Page 241 of 558
35A-1
BASIC BRAKE
SYSTEM
CONTENTS
GENERAL 2. . . . . . . . . . . . . . . . . . . . . . . . . . . . . . .
Outline of Change 2. . . . . . . . . . . . . . . . . . . . . . . . .
ON-VEHICLE SERVICE 2. . . . . . . . . . . . . . . . . .
Brake Pedal Check and Adjustment 2. . . . . . . .
BRAKE PEDAL 4. . . . . . . . . . . . . . . . . . . . . . . . . . MASTER CYLINDER AND BRAKE
BOOSTER 5. . . . . . . . . . . . . . . . . . . . . . . . . . . . . . .
Master Cylinder 7. . . . . . . . . . . . . . . . . . . . . . . . . . .
DISC BRAKE 9. . . . . . . . . . . . . . . . . . . . . . . . . . . .
Page 242 of 558
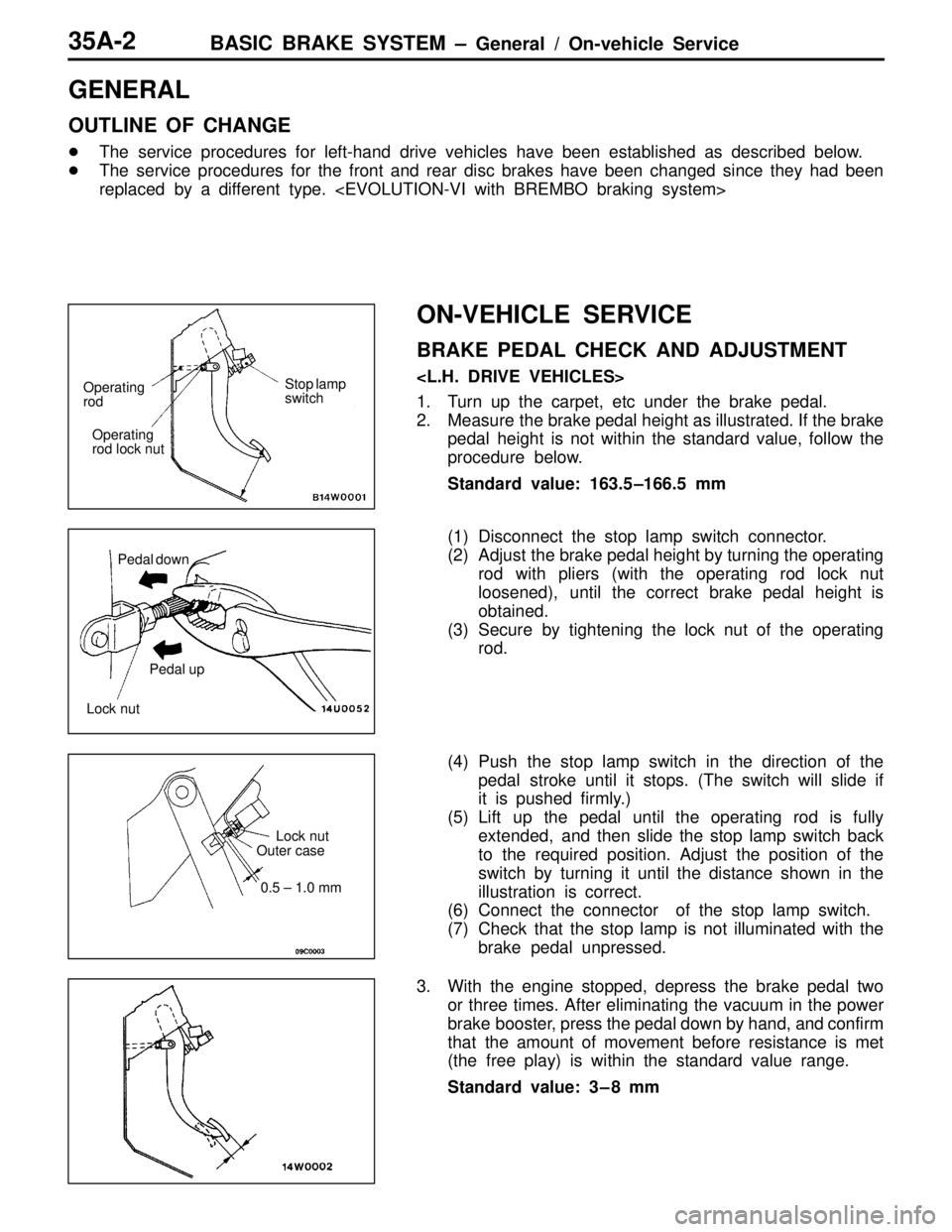
BASIC BRAKE SYSTEM – General / On-vehicle Service35A-2
GENERAL
OUTLINE OF CHANGE
The service procedures for left-hand drive vehicles have been established as described below.
The service procedures for the front and rear disc brakes have been changed since they had been
replaced by a different type.
ON-VEHICLE SERVICE
BRAKE PEDAL CHECK AND ADJUSTMENT
1. Turn up the carpet, etc under the brake pedal.
2. Measure the brake pedal height as illustrated. If the brake
pedal height is not within the standard value, follow the
procedure below.
Standard value: 163.5 –166.5 mm
(1) Disconnect the stop lamp switch connector.
(2) Adjust the brake pedal height by turning the operating
rod with pliers (with the operating rod lock nut
loosened), until the correct brake pedal height is
obtained.
(3) Secure by tightening the lock nut of the operating
rod.
(4) Push the stop lamp switch in the direction of the
pedal stroke until it stops. (The switch will slide if
it is pushed firmly.)
(5) Lift up the pedal until the operating rod is fully
extended, and then slide the stop lamp switch back
to the required position. Adjust the position of the
switch by turning it until the distance shown in the
illustration is correct.
(6) Connect the connector of the stop lamp switch.
(7) Check that the stop lamp is not illuminated with the
brake pedal unpressed.
3. With the engine stopped, depress the brake pedal two
or three times. After eliminating the vacuum in the power
brake booster, press the pedal down by hand, and confirm
that the amount of movement before resistance is met
(the free play) is within the standard value range.
Standard value: 3 – 8 mmOperating
rod
Operating
rod lock nutStop lamp
switch
Pedal down
Pedal up
Lock nut
Lock nut
Outer case
0.5 – 1.0 mm
Page 243 of 558
BASIC BRAKE SYSTEM – On-vehicle Service35A-3
If the free play exceeds the standard value, it is probably
due to excessive play between the retaining ring bolt
and brake pedal arm.
Check for excessive clearance and replace faulty parts
as required.
4. Start the engine, depress the brake pedal with
approximately 490 N of force, and measure the clearance
between the brake pedal and the floorboard.
Standard value: 80 mm or more
If the clearance is outside the standard value, check for
air trapped in the brake line, clearance between the lining
and the drum and dragging in the parking brake.
Adjust and replace defective parts as required.
5. Turn back the carpet, etc.
Page 244 of 558
BASIC BRAKE SYSTEM – Brake Pedal35A-4
BRAKE PEDAL
REMOVAL AND INSTALLATION
Pre-removal Operation
Instrument Under Cover Removal
Steering Column Assembly Removal
(Refer to GROUP 37A – Steering Wheel and Shaft.)
Accelerator Pedal RemovalPost-installation Operation
Accelerator Pedal Installation
Steering Column Assembly Installation
(Refer to GROUP 37A – Steering Wheel and Shaft.)
Instrument Under Cover Installation
Brake Pedal Adjustment (Refer to P.35A-2.)
29 Nm
12 Nm
14 Nm
1 2
3
4 5
67 813 Nm
11
910
8 9
Removal steps
1. Stop lamp switch connector
2. Stop lamp switch
3. Snap pin
4. Clevis pin
5. Brake pedal shaft bolt
6. Brake pedal7. Brake pedal pad
8. Brake pedal return spring
9. Bushing
10. Pipe
11. Pedal support member
Page 245 of 558
BASIC BRAKE SYSTEM – Master Cylinder and Brake Booster35A-5
MASTER CYLINDER AND BRAKE BOOSTER
REMOVAL AND INSTALLATION
Pre-removal Operation
Brake Fluid Draining
Air Intake Hose RemovalPost-installation Operation
Brake Fluid Supplying
Brake Line Bleeding
Brake Pedal Adjustment (Refer to P.35A-2.)
Air Intake Hose Installation
15–18 Nm 15 Nm
Sealant: 3M ATD Part No.
8661 or equivalent
6
7 3
14
2
8
5
4
14 Nm
5 9
1
10 Nm
Removal steps
1. Brake pipe connection
2. Brake fluid level sensor connector
3. Master cylinder assembly
BClearance adjustment between brake
booster push rod and primary piston
A4. Vacuum hose
(With built-in check valve)5. Fitting
6. Snap pin
7. Clevis pin assembly
8. Brake booster
9. Sealer
Page 246 of 558
BASIC BRAKE SYSTEM – Master Cylinder and Brake Booster35A-6
INSTALLATION SERVICE POINTS
AVACUUM HOSE CONNECTION
Insert securely and completely until the vacuum hose at the
engine side contacts the edge of the hexagonal part of the
fitting, and then secure by using the hose clip.
BCLEARANCE ADJUSTMENT BETWEEN BRAKE
BOOSTER PUSH ROD AND PRIMARY PISTON
Calculate clearance A from the B, C and D measurements.
A = B – C – D
Standard value: 0.65–0.85 mm
If the clearance is not within the standard value range, adjust
by changing the push rod length by turning the screw of
the push rod.
Measuring
distance BMeasuring
distance D
Block
gaugeB
AC
D
Page 247 of 558
BASIC BRAKE SYSTEM – Master Cylinder and Brake Booster35A-7
MASTER CYLINDER
DISASSEMBLY AND REASSEMBLY
Master cylinder kit
11
14
1312
141315 1
4 2
3
6
8
9 5
7
10
12
15
13
14Brake fluid: DOT3 or DOT4
11
Disassembly steps
1. Reservoir cap assembly
2. Reservoir cap
3. Diaphragm
4. Filter
5. Brake fluid level sensor
6. Float
7. Reservoir stopper bolt8. Reservoir tank
9. Reservoir seal
A10. Piston stopper bolt
11. Gasket
B12. Piston stopper ring
13. Primary piston assembly
14. Secondary piston assembly
15. Master cylinder body
Page 248 of 558
BASIC BRAKE SYSTEM – Master Cylinder and Brake Booster35A-8
DISASSEMBLY SERVICE POINTS
APISTON STOPPER BOLT DISASSEMBLY
Remove the piston stopper bolt, while depressing the piston.
BPISTON STOPPER RING DISASSEMBLY
Remove the piston stopper ring, while depressing the piston.
INSPECTION
Check the inner surface of master cylinder body for rust
or pitting.
Check the primary and secondary pistons for rust, scoring,
wear, damage or wear.
Check the diaphragm for cracks and wear.