Page 217 of 273
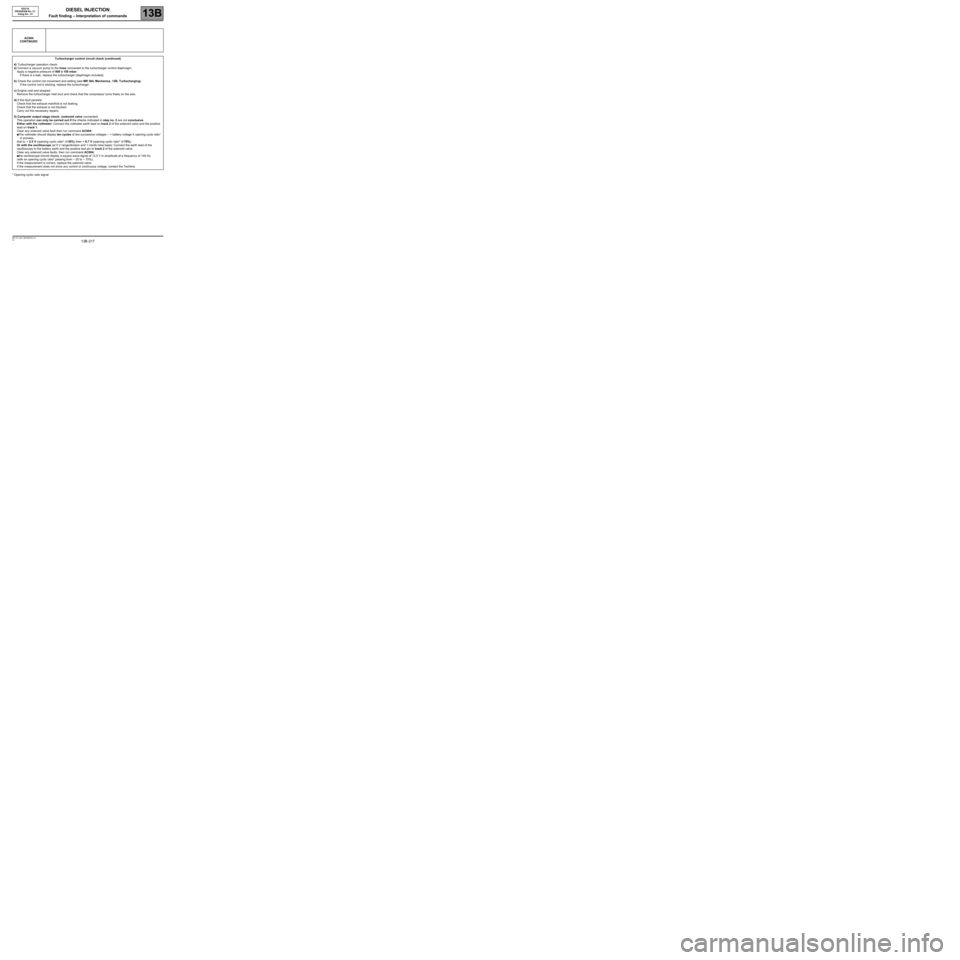
DIESEL INJECTION
Fault finding – Interpretation of commands13B
13B -217V3 MR-372-J84-13B250$765.mif
EDC16
PROGRAM No: C1
Vdiag No.: 51
* Opening cyclic ratio signalAC004
CONTINUED
Turbocharger control circuit check (continued)
4) Turbocharger operation check:
a) Connect a vacuum pump to the hose connected to the turbocharger control diaphragm.
Apply a negative pressure of 800 ± 100 mbar:
If there is a leak, replace the turbocharger (diaphragm included).
b) Check the control rod movement and setting (see MR 364, Mechanics, 12B, Turbocharging).
If the control rod is sticking, replace the turbocharger.
c) Engine cold and stopped:
Remove the turbocharger inlet duct and check that the compressor turns freely on the axis.
d) If the fault persists:
Check that the exhaust manifold is not leaking.
Check that the exhaust is not blocked.
Carry out the necessary repairs.
5) Computer output stage check: (solenoid valve connected).
This operation can only be carried out if the checks indicated in step no. 2 are not conclusive.
Either with the voltmeter: Connect the voltmeter earth lead on track 2 of the solenoid valve and the positive
lead on track 1.
Clear any solenoid valve fault then run command AC004:
●The voltmeter should display ten cycles of two successive voltages ~ = battery voltage X opening cycle ratio*
in process.
that is: ~ 2.5 V (opening cyclic ratio* of 20%) then ~ 8.7 V (opening cyclic ratio* of 70%).
Or with the oscilloscope (at 5 V range/division and 1 ms/div time base): Connect the earth lead of the
oscilloscope to the battery earth and the positive test pin to track 2 of the solenoid valve.
Clear any solenoid valve faults, then run command AC004:
●the oscilloscope should display a square wave signal of 12.5 V in amplitude at a frequency of 140 Hz
(with an opening cyclic ratio* passing from ~ 20 to ~ 70%).
If the measurement is correct, replace the solenoid valve.
If the measurement does not show any control or continuous voltage, contact the Techline.
Page 218 of 273
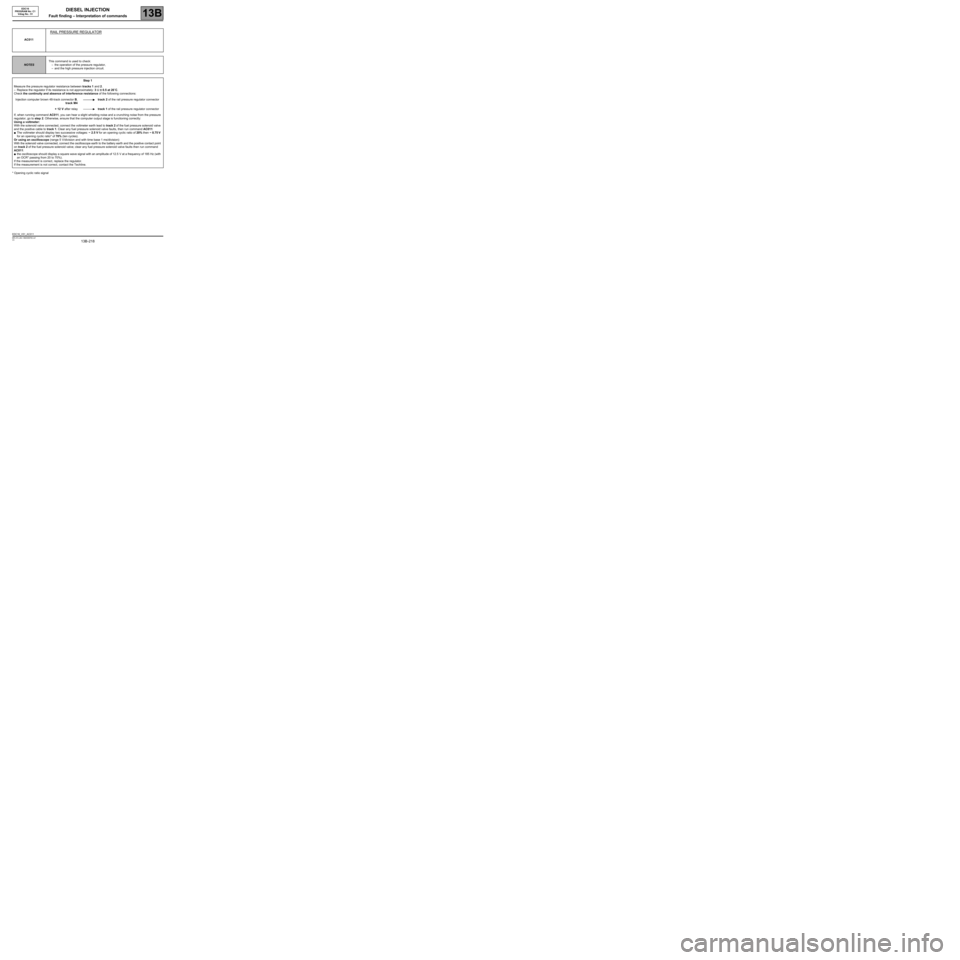
DIESEL INJECTION
Fault finding – Interpretation of commands13B
13B -218V3 MR-372-J84-13B250$765.mif
EDC16
PROGRAM No: C1
Vdiag No.: 51
* Opening cyclic ratio signalAC011
RAIL PRESSURE REGULATOR
NOTESThis command is used to check:
–the operation of the pressure regulator,
–and the high pressure injection circuit.
Step 1
Measure the pressure regulator resistance between tracks 1 and 2.
–Replace the regulator if its resistance is not approximately: 3 Ω ± 0.5 at 20˚C.
Check the continuity and absence of interference resistance of the following connections:
Injection computer brown 48-track connector B,
track M4track 2 of the rail pressure regulator connector
+ 12 V after relaytrack 1 of the rail pressure regulator connector
If, when running command AC011, you can hear a slight whistling noise and a crunching noise from the pressure
regulator, go to step 2. Otherwise, ensure that the computer output stage is functioning correctly:
Using a voltmeter:
With the solenoid valve connected, connect the voltmeter earth lead to track 2 of the fuel pressure solenoid valve
and the positive cable to track 1. Clear any fuel pressure solenoid valve faults, then run command AC011:
●The voltmeter should display two successive voltages: ~ 2.5 V for an opening cyclic ratio of 20% then ~ 8.75 V
for an opening cyclic ratio* of 70% (ten cycles).
Or using an oscilloscope (range 5 V/division and with time base 1 ms/division):
With the solenoid valve connected, connect the oscilloscope earth to the battery earth and the positive contact point
on track 2 of the fuel pressure solenoid valve; clear any fuel pressure solenoid valve faults then run command
AC011:
●the oscilloscope should display a square wave signal with an amplitude of 12.5 V at a frequency of 185 Hz (with
an OCR* passing from 20 to 70%).
If the measurement is correct, replace the regulator.
If the measurement is not correct, contact the Techline.
EDC16_V51_AC011
Page 219 of 273
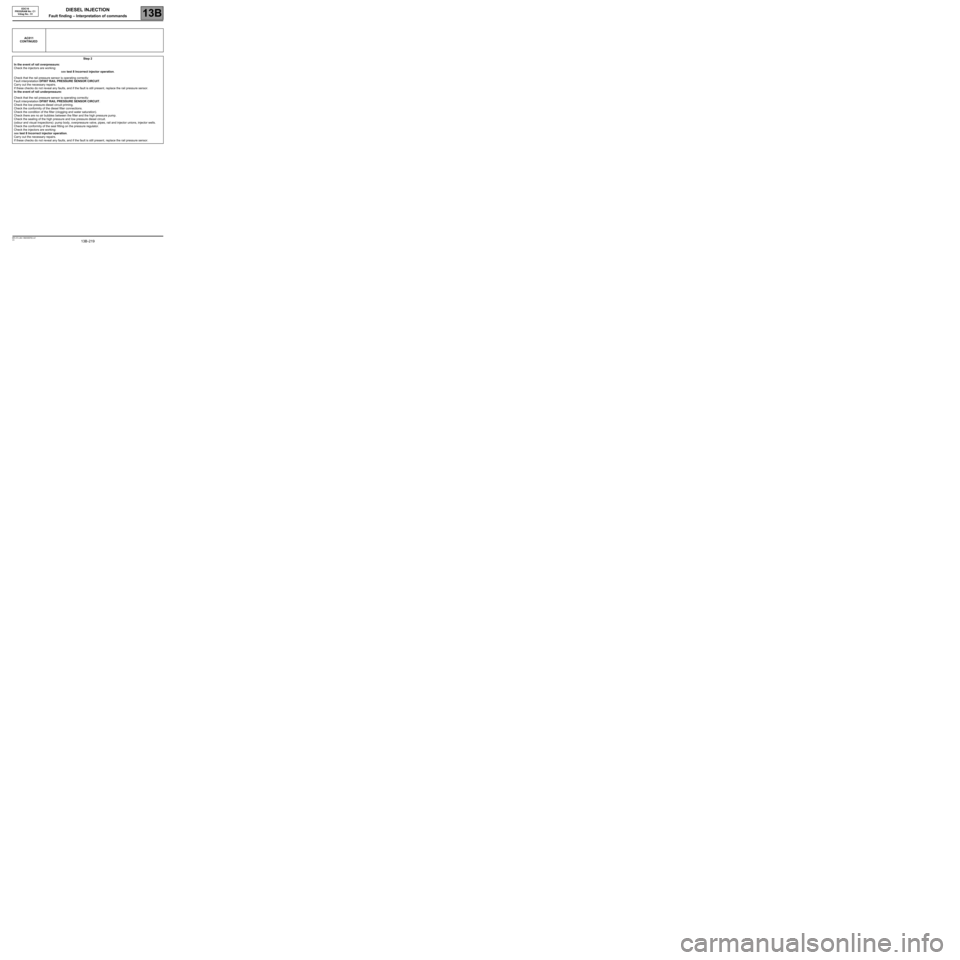
DIESEL INJECTION
Fault finding – Interpretation of commands13B
13B -219V3 MR-372-J84-13B250$765.mif
EDC16
PROGRAM No: C1
Vdiag No.: 51
AC011
CONTINUED
Step 2
In the event of rail overpressure:
Check the injectors are working:
see test 8 Incorrect injector operation.
Check that the rail pressure sensor is operating correctly:
Fault interpretation DF007 RAIL PRESSURE SENSOR CIRCUIT.
Carry out the necessary repairs.
If these checks do not reveal any faults, and if the fault is still present, replace the rail pressure sensor.
In the event of rail underpressure:
Check that the rail pressure sensor is operating correctly:
Fault interpretation DF007 RAIL PRESSURE SENSOR CIRCUIT.
Check the low pressure diesel circuit priming.
Check the conformity of the diesel filter connections.
Check the condition of the filter (clogging and water saturation).
Check there are no air bubbles between the filter and the high pressure pump.
Check the sealing of the high pressure and low pressure diesel circuit.
(odour and visual inspections): pump body, overpressure valve, pipes, rail and injector unions, injector wells.
Check the conformity of the seal fitting on the pressure regulator.
Check the injectors are working:
see test 8 Incorrect injector operation.
Carry out the necessary repairs.
If these checks do not reveal any faults, and if the fault is still present, replace the rail pressure sensor.
Page 220 of 273
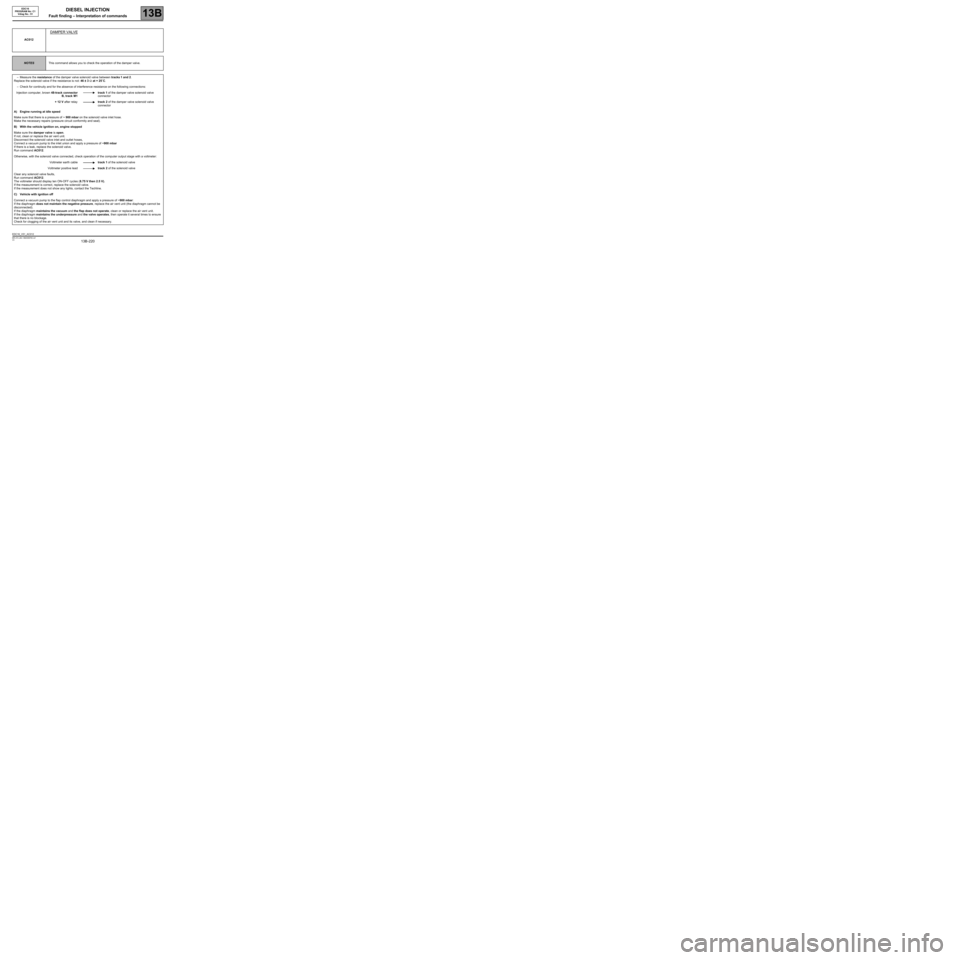
DIESEL INJECTION
Fault finding – Interpretation of commands13B
13B -220V3 MR-372-J84-13B250$765.mif
EDC16
PROGRAM No: C1
Vdiag No.: 51
AC012
DAMPER VALVE
NOTESThis command allows you to check the operation of the damper valve.
–Measure the resistance of the damper valve solenoid valve between tracks 1 and 2.
Replace the solenoid valve if the resistance is not: 46 ± 3 Ω at + 25˚C.
–Check for continuity and for the absence of interference resistance on the following connections:
Injection computer, brown 48-track connector
B, track M1track 1 of the damper valve solenoid valve
connector
+ 12 V after relaytrack 2 of the damper valve solenoid valve
connector
A) Engine running at idle speed
Make sure that there is a pressure of ~ 900 mbar on the solenoid valve inlet hose.
Make the necessary repairs (pressure circuit conformity and seal).
B) With the vehicle ignition on, engine stopped
Make sure the damper valve is open.
If not, clean or replace the air vent unit.
Disconnect the solenoid valve inlet and outlet hoses,
Connect a vacuum pump to the inlet union and apply a pressure of ~900 mbar
If there is a leak, replace the solenoid valve.
Run command AC012.
Otherwise, with the solenoid valve connected, check operation of the computer output stage with a voltmeter:
Voltmeter earth cabletrack 1 of the solenoid valve
Voltmeter positive leadtrack 2 of the solenoid valve
Clear any solenoid valve faults,
Run command AC012.
The voltmeter should display ten ON-OFF cycles (8.75 V then 2.5 V).
If the measurement is correct, replace the solenoid valve.
If the measurement does not show any lights, contact the Techline.
C) Vehicle with ignition off
Connect a vacuum pump to the flap control diaphragm and apply a pressure of ~900 mbar:
If the diaphragm does not maintain the negative pressure, replace the air vent unit (the diaphragm cannot be
disconnected).
If the diaphragm maintains the vacuum and the flap does not operate, clean or replace the air vent unit.
If the diaphragm maintains the underpressure and the valve operates, then operate it several times to ensure
that there is no blockage.
Check for clogging of the air vent unit and its valve, and clean if necessary.
EDC16_V51_AC012
Page 221 of 273
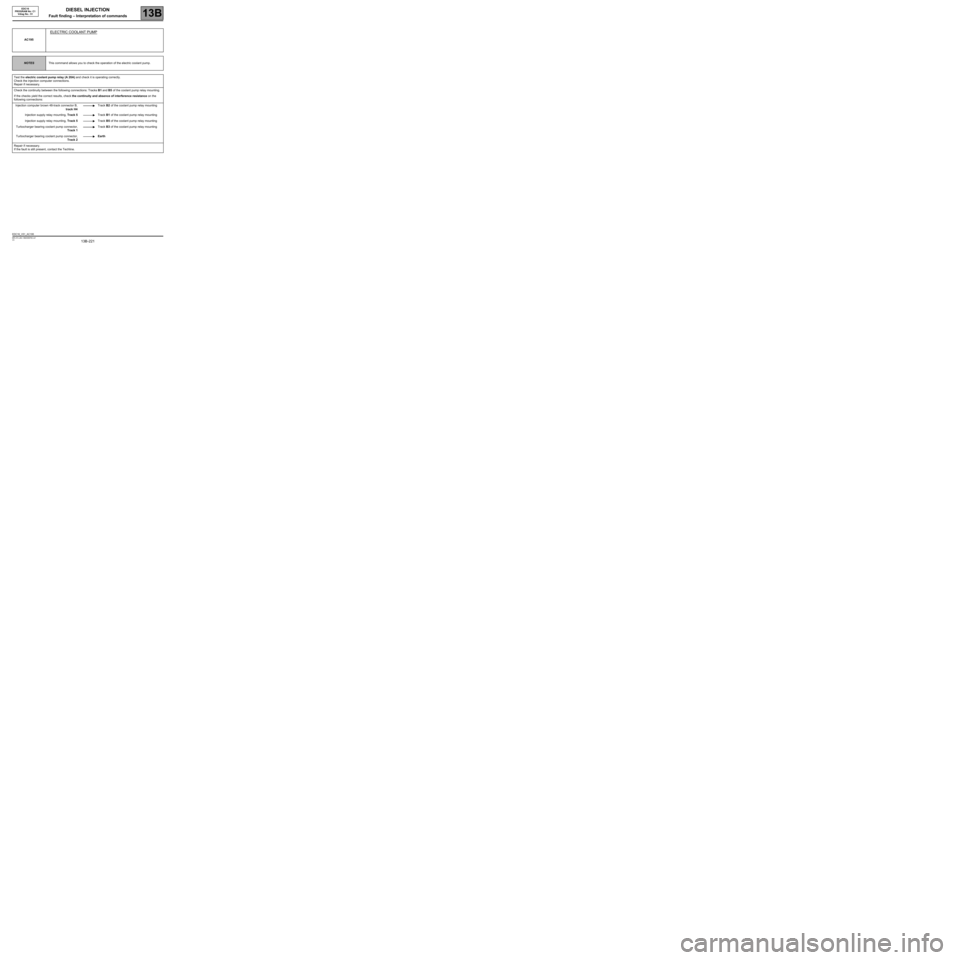
DIESEL INJECTION
Fault finding – Interpretation of commands13B
13B -221V3 MR-372-J84-13B250$765.mif
EDC16
PROGRAM No: C1
Vdiag No.: 51
AC195
ELECTRIC COOLANT PUMP
NOTESThis command allows you to check the operation of the electric coolant pump.
Test the electric coolant pump relay (A 20A) and check it is operating correctly.
Check the injection computer connections.
Repair if necessary.
Check the continuity between the following connections: Tracks B1 and B5 of the coolant pump relay mounting.
If the checks yield the correct results, check the continuity and absence of interference resistance on the
following connections:
Injection computer brown 48-track connector B,
track H4Track B2 of the coolant pump relay mounting
Injection supply relay mounting, Track 5Track B1 of the coolant pump relay mounting
Injection supply relay mounting, Track 5Track B5 of the coolant pump relay mounting
Turbocharger bearing coolant pump connector,
Track 1Track B3 of the coolant pump relay mounting
Turbocharger bearing coolant pump connector,
Track 2Earth
Repair if necessary.
If the fault is still present, contact the Techline.
EDC16_V51_AC195
Page 222 of 273
DIESEL INJECTION
Fault finding – Customer complaints13B
13B - 222V3 MR-372-J84-13B250$810.mif
EDC16
PROGRAM NO.: C1
Vdiag No.: 51DIESEL INJECTION
Fault finding – Customer complaints
NOTESBefore dealing with this customer complaint, check that there are no faults, and the
conformity (or otherwise) of the parameters and statuses using the diagnostic tool.
If the customer complaint is not eliminated, then proceed according to the
corresponding fault finding chart.
NO DIALOGUE WITH ENGINE MANAGEMENT COMPUTER ALP1
STARTING FAULT OR STARTING IMPOSSIBLE ALP2
INJECTION NOISEALP3
POOR PERFORMANCEALP4
IRREGULAR ENGINE OPERATION ALP5
EXTERNAL LEAKS FROM THE FUEL CIRCUIT ALP6
ROUGH IDLEALP7
OIL LEAKS FROM THE TURBOCHARGER ALP8
TURBOCHARGER NOISESALP9
SMOKE FROM THE EXHAUSTALP10
MR-372-J84-13B250$810.mif
Page 223 of 273
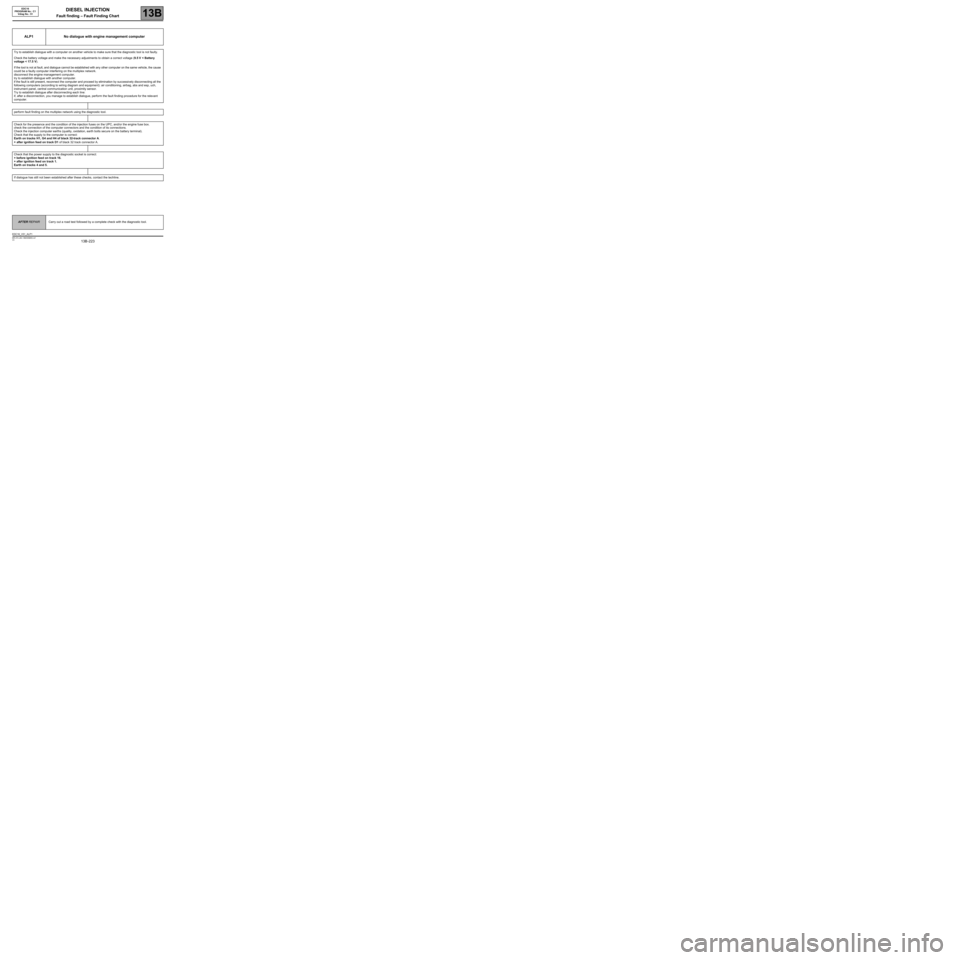
DIESEL INJECTION
Fault finding – Fault Finding Chart13B
13B -223V3 MR-372-J84-13B250$855.mif
EDC16
PROGRAM No.: C1
Vdiag No.: 51DIESEL INJECTION
Fault finding – Fault Finding Chart
ALP1 No dialogue with engine management computer
Try to establish dialogue with a computer on another vehicle to make sure that the diagnostic tool is not faulty.
Check the battery voltage and make the necessary adjustments to obtain a correct voltage (9.5 V < Battery
voltage < 17.5 V).
If the tool is not at fault, and dialogue cannot be established with any other computer on the same vehicle, the cause
could be a faulty computer interfering on the multiplex network.
disconnect the engine management computer.
try to establish dialogue with another computer.
if the fault is still present, reconnect the computer and proceed by elimination by successively disconnecting all the
following computers (according to wiring diagram and equipment): air conditioning, airbag, abs and esp, uch,
instrument panel, central communication unit, proximity sensor.
Try to establish dialogue after disconnecting each line:
if, after a disconnection, you manage to establish dialogue, perform the fault finding procedure for the relevant
computer.
perform fault finding on the multiplex network using the diagnostic tool.
Check for the presence and the condition of the injection fuses on the UPC, and/or the engine fuse box.
check the connection of the computer connectors and the condition of its connections.
Check the injection computer earths (quality, oxidation, earth bolts secure on the battery terminal).
Check that the supply to the computer is correct:
Earth on tracks H1, G4 and H4 of black 32-track connector A.
+ after ignition feed on track D1 of black 32 track connector A.
Check that the power supply to the diagnostic socket is correct:
+ before ignition feed on track 16.
+ after ignition feed on track 1.
Earth on tracks 4 and 5.
If dialogue has still not been established after these checks, contact the techline.
AFTER REPAIRCarry out a road test followed by a complete check with the diagnostic tool.
EDC16_V51_ALP1
Page 224 of 273
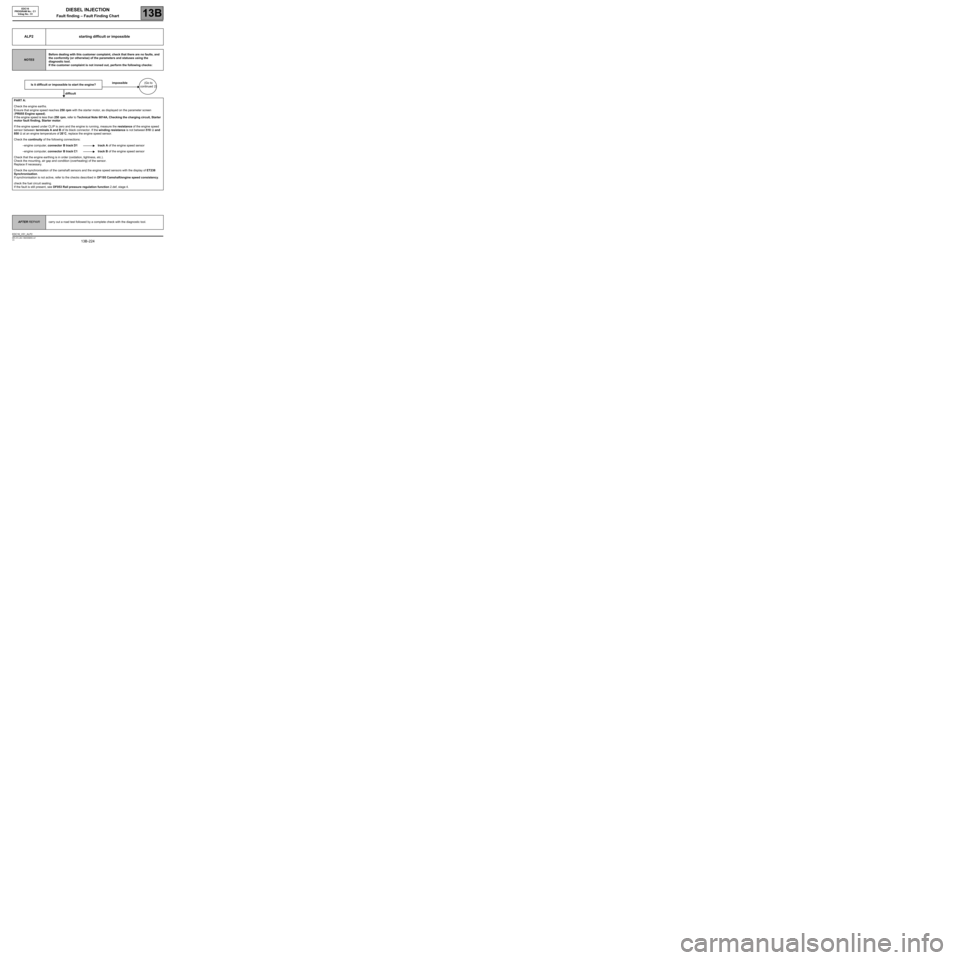
DIESEL INJECTION
Fault finding – Fault Finding Chart13B
13B -224V3 MR-372-J84-13B250$855.mif
EDC16
PROGRAM No.: C1
Vdiag No.: 51
ALP2 starting difficult or impossible
NOTESBefore dealing with this customer complaint, check that there are no faults, and
the conformity (or otherwise) of the parameters and statuses using the
diagnostic tool.
If the customer complaint is not ironed out, perform the following checks:
Is it difficult or impossible to start the engine?impossible(Go to
continued 2)
difficult
PART A:
Check the engine earths.
Ensure that engine speed reaches 250 rpm with the starter motor, as displayed on the parameter screen
(PR055 Engine speed).
If the engine speed is less than 250 rpm, refer to Technical Note 6014A, Checking the charging circuit, Starter
motor fault finding, Starter motor.
If the engine speed under CLIP is zero and the engine is running, measure the resistance of the engine speed
sensor between terminals A and B of its black connector. If the winding resistance is not between 510 Ω and
850 Ω at an engine temperature of 20˚C, replace the engine speed sensor.
Check the continuity of the following connections:
–engine computer, connector B track D1 track A of the engine speed sensor
–engine computer, connector B track C1 track B of the engine speed sensor
Check that the engine earthing is in order (oxidation, tightness, etc.).
Check the mounting, air gap and condition (overheating) of the sensor.
Replace if necessary.
Check the synchronisation of the camshaft sensors and the engine speed sensors with the display of ET238
Synchronisation.
If synchronisation is not active, refer to the checks described in DF195 Camshaft/engine speed consistency.
check the fuel circuit sealing.
If the fault is still present, see DF053 Rail pressure regulation function 2.def, stage 4.
AFTER REPAIRcarry out a road test followed by a complete check with the diagnostic tool.
EDC16_V51_ALP2