Page 209 of 648
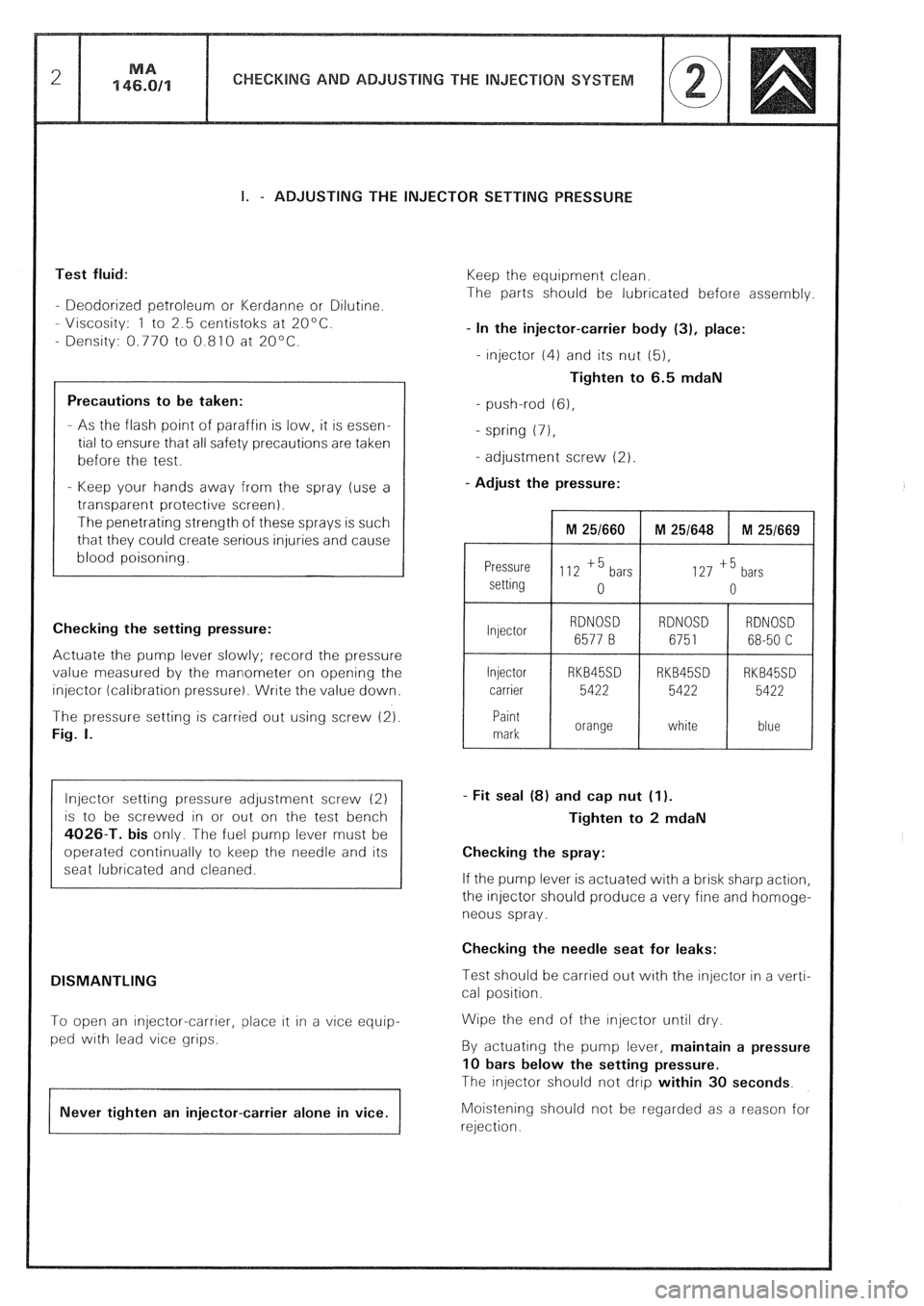
I. - ADJUSTING THE INJECTOR SETTING PRESSURE
Test fluid: Keep the equipment clean.
- Deodorized petroleum or Kerdanne or Dilutine. The parts should be lubricated before assembly.
- Viscosity: 1 to 2.5 centistoks at 2O’C.
- Density: 0.770 to 0.810 at 2O’C. - In the injector-carrier body (31, place:
- injector (4) and its nut (5),
Tighten to 6.5 mdaN
Precautions to be taken:
- push-rod (6),
- As the flash point of paraffin is low, it is essen-
- spring (7),
tial to ensure that all safety precautions are taken
before the test. - adjustment screw (2).
- Keep your hands away from the spray (use a - Adjust the pressure:
transparent protective screen).
The penetrating strength of these sprays is such
that they could create serious injuries and cause M 251660 M 251648 M 25/669
blood poisoning.
Pressure
112 t5 bars 127 t5 bars
setting
0 0
Checking the setting pressure: Injector RDNOSD RDNOSD RDNOSD
6577 B 6751 68-50 C
Actuate the pump lever slowly; record the pressure
value measured by the manometer on opening the Injector RKB45SD RKB45SD RKB45SD
Injector (calibration pressure). Write the value down. carrier 5422 5422 5422
The pressure setting is carried out using screw (2). Paint
Fig. I. mark orange white blue
Injector setting pressure adjustment screw (2)
is to be screwed in or out on the test bench
operated continually to keep the needle and its
If the pump lever is actuated with a brisk sharp action,
the injector should produce a very fine and homoge-
neous spray.
Checking the needle seat for leaks:
DISMANTLING Test should be carried out with the injector in a verti-
cal position.
To open an injector-carrier, place it in a vice equip- Wipe the end of the injector until dry.
ped with lead vice grips.
By actuating the pump lever, maintain a pressure
10 bars below the setting pressure.
The injector should not drip within 30 seconds,
Never tighten an injector-carrier alone in vice. Moistening should not be regarded as a reason for
rejection.
Page 210 of 648
Page 211 of 648
L 14.40 I --T-- I I /
3089 T F
Page 212 of 648
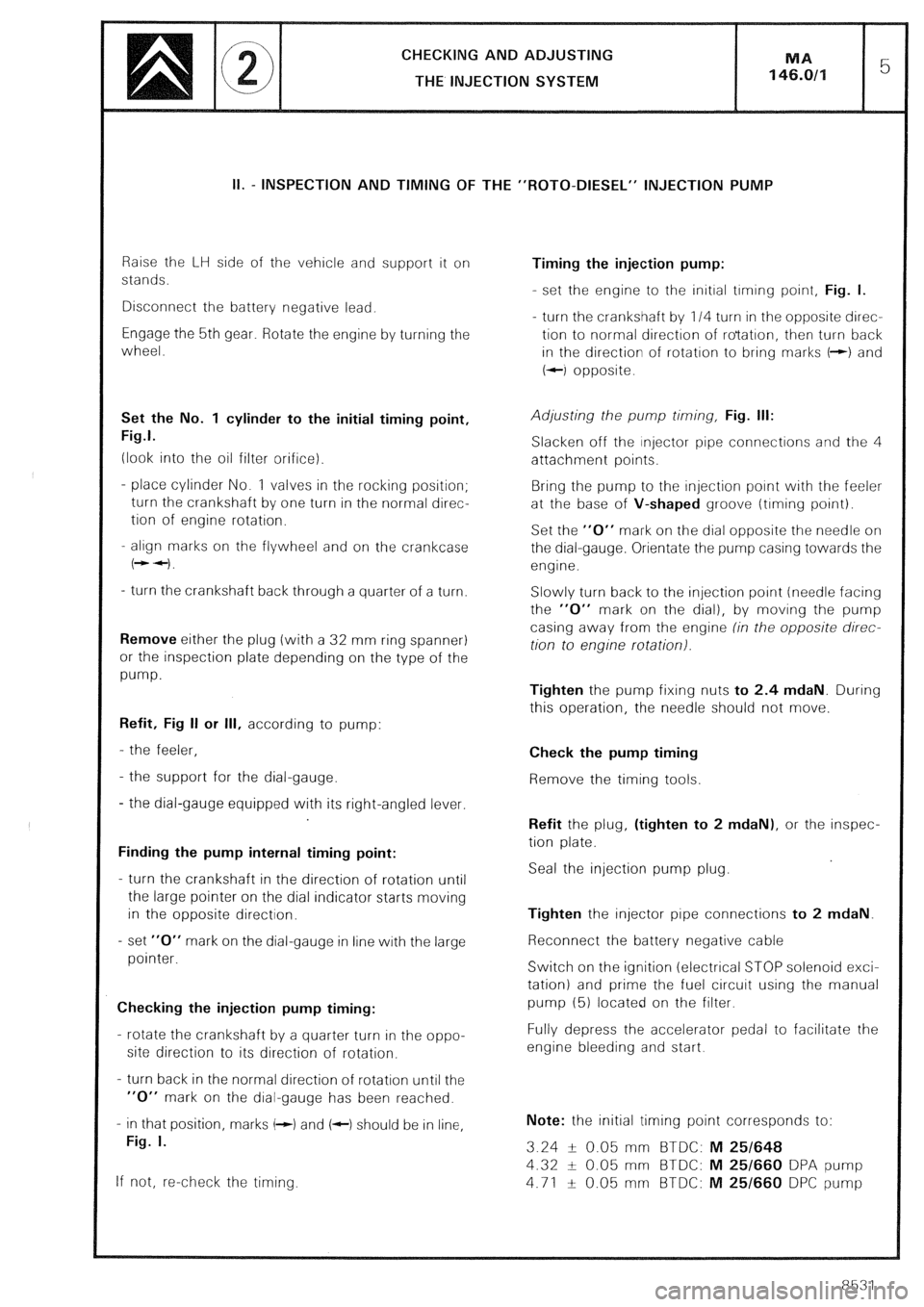
CHECKING AND ADJUSTING
THE INJECTION SYSTEM
II. - INSPECTION AND TIMING OF THE “ROT0-DIESEL” INJECTION PUMP
Raise the LH side of the vehicle and support it on
stands.
Disconnect the battery negative lead.
Engage the 5th gear. Rotate the engine by turning the
wheel.
Set the No. 1 cylinder to the initial timing point,
Fig.1.
(look into the oil filter orifice).
- place cylinder No. 1 valves in the rocking position;
turn the crankshaft by one turn in the normal direc-
tion of engine rotation.
- align marks on the flywheel and on the crankcase
(++I.
- turn the crankshaft back through a quarter of a turn.
Remove either the plug (with a 32 mm ring spanner)
or the inspection plate depending on the type of the
pump.
Refit, Fig II or Ill, according to pump:
- the feeler,
- the support for the dial-gauge.
- the dial-gauge equipped with its right-angled lever.
Finding the pump internal timing point:
- turn the crankshaft in the direction of rotation until
the large pointer on the dial indicator starts moving
in the opposite direction.
- set “0” mark on the dial-gauge in line with the large
pointer.
Checking the injection pump timing:
- rotate the crankshaft by a quarter turn in the oppo-
site direction to its direction of rotation.
- turn back in the normal direction of rotation until the
“0” mark on the dial-gauge has been reached.
- in that position, marks (-1 and (c) should be in line,
Fig. I.
If not, re-check the timing. Timing the injection pump:
- set the engine to the initial trming point, Fig. I.
- turn the crankshaft by 114 turn in the opposite direc-
tion to normal direction of ro’tatron, then turn back
in the direction of rotation to bring marks t-+) and
+-I opposite.
Adjusting the pump timing, Fig. Ill:
Slacken off the injector pipe connections and the 4
attachment points.
Bring the pump to the injection point with the feeler
at the base of V-shaped groove (timing point).
Set the “0” mark on the dial opposite the needle on
the dial-gauge. Orientate the pump casing towards the
engine.
Slowly turn back to the injection point (needle facing
the “0” mark on the dial), by moving the pump
casing away from the engine (in the opposite direc-
tion to engine rotation).
Tighten the pump fixing nuts to 2.4 mdaN. During
this operation, the needle should not move.
Check the pump timing
Remove the timing tools.
Refit the plug, (tighten to 2 mdaN), or the inspec-
tion plate.
Seal the injection pump plug.
Tighten the injector pipe connections to 2 mdaN.
Reconnect the battery negative cable
Switch on the ignition (electrical STOP solenoid exci-
tation) and prime the fuel circuit using the manual
pump (5) located on the filter.
Fully depress the accelerator pedal to facilitate the
engine bleeding and start.
Note: the initial timing point corresponds to:
3.24 -L- 0.05 mm BTDC: M 25/648
4.32 + 0.05 mm BTDC: M 25/660 DPA pump
4.71 f 0.05 mm BTDC: M 25/660 DPC pump
8531
Page 213 of 648
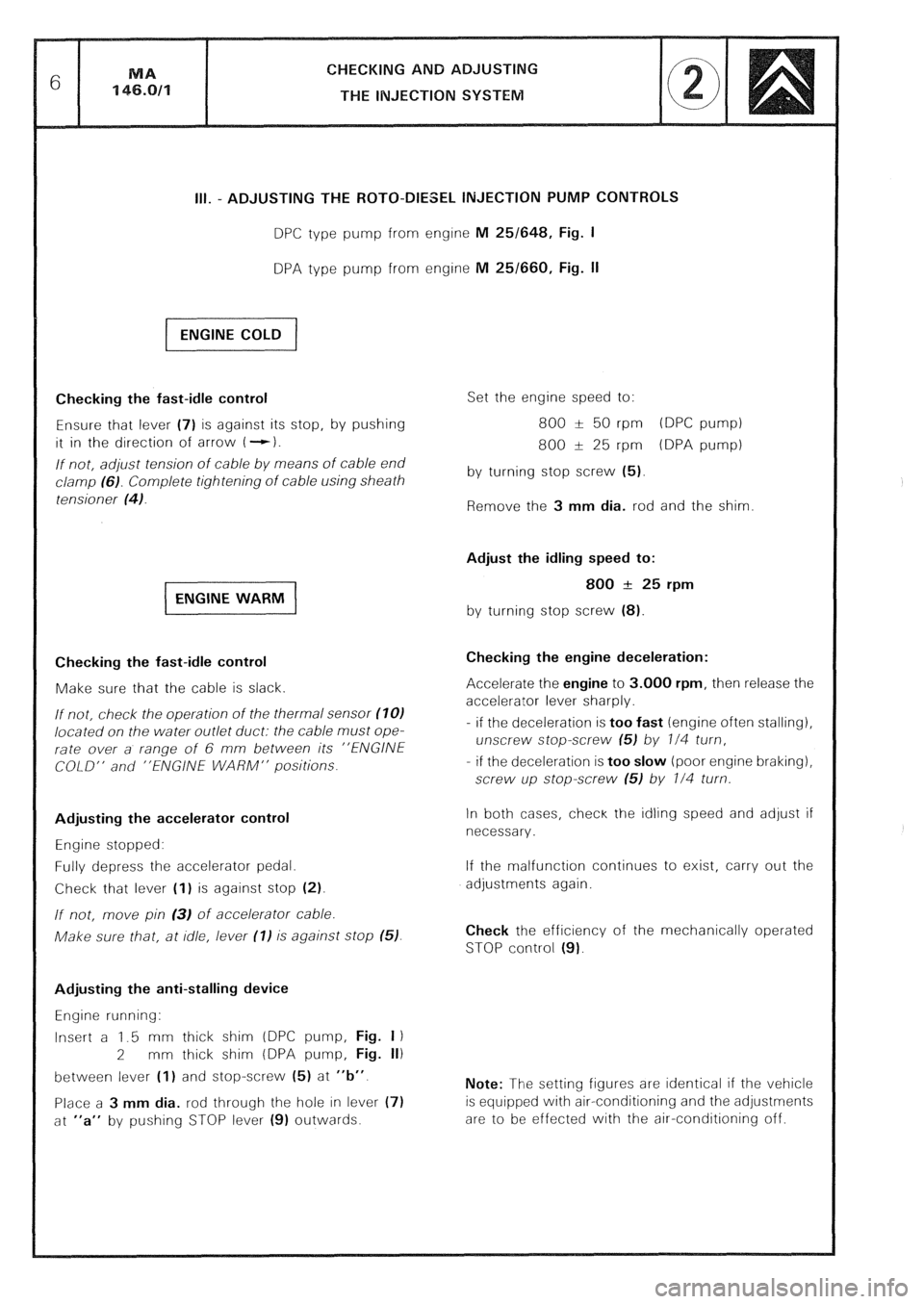
CHECKING AND ADJUSTING
THE INJECTION SYSTEM
III. - ADJUSTING THE ROTO-DIESEL INJECTION PUMP CONTROLS
DPC type pump from engine M 25/648, Fig. I
DPA type pump from engine M 25/660, Fig. II
Checking the fast-idle control
Ensure that lever (7) is against its stop, by pushing
it in the direction of arrow (-).
If not, adjust tension of cab/e by means of cable end
clamp (6). Complete tightening of cable using sheath
tensioner (41.
Checking the fast-idle control
Make sure that the cable is slack.
If not, check the operation of the thermal sensor (101
located on the water outlet duct: the cable must ope-
rate over a range of 6 mm between its “ENGINE
COLD” and “ENGINE WARM” positions.
Adjusting the accelerator control
Engine stopped:
Fully depress the accelerator pedal.
Check that lever (I) is against stop (2).
If not, move pin (3) of accelerator cable.
Make sure that, at idle, lever (I) is against stop (5).
Adjusting the anti-stalling device
Engine running:
Insert a 1.5 mm thick shim (DPC pump, Fig. I)
2 mm thick shim (DPA pump, Fig. II)
between lever (I) and stop-screw (5) at “b”.
Place a 3 mm dia. rod through the hole in lever (7)
at “a” by pushing STOP lever (9) outwards. Set the engine speed to:
800 t 50 rpm (DPC pump)
800 f 25 rpm (DPA pump)
by turning stop screw (5).
Remove the 3 mm dia. rod and the shim
Adjust the idling speed to:
800 + 25 rpm
by turning stop screw (8).
Checking the engine deceleration:
Accelerate the engine to 3.000 rpm, then release the
accelerator lever sharply.
- if the deceleration is too fast (engine often stalling),
unscrew stop-screw (5) by 114 turn,
- if the deceleration is too slow (poor engine braking),
screw up stop-screw (51 by l/4 turn.
In both cases, check the idling speed and adjust if
necessary.
If the malfunction continues to exist, carry out the
adjustments again.
Check the efficiency of the mechanically operated
STOP control (9).
Note: The setting figures are identical if the vehicle
is equipped with air-conditioning and the adjustments
are to be effected with the air-conditioning off.
Page 214 of 648
Page 215 of 648
2437-T.
3089-T.F.
3089-T.H.
4059-T.
5008-T.C
6027-T.
6028-T.
6030-T. RECOMMENDED TOOLS
Dial-gauge
Dial-gauge.
Feeler.
Right-angled lever for dial-gauge
Dial-gauge mounting fixing screw.
Set of 3 tools to check the timing
Driving pinion extractor.
Dial-gauge mounting. REFITTING D.P.A. AND D.P.C.
ROT0 DIESEL INJECTION PUMPS
8531
Page 216 of 648
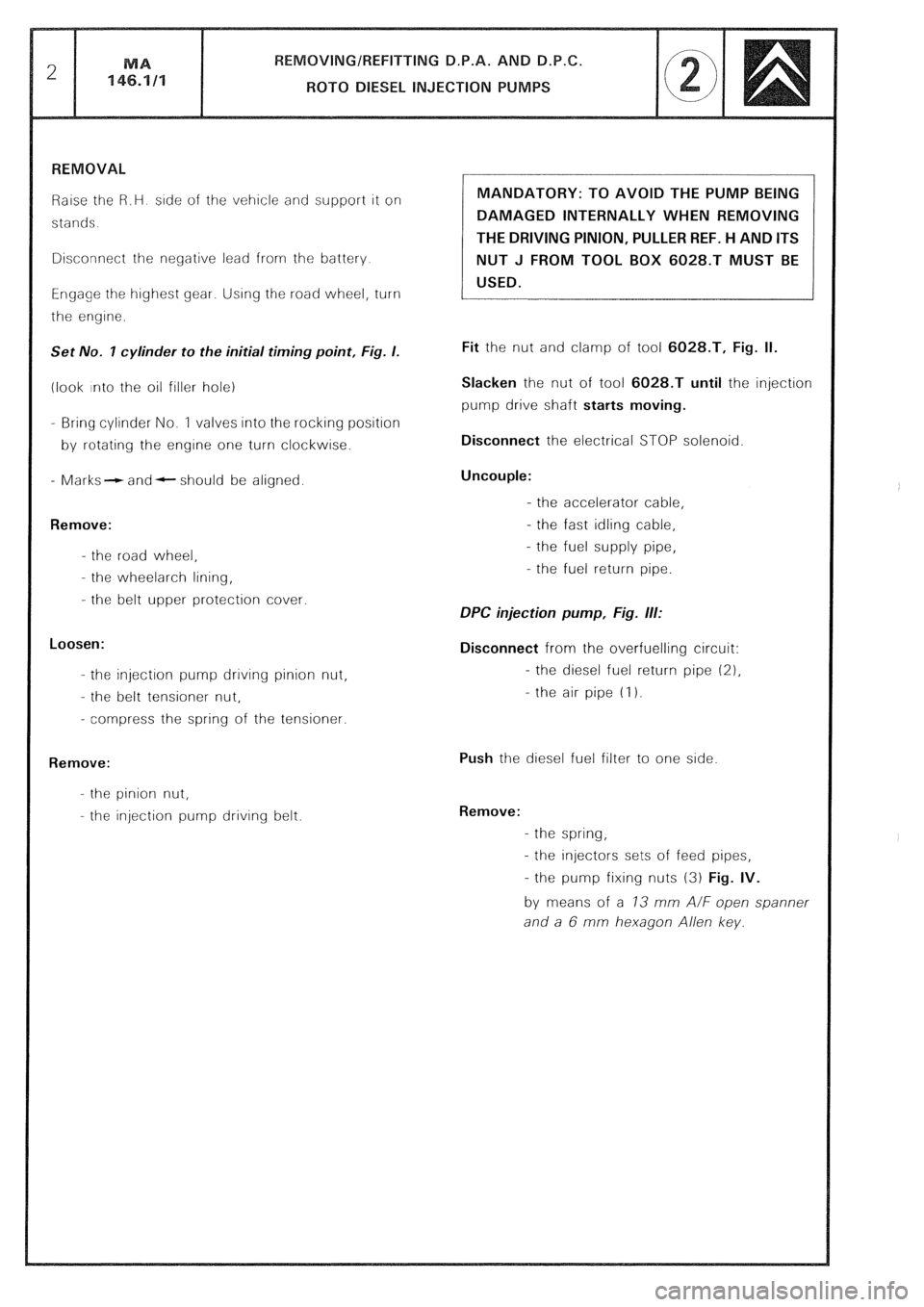
Raise the R.H side of the vehicle and support it on
stands.
Disconnect the negative lead from the battery
Engage the highest gear. Using the road wheel, turn
the engine.
Set No. I cylinder to the initial timing point, Fig. I.
(look into the oil filler hole)
- Bring cylinder No. 1 valves into the rocking position
by rotating the engine one turn clockwise.
- Marks- and- should be aligned.
Remove:
- the road wheel,
- the wheelarch lining,
- the belt upper protection cover.
Loosen:
- the injection pump drrvrng pinion nut,
- the belt tensioner nut,
- compress the spring of the tensioner.
Remove:
- the pinion nut,
- the injection pump driving belt. MANDATORY: TO AVOID THE PUMP BEING
DAMAGED INTERNALLY WHEN REMOVING
THE DRIVING PINION, PULLER REF. H AND ITS
NUT J FROM TOOL BOX 6028.T MUST BE
USED.
Fit the nut and clamp of tool 6028.T, Fig. II.
Slacken the nut of tool 6028.T until the injection
pump drive shaft starts moving.
Disconnect the electrical STOP solenoid
Uncouple:
- the accelerator cable,
- the fast idling cable,
- the fuel supply pipe,
- the fuel return pipe.
DPC injection pump, Fig. ill:
Disconnect from the overfuelling circuit:
- the diesel fuel return pipe (21,
- the air pipe (I 1.
Push the diesel fuel filter to one side
Remove:
- the spring,
- the injectors sets of feed pipes,
- the pump fixing nuts (3) Fig. IV.
by means of a 73 mm A/F open spanner
and a 6 mm hexagon Allen key.