Page 329 of 1529
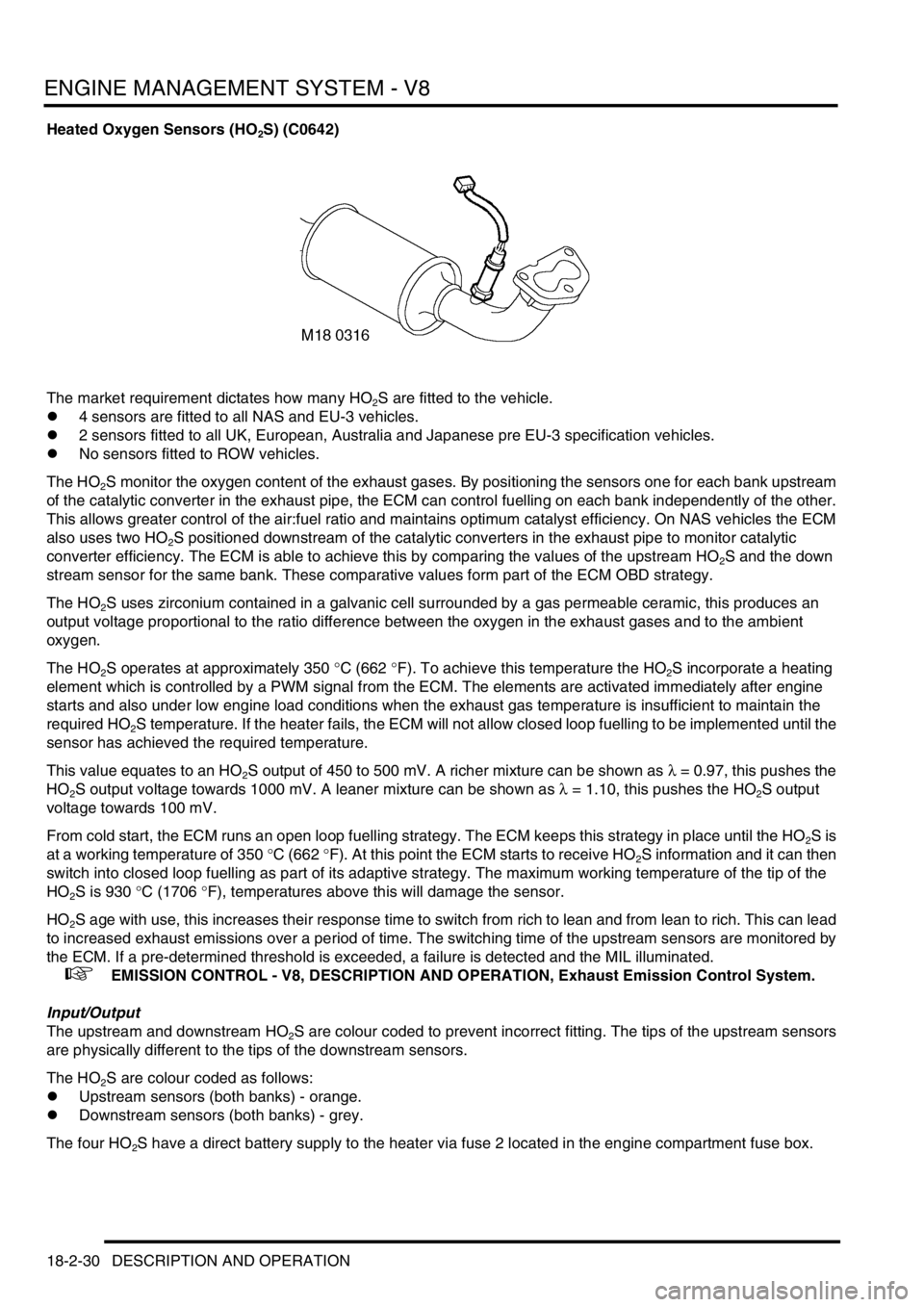
ENGINE MANAGEMENT SYSTEM - V8
18-2-30 DESCRIPTION AND OPERATION
Heated Oxygen Sensors (HO2S) (C0642)
The market requirement dictates how many HO
2S are fitted to the vehicle.
l4 sensors are fitted to all NAS and EU-3 vehicles.
l2 sensors fitted to all UK, European, Australia and Japanese pre EU-3 specification vehicles.
lNo sensors fitted to ROW vehicles.
The HO
2S monitor the oxygen content of the exhaust gases. By positioning the sensors one for each bank upstream
of the catalytic converter in the exhaust pipe, the ECM can control fuelling on each bank independently of the other.
This allows greater control of the air:fuel ratio and maintains optimum catalyst efficiency. On NAS vehicles the ECM
also uses two HO
2S positioned downstream of the catalytic converters in the exhaust pipe to monitor catalytic
converter efficiency. The ECM is able to achieve this by comparing the values of the upstream HO
2S and the down
stream sensor for the same bank. These comparative values form part of the ECM OBD strategy.
The HO
2S uses zirconium contained in a galvanic cell surrounded by a gas permeable ceramic, this produces an
output voltage proportional to the ratio difference between the oxygen in the exhaust gases and to the ambient
oxygen.
The HO
2S operates at approximately 350 °C (662 °F). To achieve this temperature the HO2S incorporate a heating
element which is controlled by a PWM signal from the ECM. The elements are activated immediately after engine
starts and also under low engine load conditions when the exhaust gas temperature is insufficient to maintain the
required HO
2S temperature. If the heater fails, the ECM will not allow closed loop fuelling to be implemented until the
sensor has achieved the required temperature.
This value equates to an HO
2S output of 450 to 500 mV. A richer mixture can be shown as λ = 0.97, this pushes the
HO
2S output voltage towards 1000 mV. A leaner mixture can be shown as λ = 1.10, this pushes the HO2S output
voltage towards 100 mV.
From cold start, the ECM runs an open loop fuelling strategy. The ECM keeps this strategy in place until the HO
2S is
at a working temperature of 350 °C (662 °F). At this point the ECM starts to receive HO
2S information and it can then
switch into closed loop fuelling as part of its adaptive strategy. The maximum working temperature of the tip of the
HO
2S is 930 °C (1706 °F), temperatures above this will damage the sensor.
HO
2S age with use, this increases their response time to switch from rich to lean and from lean to rich. This can lead
to increased exhaust emissions over a period of time. The switching time of the upstream sensors are monitored by
the ECM. If a pre-determined threshold is exceeded, a failure is detected and the MIL illuminated.
+ EMISSION CONTROL - V8, DESCRIPTION AND OPERATION, Exhaust Emission Control System.
Input/Output
The upstream and downstream HO
2S are colour coded to prevent incorrect fitting. The tips of the upstream sensors
are physically different to the tips of the downstream sensors.
The HO
2S are colour coded as follows:
lUpstream sensors (both banks) - orange.
lDownstream sensors (both banks) - grey.
The four HO
2S have a direct battery supply to the heater via fuse 2 located in the engine compartment fuse box.
Page 330 of 1529

ENGINE MANAGEMENT SYSTEM - V8
DESCRIPTION AND OPERATION 18-2-31
The heater is driven by the ECM providing an earth path for the circuit as follows:
lUpstream LH bank via pin 19 of connector C0635 of the ECM.
lUpstream RH bank via pin 13 of connector C0635 of the ECM.
lDownstream LH bank via pin 7 of connector C0635 of the ECM.
lDownstream RH bank via pin 1 of connector C0635 of the ECM.
The HO
2S output signal is measured by the ECM as follows:
lUpstream LH bank via pin 15 of connector C0635 of the ECM.
lUpstream RH bank via pin 16 of connector C0635 of the ECM.
lDownstream LH bank via pin 17 of connector C0635 of the ECM.
lDownstream RH bank via pin 14 of connector C0635 of the ECM.
The HO
2S earth path for the signal is supplied by the ECM as follows:
lUpstream LH bank via pin 9 of connector C0635 of the ECM.
lUpstream RH bank via pin 10 of connector C0635 of the ECM.
lDownstream LH bank via pin 11 of connector C0635 of the ECM.
lDownstream RH bank via pin 8 of connector C0635 of the ECM.
The HO
2S voltage is difficult to measure using a multimeter, the output can be monitored using TestBook. A rich
mixture would read 500 to 1000 mV, a weak mixture would read 100 mV to 500 mV, the reading should switch from
rich to weak. The open loop default voltage is 450 mV, this is used by the ECM to set the air/ fuel ratio until the tip of
the HO
2S reaches operating temperature.
The HO
2S can fail the following ways or supply incorrect signal:
lSensor open circuit.
lShort circuit to vehicle supply.
lShort circuit to vehicle earth.
lSensor disconnected.
lStoichiometric ratio outside the correct operating band.
lContamination from leaded fuel.
lAir leak into the exhaust system.
lWiring loom damage.
lSensors fitted incorrectly or cross wired.
In the event of a HO
2S signal failure any of the following symptoms may be observed:
lDefault to open loop fuelling on defective bank.
lIf the sensors are crossed over (LH bank to RH bank), the engine will run normally after initial start up, but
performance will become progressively worse as the sensors go towards maximum rich for one bank of cylinders
and maximum lean for the other. The ECM will eventually default into open loop fuelling.
lHigh CO reading.
lExcess emissions.
lStrong hydrogen sulphide (H
2S) smell until the ECM defaults to open loop fuelling. .
lMIL illuminated (NAS market only).
A number of diagnostic tests are performed by the ECM with regards to the HO
2sensors:
lHO
2 sensor and system diagnostics
lHO
2 sensor heater diagnostics
lHO
2 sensor switching period (ageing) diagnostics
lRear HO
2 sensor adaption diagnostic (NAS only)
lCatalyst monitoring diagnostic
For further details of the heated oxygen sensors and exhaust emission control, refer to the V8 Emission Control
section of this manual.
+ EMISSION CONTROL - V8, DESCRIPTION AND OPERATION, Exhaust Emission Control System.
Page 331 of 1529
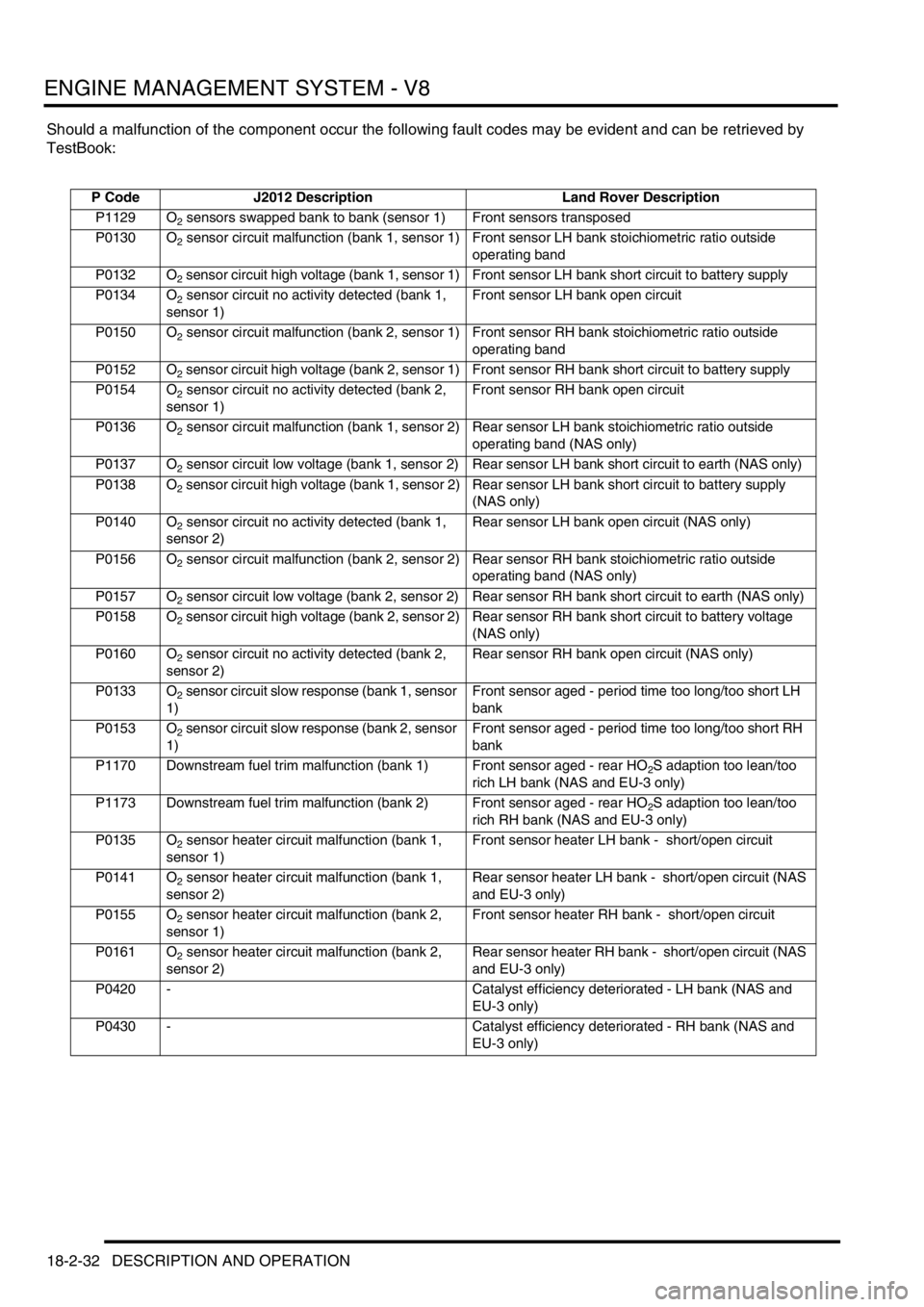
ENGINE MANAGEMENT SYSTEM - V8
18-2-32 DESCRIPTION AND OPERATION
Should a malfunction of the component occur the following fault codes may be evident and can be retrieved by
TestBook:
P Code J2012 Description Land Rover Description
P1129 O
2 sensors swapped bank to bank (sensor 1) Front sensors transposed
P0130 O
2 sensor circuit malfunction (bank 1, sensor 1) Front sensor LH bank stoichiometric ratio outside
operating band
P0132 O
2 sensor circuit high voltage (bank 1, sensor 1) Front sensor LH bank short circuit to battery supply
P0134 O
2 sensor circuit no activity detected (bank 1,
sensor 1)Front sensor LH bank open circuit
P0150 O
2 sensor circuit malfunction (bank 2, sensor 1) Front sensor RH bank stoichiometric ratio outside
operating band
P0152 O
2 sensor circuit high voltage (bank 2, sensor 1) Front sensor RH bank short circuit to battery supply
P0154 O
2 sensor circuit no activity detected (bank 2,
sensor 1)Front sensor RH bank open circuit
P0136 O
2 sensor circuit malfunction (bank 1, sensor 2) Rear sensor LH bank stoichiometric ratio outside
operating band (NAS only)
P0137 O
2 sensor circuit low voltage (bank 1, sensor 2) Rear sensor LH bank short circuit to earth (NAS only)
P0138 O
2 sensor circuit high voltage (bank 1, sensor 2) Rear sensor LH bank short circuit to battery supply
(NAS only)
P0140 O
2 sensor circuit no activity detected (bank 1,
sensor 2)Rear sensor LH bank open circuit (NAS only)
P0156 O
2 sensor circuit malfunction (bank 2, sensor 2) Rear sensor RH bank stoichiometric ratio outside
operating band (NAS only)
P0157 O
2 sensor circuit low voltage (bank 2, sensor 2) Rear sensor RH bank short circuit to earth (NAS only)
P0158 O
2 sensor circuit high voltage (bank 2, sensor 2) Rear sensor RH bank short circuit to battery voltage
(NAS only)
P0160 O
2 sensor circuit no activity detected (bank 2,
sensor 2)Rear sensor RH bank open circuit (NAS only)
P0133 O
2 sensor circuit slow response (bank 1, sensor
1)Front sensor aged - period time too long/too short LH
bank
P0153 O
2 sensor circuit slow response (bank 2, sensor
1)Front sensor aged - period time too long/too short RH
bank
P1170 Downstream fuel trim malfunction (bank 1) Front sensor aged - rear HO
2S adaption too lean/too
rich LH bank (NAS and EU-3 only)
P1173 Downstream fuel trim malfunction (bank 2) Front sensor aged - rear HO
2S adaption too lean/too
rich RH bank (NAS and EU-3 only)
P0135 O
2 sensor heater circuit malfunction (bank 1,
sensor 1)Front sensor heater LH bank - short/open circuit
P0141 O
2 sensor heater circuit malfunction (bank 1,
sensor 2)Rear sensor heater LH bank - short/open circuit (NAS
and EU-3 only)
P0155 O
2 sensor heater circuit malfunction (bank 2,
sensor 1)Front sensor heater RH bank - short/open circuit
P0161 O
2 sensor heater circuit malfunction (bank 2,
sensor 2)Rear sensor heater RH bank - short/open circuit (NAS
and EU-3 only)
P0420 - Catalyst efficiency deteriorated - LH bank (NAS and
EU-3 only)
P0430 - Catalyst efficiency deteriorated - RH bank (NAS and
EU-3 only)
Page 332 of 1529
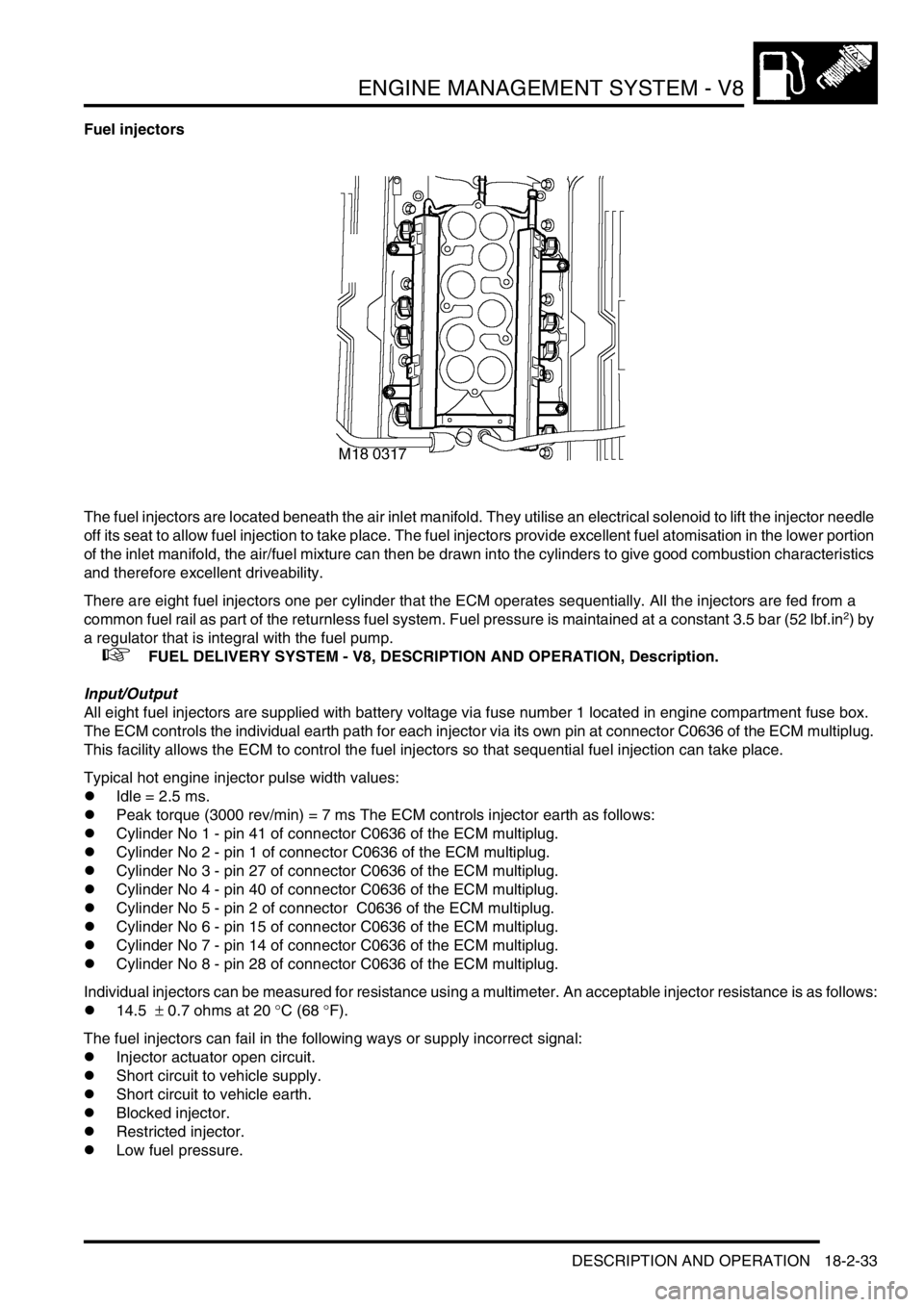
ENGINE MANAGEMENT SYSTEM - V8
DESCRIPTION AND OPERATION 18-2-33
Fuel injectors
The fuel injectors are located beneath the air inlet manifold. They utilise an electrical solenoid to lift the injector needle
off its seat to allow fuel injection to take place. The fuel injectors provide excellent fuel atomisation in the lower portion
of the inlet manifold, the air/fuel mixture can then be drawn into the cylinders to give good combustion characteristics
and therefore excellent driveability.
There are eight fuel injectors one per cylinder that the ECM operates sequentially. All the injectors are fed from a
common fuel rail as part of the returnless fuel system. Fuel pressure is maintained at a constant 3.5 bar (52 lbf.in
2) by
a regulator that is integral with the fuel pump.
+ FUEL DELIVERY SYSTEM - V8, DESCRIPTION AND OPERATION, Description.
Input/Output
All eight fuel injectors are supplied with battery voltage via fuse number 1 located in engine compartment fuse box.
The ECM controls the individual earth path for each injector via its own pin at connector C0636 of the ECM multiplug.
This facility allows the ECM to control the fuel injectors so that sequential fuel injection can take place.
Typical hot engine injector pulse width values:
lIdle = 2.5 ms.
lPeak torque (3000 rev/min) = 7 ms The ECM controls injector earth as follows:
lCylinder No 1 - pin 41 of connector C0636 of the ECM multiplug.
lCylinder No 2 - pin 1 of connector C0636 of the ECM multiplug.
lCylinder No 3 - pin 27 of connector C0636 of the ECM multiplug.
lCylinder No 4 - pin 40 of connector C0636 of the ECM multiplug.
lCylinder No 5 - pin 2 of connector C0636 of the ECM multiplug.
lCylinder No 6 - pin 15 of connector C0636 of the ECM multiplug.
lCylinder No 7 - pin 14 of connector C0636 of the ECM multiplug.
lCylinder No 8 - pin 28 of connector C0636 of the ECM multiplug.
Individual injectors can be measured for resistance using a multimeter. An acceptable injector resistance is as follows:
l14.5 ± 0.7 ohms at 20 °C (68 °F).
The fuel injectors can fail in the following ways or supply incorrect signal:
lInjector actuator open circuit.
lShort circuit to vehicle supply.
lShort circuit to vehicle earth.
lBlocked injector.
lRestricted injector.
lLow fuel pressure.
Page 333 of 1529
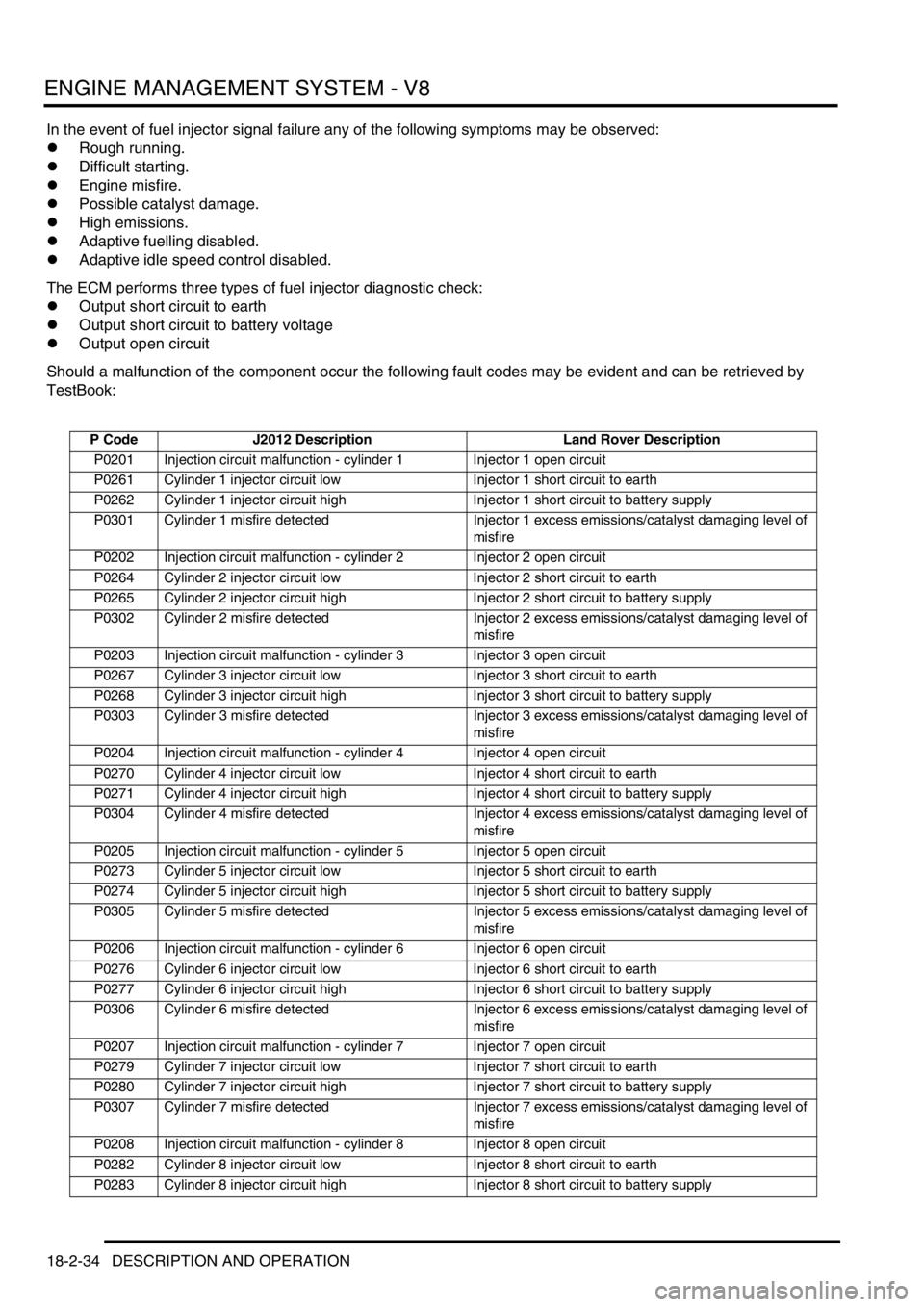
ENGINE MANAGEMENT SYSTEM - V8
18-2-34 DESCRIPTION AND OPERATION
In the event of fuel injector signal failure any of the following symptoms may be observed:
lRough running.
lDifficult starting.
lEngine misfire.
lPossible catalyst damage.
lHigh emissions.
lAdaptive fuelling disabled.
lAdaptive idle speed control disabled.
The ECM performs three types of fuel injector diagnostic check:
lOutput short circuit to earth
lOutput short circuit to battery voltage
lOutput open circuit
Should a malfunction of the component occur the following fault codes may be evident and can be retrieved by
TestBook:
P Code J2012 Description Land Rover Description
P0201 Injection circuit malfunction - cylinder 1 Injector 1 open circuit
P0261 Cylinder 1 injector circuit low Injector 1 short circuit to earth
P0262 Cylinder 1 injector circuit high Injector 1 short circuit to battery supply
P0301 Cylinder 1 misfire detected Injector 1 excess emissions/catalyst damaging level of
misfire
P0202 Injection circuit malfunction - cylinder 2 Injector 2 open circuit
P0264 Cylinder 2 injector circuit low Injector 2 short circuit to earth
P0265 Cylinder 2 injector circuit high Injector 2 short circuit to battery supply
P0302 Cylinder 2 misfire detected Injector 2 excess emissions/catalyst damaging level of
misfire
P0203 Injection circuit malfunction - cylinder 3 Injector 3 open circuit
P0267 Cylinder 3 injector circuit low Injector 3 short circuit to earth
P0268 Cylinder 3 injector circuit high Injector 3 short circuit to battery supply
P0303 Cylinder 3 misfire detected Injector 3 excess emissions/catalyst damaging level of
misfire
P0204 Injection circuit malfunction - cylinder 4 Injector 4 open circuit
P0270 Cylinder 4 injector circuit low Injector 4 short circuit to earth
P0271 Cylinder 4 injector circuit high Injector 4 short circuit to battery supply
P0304 Cylinder 4 misfire detected Injector 4 excess emissions/catalyst damaging level of
misfire
P0205 Injection circuit malfunction - cylinder 5 Injector 5 open circuit
P0273 Cylinder 5 injector circuit low Injector 5 short circuit to earth
P0274 Cylinder 5 injector circuit high Injector 5 short circuit to battery supply
P0305 Cylinder 5 misfire detected Injector 5 excess emissions/catalyst damaging level of
misfire
P0206 Injection circuit malfunction - cylinder 6 Injector 6 open circuit
P0276 Cylinder 6 injector circuit low Injector 6 short circuit to earth
P0277 Cylinder 6 injector circuit high Injector 6 short circuit to battery supply
P0306 Cylinder 6 misfire detected Injector 6 excess emissions/catalyst damaging level of
misfire
P0207 Injection circuit malfunction - cylinder 7 Injector 7 open circuit
P0279 Cylinder 7 injector circuit low Injector 7 short circuit to earth
P0280 Cylinder 7 injector circuit high Injector 7 short circuit to battery supply
P0307 Cylinder 7 misfire detected Injector 7 excess emissions/catalyst damaging level of
misfire
P0208 Injection circuit malfunction - cylinder 8 Injector 8 open circuit
P0282 Cylinder 8 injector circuit low Injector 8 short circuit to earth
P0283 Cylinder 8 injector circuit high Injector 8 short circuit to battery supply
Page 334 of 1529

ENGINE MANAGEMENT SYSTEM - V8
DESCRIPTION AND OPERATION 18-2-35
P0308 Cylinder 8 misfire detected Injector 8 excess emissions/catalyst damaging level of
misfire
P0171 System too lean (bank 1) Multiplication injector adaptive fuelling - lean limit
exceeded LH bank
P0172 System too rich (bank 1) Multiplication injector adaptive fuelling - rich limit
exceeded LH bank
P0174 System too lean (bank 2) Multiplication injector adaptive fuelling - lean limit
exceeded RH bank
P0175 System too rich (bank 2) Multiplication injector adaptive fuelling - rich limit
exceeded RH bank
P1171 System too lean (bank 1) Additive injector adaptive fuelling - lean limit exceeded
LH bank
P1172 System too rich (bank1) Additive injector adaptive fuelling - rich limit exceeded
LH bank
P1174 System too lean (bank 2) Additive injector adaptive fuelling - lean limit exceeded
RH bank
P1175 System too rich (bank 2) Additive injector adaptive fuelling - rich limit exceeded
RH bank
P0300 Random/multiple cylinder excess emissions
detectedExcess emissions detected on more than one cylinder
P1300 Random/multiple cylinder misfire detected Catalyst damaging level of misfire on more than one
cylinder
P1319 Misfire detected with low fuel level P Code J2012 Description Land Rover Description
Page 335 of 1529
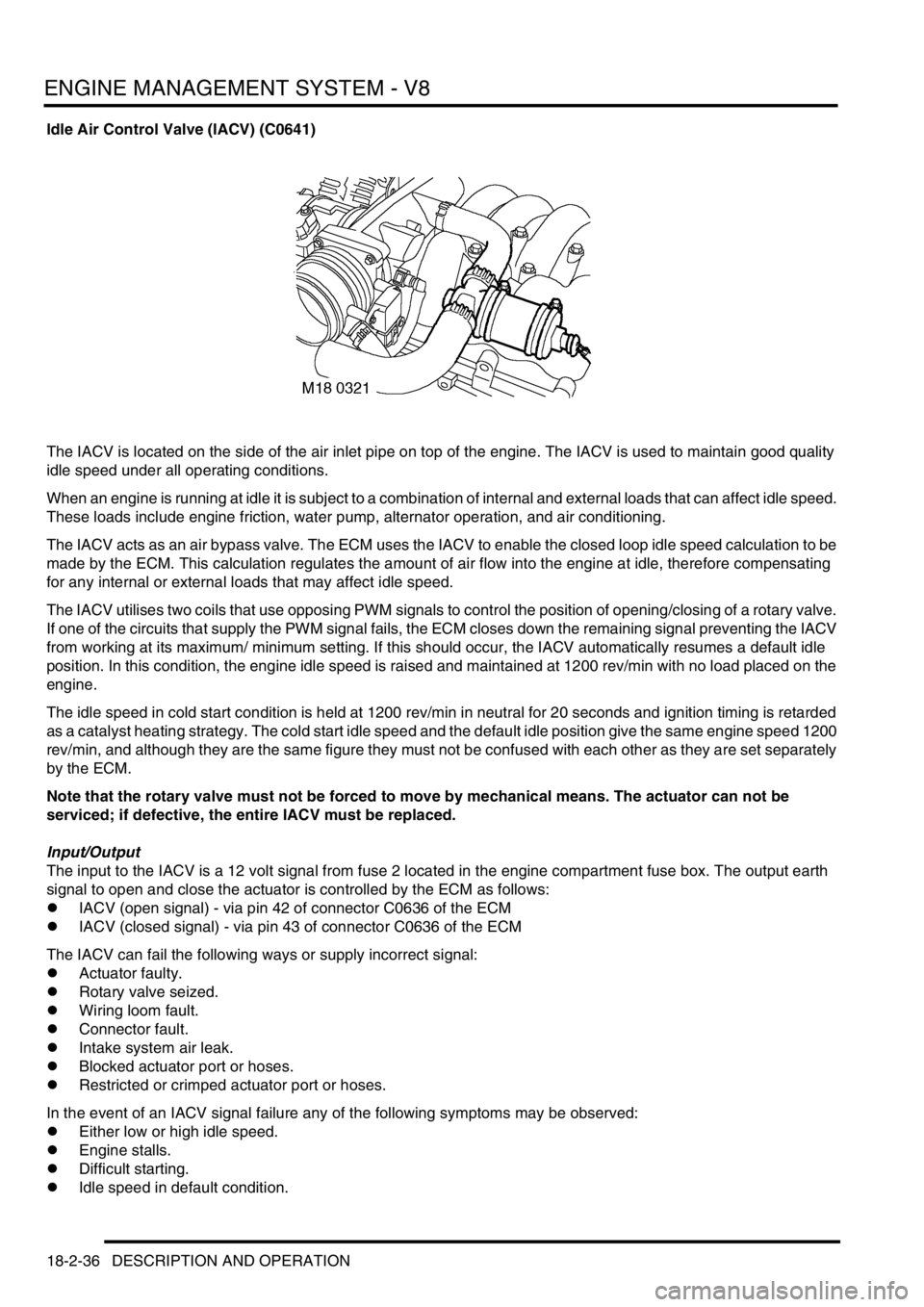
ENGINE MANAGEMENT SYSTEM - V8
18-2-36 DESCRIPTION AND OPERATION
Idle Air Control Valve (IACV) (C0641)
The IACV is located on the side of the air inlet pipe on top of the engine. The IACV is used to maintain good quality
idle speed under all operating conditions.
When an engine is running at idle it is subject to a combination of internal and external loads that can affect idle speed.
These loads include engine friction, water pump, alternator operation, and air conditioning.
The IACV acts as an air bypass valve. The ECM uses the IACV to enable the closed loop idle speed calculation to be
made by the ECM. This calculation regulates the amount of air flow into the engine at idle, therefore compensating
for any internal or external loads that may affect idle speed.
The IACV utilises two coils that use opposing PWM signals to control the position of opening/closing of a rotary valve.
If one of the circuits that supply the PWM signal fails, the ECM closes down the remaining signal preventing the IACV
from working at its maximum/ minimum setting. If this should occur, the IACV automatically resumes a default idle
position. In this condition, the engine idle speed is raised and maintained at 1200 rev/min with no load placed on the
engine.
The idle speed in cold start condition is held at 1200 rev/min in neutral for 20 seconds and ignition timing is retarded
as a catalyst heating strategy. The cold start idle speed and the default idle position give the same engine speed 1200
rev/min, and although they are the same figure they must not be confused with each other as they are set separately
by the ECM.
Note that the rotary valve must not be forced to move by mechanical means. The actuator can not be
serviced; if defective, the entire IACV must be replaced.
Input/Output
The input to the IACV is a 12 volt signal from fuse 2 located in the engine compartment fuse box. The output earth
signal to open and close the actuator is controlled by the ECM as follows:
lIACV (open signal) - via pin 42 of connector C0636 of the ECM
lIACV (closed signal) - via pin 43 of connector C0636 of the ECM
The IACV can fail the following ways or supply incorrect signal:
lActuator faulty.
lRotary valve seized.
lWiring loom fault.
lConnector fault.
lIntake system air leak.
lBlocked actuator port or hoses.
lRestricted or crimped actuator port or hoses.
In the event of an IACV signal failure any of the following symptoms may be observed:
lEither low or high idle speed.
lEngine stalls.
lDifficult starting.
lIdle speed in default condition.
Page 336 of 1529
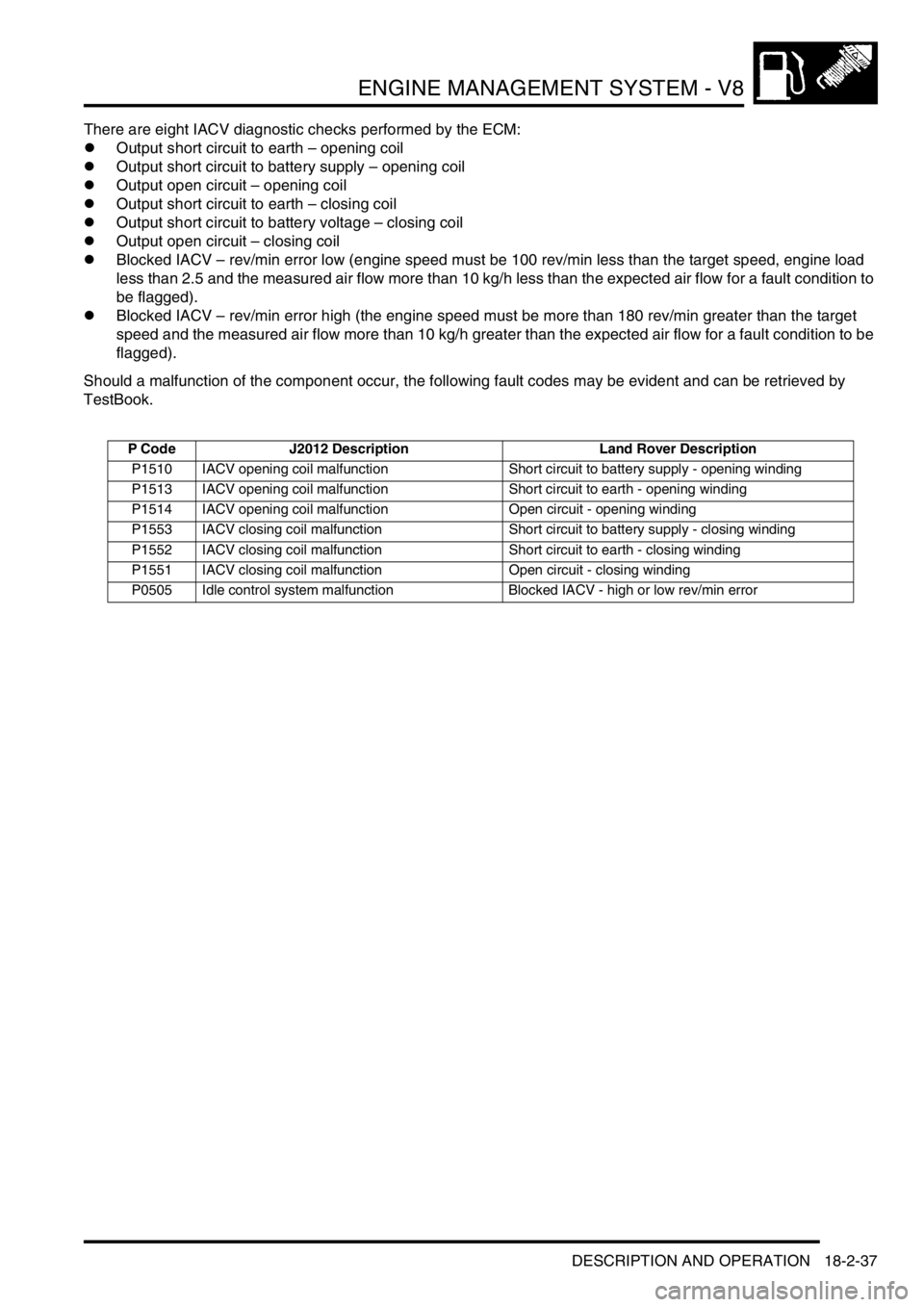
ENGINE MANAGEMENT SYSTEM - V8
DESCRIPTION AND OPERATION 18-2-37
There are eight IACV diagnostic checks performed by the ECM:
lOutput short circuit to earth – opening coil
lOutput short circuit to battery supply – opening coil
lOutput open circuit – opening coil
lOutput short circuit to earth – closing coil
lOutput short circuit to battery voltage – closing coil
lOutput open circuit – closing coil
lBlocked IACV – rev/min error low (engine speed must be 100 rev/min less than the target speed, engine load
less than 2.5 and the measured air flow more than 10 kg/h less than the expected air flow for a fault condition to
be flagged).
lBlocked IACV – rev/min error high (the engine speed must be more than 180 rev/min greater than the target
speed and the measured air flow more than 10 kg/h greater than the expected air flow for a fault condition to be
flagged).
Should a malfunction of the component occur, the following fault codes may be evident and can be retrieved by
TestBook.
P Code J2012 Description Land Rover Description
P1510 IACV opening coil malfunction Short circuit to battery supply - opening winding
P1513 IACV opening coil malfunction Short circuit to earth - opening winding
P1514 IACV opening coil malfunction Open circuit - opening winding
P1553 IACV closing coil malfunction Short circuit to battery supply - closing winding
P1552 IACV closing coil malfunction Short circuit to earth - closing winding
P1551 IACV closing coil malfunction Open circuit - closing winding
P0505 Idle control system malfunction Blocked IACV - high or low rev/min error