Page 217 of 648
Page 218 of 648
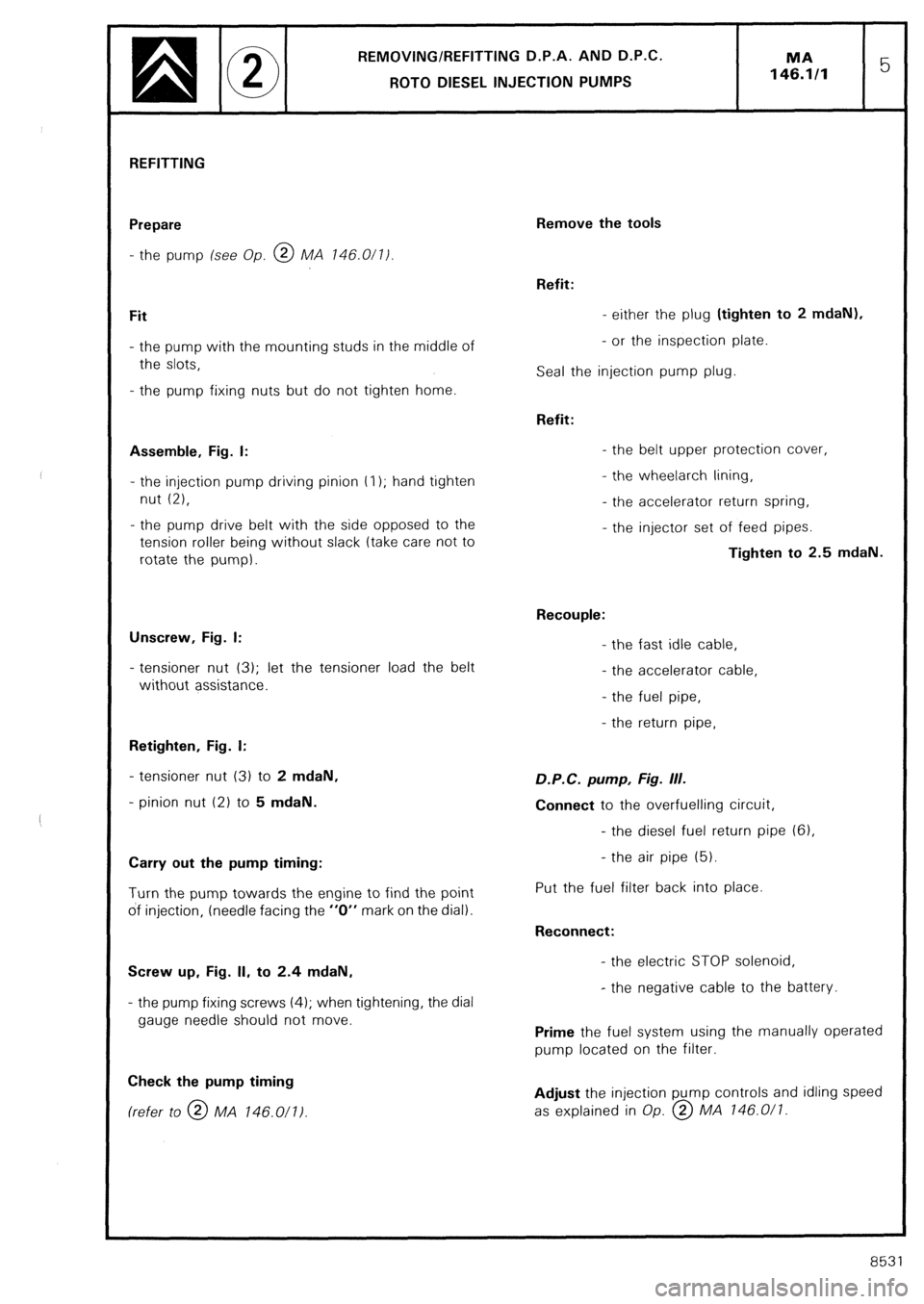
REMOVING/REFITTING D.P.A. AND D.P.C.
ROT0 DIESEL INJECTION PUMPS MA
146.1/l 5
REFITTING
Prepare
- the pump (see Op. @ MA 146.0/l/
Fit
- the pump with the mounting studs in the middle of
the slots,
- the pump fixing nuts but do not tighten home.
Assemble, Fig. I:
- the injection pump driving pinion t I); hand tighten
nut (2),
- the pump drive belt with the side opposed to the
tension roller being without slack (take care not to
rotate the pump).
Unscrew, Fig. I:
- tensioner nut (3); let the tensioner load the belt
without assistance.
Retighten, Fig. I:
- tensioner nut (3) to 2 mdaN,
- pinion nut (2) to 5 mdaN.
Carry out the pump timing:
Turn the pump towards the engine to find the point
of injection, (needle facing the “0” mark on the dial).
Screw up, Fig. II, to 2.4 mdaN,
- the pump fixing screws (4); when tightening, the dial
gauge needle should not move.
Check the pump timing (refer to @ MA 146.011)
Remove the tools
Refit:
- either the plug (tighten to 2 mdaN),
- or the inspection plate.
Seal the injection pump plug.
Refit:
- the belt upper protection cover,
- the wheelarch lining,
- the accelerator return spring,
- the injector set of feed pipes.
Tighten to 2.5 mdaN.
Recouple:
- the fast idle cable,
- the accelerator cable,
- the fuel pipe,
- the return pipe, D.P.C. pump, Fig. III.
Connect to the overfuelling circuit,
- the diesel fuel return pipe (61,
- the air pipe (5).
Put the fuel filter back into place.
Reconnect:
- the electric STOP solenoid,
- the negative cable to the battery.
Prime the fuel system using the manually operated
pump located on the filter.
Adjust the injection pump controls and idling speed
as explained in Op. @ MA 146.0/l.
8531
Page 219 of 648
TAO3 : 470 mbar
MAXI
T3 : 440 mbar
5000 tr/mn
0.025 + 0.100 mm
I I
n-r 0 :m”_
/d
0,7 -+ 2,1 bar
0,080 --) 0,165 mm
8531
Page 220 of 648
I I
Garrett TAO3 + M 251648
TO25 -+ M 251669
I
I
TAO3 : 3700 tr/mn
720 mbar MAXI
TO25 : 3900 tr/mn
800 mbar MAXI
MAXI
Page 221 of 648
CARBURATION
SPECIFICATION AND PARTICULAR FEATURES
\>
Page 222 of 648

SPECIFICATION AND SPECIAL FEATURES
OF THE AIR SUPPLY SYSTEM
Engines types 829.A5 and J6T.A500 are fitted with a device regulating the temperature of intake air.
This device has been designed for maintaining a minimum temperature of the air drawn into the carburettor
It consists of a thermal sensor and a vacuum capsule operating a flap. Thermal source
The thermal sensor is located in the pipe connecting the air filter to the inlet manifold of the carburettor
This bi-metal type thermostat, is subjected to the inlet air temperature
It controls the opening of valves allowing passage for a depression towards the capsule
This depression is picked up by a union having a calibrated orifice, fitted to the pipe connecting the oil breather
to the intake manifold of the carburettor, and by a T-shaped union situated near the carburettor base plate, so
as to have an action over the engine load.
The thermal sensor allows the depression to circulate when the temperature is below 15°C and stops it when the
temperature exceeds 25°C. Vacuum capsule.
The capsule, located in the inlet of the air filter, is subjected to the depression. When energised, it operates a flap
which lets the heated air coming from a tapping located on the exhaust shield enter. At rest, the flap lets intake
air coming from behind the grill enter.
Page 223 of 648
CARBURATION
CHECKING THE PETROL SUPPLY
8531
Page 224 of 648
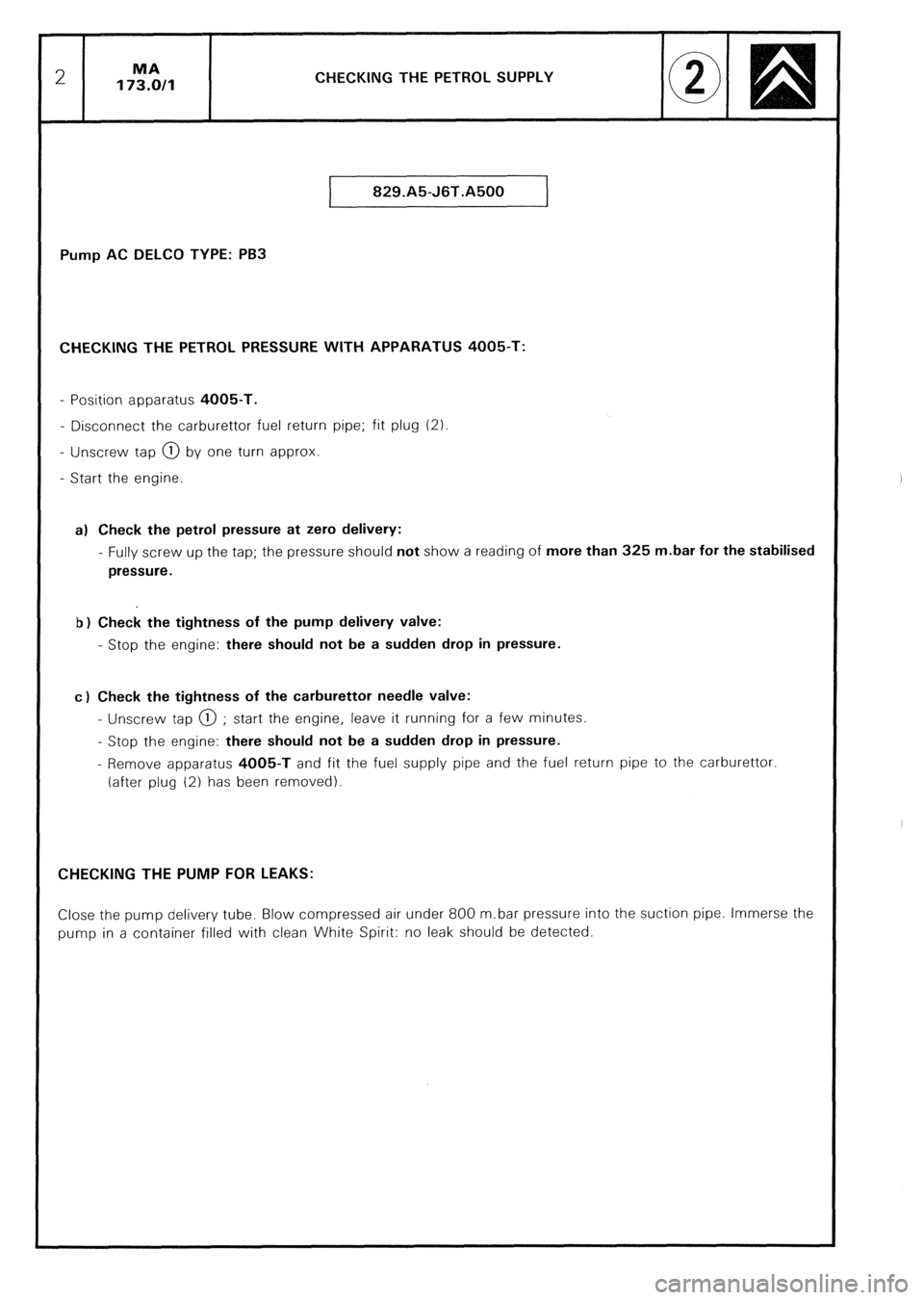
CHECKING THE PETROL SUPPLY
829.A5-J6T.A500
Pump AC DELCO TYPE: PB3
CHECKING THE PETROL PRESSURE WITH APPARATUS 4005-T:
- Position apparatus 4005-T.
- Disconnect the carburettor fuel return pipe; fit plug (2)
- Unscrew tap @ by one turn approx.
- Start the engine.
a) Check the petrol pressure at zero delivery:
- Fully screw up the tap; the pressure should not show a reading of more than 325 m.bar for the stabilised
pressure.
b) Check the tightness of the pump delivery valve:
- Stop the engine: there should not be a sudden drop in pressure.
c) Check the tightness of the carburettor needle valve:
- Unscrew tap @ ; start the engine, leave it running for a few minutes.
- Stop the engine: there should not be a sudden drop in pressure.
- Remove apparatus 4005-T and fit the fuel supply pipe and the fuel return pipe to the carburettor
(after plug (2) has been removed).
CHECKING THE PUMP FOR LEAKS:
Close the pump delivery tube. Blow compressed air under 800 m.bar pressure into the suction pipe. Immerse the
pump in a container filled with clean White Spirit: no leak should be detected.