Page 73 of 558
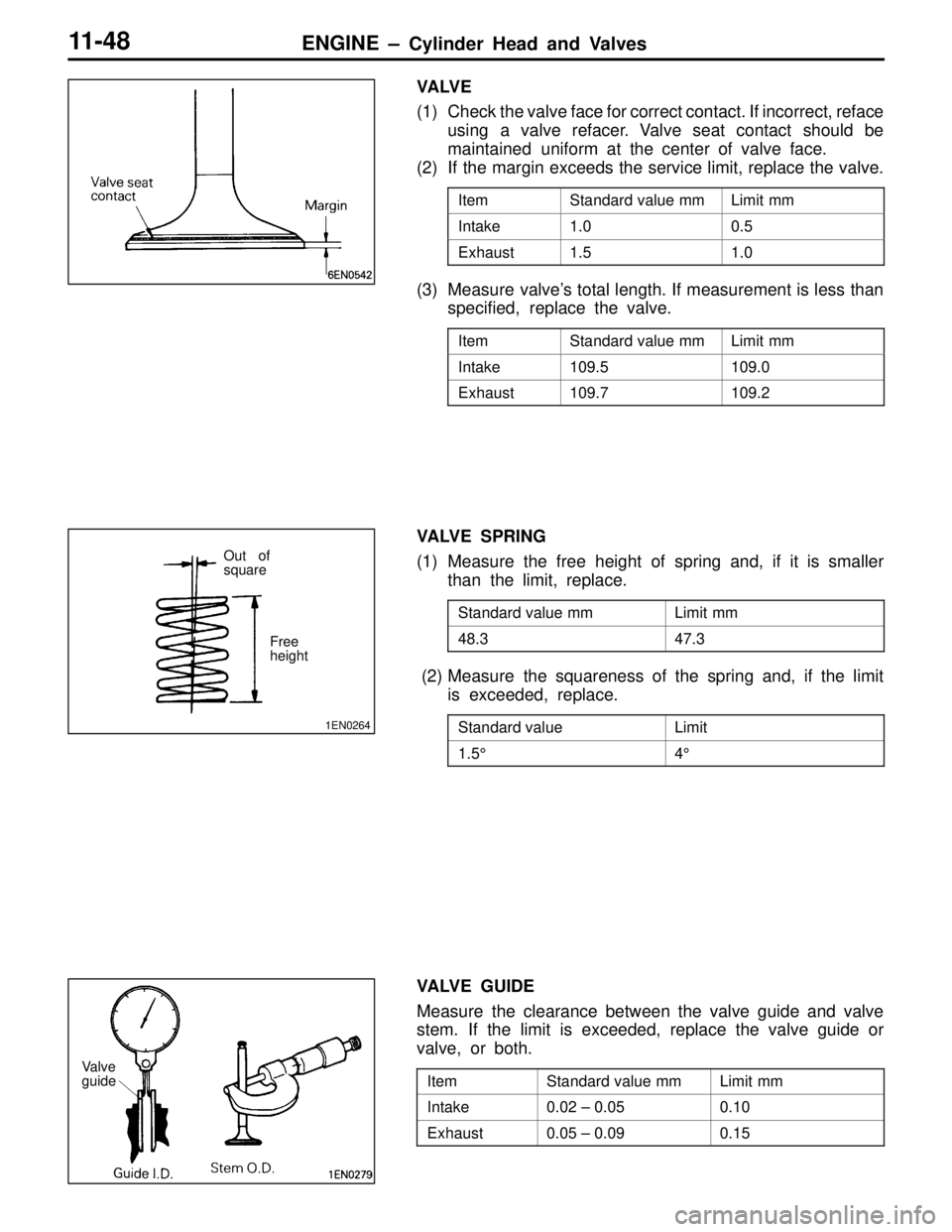
ENGINE – Cylinder Head and Valves11-48
VA LV E
(1) Check the valve face for correct contact. If incorrect, reface
using a valve refacer. Valve seat contact should be
maintained uniform at the center of valve face.
(2) If the margin exceeds the service limit, replace the valve.
ItemStandard value mmLimit mm
Intake1.00.5
Exhaust1.51.0
(3) Measure valve’s total length. If measurement is less than
specified, replace the valve.
ItemStandard value mmLimit mm
Intake109.5109.0
Exhaust109.7109.2
VALVE SPRING
(1) Measure the free height of spring and, if it is smaller
than the limit, replace.
Standard value mmLimit mm
48.347.3
(2) Measure the squareness of the spring and, if the limit
is exceeded, replace.
Standard valueLimit
1.5°4°
VALVE GUIDE
Measure the clearance between the valve guide and valve
stem. If the limit is exceeded, replace the valve guide or
valve, or both.
ItemStandard value mmLimit mm
Intake0.02 – 0.050.10
Exhaust0.05 – 0.090.15
1EN0264
Free
height
Out of
square
Valve
guide
Page 74 of 558
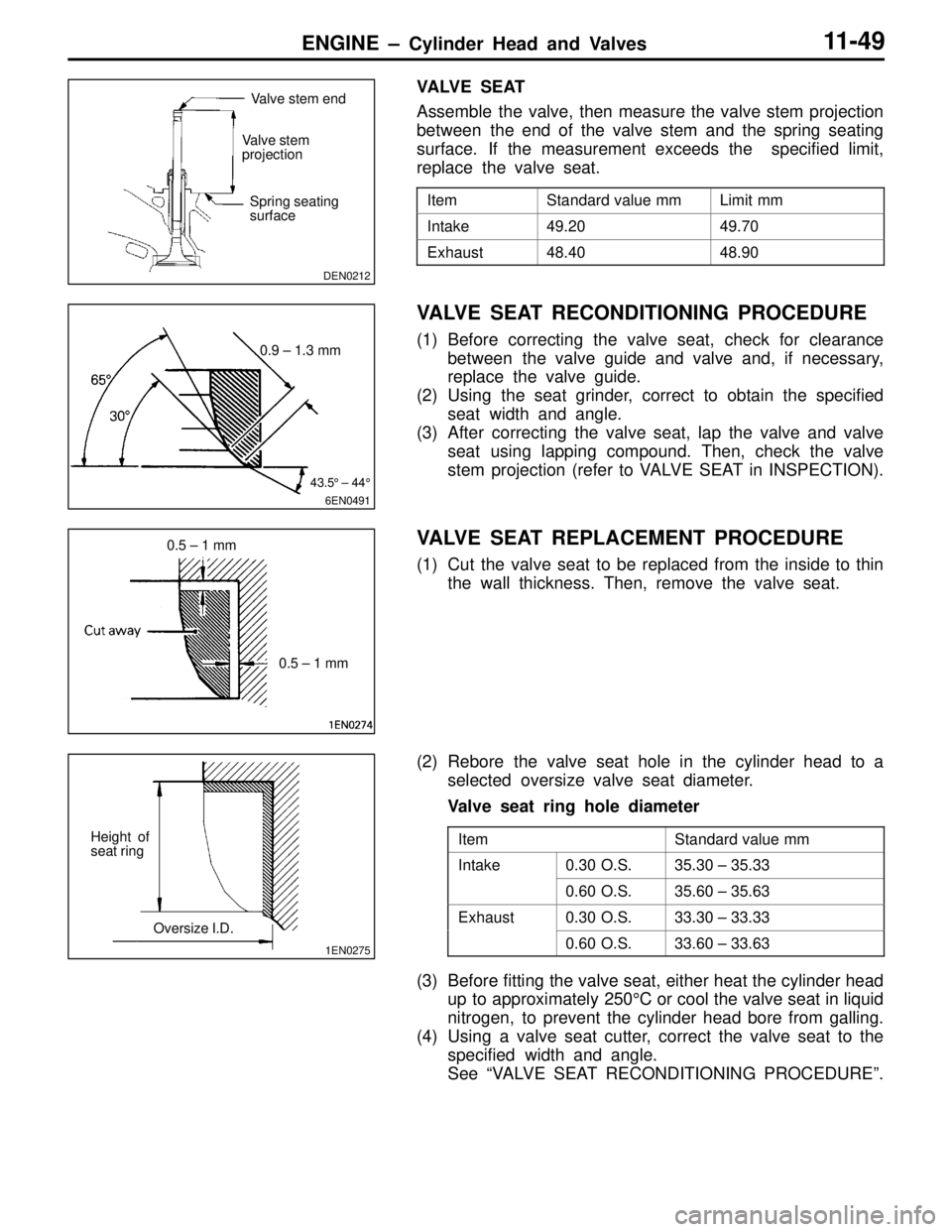
ENGINE – Cylinder Head and Valves11-49
VA LV E S E AT
Assemble the valve, then measure the valve stem projection
between the end of the valve stem and the spring seating
surface. If the measurement exceeds the specified limit,
replace the valve seat.
ItemStandard value mmLimit mm
Intake49.2049.70
Exhaust48.4048.90
VALVE SEAT RECONDITIONING PROCEDURE
(1) Before correcting the valve seat, check for clearance
between the valve guide and valve and, if necessary,
replace the valve guide.
(2) Using the seat grinder, correct to obtain the specified
seat width and angle.
(3) After correcting the valve seat, lap the valve and valve
seat using lapping compound. Then, check the valve
stem projection (refer to VALVE SEAT in INSPECTION).
VALVE SEAT REPLACEMENT PROCEDURE
(1) Cut the valve seat to be replaced from the inside to thin
the wall thickness. Then, remove the valve seat.
(2) Rebore the valve seat hole in the cylinder head to a
selected oversize valve seat diameter.
Valve seat ring hole diameter
ItemStandard value mm
Intake0.30 O.S.35.30 – 35.33
0.60 O.S.35.60 – 35.63
Exhaust0.30 O.S.33.30 – 33.33
0.60 O.S.33.60 – 33.63
(3) Before fitting the valve seat, either heat the cylinder head
up to approximately 250°C or cool the valve seat in liquid
nitrogen, to prevent the cylinder head bore from galling.
(4) Using a valve seat cutter, correct the valve seat to the
specified width and angle.
See “VALVE SEAT RECONDITIONING PROCEDURE”.
DEN0212
Valve stem end
Valve stem
projection
Spring seating
surface
6EN0491
0.9 – 1.3 mm
43.5° – 44°
0.5 – 1 mm
0.5 – 1 mm
1EN0275
Height of
seat ring
Oversize I.D.
Page 75 of 558
ENGINE – Cylinder Head and Valves11-50
VALVE GUIDE REPLACEMENT PROCEDURE
(1) Force the valve guide out toward the cylinder block using
a press.
(2) Machine the valve guide hole in the cylinder head to
the size of the oversize valve guide to be installed.
Caution
Do not use the valve guide of the same size as the
removed one.
Valve gauge hole diameters in cylinder head
ItemStandard value mm
0.05 O.S.12.05 – 12.07
0.25 O.S.12.25 – 12.27
0.50 O.S.12.50 – 12.52
(3) Press-fit the valve guide until it protrude specified value
19.5 mm as shown in the illustration.
Caution
1. Press the valve guide from the cylinder head top
surface.
2. Valve guide for intake valve and that for exhaust
valve are different in length. (45.5 mm for intake
valve; 50.5 mm for exhaust valve)
(4) After the valve guide has been installed, insert a new
valve to check for smooth sliding motion.
1EN0106
Protrusion
Page 76 of 558
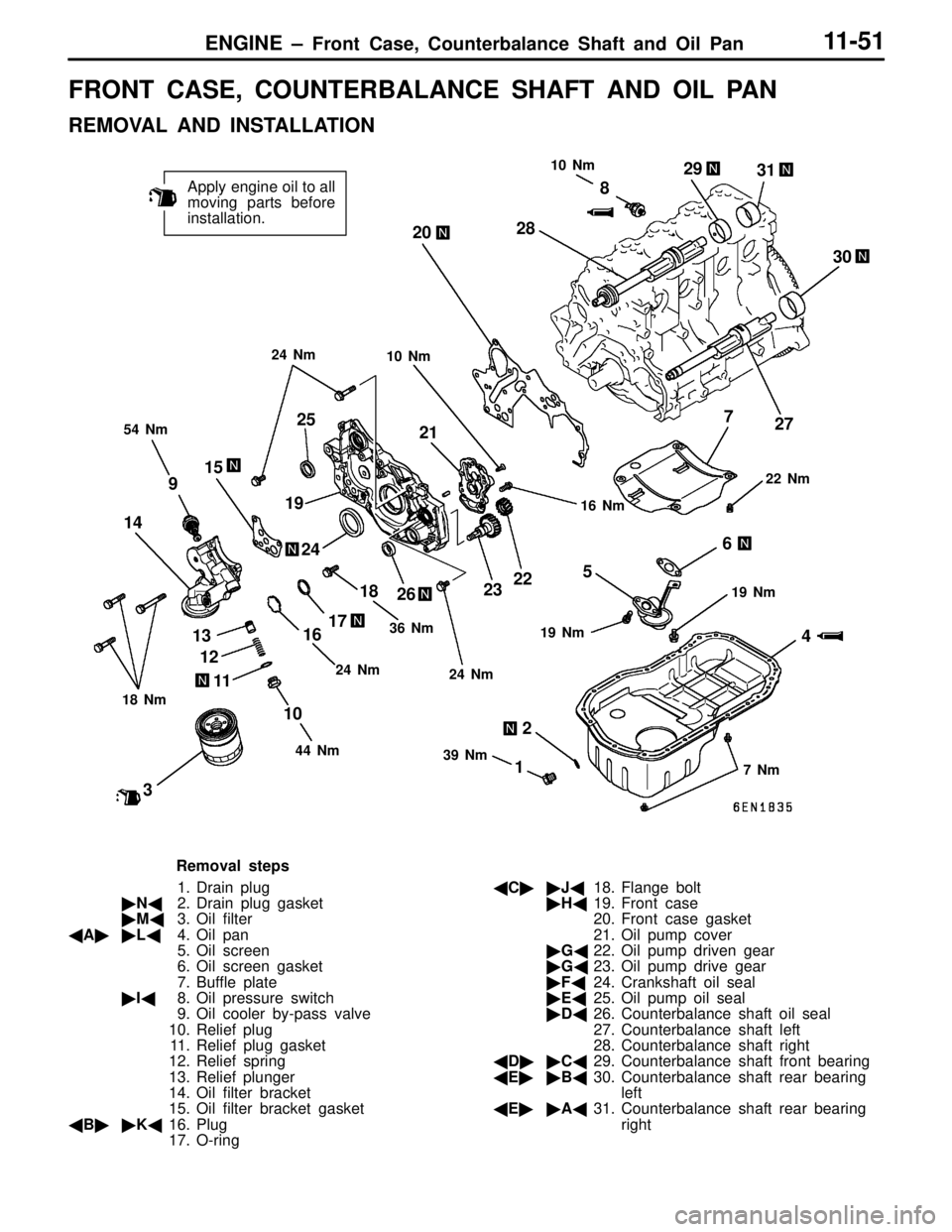
ENGINE – Front Case, Counterbalance Shaft and Oil Pan11-51
FRONT CASE, COUNTERBALANCE SHAFT AND OIL PAN
REMOVAL AND INSTALLATION
16 Nm 10 Nm
39 Nm22 Nm
Apply engine oil to all
moving parts before
installation.
12
34 567 8
9
10 11 12 13 1415
161718 1920
21
22
23 24 25
2627 2829
30
36 Nm
24 Nm 24 Nm19 Nm
44 Nm 18 Nm24 Nm
54 Nm10 Nm
19 Nm
7 Nm
31
Removal steps
1. Drain plug
N2. Drain plug gasket
M3. Oil filter
AL4. Oil pan
5. Oil screen
6. Oil screen gasket
7. Buffle plate
I8. Oil pressure switch
9. Oil cooler by-pass valve
10. Relief plug
11. Relief plug gasket
12. Relief spring
13. Relief plunger
14. Oil filter bracket
15. Oil filter bracket gasket
BK16. Plug
17. O-ringCJ18. Flange bolt
H19. Front case
20. Front case gasket
21. Oil pump cover
G22. Oil pump driven gear
G23. Oil pump drive gear
F24. Crankshaft oil seal
E25. Oil pump oil seal
D26. Counterbalance shaft oil seal
27. Counterbalance shaft left
28. Counterbalance shaft right
DC29. Counterbalance shaft front bearing
EB30. Counterbalance shaft rear bearing
left
EA31. Counterbalance shaft rear bearing
right
Page 77 of 558
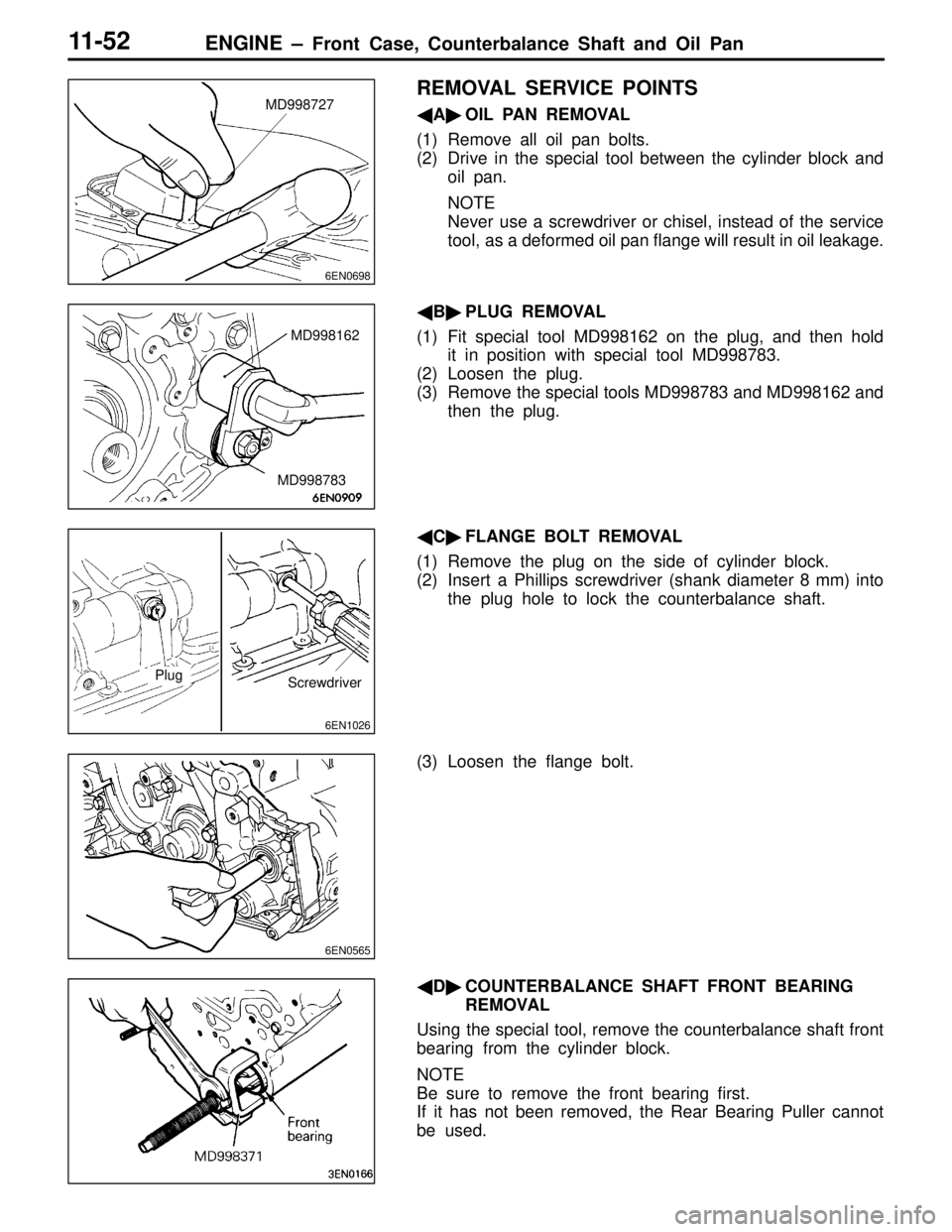
ENGINE – Front Case, Counterbalance Shaft and Oil Pan11-52
REMOVAL SERVICE POINTS
AOIL PAN REMOVAL
(1) Remove all oil pan bolts.
(2) Drive in the special tool between the cylinder block and
oil pan.
NOTE
Never use a screwdriver or chisel, instead of the service
tool, as a deformed oil pan flange will result in oil leakage.
BPLUG REMOVAL
(1) Fit special tool MD998162 on the plug, and then hold
it in position with special tool MD998783.
(2) Loosen the plug.
(3) Remove the special tools MD998783 and MD998162 and
then the plug.
CFLANGE BOLT REMOVAL
(1) Remove the plug on the side of cylinder block.
(2) Insert a Phillips screwdriver (shank diameter 8 mm) into
the plug hole to lock the counterbalance shaft.
(3) Loosen the flange bolt.
DCOUNTERBALANCE SHAFT FRONT BEARING
REMOVAL
Using the special tool, remove the counterbalance shaft front
bearing from the cylinder block.
NOTE
Be sure to remove the front bearing first.
If it has not been removed, the Rear Bearing Puller cannot
be used.
6EN0698
MD998727
MD998162
MD998783
6EN1026
Plug
Screwdriver
6EN0565
Page 78 of 558
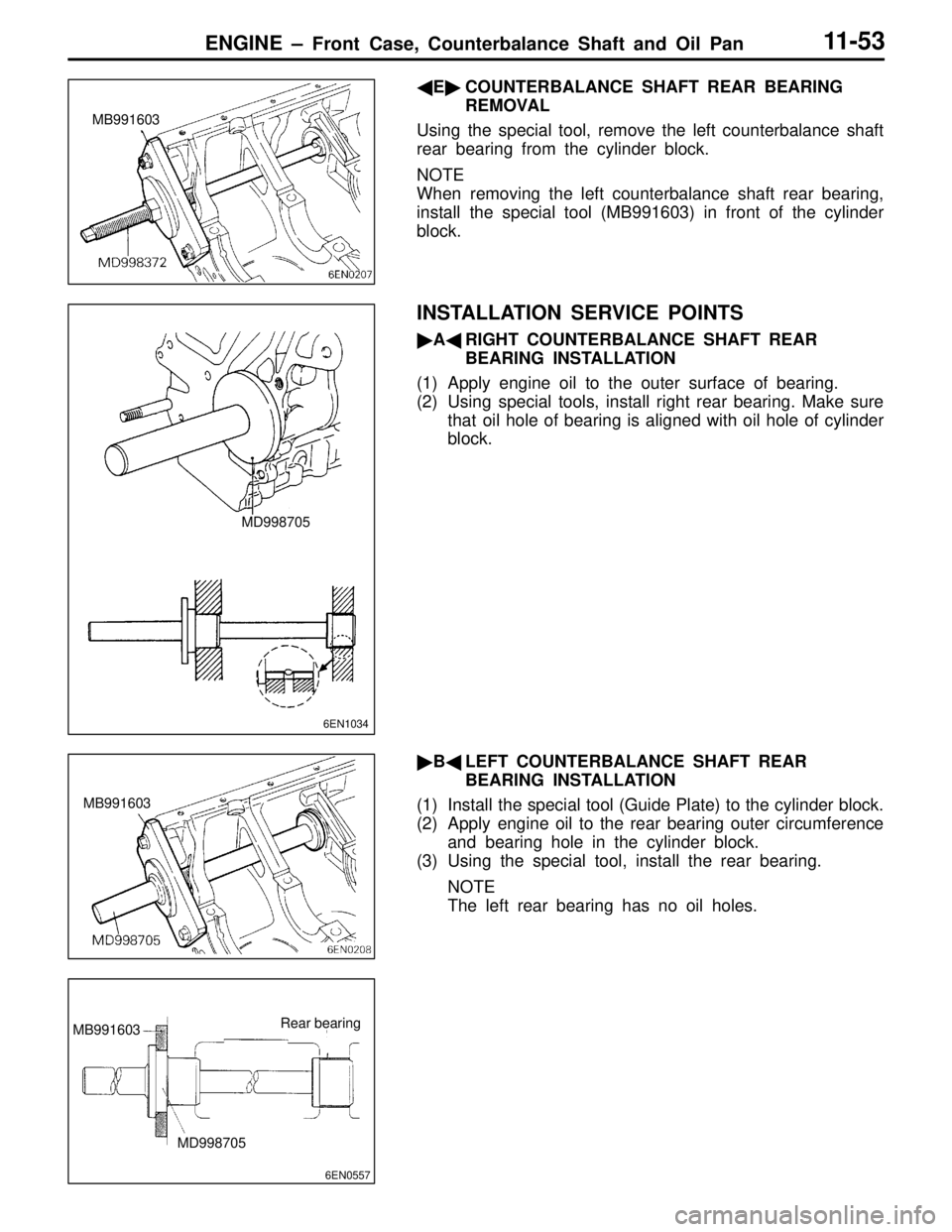
ENGINE – Front Case, Counterbalance Shaft and Oil Pan11-53
ECOUNTERBALANCE SHAFT REAR BEARING
REMOVAL
Using the special tool, remove the left counterbalance shaft
rear bearing from the cylinder block.
NOTE
When removing the left counterbalance shaft rear bearing,
install the special tool (MB991603) in front of the cylinder
block.
INSTALLATION SERVICE POINTS
ARIGHT COUNTERBALANCE SHAFT REAR
BEARING INSTALLATION
(1) Apply engine oil to the outer surface of bearing.
(2) Using special tools, install right rear bearing. Make sure
that oil hole of bearing is aligned with oil hole of cylinder
block.
BLEFT COUNTERBALANCE SHAFT REAR
BEARING INSTALLATION
(1) Install the special tool (Guide Plate) to the cylinder block.
(2) Apply engine oil to the rear bearing outer circumference
and bearing hole in the cylinder block.
(3) Using the special tool, install the rear bearing.
NOTE
The left rear bearing has no oil holes.
MB991603
6EN1034
MD998705
MB991603
6EN0557
MB991603Rear bearing
MD998705
Page 79 of 558
ENGINE – Front Case, Counterbalance Shaft and Oil Pan11-54
CCOUNTERBALANCE SHAFT FRONT BEARING
INSTALLATION
Using special tools, install front bearing.
DCOUNTERBALANCE SHAFT OIL SEAL
INSTALLATION
Using a suitable socket wrench, install the counterbalance
shaft oil seal into the front case.
EOIL PUMP OIL SEAL INSTALLATION
Using a suitable socket wrench, install the oil pump oil seal
into the front case.
FCRANKSHAFT FRONT OIL SEAL INSTALLATION
Using the special tool, install the crankshaft front oil seal
into the front case.
6EN1035
MD998705
MD998705
Bearing
Cylinder block
Page 80 of 558
ENGINE – Front Case, Counterbalance Shaft and Oil Pan11-55
GOIL PUMP DRIVEN GEAR / OIL PUMP DRIVE
GEAR INSTALLATION
Apply engine oil amply to the gears and line up the alignment
marks.
HFRONT CASE ASSEMBLY INSTALLATION
(1) Set the special tool on the front end of crankshaft and
apply a thin coat of engine oil to the outer circumference
of the special tool to install the front case.
(2) Install the front case assembly through a new front case
gasket and temporarily tighten the flange bolts (other
than those for tightening the filter bracket).
ISEALANT APPLICATION TO OIL PRESSURE
SWITCH
Coat the threads of switch with sealant and install the switch
using the special tool.
Specified sealant: 3M
TM AAD Part No. 8672 or equivalent
Caution
(1) Keep the end of the thread portion clear or sealant.
(2) Avoid an overtightening.
JFLANGE BOLT INSTALLATION
(1) Insert a Phillips screwdriver into a hole in the left side
of the cylinder block to lock the silent shaft.
6EN0564