Page 26 of 557
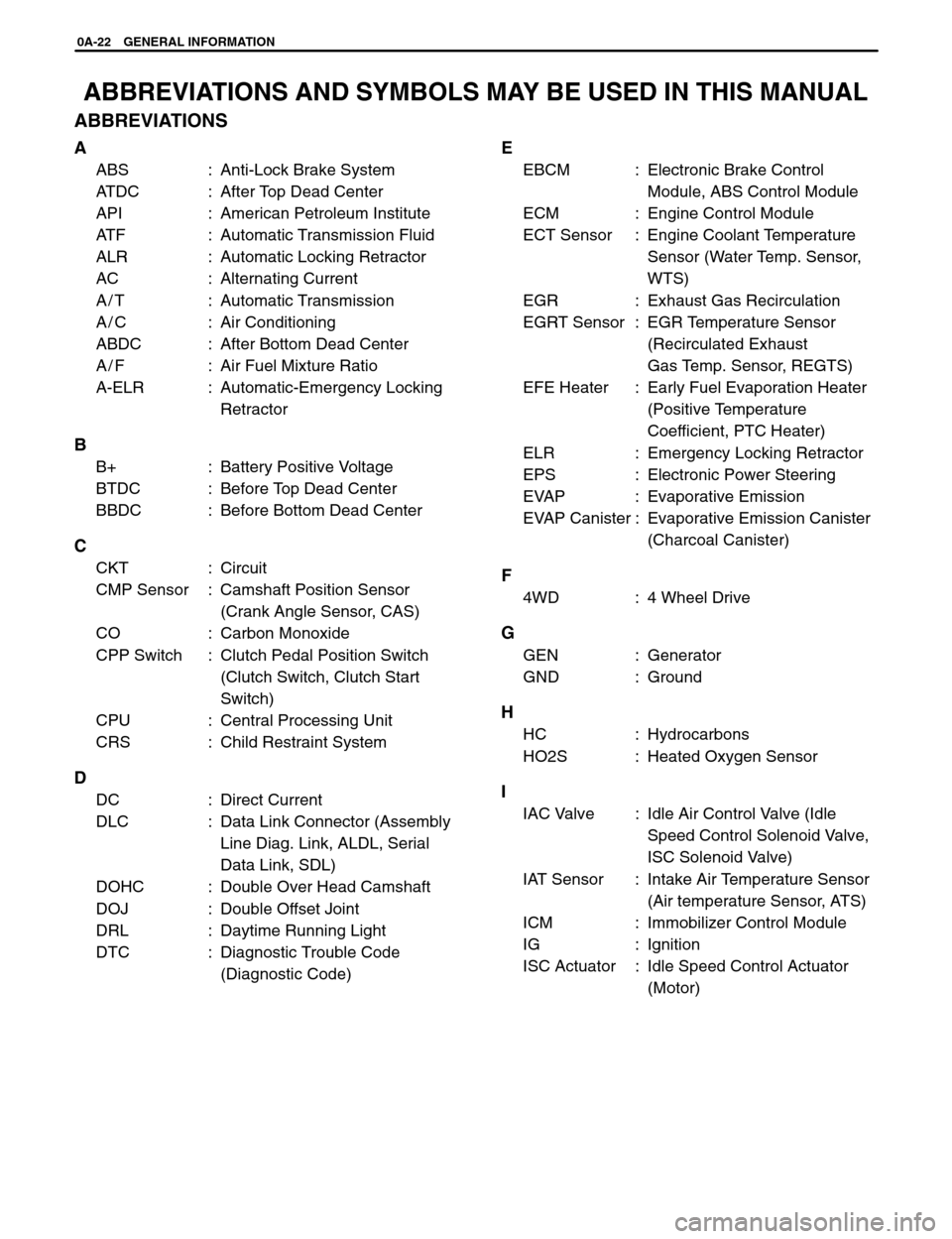
0A-22 GENERAL INFORMATION
A
ABS : Anti-Lock Brake System
ATDC : After Top Dead Center
API : American Petroleum Institute
ATF : Automatic Transmission Fluid
ALR : Automatic Locking Retractor
AC : Alternating Current
A / T : Automatic Transmission
A / C : Air Conditioning
ABDC : After Bottom Dead Center
A / F : Air Fuel Mixture Ratio
A-ELR : Automatic-Emergency Locking
Retractor
B
B+ : Battery Positive Voltage
BTDC : Before Top Dead Center
BBDC : Before Bottom Dead Center
C
CKT : Circuit
CMP Sensor : Camshaft Position Sensor
(Crank Angle Sensor, CAS)
CO : Carbon Monoxide
CPP Switch : Clutch Pedal Position Switch
(Clutch Switch, Clutch Start
Switch)
CPU : Central Processing Unit
CRS : Child Restraint System
D
DC : Direct Current
DLC : Data Link Connector (Assembly
Line Diag. Link, ALDL, Serial
Data Link, SDL)
DOHC : Double Over Head Camshaft
DOJ : Double Offset Joint
DRL : Daytime Running Light
DTC : Diagnostic Trouble Code
(Diagnostic Code)
E
EBCM : Electronic Brake Control
Module, ABS Control Module
ECM : Engine Control Module
ECT Sensor : Engine Coolant Temperature
Sensor (Water Temp. Sensor,
WTS)
EGR : Exhaust Gas Recirculation
EGRT Sensor : EGR Temperature Sensor
(Recirculated Exhaust
Gas Temp. Sensor, REGTS)
EFE Heater : Early Fuel Evaporation Heater
(Positive Temperature
Coefficient, PTC Heater)
ELR : Emergency Locking Retractor
EPS : Electronic Power Steering
EVAP : Evaporative Emission
EVAP Canister : Evaporative Emission Canister
(Charcoal Canister)
F
4WD : 4 Wheel Drive
G
GEN : Generator
GND : Ground
H
HC : Hydrocarbons
HO2S : Heated Oxygen Sensor
I
IAC Valve : Idle Air Control Valve (Idle
Speed Control Solenoid Valve,
ISC Solenoid Valve)
IAT Sensor : Intake Air Temperature Sensor
(Air temperature Sensor, ATS)
ICM : Immobilizer Control Module
IG : Ignition
ISC Actuator : Idle Speed Control Actuator
(Motor)
ABBREVIATIONS AND SYMBOLS MAY BE USED IN THIS MANUAL
ABBREVIATIONS
Page 105 of 557
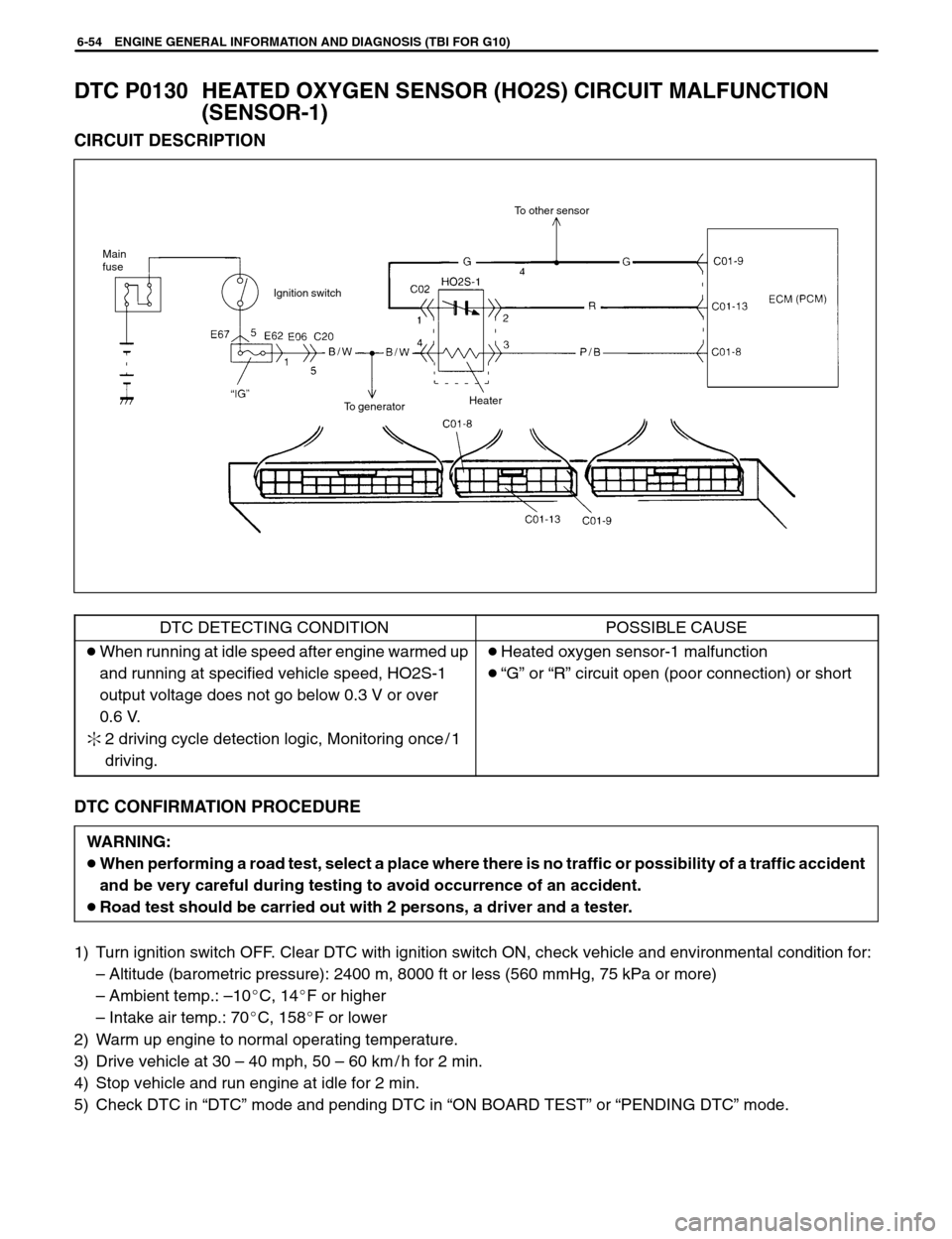
To generatorTo other sensor
Main
fuse
Ignition switch
Heater
6-54 ENGINE GENERAL INFORMATION AND DIAGNOSIS (TBI FOR G10)
DTC P0130 HEATED OXYGEN SENSOR (HO2S) CIRCUIT MALFUNCTION
(SENSOR-1)
CIRCUIT DESCRIPTION
DTC DETECTING CONDITIONPOSSIBLE CAUSE
When running at idle speed after engine warmed up
and running at specified vehicle speed, HO2S-1
output voltage does not go below 0.3 V or over
0.6 V.
2 driving cycle detection logic, Monitoring once / 1
driving.Heated oxygen sensor-1 malfunction
“G” or “R” circuit open (poor connection) or short
DTC CONFIRMATION PROCEDURE
WARNING:
When performing a road test, select a place where there is no traffic or possibility of a traffic accident
and be very careful during testing to avoid occurrence of an accident.
Road test should be carried out with 2 persons, a driver and a tester.
1) Turn ignition switch OFF. Clear DTC with ignition switch ON, check vehicle and environmental condition for:
–Altitude (barometric pressure): 2400 m, 8000 ft or less (560 mmHg, 75 kPa or more)
–Ambient temp.: –10C, 14F or higher
–Intake air temp.: 70C, 158F or lower
2) Warm up engine to normal operating temperature.
3) Drive vehicle at 30 – 40 mph, 50 – 60 km / h for 2 min.
4) Stop vehicle and run engine at idle for 2 min.
5) Check DTC in “DTC” mode and pending DTC in “ON BOARD TEST” or “PENDING DTC” mode.
Page 108 of 557
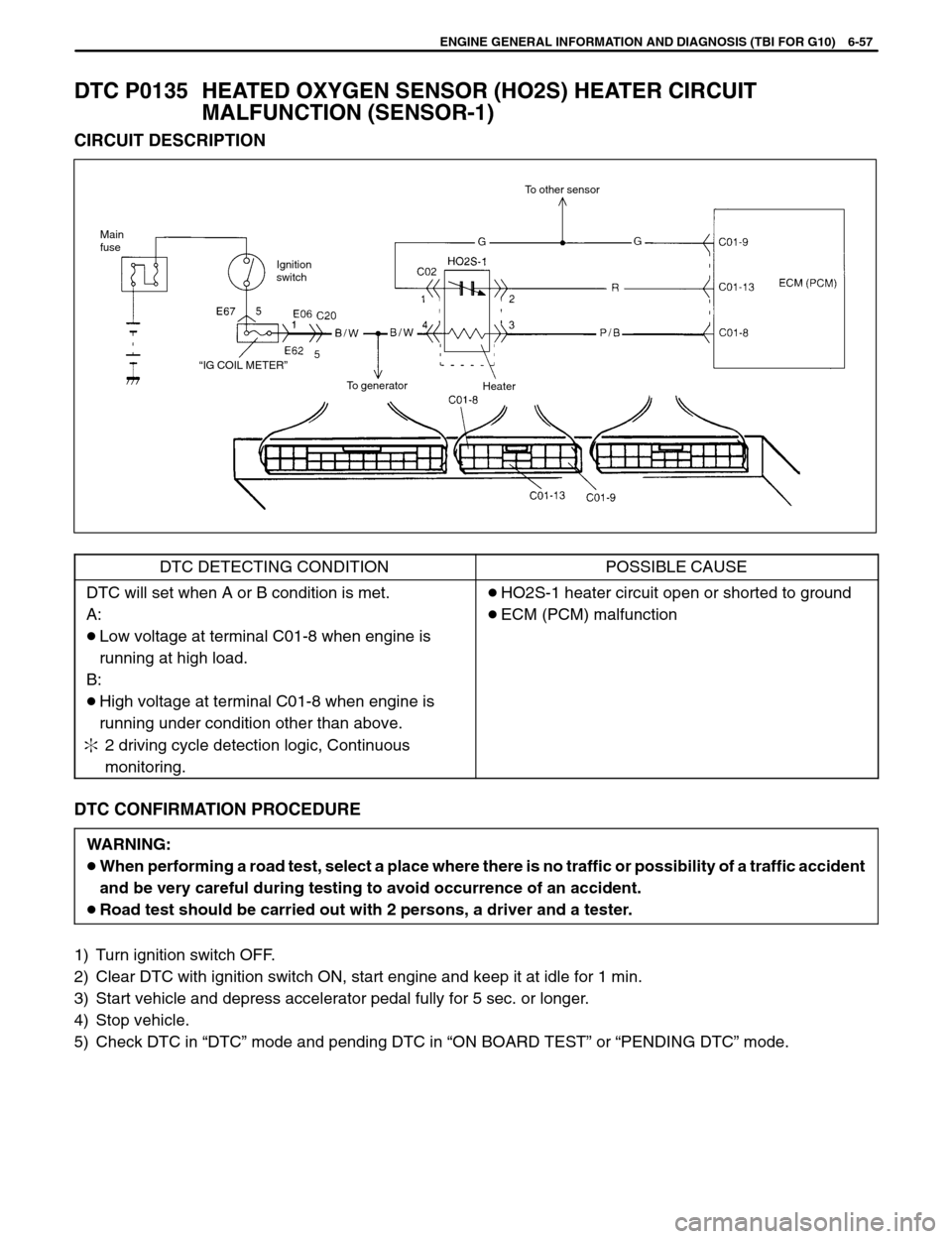
To generatorTo other sensor
Heater Ignition
switch Main
fuse
“IG COIL METER”
ENGINE GENERAL INFORMATION AND DIAGNOSIS (TBI FOR G10) 6-57
DTC P0135 HEATED OXYGEN SENSOR (HO2S) HEATER CIRCUIT
MALFUNCTION (SENSOR-1)
CIRCUIT DESCRIPTION
DTC DETECTING CONDITIONPOSSIBLE CAUSE
DTC will set when A or B condition is met.
A:
Low voltage at terminal C01-8 when engine is
running at high load.
B:
High voltage at terminal C01-8 when engine is
running under condition other than above.
2 driving cycle detection logic, Continuous
monitoring.HO2S-1 heater circuit open or shorted to ground
ECM (PCM) malfunction
DTC CONFIRMATION PROCEDURE
WARNING:
When performing a road test, select a place where there is no traffic or possibility of a traffic accident
and be very careful during testing to avoid occurrence of an accident.
Road test should be carried out with 2 persons, a driver and a tester.
1) Turn ignition switch OFF.
2) Clear DTC with ignition switch ON, start engine and keep it at idle for 1 min.
3) Start vehicle and depress accelerator pedal fully for 5 sec. or longer.
4) Stop vehicle.
5) Check DTC in “DTC” mode and pending DTC in “ON BOARD TEST” or “PENDING DTC” mode.
Page 274 of 557
1. Timing belt
2. Tensioner
3. Tensioner plate
4. Tensioner spring
5. Spring damper
6. Camshaft timing pulley
7. Pin
8. Pulley bolt
9. Seal
10. Inside cover seal
11. Inside cover
12. Outside cover seal
13. Outside cover
14. Tensioner stud
15. Tensioner bolt
16. Tensioner spring screw
: Tightening Torque
6A-10 ENGINE MECHANICAL (G10, 1-CAM 6-VALVES ENGINE)
TIMING BELT AND BELT TENSIONER
REMOVAL
1) Disconnect negative cable at battery.
2) Hoist vehicle.
3) Remove clip (2) after pushing center pin, and then remove fend-
er apron extension (1) on right side.
NOTE:
Do not push center pin (3) too far in, or it will fall off into
fender.
4) Remove air cleaner assembly as previously outlined.
5) Remove A / C compressor drive belt, if equipped.
6) Loosen water pump pulley bolts (1).
7) Loosen generator pivot bolts (3) and its adjusting bolt (2) and re-
move water pump belt (4) and its pulley (5).
Page 288 of 557
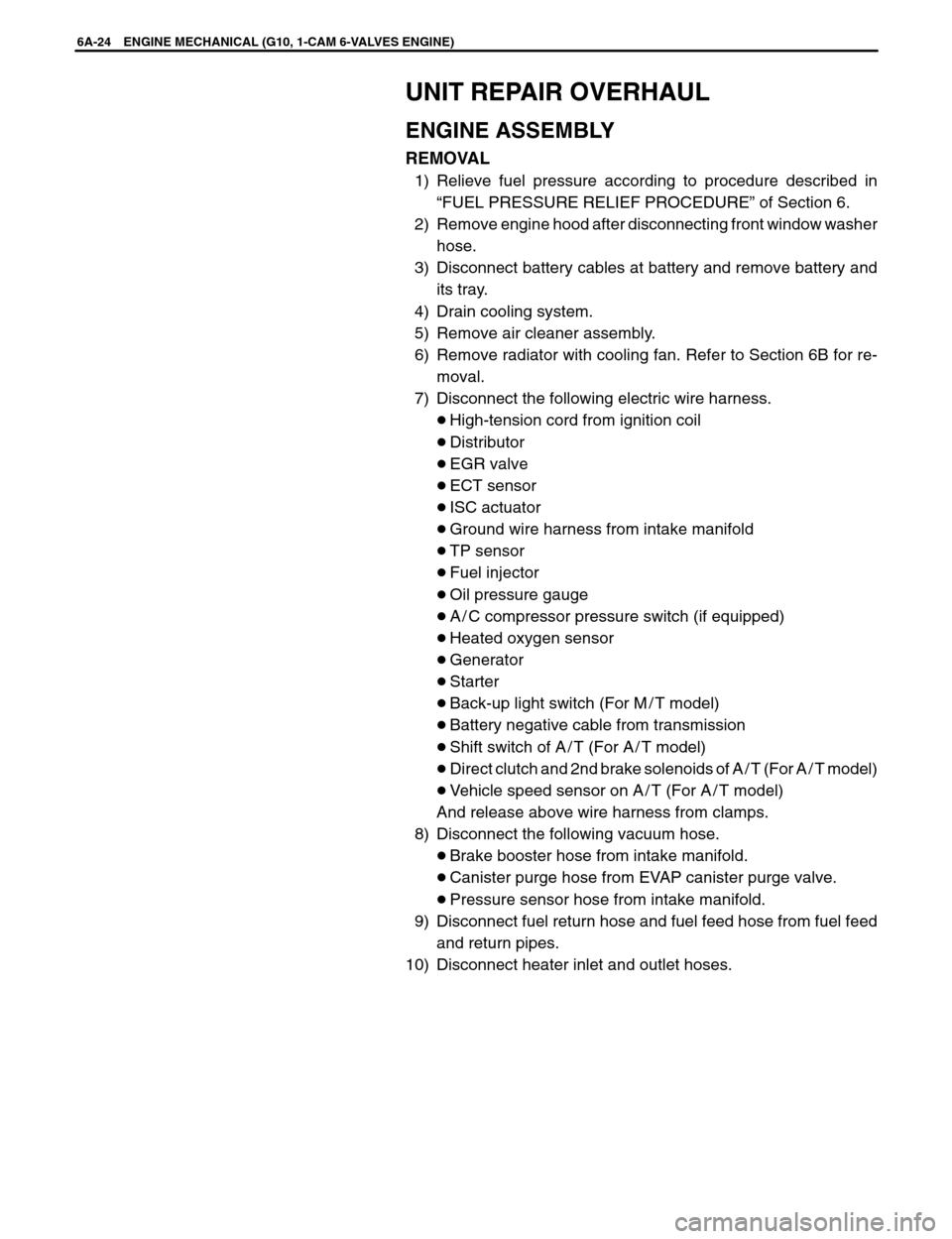
6A-24 ENGINE MECHANICAL (G10, 1-CAM 6-VALVES ENGINE)
UNIT REPAIR OVERHAUL
ENGINE ASSEMBLY
REMOVAL
1) Relieve fuel pressure according to procedure described in
“FUEL PRESSURE RELIEF PROCEDURE” of Section 6.
2) Remove engine hood after disconnecting front window washer
hose.
3) Disconnect battery cables at battery and remove battery and
its tray.
4) Drain cooling system.
5) Remove air cleaner assembly.
6) Remove radiator with cooling fan. Refer to Section 6B for re-
moval.
7) Disconnect the following electric wire harness.
High-tension cord from ignition coil
Distributor
EGR valve
ECT sensor
ISC actuator
Ground wire harness from intake manifold
TP sensor
Fuel injector
Oil pressure gauge
A / C compressor pressure switch (if equipped)
Heated oxygen sensor
Generator
Starter
Back-up light switch (For M / T model)
Battery negative cable from transmission
Shift switch of A / T (For A / T model)
Direct clutch and 2nd brake solenoids of A / T (For A / T model)
Vehicle speed sensor on A / T (For A / T model)
And release above wire harness from clamps.
8) Disconnect the following vacuum hose.
Brake booster hose from intake manifold.
Canister purge hose from EVAP canister purge valve.
Pressure sensor hose from intake manifold.
9) Disconnect fuel return hose and fuel feed hose from fuel feed
and return pipes.
10) Disconnect heater inlet and outlet hoses.
Page 291 of 557
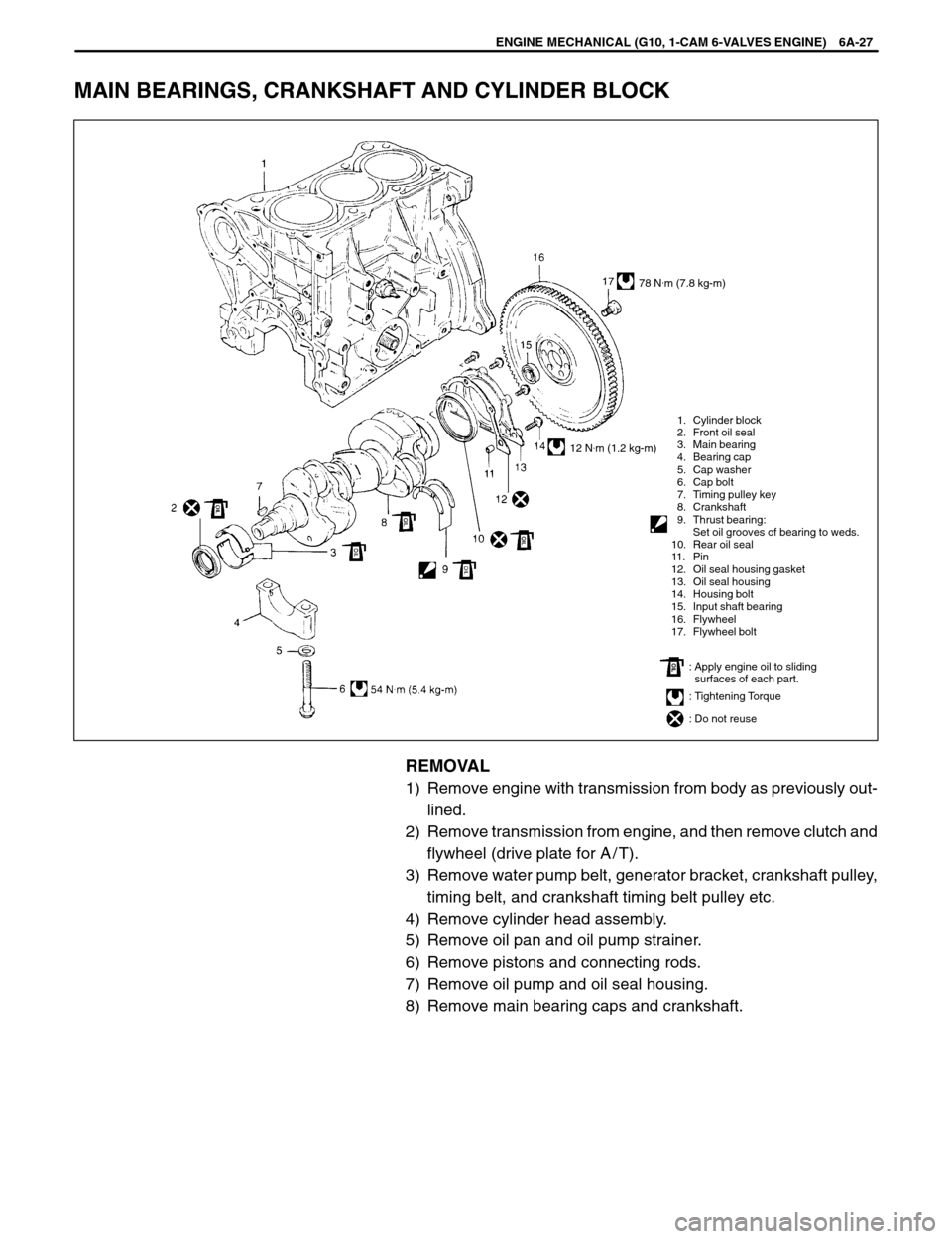
1. Cylinder block
2. Front oil seal
3. Main bearing
4. Bearing cap
5. Cap washer
6. Cap bolt
7. Timing pulley key
8. Crankshaft
9. Thrust bearing:
Set oil grooves of bearing to weds.
10. Rear oil seal
11. Pin
12. Oil seal housing gasket
13. Oil seal housing
14. Housing bolt
15. Input shaft bearing
16. Flywheel
17. Flywheel bolt
: Tightening Torque
: Do not reuse
: Apply engine oil to sliding
: surfaces of each part.
78 N.m (7.8 kg-m)
12 N
.m (1.2 kg-m)
ENGINE MECHANICAL (G10, 1-CAM 6-VALVES ENGINE) 6A-27
MAIN BEARINGS, CRANKSHAFT AND CYLINDER BLOCK
REMOVAL
1) Remove engine with transmission from body as previously out-
lined.
2) Remove transmission from engine, and then remove clutch and
flywheel (drive plate for A / T).
3) Remove water pump belt, generator bracket, crankshaft pulley,
timing belt, and crankshaft timing belt pulley etc.
4) Remove cylinder head assembly.
5) Remove oil pan and oil pump strainer.
6) Remove pistons and connecting rods.
7) Remove oil pump and oil seal housing.
8) Remove main bearing caps and crankshaft.
Page 311 of 557
1. Long bolt
2. Short bolt
6A1-16 ENGINE MECHANICAL (G13B, 1-CAM 16-VALVES ENGINE)
10) Remove intake manifold rear stiffener (1) and generator adjust
arm reinforcement (2) from intake manifold (3).
11) Remove intake manifold with throttle body from cylinder head,
and then its gasket.
INSTALLATION
Reverse removal procedure for installation noting the followings.
Use new intake manifold gasket.
When installing intake manifold, install clamps securely.
Tightening Torque
(a): 23 N
.m (2.3 kg-m, 17.0 lb-ft)
Adjust accelerator cable play, referring to Section 6E.
Check to ensure that all removed parts are back in place.
Reinstall any necessary parts which have not been reinstalled.
Refill cooling system referring to Section 6B.
Upon completion of installation, turn ignition switch ON but en-
gine OFF and check for fuel leaks.
Finally, start engine and check for engine coolant leaks.
Page 323 of 557
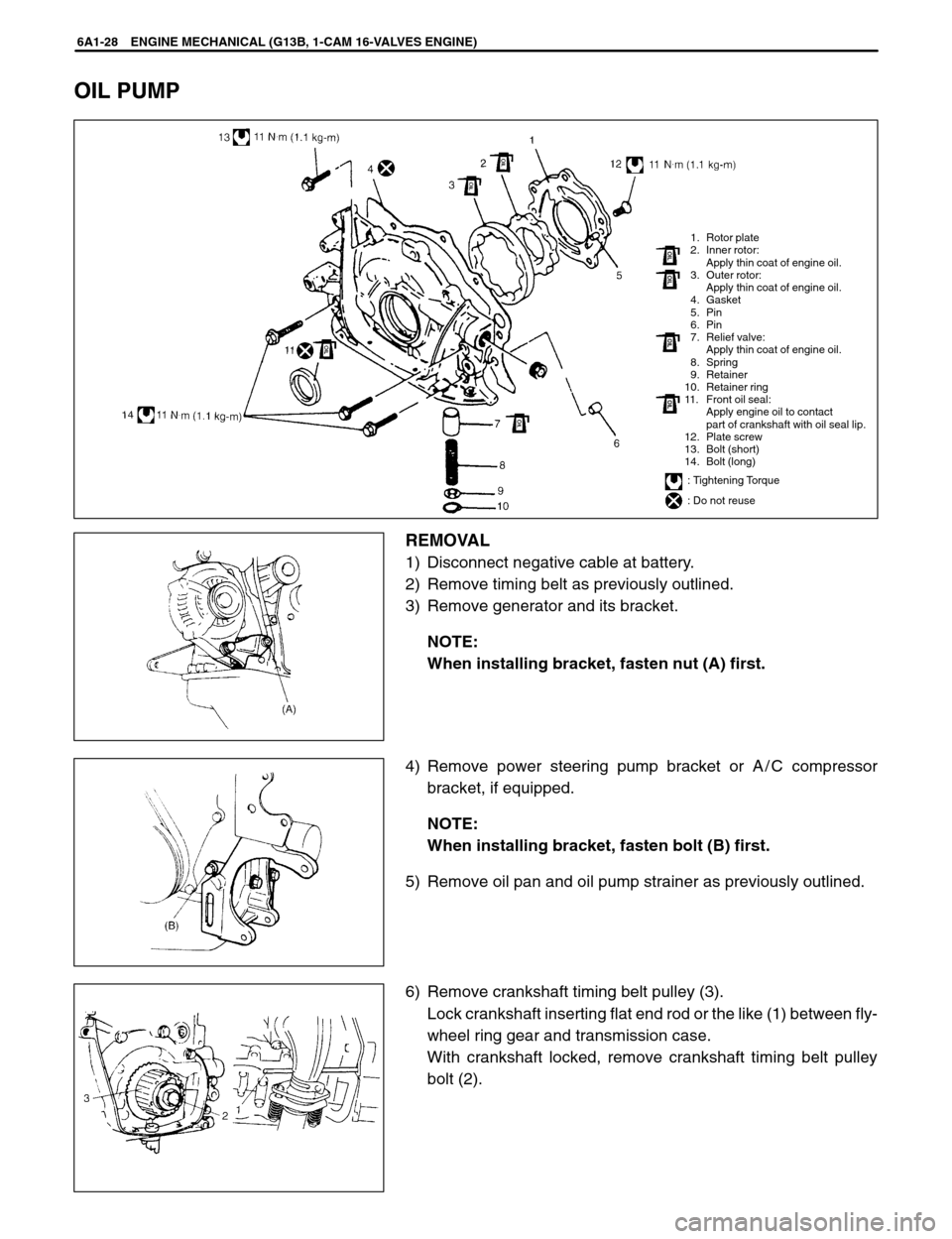
1. Rotor plate
2. Inner rotor:
Apply thin coat of engine oil.
3. Outer rotor:
Apply thin coat of engine oil.
4. Gasket
5. Pin
6. Pin
7. Relief valve:
Apply thin coat of engine oil.
8. Spring
9. Retainer
10. Retainer ring
11. Front oil seal:
Apply engine oil to contact
part of crankshaft with oil seal lip.
12. Plate screw
13. Bolt (short)
14. Bolt (long)
: Tightening Torque
: Do not reuse
6A1-28 ENGINE MECHANICAL (G13B, 1-CAM 16-VALVES ENGINE)
OIL PUMP
REMOVAL
1) Disconnect negative cable at battery.
2) Remove timing belt as previously outlined.
3) Remove generator and its bracket.
NOTE:
When installing bracket, fasten nut (A) first.
4) Remove power steering pump bracket or A / C compressor
bracket, if equipped.
NOTE:
When installing bracket, fasten bolt (B) first.
5) Remove oil pan and oil pump strainer as previously outlined.
6) Remove crankshaft timing belt pulley (3).
Lock crankshaft inserting flat end rod or the like (1) between fly-
wheel ring gear and transmission case.
With crankshaft locked, remove crankshaft timing belt pulley
bolt (2).