Page 16 of 558
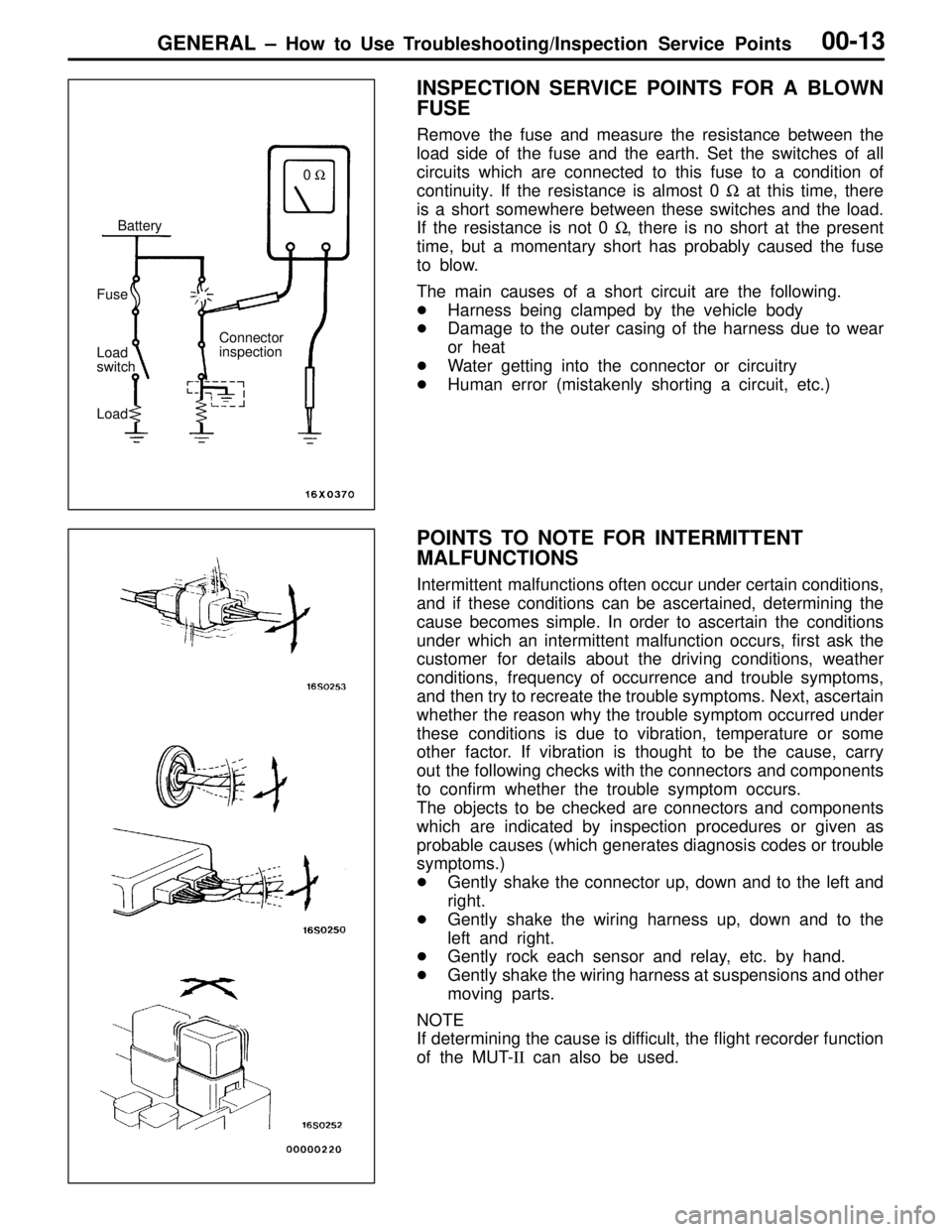
GENERAL – How to Use Troubleshooting/Inspection Service Points00-13
INSPECTION SERVICE POINTS FOR A BLOWN
FUSE
Remove the fuse and measure the resistance between the
load side of the fuse and the earth. Set the switches of all
circuits which are connected to this fuse to a condition of
continuity. If the resistance is almost 0 Ω at this time, there
is a short somewhere between these switches and the load.
If the resistance is not 0 Ω, there is no short at the present
time, but a momentary short has probably caused the fuse
to blow.
The main causes of a short circuit are the following.
Harness being clamped by the vehicle body
Damage to the outer casing of the harness due to wear
or heat
Water getting into the connector or circuitry
Human error (mistakenly shorting a circuit, etc.)
POINTS TO NOTE FOR INTERMITTENT
MALFUNCTIONS
Intermittent malfunctions often occur under certain conditions,
and if these conditions can be ascertained, determining the
cause becomes simple. In order to ascertain the conditions
under which an intermittent malfunction occurs, first ask the
customer for details about the driving conditions, weather
conditions, frequency of occurrence and trouble symptoms,
and then try to recreate the trouble symptoms. Next, ascertain
whether the reason why the trouble symptom occurred under
these conditions is due to vibration, temperature or some
other factor. If vibration is thought to be the cause, carry
out the following checks with the connectors and components
to confirm whether the trouble symptom occurs.
The objects to be checked are connectors and components
which are indicated by inspection procedures or given as
probable causes (which generates diagnosis codes or trouble
symptoms.)
Gently shake the connector up, down and to the left and
right.
Gently shake the wiring harness up, down and to the
left and right.
Gently rock each sensor and relay, etc. by hand.
Gently shake the wiring harness at suspensions and other
moving parts.
NOTE
If determining the cause is difficult, the flight recorder function
of the MUT-II can also be used.
Battery
Fuse
Load
switch
LoadConnector
inspection0 Ω
Page 19 of 558
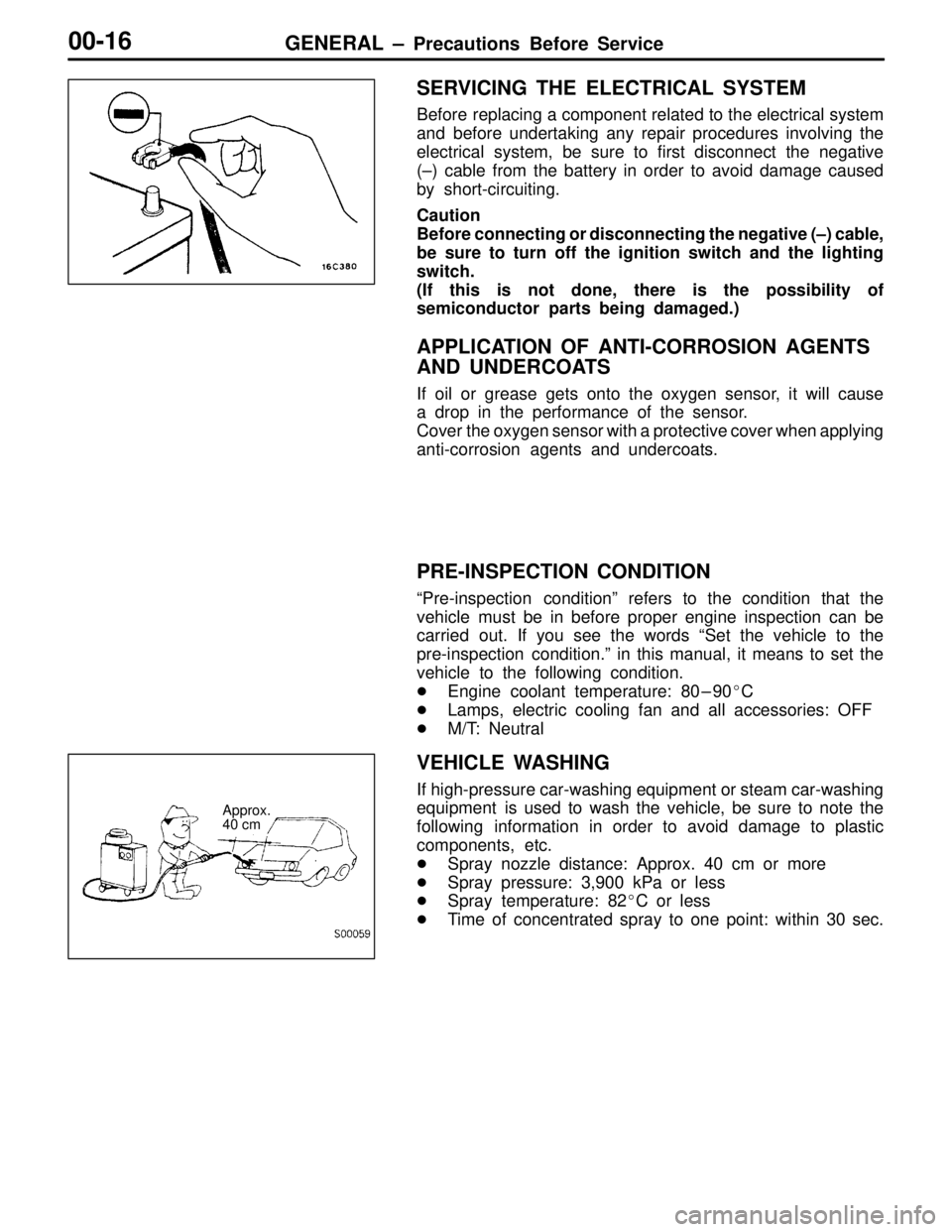
GENERAL – Precautions Before Service00-16
SERVICING THE ELECTRICAL SYSTEM
Before replacing a component related to the electrical system
and before undertaking any repair procedures involving the
electrical system, be sure to first disconnect the negative
(–) cable from the battery in order to avoid damage caused
by short-circuiting.
Caution
Before connecting or disconnecting the negative (–) cable,
be sure to turn off the ignition switch and the lighting
switch.
(If this is not done, there is the possibility of
semiconductor parts being damaged.)
APPLICATION OF ANTI-CORROSION AGENTS
AND UNDERCOATS
If oil or grease gets onto the oxygen sensor, it will cause
a drop in the performance of the sensor.
Cover the oxygen sensor with a protective cover when applying
anti-corrosion agents and undercoats.
PRE-INSPECTION CONDITION
“Pre-inspection condition” refers to the condition that the
vehicle must be in before proper engine inspection can be
carried out. If you see the words “Set the vehicle to the
pre-inspection condition.” in this manual, it means to set the
vehicle to the following condition.
Engine coolant temperature: 80–90C
Lamps, electric cooling fan and all accessories: OFF
M/T: Neutral
VEHICLE WASHING
If high-pressure car-washing equipment or steam car-washing
equipment is used to wash the vehicle, be sure to note the
following information in order to avoid damage to plastic
components, etc.
Spray nozzle distance: Approx. 40 cm or more
Spray pressure: 3,900 kPa or less
Spray temperature: 82C or less
Time of concentrated spray to one point: within 30 sec.
Approx.
40 cm
Page 30 of 558
ENGINE – Specifications11-5
ItemsLimit Standard value
Alternator
Rotor coil resistance ΩApprox. 3 – 5–
Protrusion length of brush mm–2
Starter motor
Commutator runout mm0.050.1
Commutator outer diameter mm32.031.4
Commutator undercut mm0.5–
TORQUE SPECIFICATIONS
ItemsNm
Alternator and ignition system
Oil level gauge guide13
Water pump pulley9
Alternator brace (Alternator side)21
Alternator brace (Tightened with water pump)23
Alternator pivot bolt44
Crankshaft pulley25
Center cover3
Spark plug25
Ignition coil10
Timing belt
Timing belt cover (Flange bolt)11
Timing belt cover (Washer bolt)9
Power steering pump bracket49
Tensioner pulley49
Tensioner arm24
Auto tensioner24
Idler pulley48
Crank angle sensor9
Oil pump sprocket54
Camshaft bolt11 8
Tensioner “B”19
Counterbalance shaft sprocket45
Page 31 of 558
ENGINE – Specifications11-6
ItemsNm
Rocker cover3.5
Engine support bracket49
Camshaft sprocket bolt88
Timing belt rear right cover11
Timing belt rear left upper cover11
Fuel and emission control parts
Throttle body18
Fuel pressure regulator9
Delivery pipe11
Vacuum tank bracket9
Solenoid valve bracket9
Solenoid valve9
Vacuum hose and vacuum pipe11
Secondary air intake manifold
Heat protector13
Vacuum hose and vacuum pipe11
Air pipe (Heat protector side)13
Air pipe (Cam position sensor side)11
Air pipe (Eye bolt)49
Air pipe (Control valve side)24
Air control valve21
Air control valve bracket24
Intake manifold stay30
Intake manifold (M8)19
Intake manifold (M10)35
Exhaust manifold
Engine hanger12
Heat protector (Turbocharger side)14
Oxygen sensor54
Exhaust fitting bolt59
Exhaust fitting nut59
Air outlet fitting19
Page 32 of 558
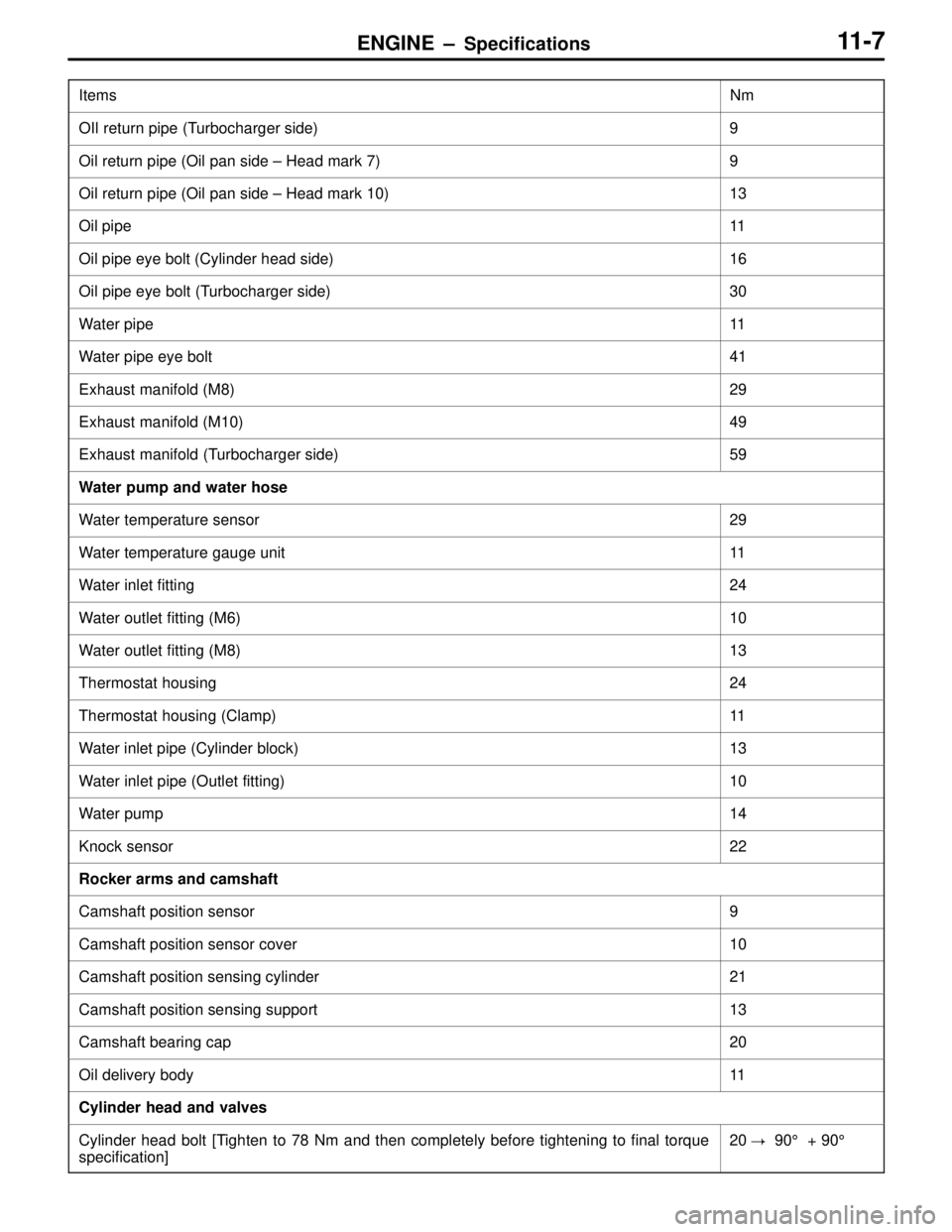
ENGINE – Specifications11-7
ItemsNm
OIl return pipe (Turbocharger side)9
Oil return pipe (Oil pan side – Head mark 7)9
Oil return pipe (Oil pan side – Head mark 10)13
Oil pipe11
Oil pipe eye bolt (Cylinder head side)16
Oil pipe eye bolt (Turbocharger side)30
Water pipe11
Water pipe eye bolt41
Exhaust manifold (M8)29
Exhaust manifold (M10)49
Exhaust manifold (Turbocharger side)59
Water pump and water hose
Water temperature sensor29
Water temperature gauge unit11
Water inlet fitting24
Water outlet fitting (M6)10
Water outlet fitting (M8)13
Thermostat housing24
Thermostat housing (Clamp)11
Water inlet pipe (Cylinder block)13
Water inlet pipe (Outlet fitting)10
Water pump14
Knock sensor22
Rocker arms and camshaft
Camshaft position sensor9
Camshaft position sensor cover10
Camshaft position sensing cylinder21
Camshaft position sensing support13
Camshaft bearing cap20
Oil delivery body11
Cylinder head and valves
Cylinder head bolt [Tighten to 78 Nm and then completely before tightening to final torque
specification]20 90° + 90°
Page 33 of 558
ENGINE – Specifications11-8
ItemsNm
Front case and oil pan
Drain plug39
Oil pan7
Oil screen19
Buffle plate22
Oil pressure switch10
Oil cooler by-pass valve54
Relief plug44
Plug24
Front case24
Oil pump cover (Screw)10
Oil pump cover (Bolt)16
Piston and connecting rods
Connecting rod nut20 + 90° to 94°
Crankshaft and flywheel
Flywheel bolt132
Rear plate11
Bell housing cover9
Oil seal case11
Beam bearing cap bolt25 + 90°
Check valve32
Throttle body
Throttle position sensor3.5
Idle speed control body assembly3.5
Turbocharger
Waste gate actuator11
Page 34 of 558
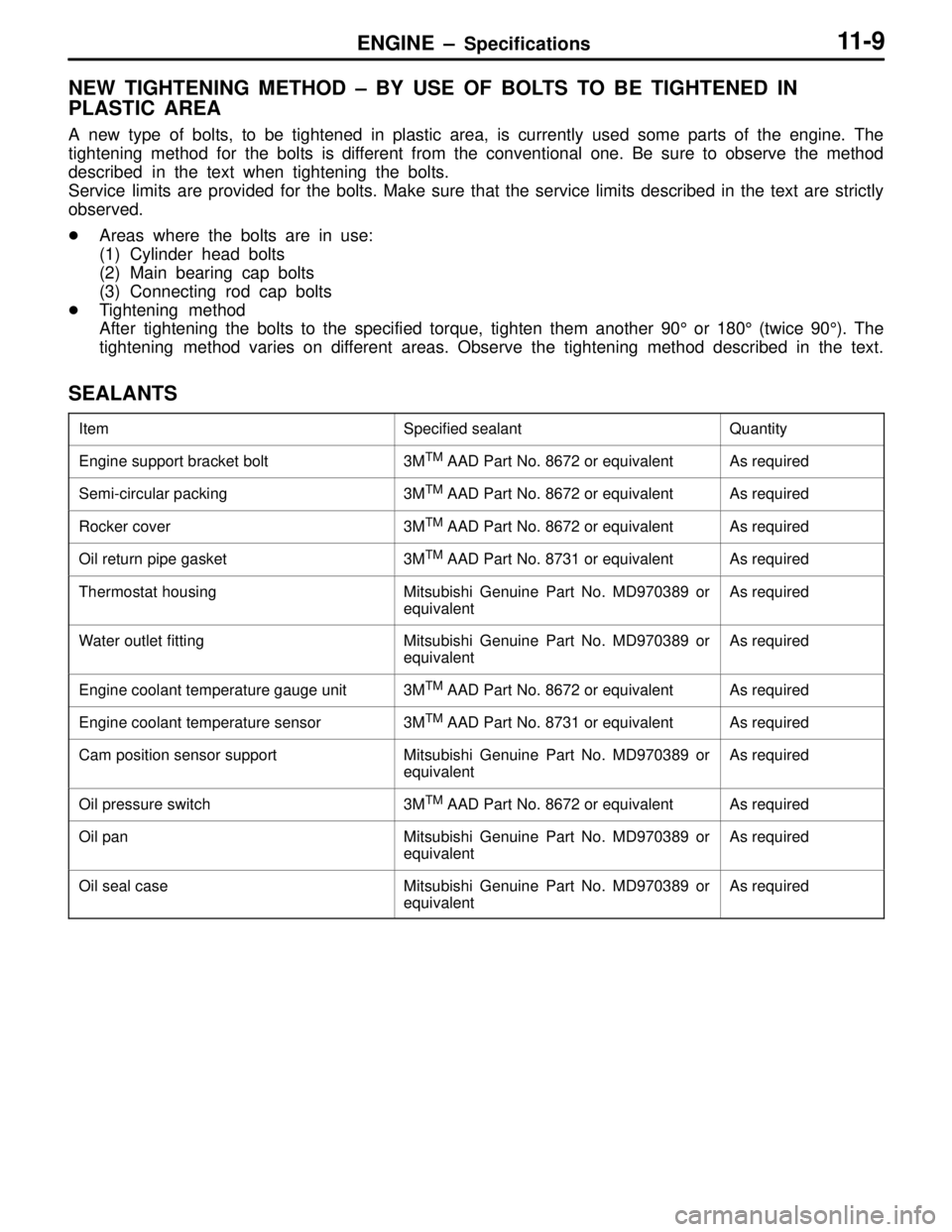
ENGINE – Specifications11-9
NEW TIGHTENING METHOD – BY USE OF BOLTS TO BE TIGHTENED IN
PLASTIC AREA
A new type of bolts, to be tightened in plastic area, is currently used some parts of the engine. The
tightening method for the bolts is different from the conventional one. Be sure to observe the method
described in the text when tightening the bolts.
Service limits are provided for the bolts. Make sure that the service limits described in the text are strictly
observed.
Areas where the bolts are in use:
(1) Cylinder head bolts
(2) Main bearing cap bolts
(3) Connecting rod cap bolts
Tightening method
After tightening the bolts to the specified torque, tighten them another 90° or 180° (twice 90°). The
tightening method varies on different areas. Observe the tightening method described in the text.
SEALANTS
ItemSpecified sealantQuantity
Engine support bracket bolt3MTM AAD Part No. 8672 or equivalentAs required
Semi-circular packing3MTM AAD Part No. 8672 or equivalentAs required
Rocker cover3MTM AAD Part No. 8672 or equivalentAs required
Oil return pipe gasket3MTM AAD Part No. 8731 or equivalentAs required
Thermostat housingMitsubishi Genuine Part No. MD970389 or
equivalentAs required
Water outlet fittingMitsubishi Genuine Part No. MD970389 or
equivalentAs required
Engine coolant temperature gauge unit3MTM AAD Part No. 8672 or equivalentAs required
Engine coolant temperature sensor3MTM AAD Part No. 8731 or equivalentAs required
Cam position sensor supportMitsubishi Genuine Part No. MD970389 or
equivalentAs required
Oil pressure switch3MTM AAD Part No. 8672 or equivalentAs required
Oil panMitsubishi Genuine Part No. MD970389 or
equivalentAs required
Oil seal caseMitsubishi Genuine Part No. MD970389 or
equivalentAs required
Page 40 of 558
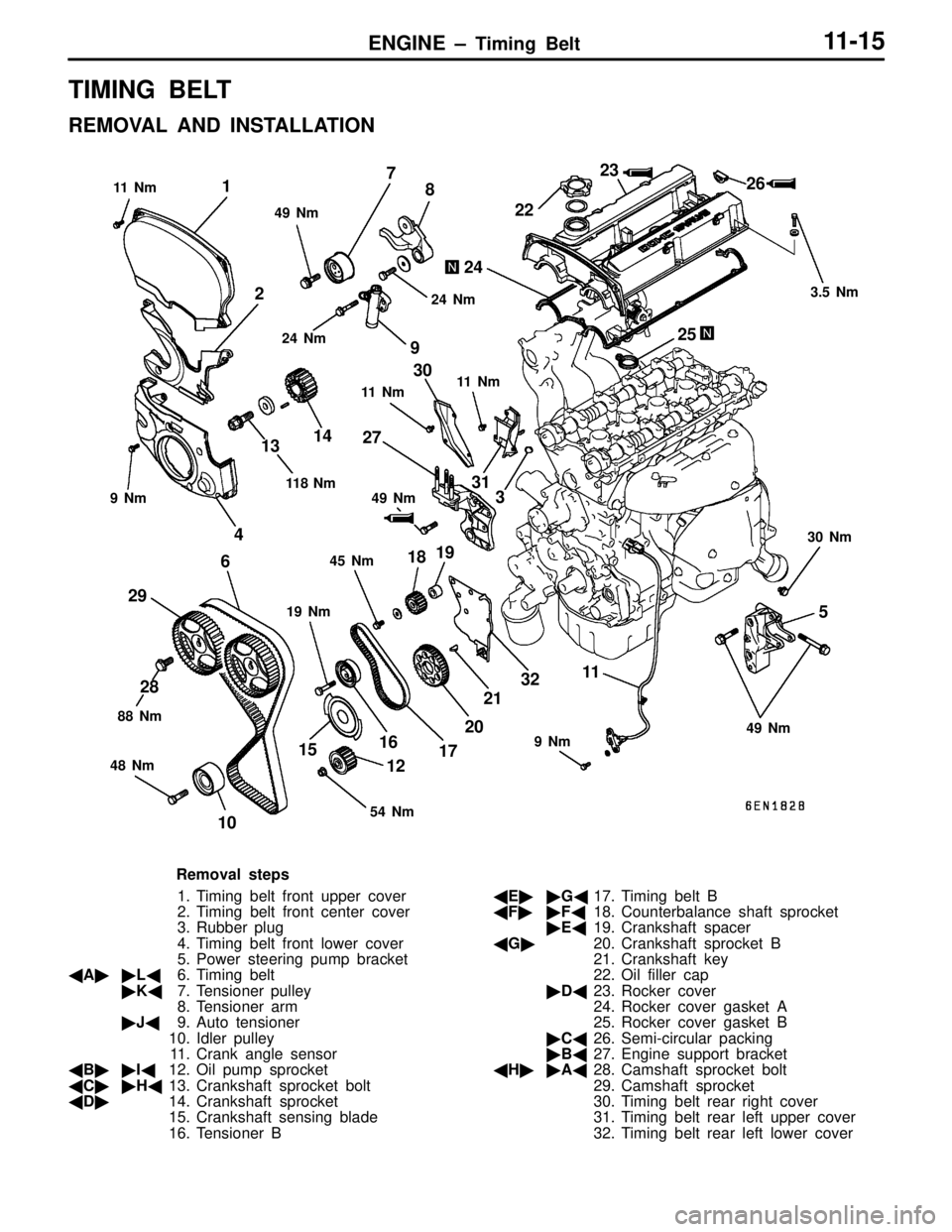
ENGINE – Timing Belt11-15
TIMING BELT
REMOVAL AND INSTALLATION
1
2
3
4
5 67
8
9
1011
12 1314
1516
17 1819
20212223
24
2526
27
28 2930
31
32
9 Nm
9 Nm 49 Nm 11 N m
11 N m
19 Nm 3.5 Nm
30 Nm
45 Nm 49 Nm 11 8 N m
88 Nm
48 Nm 49 Nm 11 N m
24 Nm
24 Nm
54 Nm
Removal steps
1. Timing belt front upper cover
2. Timing belt front center cover
3. Rubber plug
4. Timing belt front lower cover
5. Power steering pump bracket
AL6. Timing belt
K7. Tensioner pulley
8. Tensioner arm
J9. Auto tensioner
10. Idler pulley
11. Crank angle sensor
BI12. Oil pump sprocket
CH13. Crankshaft sprocket bolt
D14. Crankshaft sprocket
15. Crankshaft sensing blade
16. Tensioner BEG17. Timing belt B
FF18. Counterbalance shaft sprocket
E19. Crankshaft spacer
G20. Crankshaft sprocket B
21. Crankshaft key
22. Oil filler cap
D23. Rocker cover
24. Rocker cover gasket A
25. Rocker cover gasket B
C26. Semi-circular packing
B27. Engine support bracket
HA28. Camshaft sprocket bolt
29. Camshaft sprocket
30. Timing belt rear right cover
31. Timing belt rear left upper cover
32. Timing belt rear left lower cover