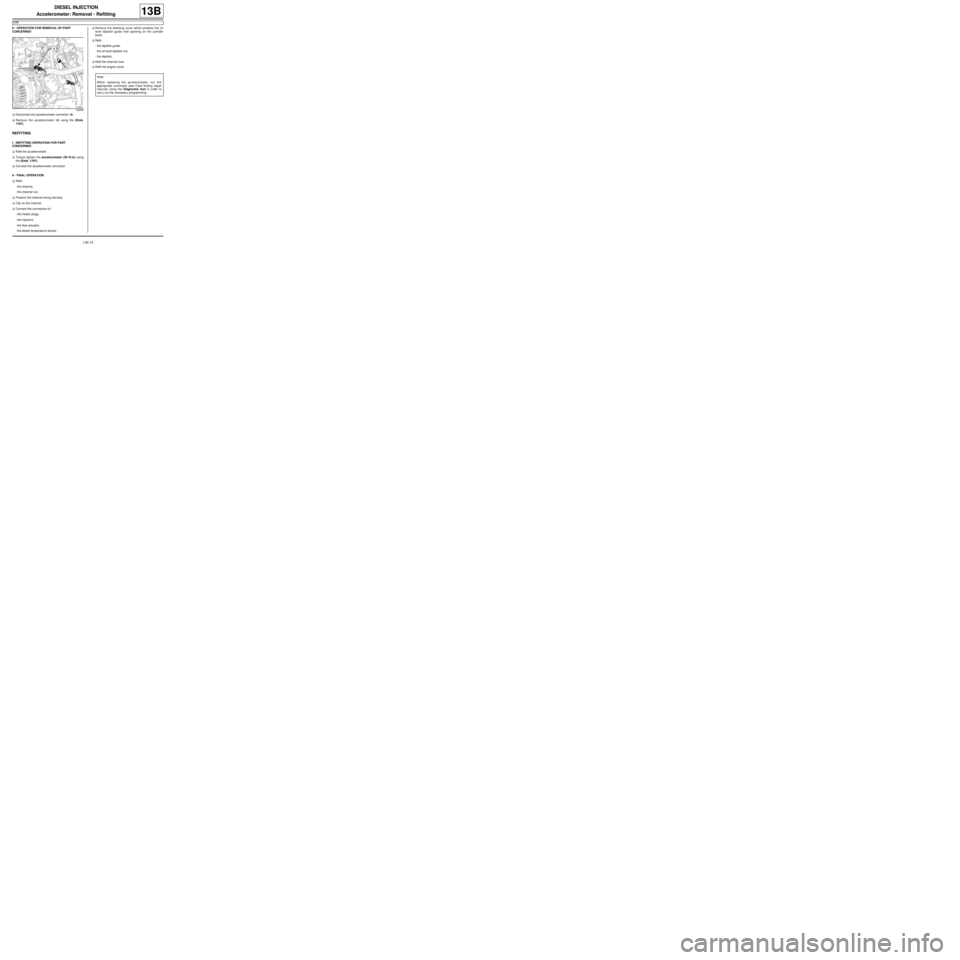
13B-54
DIESEL INJECTION
Accelerometer: Removal - Refitting
K9K
13B
II - OPERATION FOR REMOVAL OF PART
CONCERNED
aDisconnect the accelerometer connector (4) .
aRemove the accelerometer (4) using the (Emb.
1797).
REFITTING
I - REFITTING OPERATION FOR PART
CONCERNED
aRefit the accelerometer.
aTorque tighten the accelerometer (20 N.m) using
the (Emb. 1797).
aConnect the accelerometer connector.
II - FINAL OPERATION
aRefit:
-the channel,
-the channel nut.
aPosition the channel wiring harness.
aClip on the channel.
aConnect the connectors of:
-the heater plugs,
-the injectors,
-the flow actuator,
-the diesel temperature sensor.aRemove the blanking cover which protects the oil
level dipstick guide inlet opening on the cylinder
block.
aRefit:
-the dipstick guide,
-the oil level dipstick nut,
-the dipstick.
aRefit the channel nuts.
aRefit the engine cover.
109939
Note:
When replacing the accelerometer, run the
appropriate command (see Fault finding repair
manual) using the Diagnostic tool in order to
carr y out the necessary programming.
Page 416 of 652
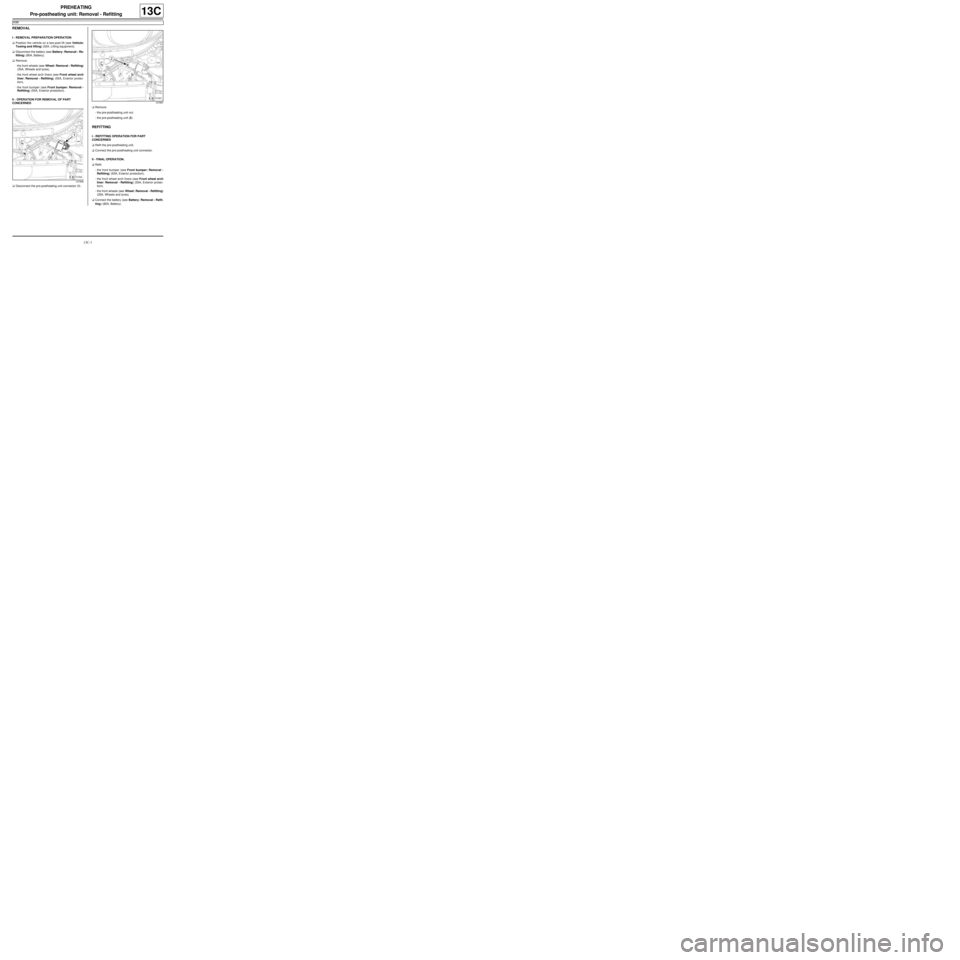
13C-1
PREHEATING
Pre-postheating unit: Removal - Refitting
K9K
13C
REMOVAL
I - REMOVAL PREPARATION OPERATION
aPosition the vehicle on a two-post lift (see Vehicle:
Towing and lifting) (02A, Lifting equipment).
aDisconnect the battery (see Battery: Removal - Re-
fitting) (80A, Battery).
aRemove:
-the front wheels (see Wheel: Removal - Refitting)
(35A, Wheels and tyres),
-the front wheel arch liners (see Front wheel arch
liner: Removal - Refitting) (55A, Exterior protec-
tion),
-the front bumper (see Front bumper: Removal -
Refitting) (55A, Exterior protection).
II - OPERATION FOR REMOVAL OF PART
CONCERNED
aDisconnect the pre-postheating unit connector (1) .aRemove:
-the pre-postheating unit nut.
-the pre-postheating unit (2) .
REFITTING
I - REFITTING OPERATION FOR PART
CONCERNED
aRefit the pre-postheating unit.
aConnect the pre-postheating unit connector.
II - FINAL OPERATION.
aRefit:
-the front bumper (see Front bumper: Removal -
Refitting) (55A, Exterior protection),
-the front wheel arch liners (see Front wheel arch
liner: Removal - Refitting) (55A, Exterior protec-
tion),
-the front wheels (see Wheel: Removal - Refitting)
(35A, Wheels and tyres).
aConnect the battery (see Battery: Removal - Refit-
ting) (80A, Battery).
127896
127897