Page 257 of 273
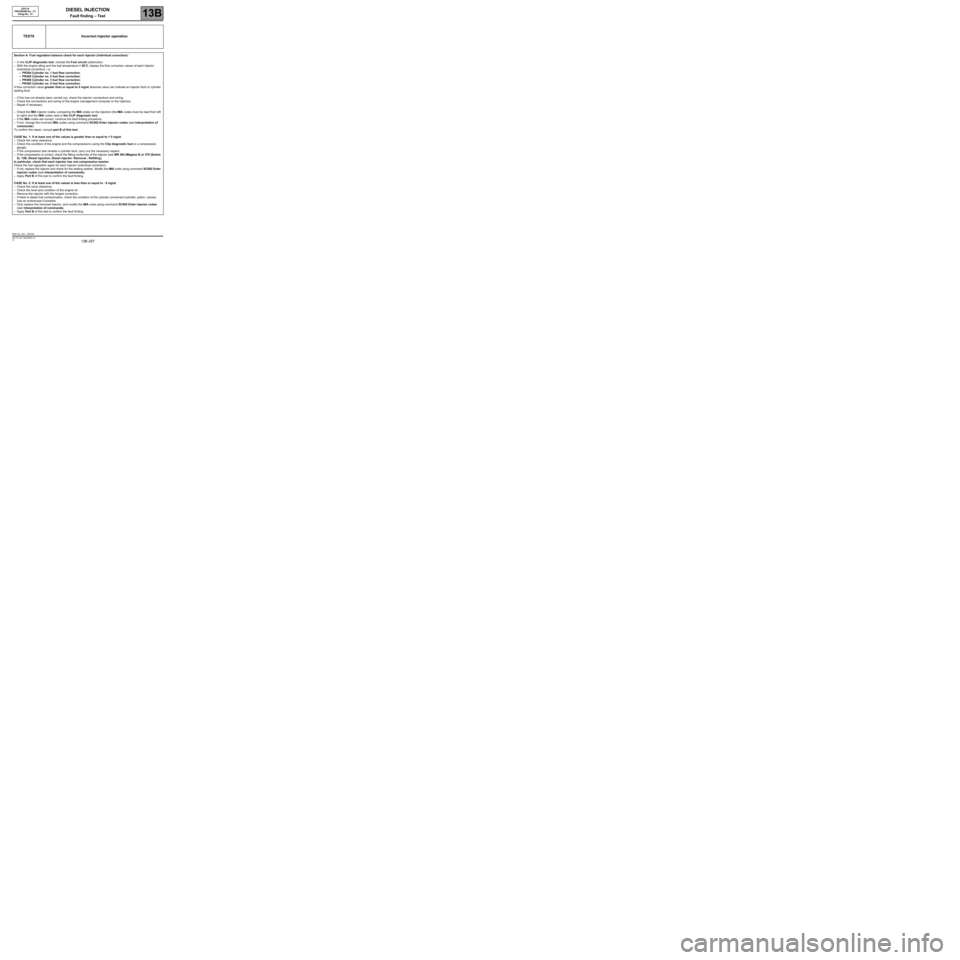
DIESEL INJECTION
Fault finding – Test13B
13B -257V3 MR-372-J84-13B250$900.mif
EDC16
PROGRAM No.: C1
Vdiag No.: 51
TEST8 Incorrect injector operation
Section A: Fuel regulation balance check for each injector (individual correction):
–In the CLIP diagnostic tool, choose the Fuel circuit subfunction.
–With the engine idling and the fuel temperature > 50˚C, display the flow correction values of each injector
(individual correction), i.e.:
–PR364 Cylinder no. 1 fuel flow correction.
–PR405 Cylinder no. 2 fuel flow correction.
–PR406 Cylinder no. 3 fuel flow correction.
–PR365 Cylinder no. 4 fuel flow correction.
A flow correction value greater than or equal to 5 mg/st absolute value can indicate an injector fault or cylinder
sealing fault.
–If this has not already been carried out, check the injector connections and wiring.
–Check the connections and wiring of the engine management computer to the injectors.
–Repair if necessary.
–Check the IMA injector codes, comparing the IMA codes on the injectors (the IMA codes must be read from left
to right) and the IMA codes read in the CLIP diagnostic tool.
–If the IMA codes are correct, continue the fault finding procedure,
–If not, change the incorrect IMA codes using command SC002 Enter injector codes (see Interpretation of
commands).
To confirm the repair, consult part B of this test.
CASE No. 1: If at least one of the values is greater than or equal to + 5 mg/st
–Check the valve clearance.
–Check the condition of the engine and the compressions (using the Clip diagnostic tool or a compression
gauge).
–If the compression test reveals a cylinder fault, carry out the necessary repairs.
–If the compression is correct, check the fitting conformity of the injector (see MR 364 (Mégane II) or 370 (Scénic
II), 13B, Diesel injection, Diesel injector: Removal - Refitting)
In particular, check that each injector has one compression washer.
Check the fuel regulation again for each injector (individual correction).
–If not, replace the injector and check for the sealing washer. Modify the IMA code using command SC002 Enter
injector codes (see Interpretation of commands).
–Apply Part B of this test to confirm the fault finding.
CASE No. 2: If at least one of the values is less than or equal to - 5 mg/st
–Check the valve clearance.
–Check the level and condition of the engine oil.
–Remove the injector with the largest correction.
–If there is diesel fuel contamination, check the condition of the cylinder concerned (cylinder, piston, valves).
Use an endoscope if possible.
–Only replace the removed injector, and modify the IMA code using command SC002 Enter injector codes
(see Interpretation of commands).
–Apply Part B of this test to confirm the fault finding.
EDC16_V51_TEST8
Page 258 of 273
DIESEL INJECTION
Fault finding – Test13B
13B -258V3 MR-372-J84-13B250$900.mif
EDC16
PROGRAM No.: C1
Vdiag No.: 51
TEST8
CONTINUED 1
CASE No. 3: If at least one of these values does not stabilise (20 seconds after starting)
–Check the low pressure circuit with test 2 Low pressure circuit check.
–Check the conformity of the fuel used, apply test 10 Diesel fuel conformity check.
–Apply Part B of this test to confirm the fault finding procedure
CASE No. 4: If the fuel flow correction values are all correct (between - 5 mg/st and + 5 mg/st)
Apply Part C of this test (Fuel return flow measurement).
Page 259 of 273
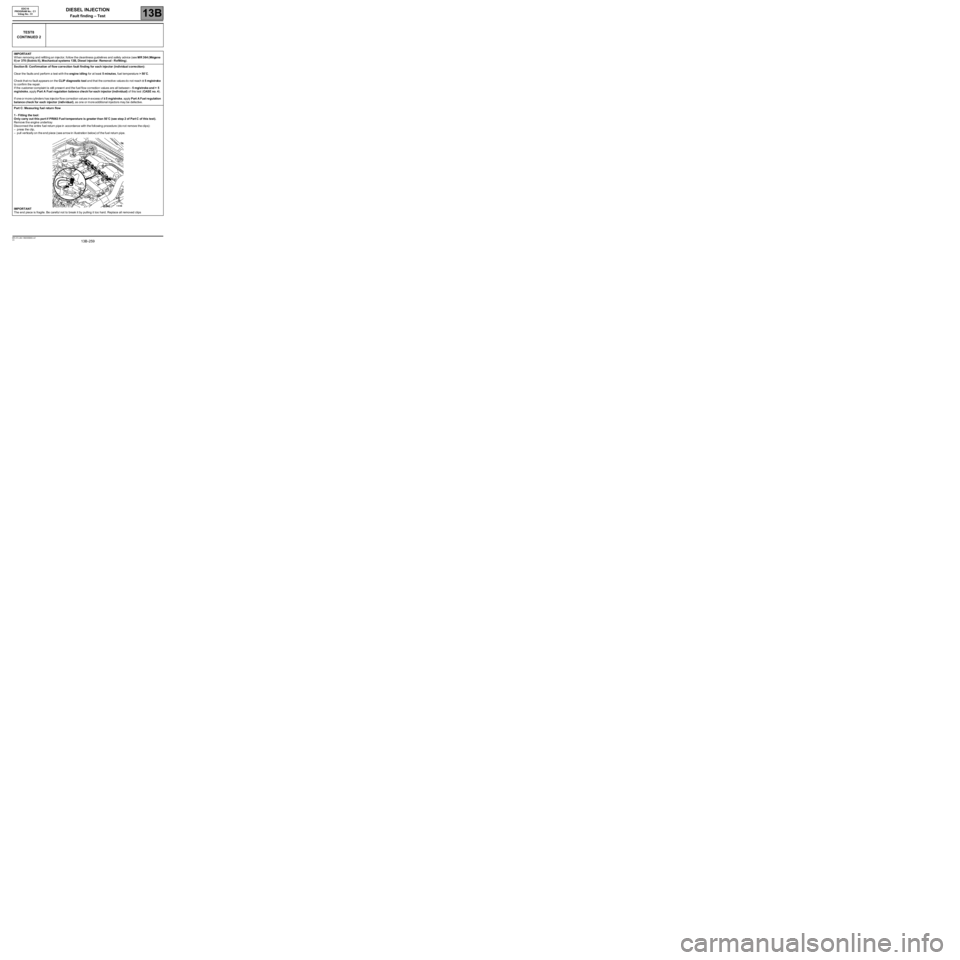
DIESEL INJECTION
Fault finding – Test13B
13B -259V3 MR-372-J84-13B250$900.mif
TEST8
CONTINUED 2
IMPORTA NT
When removing and refitting an injector, follow the cleanliness guidelines and safety advice (seeMR 364 (Mégane
II) or 370 (Scénic II), Mechanical systems 13B, Diesel injector: Removal - R efitting).
Section B: Conf irmation of flow corre ction fault finding for each inje ctor (individua l c orre ction):
Cle ar the faultsandperform a test wi th theengine idlingfor at l east5minutes,fueltemperature>50˚C.
Ch eck th at n o fault a p p e a r s o n t heCLIPdiagnostic tooland that the corrective values do not reach±5mg/stroke
to confirm therepair.
Ifthecustomer complaint is still present and the fuel flow correction values are all between-5mg/stroke a nd + 5
mg/strok e,applyPartAFuel regulation balanc e che ck f or each injector (individual)of this test (CAS Eno. 4).
If one or more cylinders has injector flow correction values in excess of±5 mg/stroke,applyPart AFuel re gulation
ba lance c heck for each inj e c t or(individu a l ),asoneormoreadditional injectors may be defective.
Part C: Measuring fuelreturnflow
1-Fitting the tool:
Only carryout this pa rt if PR063 Fuel t empera ture is greater t han 50˚C (see step 2 of Part C of this test).
Remove the engine undertray
Disco nnect the entire fuel return pipe in accordance with the foll owing procedure (do not remove the clips):
–pressthe clip ,
–pullvertically on the end piece ( see arrow in i llustration below) of the fuel return pipe.
IMPORTANT
The end piece is fragile. Be careful not to break it by pulling it too hard. Replace all removed clips
EDC16
PROGRAM No.: C1
Vdiag No.: 51
Page 260 of 273
DIESEL INJECTION
Fault finding – Test13B
13B -260V3 MR-372-J84-13B250$900.mif
EDC16
PROGRAM No.: C1
Vdiag No.: 51
TEST8
CONTINUED 3
Fit the blanking plugs (B), from the kit (part number 77 01 208 229), on the end pieces of the fuel return pipe.
If Mot. 1760 is not fitted on the injectors immediately, place blanking plugs (A) on the injector fuel return openings.
On the pipes of Mot.1760 (see illustration 113195 above), remove the clips and the plugs from the end pieces (on
the right in the diagram) and leave the plugs (on the left in the diagram) in place.
Page 261 of 273
DIESEL INJECTION
Fault finding – Test13B
13B -261V3 MR-372-J84-13B250$900.mif
EDC16
PROGRAM No.: C1
Vdiag No.: 51
TEST8
CONTINUED 4
Connect the pipes from the Mot.1760 tool to the injectors (without removing the clips on the injectors):
–press on the injector clip,
–insert the end piece into the injector fuel return opening.
–remember to fit the end piece plugs to the injector fuel return openings with the clips provided.
–Remove the plugs left on the Mot.1760
Insert the ends of the pipes into the measuring cylinders of tool Mot.1760. The measuring cylinders are taken from
tool Mot. 1711.
Page 262 of 273
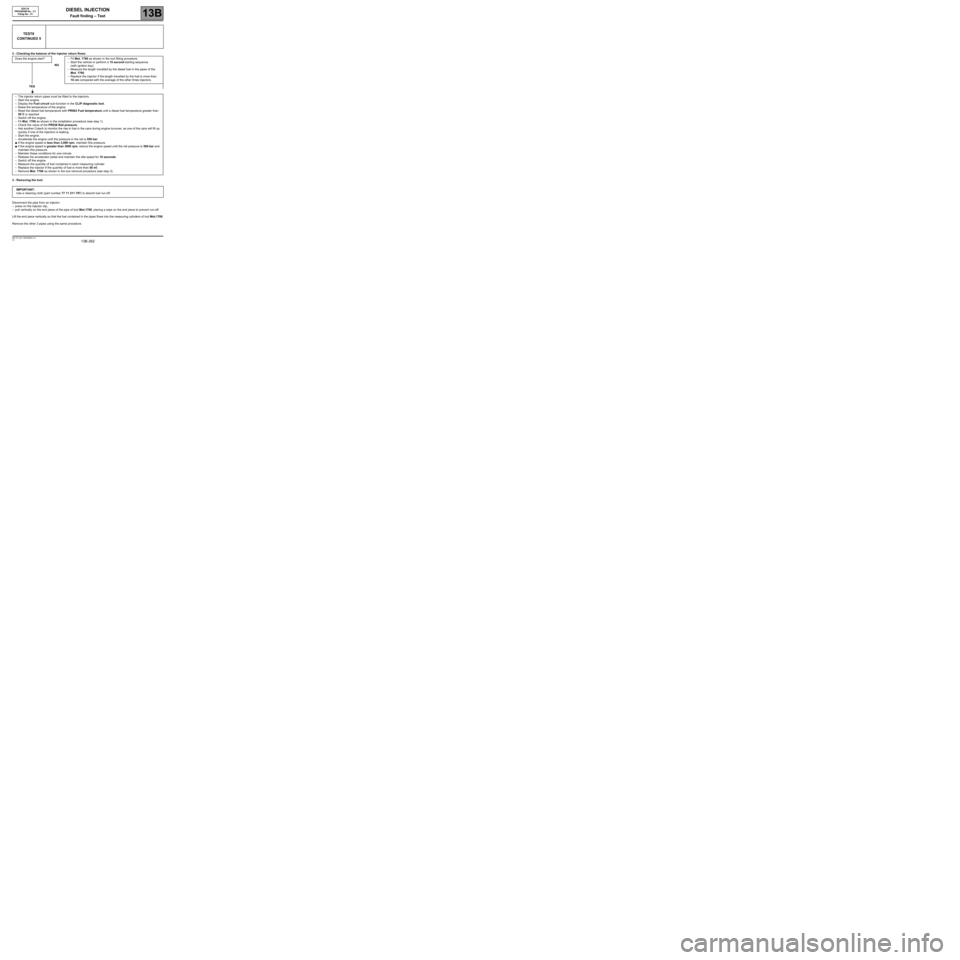
DIESEL INJECTION
Fault finding – Test13B
13B -262V3 MR-372-J84-13B250$900.mif
EDC16
PROGRAM No.: C1
Vdiag No.: 51
2 - Checking the balance of the injector return flows:
3 - Removing the tool:
Disconnect the pipe from an injector:
–press on the injector clip,
–pull vertically on the end piece of the pipe of tool Mot.1760, placing a wipe on the end piece to prevent run-off.
Lift the end piece vertically so that the fuel contained in the pipes flows into the measuring cylinders of tool Mot.1760.
Remove the other 3 pipes using the same procedure.
TEST8
CONTINUED 5
Does the engine start? – Fit Mot. 1760 as shown in the tool fitting procedure.
–Start the vehicle or perform a 15 second starting sequence
(with ignition key).
–Measure the length travelled by the diesel fuel in the pipes of the
Mot. 1760.
–Replace the injector if the length travelled by the fuel is more than
10 cm compared with the average of the other three injectors. NO
YES
–The injector return pipes must be fitted to the injectors.
–Start the engine.
–Display the Fuel circuit sub-function in the CLIP diagnostic tool.
–Raise the temperature of the engine.
–Read the diesel fuel temperature with PR063 Fuel temperature until a diesel fuel temperature greater than
50˚C is reached
–Switch off the engine.
–Fit Mot. 1760 as shown in the installation procedure (see step 1).
–Check the value of the PR038 Rail pressure.
–Ask another Cotech to monitor the rise in fuel in the cans during engine turnover, as one of the cans will fill up
quickly if one of the injectors is leaking.
–Start the engine.
–Accelerate the engine until the pressure in the rail is 550 bar:
●if the engine speed is less than 3,000 rpm, maintain this pressure.
●if the engine speed is greater than 3000 rpm, reduce the engine speed until the rail pressure is 500 bar and
maintain this pressure.
–Maintain these conditions for one minute.
–Release the accelerator pedal and maintain the idle speed for 10 seconds.
–Switch off the engine.
–Measure the quantity of fuel contained in each measuring cylinder.
–Replace the injector if the quantity of fuel is more than 50 ml.
–Remove Mot. 1760 as shown in the tool removal procedure (see step 3).
IMPORTANT:
Use a cleaning cloth (part number 77 11 211 707) to absorb fuel run-off.
Page 263 of 273
DIESEL INJECTION
Fault finding – Test13B
13B -263V3 MR-372-J84-13B250$900.mif
EDC16
PROGRAM No.: C1
Vdiag No.: 51
TEST8
CONTINUED 6
Remove the plug welds from the fuel return pipe end pieces.
Connect the complete fuel return pipe to the injectors.
Wipe up any fuel run-off with a cleaning cloth (part number 77 11 211 707).
End of test8.
Page 264 of 273
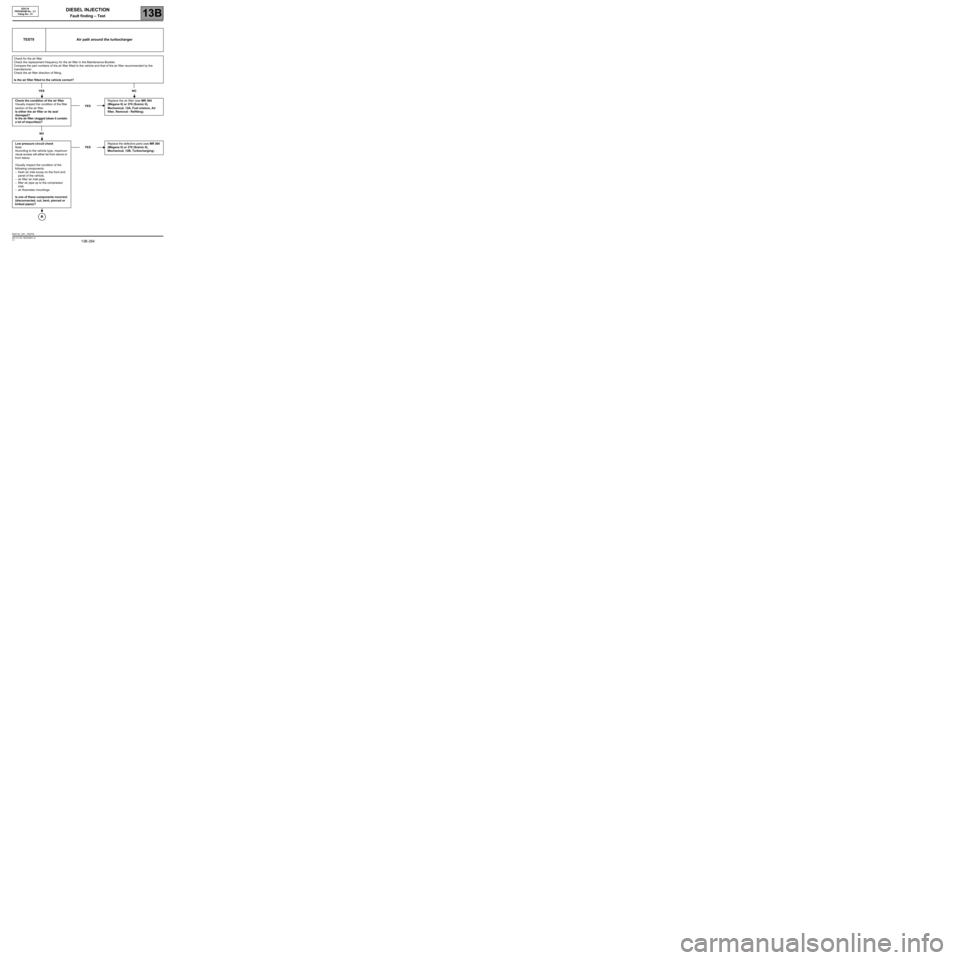
DIESEL INJECTION
Fault finding – Test13B
13B -264V3 MR-372-J84-13B250$900.mif
TEST9 Air path around the turbocharger
Check for the air filter
Check the replacement frequency for the air filter in the Maintenance Booklet.
Compare the part numbers of the air filter fitted to the vehicle and that of the air filter recommended by the
manufacturer.
Check the air filter direction of fitting.
Is the air filter fitted to the vehicle correct?
YES NO
Check the condition of the air filter
Visually inspect the condition of the filter
section of the air filter.
Is either the air filter or its seal
damaged?
Is the air filter clogged (does it contain
a lot of impurities)?YESReplace the air filter (see MR 364
(Mégane II) or 370 (Scénic II),
Mechanical, 12A, Fuel mixture, Air
filter, Removal - Refitting).
NO
Low pressure circuit check
Note:
According to the vehicle type, maximum
visual access will either be from above or
from below.
Visually inspect the condition of the
following components:
–fresh air inlet scoop on the front end
panel of the vehicle,
–air filter air inlet pipe,
–filter air pipe up to the compressor
inlet,
–air flowmeter mountings.
Is one of these components incorrect
(disconnected, cut, bent, pierced or
kinked pipes)?YESReplace the defective parts (see MR 364
(Mégane II) or 370 (Scénic II),
Mechanical, 12B, Turbocharging).
EDC16
PROGRAM No.: C1
Vdiag No.: 51
EDC16_V51_TEST9