Page 49 of 557
“A”: Oil point
1. Upper hinge
2. Lower hinge
3. Door
4. Body
MAINTENANCE AND LUBRICATION 0B-19
ITEM 6-10
All Latches, Hinges and Locks Inspection
Doors
Check that each door of front, rear and back doors opens and
closes smoothly and locks securely when closed.
If any malfunction is found, lubricate hinge and latch or repair door
lock system.
Engine hood
Check that secondary latch operates properly (check that second-
ary latch keeps hood from opening all the way even when pulling
hood release handle inside vehicle.). Also check that hood opens
and closes smoothly and properly and hood locks securely when
closed.
If any malfunction is found, lubricate hinge and latch, or repair hood
lock system.
Page 50 of 557
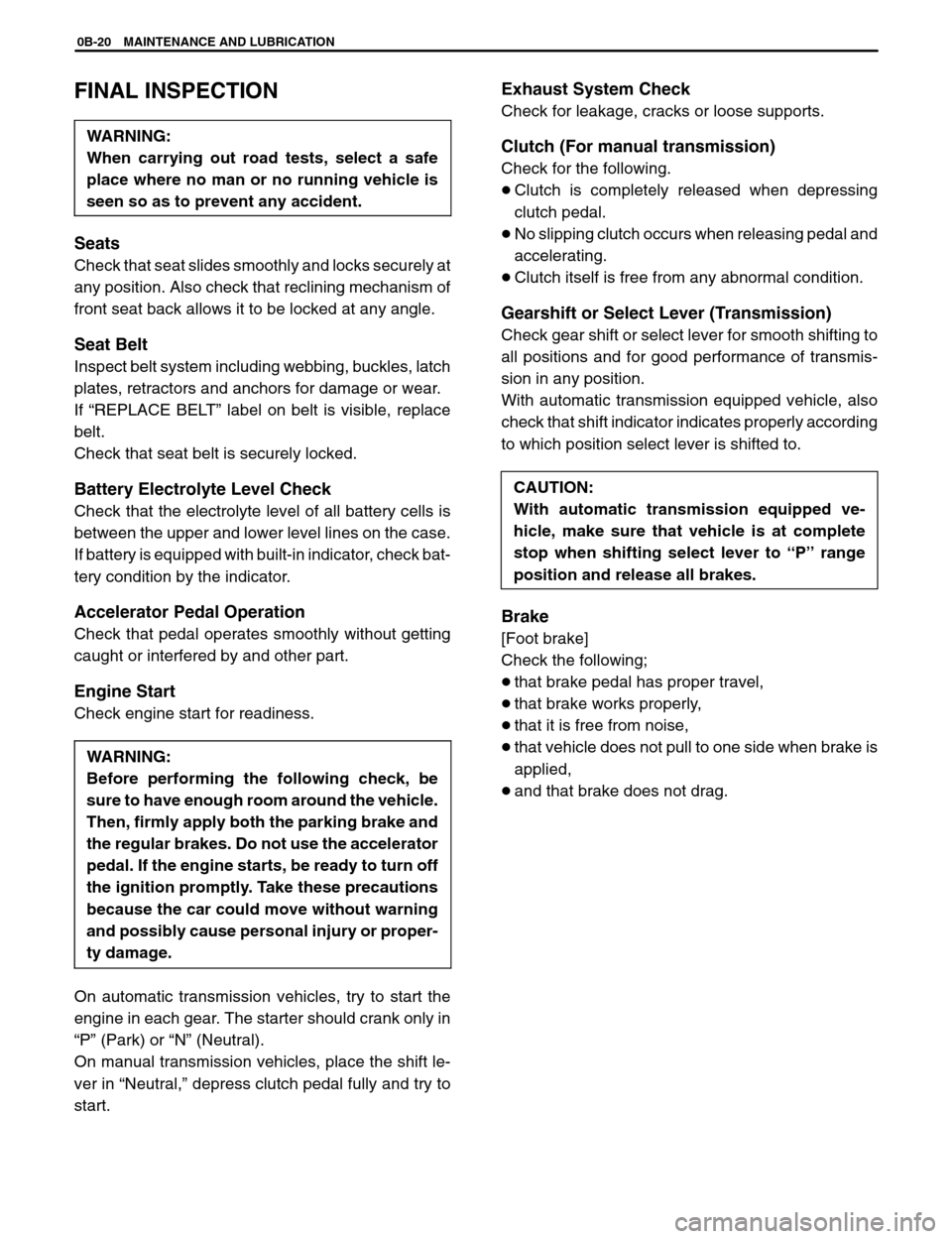
0B-20 MAINTENANCE AND LUBRICATION
FINAL INSPECTION
Seats
Check that seat slides smoothly and locks securely at
any position. Also check that reclining mechanism of
front seat back allows it to be locked at any angle.
Seat Belt
Inspect belt system including webbing, buckles, latch
plates, retractors and anchors for damage or wear.
If “REPLACE BELT” label on belt is visible, replace
belt.
Check that seat belt is securely locked.
Battery Electrolyte Level Check
Check that the electrolyte level of all battery cells is
between the upper and lower level lines on the case.
If battery is equipped with built-in indicator, check bat-
tery condition by the indicator.
Accelerator Pedal Operation
Check that pedal operates smoothly without getting
caught or interfered by and other part.
Engine Start
Check engine start for readiness.
On automatic transmission vehicles, try to start the
engine in each gear. The starter should crank only in
“P” (Park) or “N” (Neutral).
On manual transmission vehicles, place the shift le-
ver in “Neutral,” depress clutch pedal fully and try to
start.
Exhaust System Check
Check for leakage, cracks or loose supports.
Clutch (For manual transmission)
Check for the following.
Clutch is completely released when depressing
clutch pedal.
No slipping clutch occurs when releasing pedal and
accelerating.
Clutch itself is free from any abnormal condition.
Gearshift or Select Lever (Transmission)
Check gear shift or select lever for smooth shifting to
all positions and for good performance of transmis-
sion in any position.
With automatic transmission equipped vehicle, also
check that shift indicator indicates properly according
to which position select lever is shifted to.
CAUTION:
With automatic transmission equipped ve-
hicle, make sure that vehicle is at complete
stop when shifting select lever to “P” range
position and release all brakes.
Brake
[Foot brake]
Check the following;
that brake pedal has proper travel,
that brake works properly,
that it is free from noise,
that vehicle does not pull to one side when brake is
applied,
and that brake does not drag.
WARNING:
When carrying out road tests, select a safe
place where no man or no running vehicle is
seen so as to prevent any accident.
WARNING:
Before performing the following check, be
sure to have enough room around the vehicle.
Then, firmly apply both the parking brake and
the regular brakes. Do not use the accelerator
pedal. If the engine starts, be ready to turn off
the ignition promptly. Take these precautions
because the car could move without warning
and possibly cause personal injury or proper-
ty damage.
Page 51 of 557
![SUZUKI SWIFT 2000 1.G SF310 Service Workshop Manual MAINTENANCE AND LUBRICATION 0B-21
[Parking brake]
Check that lever has proper travel.
Check to ensure that parking brake is fully effective
when the vehicle is stopped on the safe slope and
brake leve SUZUKI SWIFT 2000 1.G SF310 Service Workshop Manual MAINTENANCE AND LUBRICATION 0B-21
[Parking brake]
Check that lever has proper travel.
Check to ensure that parking brake is fully effective
when the vehicle is stopped on the safe slope and
brake leve](/manual-img/20/7602/w960_7602-50.png)
MAINTENANCE AND LUBRICATION 0B-21
[Parking brake]
Check that lever has proper travel.
Check to ensure that parking brake is fully effective
when the vehicle is stopped on the safe slope and
brake lever is pulled all the way.
Steering
Check to ensure that steering wheel is free from in-
stability, or abnormally heavy feeling.
Check that the vehicle does not wander or pull to
one side.
Engine
Check that engine responds readily at all speeds.
Check that engine is free from abnormal noise and
abnormal vibration.
Body, Wheels and Power Transmitting System
Check that body, wheels and power transmitting sys-
tem are free from abnormal noise and abnormal
vibration or any other abnormal condition.
Meters and Gauge
Check that speedometer, odometer, fuel meter, tem-
perature gauge, etc. are operating accurately.
Lights
Check that all lights operate properly.
Windshield Defroster
Periodically check that air comes out from defroster
outlet when operating heater or air conditioning.
Set fan switch lever to “HI” position and mode lever to
defroster position for this check. WARNING:
With vehicle parked on a fairly steep slope,
make sure nothing is in the way downhill to
avoid any personal injury or property damage.
Be prepared to apply regular brake quickly
even if vehicle should start to move.
RECOMMENDED FLUIDS AND LUBRICANTS
Engine oilSE, SF, SG, SH or SJ (Refer to engine oil viscosity chart in item 1-4.)
Engine coolantEthylene-glycol base coolant (“Antifreeze / Anticorrosion coolant”)
Brake fluidDOT3
Manual transmission oilSee SECTION 7A
Rear differential oilSee SECTION 7E
Automatic transmission fluidAn equivalent of DEXRON-IIE or DEXRON-III
Power steering fluidSee material table on SECTION 3B1
Door hingesEngine oil
Engine hood latchEngine oil
Key lock cylinderSpray lubricant
Page 52 of 557
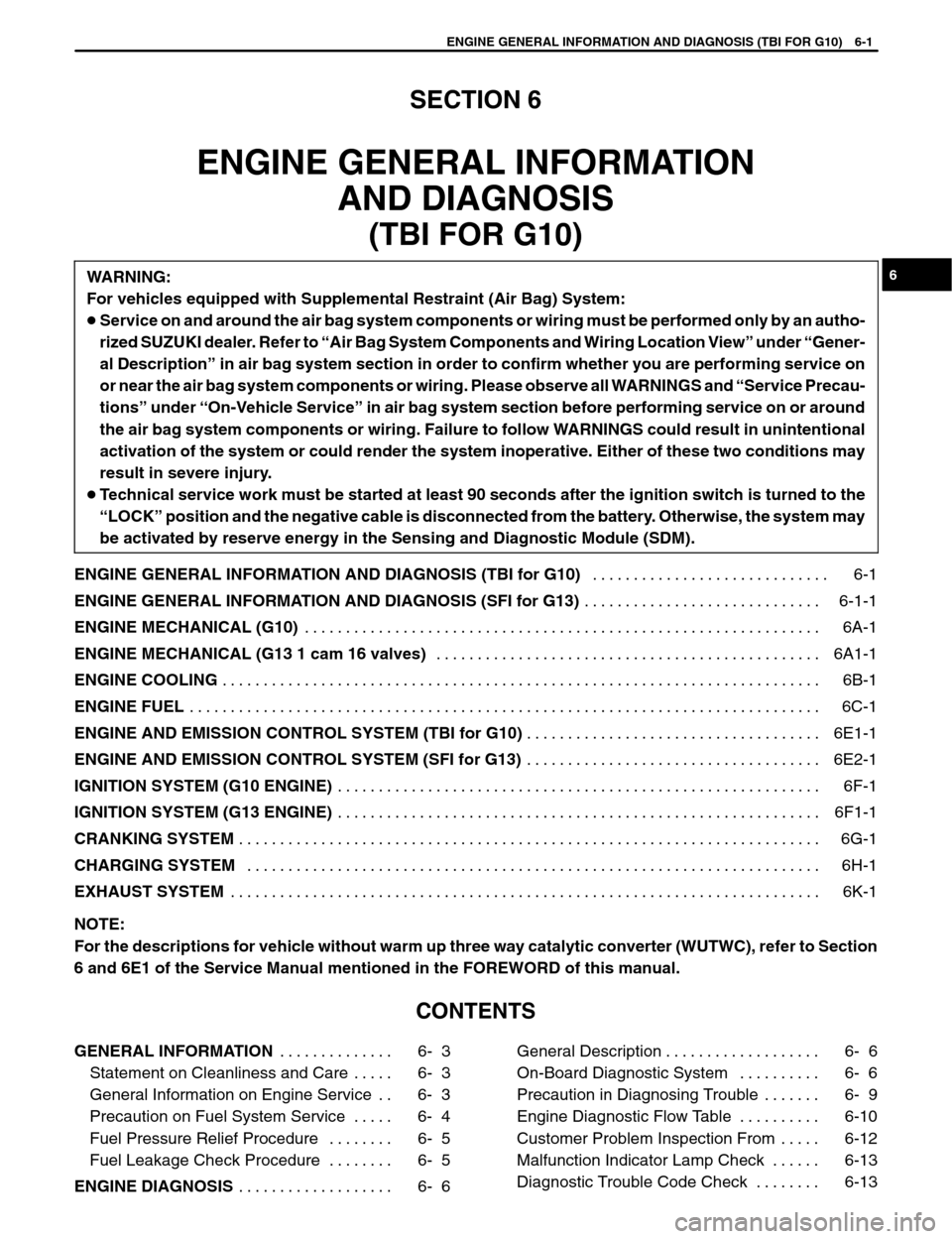
6
ENGINE GENERAL INFORMATION AND DIAGNOSIS (TBI FOR G10) 6-1
GENERAL INFORMATION6- 3 . . . . . . . . . . . . . .
Statement on Cleanliness and Care 6- 3. . . . .
General Information on Engine Service 6- 3. .
Precaution on Fuel System Service 6- 4. . . . .
Fuel Pressure Relief Procedure 6- 5. . . . . . . .
Fuel Leakage Check Procedure 6- 5. . . . . . . .
ENGINE DIAGNOSIS6- 6 . . . . . . . . . . . . . . . . . . . General Description 6- 6. . . . . . . . . . . . . . . . . . .
On-Board Diagnostic System 6- 6. . . . . . . . . .
Precaution in Diagnosing Trouble 6- 9. . . . . . .
Engine Diagnostic Flow Table 6-10. . . . . . . . . .
Customer Problem Inspection From 6-12. . . . .
Malfunction Indicator Lamp Check 6-13. . . . . .
Diagnostic Trouble Code Check 6-13. . . . . . . .
SECTION 6
ENGINE GENERAL INFORMATION
AND DIAGNOSIS
(TBI FOR G10)
WARNING:
For vehicles equipped with Supplemental Restraint (Air Bag) System:
Service on and around the air bag system components or wiring must be performed only by an autho-
rized SUZUKI dealer. Refer to “Air Bag System Components and Wiring Location View” under “Gener-
al Description” in air bag system section in order to confirm whether you are performing service on
or near the air bag system components or wiring. Please observe all WARNINGS and “Service Precau-
tions” under “On-Vehicle Service” in air bag system section before performing service on or around
the air bag system components or wiring. Failure to follow WARNINGS could result in unintentional
activation of the system or could render the system inoperative. Either of these two conditions may
result in severe injury.
Technical service work must be started at least 90 seconds after the ignition switch is turned to the
“LOCK” position and the negative cable is disconnected from the battery. Otherwise, the system may
be activated by reserve energy in the Sensing and Diagnostic Module (SDM).
ENGINE GENERAL INFORMATION AND DIAGNOSIS (TBI for G10)6-1 . . . . . . . . . . . . . . . . . . . . . . . . . . . . .
ENGINE GENERAL INFORMATION AND DIAGNOSIS (SFI for G13)6-1-1 . . . . . . . . . . . . . . . . . . . . . . . . . . . . .
ENGINE MECHANICAL (G10)6A-1 . . . . . . . . . . . . . . . . . . . . . . . . . . . . . . . . . . . . . . . . . . . . . . . . . . . . . . . . . . . . . . .
ENGINE MECHANICAL (G13 1 cam 16 valves)6A1-1 . . . . . . . . . . . . . . . . . . . . . . . . . . . . . . . . . . . . . . . . . . . . . . .
ENGINE COOLING6B-1 . . . . . . . . . . . . . . . . . . . . . . . . . . . . . . . . . . . . . . . . . . . . . . . . . . . . . . . . . . . . . . . . . . . . . . . . .
ENGINE FUEL6C-1 . . . . . . . . . . . . . . . . . . . . . . . . . . . . . . . . . . . . . . . . . . . . . . . . . . . . . . . . . . . . . . . . . . . . . . . . . . . . .
ENGINE AND EMISSION CONTROL SYSTEM (TBI for G10)6E1-1 . . . . . . . . . . . . . . . . . . . . . . . . . . . . . . . . . . . .
ENGINE AND EMISSION CONTROL SYSTEM (SFI for G13)6E2-1 . . . . . . . . . . . . . . . . . . . . . . . . . . . . . . . . . . . .
IGNITION SYSTEM (G10 ENGINE)6F-1 . . . . . . . . . . . . . . . . . . . . . . . . . . . . . . . . . . . . . . . . . . . . . . . . . . . . . . . . . . .
IGNITION SYSTEM (G13 ENGINE)6F1-1 . . . . . . . . . . . . . . . . . . . . . . . . . . . . . . . . . . . . . . . . . . . . . . . . . . . . . . . . . . .
CRANKING SYSTEM6G-1 . . . . . . . . . . . . . . . . . . . . . . . . . . . . . . . . . . . . . . . . . . . . . . . . . . . . . . . . . . . . . . . . . . . . . . .
CHARGING SYSTEM6H-1 . . . . . . . . . . . . . . . . . . . . . . . . . . . . . . . . . . . . . . . . . . . . . . . . . . . . . . . . . . . . . . . . . . . . . .
EXHAUST SYSTEM6K-1 . . . . . . . . . . . . . . . . . . . . . . . . . . . . . . . . . . . . . . . . . . . . . . . . . . . . . . . . . . . . . . . . . . . . . . . .
NOTE:
For the descriptions for vehicle without warm up three way catalytic converter (WUTWC), refer to Section
6 and 6E1 of the Service Manual mentioned in the FOREWORD of this manual.
CONTENTS
Page 53 of 557
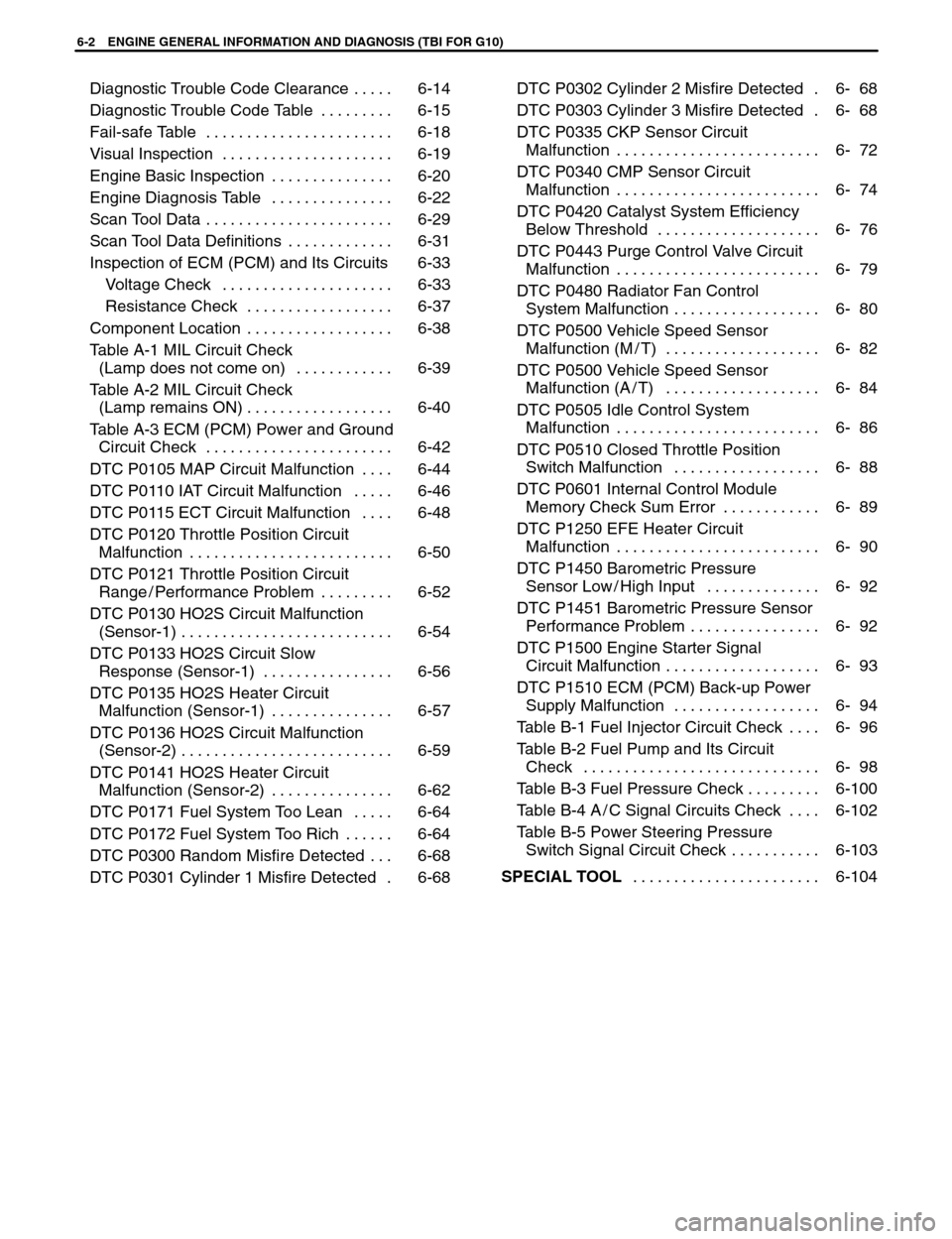
Diagnostic Trouble Code Clearance 6-14. . . . .
Diagnostic Trouble Code Table 6-15. . . . . . . . .
Fail-safe Table 6-18. . . . . . . . . . . . . . . . . . . . . . .
Visual Inspection 6-19. . . . . . . . . . . . . . . . . . . . .
Engine Basic Inspection 6-20. . . . . . . . . . . . . . .
Engine Diagnosis Table 6-22. . . . . . . . . . . . . . .
Scan Tool Data 6-29. . . . . . . . . . . . . . . . . . . . . . .
Scan Tool Data Definitions 6-31. . . . . . . . . . . . .
Inspection of ECM (PCM) and Its Circuits 6-33
Voltage Check 6-33. . . . . . . . . . . . . . . . . . . . .
Resistance Check 6-37. . . . . . . . . . . . . . . . . .
Component Location 6-38. . . . . . . . . . . . . . . . . .
Table A-1 MIL Circuit Check
(Lamp does not come on) 6-39. . . . . . . . . . . .
Table A-2 MIL Circuit Check
(Lamp remains ON) 6-40. . . . . . . . . . . . . . . . . .
Table A-3 ECM (PCM) Power and Ground
Circuit Check 6-42. . . . . . . . . . . . . . . . . . . . . . .
DTC P0105 MAP Circuit Malfunction 6-44. . . .
DTC P0110 IAT Circuit Malfunction 6-46. . . . .
DTC P0115 ECT Circuit Malfunction 6-48. . . .
DTC P0120 Throttle Position Circuit
Malfunction 6-50. . . . . . . . . . . . . . . . . . . . . . . . .
DTC P0121 Throttle Position Circuit
Range / Performance Problem 6-52. . . . . . . . .
DTC P0130 HO2S Circuit Malfunction
(Sensor-1) 6-54. . . . . . . . . . . . . . . . . . . . . . . . . .
DTC P0133 HO2S Circuit Slow
Response (Sensor-1) 6-56. . . . . . . . . . . . . . . .
DTC P0135 HO2S Heater Circuit
Malfunction (Sensor-1) 6-57. . . . . . . . . . . . . . .
DTC P0136 HO2S Circuit Malfunction
(Sensor-2) 6-59. . . . . . . . . . . . . . . . . . . . . . . . . .
DTC P0141 HO2S Heater Circuit
Malfunction (Sensor-2) 6-62. . . . . . . . . . . . . . .
DTC P0171 Fuel System Too Lean 6-64. . . . .
DTC P0172 Fuel System Too Rich 6-64. . . . . .
DTC P0300 Random Misfire Detected 6-68. . .
DTC P0301 Cylinder 1 Misfire Detected 6-68. DTC P0302 Cylinder 2 Misfire Detected 6- 68.
DTC P0303 Cylinder 3 Misfire Detected 6- 68.
DTC P0335 CKP Sensor Circuit
Malfunction 6- 72. . . . . . . . . . . . . . . . . . . . . . . . .
DTC P0340 CMP Sensor Circuit
Malfunction 6- 74. . . . . . . . . . . . . . . . . . . . . . . . .
DTC P0420 Catalyst System Efficiency
Below Threshold 6- 76. . . . . . . . . . . . . . . . . . . .
DTC P0443 Purge Control Valve Circuit
Malfunction 6- 79. . . . . . . . . . . . . . . . . . . . . . . . .
DTC P0480 Radiator Fan Control
System Malfunction 6- 80. . . . . . . . . . . . . . . . . .
DTC P0500 Vehicle Speed Sensor
Malfunction (M / T) 6- 82. . . . . . . . . . . . . . . . . . .
DTC P0500 Vehicle Speed Sensor
Malfunction (A / T) 6- 84. . . . . . . . . . . . . . . . . . .
DTC P0505 Idle Control System
Malfunction 6- 86. . . . . . . . . . . . . . . . . . . . . . . . .
DTC P0510 Closed Throttle Position
Switch Malfunction 6- 88. . . . . . . . . . . . . . . . . .
DTC P0601 Internal Control Module
Memory Check Sum Error 6- 89. . . . . . . . . . . .
DTC P1250 EFE Heater Circuit
Malfunction 6- 90. . . . . . . . . . . . . . . . . . . . . . . . .
DTC P1450 Barometric Pressure
Sensor Low / High Input 6- 92. . . . . . . . . . . . . .
DTC P1451 Barometric Pressure Sensor
Performance Problem 6- 92. . . . . . . . . . . . . . . .
DTC P1500 Engine Starter Signal
Circuit Malfunction 6- 93. . . . . . . . . . . . . . . . . . .
DTC P1510 ECM (PCM) Back-up Power
Supply Malfunction 6- 94. . . . . . . . . . . . . . . . . .
Table B-1 Fuel Injector Circuit Check 6- 96. . . .
Table B-2 Fuel Pump and Its Circuit
Check 6- 98. . . . . . . . . . . . . . . . . . . . . . . . . . . . .
Table B-3 Fuel Pressure Check 6-100. . . . . . . . .
Table B-4 A / C Signal Circuits Check 6-102. . . .
Table B-5 Power Steering Pressure
Switch Signal Circuit Check 6-103. . . . . . . . . . .
SPECIAL TOOL6-104 . . . . . . . . . . . . . . . . . . . . . . .
6-2 ENGINE GENERAL INFORMATION AND DIAGNOSIS (TBI FOR G10)
Page 54 of 557
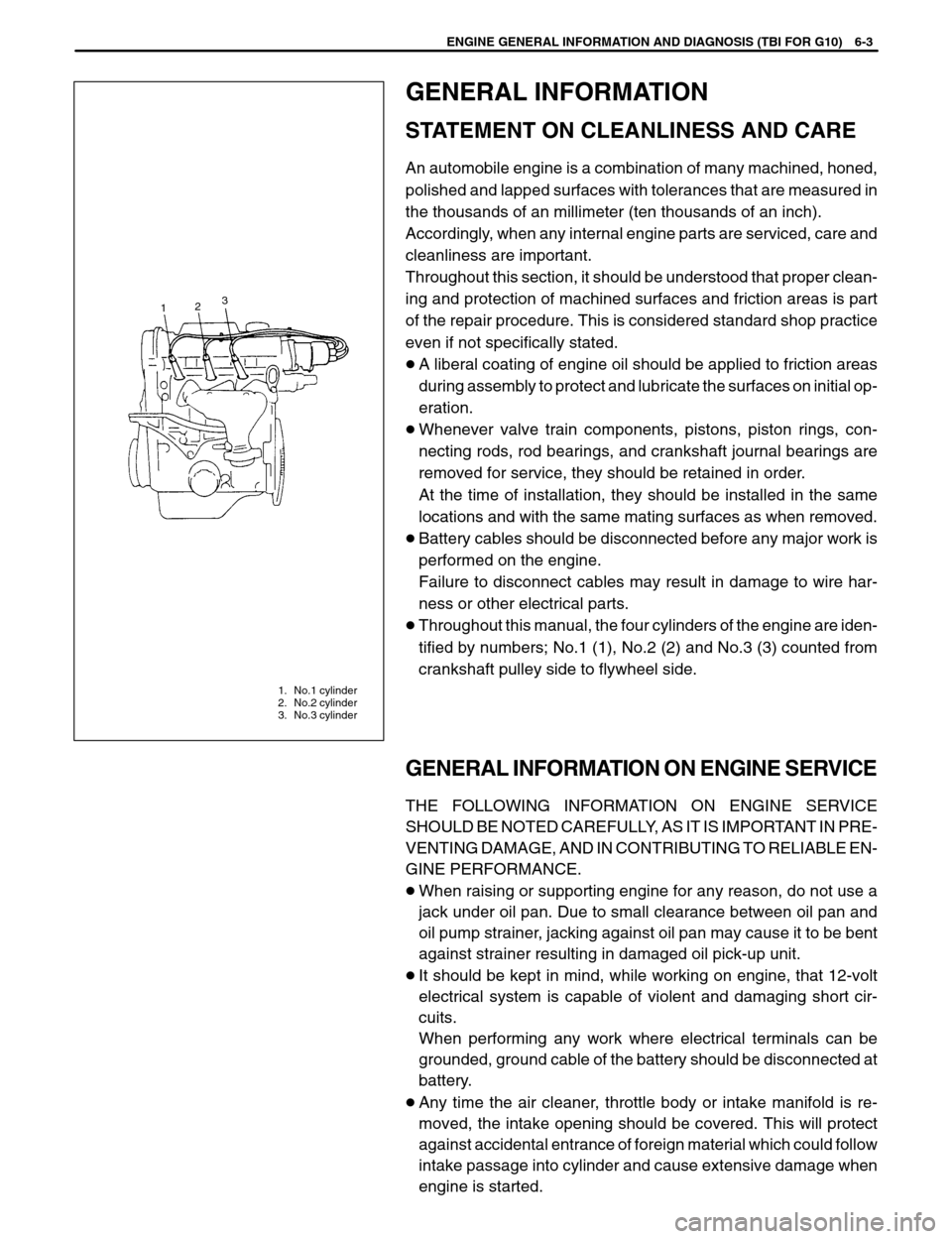
1. No.1 cylinder
2. No.2 cylinder
3. No.3 cylinder
123
ENGINE GENERAL INFORMATION AND DIAGNOSIS (TBI FOR G10) 6-3
GENERAL INFORMATION
STATEMENT ON CLEANLINESS AND CARE
An automobile engine is a combination of many machined, honed,
polished and lapped surfaces with tolerances that are measured in
the thousands of an millimeter (ten thousands of an inch).
Accordingly, when any internal engine parts are serviced, care and
cleanliness are important.
Throughout this section, it should be understood that proper clean-
ing and protection of machined surfaces and friction areas is part
of the repair procedure. This is considered standard shop practice
even if not specifically stated.
A liberal coating of engine oil should be applied to friction areas
during assembly to protect and lubricate the surfaces on initial op-
eration.
Whenever valve train components, pistons, piston rings, con-
necting rods, rod bearings, and crankshaft journal bearings are
removed for service, they should be retained in order.
At the time of installation, they should be installed in the same
locations and with the same mating surfaces as when removed.
Battery cables should be disconnected before any major work is
performed on the engine.
Failure to disconnect cables may result in damage to wire har-
ness or other electrical parts.
Throughout this manual, the four cylinders of the engine are iden-
tified by numbers; No.1 (1), No.2 (2) and No.3 (3) counted from
crankshaft pulley side to flywheel side.
GENERAL INFORMATION ON ENGINE SERVICE
THE FOLLOWING INFORMATION ON ENGINE SERVICE
SHOULD BE NOTED CAREFULLY, AS IT IS IMPORTANT IN PRE-
VENTING DAMAGE, AND IN CONTRIBUTING TO RELIABLE EN-
GINE PERFORMANCE.
When raising or supporting engine for any reason, do not use a
jack under oil pan. Due to small clearance between oil pan and
oil pump strainer, jacking against oil pan may cause it to be bent
against strainer resulting in damaged oil pick-up unit.
It should be kept in mind, while working on engine, that 12-volt
electrical system is capable of violent and damaging short cir-
cuits.
When performing any work where electrical terminals can be
grounded, ground cable of the battery should be disconnected at
battery.
Any time the air cleaner, throttle body or intake manifold is re-
moved, the intake opening should be covered. This will protect
against accidental entrance of foreign material which could follow
intake passage into cylinder and cause extensive damage when
engine is started.
Page 55 of 557
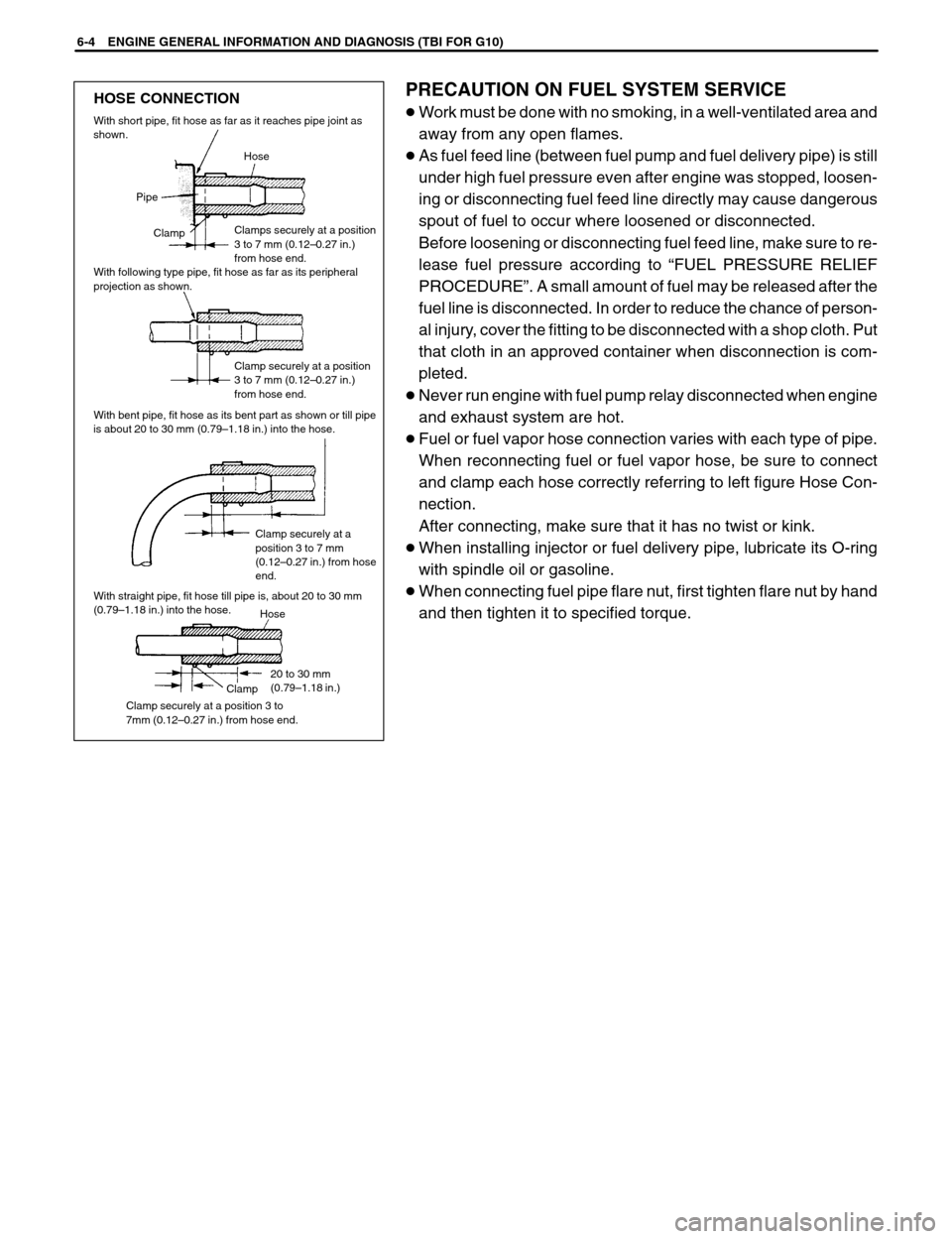
HOSE CONNECTION
Clamp securely at a position 3 to
7mm (0.12–0.27 in.) from hose end. With short pipe, fit hose as far as it reaches pipe joint as
shown.
Hose
Pipe
ClampClamps securely at a position
3 to 7 mm (0.12–0.27 in.)
from hose end.
With following type pipe, fit hose as far as its peripheral
projection as shown.
Clamp securely at a position
3 to 7 mm (0.12–0.27 in.)
from hose end.
With bent pipe, fit hose as its bent part as shown or till pipe
is about 20 to 30 mm (0.79–1.18 in.) into the hose.
Clamp securely at a
position 3 to 7 mm
(0.12–0.27 in.) from hose
end.
With straight pipe, fit hose till pipe is, about 20 to 30 mm
(0.79–1.18 in.) into the hose.
Hose
20 to 30 mm
(0.79–1.18 in.)
Clamp
6-4 ENGINE GENERAL INFORMATION AND DIAGNOSIS (TBI FOR G10)
PRECAUTION ON FUEL SYSTEM SERVICE
Work must be done with no smoking, in a well-ventilated area and
away from any open flames.
As fuel feed line (between fuel pump and fuel delivery pipe) is still
under high fuel pressure even after engine was stopped, loosen-
ing or disconnecting fuel feed line directly may cause dangerous
spout of fuel to occur where loosened or disconnected.
Before loosening or disconnecting fuel feed line, make sure to re-
lease fuel pressure according to “FUEL PRESSURE RELIEF
PROCEDURE”. A small amount of fuel may be released after the
fuel line is disconnected. In order to reduce the chance of person-
al injury, cover the fitting to be disconnected with a shop cloth. Put
that cloth in an approved container when disconnection is com-
pleted.
Never run engine with fuel pump relay disconnected when engine
and exhaust system are hot.
Fuel or fuel vapor hose connection varies with each type of pipe.
When reconnecting fuel or fuel vapor hose, be sure to connect
and clamp each hose correctly referring to left figure Hose Con-
nection.
After connecting, make sure that it has no twist or kink.
When installing injector or fuel delivery pipe, lubricate its O-ring
with spindle oil or gasoline.
When connecting fuel pipe flare nut, first tighten flare nut by hand
and then tighten it to specified torque.
Page 56 of 557
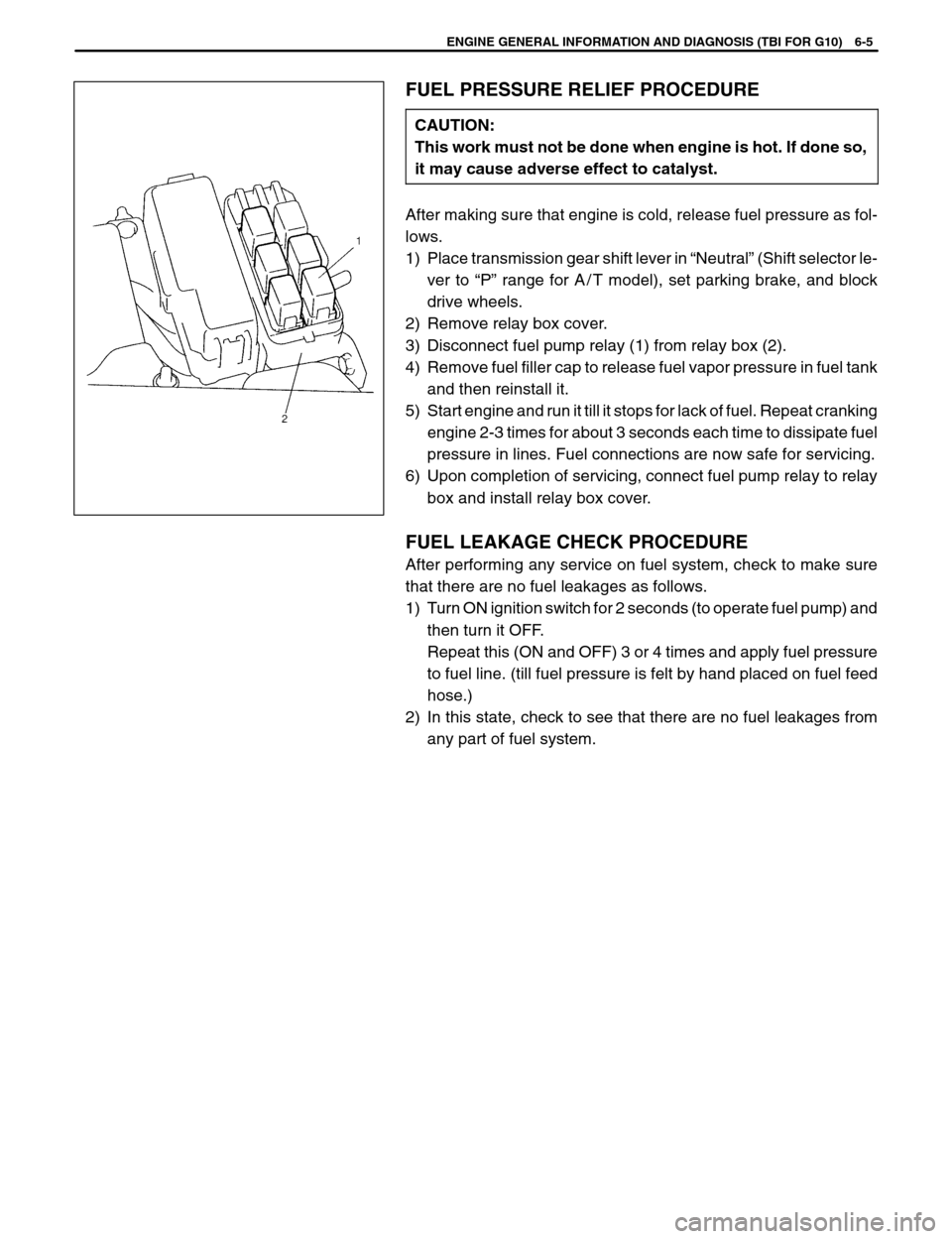
ENGINE GENERAL INFORMATION AND DIAGNOSIS (TBI FOR G10) 6-5
FUEL PRESSURE RELIEF PROCEDURE
CAUTION:
This work must not be done when engine is hot. If done so,
it may cause adverse effect to catalyst.
After making sure that engine is cold, release fuel pressure as fol-
lows.
1) Place transmission gear shift lever in “Neutral” (Shift selector le-
ver to “P” range for A / T model), set parking brake, and block
drive wheels.
2) Remove relay box cover.
3) Disconnect fuel pump relay (1) from relay box (2).
4) Remove fuel filler cap to release fuel vapor pressure in fuel tank
and then reinstall it.
5) Start engine and run it till it stops for lack of fuel. Repeat cranking
engine 2-3 times for about 3 seconds each time to dissipate fuel
pressure in lines. Fuel connections are now safe for servicing.
6) Upon completion of servicing, connect fuel pump relay to relay
box and install relay box cover.
FUEL LEAKAGE CHECK PROCEDURE
After performing any service on fuel system, check to make sure
that there are no fuel leakages as follows.
1) Turn ON ignition switch for 2 seconds (to operate fuel pump) and
then turn it OFF.
Repeat this (ON and OFF) 3 or 4 times and apply fuel pressure
to fuel line. (till fuel pressure is felt by hand placed on fuel feed
hose.)
2) In this state, check to see that there are no fuel leakages from
any part of fuel system.