Page 2584 of 3061
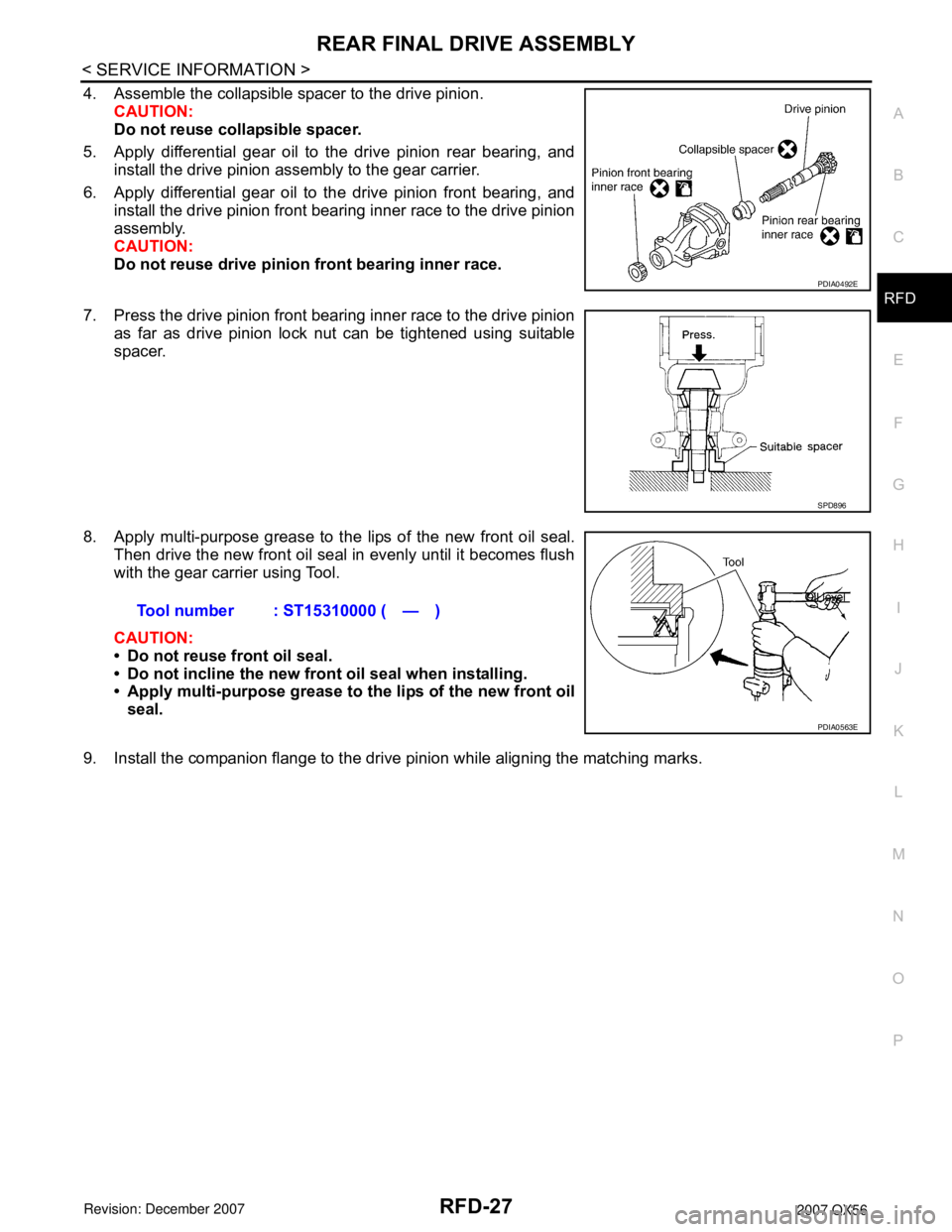
REAR FINAL DRIVE ASSEMBLY
RFD-27
< SERVICE INFORMATION >
C
E
F
G
H
I
J
K
L
MA
B
RFD
N
O
P
4. Assemble the collapsible spacer to the drive pinion.
CAUTION:
Do not reuse collapsible spacer.
5. Apply differential gear oil to the drive pinion rear bearing, and
install the drive pinion assembly to the gear carrier.
6. Apply differential gear oil to the drive pinion front bearing, and
install the drive pinion front bearing inner race to the drive pinion
assembly.
CAUTION:
Do not reuse drive pinion front bearing inner race.
7. Press the drive pinion front bearing inner race to the drive pinion
as far as drive pinion lock nut can be tightened using suitable
spacer.
8. Apply multi-purpose grease to the lips of the new front oil seal.
Then drive the new front oil seal in evenly until it becomes flush
with the gear carrier using Tool.
CAUTION:
• Do not reuse front oil seal.
• Do not incline the new front oil seal when installing.
• Apply multi-purpose grease to the lips of the new front oil
seal.
9. Install the companion flange to the drive pinion while aligning the matching marks.
PDIA0492E
SPD896
Tool number : ST15310000 ( — )
PDIA0563E
Page 2585 of 3061
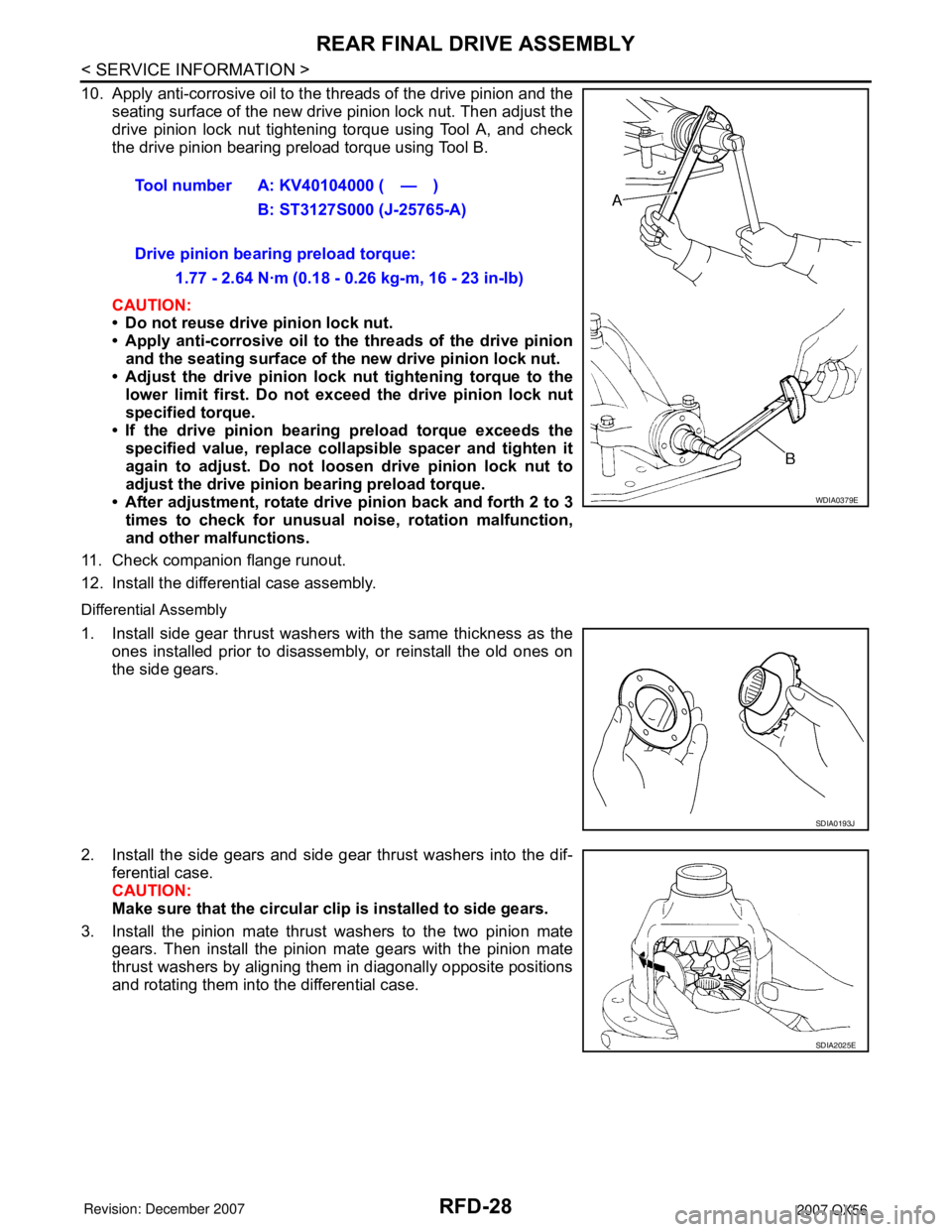
RFD-28
< SERVICE INFORMATION >
REAR FINAL DRIVE ASSEMBLY
10. Apply anti-corrosive oil to the threads of the drive pinion and the
seating surface of the new drive pinion lock nut. Then adjust the
drive pinion lock nut tightening torque using Tool A, and check
the drive pinion bearing preload torque using Tool B.
CAUTION:
• Do not reuse drive pinion lock nut.
• Apply anti-corrosive oil to the threads of the drive pinion
and the seating surface of the new drive pinion lock nut.
• Adjust the drive pinion lock nut tightening torque to the
lower limit first. Do not exceed the drive pinion lock nut
specified torque.
• If the drive pinion bearing preload torque exceeds the
specified value, replace collapsible spacer and tighten it
again to adjust. Do not loosen drive pinion lock nut to
adjust the drive pinion bearing preload torque.
• After adjustment, rotate drive pinion back and forth 2 to 3
times to check for unusual noise, rotation malfunction,
and other malfunctions.
11. Check companion flange runout.
12. Install the differential case assembly.
Differential Assembly
1. Install side gear thrust washers with the same thickness as the
ones installed prior to disassembly, or reinstall the old ones on
the side gears.
2. Install the side gears and side gear thrust washers into the dif-
ferential case.
CAUTION:
Make sure that the circular clip is installed to side gears.
3. Install the pinion mate thrust washers to the two pinion mate
gears. Then install the pinion mate gears with the pinion mate
thrust washers by aligning them in diagonally opposite positions
and rotating them into the differential case.Tool number A: KV40104000 ( — )
B: ST3127S000 (J-25765-A)
Drive pinion bearing preload torque:
1.77 - 2.64 N·m (0.18 - 0.26 kg-m, 16 - 23 in-lb)
WDIA0379E
SDIA0193J
SDIA2025E
Page 2586 of 3061
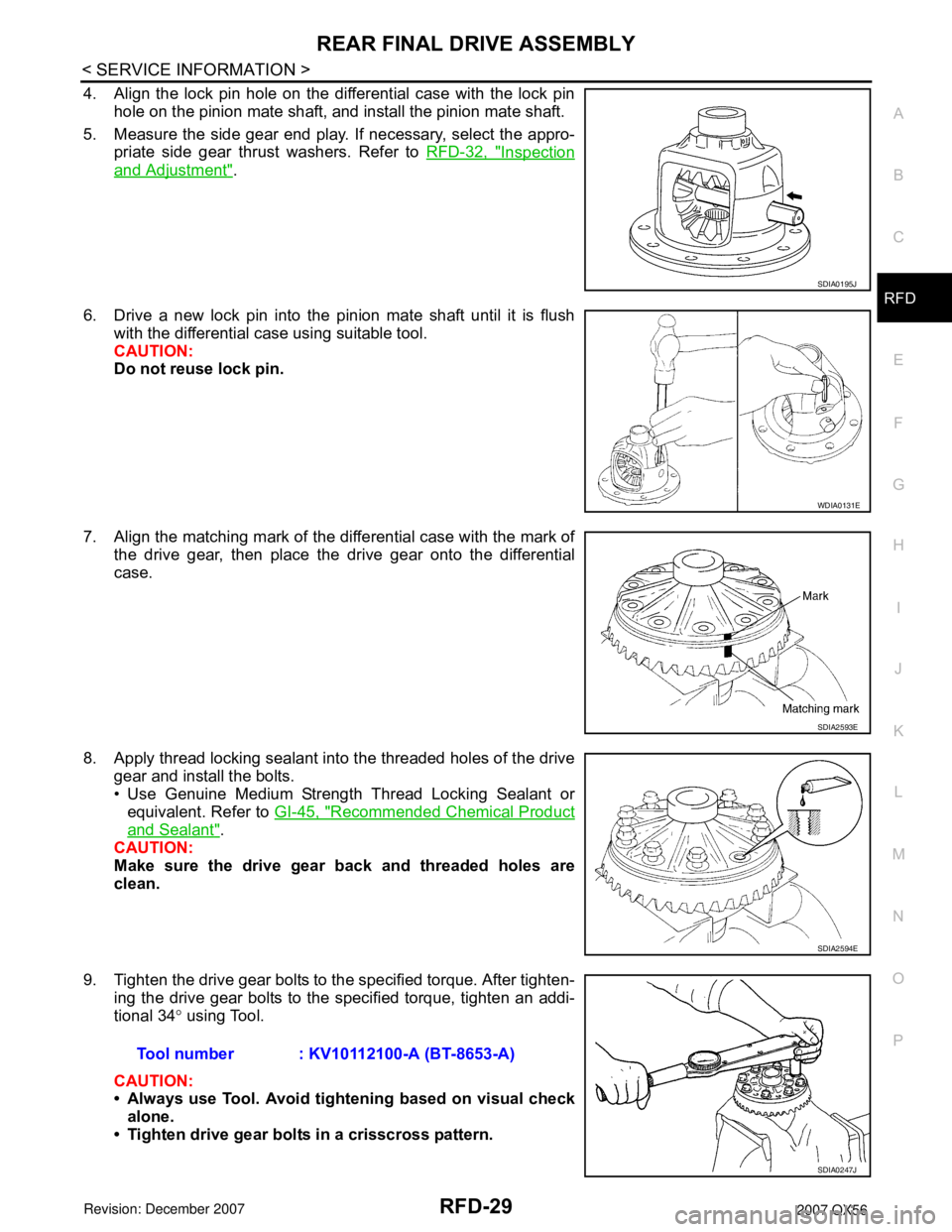
REAR FINAL DRIVE ASSEMBLY
RFD-29
< SERVICE INFORMATION >
C
E
F
G
H
I
J
K
L
MA
B
RFD
N
O
P
4. Align the lock pin hole on the differential case with the lock pin
hole on the pinion mate shaft, and install the pinion mate shaft.
5. Measure the side gear end play. If necessary, select the appro-
priate side gear thrust washers. Refer to RFD-32, "
Inspection
and Adjustment".
6. Drive a new lock pin into the pinion mate shaft until it is flush
with the differential case using suitable tool.
CAUTION:
Do not reuse lock pin.
7. Align the matching mark of the differential case with the mark of
the drive gear, then place the drive gear onto the differential
case.
8. Apply thread locking sealant into the threaded holes of the drive
gear and install the bolts.
• Use Genuine Medium Strength Thread Locking Sealant or
equivalent. Refer to GI-45, "
Recommended Chemical Product
and Sealant".
CAUTION:
Make sure the drive gear back and threaded holes are
clean.
9. Tighten the drive gear bolts to the specified torque. After tighten-
ing the drive gear bolts to the specified torque, tighten an addi-
tional 34° using Tool.
CAUTION:
• Always use Tool. Avoid tightening based on visual check
alone.
• Tighten drive gear bolts in a crisscross pattern.
SDIA0195J
WDIA0131E
SDIA2593E
SDIA2594E
Tool number : KV10112100-A (BT-8653-A)
SDIA0247J
Page 2587 of 3061
RFD-30
< SERVICE INFORMATION >
REAR FINAL DRIVE ASSEMBLY
10. Press the side bearing inner races into the differential case
using Tools.
CAUTION:
Do not reuse side bearing inner race.
11. Install the differential case assembly with the side bearing outer
races into the gear carrier.
12. Measure the side bearing preload torque. If necessary, select
the appropriate side bearing adjusting washers.
13. Insert the selected left and right side bearing adjusting washers
in place between the side bearings and gear carrier.
14. Install the side bearing caps with the matching marks aligned
and tighten the side bearing cap bolts to the specified torque.
15. Check and adjust the drive gear runout, tooth contact, drive gear to drive pinion backlash, and total pre-
load torque.
Recheck the above items.
16. Install the side flanges. Tool number A: KV38100200 (J-26233)
B: ST33081000 ( — )
SPD353
SPD919
SPD924
SPD889
Page 2589 of 3061
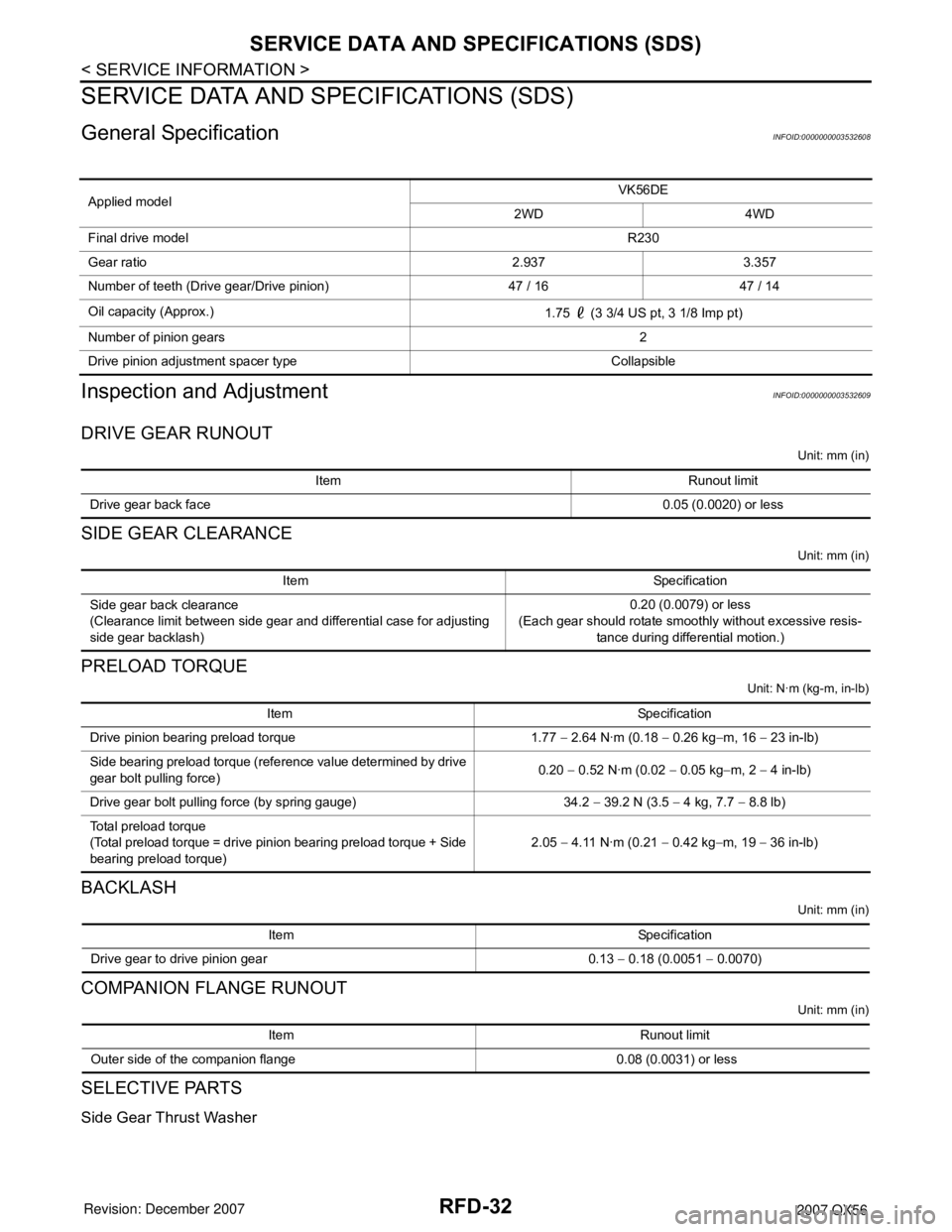
RFD-32
< SERVICE INFORMATION >
SERVICE DATA AND SPECIFICATIONS (SDS)
SERVICE DATA AND SPECIFICATIONS (SDS)
General SpecificationINFOID:0000000003532608
Inspection and AdjustmentINFOID:0000000003532609
DRIVE GEAR RUNOUT
Unit: mm (in)
SIDE GEAR CLEARANCE
Unit: mm (in)
PRELOAD TORQUE
Unit: N·m (kg-m, in-lb)
BACKLASH
Unit: mm (in)
COMPANION FLANGE RUNOUT
Unit: mm (in)
SELECTIVE PARTS
Side Gear Thrust Washer
Applied modelVK56DE
2WD 4WD
Final drive modelR230
Gear ratio 2.937 3.357
Number of teeth (Drive gear/Drive pinion) 47 / 16 47 / 14
Oil capacity (Approx.)
1.75 (3 3/4 US pt, 3 1/8 Imp pt)
Number of pinion gears 2
Drive pinion adjustment spacer type Collapsible
Item Runout limit
Drive gear back face0.05 (0.0020) or less
Item Specification
Side gear back clearance
(Clearance limit between side gear and differential case for adjusting
side gear backlash)0.20 (0.0079) or less
(Each gear should rotate smoothly without excessive resis-
tance during differential motion.)
Item Specification
Drive pinion bearing preload torque 1.77 − 2.64 N·m (0.18 − 0.26 kg−m, 16 − 23 in-lb)
Side bearing preload torque (reference value determined by drive
gear bolt pulling force)0.20 − 0.52 N·m (0.02 − 0.05 kg−m, 2 − 4 in-lb)
Drive gear bolt pulling force (by spring gauge) 34.2 − 39.2 N (3.5 − 4 kg, 7.7 − 8.8 lb)
Total preload torque
(Total preload torque = drive pinion bearing preload torque + Side
bearing preload torque)2.05 − 4.11 N·m (0.21 − 0.42 kg−m, 19 − 36 in-lb)
Item Specification
Drive gear to drive pinion gear 0.13 − 0.18 (0.0051 − 0.0070)
Item Runout limit
Outer side of the companion flange 0.08 (0.0031) or less
Page 2594 of 3061
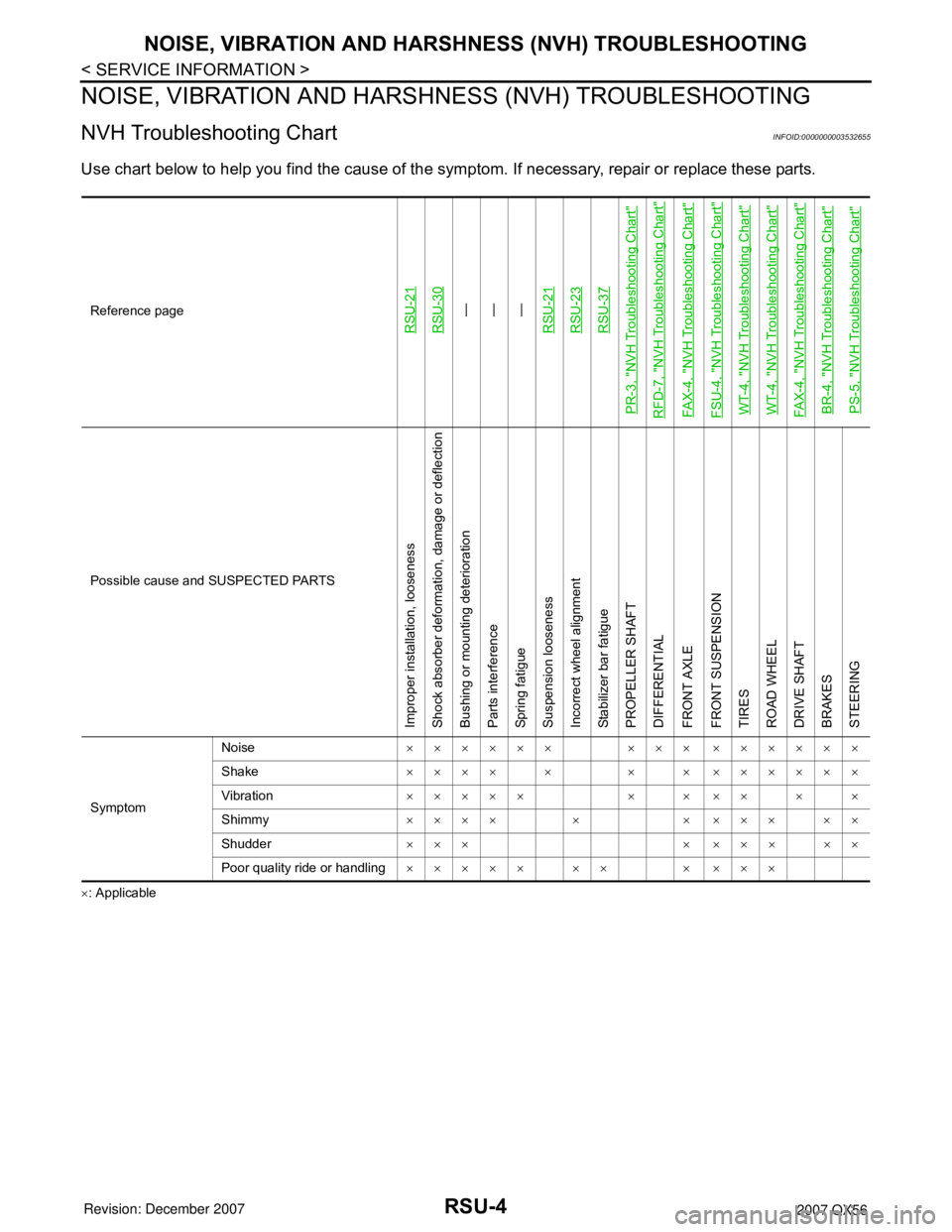
RSU-4
< SERVICE INFORMATION >
NOISE, VIBRATION AND HARSHNESS (NVH) TROUBLESHOOTING
NOISE, VIBRATION AND HARSHNESS (NVH) TROUBLESHOOTING
NVH Troubleshooting ChartINFOID:0000000003532655
Use chart below to help you find the cause of the symptom. If necessary, repair or replace these parts.
×: ApplicableReference page
RSU-21RSU-30
—
—
—
RSU-21
RSU-23RSU-37
PR-3, "
NVH Troubleshooting Chart
"
RFD-7, "
NVH Troubleshooting Chart
"
FAX-4, "
NVH Troubleshooting Chart
"
FSU-4, "
NVH Troubleshooting Chart
"
WT-4, "
NVH Troubleshooting Chart
"
WT-4, "
NVH Troubleshooting Chart
"
FAX-4, "
NVH Troubleshooting Chart
"
BR-4, "
NVH Troubleshooting Chart
"
PS-5, "
NVH Troubleshooting Chart
"
Possible cause and SUSPECTED PARTS
Improper installation, looseness
Shock absorber deformation, damage or deflection
Bushing or mounting deterioration
Parts interference
Spring fatigue
Suspension looseness
Incorrect wheel alignment
Stabilizer bar fatigue
PROPELLER SHAFT
DIFFERENTIAL
FRONT AXLE
FRONT SUSPENSION
TIRES
ROAD WHEEL
DRIVE SHAFT
BRAKES
STEERING
SymptomNoise×××××× ××× ××××××
Shake×××× × × × ××××××
Vibration××××× × × ×× × ×
Shimmy×××× × × ××× ××
Shudder ××× × ××× ××
Poor quality ride or handling××××× ×× × ×××
Page 2993 of 3061
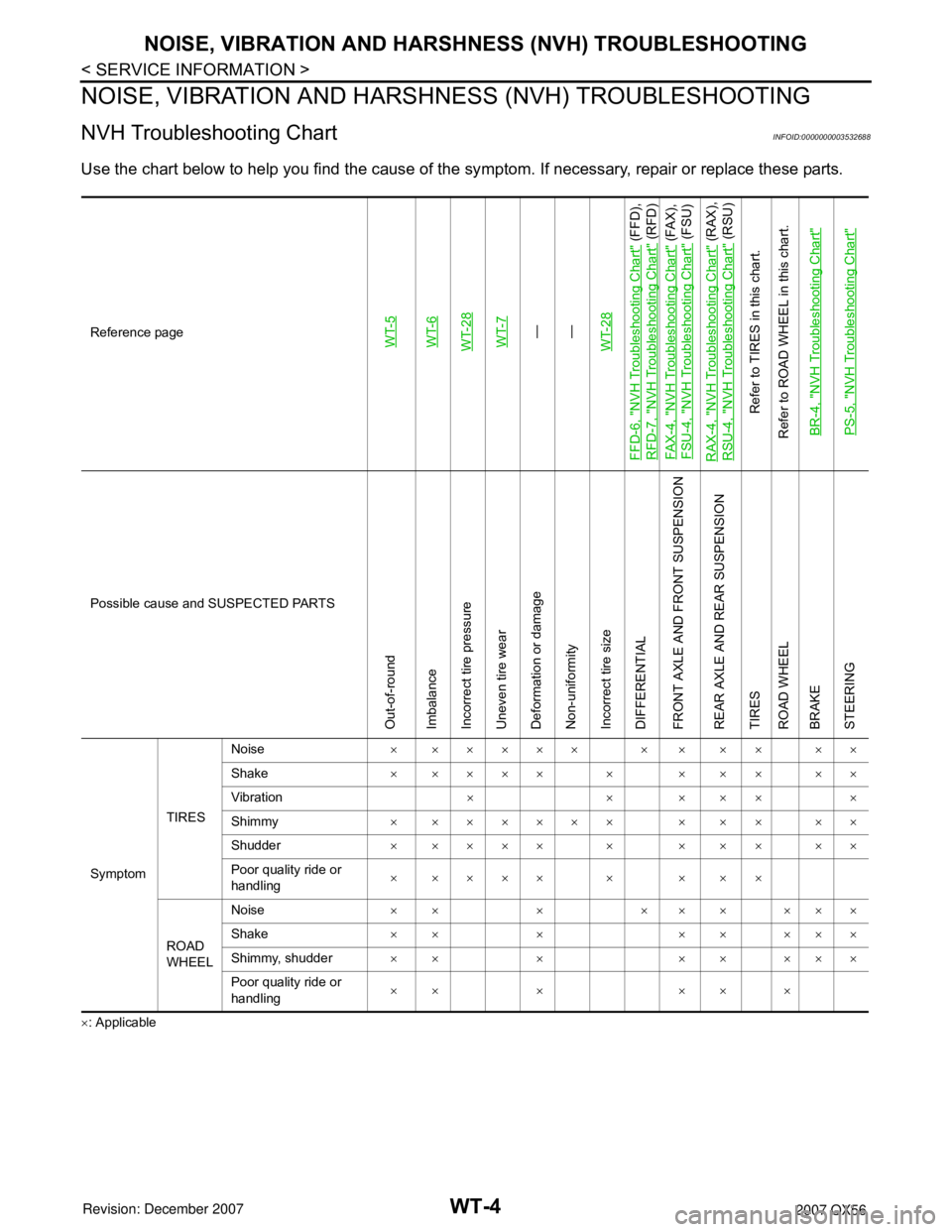
WT-4
< SERVICE INFORMATION >
NOISE, VIBRATION AND HARSHNESS (NVH) TROUBLESHOOTING
NOISE, VIBRATION AND HARSHNESS (NVH) TROUBLESHOOTING
NVH Troubleshooting ChartINFOID:0000000003532688
Use the chart below to help you find the cause of the symptom. If necessary, repair or replace these parts.
×: ApplicableReference page
WT-5WT-6WT-28WT-7—
—
WT-28
FFD-6, "
NVH Troubleshooting Chart
" (FFD),
RFD-7, "
NVH Troubleshooting Chart
" (RFD)
FA X - 4 , "
NVH Troubleshooting Chart
" (FAX),
FSU-4, "
NVH Troubleshooting Chart
" (FSU)
RAX-4, "
NVH Troubleshooting Chart
" (RAX),
RSU-4, "
NVH Troubleshooting Chart
" (RSU)
Refer to TIRES in this chart.
Refer to ROAD WHEEL in this chart.
BR-4, "
NVH Troubleshooting Chart
"
PS-5, "
NVH Troubleshooting Chart
"
Possible cause and SUSPECTED PARTS
Out-of-round
Imbalance
Incorrect tire pressure
Uneven tire wear
Deformation or damage
Non-uniformity
Incorrect tire size
DIFFERENTIAL
FRONT AXLE AND FRONT SUSPENSION
REAR AXLE AND REAR SUSPENSION
TIRES
ROAD WHEEL
BRAKE
STEERING
SymptomTIRESNoise× ××××× × × × × ××
Shake× ×××× × × × × ××
Vibration××××××
Shimmy× ×××××× × × × ××
Shudder× ×××× × × × × ××
Poor quality ride or
handling× ×××× × × × ×
ROAD
WHEELNoise×× × ××× ×××
Shake×× × ×× ×××
Shimmy, shudder×× × ×× ×××
Poor quality ride or
handling×× × ×× ×