Page 473 of 557
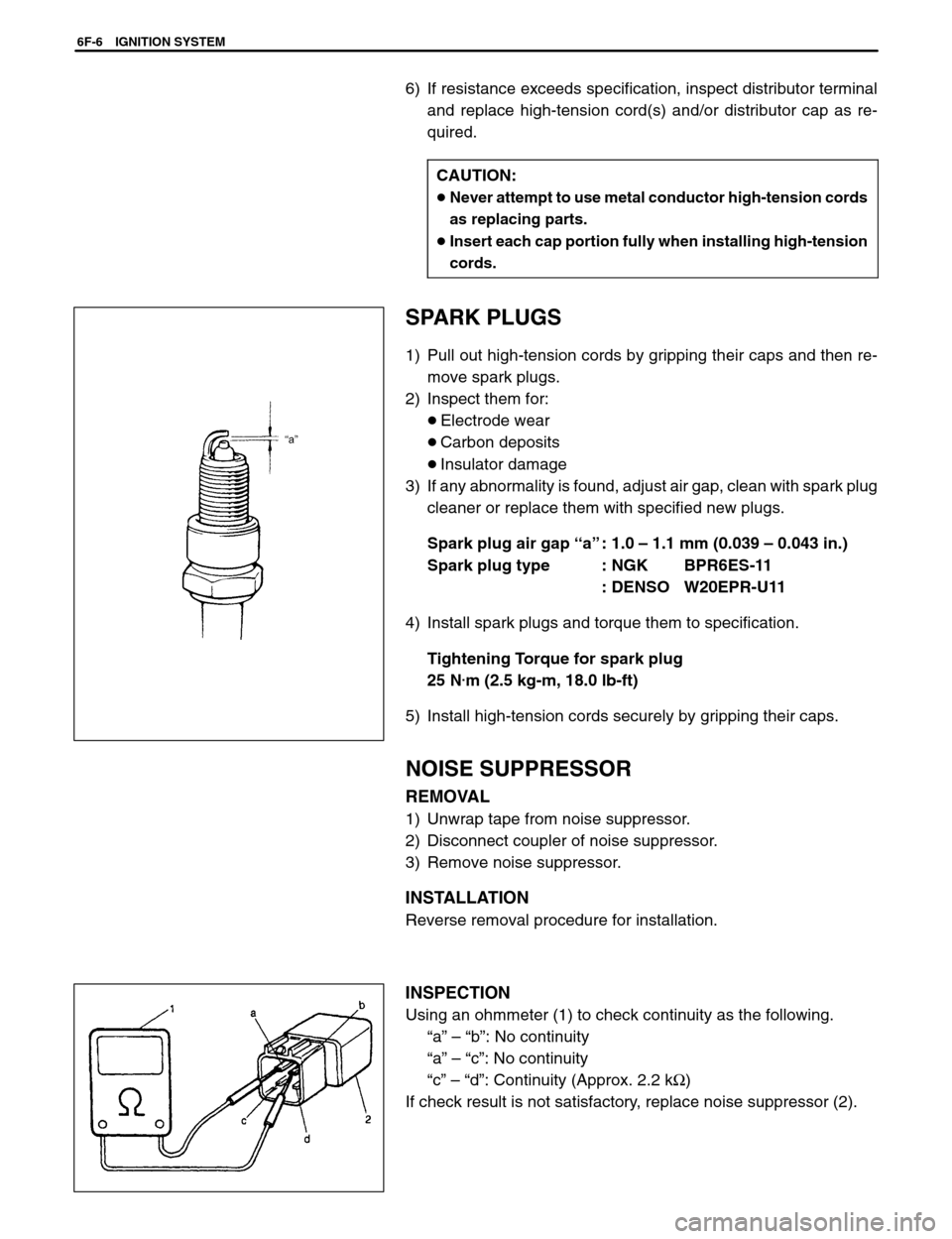
6F-6 IGNITION SYSTEM
6) If resistance exceeds specification, inspect distributor terminal
and replace high-tension cord(s) and/or distributor cap as re-
quired.
CAUTION:
Never attempt to use metal conductor high-tension cords
as replacing parts.
Insert each cap portion fully when installing high-tension
cords.
SPARK PLUGS
1) Pull out high-tension cords by gripping their caps and then re-
move spark plugs.
2) Inspect them for:
Electrode wear
Carbon deposits
Insulator damage
3) If any abnormality is found, adjust air gap, clean with spark plug
cleaner or replace them with specified new plugs.
Spark plug air gap “a’’: 1.0 – 1.1 mm (0.039 – 0.043 in.)
Spark plug type : NGK BPR6ES-11
: DENSO W20EPR-U11
4) Install spark plugs and torque them to specification.
Tightening Torque for spark plug
25 N
.m (2.5 kg-m, 18.0 lb-ft)
5) Install high-tension cords securely by gripping their caps.
NOISE SUPPRESSOR
REMOVAL
1) Unwrap tape from noise suppressor.
2) Disconnect coupler of noise suppressor.
3) Remove noise suppressor.
INSTALLATION
Reverse removal procedure for installation.
INSPECTION
Using an ohmmeter (1) to check continuity as the following.
“a” – “b”: No continuity
“a” – “c”: No continuity
“c” – “d”: Continuity (Approx. 2.2 kΩ)
If check result is not satisfactory, replace noise suppressor (2).
Page 474 of 557
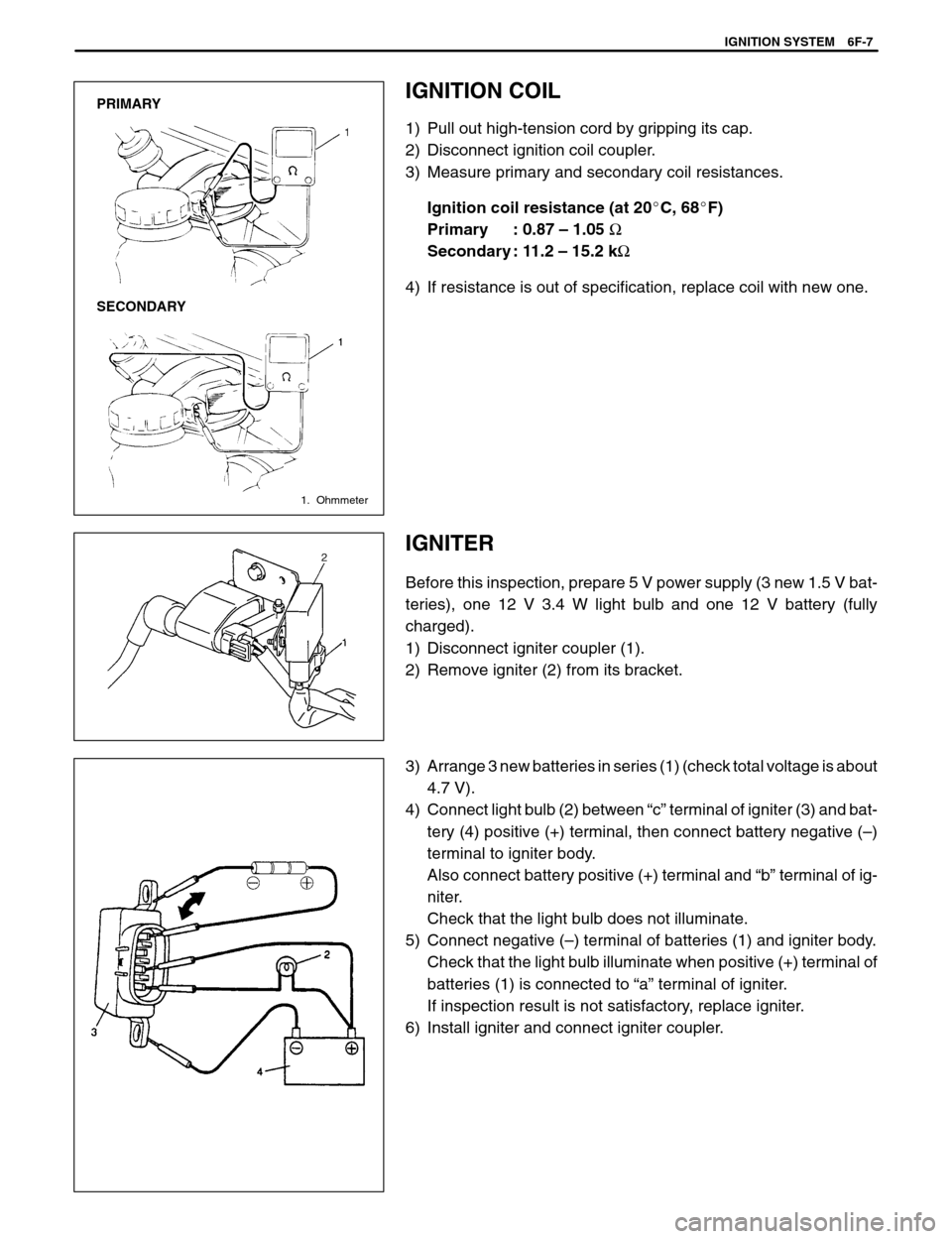
PRIMARY
SECONDARY
1. Ohmmeter
IGNITION SYSTEM 6F-7
IGNITION COIL
1) Pull out high-tension cord by gripping its cap.
2) Disconnect ignition coil coupler.
3) Measure primary and secondary coil resistances.
Ignition coil resistance (at 20C, 68F)
Primary : 0.87 – 1.05 Ω
Secondary : 11.2 – 15.2 kΩ
4) If resistance is out of specification, replace coil with new one.
IGNITER
Before this inspection, prepare 5 V power supply (3 new 1.5 V bat-
teries), one 12 V 3.4 W light bulb and one 12 V battery (fully
charged).
1) Disconnect igniter coupler (1).
2) Remove igniter (2) from its bracket.
3) Arrange 3 new batteries in series (1) (check total voltage is about
4.7 V).
4) Connect light bulb (2) between “c” terminal of igniter (3) and bat-
tery (4) positive (+) terminal, then connect battery negative (–)
terminal to igniter body.
Also connect battery positive (+) terminal and “b” terminal of ig-
niter.
Check that the light bulb does not illuminate.
5) Connect negative (–) terminal of batteries (1) and igniter body.
Check that the light bulb illuminate when positive (+) terminal of
batteries (1) is connected to “a” terminal of igniter.
If inspection result is not satisfactory, replace igniter.
6) Install igniter and connect igniter coupler.
Page 475 of 557
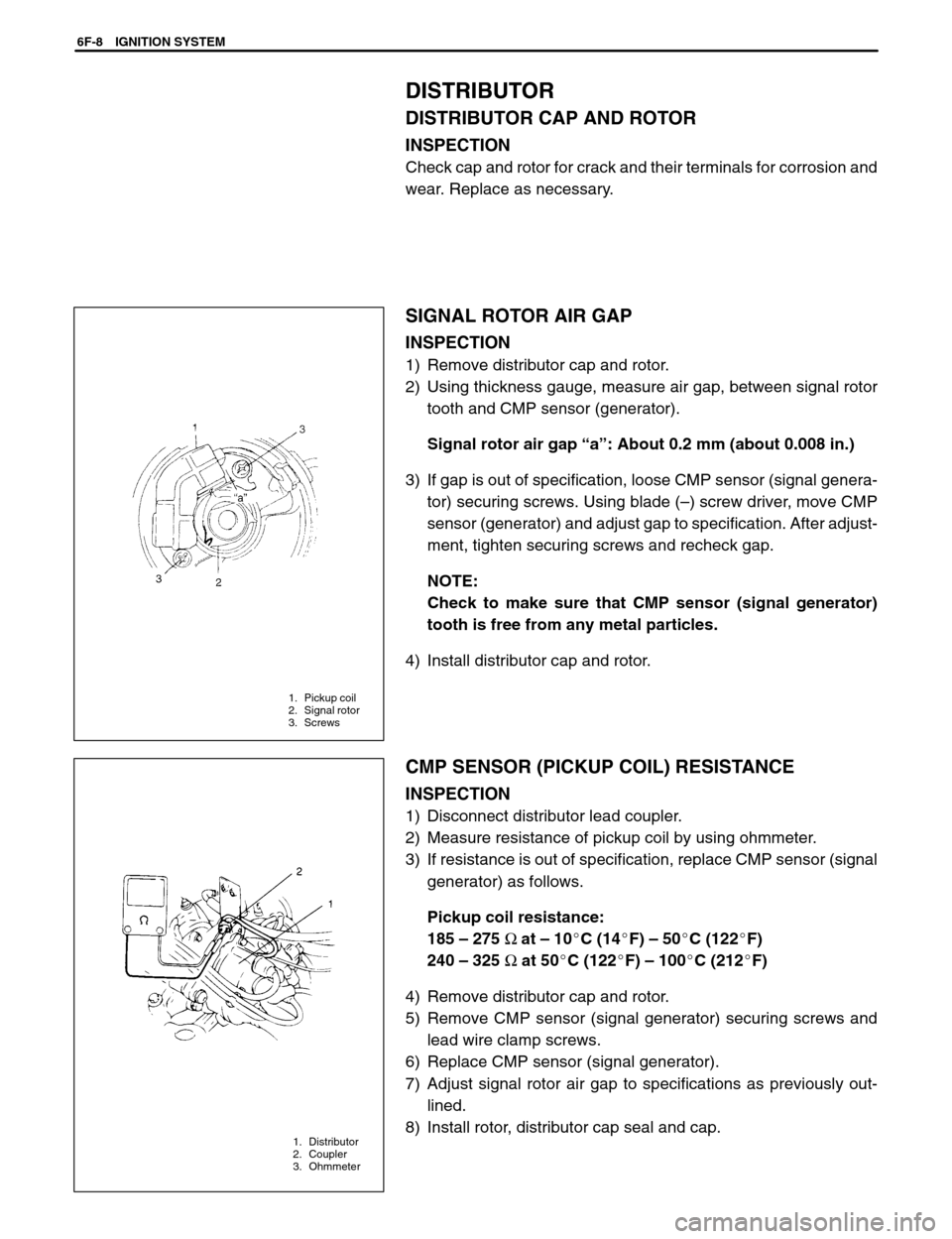
1. Pickup coil
2. Signal rotor
3. Screws
1. Distributor
2. Coupler
3. Ohmmeter
6F-8 IGNITION SYSTEM
DISTRIBUTOR
DISTRIBUTOR CAP AND ROTOR
INSPECTION
Check cap and rotor for crack and their terminals for corrosion and
wear. Replace as necessary.
SIGNAL ROTOR AIR GAP
INSPECTION
1) Remove distributor cap and rotor.
2) Using thickness gauge, measure air gap, between signal rotor
tooth and CMP sensor (generator).
Signal rotor air gap “a”: About 0.2 mm (about 0.008 in.)
3) If gap is out of specification, loose CMP sensor (signal genera-
tor) securing screws. Using blade (–) screw driver, move CMP
sensor (generator) and adjust gap to specification. After adjust-
ment, tighten securing screws and recheck gap.
NOTE:
Check to make sure that CMP sensor (signal generator)
tooth is free from any metal particles.
4) Install distributor cap and rotor.
CMP SENSOR (PICKUP COIL) RESISTANCE
INSPECTION
1) Disconnect distributor lead coupler.
2) Measure resistance of pickup coil by using ohmmeter.
3) If resistance is out of specification, replace CMP sensor (signal
generator) as follows.
Pickup coil resistance:
185 – 275 Ω at – 10C (14F) – 50C (122F)
240 – 325 Ω at 50C (122F) – 100C (212F)
4) Remove distributor cap and rotor.
5) Remove CMP sensor (signal generator) securing screws and
lead wire clamp screws.
6) Replace CMP sensor (signal generator).
7) Adjust signal rotor air gap to specifications as previously out-
lined.
8) Install rotor, distributor cap seal and cap.
Page 476 of 557
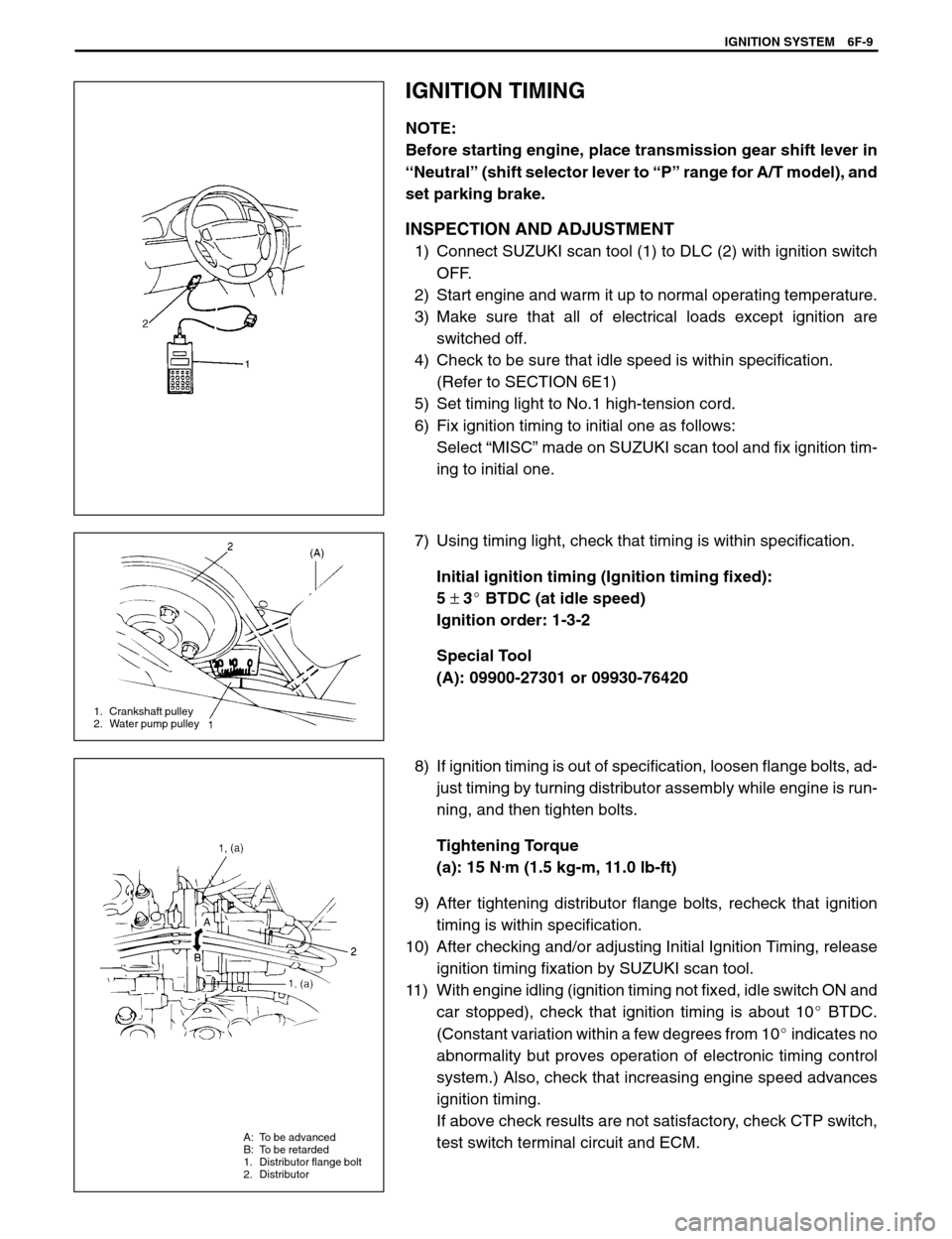
1. Crankshaft pulley
2. Water pump pulley
A: To be advanced
B: To be retarded
1. Distributor flange bolt
2. Distributor
IGNITION SYSTEM 6F-9
IGNITION TIMING
NOTE:
Before starting engine, place transmission gear shift lever in
“Neutral” (shift selector lever to “P” range for A/T model), and
set parking brake.
INSPECTION AND ADJUSTMENT
1) Connect SUZUKI scan tool (1) to DLC (2) with ignition switch
OFF.
2) Start engine and warm it up to normal operating temperature.
3) Make sure that all of electrical loads except ignition are
switched off.
4) Check to be sure that idle speed is within specification.
(Refer to SECTION 6E1)
5) Set timing light to No.1 high-tension cord.
6) Fix ignition timing to initial one as follows:
Select “MISC” made on SUZUKI scan tool and fix ignition tim-
ing to initial one.
7) Using timing light, check that timing is within specification.
Initial ignition timing (Ignition timing fixed):
5 ±3 BTDC (at idle speed)
Ignition order: 1-3-2
Special Tool
(A): 09900-27301 or 09930-76420
8) If ignition timing is out of specification, loosen flange bolts, ad-
just timing by turning distributor assembly while engine is run-
ning, and then tighten bolts.
Tightening Torque
(a): 15 N
.m (1.5 kg-m, 11.0 lb-ft)
9) After tightening distributor flange bolts, recheck that ignition
timing is within specification.
10) After checking and/or adjusting Initial Ignition Timing, release
ignition timing fixation by SUZUKI scan tool.
11) With engine idling (ignition timing not fixed, idle switch ON and
car stopped), check that ignition timing is about 10 BTDC.
(Constant variation within a few degrees from 10 indicates no
abnormality but proves operation of electronic timing control
system.) Also, check that increasing engine speed advances
ignition timing.
If above check results are not satisfactory, check CTP switch,
test switch terminal circuit and ECM.
Page 477 of 557
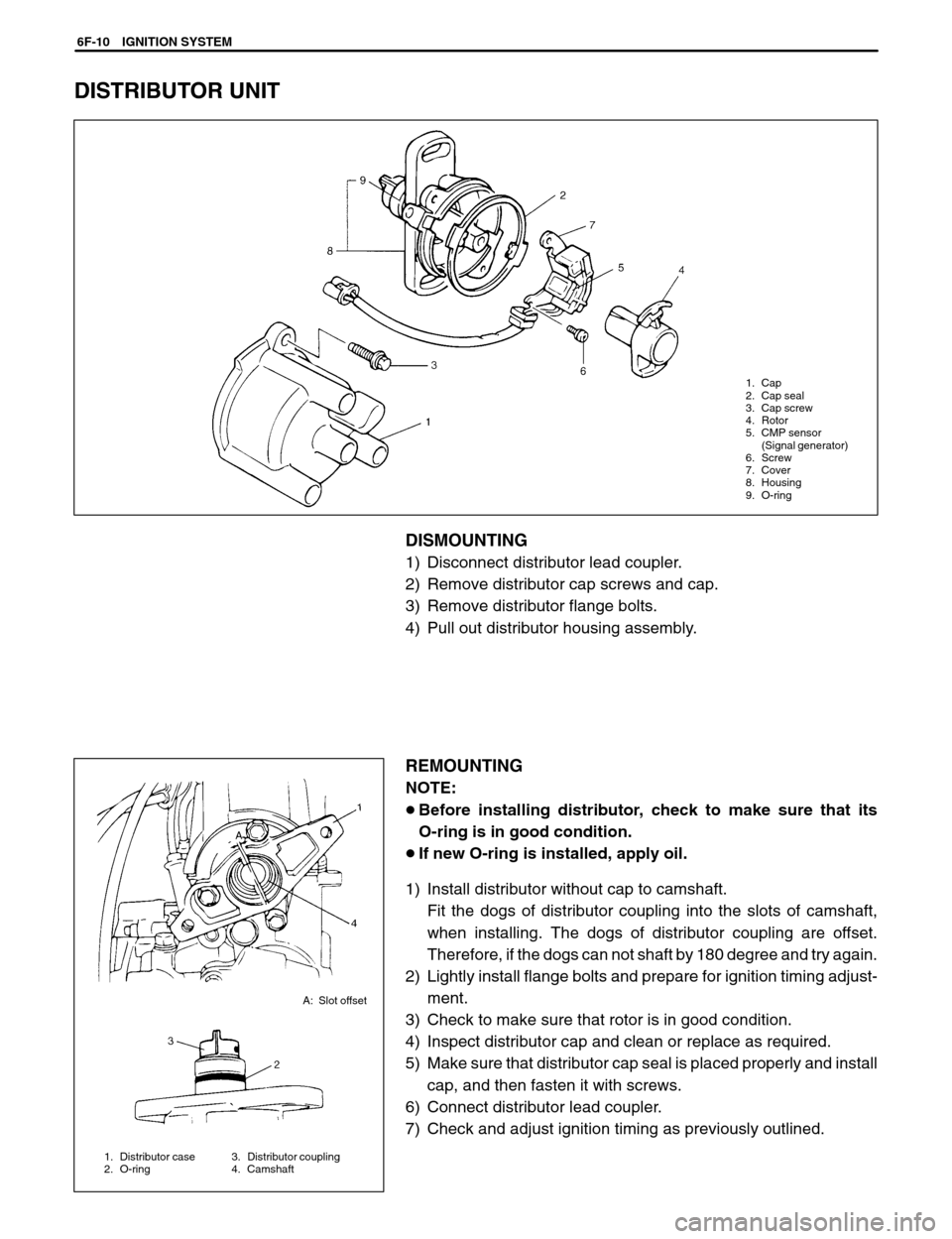
1. Cap
2. Cap seal
3. Cap screw
4. Rotor
5. CMP sensor
(Signal generator)
6. Screw
7. Cover
8. Housing
9. O-ring
A: Slot offset
1. Distributor case
2. O-ring3. Distributor coupling
4. Camshaft
6F-10 IGNITION SYSTEM
DISTRIBUTOR UNIT
DISMOUNTING
1) Disconnect distributor lead coupler.
2) Remove distributor cap screws and cap.
3) Remove distributor flange bolts.
4) Pull out distributor housing assembly.
REMOUNTING
NOTE:
Before installing distributor, check to make sure that its
O-ring is in good condition.
If new O-ring is installed, apply oil.
1) Install distributor without cap to camshaft.
Fit the dogs of distributor coupling into the slots of camshaft,
when installing. The dogs of distributor coupling are offset.
Therefore, if the dogs can not shaft by 180 degree and try again.
2) Lightly install flange bolts and prepare for ignition timing adjust-
ment.
3) Check to make sure that rotor is in good condition.
4) Inspect distributor cap and clean or replace as required.
5) Make sure that distributor cap seal is placed properly and install
cap, and then fasten it with screws.
6) Connect distributor lead coupler.
7) Check and adjust ignition timing as previously outlined.
Page 478 of 557
IGNITION SYSTEM 6F-11
09913-76011
SUZUKI scan tool (Tech 1A) kitMass storage cartridge09931-76030
16 / 14 pin DLC cable
09930-76420
Timing light (Dry cell type)1. Storage case
2. Operator’s manual
3. Tech 1A
4. DLC cable (14/26 pin,
09931-76040)
5. Test lead/probe
6. Power source cable
7. DLC cable adaptor
8. Self-test adaptor
09900-27301
Timing light (DC 12 V)
SPECIAL TOOLS
Page 479 of 557
IGNITION SYSTEM (TBI FOR G13) 6F-1
SECTION 6F
IGNITION SYSTEM
(TBI FOR G13)
NOTE:
For the details of this section, refer to the same section of the Service manual mentioned in the FORE-
WORD of this manual.
Page 480 of 557
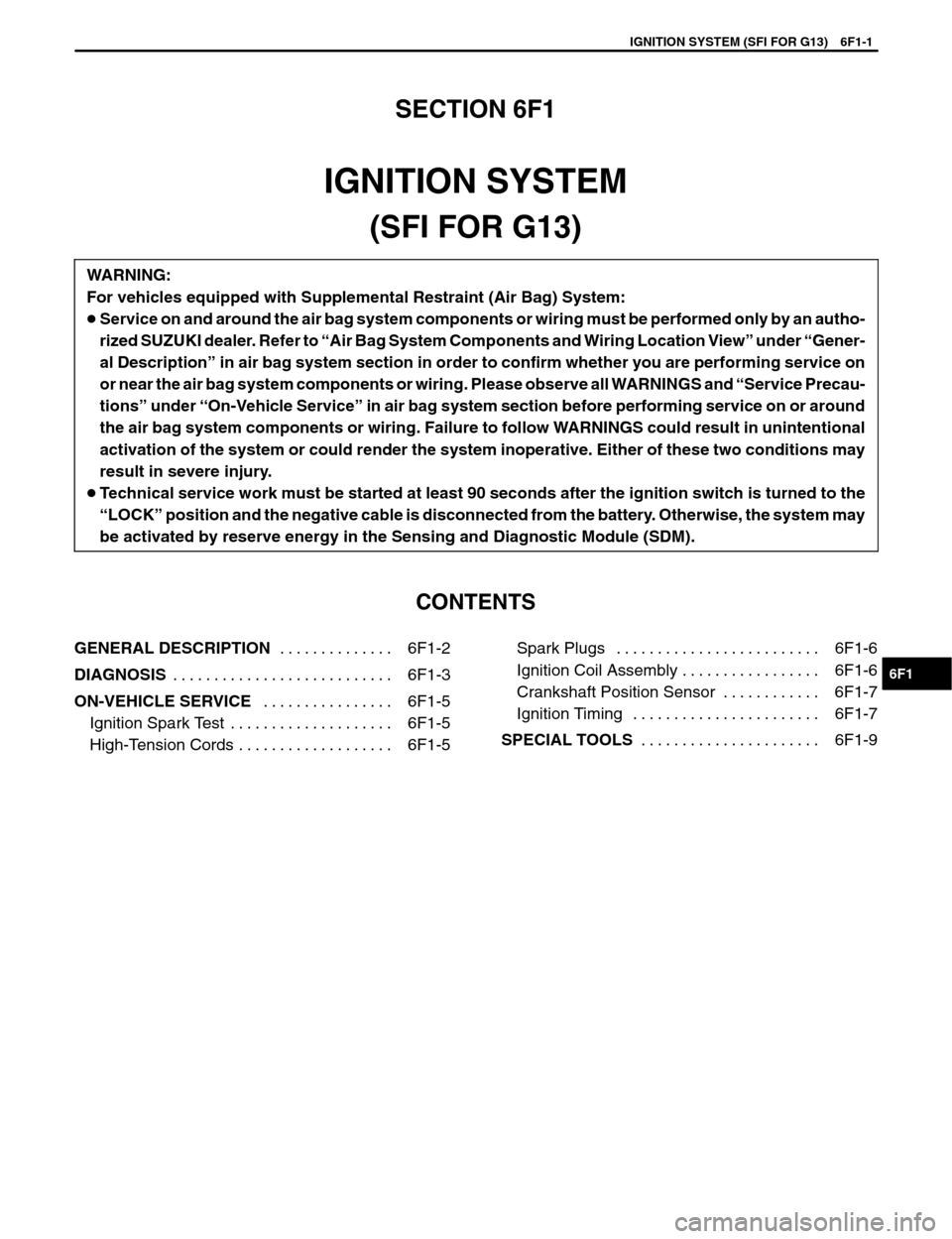
6F1
IGNITION SYSTEM (SFI FOR G13) 6F1-1
GENERAL DESCRIPTION6F1-2 . . . . . . . . . . . . . .
DIAGNOSIS6F1-3 . . . . . . . . . . . . . . . . . . . . . . . . . . .
ON-VEHICLE SERVICE6F1-5 . . . . . . . . . . . . . . . .
Ignition Spark Test 6F1-5. . . . . . . . . . . . . . . . . . . .
High-Tension Cords 6F1-5. . . . . . . . . . . . . . . . . . . Spark Plugs 6F1-6. . . . . . . . . . . . . . . . . . . . . . . . .
Ignition Coil Assembly 6F1-6. . . . . . . . . . . . . . . . .
Crankshaft Position Sensor 6F1-7. . . . . . . . . . . .
Ignition Timing 6F1-7. . . . . . . . . . . . . . . . . . . . . . .
SPECIAL TOOLS6F1-9 . . . . . . . . . . . . . . . . . . . . . .
SECTION 6F1
IGNITION SYSTEM
(SFI FOR G13)
WARNING:
For vehicles equipped with Supplemental Restraint (Air Bag) System:
Service on and around the air bag system components or wiring must be performed only by an autho-
rized SUZUKI dealer. Refer to “Air Bag System Components and Wiring Location View” under “Gener-
al Description” in air bag system section in order to confirm whether you are performing service on
or near the air bag system components or wiring. Please observe all WARNINGS and “Service Precau-
tions” under “On-Vehicle Service” in air bag system section before performing service on or around
the air bag system components or wiring. Failure to follow WARNINGS could result in unintentional
activation of the system or could render the system inoperative. Either of these two conditions may
result in severe injury.
Technical service work must be started at least 90 seconds after the ignition switch is turned to the
“LOCK” position and the negative cable is disconnected from the battery. Otherwise, the system may
be activated by reserve energy in the Sensing and Diagnostic Module (SDM).
CONTENTS