Page 9 of 558
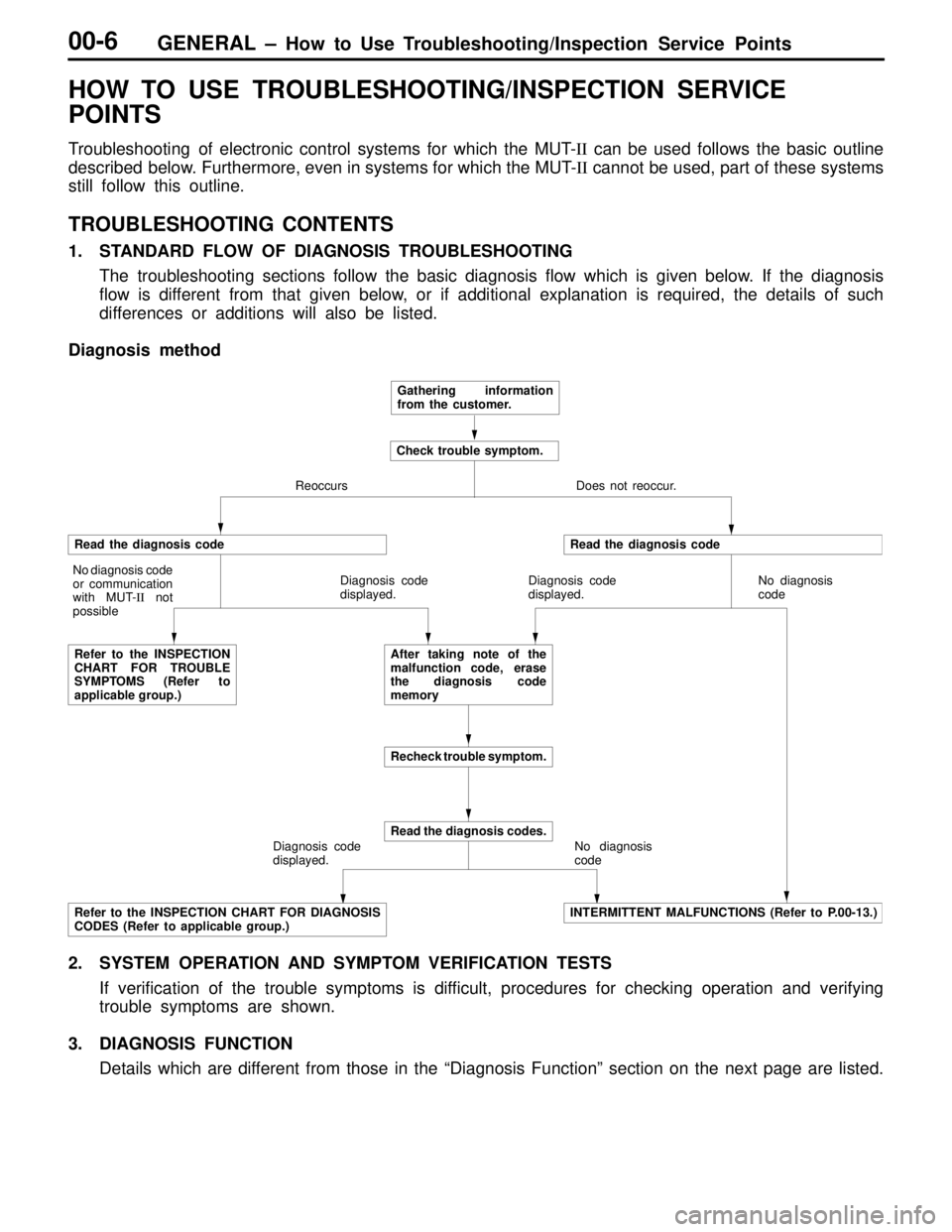
GENERAL – How to Use Troubleshooting/Inspection Service Points00-6
HOW TO USE TROUBLESHOOTING/INSPECTION SERVICE
POINTS
Troubleshooting of electronic control systems for which the MUT-II can be used follows the basic outline
described below. Furthermore, even in systems for which the MUT-II cannot be used, part of these systems
still follow this outline.
TROUBLESHOOTING CONTENTS
1. STANDARD FLOW OF DIAGNOSIS TROUBLESHOOTING
The troubleshooting sections follow the basic diagnosis flow which is given below. If the diagnosis
flow is different from that given below, or if additional explanation is required, the details of such
differences or additions will also be listed.
Diagnosis method
Gathering information
from the customer.
Check trouble symptom.
Reoccurs Does not reoccur.
Read the diagnosis code
No diagnosis code
or communication
with MUT-II not
possible
Refer to the INSPECTION
CHART FOR TROUBLE
SYMPTOMS (Refer to
applicable group.)Diagnosis code
displayed.
Read the diagnosis code
Diagnosis code
displayed.No diagnosis
code
After taking note of the
malfunction code, erase
the diagnosis code
memory
Recheck trouble symptom.
Diagnosis code
displayed.
Read the diagnosis codes.
No diagnosis
code
Refer to the INSPECTION CHART FOR DIAGNOSIS
CODES (Refer to applicable group.)INTERMITTENT MALFUNCTIONS (Refer to P.00-13.)
2. SYSTEM OPERATION AND SYMPTOM VERIFICATION TESTS
If verification of the trouble symptoms is difficult, procedures for checking operation and verifying
trouble symptoms are shown.
3. DIAGNOSIS FUNCTION
Details which are different from those in the “Diagnosis Function” section on the next page are listed.
Page 10 of 558
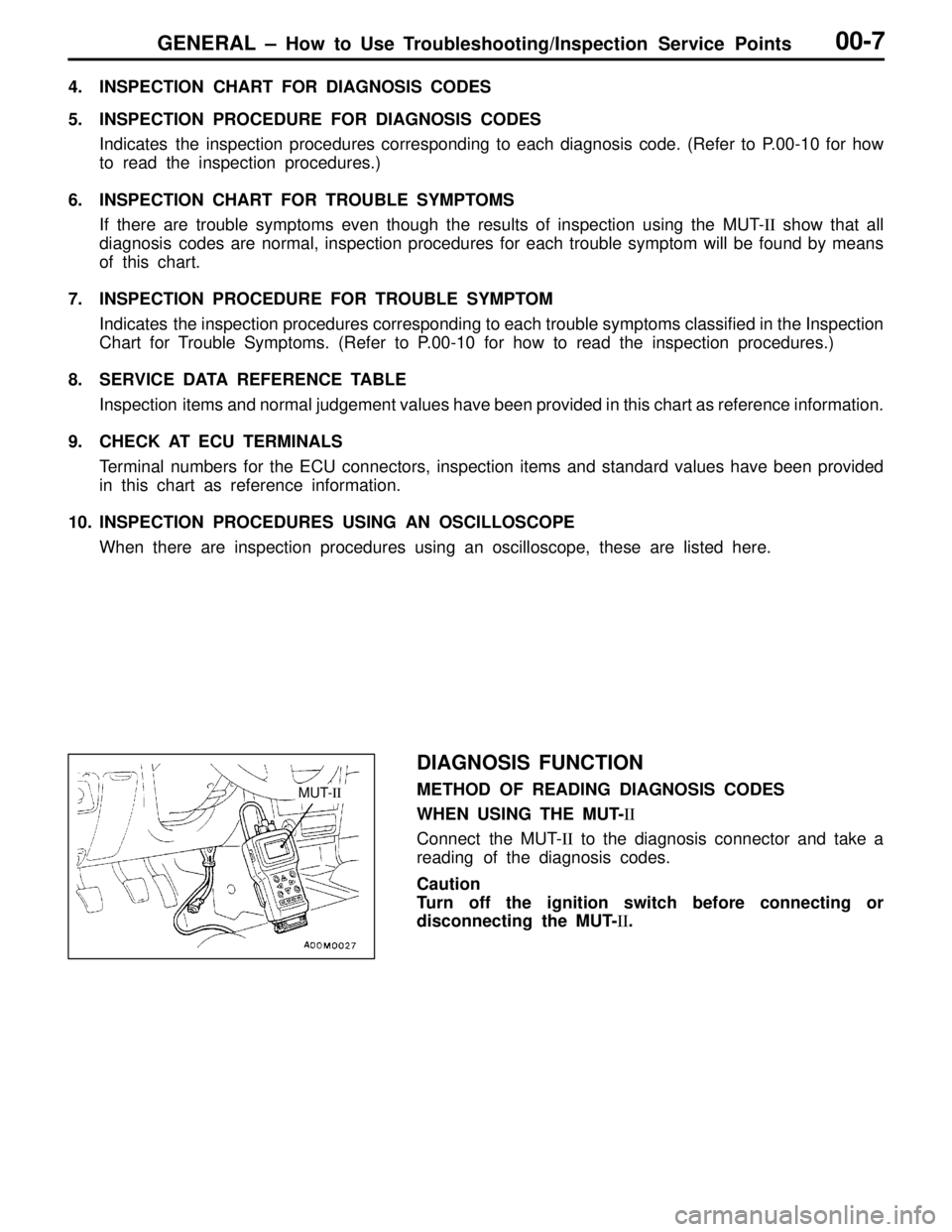
GENERAL – How to Use Troubleshooting/Inspection Service Points00-7
4. INSPECTION CHART FOR DIAGNOSIS CODES
5. INSPECTION PROCEDURE FOR DIAGNOSIS CODES
Indicates the inspection procedures corresponding to each diagnosis code. (Refer to P.00-10 for how
to read the inspection procedures.)
6. INSPECTION CHART FOR TROUBLE SYMPTOMS
If there are trouble symptoms even though the results of inspection using the MUT-II show that all
diagnosis codes are normal, inspection procedures for each trouble symptom will be found by means
of this chart.
7. INSPECTION PROCEDURE FOR TROUBLE SYMPTOM
Indicates the inspection procedures corresponding to each trouble symptoms classified in the Inspection
Chart for Trouble Symptoms. (Refer to P.00-10 for how to read the inspection procedures.)
8. SERVICE DATA REFERENCE TABLE
Inspection items and normal judgement values have been provided in this chart as reference information.
9. CHECK AT ECU TERMINALS
Terminal numbers for the ECU connectors, inspection items and standard values have been provided
in this chart as reference information.
10. INSPECTION PROCEDURES USING AN OSCILLOSCOPE
When there are inspection procedures using an oscilloscope, these are listed here.
DIAGNOSIS FUNCTION
METHOD OF READING DIAGNOSIS CODES
WHEN USING THE MUT-II
Connect the MUT-II to the diagnosis connector and take a
reading of the diagnosis codes.
Caution
Turn off the ignition switch before connecting or
disconnecting the MUT-II.MUT-II
Page 11 of 558
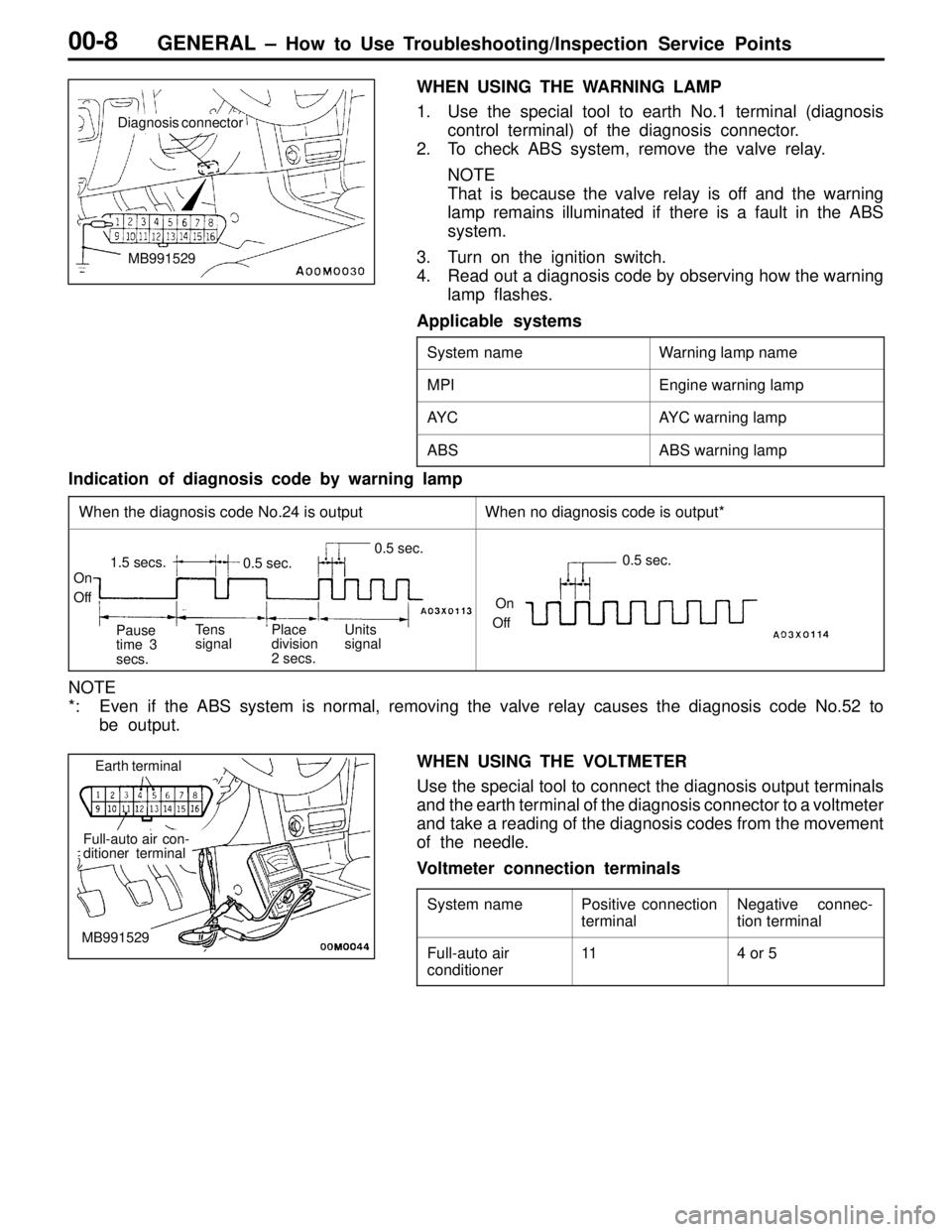
GENERAL – How to Use Troubleshooting/Inspection Service Points00-8
WHEN USING THE WARNING LAMP
1. Use the special tool to earth No.1 terminal (diagnosis
control terminal) of the diagnosis connector.
2. To check ABS system, remove the valve relay.
NOTE
That is because the valve relay is off and the warning
lamp remains illuminated if there is a fault in the ABS
system.
3. Turn on the ignition switch.
4. Read out a diagnosis code by observing how the warning
lamp flashes.
Applicable systems
System nameWarning lamp name
MPIEngine warning lamp
AY CAYC warning lamp
ABSABS warning lamp
Indication of diagnosis code by warning lamp
When the diagnosis code No.24 is outputWhen no diagnosis code is output*
On
Off
1.5 secs.0.5 sec.0.5 sec.
Pause
time 3
secs.Tens
signalPlace
division
2 secs.Units
signal
On
Off
0.5 sec.
NOTE
*: Even if the ABS system is normal, removing the valve relay causes the diagnosis code No.52 to
be output.
WHEN USING THE VOLTMETER
Use the special tool to connect the diagnosis output terminals
and the earth terminal of the diagnosis connector to a voltmeter
and take a reading of the diagnosis codes from the movement
of the needle.
Voltmeter connection terminals
System namePositive connection
terminalNegative connec-
tion terminal
Full-auto air
conditioner114 or 5
Diagnosis connector
MB991529
Earth terminal
Full-auto air con-
ditioner terminal
MB991529
Page 12 of 558
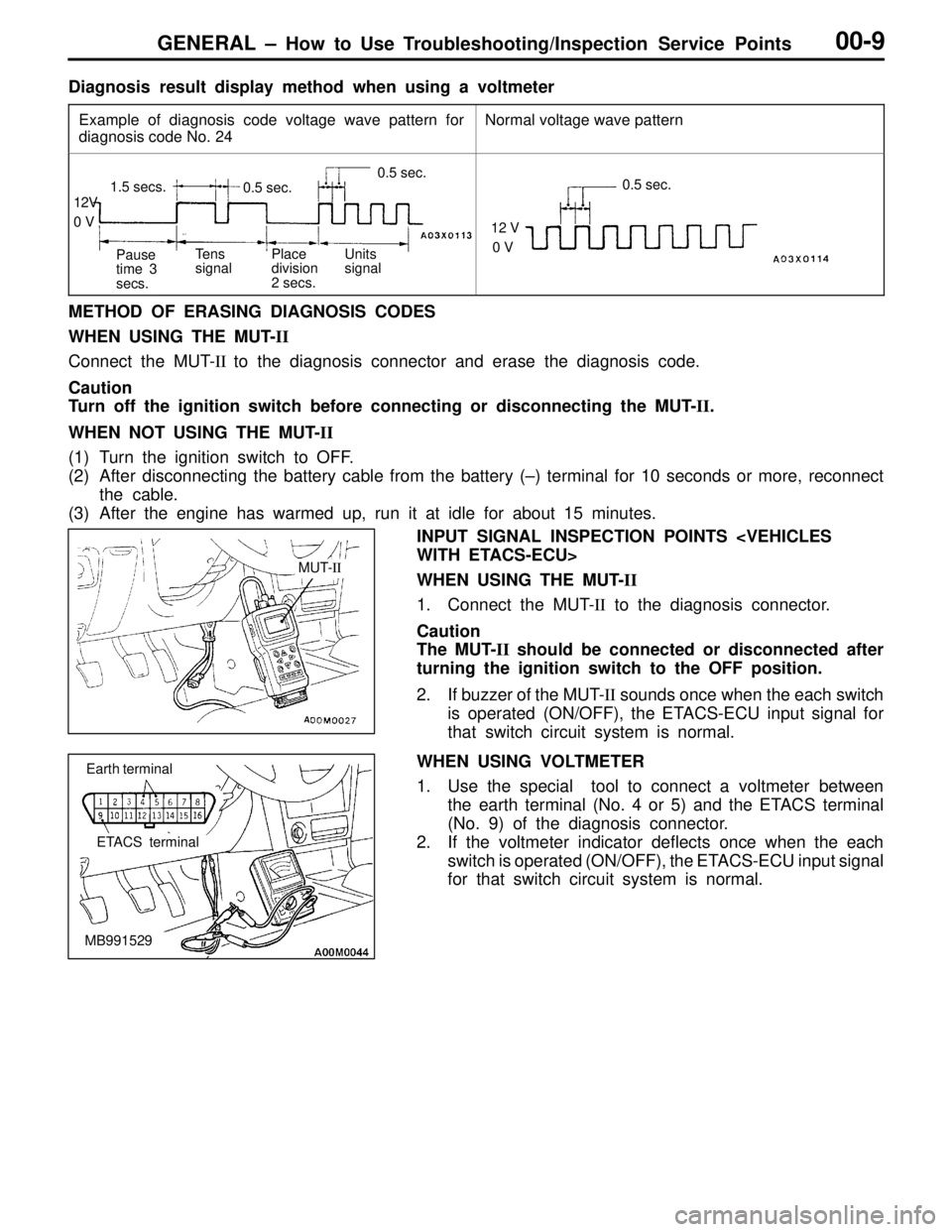
GENERAL – How to Use Troubleshooting/Inspection Service Points00-9
Diagnosis result display method when using a voltmeter
Example of diagnosis code voltage wave pattern for
diagnosis code No. 24Normal voltage wave pattern
12V
0 V
1.5 secs.0.5 sec.0.5 sec.
Pause
time 3
secs.Tens
signalPlace
division
2 secs.Units
signal
12 V
0 V
0.5 sec.
METHOD OF ERASING DIAGNOSIS CODES
WHEN USING THE MUT-II
Connect the MUT-II to the diagnosis connector and erase the diagnosis code.
Caution
Turn off the ignition switch before connecting or disconnecting the MUT-II.
WHEN NOT USING THE MUT-II
(1) Turn the ignition switch to OFF.
(2) After disconnecting the battery cable from the battery (–) terminal for 10 seconds or more, reconnect
the cable.
(3) After the engine has warmed up, run it at idle for about 15 minutes.
INPUT SIGNAL INSPECTION POINTS
WITH ETACS-ECU>
WHEN USING THE MUT-II
1. Connect the MUT-II to the diagnosis connector.
Caution
The MUT-II should be connected or disconnected after
turning the ignition switch to the OFF position.
2. If buzzer of the MUT-II sounds once when the each switch
is operated (ON/OFF), the ETACS-ECU input signal for
that switch circuit system is normal.
WHEN USING VOLTMETER
1. Use the special tool to connect a voltmeter between
the earth terminal (No. 4 or 5) and the ETACS terminal
(No. 9) of the diagnosis connector.
2. If the voltmeter indicator deflects once when the each
switch is operated (ON/OFF), the ETACS-ECU input signal
for that switch circuit system is normal.
MUT-II
Earth terminal
ETACS terminal
MB991529
Page 13 of 558
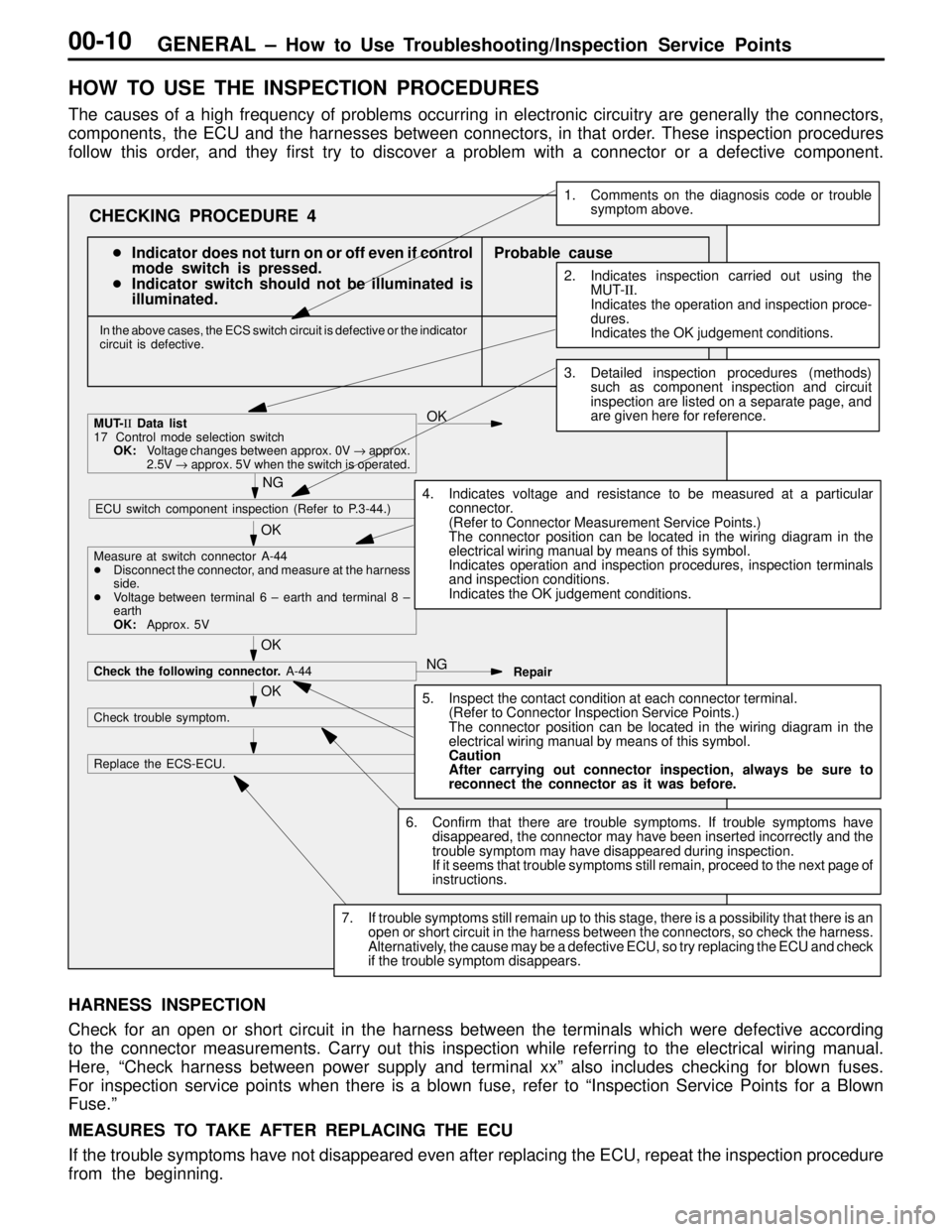
GENERAL – How to Use Troubleshooting/Inspection Service Points00-10
HOW TO USE THE INSPECTION PROCEDURES
The causes of a high frequency of problems occurring in electronic circuitry are generally the connectors,
components, the ECU and the harnesses between connectors, in that order. These inspection procedures
follow this order, and they first try to discover a problem with a connector or a defective component.
Indicator does not turn on or off even if control
mode switch is pressed.
Indicator switch should not be illuminated is
illuminated.Probable cause
OK
OK
OK
Measure at switch connector A-44
Disconnect the connector, and measure at the harness
side.
Voltage between terminal 6 – earth and terminal 8 –
earth
OK:Approx. 5V
OK
NG
Check the following connector. A-44
Repair
OK
Check trouble symptom.
Replace the ECS-ECU.
In the above cases, the ECS switch circuit is defective or the indicator
circuit is defective.
CHECKING PROCEDURE 4
2. Indicates inspection carried out using the
MUT-II.
Indicates the operation and inspection proce-
dures.
Indicates the OK judgement conditions.
3. Detailed inspection procedures (methods)
such as component inspection and circuit
inspection are listed on a separate page, and
are given here for reference.
5. Inspect the contact condition at each connector terminal.
(Refer to Connector Inspection Service Points.)
The connector position can be located in the wiring diagram in the
electrical wiring manual by means of this symbol.
Caution
After carrying out connector inspection, always be sure to
reconnect the connector as it was before.
6. Confirm that there are trouble symptoms. If trouble symptoms have
disappeared, the connector may have been inserted incorrectly and the
trouble symptom may have disappeared during inspection.
If it seems that trouble symptoms still remain, proceed to the next page of
instructions.
7. If trouble symptoms still remain up to this stage, there is a possibility that there is an
open or short circuit in the harness between the connectors, so check the harness.
Alternatively, the cause may be a defective ECU, so try replacing the ECU and check
if the trouble symptom disappears.
NGECU switch component inspection (Refer to P.3-44.)
NG
1. Comments on the diagnosis code or trouble
symptom above.
MUT-II Data list
17 Control mode selection switch
OK:Voltage changes between approx. 0V → approx.
2.5V → approx. 5V when the switch is operated.
4. Indicates voltage and resistance to be measured at a particular
connector.
(Refer to Connector Measurement Service Points.)
The connector position can be located in the wiring diagram in the
electrical wiring manual by means of this symbol.
Indicates operation and inspection procedures, inspection terminals
and inspection conditions.
Indicates the OK judgement conditions.
HARNESS INSPECTION
Check for an open or short circuit in the harness between the terminals which were defective according
to the connector measurements. Carry out this inspection while referring to the electrical wiring manual.
Here, “Check harness between power supply and terminal xx” also includes checking for blown fuses.
For inspection service points when there is a blown fuse, refer to “Inspection Service Points for a Blown
Fuse.”
MEASURES TO TAKE AFTER REPLACING THE ECU
If the trouble symptoms have not disappeared even after replacing the ECU, repeat the inspection procedure
from the beginning.
Page 14 of 558

GENERAL – How to Use Troubleshooting/Inspection Service Points00-11
CONNECTOR MEASUREMENT SERVICE POINTS
Turn the ignition switch to OFF when connecting disconnecting
the connectors, and turn the ignition switch to ON when
measuring if there are no instructions to be contrary.
IF INSPECTING WITH THE CONNECTOR CONNECTED
(WITH CIRCUIT IN A CONDITION OF CONTINUITY)
Waterproof Connectors
Be sure to use the special tool (harness connector). Never
insert a test bar from the harness side, because to do so
will reduce the waterproof performance and result in corrosion.
Ordinary (non-waterproof) Connectors
Check by inserting the test bar from the harness side. Note
that if the connector (control unit, etc.) is too small to permit
insertion of the test bar, it should not be forced; use a special
tool (the extra-thin probe in the harness set for checking
for this purpose.
IF INSPECTING WITH THE CONNECTOR DISCONNECTED
Use the special tool (inspection harness for connector pin
contact pressure in the harness set for inspection).
The inspection harness for connector pin contact pressure
should be used. the test bar should never be forcibly inserted,
as it may cause a defective contact.
Touch the pin directly with the test bar.
Caution
At this time, be careful not to short the connector pins
with the test bars. To do so may damage the circuits
inside the ECU.
Harness connector
Extra-thin probe
Test bar
Connector
Inspection harness
for connector pin
contact pressure
Page 15 of 558
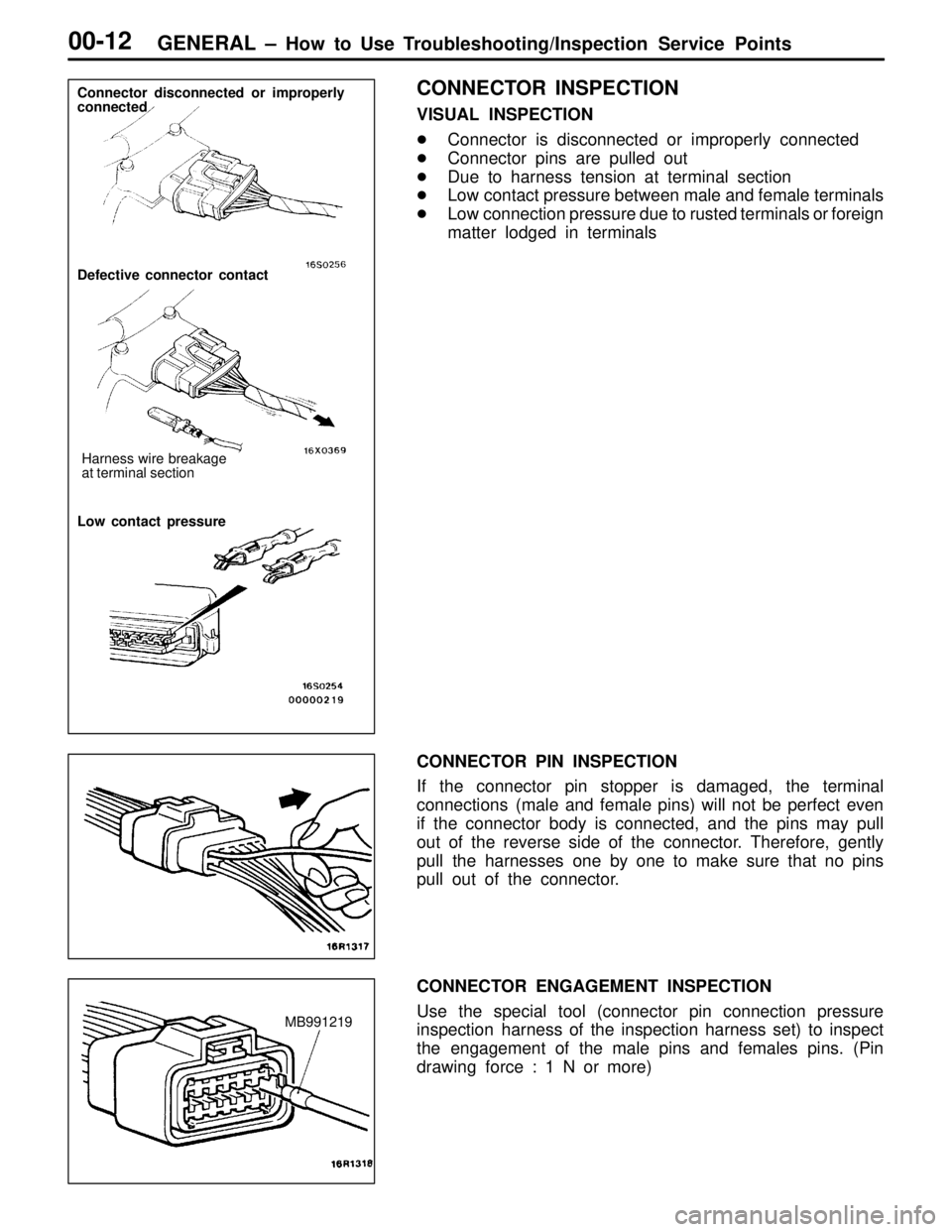
GENERAL – How to Use Troubleshooting/Inspection Service Points00-12
CONNECTOR INSPECTION
VISUAL INSPECTION
Connector is disconnected or improperly connected
Connector pins are pulled out
Due to harness tension at terminal section
Low contact pressure between male and female terminals
Low connection pressure due to rusted terminals or foreign
matter lodged in terminals
CONNECTOR PIN INSPECTION
If the connector pin stopper is damaged, the terminal
connections (male and female pins) will not be perfect even
if the connector body is connected, and the pins may pull
out of the reverse side of the connector. Therefore, gently
pull the harnesses one by one to make sure that no pins
pull out of the connector.
CONNECTOR ENGAGEMENT INSPECTION
Use the special tool (connector pin connection pressure
inspection harness of the inspection harness set) to inspect
the engagement of the male pins and females pins. (Pin
drawing force : 1 N or more)
Connector disconnected or improperly
connected
Defective connector contact
Harness wire breakage
at terminal section
Low contact pressure
MB991219
Page 16 of 558
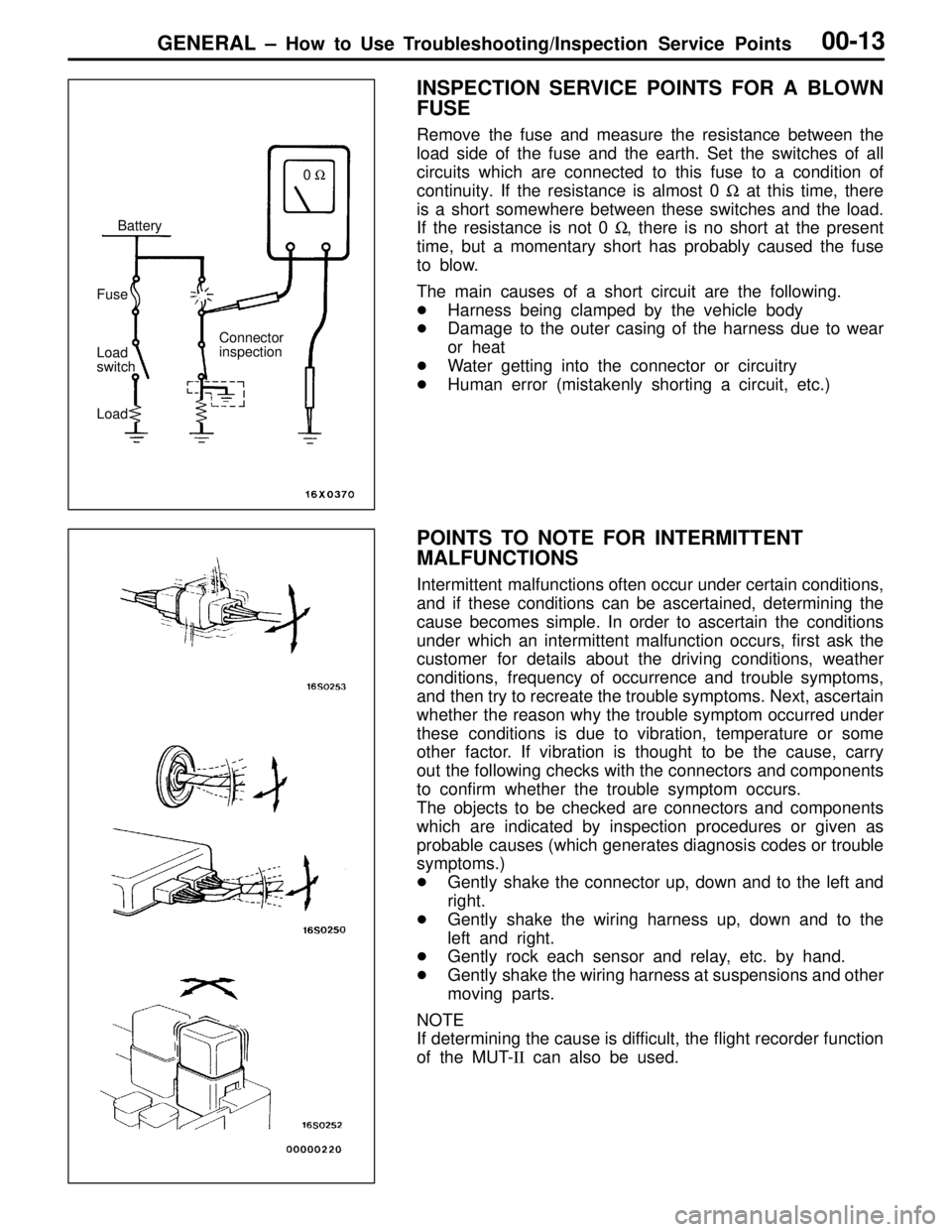
GENERAL – How to Use Troubleshooting/Inspection Service Points00-13
INSPECTION SERVICE POINTS FOR A BLOWN
FUSE
Remove the fuse and measure the resistance between the
load side of the fuse and the earth. Set the switches of all
circuits which are connected to this fuse to a condition of
continuity. If the resistance is almost 0 Ω at this time, there
is a short somewhere between these switches and the load.
If the resistance is not 0 Ω, there is no short at the present
time, but a momentary short has probably caused the fuse
to blow.
The main causes of a short circuit are the following.
Harness being clamped by the vehicle body
Damage to the outer casing of the harness due to wear
or heat
Water getting into the connector or circuitry
Human error (mistakenly shorting a circuit, etc.)
POINTS TO NOTE FOR INTERMITTENT
MALFUNCTIONS
Intermittent malfunctions often occur under certain conditions,
and if these conditions can be ascertained, determining the
cause becomes simple. In order to ascertain the conditions
under which an intermittent malfunction occurs, first ask the
customer for details about the driving conditions, weather
conditions, frequency of occurrence and trouble symptoms,
and then try to recreate the trouble symptoms. Next, ascertain
whether the reason why the trouble symptom occurred under
these conditions is due to vibration, temperature or some
other factor. If vibration is thought to be the cause, carry
out the following checks with the connectors and components
to confirm whether the trouble symptom occurs.
The objects to be checked are connectors and components
which are indicated by inspection procedures or given as
probable causes (which generates diagnosis codes or trouble
symptoms.)
Gently shake the connector up, down and to the left and
right.
Gently shake the wiring harness up, down and to the
left and right.
Gently rock each sensor and relay, etc. by hand.
Gently shake the wiring harness at suspensions and other
moving parts.
NOTE
If determining the cause is difficult, the flight recorder function
of the MUT-II can also be used.
Battery
Fuse
Load
switch
LoadConnector
inspection0 Ω