Page 428 of 1216
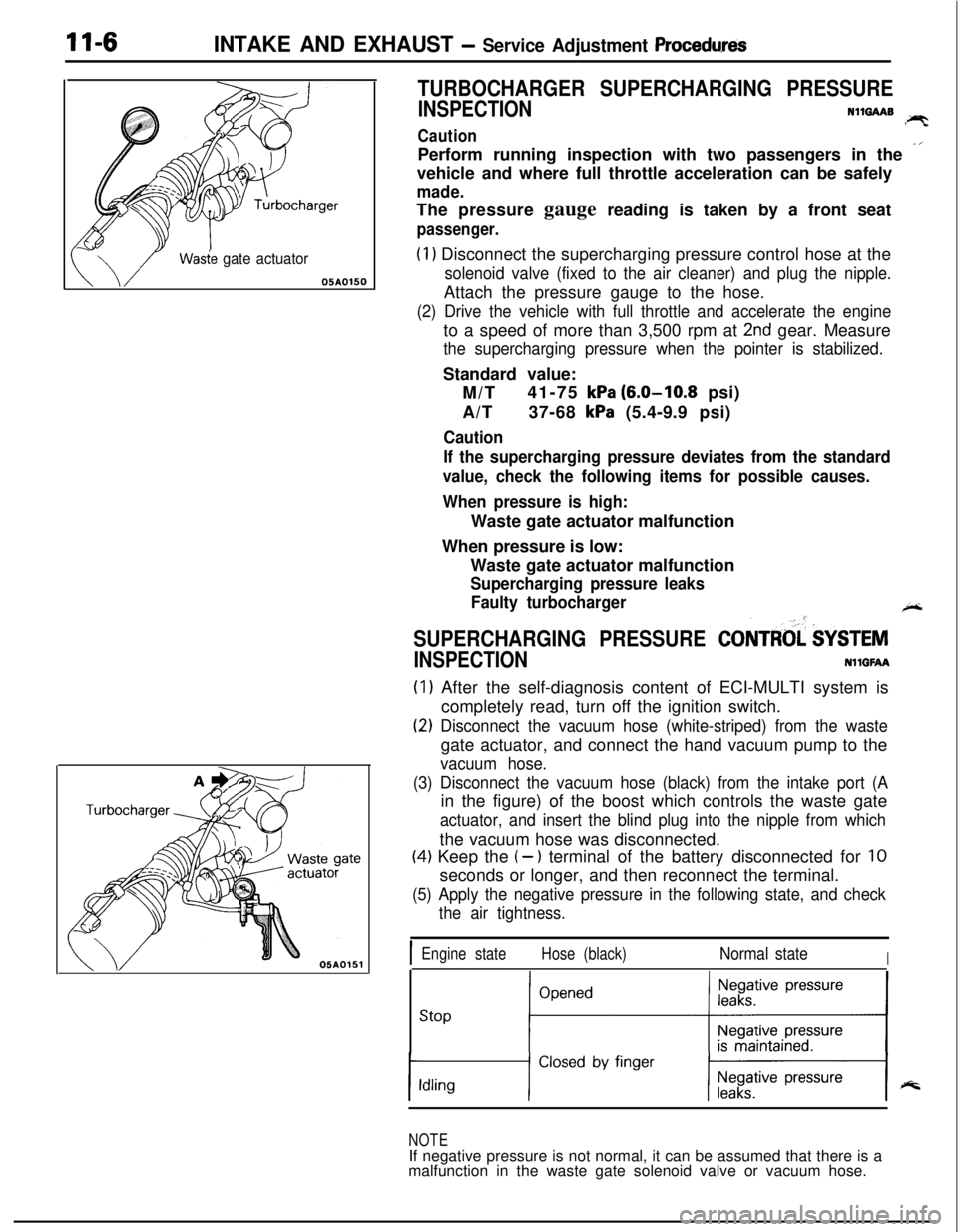
11-6INTAKE AND EXHAUST - Service Adjustment Procedwes
Wasie gate actuator05AOlSO
TURBOCHARGER SUPERCHARGING PRESSURE
INSPECTIONN1mAAB!PTCautionPerform running inspection with two passengers in the
-’vehicle and where full throttle acceleration can be safely
made.The pressure gauge reading is taken by a front seat
passenger.
(1) Disconnect the supercharging pressure control hose at the
solenoid valve (fixed to the air cleaner) and plug the nipple.Attach the pressure gauge to the hose.
(2) Drive the vehicle with full throttle and accelerate the engineto a speed of more than 3,500 rpm at
2nd gear. Measure
the supercharging pressure when the pointer is stabilized.Standard value:
M/T41-75
kPa (6.0-10.8 psi)
A/T37-68
kPa (5.4-9.9 psi)
Caution
If the supercharging pressure deviates from the standard
value, check the following items for possible causes.
When pressure is high:Waste gate actuator malfunction
When pressure is low:
Waste gate actuator malfunction
Supercharging pressure leaks
Faulty turbocharger
+-
SUPERCHARGING PRESSURE CONTRtd $YSTEM
INSPECTIONNllGFAA
(1) After the self-diagnosis content of ECI-MULTI system is
completely read, turn off the ignition switch.
(2) Disconnect the vacuum hose (white-striped) from the wastegate actuator, and connect the hand vacuum pump to the
vacuum hose.
(3) Disconnect the vacuum hose (black) from the intake port (Ain the figure) of the boost which controls the waste gate
actuator, and insert the blind plug into the nipple from whichthe vacuum hose was disconnected.
(4) Keep the (- ) terminal of the battery disconnected for 10seconds or longer, and then reconnect the terminal.
(5) Apply the negative pressure in the following state, and check
the air tightness.
IEngine stateHose (black)Normal stateI
stop ;“““*I
NOTEIf negative pressure is not normal, it can be assumed that there is a
malfunction in the waste gate solenoid valve or vacuum hose.
Page 429 of 1216
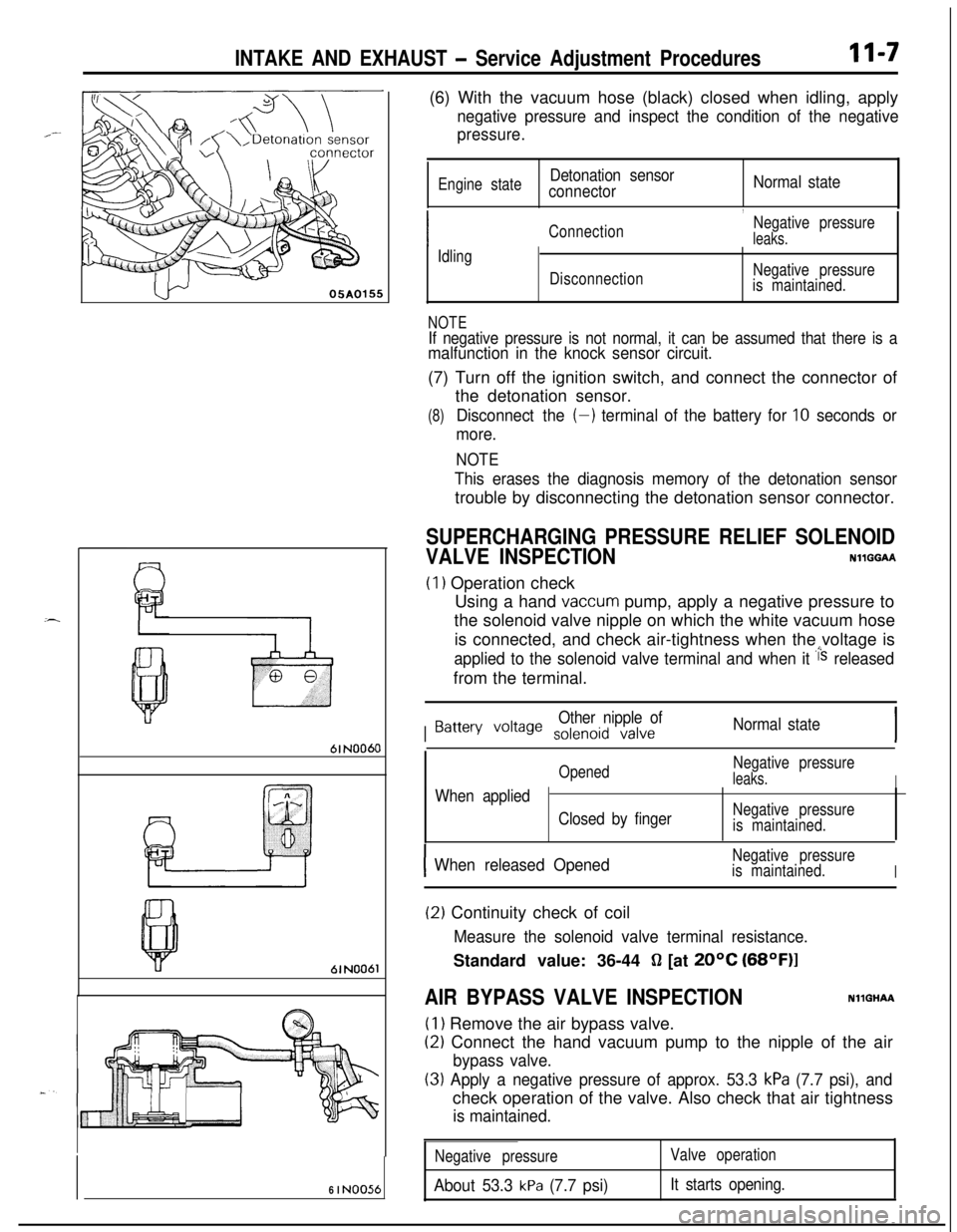
INTAKE AND EXHAUST - Service Adjustment ProceduresII-7
w05A0155
h61
NO06061
NO0616 I
NO056(6) With the vacuum hose (black) closed when idling, apply
negative pressure and inspect the condition of the negative
pressure.
Engine stateDetonation sensor
connectorNormal state
,
ConnectionNegative pressureleaks.
Idling
DisconnectionNegative pressure
is maintained.
NOTEIf negative pressure is not normal, it can be assumed that there is amalfunction in the knock sensor circuit.(7) Turn off the ignition switch, and connect the connector of
the detonation sensor.
(8)Disconnect the (-) terminal of the battery for 10 seconds or
more.
NOTE
This erases the diagnosis memory of the detonation sensortrouble by disconnecting the detonation sensor connector.
SUPERCHARGING PRESSURE RELIEF SOLENOID
VALVE INSPECTIONNllGGAA
(1) Operation check
Using a hand
vaccum pump, apply a negative pressure to
the solenoid valve nipple on which the white vacuum hose
is connected, and check air-tightness when the voltage is
applied to the solenoid valve terminal and when it i‘s releasedfrom the terminal.
I
Other nipple ofBattery voile solenoid valveNormal state
OpenedNegative pressureleaks.IWhen applied
Closed by fingerNegative pressure
is maintained.
IWhen released OpenedNegative pressure
is maintained.
I
(2) Continuity check of coil
Measure the solenoid valve terminal resistance.Standard value: 36-44
fl [at 20°C (68OF)l
AIR BYPASS VALVE INSPECTIONNllGHAA
(1) Remove the air bypass valve.
(2) Connect the hand vacuum pump to the nipple of the air
bypass valve.
(3) Apply a negative pressure of approx. 53.3 kPa (7.7 psi), andcheck operation of the valve. Also check that air tightness
is maintained.
Negative pressure
About 53.3 kPa (7.7 psi)
Valve operation
It starts opening.
Page 433 of 1216
INTAKE AND EXHAUST - Intercooler11-11
INTERCOOLER
A-- REMOVAL AND INSTALLATIONNllTA-.
615-22
Nm11-16 ft.lbs.
Removal steps
1. Air hose C
2. Air pipe B3. Air by-pass hose4.Vacuumhose
5.Vacuumhose
l *6. Air cleaner7. Air intake hose8. Air hose B
9. Splash shield extensionl + 10. Intercooler11. Air hose A12. Air by-pass valve13.Gasket
i
05AOl85
05A0140
NOTE(1) Reverse the removal procedures to reinstall.(2) l * : Refer to “Service Points of Removal”.(3) *+ : Refer to “Service Points of Installation”(4) q : Non-reusable parts
Page 434 of 1216
11-12INTAKE AND EXHAUST - Intercooler
05AO184
SERVICE POINTS OF REMOVAL6. REMOVAL OF AIR CLEANER
Refer to P.l l-9.
INSPECTIONNllTCAA
l
Check the intercooler fins for bending, damage, or foreign
matter.0
Check the intercooler hoses for cracking, damage, or wear.
SERVICE POINTS OF INSTALLATIONNllTDAB
10. INSTALLATION OF
INTERCObLER
Connect the air hoses and air pipes by aligning the paint
marks on the hoses with the projections and indentations on?
the pipes.
Caution
Be careful not to allow any foreign matter to get into thehoses, pipes, or the
intercooler itself.
NOTE
@ : Projection or indentation (pipe)
+ : Paint mark (hose)
Page 435 of 1216
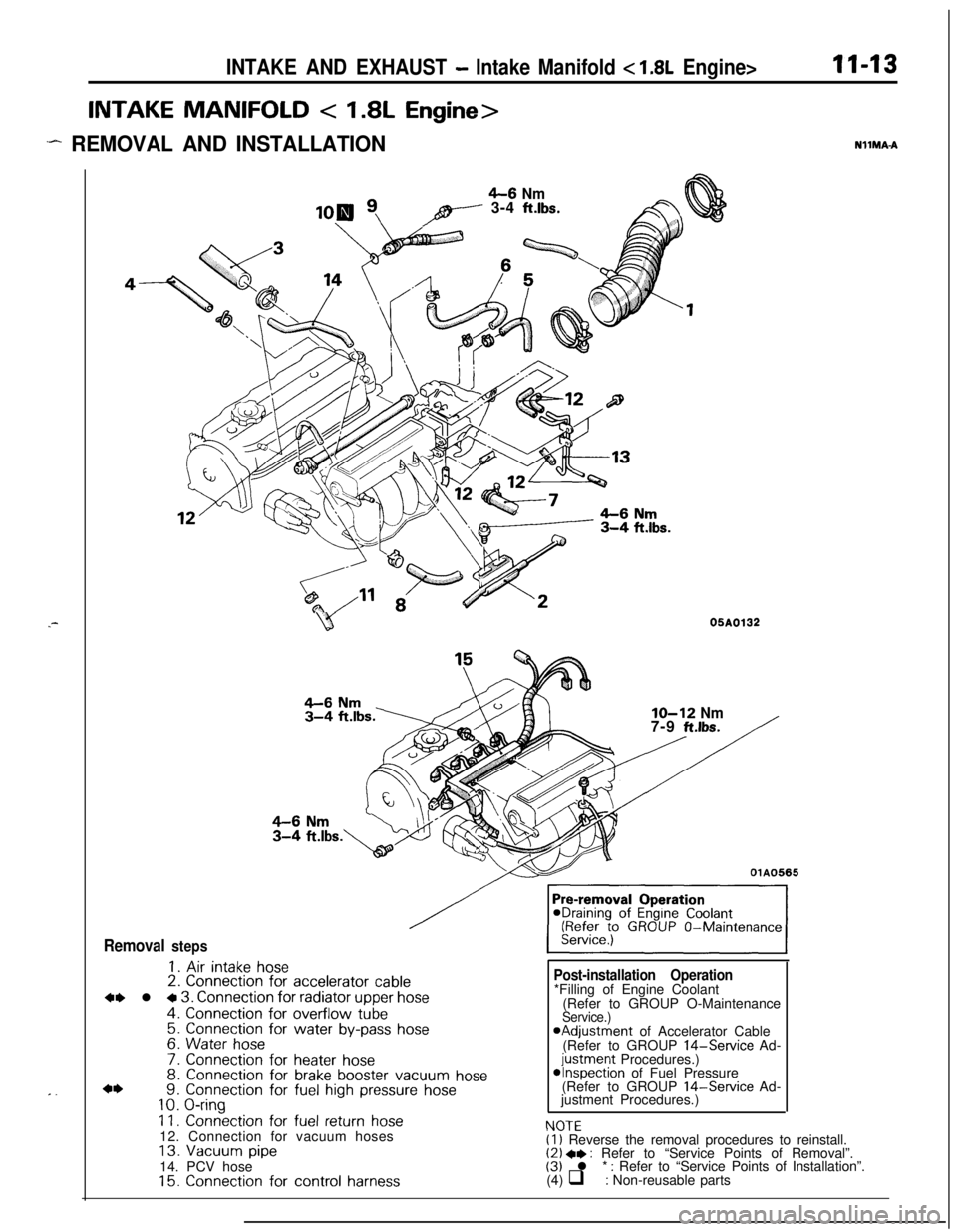
INTAKE AND EXHAUST - Intake Manifold < 1.8L Engine>
INTAKE MANIFOLD < 1.8L Engine>
.- REMOVAL AND INSTALLATION
11-13NllMA-A.-
. .
4-6 Nmpy---- 3-4 ft.lbs.
B05A0132
Removal steps
1. Air intake hose2. Connection for accelerator cable
4, l + 3. Connection for radiator upper hose
4. Connection for overflow tube5. Connection for water by-pass hose6. Water hose
7. Connection for heater hose8. Connection for brake booster vacuum hose9. Connection for fuel high pressure hose10. O-ring
11. Connection for fuel return hose12. Connection for vacuum hoses
13. Vacuum pipe14. PCV hose
15. Connection for control harness
IO-12 Nm7-9 ft.lbs.
OlA0565
Post-installation Operation
NfJTF*Filling of Engine Coolant
(Refer to GROUP O-Maintenance
Service.)aAdjustment of Accelerator Cable
(Refer to GROUP 14-Service Ad-
justment Procedures.)*Inspection of Fuel Pressure
(Refer to GROUP 14-Service Ad-
justment Procedures.)
I.” IL(1) Reverse the removal procedures to reinstall.(2) +* : Refer to “Service Points of Removal”.(3) l * : Refer to “Service Points of Installation”.
(4) q : Non-reusable parts
Page 436 of 1216
II-14INTAKE AND EXHAUST -Intake Manifold < 1.8L Engine>
/15-20 Nm
11-14
ft.lbs.
lo-13 Nm
18167-9 ft.lbs.15-20 Nm11-14
ft.lbs.I/15-20 Nm
I26IO-15 Nm7-11
ftm’bs.
-17-20 Nm
12-14 ft.lbs.15-20 Nm
Removal steps05AO180
+* l a 16. Delivery pipe, fuel injector and pressureregulator17.Insulator
18.Insulator19. Intake manifold stay20.Engine hanger
2 1.Thermostat housing22.Intake manifold23. Intake manifold gasket24. Throttle body assembly25.Gasket26. Air intake plenum stay
27. Air intake plenum
28. Air intake plenum gasket
lb+ 29. Cover 30. Gasket 31. EGR valve 32. EGR gasket
33. EGR temperature sensor 34. Water outlet fitting35. Gasket36. Thermostat
NOTE(1) Reverse the removal procedures to reinstall.
(2) a* : Refer to “Service Points of Removal”.
(3) l * : Refer to “Service Points of Installation”
(4) q : Non-reusable parts
Page 437 of 1216
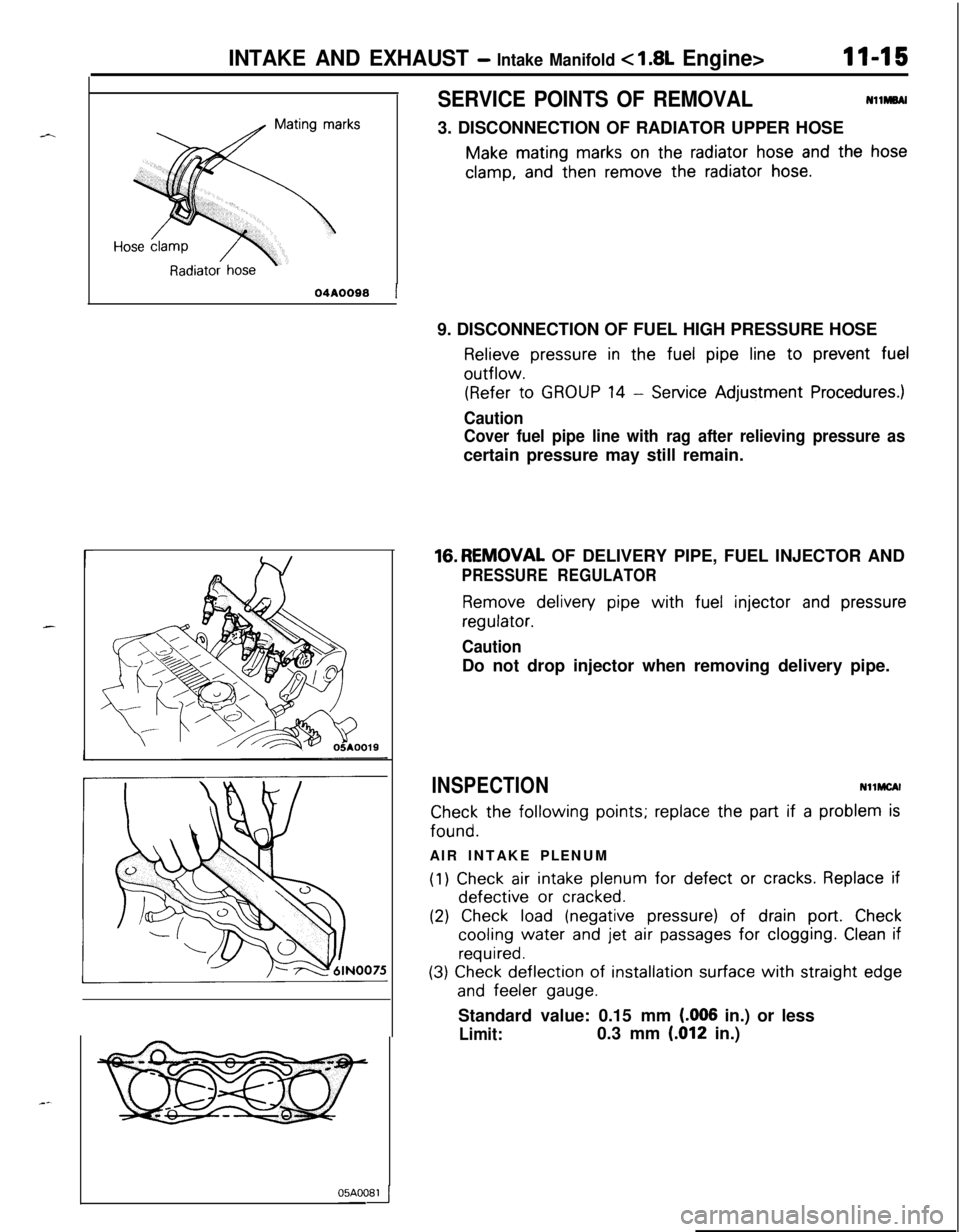
INTAKE AND EXHAUST - Intake Manifold < 1.8L Engine>1145
SERVICE POINTS OF REMOVALNllMBAI
3. DISCONNECTION OF RADIATOR UPPER HOSE
Make mating marks on the radiator hose and the hose
clamp, and then remove the radiator hose.
r
04A0088 19. DISCONNECTION OF FUEL HIGH PRESSURE HOSE
Relieve pressure in the fuel pipe line to prevent fueloutflow.
(Refer to GROUP 14 - Service Adjustment Procedures.)
Caution
Cover fuel pipe line with rag after relieving pressure ascertain pressure may still remain.16.REMOVAL OF DELIVERY PIPE, FUEL INJECTOR AND
PRESSURE REGULATOR
Remove delivery pipe with fuel injector and pressure
regulator.
CautionDo not drop injector when removing delivery pipe.
INSPECTIONNllMCAl
Check the following points; replace the part if a problem isfound.
AIR INTAKE PLENUM
(1) Check air intake plenum for defect or cracks. Replace ifdefective
or cracked.
(2) Check load (negative pressure) of drain port. Check
cooling water and jet air passages for clogging. Clean if
required.
(3) Check deflection of installation surface with straight edge
and feeler gauge.Standard value: 0.15 mm
(.006 in.) or less
Limit:0.3 mm (.012 in.)05AOOB4
Page 438 of 1216
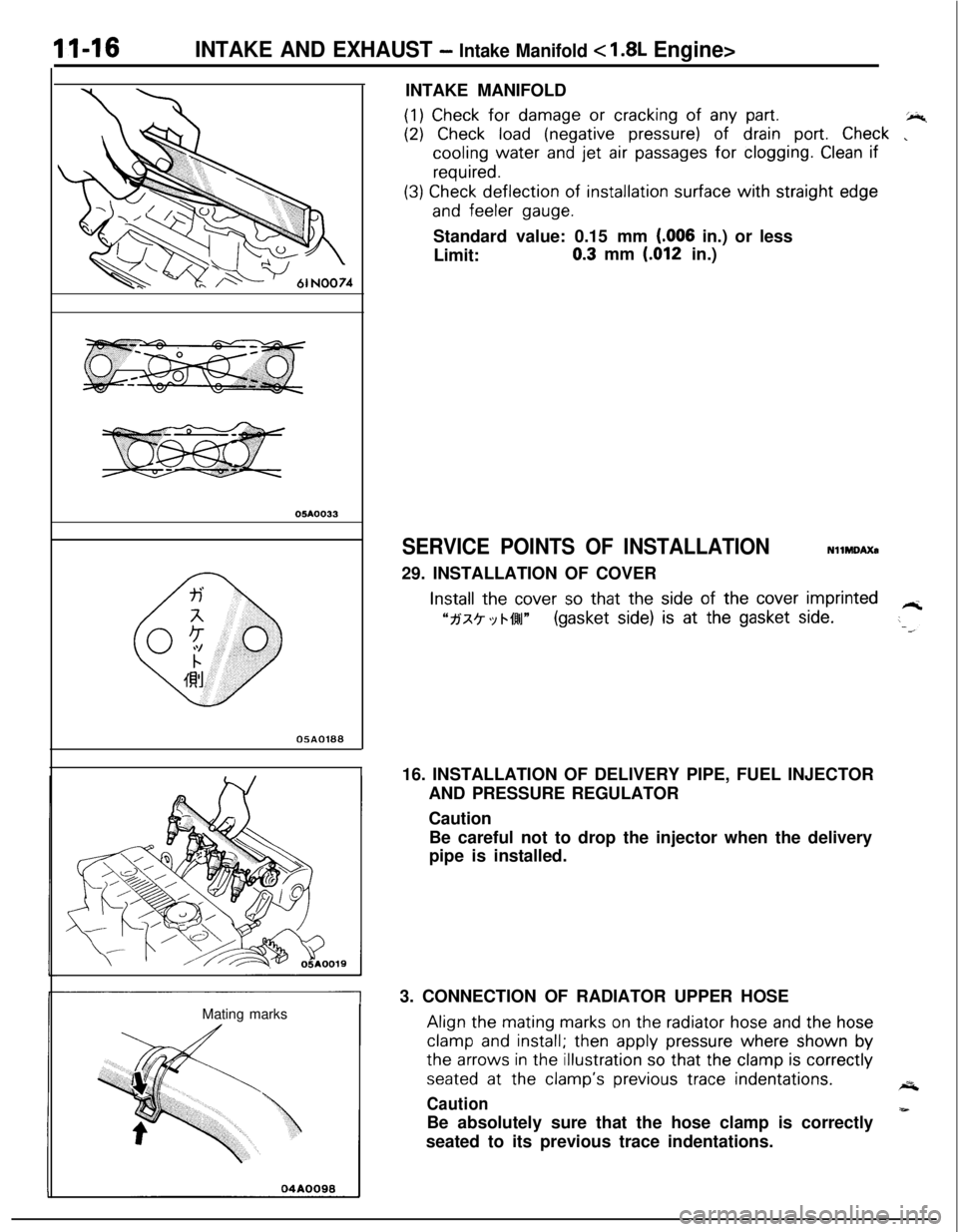
II-16INTAKE AND EXHAUST - Intake Manifold c 1.8L Engine>
05A0033
0580188Mating marksINTAKE MANIFOLD
(1) Check for damage or cracking of any part.+4
(2) Check load (negative pressure) of drain port. Check ,cooling water
and jet air passages for clogging. Clean if
required.
(3) Check deflection of installation surface with straight edge
and feeler gauge.Standard value: 0.15 mm
(006 in.) or less
Limit:
0.3 mm (.012 in.)
SERVICE POINTS OF INSTALLATIONNllMDAXa
29. INSTALLATION OF COVER
Install the cover so that the side of the cover imprinted
“fj‘x? ‘Y bf4l~(gasket side) is at the gasket side.-T16. INSTALLATION OF DELIVERY PIPE, FUEL INJECTOR
AND PRESSURE REGULATOR
Caution
Be careful not to drop the injector when the delivery
pipe is installed.
3. CONNECTION OF RADIATOR UPPER HOSEAlign the
mating marks on the radiator hose and the hose
clamp and install; then apply pressure where shown bythe
arrows in the illustration so that the clamp is correctly
seated at the clamp’s previous trace indentations.A
Caution
-Be absolutely sure that the hose clamp is correctly
seated to its previous trace indentations.