Page 361 of 557
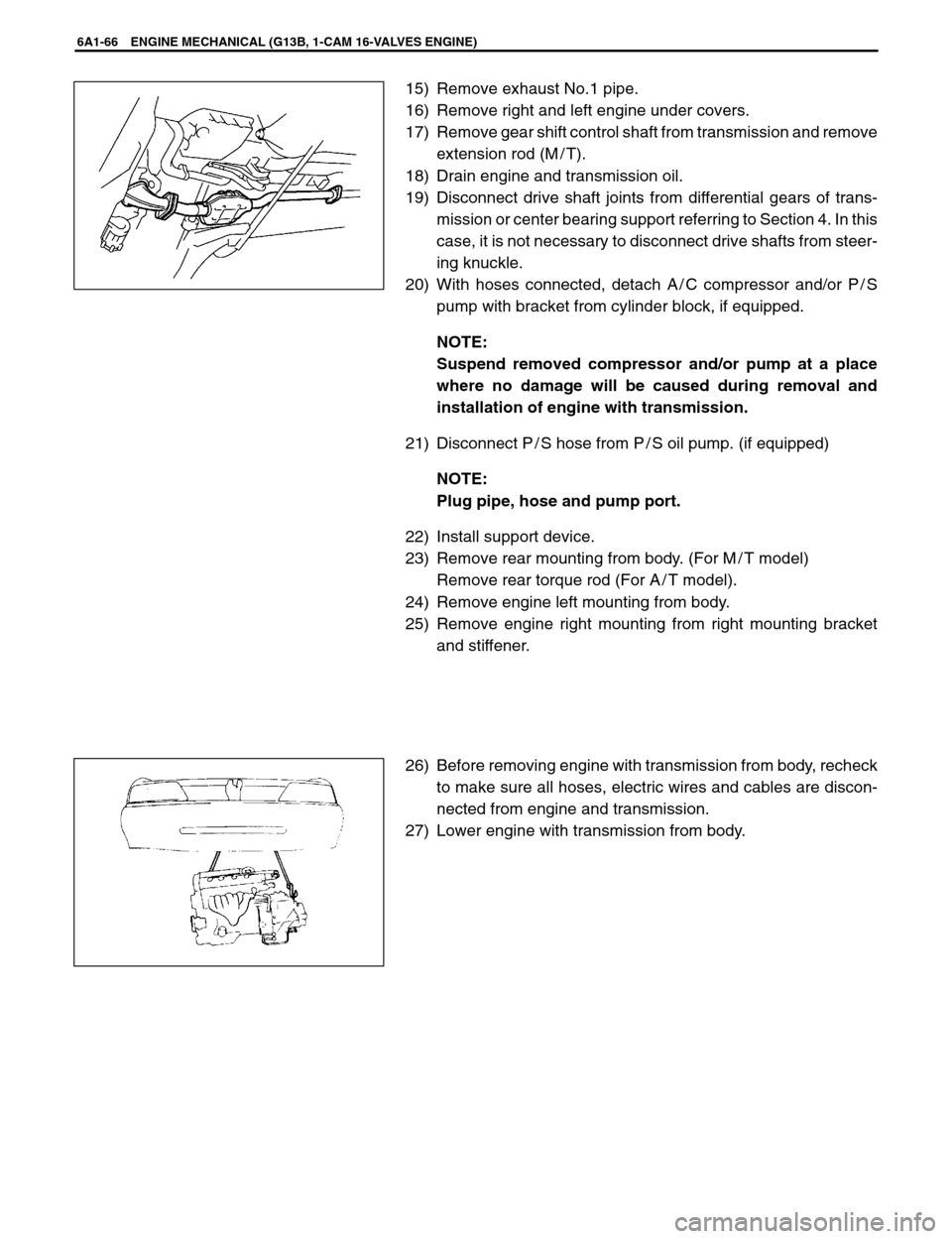
6A1-66 ENGINE MECHANICAL (G13B, 1-CAM 16-VALVES ENGINE)
15) Remove exhaust No.1 pipe.
16) Remove right and left engine under covers.
17) Remove gear shift control shaft from transmission and remove
extension rod (M / T).
18) Drain engine and transmission oil.
19) Disconnect drive shaft joints from differential gears of trans-
mission or center bearing support referring to Section 4. In this
case, it is not necessary to disconnect drive shafts from steer-
ing knuckle.
20) With hoses connected, detach A / C compressor and/or P / S
pump with bracket from cylinder block, if equipped.
NOTE:
Suspend removed compressor and/or pump at a place
where no damage will be caused during removal and
installation of engine with transmission.
21) Disconnect P / S hose from P / S oil pump. (if equipped)
NOTE:
Plug pipe, hose and pump port.
22) Install support device.
23) Remove rear mounting from body. (For M / T model)
Remove rear torque rod (For A / T model).
24) Remove engine left mounting from body.
25) Remove engine right mounting from right mounting bracket
and stiffener.
26) Before removing engine with transmission from body, recheck
to make sure all hoses, electric wires and cables are discon-
nected from engine and transmission.
27) Lower engine with transmission from body.
Page 362 of 557
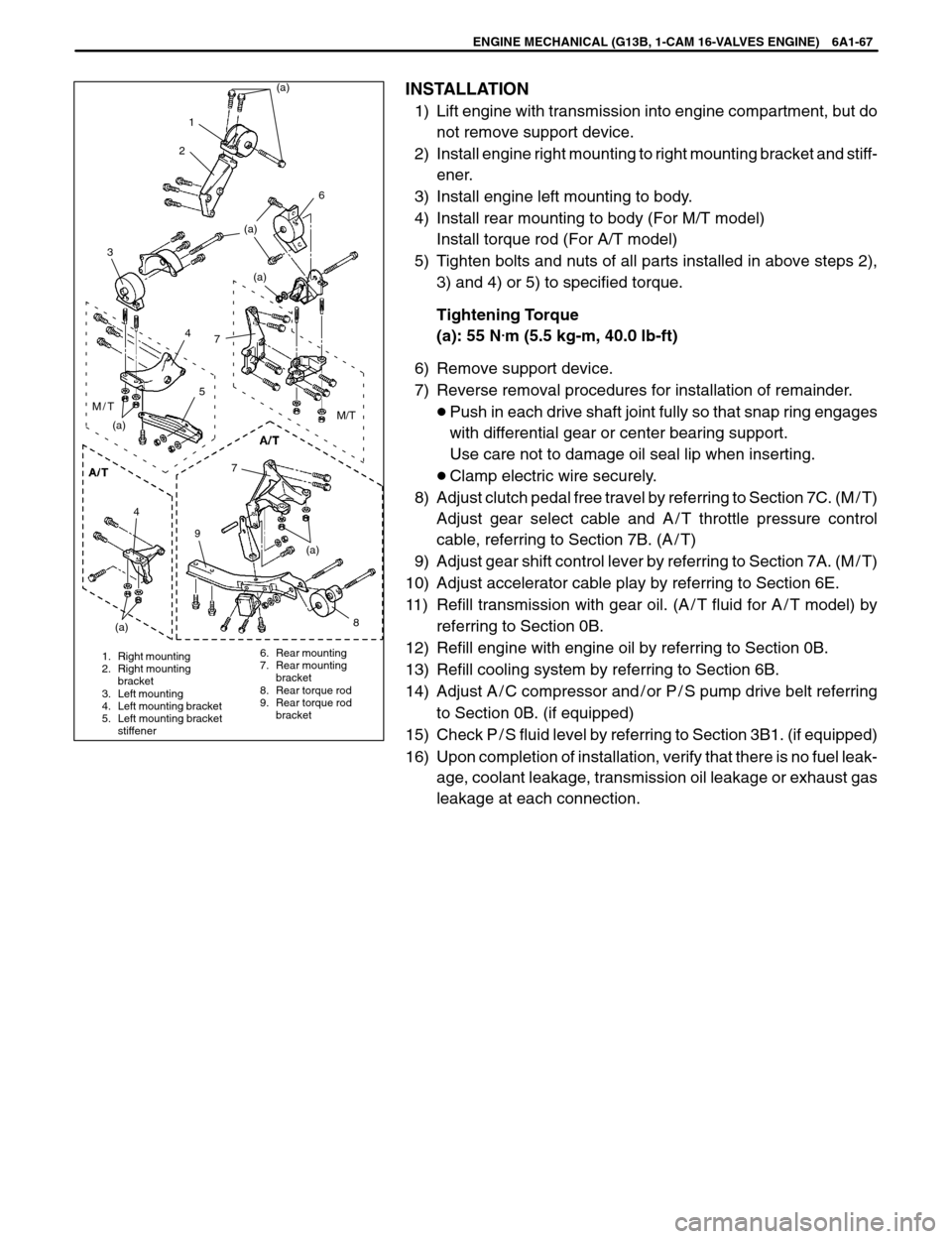
(a)
1
2
3
(a)
(a)
6
74
5
(a)
M/TM/T
9
(a)
4
7
(a)
8
1. Right mounting
2. Right mounting
bracket
3. Left mounting
4. Left mounting bracket
5. Left mounting bracket
stiffener6. Rear mounting
7. Rear mounting
bracket
8. Rear torque rod
9. Rear torque rod
bracket
ENGINE MECHANICAL (G13B, 1-CAM 16-VALVES ENGINE) 6A1-67
INSTALLATION
1) Lift engine with transmission into engine compartment, but do
not remove support device.
2) Install engine right mounting to right mounting bracket and stiff-
ener.
3) Install engine left mounting to body.
4) Install rear mounting to body (For M/T model)
Install torque rod (For A/T model)
5) Tighten bolts and nuts of all parts installed in above steps 2),
3) and 4) or 5) to specified torque.
Tightening Torque
(a): 55 N
.m (5.5 kg-m, 40.0 lb-ft)
6) Remove support device.
7) Reverse removal procedures for installation of remainder.
Push in each drive shaft joint fully so that snap ring engages
with differential gear or center bearing support.
Use care not to damage oil seal lip when inserting.
Clamp electric wire securely.
8) Adjust clutch pedal free travel by referring to Section 7C. (M / T)
Adjust gear select cable and A / T throttle pressure control
cable, referring to Section 7B. (A / T)
9) Adjust gear shift control lever by referring to Section 7A. (M / T)
10) Adjust accelerator cable play by referring to Section 6E.
11) Refill transmission with gear oil. (A / T fluid for A / T model) by
referring to Section 0B.
12) Refill engine with engine oil by referring to Section 0B.
13) Refill cooling system by referring to Section 6B.
14) Adjust A / C compressor and / or P / S pump drive belt referring
to Section 0B. (if equipped)
15) Check P / S fluid level by referring to Section 3B1. (if equipped)
16) Upon completion of installation, verify that there is no fuel leak-
age, coolant leakage, transmission oil leakage or exhaust gas
leakage at each connection.
Page 363 of 557
1. Cylinder block
2. Front oil seal:
Apply engine oil to contact part
of crankshaft with oil seal lip.
3. Main bearing:
Apply engine oil to bearing
inside surfaces.
4. Bearing cap
5. Cap bolt:
Apply engine oil to bolt and
bearing surfaces.
6. Timing pulley key7. Crankshaft:
Apply engine oil to crankshaft
journals.
8. Thrust bearing:
Set oil grooves of bearing to
crank weds.
Apply engine oil.
9. Rear oil seal:
Apply engine oil to contact part
of crankshaft with oil seal lip.10. Pin
11. Oil seal housing gasket
12. Oil seal housing
13. Housing bolt
14. Input shaft bearing
15. Flywheel
16. Flywheel bolt
: Do not reuse
: Tightening Torque
15 16
78 N.m (7.8 kg-m) for flywheel
95 N.m (9.5 kg-m) for drive plate
6A1-68 ENGINE MECHANICAL (G13B, 1-CAM 16-VALVES ENGINE)
MAIN BEARINGS, CRANKSHAFT AND CYLINDER BLOCK
Page 364 of 557
1. Flywheel bolt
2. Bolt
ENGINE MECHANICAL (G13B, 1-CAM 16-VALVES ENGINE) 6A1-69
REMOVAL
1) Remove engine assembly from body as previously outlined.
2) Remove clutch cover, clutch disc and flywheel (drive plate for
A / T).
Special Tool
(A): 09924-17810
3) Remove crankshaft pulley, timing belt and crankshaft timing
pulley.
4) Remove cylinder head assembly.
5) Remove oil pan and oil pump strainer.
6) Remove oil pump (1).
7) Remove oil seal housing.
8) Remove connecting rod bearing caps.
9) Loosen crankshaft bearing cap bolts in such order as indicated
in figure a little at a time and remove bearing caps.
10) Remove crankshaft from cylinder block.
Page 365 of 557
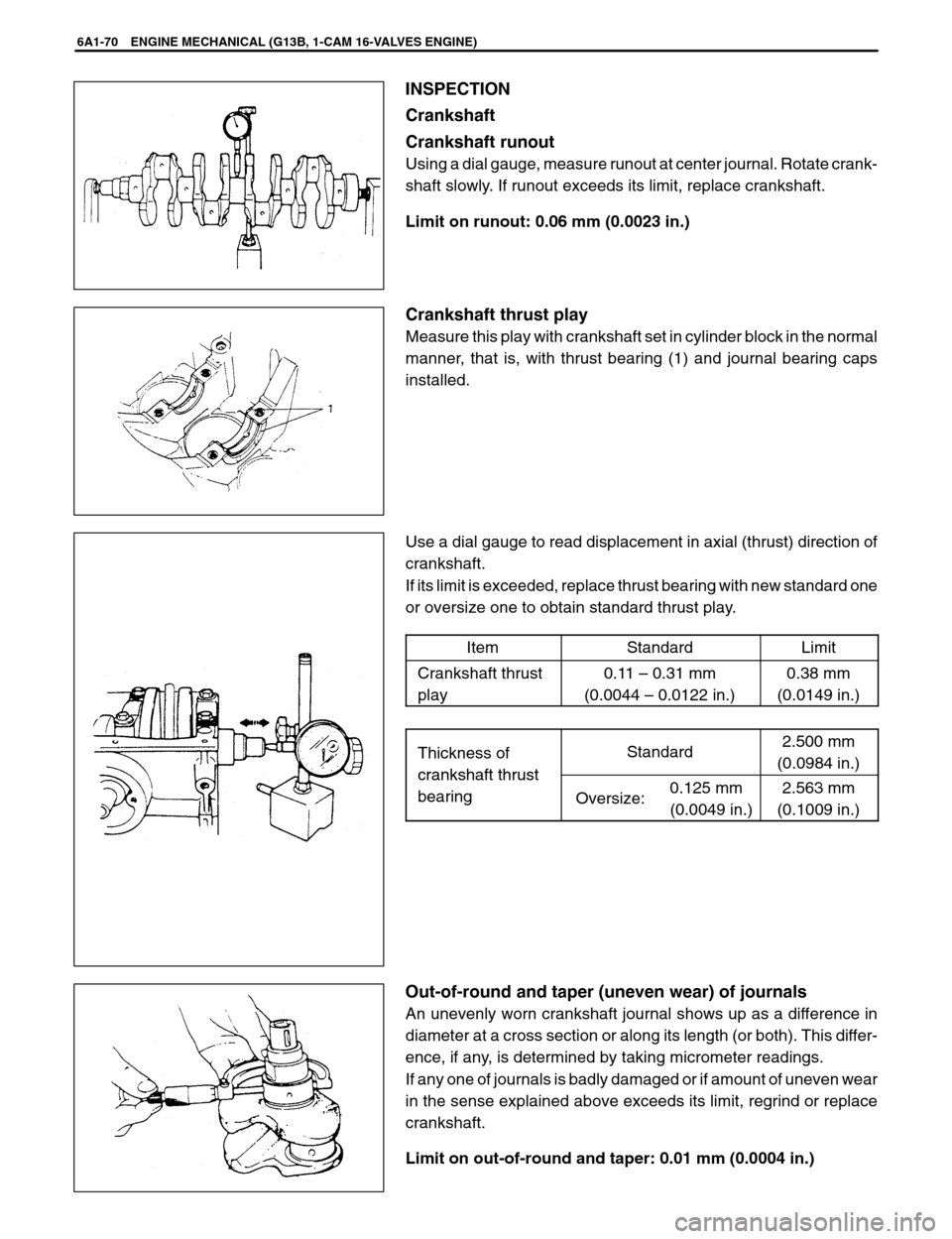
6A1-70 ENGINE MECHANICAL (G13B, 1-CAM 16-VALVES ENGINE)
INSPECTION
Crankshaft
Crankshaft runout
Using a dial gauge, measure runout at center journal. Rotate crank-
shaft slowly. If runout exceeds its limit, replace crankshaft.
Limit on runout: 0.06 mm (0.0023 in.)
Crankshaft thrust play
Measure this play with crankshaft set in cylinder block in the normal
manner, that is, with thrust bearing (1) and journal bearing caps
installed.
Use a dial gauge to read displacement in axial (thrust) direction of
crankshaft.
If its limit is exceeded, replace thrust bearing with new standard one
or oversize one to obtain standard thrust play.
Item
StandardLimit
Crankshaft thrust
play0.11 – 0.31 mm
(0.0044 – 0.0122 in.)0.38 mm
(0.0149 in.)
Thickness of
crankshaft thrust
Standard2.500 mm
(0.0984 in.)
crankshaft thrust
bearingOversize:0.125 mm
(0.0049 in.)2.563 mm
(0.1009 in.)
Out-of-round and taper (uneven wear) of journals
An unevenly worn crankshaft journal shows up as a difference in
diameter at a cross section or along its length (or both). This differ-
ence, if any, is determined by taking micrometer readings.
If any one of journals is badly damaged or if amount of uneven wear
in the sense explained above exceeds its limit, regrind or replace
crankshaft.
Limit on out-of-round and taper: 0.01 mm (0.0004 in.)
Page 366 of 557
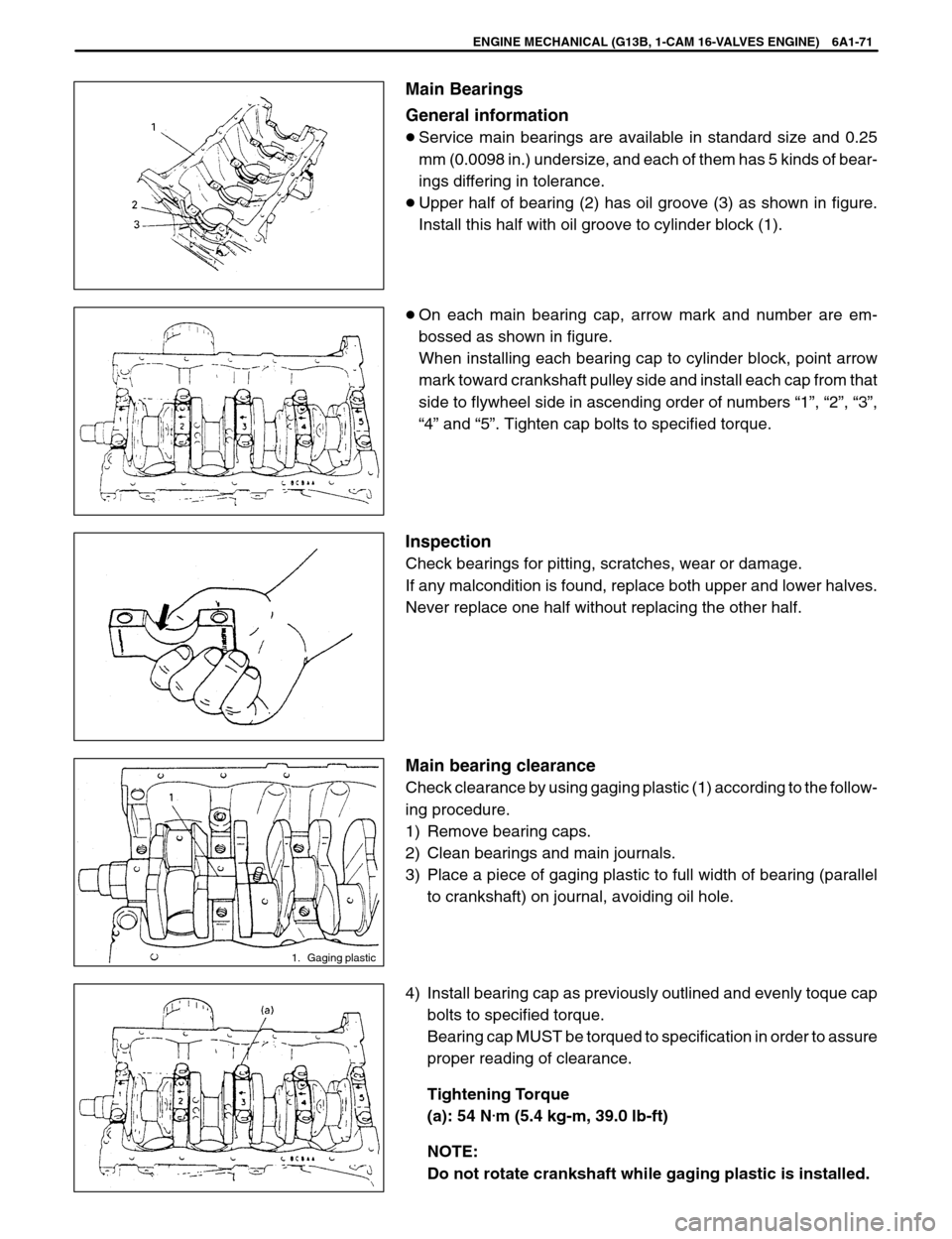
1. Gaging plastic
ENGINE MECHANICAL (G13B, 1-CAM 16-VALVES ENGINE) 6A1-71
Main Bearings
General information
Service main bearings are available in standard size and 0.25
mm (0.0098 in.) undersize, and each of them has 5 kinds of bear-
ings differing in tolerance.
Upper half of bearing (2) has oil groove (3) as shown in figure.
Install this half with oil groove to cylinder block (1).
On each main bearing cap, arrow mark and number are em-
bossed as shown in figure.
When installing each bearing cap to cylinder block, point arrow
mark toward crankshaft pulley side and install each cap from that
side to flywheel side in ascending order of numbers “1”, “2”, “3”,
“4” and “5”. Tighten cap bolts to specified torque.
Inspection
Check bearings for pitting, scratches, wear or damage.
If any malcondition is found, replace both upper and lower halves.
Never replace one half without replacing the other half.
Main bearing clearance
Check clearance by using gaging plastic (1) according to the follow-
ing procedure.
1) Remove bearing caps.
2) Clean bearings and main journals.
3) Place a piece of gaging plastic to full width of bearing (parallel
to crankshaft) on journal, avoiding oil hole.
4) Install bearing cap as previously outlined and evenly toque cap
bolts to specified torque.
Bearing cap MUST be torqued to specification in order to assure
proper reading of clearance.
Tightening Torque
(a): 54 N
.m (5.4 kg-m, 39.0 lb-ft)
NOTE:
Do not rotate crankshaft while gaging plastic is installed.
Page 367 of 557
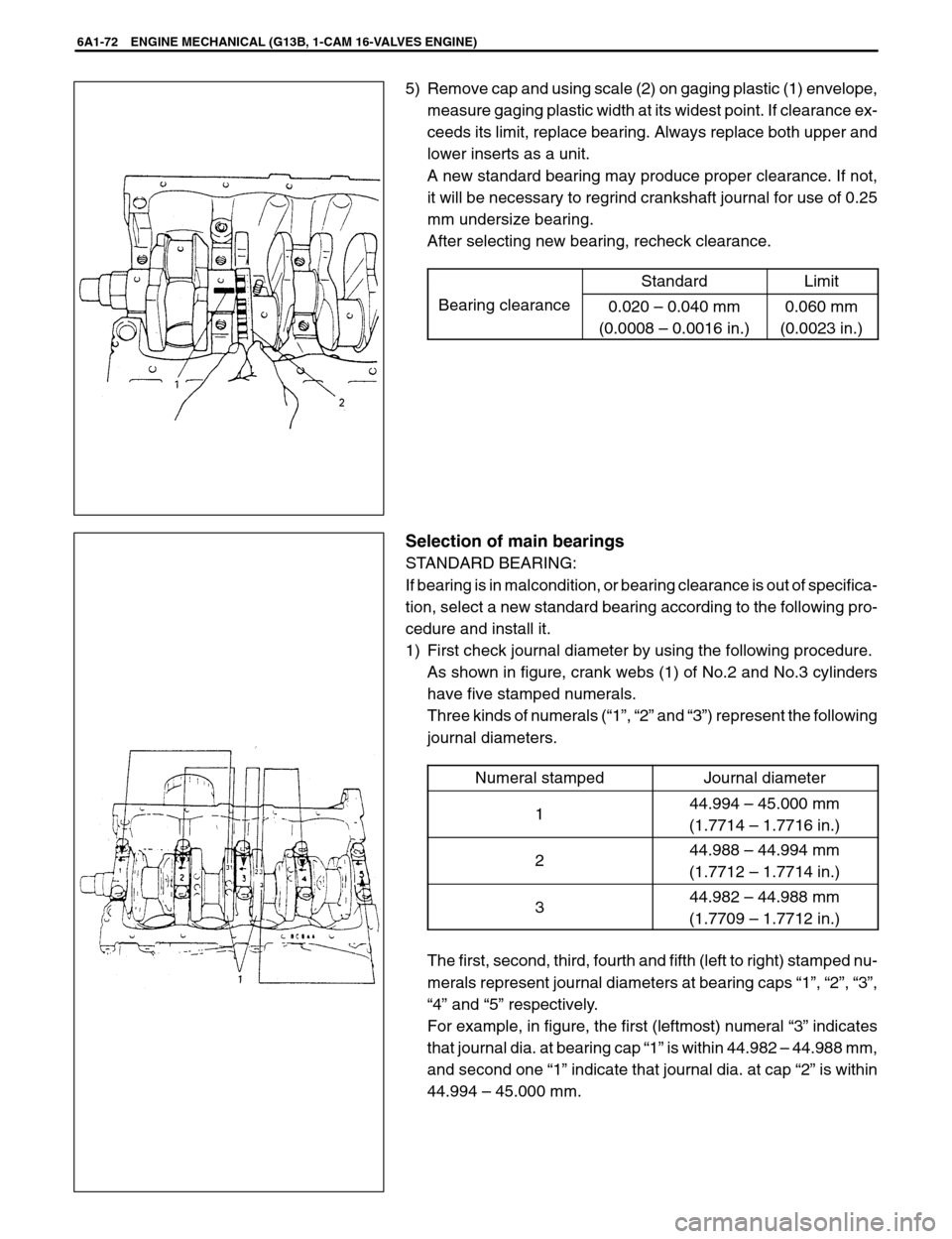
6A1-72 ENGINE MECHANICAL (G13B, 1-CAM 16-VALVES ENGINE)
5) Remove cap and using scale (2) on gaging plastic (1) envelope,
measure gaging plastic width at its widest point. If clearance ex-
ceeds its limit, replace bearing. Always replace both upper and
lower inserts as a unit.
A new standard bearing may produce proper clearance. If not,
it will be necessary to regrind crankshaft journal for use of 0.25
mm undersize bearing.
After selecting new bearing, recheck clearance.
StandardLimit
Bearing clearance0.020 – 0.040 mm
(0.0008 – 0.0016 in.)0.060 mm
(0.0023 in.)
Selection of main bearings
STANDARD BEARING:
If bearing is in malcondition, or bearing clearance is out of specifica-
tion, select a new standard bearing according to the following pro-
cedure and install it.
1) First check journal diameter by using the following procedure.
As shown in figure, crank webs (1) of No.2 and No.3 cylinders
have five stamped numerals.
Three kinds of numerals (“1”, “2” and “3”) represent the following
journal diameters.
Numeral stamped
Journal diameter
144.994 – 45.000 mm
(1.7714 – 1.7716 in.)
244.988 – 44.994 mm
(1.7712 – 1.7714 in.)
344.982 – 44.988 mm
(1.7709 – 1.7712 in.)
The first, second, third, fourth and fifth (left to right) stamped nu-
merals represent journal diameters at bearing caps “1”, “2”, “3”,
“4” and “5” respectively.
For example, in figure, the first (leftmost) numeral “3” indicates
that journal dia. at bearing cap “1” is within 44.982 – 44.988 mm,
and second one “1” indicate that journal dia. at cap “2” is within
44.994 – 45.000 mm.
Page 368 of 557
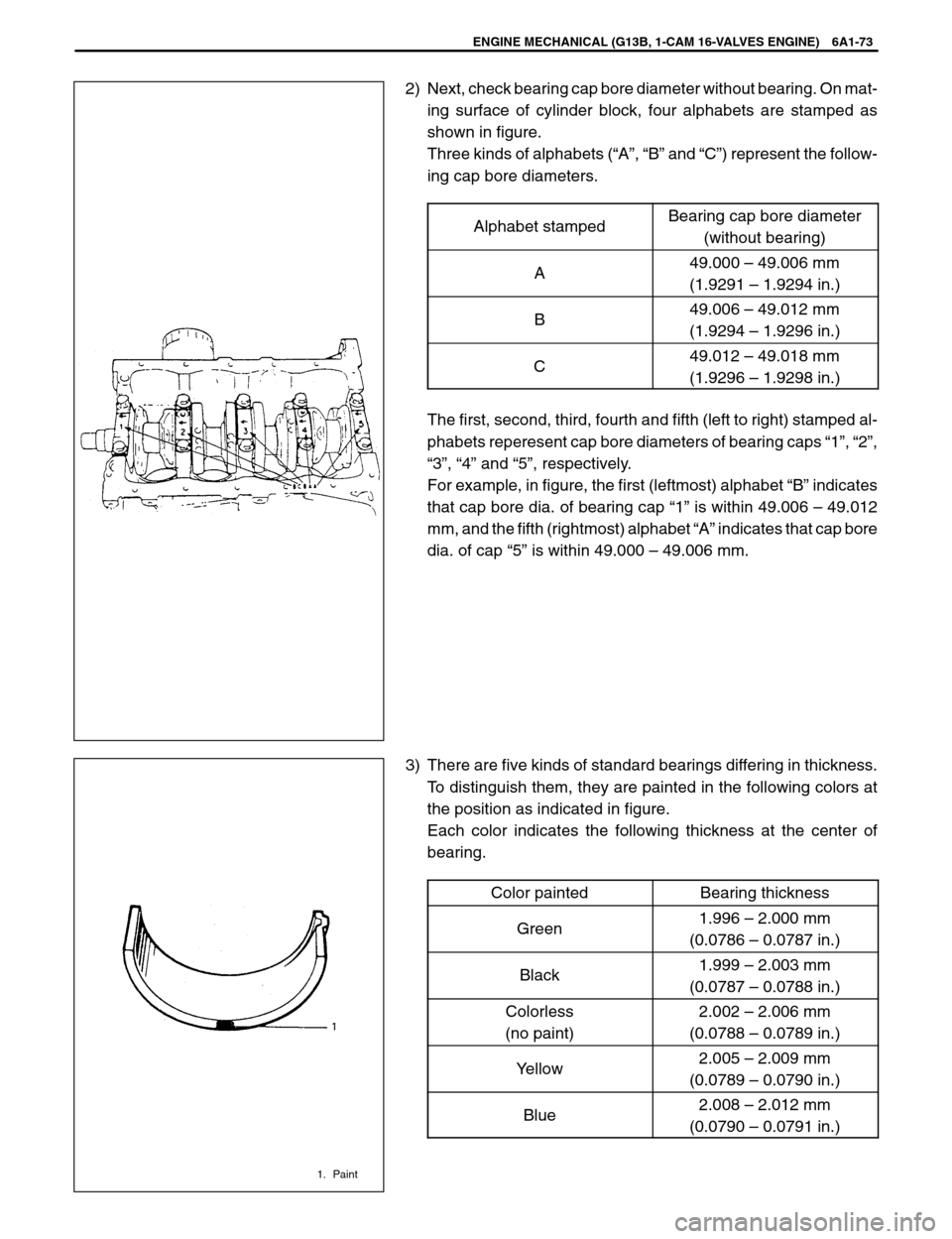
1. Paint
ENGINE MECHANICAL (G13B, 1-CAM 16-VALVES ENGINE) 6A1-73
2) Next, check bearing cap bore diameter without bearing. On mat-
ing surface of cylinder block, four alphabets are stamped as
shown in figure.
Three kinds of alphabets (“A”, “B” and “C”) represent the follow-
ing cap bore diameters.
Alphabet stamped
Bearing cap bore diameter
(without bearing)
A49.000 – 49.006 mm
(1.9291 – 1.9294 in.)
B49.006 – 49.012 mm
(1.9294 – 1.9296 in.)
C49.012 – 49.018 mm
(1.9296 – 1.9298 in.)
The first, second, third, fourth and fifth (left to right) stamped al-
phabets reperesent cap bore diameters of bearing caps “1”, “2”,
“3”, “4” and “5”, respectively.
For example, in figure, the first (leftmost) alphabet “B” indicates
that cap bore dia. of bearing cap “1” is within 49.006 – 49.012
mm, and the fifth (rightmost) alphabet “A” indicates that cap bore
dia. of cap “5” is within 49.000 – 49.006 mm.
3) There are five kinds of standard bearings differing in thickness.
To distinguish them, they are painted in the following colors at
the position as indicated in figure.
Each color indicates the following thickness at the center of
bearing.
Color painted
Bearing thickness
Green1.996 – 2.000 mm
(0.0786 – 0.0787 in.)
Black1.999 – 2.003 mm
(0.0787 – 0.0788 in.)
Colorless
(no paint)2.002 – 2.006 mm
(0.0788 – 0.0789 in.)
Yellow2.005 – 2.009 mm
(0.0789 – 0.0790 in.)
Blue2.008 – 2.012 mm
(0.0790 – 0.0791 in.)