Page 355 of 2898
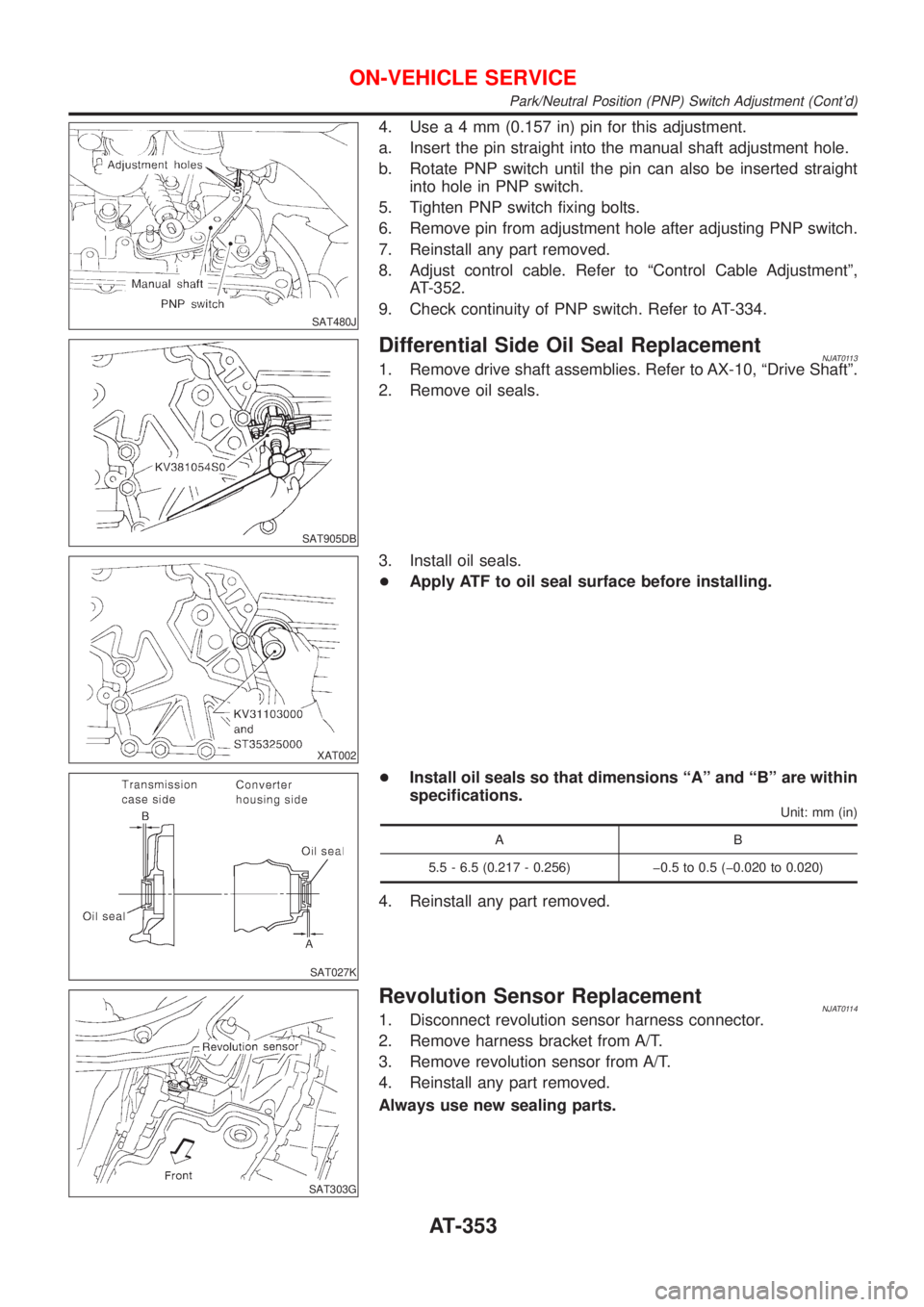
SAT480J
4. Usea4mm(0.157 in) pin for this adjustment.
a. Insert the pin straight into the manual shaft adjustment hole.
b. Rotate PNP switch until the pin can also be inserted straight
into hole in PNP switch.
5. Tighten PNP switch fixing bolts.
6. Remove pin from adjustment hole after adjusting PNP switch.
7. Reinstall any part removed.
8. Adjust control cable. Refer to ªControl Cable Adjustmentº,
AT-352.
9. Check continuity of PNP switch. Refer to AT-334.
SAT905DB
Differential Side Oil Seal ReplacementNJAT01131. Remove drive shaft assemblies. Refer to AX-10, ªDrive Shaftº.
2. Remove oil seals.
XAT002
3. Install oil seals.
+Apply ATF to oil seal surface before installing.
SAT027K
+Install oil seals so that dimensions ªAº and ªBº are within
specifications.
Unit: mm (in)
AB
5.5 - 6.5 (0.217 - 0.256) þ0.5 to 0.5 (þ0.020 to 0.020)
4. Reinstall any part removed.
SAT303G
Revolution Sensor ReplacementNJAT01141. Disconnect revolution sensor harness connector.
2. Remove harness bracket from A/T.
3. Remove revolution sensor from A/T.
4. Reinstall any part removed.
Always use new sealing parts.
ON-VEHICLE SERVICE
Park/Neutral Position (PNP) Switch Adjustment (Cont'd)
AT-353
Page 450 of 2898
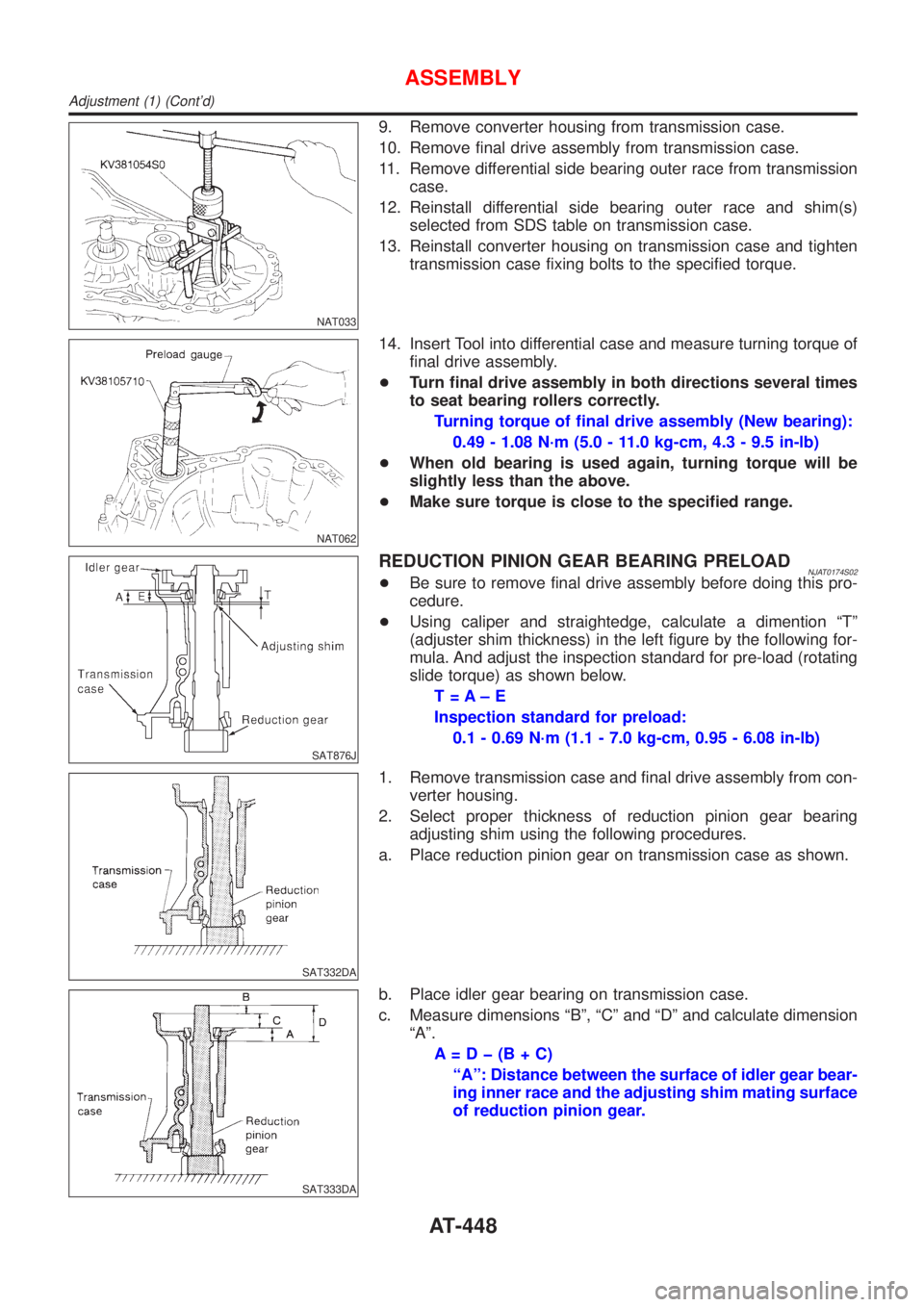
NAT033
9. Remove converter housing from transmission case.
10. Remove final drive assembly from transmission case.
11. Remove differential side bearing outer race from transmission
case.
12. Reinstall differential side bearing outer race and shim(s)
selected from SDS table on transmission case.
13. Reinstall converter housing on transmission case and tighten
transmission case fixing bolts to the specified torque.
NAT062
14. Insert Tool into differential case and measure turning torque of
final drive assembly.
+Turn final drive assembly in both directions several times
to seat bearing rollers correctly.
Turning torque of final drive assembly (New bearing):
0.49 - 1.08 N´m (5.0 - 11.0 kg-cm, 4.3 - 9.5 in-lb)
+When old bearing is used again, turning torque will be
slightly less than the above.
+Make sure torque is close to the specified range.
SAT876J
REDUCTION PINION GEAR BEARING PRELOADNJAT0174S02+Be sure to remove final drive assembly before doing this pro-
cedure.
+Using caliper and straightedge, calculate a dimention ªTº
(adjuster shim thickness) in the left figure by the following for-
mula. And adjust the inspection standard for pre-load (rotating
slide torque) as shown below.
T=A±E
Inspection standard for preload:
0.1 - 0.69 N´m (1.1 - 7.0 kg-cm, 0.95 - 6.08 in-lb)
SAT332DA
1. Remove transmission case and final drive assembly from con-
verter housing.
2. Select proper thickness of reduction pinion gear bearing
adjusting shim using the following procedures.
a. Place reduction pinion gear on transmission case as shown.
SAT333DA
b. Place idler gear bearing on transmission case.
c. Measure dimensions ªBº, ªCº and ªDº and calculate dimension
ªAº.
A=Dþ(B+C)
ªAº: Distance between the surface of idler gear bear-
ing inner race and the adjusting shim mating surface
of reduction pinion gear.
ASSEMBLY
Adjustment (1) (Cont'd)
AT-448
Page 452 of 2898
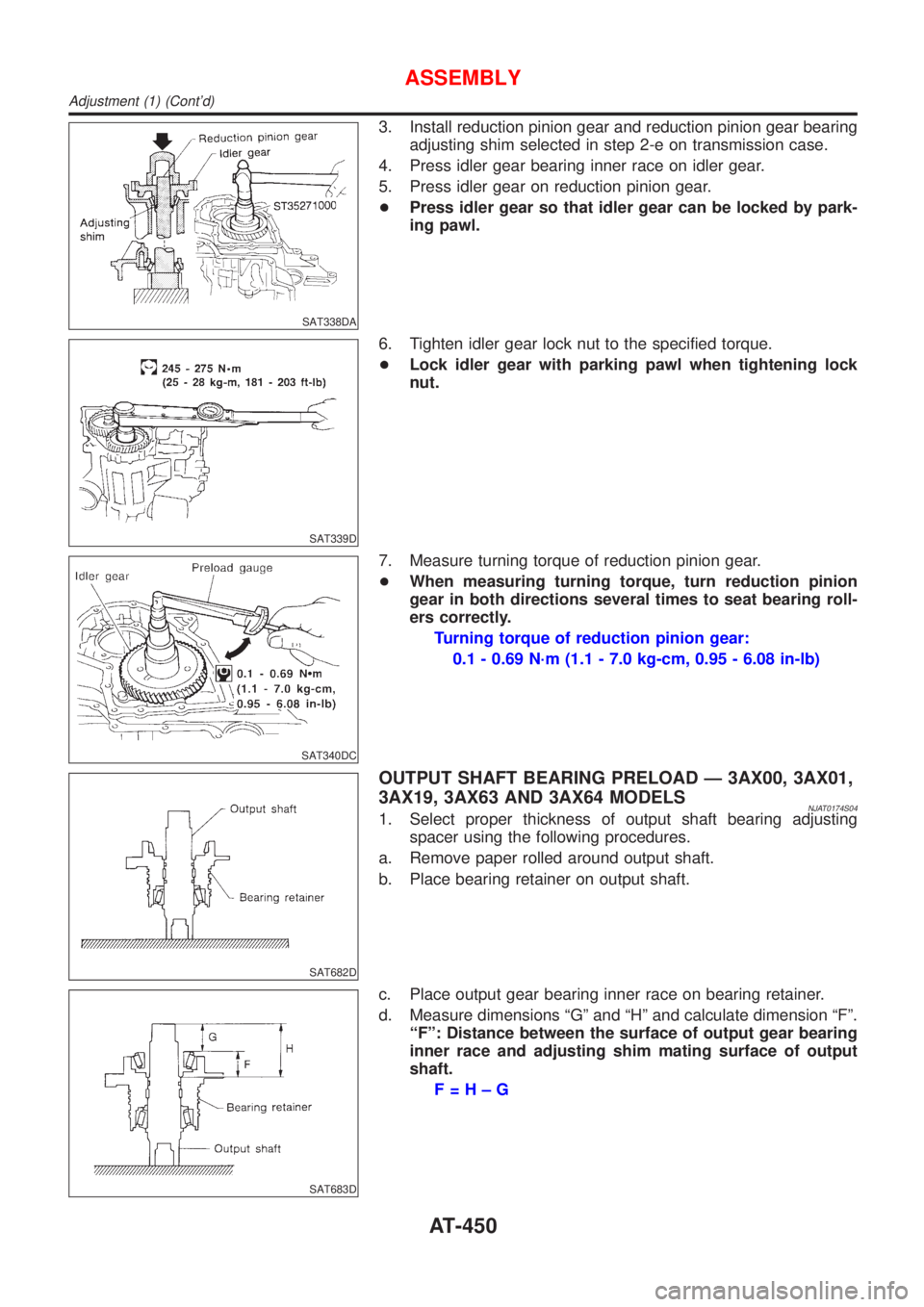
SAT338DA
3. Install reduction pinion gear and reduction pinion gear bearing
adjusting shim selected in step 2-e on transmission case.
4. Press idler gear bearing inner race on idler gear.
5. Press idler gear on reduction pinion gear.
+Press idler gear so that idler gear can be locked by park-
ing pawl.
SAT339D
6. Tighten idler gear lock nut to the specified torque.
+Lock idler gear with parking pawl when tightening lock
nut.
SAT340DC
7. Measure turning torque of reduction pinion gear.
+When measuring turning torque, turn reduction pinion
gear in both directions several times to seat bearing roll-
ers correctly.
Turning torque of reduction pinion gear:
0.1 - 0.69 N´m (1.1 - 7.0 kg-cm, 0.95 - 6.08 in-lb)
SAT682D
OUTPUT SHAFT BEARING PRELOAD Ð 3AX00, 3AX01,
3AX19, 3AX63 AND 3AX64 MODELS
NJAT0174S041. Select proper thickness of output shaft bearing adjusting
spacer using the following procedures.
a. Remove paper rolled around output shaft.
b. Place bearing retainer on output shaft.
SAT683D
c. Place output gear bearing inner race on bearing retainer.
d. Measure dimensions ªGº and ªHº and calculate dimension ªFº.
ªFº: Distance between the surface of output gear bearing
inner race and adjusting shim mating surface of output
shaft.
F=H±G
ASSEMBLY
Adjustment (1) (Cont'd)
AT-450
Page 456 of 2898
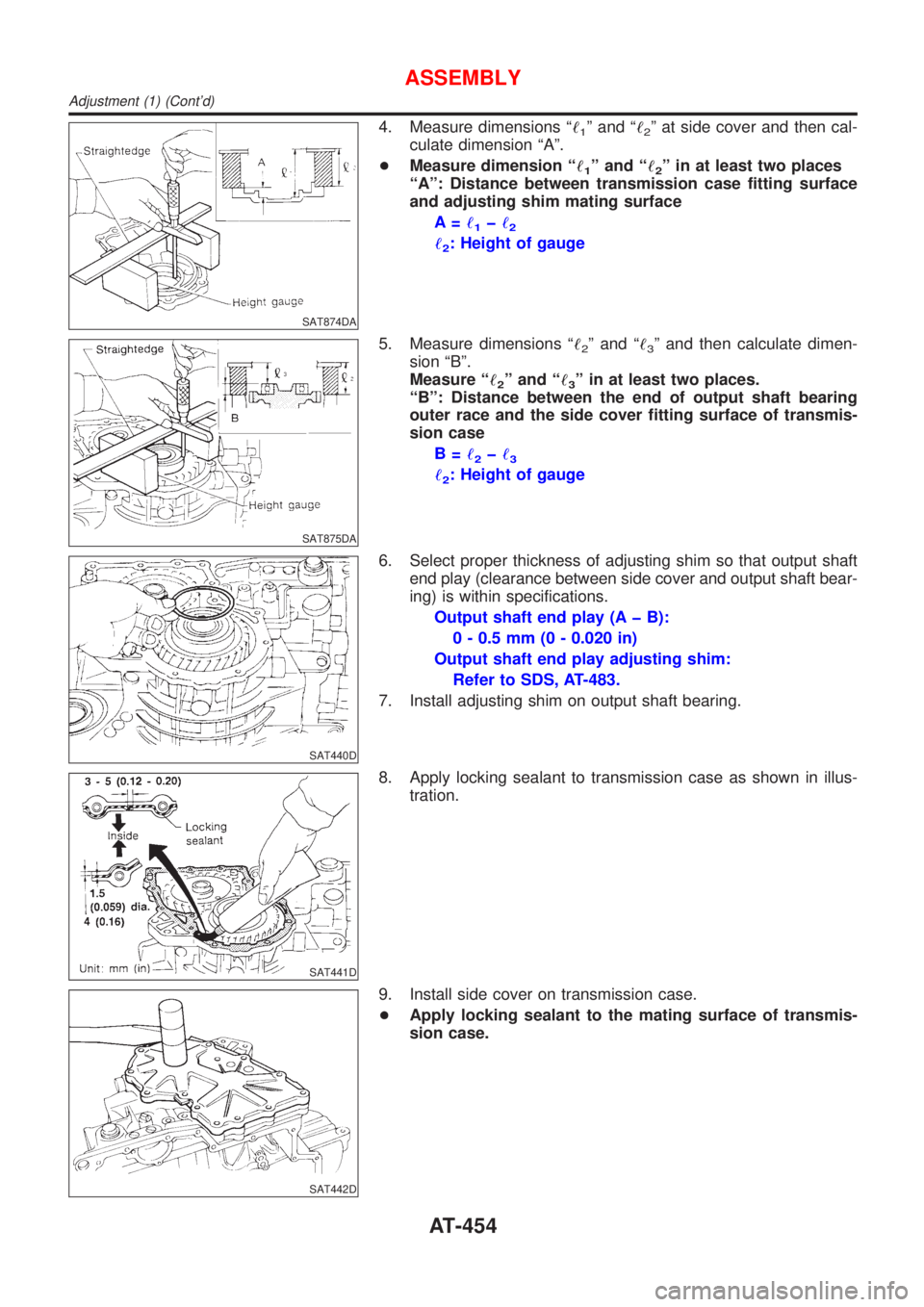
SAT874DA
4. Measure dimensions ª!1º and ª!2º at side cover and then cal-
culate dimension ªAº.
+Measure dimension ª!
1º and ª!2º in at least two places
ªAº: Distance between transmission case fitting surface
and adjusting shim mating surface
A=!
1þ!2
!2: Height of gauge
SAT875DA
5. Measure dimensions ª!2º and ª!3º and then calculate dimen-
sion ªBº.
Measure ª!
2º and ª!3º in at least two places.
ªBº: Distance between the end of output shaft bearing
outer race and the side cover fitting surface of transmis-
sion case
B=!
2þ!3
!2: Height of gauge
SAT440D
6. Select proper thickness of adjusting shim so that output shaft
end play (clearance between side cover and output shaft bear-
ing) is within specifications.
Output shaft end play (A þ B):
0 - 0.5 mm (0 - 0.020 in)
Output shaft end play adjusting shim:
Refer to SDS, AT-483.
7. Install adjusting shim on output shaft bearing.
SAT441D
8. Apply locking sealant to transmission case as shown in illus-
tration.
SAT442D
9. Install side cover on transmission case.
+Apply locking sealant to the mating surface of transmis-
sion case.
ASSEMBLY
Adjustment (1) (Cont'd)
AT-454
Page 461 of 2898
SAT373D
23. Install reverse clutch assembly.
+Align teeth of reverse clutch drive plates before installing.
Adjustment (2)NJAT0176When any parts listed below are replaced, adjust total end play and
reverse clutch end play.
Part name Total end playReverse clutch
end play
Transmission case++
Overrun clutch hub++
Rear internal gear++
Rear planetary carrier++
Rear sun gear++
Front planetary carrier++
Front sun gear++
High clutch hub++
High clutch drum++
Oil pump cover++
Reverse clutch drum Ð+
SAT374D
TOTAL END PLAYNJAT0176S01+Measure clearance between reverse clutch drum and needle
bearing for oil pump cover.
+Select proper thickness of bearing race so that end play is
within specifications.
SAT375D
1. Measure dimensions ªKº and ªLº and then calculate dimension
ªJº.
ASSEMBLY
Assembly (2) (Cont'd)
AT-459
Page 463 of 2898
3. Adjust total end play ªT3º.
T
3=JþM
Total end play ªT
3º:
0.25 - 0.55 mm (0.0098 - 0.0217 in)
+Select proper thickness of bearing race so that total end play
is within specifications.
Bearing races: Refer to SDS, AT-484.
SAT380D
REVERSE CLUTCH END PLAYNJAT0176S02+Measure clearance between oil pump cover and thrust washer
for reverse clutch drum.
+Select proper thickness of thrust washer so that end play is
within specifications.
SAT381D
1. Measure dimensions ªOº and ªPº and then calculate dimension
ªNº.
SAT382D
a. Place thrust washer on reverse clutch drum.
b. Measure dimension ªOº.
SAT383D
c. Measure dimension ªPº.
d. Calculate dimension ªNº.
ªNº: Distance between oil pump fitting surface of trans-
mission case and thrust washer on reverse clutch drum
N=OþP
ASSEMBLY
Adjustment (2) (Cont'd)
AT-461
Page 464 of 2898
SAT384D
2. Measure dimensions ªRº and ªSº and then calculate dimension
ªQº.
SAT385D
a. Measure dimension ªRº.
SAT386D
b. Measure dimension ªSº.
c. Calculate dimension ªQº.
ªQº: Distance between transmission case fitting surface
and thrust washer mating surface
Q=RþS
3. Adjust reverse clutch end play ªT
4º.
T
4=NþQ
Reverse clutch end play:
0.65 - 1.00 mm (0.0256 - 0.0394 in)
+Select proper thickness of thrust washer so that reverse clutch
end play is within specifications.
Thrust washer: Refer to SDS, AT-484.
SAT387D
Assembly (3)NJAT01771. Remove reverse clutch assembly and install needle bearing on
high clutch assembly.
+Pay attention to direction of needle bearing.
2. Install reverse clutch assembly.
ASSEMBLY
Adjustment (2) (Cont'd)
AT-462
Page 695 of 2898
AlignmentNJBT0026+All dimensions indicated in figures are actual ones.
+When using a tracking gauge, adjust both pointers to equal length. Then check the pointers and gauge
itself to make sure there is no free play.
+When a measuring tape is used, check to be sure there is no elongation, twisting or bending.
+Measurements should be taken at the center of the mounting holes.
+An asterisk (*) following the value at the measuring point indicates that the measuring point on the other
side is symmetrically the same value.
+The coordinates of the measurement points are the distances measured from the standard line of ªXº, ªYº
and ªZº.
SBF874GB
BODY (ALIGNMENT)
Alignment
BT-77