Page 305 of 557
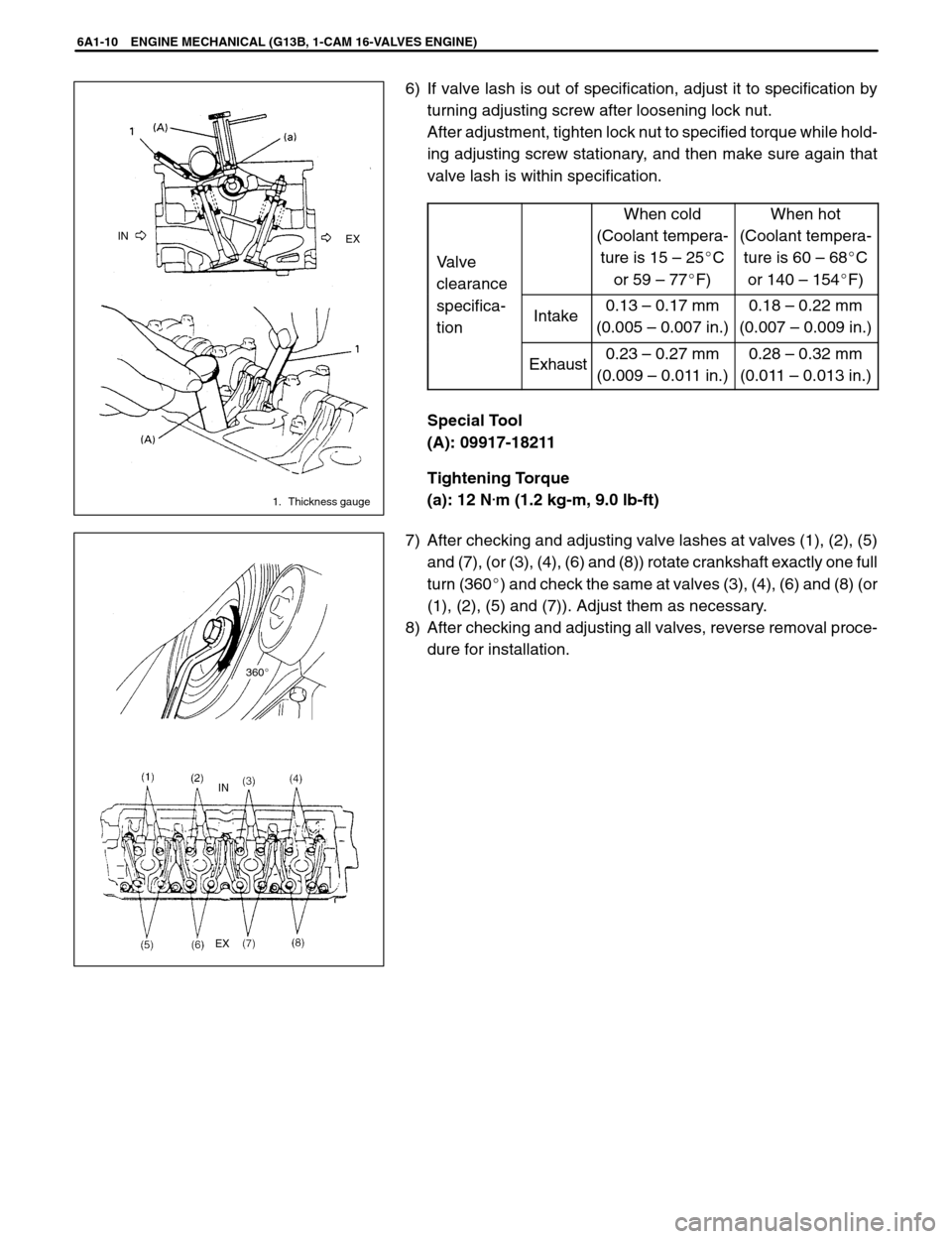
1. Thickness gauge IN
EX
360
IN
EX
6A1-10 ENGINE MECHANICAL (G13B, 1-CAM 16-VALVES ENGINE)
6) If valve lash is out of specification, adjust it to specification by
turning adjusting screw after loosening lock nut.
After adjustment, tighten lock nut to specified torque while hold-
ing adjusting screw stationary, and then make sure again that
valve lash is within specification.
Valve
clearance
When cold
(Coolant tempera-
ture is 15 – 25C
or 59 – 77F)When hot
(Coolant tempera-
ture is 60 – 68C
or 140 – 154F)
specifica-
tionIntake0.13 – 0.17 mm
(0.005 – 0.007 in.)0.18 – 0.22 mm
(0.007 – 0.009 in.)
Exhaust0.23 – 0.27 mm
(0.009 – 0.011 in.)0.28 – 0.32 mm
(0.011 – 0.013 in.)
Special Tool
(A): 09917-18211
Tightening Torque
(a): 12 N
.m (1.2 kg-m, 9.0 lb-ft)
7) After checking and adjusting valve lashes at valves (1), (2), (5)
and (7), (or (3), (4), (6) and (8)) rotate crankshaft exactly one full
turn (360) and check the same at valves (3), (4), (6) and (8) (or
(1), (2), (5) and (7)). Adjust them as necessary.
8) After checking and adjusting all valves, reverse removal proce-
dure for installation.
Page 306 of 557
3
ENGINE MECHANICAL (G13B, 1-CAM 16-VALVES ENGINE) 6A1-11
AIR CLEANER ELEMENT
REMOVAL
1) Disconnect air cleaner outlet hose from case after loosening its
clamp (2) and removing bolt (1) shown in figure.
2) Remove air cleaner cap (3) from case by unhooking its clamps,
then take out air cleaner element.
INSPECTION
Check air cleaner element for dirt. Replace excessively dirty ele-
ment.
CLEAN
Blow off dust by compressed air from air outlet side of element.
INSTALLATION
Reverse removal procedure for installation.
Page 307 of 557
6A1-12 ENGINE MECHANICAL (G13B, 1-CAM 16-VALVES ENGINE)
AIR CLEANER OUTLET HOSE
REMOVAL
1) Disconnect negative cable at battery.
2) Disconnect resonator after loosening its clamp.
3) Disconnect breather hose from air cleaner outlet hose.
4) Disconnect IAT sensor wire at coupler.
5) Remove bolt and then air cleaner outlet hose after loosening its
clamps.
INSTALLATION
Reverse removal procedure for installation, noting the following.
Clamp each hose securely.
Page 308 of 557
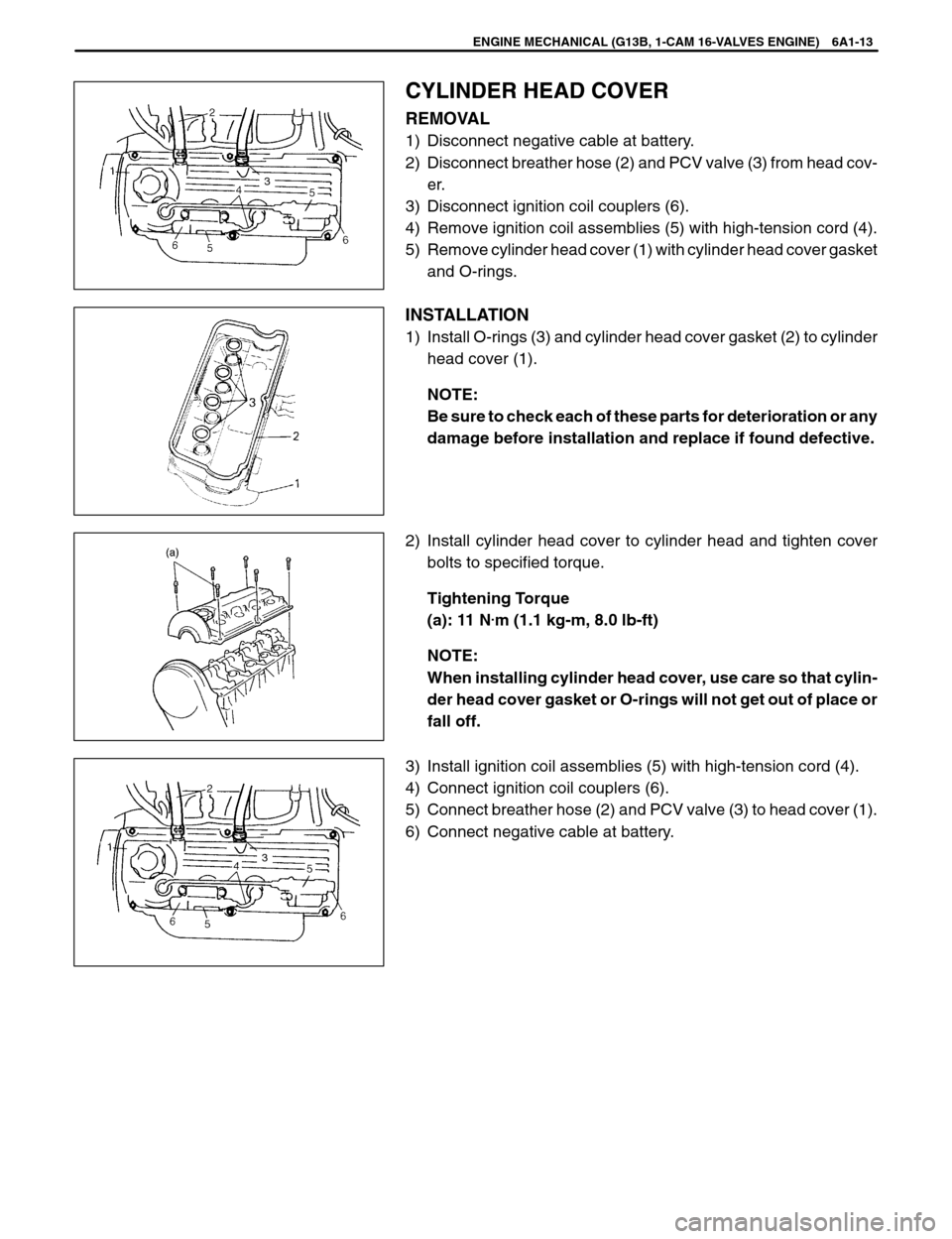
3
3
ENGINE MECHANICAL (G13B, 1-CAM 16-VALVES ENGINE) 6A1-13
CYLINDER HEAD COVER
REMOVAL
1) Disconnect negative cable at battery.
2) Disconnect breather hose (2) and PCV valve (3) from head cov-
er.
3) Disconnect ignition coil couplers (6).
4) Remove ignition coil assemblies (5) with high-tension cord (4).
5) Remove cylinder head cover (1) with cylinder head cover gasket
and O-rings.
INSTALLATION
1) Install O-rings (3) and cylinder head cover gasket (2) to cylinder
head cover (1).
NOTE:
Be sure to check each of these parts for deterioration or any
damage before installation and replace if found defective.
2) Install cylinder head cover to cylinder head and tighten cover
bolts to specified torque.
Tightening Torque
(a): 11 N
.m (1.1 kg-m, 8.0 lb-ft)
NOTE:
When installing cylinder head cover, use care so that cylin-
der head cover gasket or O-rings will not get out of place or
fall off.
3) Install ignition coil assemblies (5) with high-tension cord (4).
4) Connect ignition coil couplers (6).
5) Connect breather hose (2) and PCV valve (3) to head cover (1).
6) Connect negative cable at battery.
Page 309 of 557
1. Intake manifold
2. Throttle body
3. Gasket
4. EGR valve
5. Fuel delivery pipe
6. Fuel injector7. Fuel pressure regulator
8. EVAP canister purge valve
9. MAP sensor
10. O-ring
11. Gasket
12. Cushion : Tightening Torque
: Do not reuse
1
2
6A1-14 ENGINE MECHANICAL (G13B, 1-CAM 16-VALVES ENGINE)
THROTTLE BODY AND INTAKE MANIFOLD
REMOVAL
1) Relieve fuel pressure according to procedure described in Sec-
tion 6.
2) Disconnect negative cable at battery.
3) Drain cooling system.
WARNING:
To help avoid danger of being burned, do not remove
drain plug (2) and radiator cap while engine and radiator
(1) are still hot. Scalding fluid and steam can be blown out
under pressure if plug and cap are taken off too soon.
4) Disconnect IAT sensor at coupler.
5) Remove air cleaner outlet hose (2) with resonator.
6) Disconnect accelerator cable (1) from throttle body.
Page 310 of 557
ENGINE MECHANICAL (G13B, 1-CAM 16-VALVES ENGINE) 6A1-15
7) Disconnect the following electric lead wires and release clamp:
Ground wires (5) from intake manifold
TP sensor (3)
IAC valve (4)
Fuel injectors
EVAP canister purge valve (2)
MAP sensor (6)
EGR valve (1)
8) Disconnect the following hoses:
Brake booster hose (1) from intake manifold
Canister purge hose (3) from EVAP canister purge valve
Engine cooling water (coolant) hose (2) from IAC valve
PCV hose (4)
Breather hose from cylinder head
9) Disconnect fuel feed hose (2) from pipe (1), and disconnect fuel
return hose (3) from fuel pressure regulator.
Page 311 of 557
1. Long bolt
2. Short bolt
6A1-16 ENGINE MECHANICAL (G13B, 1-CAM 16-VALVES ENGINE)
10) Remove intake manifold rear stiffener (1) and generator adjust
arm reinforcement (2) from intake manifold (3).
11) Remove intake manifold with throttle body from cylinder head,
and then its gasket.
INSTALLATION
Reverse removal procedure for installation noting the followings.
Use new intake manifold gasket.
When installing intake manifold, install clamps securely.
Tightening Torque
(a): 23 N
.m (2.3 kg-m, 17.0 lb-ft)
Adjust accelerator cable play, referring to Section 6E.
Check to ensure that all removed parts are back in place.
Reinstall any necessary parts which have not been reinstalled.
Refill cooling system referring to Section 6B.
Upon completion of installation, turn ignition switch ON but en-
gine OFF and check for fuel leaks.
Finally, start engine and check for engine coolant leaks.
Page 312 of 557
: Tightening Torque
: Do not reuse
1. Exhaust manifold
2. Gasket
3. Cover
4. Heated oxygen sensor
7. Gasket
8. Exhaust No.1 pipe.
21
ENGINE MECHANICAL (G13B, 1-CAM 16-VALVES ENGINE) 6A1-17
EXHAUST MANIFOLD
WARNING:
To avoid danger of being burned, do not service exhaust
system while it is still hot.
Service should be performed after system cools down.
REMOVAL
1) Disconnect negative cable at battery.
2) Disconnect heated oxygen sensor coupler.
Release its wire from clamps.
3) Disconnect exhaust No.1 pipe (1) from WU-TWC.
4) Remove WU-TWC stiffener (2) (if equipped).
5) Remove exhaust manifold (1) and its gasket from cylinder head.