Page 439 of 1216
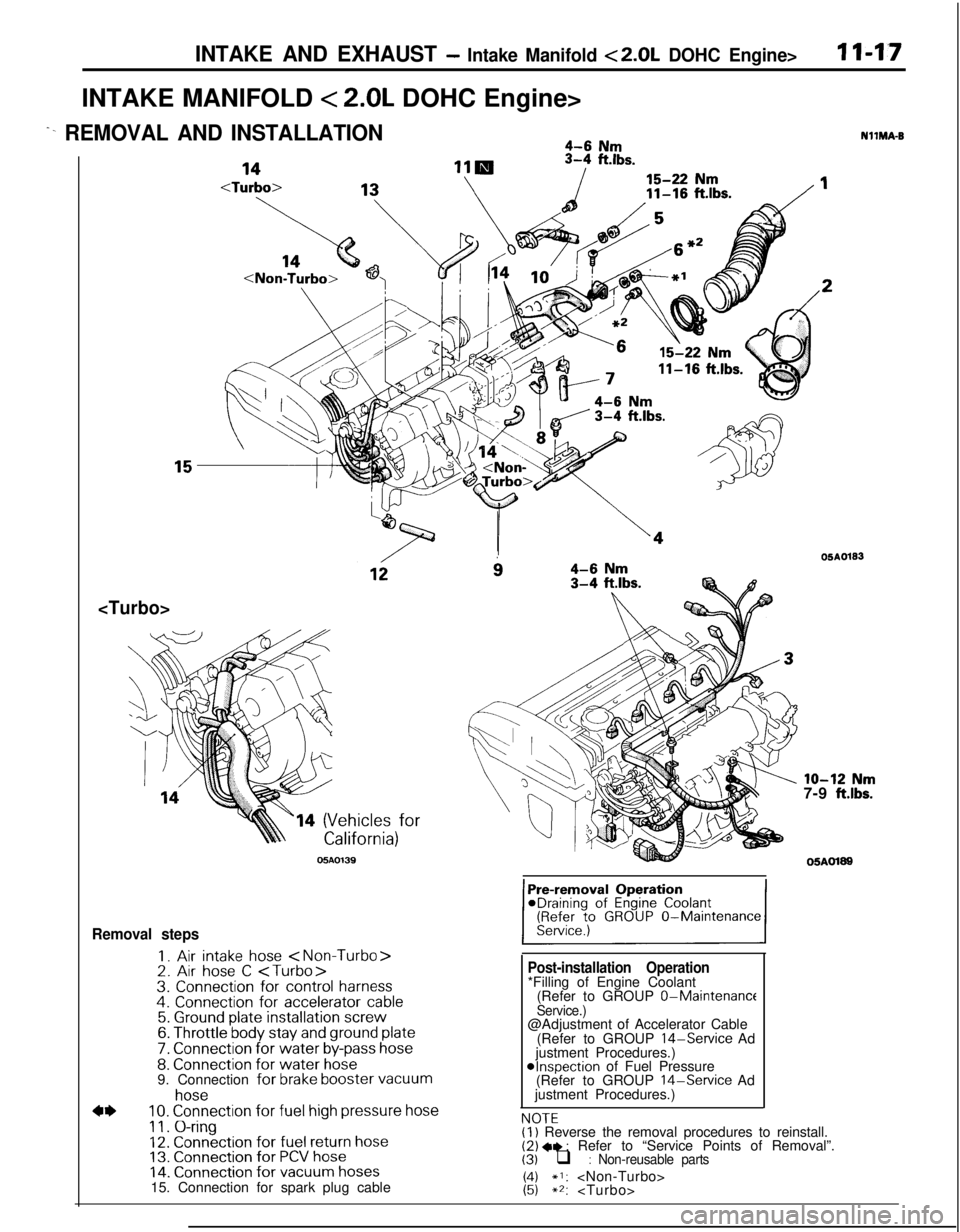
INTAKE AND EXHAUST - Intake Manifold <2.0L DOHC Engine>I I-1.7INTAKE MANIFOLD
< 2.0L DOHC Engine>
^- REMOVAL AND INSTALLATION4-6 Nm
11-16
ft.lbs.
14 (Vehicles for
05AO139
i34-6 Nm3-4 ftlbs.
Removal steps
I. Air intake hose 2. Air hose C 3. Connection for control harness4. Connection for accelerator cable5. Ground plate installation screw6. Throttle body stay and ground plate
7. Connection for water by-pass hose8. Connection for water hose9. Connection for brake booster vacuum
4*
hose10. Connection for fuel high pressure hose
11. O-ring12. Connection for fuel return hose13. Connection for PCV hose14. Connection for vacuum hoses15. Connection for spark plug cable
Post-installation Operation*Filling of Engine Coolant
(Refer to GROUP 0-Maintenance
Service.)@Adjustment of Accelerator Cable
(Refer to GROUP
14-Service Ad
justment Procedures.)
@Inspection of Fuel Pressure
(Refer to GROUP 14-Service Ad
justment Procedures.)
NOTFNllMA-B
OSAO133
lo-12 Nm7-9 ft.lbs.
05AOl89
,.-.-(I) Reverse the removal procedures to reinstall.(2) +e : Refer to “Service Points of Removal”.(3) q : Non-reusable parts
1:;*I: **:
Page 440 of 1216
11-18INTAKE AND EXHAUST - Intake Manifold < 2.0L DOHC Engine>
10-27 Nm14-20 ft.lbs.
18hIO-13 Nm
7-9
ft.lbs.15-22 Nm11-16
ft.lbs.IO-12 Nm
7-9
ftlbs.05A0197
15-22 Nm
11-16
ftlbs.
wi2” vlo-12 Nm
7-9 ftlbs.25-30 Nm
18-22
ft.lbs.
24
\‘27
28lll
Removal steps
+e l + 16. Delivery pipe, fuel injector and pressureregulator17. Insulator18. Insulator19. Intake manifold stay
20. Intake manifold21. Intake manifold gasket22. Ignition coil23. Power transistor unit24. EGR valve25. Gasket26. EGR temperature sensor 27. Air fitting 28. Gasket 05A0196
29. Connection for control harness
30. Throttle body31. Gasket
NOTE(I) Reverse the removal procedures to reinstall.(2) l * : Refer to “Service Points of Removal”.(3) l + : Refer to “Service Points of Installation”.(4) 0 : Non-reusable parts
Page 441 of 1216
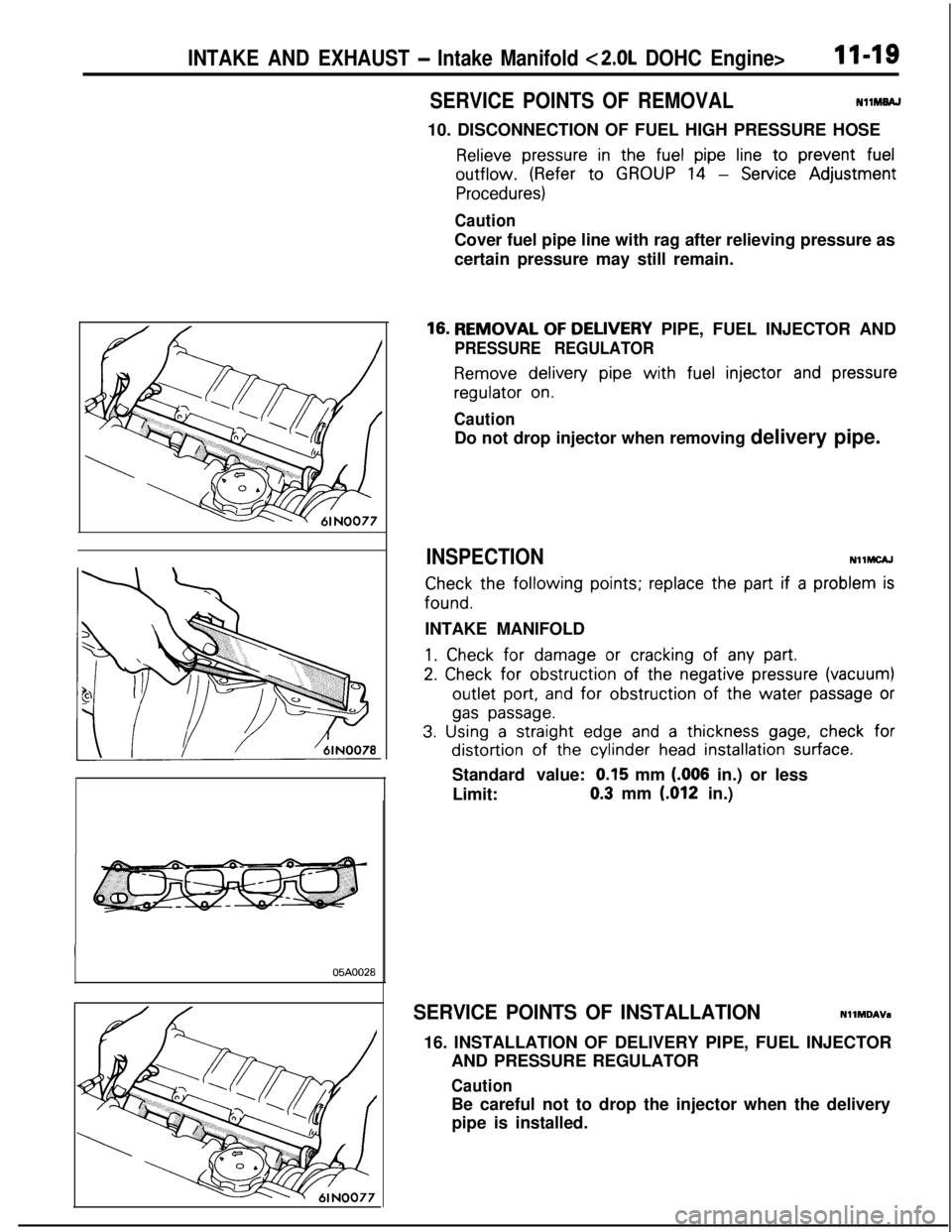
INTAKE AND EXHAUST - Intake Manifold <2.0L DOHC Engine>11-19
SERVICE POINTS OF REMOVALNllMBAJ
10. DISCONNECTION OF FUEL HIGH PRESSURE HOSE
Relieve pressure in the fuel pipe line to prevent fueloutflow.
(Refer to GROUP 14 - Service Adjustment
Procedures)
CautionCover fuel pipe line with rag after relieving pressure as
certain pressure may still remain.
05AOO28
16. REMOVAL OF DELIVERY PIPE, FUEL INJECTOR AND
PRESSURE REGULATOR
Remove delivery pipe with fuel injector and pressureregulator
on.
CautionDo not drop injector when removing delivery pipe.
INSPECTIONNllMCAJ
Check the following points; replace the part if a problem isfound.
INTAKE MANIFOLD
1. Check for damage or cracking of any part.
2. Check for obstruction of the negative pressure (vacuum)outlet
port, and for obstruction of the water passage or
gas passage.
3. Using a straight edge and a thickness gage, check fordistortion of the cylinder
head installation surface.Standard value:
0.15 mm (.006 in.) or less
Limit:0.3 mm
(012 in.)
SERVICE POINTS OF INSTALLATIONNllMDAVa
16. INSTALLATION OF DELIVERY PIPE, FUEL INJECTOR
AND PRESSURE REGULATOR
CautionBe careful not to drop the injector when the delivery
pipe is installed.
Page 442 of 1216
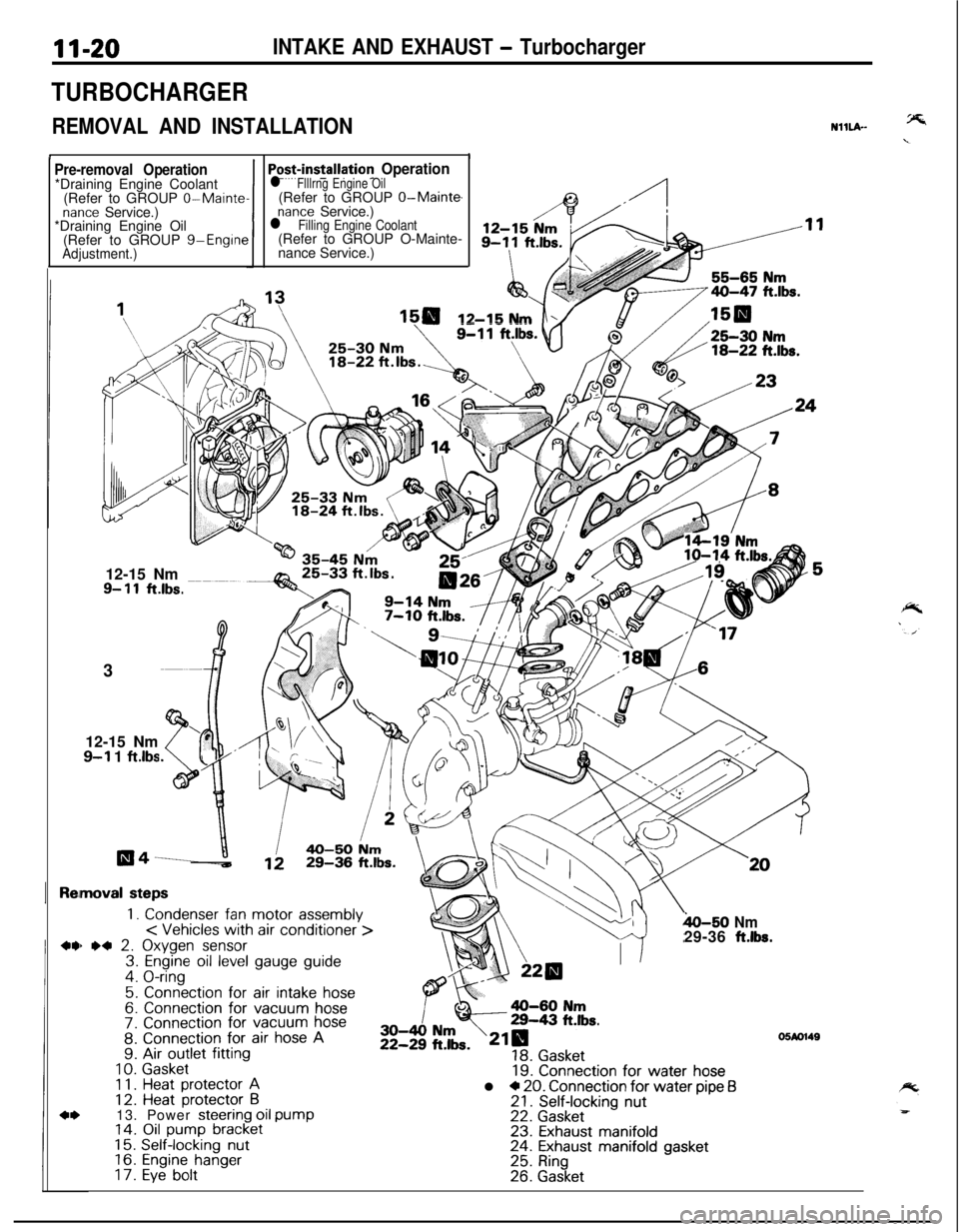
II-20INTAKE AND EXHAUST - Turbocharger
TURBOCHARGER
REMOVAL AND INSTALLATION
II
NHLA-
Pre-removal Operation*Draining Engine Coolant
(Refer to GROUP
0-Maintenance Service.)
*Draining Engine Oil
(Refer to GROUP g-Engine
Adjustment.)1
Po+installation Operationl Flllrng Engine Oil(Refer to GROUP O-Main@
nance Service.)l Filling Engine Coolant(Refer to GROUP O-Mainte-
nance Service.)
12-15 Nm12-15 Nm
9- 11ft.lbs.3
12-15 Nm
9-l 1 ftlbs
moval steps
1. Condenser fan motor assembly< Vehicles with air conditioner >) *4 2. Oxygen sensor3. Engine oil level gauge guide4. O-ring
5. Connection for air intake hose6. Connection for vacuum hose7. Connection for vacuum hose8. Connection for air hose A9. Air outlet fitting
10.Gasket1 1.Heat protector A12. Heat protector B13. Power steering oil pump14. Oil pump bracket15.Self-locking nut16.Engine hanger17.Eye bolt
h-50 Nm29-36 ft.lbs.
19. Connection for water hosel * 20. Connection for water pipe f321. Self-locking nut22. Gasket23. Exhaust manifold24. Exhaust manifold gasket25. Ring26. Gasket
05M1149
Page 443 of 1216
INTAKE AND EXHAUST - Turbocharger11-21
35-50 Nm25-Qg
ft-lbs*26-34 Nm
20-25 ftlbs.
\/3655-65 Nm
4o-4: ft*lbs-
35-50 Nm25-36 ftlbs.
05A0136
NOTE(1) Reverse the removal procedures to reinstall.(2) l * : Refer to “Service Points of Removal”.(3) l + : Refer to “Service Points of Installation”.(4) q : Non-reusable parts
27. Oil return pipe28.
Gasketl * l a 29. Turbocharger30. Eye bolt
31. Gasket
32. Water pipe B33. Eye bolt
34. Gasket35. Water pipe A36. Eye bolt37. Gasketw l c 38. Oil pipe39. Exhaust fitting40. GasketMD998748
1SERVICE POINTS OF REMOVALNllL9AD
2. REMOVAL OF OXYGEN SENSORDisconnect the
connector of the oxygen sensor, and install
the special tool to the oxygen sensor.
Then, using an offset (box-end) wrench, remove the oxygen
sensor.
Page 444 of 1216
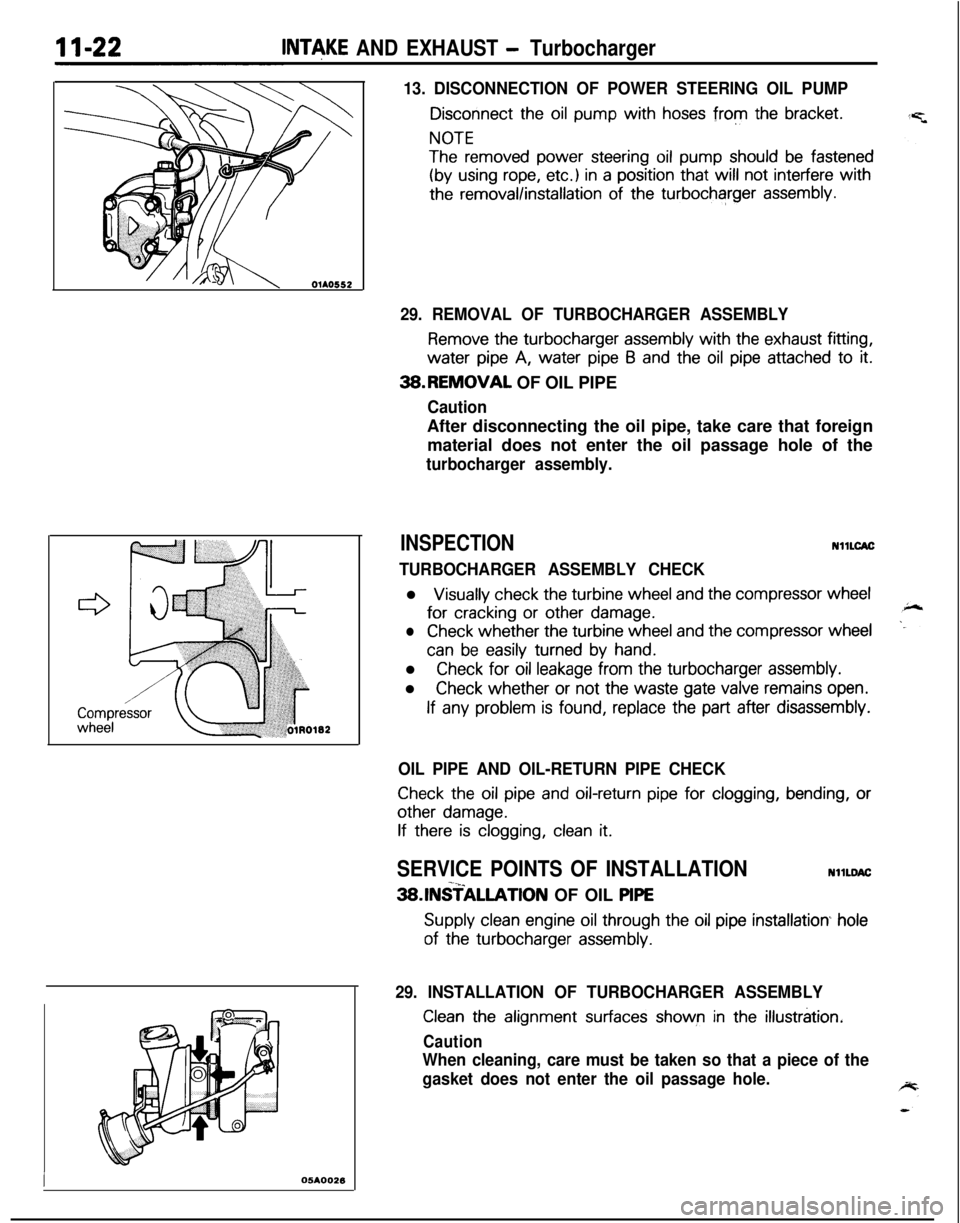
INTeKE AND EXHAUST - Turbocharger
13. DISCONNECTION OF POWER STEERING OIL PUMP
Disconnect the oil pump with hoses from the bracket.
NOTE
The removed power steering oil pump should be fastened
(by using rope, etc.) in a position that will not interfere with
the removal/installation of the turbocharger assembly.
I05AOO26
29. REMOVAL OF TURBOCHARGER ASSEMBLY
Remove the turbocharger assembly with the exhaust fitting,water
pipe A, water pipe 6 and the oil pipe attached to it.3B.REMOVAL OF OIL PIPE
CautionAfter disconnecting the oil pipe, take care that foreign
material does not enter the oil passage hole of the
turbocharger assembly.
INSPECTIONNllLCAC
TURBOCHARGER ASSEMBLY CHECKl
Visually check the turbine wheel and the compressor wheelfor
cracking or other damage.
lCheck whether the turbine wheel and the compressor wheel
can be easily turned by hand.l
Check for oil leakage from the turbocharger assembly.l
Check whether or not the waste gate valve remains open.
If any problem is found, replace the part after disassembly.
OIL PIPE AND OIL-RETURN PIPE CHECK
Check the oil pipe and oil-return pipe for clogging, bending, or
other damage.
If there is clogging, clean it.
SERVICE POINTS OF INSTALLATIONNllLDAC-x_3SlNSTALLATlON OF OIL PlPE
Supply clean engine oil through the oil pipe installation hole
of the turbocharger assembly.
29. INSTALLATION OF TURBOCHARGER ASSEMBLY
Clean the alignment surfaces shown in the illustration.
Caution
When cleaning, care must be taken so that a piece of the
gasket does not enter the oil passage hole.
Page 445 of 1216
INTAKE AND EXHAUST - TurbochargerII-23
05K557
’ MD998748
05A0023
DISASSEMBLY AND REASSEMBLY20.lNSTALLATlON OF WATER PIPE
(B)
Before installing to the water inlet pipe, apply machine oil to
the inner surface of the pipe flare.2. INSTALLATION OF OXYGEN SENSOR
Use the special tool to install the oxygen sensor.NllLE-.
lo-13 Nm7-9 Mbs.
Disassembly steps
1. Snap pin2. Waste gate actuator
3. Couplingl 4. Turbine housingl *l C 5. Snap ring+e *a 6. Cartridge assemblyl * 7. O-ring8. Compressor cover
NOTE(I) Reverse the disassembly procedures to reassemble.(2) 4~ : Refer to “Service Points of Disassembly”.
(3) ++ : Refer to “Service Points of Reassembly”.
(4) q : Non-reusable parts6 1 NO084
Page 446 of 1216
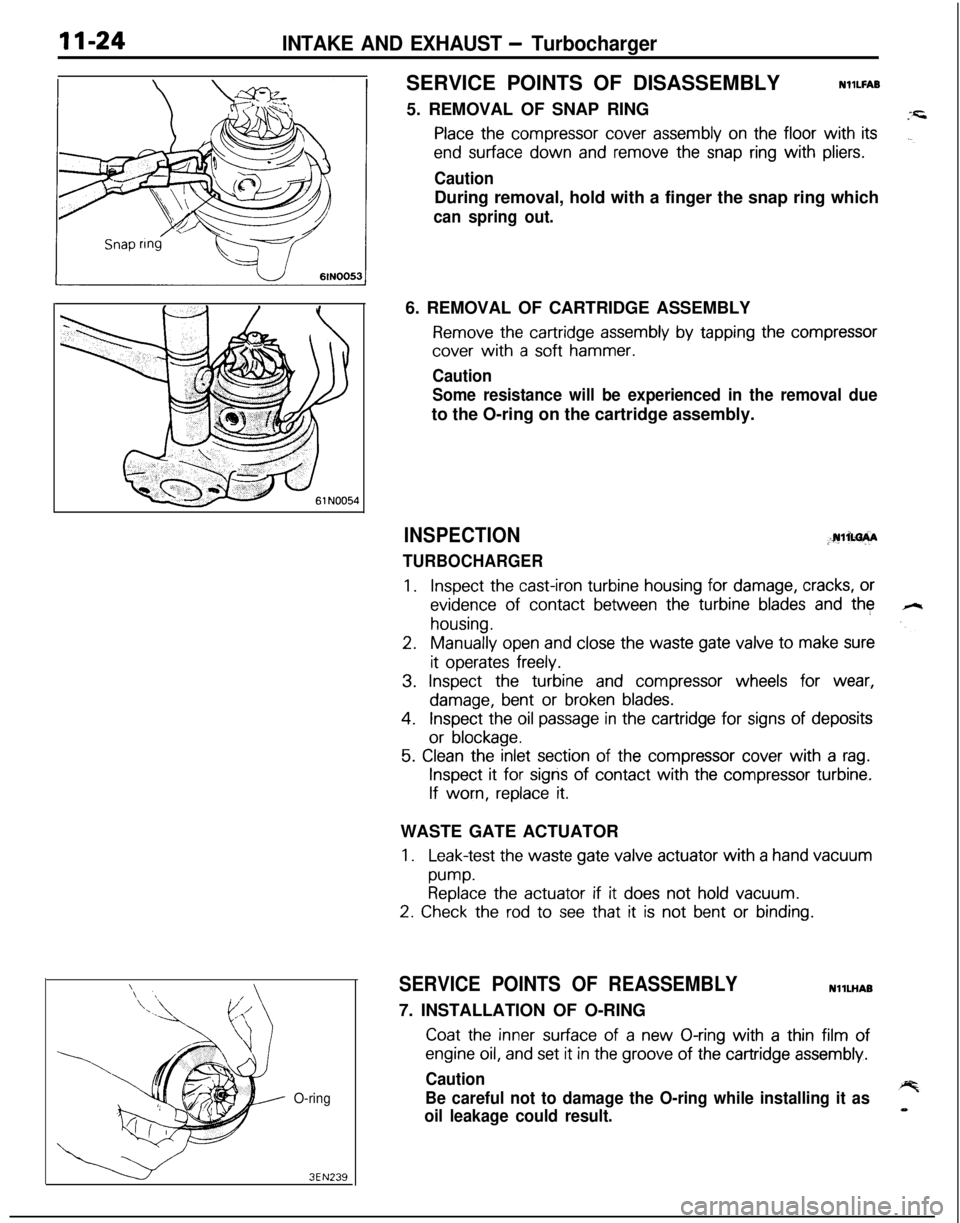
II-24INTAKE AND EXHAUST - TurbochargerSERVICE POINTS OF DISASSEMBLYNllLFAB
5. REMOVAL OF SNAP RING
Place the compressor cover assembly on the floor with its
end surface down and remove the snap ring with pliers.
CautionDuring removal, hold with a finger the snap ring which
can spring out.
O-ring
3EN2396. REMOVAL OF CARTRIDGE ASSEMBLY
Remove the cartridge assembly by tapping the compressor
cover with a soft hammer.
Caution
Some resistance will be experienced in the removal dueto the O-ring on the cartridge assembly.
INSPECTION;.rulim+A
TURBOCHARGER
1.Inspect the cast-iron turbine housing for damage, cracks, or
evidence of contact between the turbine blades and the
housing.
2.Manually open and close the waste gate valve to make sure
it operates freely.
3. Inspect the turbine and compressor wheels for wear,
damage, bent or broken blades.
4.Inspect the oil passage in the cartridge for signs of deposits
or blockage.
5. Clean the inlet section of the compressor cover with a rag.
Inspect it for signs of contact with the compressor turbine.
If worn, replace it.WASTE GATE ACTUATOR
1.Leak-test the waste gate valve actuator with a hand vacuum
pump.Replace the actuator if it does not hold vacuum.
2. Check the rod to see that it is not bent or binding.
SERVICE POINTS OF REASSEMBLYNllLHAB
7. INSTALLATION OF O-RING
Coat the inner surface of a new O-ring with a thin film of
engine oil, and set it in the groove of the cartridge assembly.
Caution
Be careful not to damage the O-ring while installing it as
oil leakage could result.