Page 7 of 557
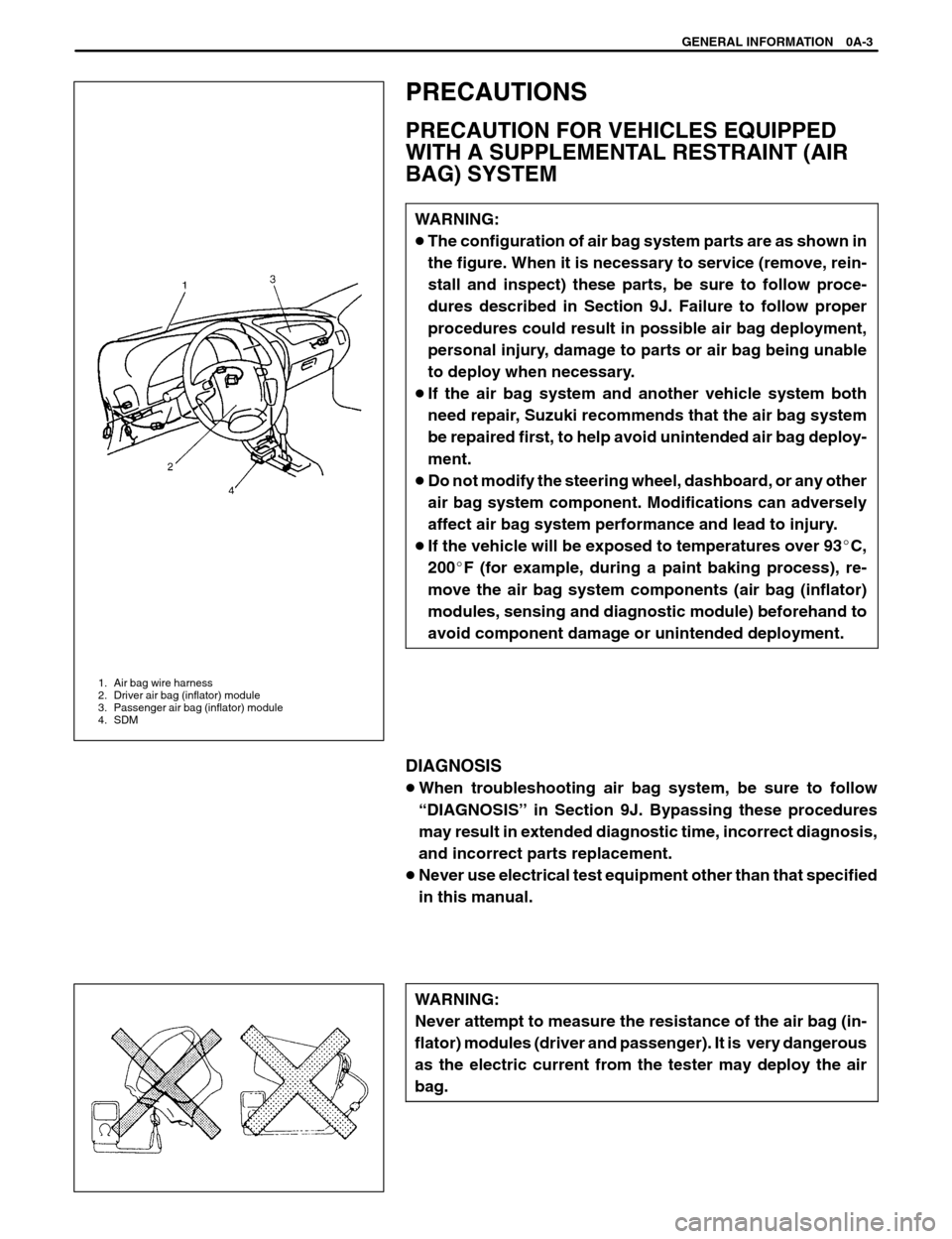
1. Air bag wire harness
2. Driver air bag (inflator) module
3. Passenger air bag (inflator) module
4. SDM
GENERAL INFORMATION 0A-3
PRECAUTIONS
PRECAUTION FOR VEHICLES EQUIPPED
WITH A SUPPLEMENTAL RESTRAINT (AIR
BAG) SYSTEM
WARNING:
The configuration of air bag system parts are as shown in
the figure. When it is necessary to service (remove, rein-
stall and inspect) these parts, be sure to follow proce-
dures described in Section 9J. Failure to follow proper
procedures could result in possible air bag deployment,
personal injury, damage to parts or air bag being unable
to deploy when necessary.
If the air bag system and another vehicle system both
need repair, Suzuki recommends that the air bag system
be repaired first, to help avoid unintended air bag deploy-
ment.
Do not modify the steering wheel, dashboard, or any other
air bag system component. Modifications can adversely
affect air bag system performance and lead to injury.
If the vehicle will be exposed to temperatures over 93C,
200F (for example, during a paint baking process), re-
move the air bag system components (air bag (inflator)
modules, sensing and diagnostic module) beforehand to
avoid component damage or unintended deployment.
DIAGNOSIS
When troubleshooting air bag system, be sure to follow
“DIAGNOSIS” in Section 9J. Bypassing these procedures
may result in extended diagnostic time, incorrect diagnosis,
and incorrect parts replacement.
Never use electrical test equipment other than that specified
in this manual.
WARNING:
Never attempt to measure the resistance of the air bag (in-
flator) modules (driver and passenger). It is very dangerous
as the electric current from the tester may deploy the air
bag.
Page 29 of 557
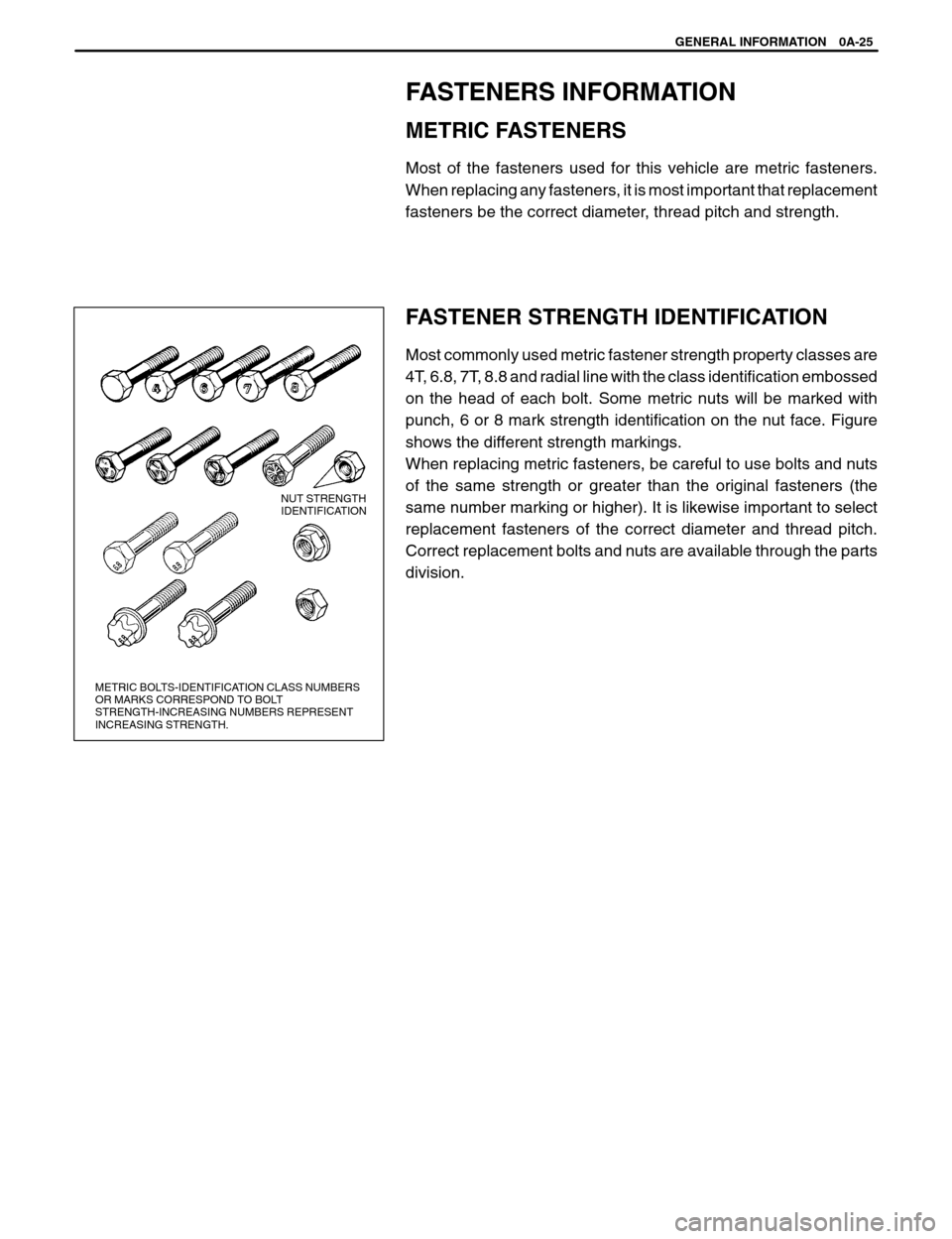
GENERAL INFORMATION 0A-25
METRIC BOLTS-IDENTIFICATION CLASS NUMBERS
OR MARKS CORRESPOND TO BOLT
STRENGTH-INCREASING NUMBERS REPRESENT
INCREASING STRENGTH.NUT STRENGTH
IDENTIFICATION
FASTENERS INFORMATION
METRIC FASTENERS
Most of the fasteners used for this vehicle are metric fasteners.
When replacing any fasteners, it is most important that replacement
fasteners be the correct diameter, thread pitch and strength.
FASTENER STRENGTH IDENTIFICATION
Most commonly used metric fastener strength property classes are
4T, 6.8, 7T, 8.8 and radial line with the class identification embossed
on the head of each bolt. Some metric nuts will be marked with
punch, 6 or 8 mark strength identification on the nut face. Figure
shows the different strength markings.
When replacing metric fasteners, be careful to use bolts and nuts
of the same strength or greater than the original fasteners (the
same number marking or higher). It is likewise important to select
replacement fasteners of the correct diameter and thread pitch.
Correct replacement bolts and nuts are available through the parts
division.
Page 35 of 557
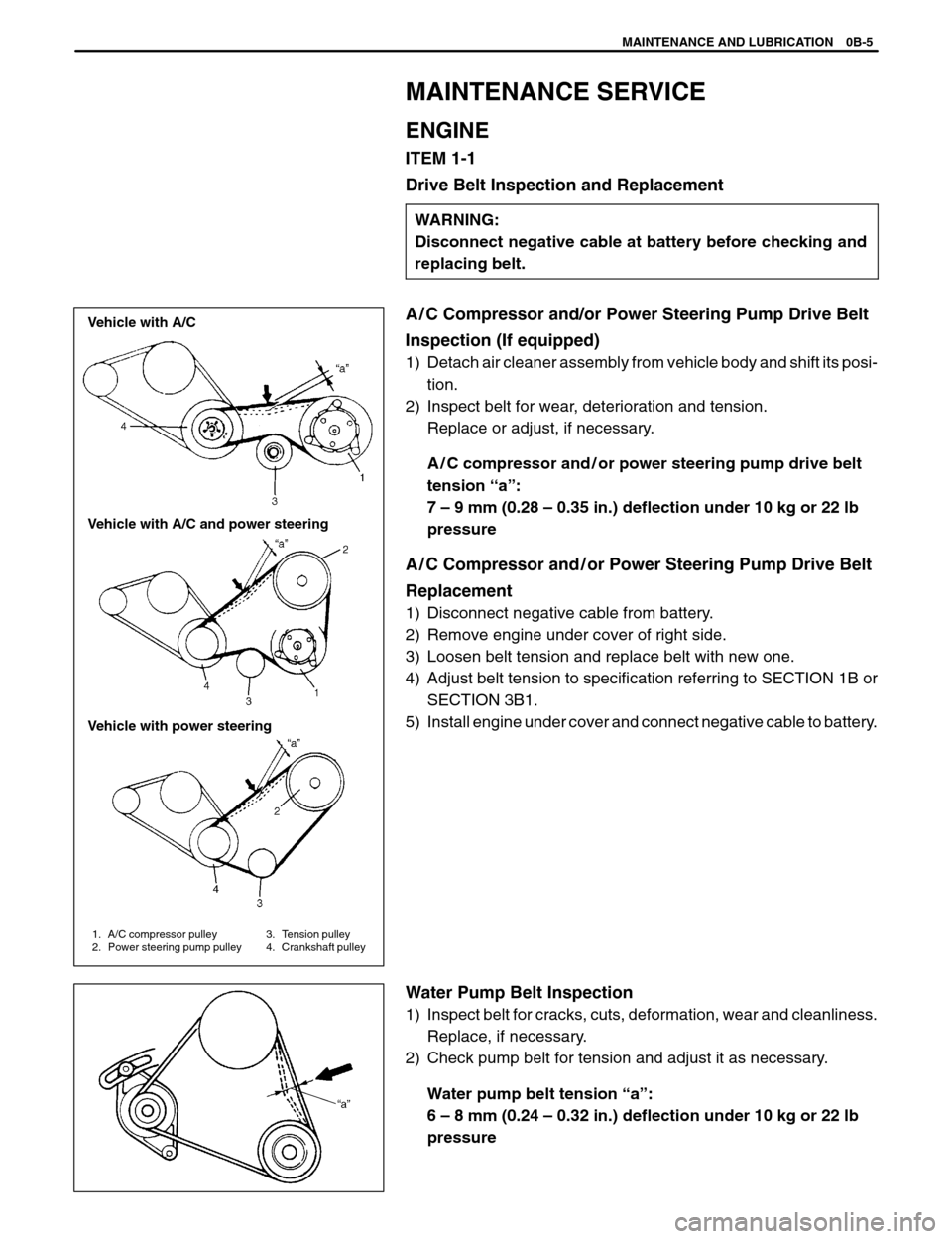
Vehicle with A/C
Vehicle with A/C and power steering
Vehicle with power steering
1. A/C compressor pulley
2. Power steering pump pulley3. Tension pulley
4. Crankshaft pulley
MAINTENANCE AND LUBRICATION 0B-5
MAINTENANCE SERVICE
ENGINE
ITEM 1-1
Drive Belt Inspection and Replacement
WARNING:
Disconnect negative cable at battery before checking and
replacing belt.
A / C Compressor and/or Power Steering Pump Drive Belt
Inspection (If equipped)
1) Detach air cleaner assembly from vehicle body and shift its posi-
tion.
2) Inspect belt for wear, deterioration and tension.
Replace or adjust, if necessary.
A / C compressor and / or power steering pump drive belt
tension “a”:
7 – 9 mm (0.28 – 0.35 in.) deflection under 10 kg or 22 lb
pressure
A / C Compressor and / or Power Steering Pump Drive Belt
Replacement
1) Disconnect negative cable from battery.
2) Remove engine under cover of right side.
3) Loosen belt tension and replace belt with new one.
4) Adjust belt tension to specification referring to SECTION 1B or
SECTION 3B1.
5) Install engine under cover and connect negative cable to battery.
Water Pump Belt Inspection
1) Inspect belt for cracks, cuts, deformation, wear and cleanliness.
Replace, if necessary.
2) Check pump belt for tension and adjust it as necessary.
Water pump belt tension “a”:
6 – 8 mm (0.24 – 0.32 in.) deflection under 10 kg or 22 lb
pressure
Page 36 of 557
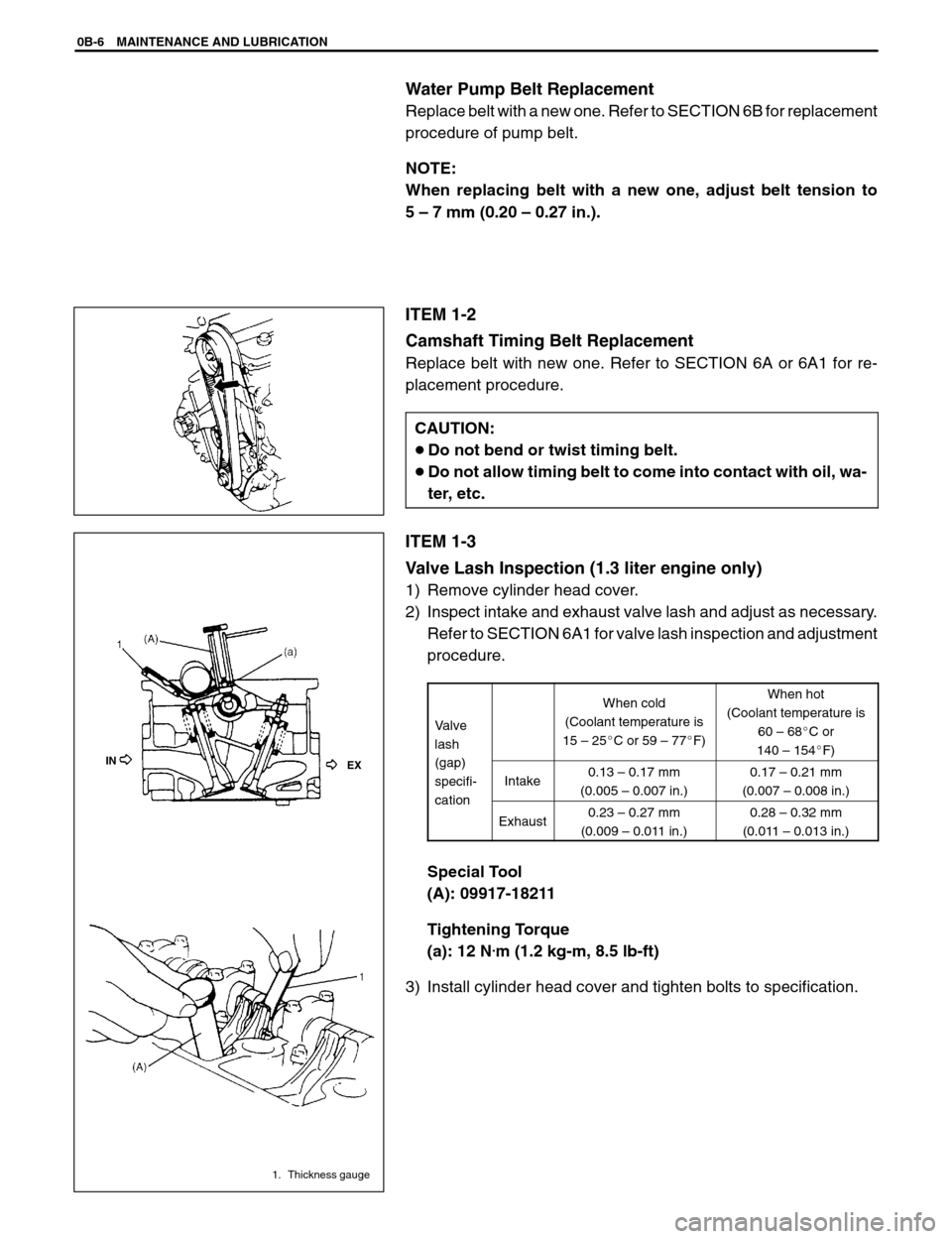
1. Thickness gauge IN
EX
0B-6 MAINTENANCE AND LUBRICATION
Water Pump Belt Replacement
Replace belt with a new one. Refer to SECTION 6B for replacement
procedure of pump belt.
NOTE:
When replacing belt with a new one, adjust belt tension to
5 – 7 mm (0.20 – 0.27 in.).
ITEM 1-2
Camshaft Timing Belt Replacement
Replace belt with new one. Refer to SECTION 6A or 6A1 for re-
placement procedure.
CAUTION:
Do not bend or twist timing belt.
Do not allow timing belt to come into contact with oil, wa-
ter, etc.
ITEM 1-3
Valve Lash Inspection (1.3 liter engine only)
1) Remove cylinder head cover.
2) Inspect intake and exhaust valve lash and adjust as necessary.
Refer to SECTION 6A1 for valve lash inspection and adjustment
procedure.
Valve
lash
(gap)
When cold
(Coolant temperature is
15 – 25C or 59 – 77F)When hot
(Coolant temperature is
60 – 68C or
140 – 154F)
(gap)
specifi-
cation
Intake0.13 – 0.17 mm
(0.005 – 0.007 in.)0.17 – 0.21 mm
(0.007 – 0.008 in.)
cation
Exhaust0.23 – 0.27 mm
(0.009 – 0.011 in.)0.28 – 0.32 mm
(0.011 – 0.013 in.)
Special Tool
(A): 09917-18211
Tightening Torque
(a): 12 N
.m (1.2 kg-m, 8.5 lb-ft)
3) Install cylinder head cover and tighten bolts to specification.
Page 40 of 557
0B-10 MAINTENANCE AND LUBRICATION
IGNITION SYSTEM
ITEM 2-1
Spark Plugs Replacement
Replace spark plugs with new ones referring to SECTION 6F or
6F1.
ITEM 2-2
Distributor Cap and Rotor Inspection (if equipped)
Check distributor cap and rubber caps for cracks.
Clean dusty and stained parts using a dry, soft cloth.
Check center electrode and terminals for wear.
Check rotor for cracks and its electrode for wear.
Repair or replace any component which is found to be in malcondi-
tion.
FUEL SYSTEM
ITEM 3-1
Air Cleaner Filter Inspection
1) Take out air cleaner filter as follows.
For 1.0 liter engine:
i) Remove air cleaner upper case after removing case nut and
clamps.
ii) Remove air cleaner filter.
For 1.3 liter engine:
i) Disconnect air cleaner outlet hose from case after loosening
its clamp and removing bolt (1) shown in figure.
ii) Remove air cleaner case cap (3) from case by unhooking its
clamps (2), then take out air cleaner filter.
Page 41 of 557
1.0 liter engine
1.3 liter engine
MAINTENANCE AND LUBRICATION 0B-11
2) Visually check that air cleaner filter is not excessively dirty, dam-
aged or oily.
3) Clean filter with compressed air from air outlet side of filter.
4) Install air cleaner filter into case.
5) Clamp case cap securely and install hose to case and bracket
if removed.
Air Cleaner Filter Replacement
Replace air cleaner filter with new one according to steps 1), 4) and
5) of Air Cleaner Filter Inspection.
ITEM 3-2
Fuel Lines Inspection
Check fuel lines for loose connection, deterioration or damage
which could cause leakage.
Make sure all clamps are secure.
Replace any damaged or deteriorate parts.
There should be no sign of fuel leakage or moisture at any fuel
connection.
ITEM 3-3
Fuel Tank Inspection
Check fuel tank for damage, cracks, fuel leakage, corrosion and
tank bolts looseness.
If a problem is found, repair or replace.
Page 48 of 557
1. Oil level gauge
2. FULL HOT mark
3. LOW HOT mark
4. FULL COLD mark
5. LOW COLD mark
1. Drain plug
0B-18 MAINTENANCE AND LUBRICATION
ITEM 6-9
Automatic Transmission
[Fluid level inspection]
1) Inspect transmission case for evidence of fluid leakage.
Repair leaky point, if any.
2) Make sure that vehicle is placed level for fluid level check.
3) Check fluid level.
For fluid level checking procedure, refer to ON-VEHICLE SER-
VICE in SECTION 7B and be sure to perform it under specified
conditions. If fluid level is low, replenish specified fluid.
[Fluid change]
1) Perform steps 1) and 2) of above Fluid Level Inspection.
2) Change fluid. For its procedure, refer to ON-VEHICLE SER-
VICE in SECTION 7B.
CAUTION:
Use of specified fluid is absolutely necessary.
[Fluid cooler hose change]
Replace inlet and outlet hoses (1) of cooler hose and their clamps.
For replacement procedure, refer to ON-VEHICLE SERVICE in
SECTION 7B.
Page 60 of 557
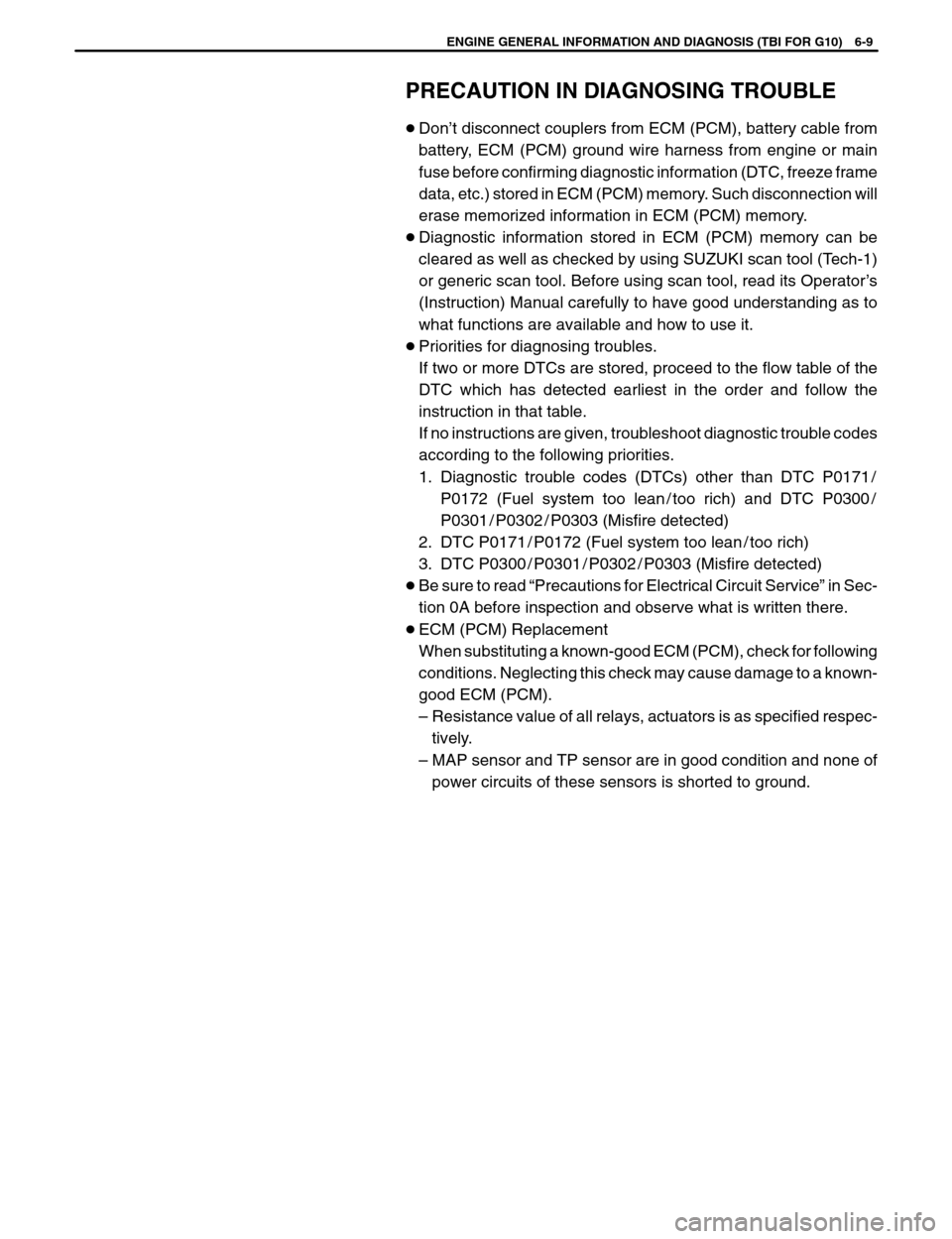
ENGINE GENERAL INFORMATION AND DIAGNOSIS (TBI FOR G10) 6-9
PRECAUTION IN DIAGNOSING TROUBLE
Don’t disconnect couplers from ECM (PCM), battery cable from
battery, ECM (PCM) ground wire harness from engine or main
fuse before confirming diagnostic information (DTC, freeze frame
data, etc.) stored in ECM (PCM) memory. Such disconnection will
erase memorized information in ECM (PCM) memory.
Diagnostic information stored in ECM (PCM) memory can be
cleared as well as checked by using SUZUKI scan tool (Tech-1)
or generic scan tool. Before using scan tool, read its Operator’s
(Instruction) Manual carefully to have good understanding as to
what functions are available and how to use it.
Priorities for diagnosing troubles.
If two or more DTCs are stored, proceed to the flow table of the
DTC which has detected earliest in the order and follow the
instruction in that table.
If no instructions are given, troubleshoot diagnostic trouble codes
according to the following priorities.
1. Diagnostic trouble codes (DTCs) other than DTC P0171 /
P0172 (Fuel system too lean / too rich) and DTC P0300 /
P0301 / P0302 / P0303 (Misfire detected)
2. DTC P0171 / P0172 (Fuel system too lean / too rich)
3. DTC P0300 / P0301 / P0302 / P0303 (Misfire detected)
Be sure to read “Precautions for Electrical Circuit Service” in Sec-
tion 0A before inspection and observe what is written there.
ECM (PCM) Replacement
When substituting a known-good ECM (PCM), check for following
conditions. Neglecting this check may cause damage to a known-
good ECM (PCM).
–Resistance value of all relays, actuators is as specified respec-
tively.
–MAP sensor and TP sensor are in good condition and none of
power circuits of these sensors is shorted to ground.