Page 529 of 557
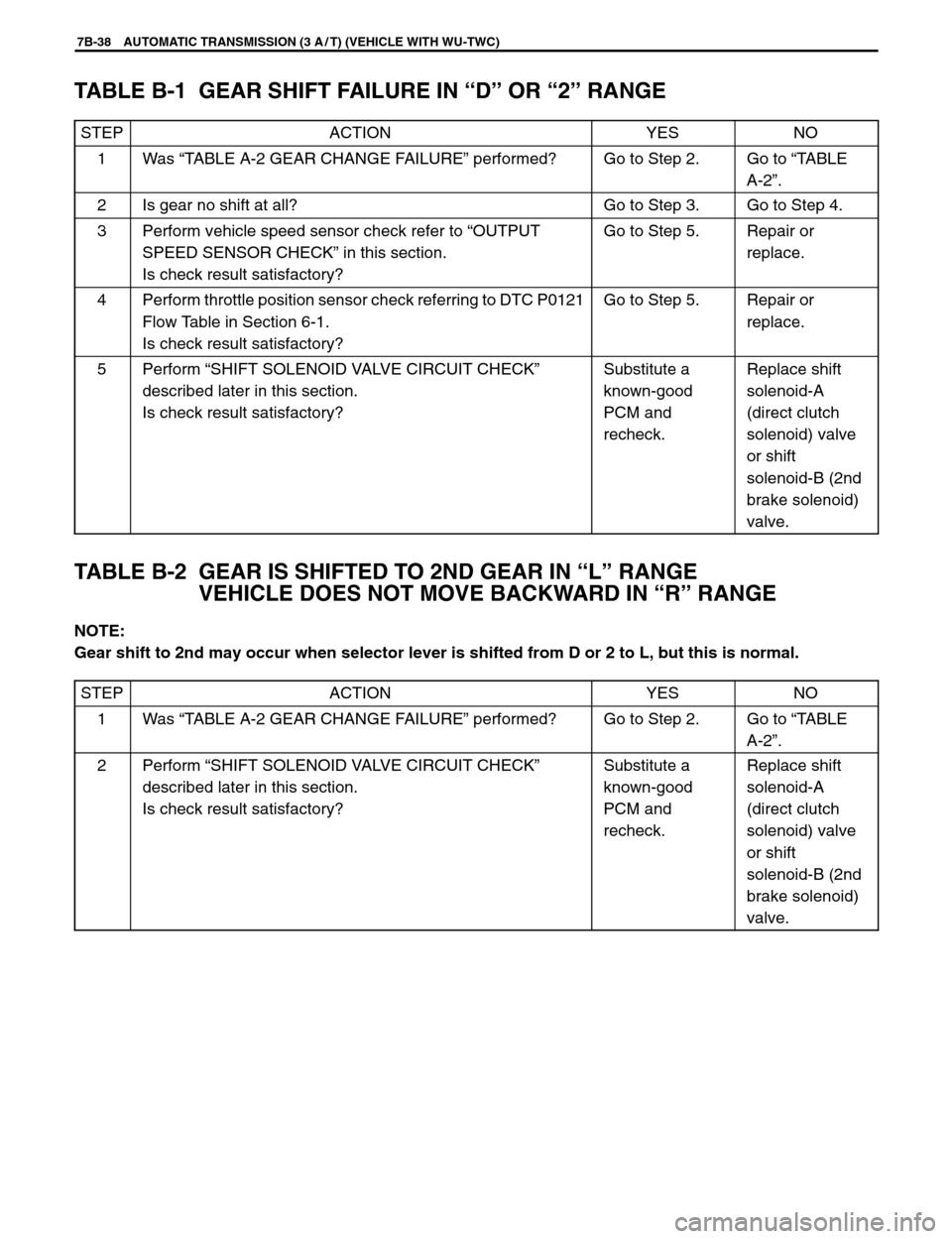
7B-38 AUTOMATIC TRANSMISSION (3 A / T) (VEHICLE WITH WU-TWC)
TABLE B-1 GEAR SHIFT FAILURE IN “D” OR “2” RANGE
STEPACTIONYESNO
1Was “TABLE A-2 GEAR CHANGE FAILURE” performed?Go to Step 2.Go to “TABLE
A-2”.
2Is gear no shift at all?Go to Step 3.Go to Step 4.
3Perform vehicle speed sensor check refer to “OUTPUT
SPEED SENSOR CHECK” in this section.
Is check result satisfactory?Go to Step 5.Repair or
replace.
4Perform throttle position sensor check referring to DTC P0121
Flow Table in Section 6-1.
Is check result satisfactory?Go to Step 5.Repair or
replace.
5Perform “SHIFT SOLENOID VALVE CIRCUIT CHECK”
described later in this section.
Is check result satisfactory?Substitute a
known-good
PCM and
recheck.Replace shift
solenoid-A
(direct clutch
solenoid) valve
or shift
solenoid-B (2nd
brake solenoid)
valve.
TABLE B-2 GEAR IS SHIFTED TO 2ND GEAR IN “L” RANGE
VEHICLE DOES NOT MOVE BACKWARD IN “R” RANGE
NOTE:
Gear shift to 2nd may occur when selector lever is shifted from D or 2 to L, but this is normal.
STEP
ACTIONYESNO
1Was “TABLE A-2 GEAR CHANGE FAILURE” performed?Go to Step 2.Go to “TABLE
A-2”.
2Perform “SHIFT SOLENOID VALVE CIRCUIT CHECK”
described later in this section.
Is check result satisfactory?Substitute a
known-good
PCM and
recheck.Replace shift
solenoid-A
(direct clutch
solenoid) valve
or shift
solenoid-B (2nd
brake solenoid)
valve.
Page 530 of 557
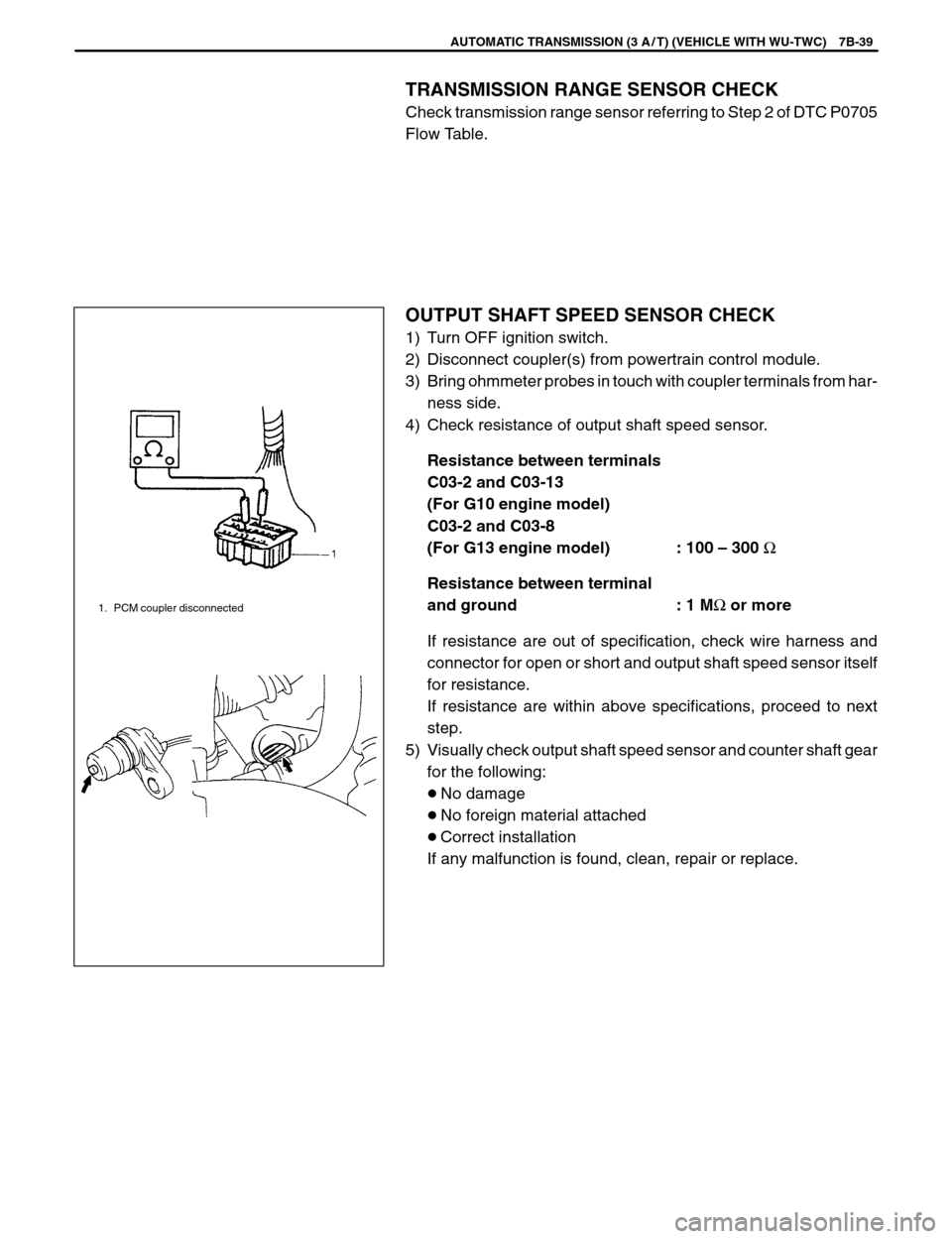
1. PCM coupler disconnected
AUTOMATIC TRANSMISSION (3 A / T) (VEHICLE WITH WU-TWC) 7B-39
TRANSMISSION RANGE SENSOR CHECK
Check transmission range sensor referring to Step 2 of DTC P0705
Flow Table.
OUTPUT SHAFT SPEED SENSOR CHECK
1) Turn OFF ignition switch.
2) Disconnect coupler(s) from powertrain control module.
3) Bring ohmmeter probes in touch with coupler terminals from har-
ness side.
4) Check resistance of output shaft speed sensor.
Resistance between terminals
C03-2 and C03-13
(For G10 engine model)
C03-2 and C03-8
(For G13 engine model) : 100 – 300 Ω
Resistance between terminal
and ground : 1 MΩ or more
If resistance are out of specification, check wire harness and
connector for open or short and output shaft speed sensor itself
for resistance.
If resistance are within above specifications, proceed to next
step.
5) Visually check output shaft speed sensor and counter shaft gear
for the following:
No damage
No foreign material attached
Correct installation
If any malfunction is found, clean, repair or replace.
Page 531 of 557
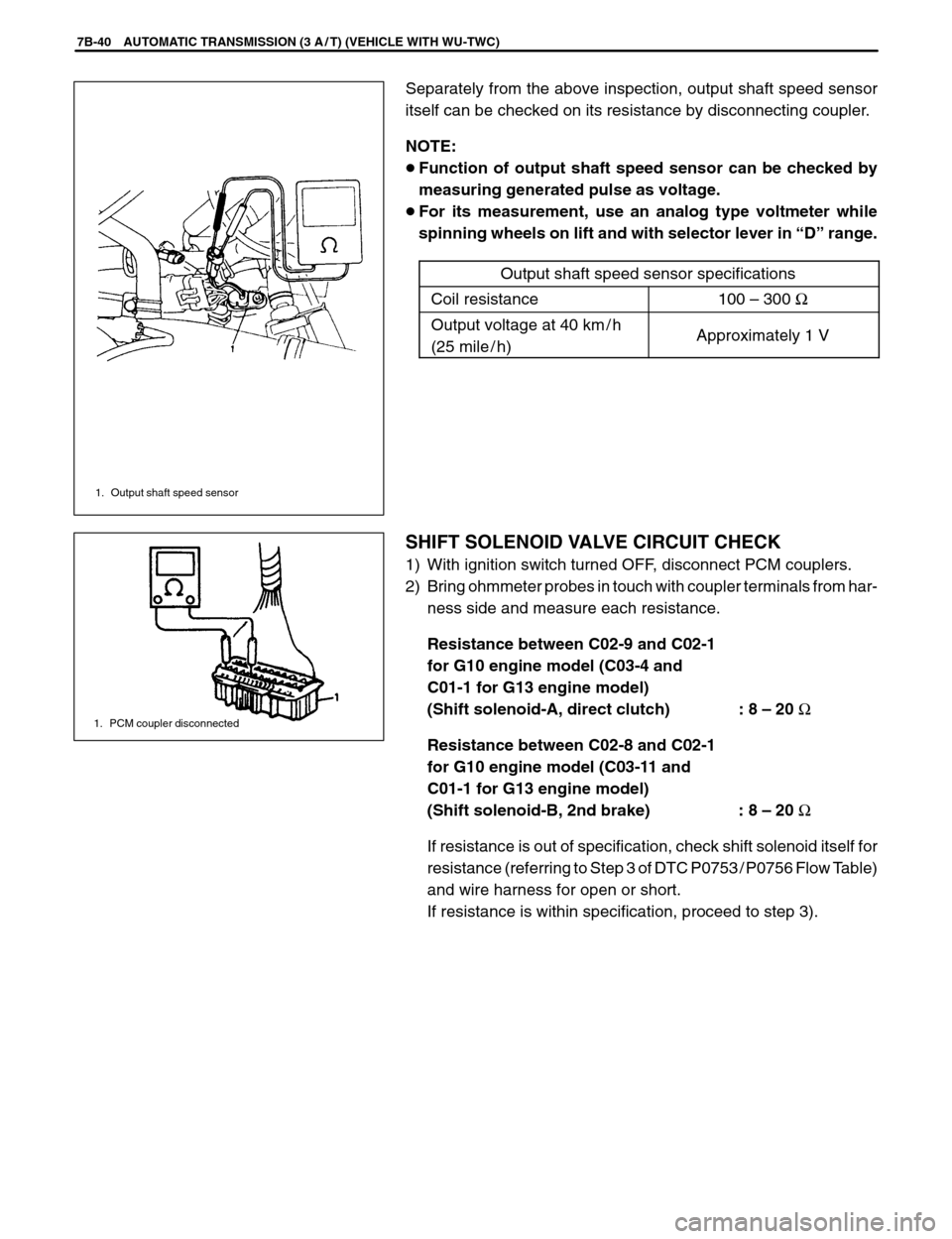
1. Output shaft speed sensor
1. PCM coupler disconnected
7B-40 AUTOMATIC TRANSMISSION (3 A / T) (VEHICLE WITH WU-TWC)
Separately from the above inspection, output shaft speed sensor
itself can be checked on its resistance by disconnecting coupler.
NOTE:
Function of output shaft speed sensor can be checked by
measuring generated pulse as voltage.
For its measurement, use an analog type voltmeter while
spinning wheels on lift and with selector lever in “D” range.
Output shaft speed sensor specifications
Coil resistance100 – 300 Ω
Output voltage at 40 km / h
(25 mile / h)Approximately 1 V
SHIFT SOLENOID VALVE CIRCUIT CHECK
1) With ignition switch turned OFF, disconnect PCM couplers.
2) Bring ohmmeter probes in touch with coupler terminals from har-
ness side and measure each resistance.
Resistance between C02-9 and C02-1
for G10 engine model (C03-4 and
C01-1 for G13 engine model)
(Shift solenoid-A, direct clutch) : 8 – 20 Ω
Resistance between C02-8 and C02-1
for G10 engine model (C03-11 and
C01-1 for G13 engine model)
(Shift solenoid-B, 2nd brake) : 8 – 20 Ω
If resistance is out of specification, check shift solenoid itself for
resistance (referring to Step 3 of DTC P0753 / P0756 Flow Table)
and wire harness for open or short.
If resistance is within specification, proceed to step 3).
Page 532 of 557
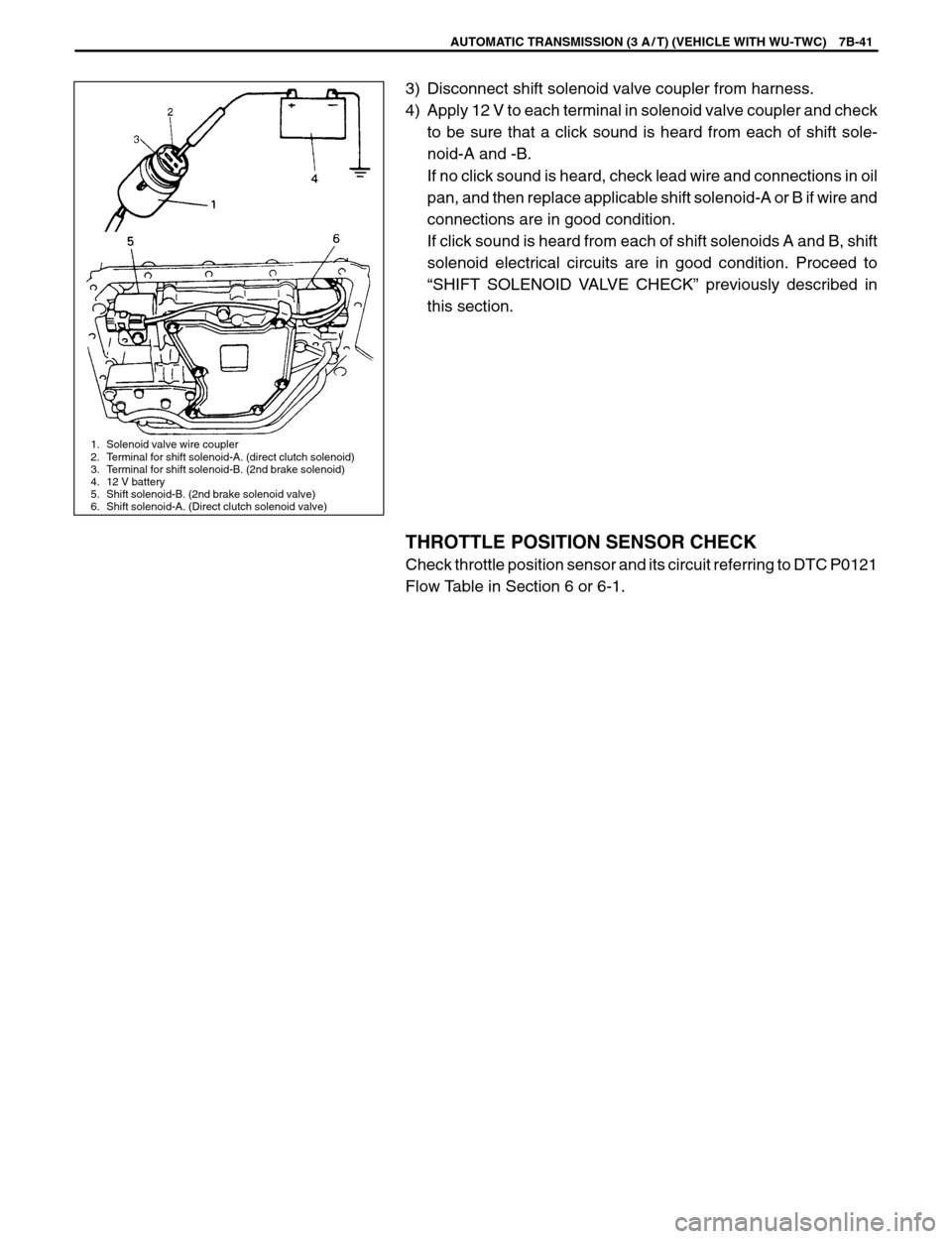
1. Solenoid valve wire coupler
2. Terminal for shift solenoid-A. (direct clutch solenoid)
3. Terminal for shift solenoid-B. (2nd brake solenoid)
4. 12 V battery
5. Shift solenoid-B. (2nd brake solenoid valve)
6. Shift solenoid-A. (Direct clutch solenoid valve)
AUTOMATIC TRANSMISSION (3 A / T) (VEHICLE WITH WU-TWC) 7B-41
3) Disconnect shift solenoid valve coupler from harness.
4) Apply 12 V to each terminal in solenoid valve coupler and check
to be sure that a click sound is heard from each of shift sole-
noid-A and -B.
If no click sound is heard, check lead wire and connections in oil
pan, and then replace applicable shift solenoid-A or B if wire and
connections are in good condition.
If click sound is heard from each of shift solenoids A and B, shift
solenoid electrical circuits are in good condition. Proceed to
“SHIFT SOLENOID VALVE CHECK” previously described in
this section.
THROTTLE POSITION SENSOR CHECK
Check throttle position sensor and its circuit referring to DTC P0121
Flow Table in Section 6 or 6-1.
Page 533 of 557
7B-42 AUTOMATIC TRANSMISSION (3 A / T) (VEHICLE WITH WU-TWC)
TIGHTENING TORQUE SPECIFICATIONS
Refer to the same section of the service manual mentioned in the “FOREWORD” of this manual.
SPECIAL TOOLS
Refer to the same section of the service manual mentioned in the “FOREWORD” of this manual.
Page 534 of 557
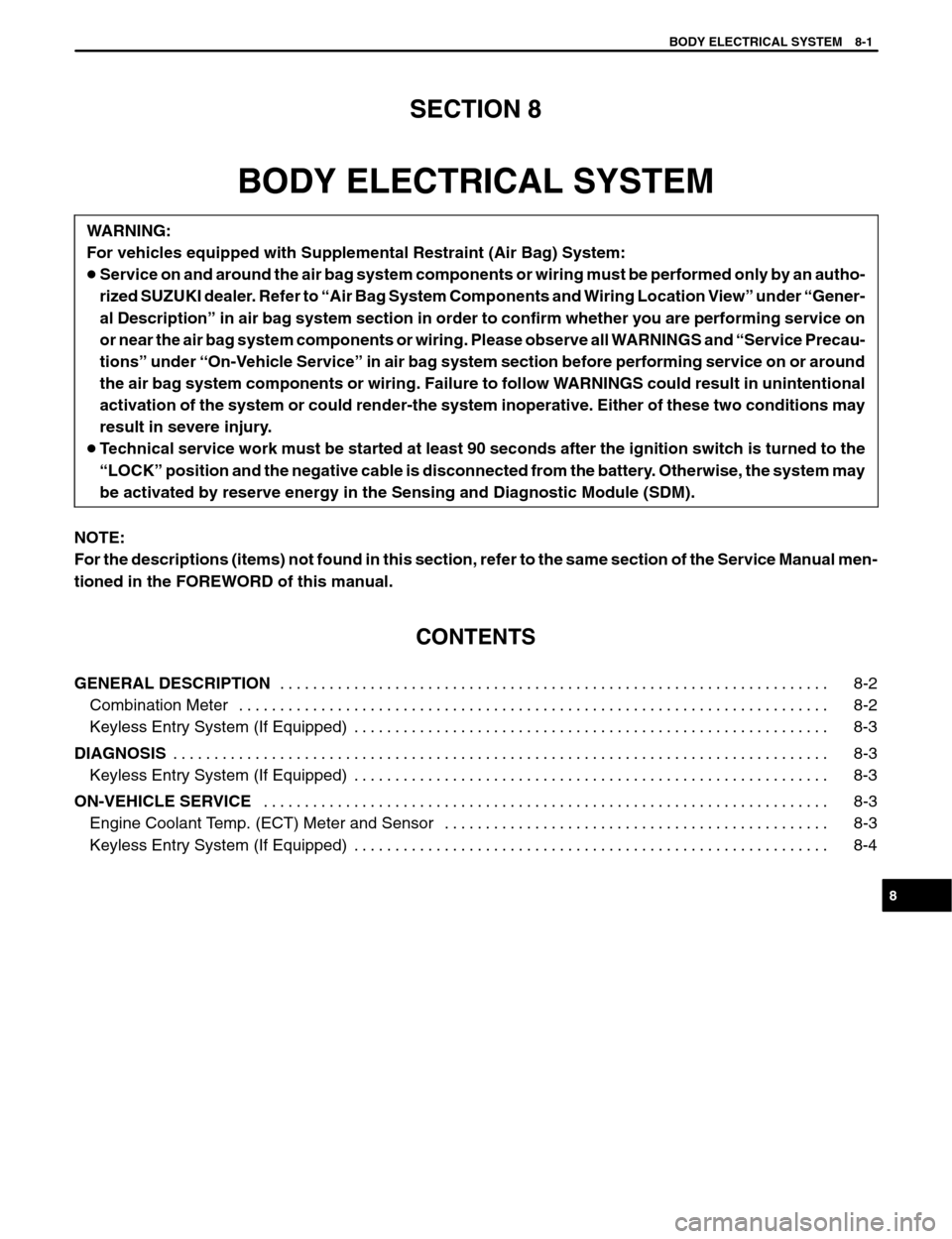
8
BODY ELECTRICAL SYSTEM 8-1
SECTION 8
BODY ELECTRICAL SYSTEM
WARNING:
For vehicles equipped with Supplemental Restraint (Air Bag) System:
Service on and around the air bag system components or wiring must be performed only by an autho-
rized SUZUKI dealer. Refer to “Air Bag System Components and Wiring Location View” under “Gener-
al Description” in air bag system section in order to confirm whether you are performing service on
or near the air bag system components or wiring. Please observe all WARNINGS and “Service Precau-
tions” under “On-Vehicle Service” in air bag system section before performing service on or around
the air bag system components or wiring. Failure to follow WARNINGS could result in unintentional
activation of the system or could render-the system inoperative. Either of these two conditions may
result in severe injury.
Technical service work must be started at least 90 seconds after the ignition switch is turned to the
“LOCK” position and the negative cable is disconnected from the battery. Otherwise, the system may
be activated by reserve energy in the Sensing and Diagnostic Module (SDM).
NOTE:
For the descriptions (items) not found in this section, refer to the same section of the Service Manual men-
tioned in the FOREWORD of this manual.
CONTENTS
GENERAL DESCRIPTION8-2 . . . . . . . . . . . . . . . . . . . . . . . . . . . . . . . . . . . . . . . . . . . . . . . . . . . . . . . . . . . . . . . . . . .
Combination Meter8-2 . . . . . . . . . . . . . . . . . . . . . . . . . . . . . . . . . . . . . . . . . . . . . . . . . . . . . . . . . . . . . . . . . . . . . . . .
Keyless Entry System (If Equipped) 8-3. . . . . . . . . . . . . . . . . . . . . . . . . . . . . . . . . . . . . . . . . . . . . . . . . . . . . . . . . .
DIAGNOSIS8-3 . . . . . . . . . . . . . . . . . . . . . . . . . . . . . . . . . . . . . . . . . . . . . . . . . . . . . . . . . . . . . . . . . . . . . . . . . . . . . . . .
Keyless Entry System (If Equipped) 8-3. . . . . . . . . . . . . . . . . . . . . . . . . . . . . . . . . . . . . . . . . . . . . . . . . . . . . . . . . .
ON-VEHICLE SERVICE8-3 . . . . . . . . . . . . . . . . . . . . . . . . . . . . . . . . . . . . . . . . . . . . . . . . . . . . . . . . . . . . . . . . . . . . .
Engine Coolant Temp. (ECT) Meter and Sensor 8-3. . . . . . . . . . . . . . . . . . . . . . . . . . . . . . . . . . . . . . . . . . . . . . .
Keyless Entry System (If Equipped) 8-4. . . . . . . . . . . . . . . . . . . . . . . . . . . . . . . . . . . . . . . . . . . . . . . . . . . . . . . . . .
Page 535 of 557
NOTE:
Terminal arrangement of coupler viewed from harness side.
Coupler A
1. To generator W / R
2. To ignition switch B / W
3. To ECM V / G
4. To ECM V
5. Blank –
6. To ECT sensor Y / W
7. Blank —
8. To engine oil pressure switch Y / B
9. To ECM Br
10. Blank —
11. To SDM (if equipped) Bl
12. Blank —
13. Blank —
14. Blank —
15. To ground R
16. To combination switch R / Y
Coupler B
1. To combination switch G / R
2. Blank —
3. Blank —
4. To ECM Y / G
5. To brake fluid level switch and R / B
parking brake switch
6. Blank —
7. To ABS control module R / Bl
(if equipped)
8. Blank —
9. To fuel level gauge Y / R
10. To ground B / Bl
11. To ignition switch B / W
12. Blank —
13. Blank —
Coupler C
1. Blank —
2. Blank —
3. Blank —
4. Blank —
5. Blank —
6. Blank —
7. To main fuse R
8. To combination switch W / Bl
9. To ground B
10. To combination switch G / Y
Coupler A Coupler B Coupler C
8-2 BODY ELECTRICAL SYSTEM
GENERAL DESCRIPTION
COMBINATION METER
Page 536 of 557
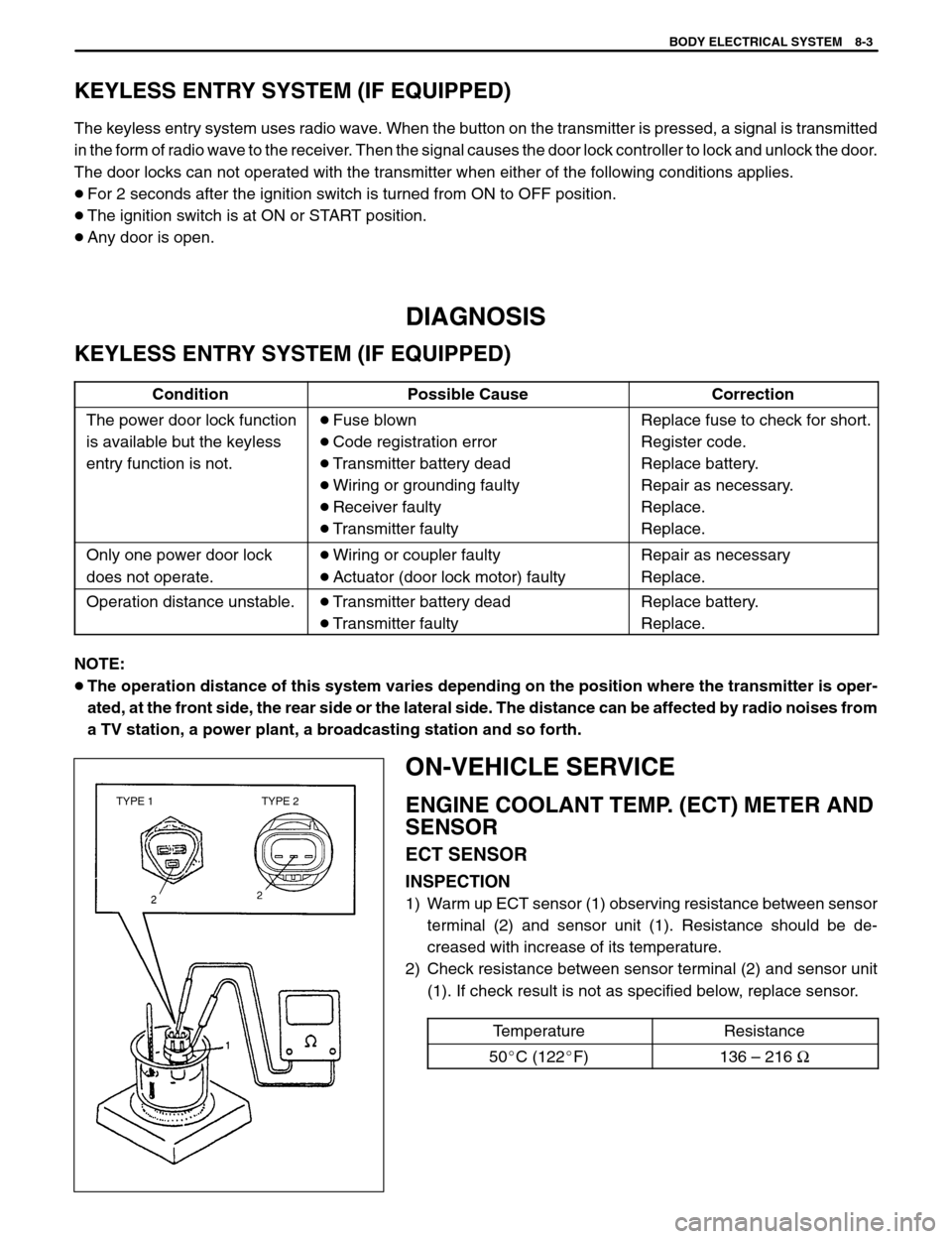
TYPE 1 TYPE 2
BODY ELECTRICAL SYSTEM 8-3
KEYLESS ENTRY SYSTEM (IF EQUIPPED)
The keyless entry system uses radio wave. When the button on the transmitter is pressed, a signal is transmitted
in the form of radio wave to the receiver. Then the signal causes the door lock controller to lock and unlock the door.
The door locks can not operated with the transmitter when either of the following conditions applies.
For 2 seconds after the ignition switch is turned from ON to OFF position.
The ignition switch is at ON or START position.
Any door is open.
DIAGNOSIS
KEYLESS ENTRY SYSTEM (IF EQUIPPED)
ConditionPossible CauseCorrection
The power door lock function
is available but the keyless
entry function is not.Fuse blown
Code registration error
Transmitter battery dead
Wiring or grounding faulty
Receiver faulty
Transmitter faultyReplace fuse to check for short.
Register code.
Replace battery.
Repair as necessary.
Replace.
Replace.
Only one power door lock
does not operate.Wiring or coupler faulty
Actuator (door lock motor) faultyRepair as necessary
Replace.
Operation distance unstable.Transmitter battery dead
Transmitter faultyReplace battery.
Replace.
NOTE:
The operation distance of this system varies depending on the position where the transmitter is oper-
ated, at the front side, the rear side or the lateral side. The distance can be affected by radio noises from
a TV station, a power plant, a broadcasting station and so forth.
ON-VEHICLE SERVICE
ENGINE COOLANT TEMP. (ECT) METER AND
SENSOR
ECT SENSOR
INSPECTION
1) Warm up ECT sensor (1) observing resistance between sensor
terminal (2) and sensor unit (1). Resistance should be de-
creased with increase of its temperature.
2) Check resistance between sensor terminal (2) and sensor unit
(1). If check result is not as specified below, replace sensor.
Temperature
Resistance
50C (122F)136 – 216 Ω