Page 1238 of 3061
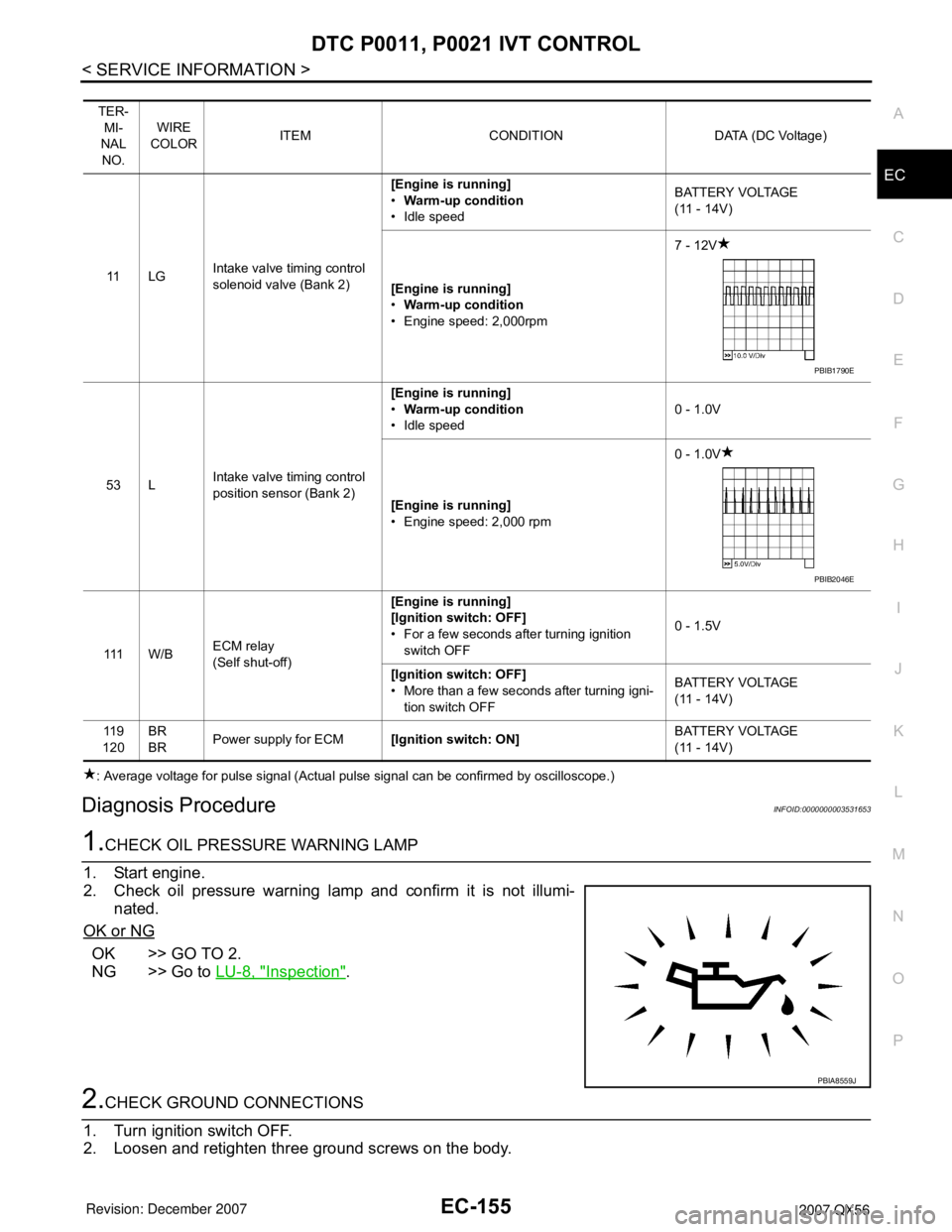
DTC P0011, P0021 IVT CONTROL
EC-155
< SERVICE INFORMATION >
C
D
E
F
G
H
I
J
K
L
MA
EC
N
P O
: Average voltage for pulse signal (Actual pulse signal can be confirmed by oscilloscope.)
Diagnosis ProcedureINFOID:0000000003531653
1.CHECK OIL PRESSURE WARNING LAMP
1. Start engine.
2. Check oil pressure warning lamp and confirm it is not illumi-
nated.
OK or NG
OK >> GO TO 2.
NG >> Go to LU-8, "
Inspection".
2.CHECK GROUND CONNECTIONS
1. Turn ignition switch OFF.
2. Loosen and retighten three ground screws on the body.
TER-
MI-
NAL
NO.WIRE
COLORITEM CONDITION DATA (DC Voltage)
11 L GIntake valve timing control
solenoid valve (Bank 2)[Engine is running]
•Warm-up condition
• Idle speedBATTERY VOLTAGE
(11 - 14V)
[Engine is running]
•Warm-up condition
• Engine speed: 2,000rpm7 - 12V
53 LIntake valve timing control
position sensor (Bank 2)[Engine is running]
•Warm-up condition
• Idle speed0 - 1.0V
[Engine is running]
• Engine speed: 2,000 rpm0 - 1.0V
111 W / BECM relay
(Self shut-off)[Engine is running]
[Ignition switch: OFF]
• For a few seconds after turning ignition
switch OFF0 - 1.5V
[Ignition switch: OFF]
• More than a few seconds after turning igni-
tion switch OFFBATTERY VOLTAGE
(11 - 14V)
11 9
120BR
BRPower supply for ECM[Ignition switch: ON]BATTERY VOLTAGE
(11 - 14V)
PBIB1790E
PBIB2046E
PBIA8559J
Page 1243 of 3061
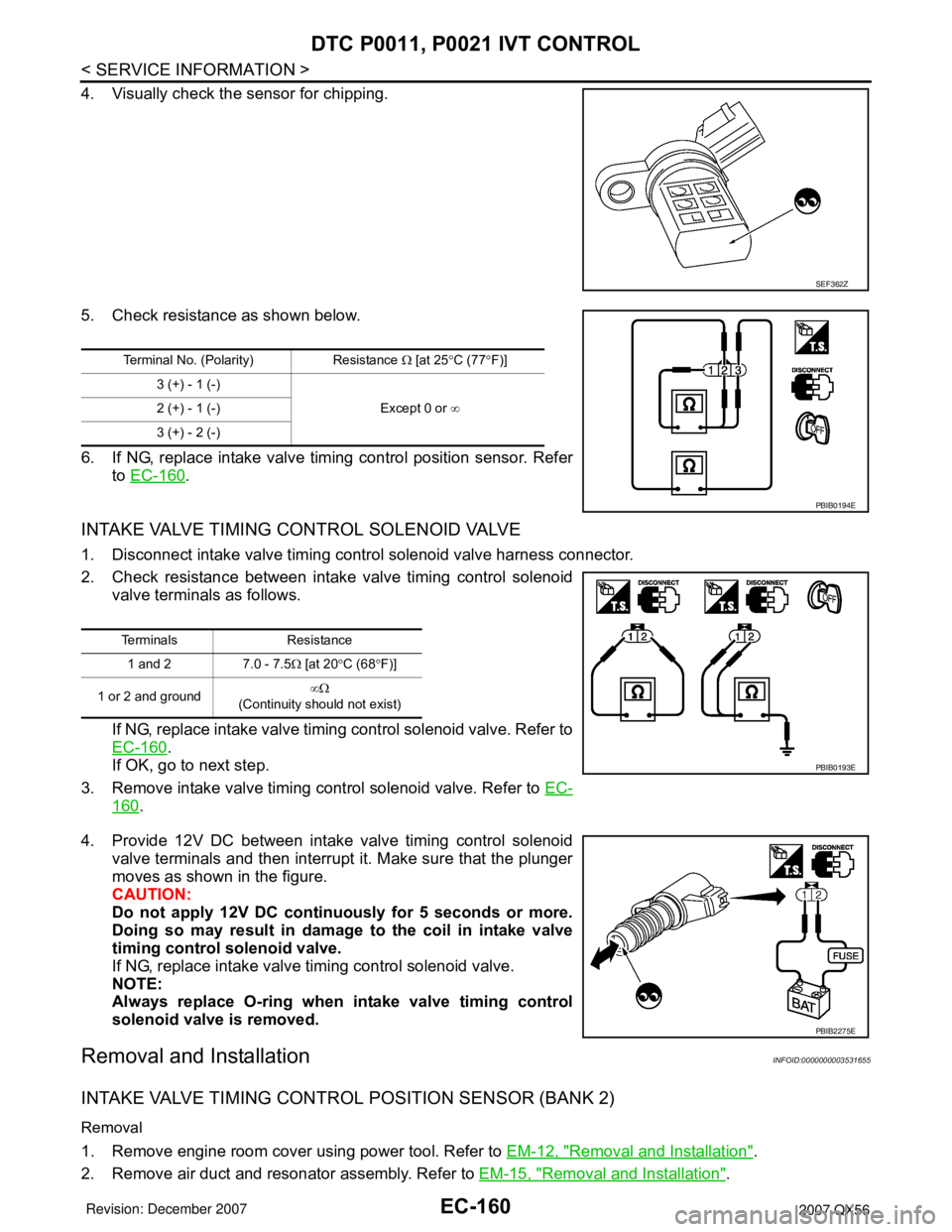
EC-160
< SERVICE INFORMATION >
DTC P0011, P0021 IVT CONTROL
4. Visually check the sensor for chipping.
5. Check resistance as shown below.
6. If NG, replace intake valve timing control position sensor. Refer
to EC-160
.
INTAKE VALVE TIMING CONTROL SOLENOID VALVE
1. Disconnect intake valve timing control solenoid valve harness connector.
2. Check resistance between intake valve timing control solenoid
valve terminals as follows.
If NG, replace intake valve timing control solenoid valve. Refer to
EC-160
.
If OK, go to next step.
3. Remove intake valve timing control solenoid valve. Refer to EC-
160.
4. Provide 12V DC between intake valve timing control solenoid
valve terminals and then interrupt it. Make sure that the plunger
moves as shown in the figure.
CAUTION:
Do not apply 12V DC continuously for 5 seconds or more.
Doing so may result in damage to the coil in intake valve
timing control solenoid valve.
If NG, replace intake valve timing control solenoid valve.
NOTE:
Always replace O-ring when intake valve timing control
solenoid valve is removed.
Removal and InstallationINFOID:0000000003531655
INTAKE VALVE TIMING CONTROL POSITION SENSOR (BANK 2)
Removal
1. Remove engine room cover using power tool. Refer to EM-12, "Removal and Installation".
2. Remove air duct and resonator assembly. Refer to EM-15, "
Removal and Installation".
SEF362Z
Terminal No. (Polarity) Resistance Ω [at 25°C (77°F)]
3 (+) - 1 (-)
Except 0 or ∞ 2 (+) - 1 (-)
3 (+) - 2 (-)
PBIB0194E
Terminals Resistance
1 and 2 7.0 - 7.5Ω [at 20°C (68°F)]
1 or 2 and ground∞Ω
(Continuity should not exist)
PBIB0193E
PBIB2275E
Page 1267 of 3061
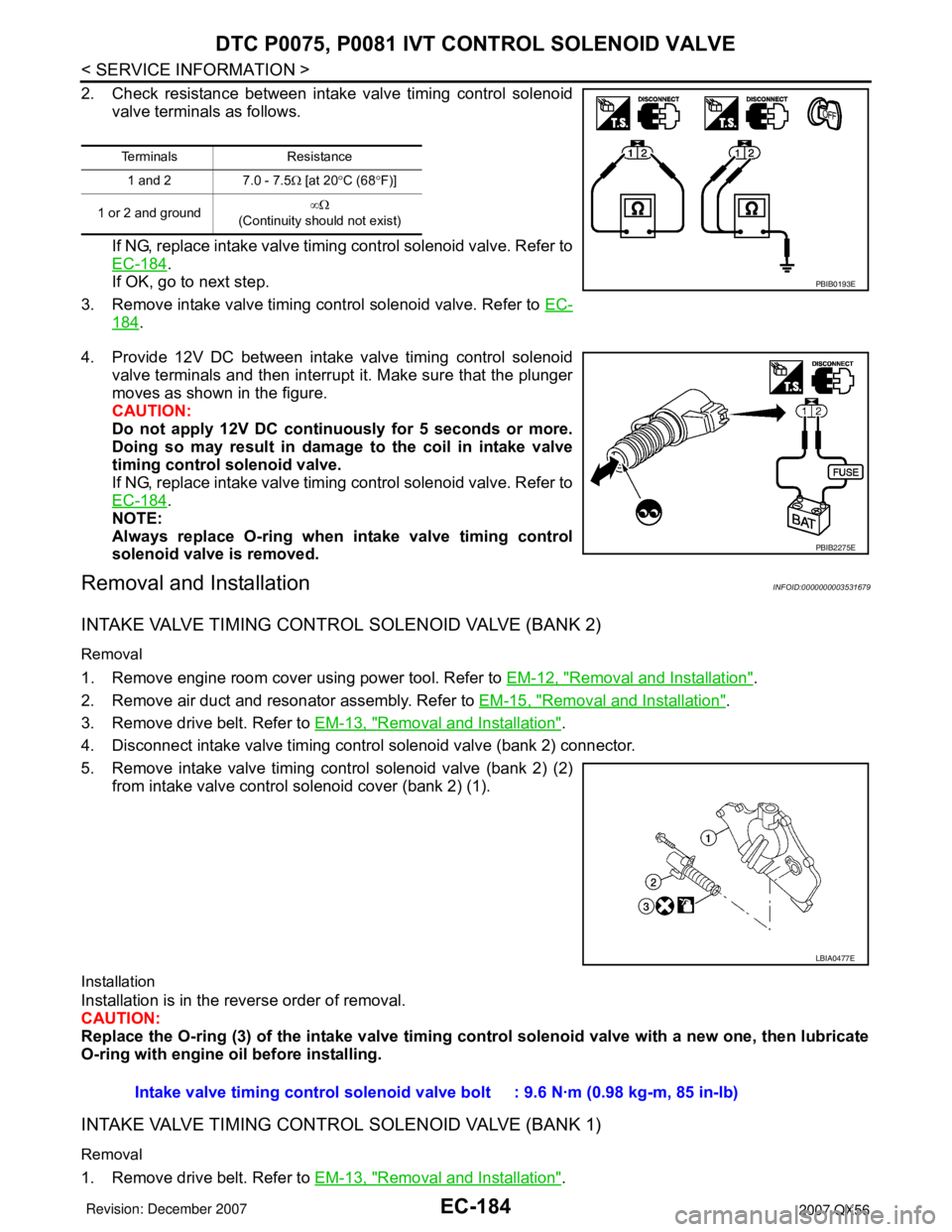
EC-184
< SERVICE INFORMATION >
DTC P0075, P0081 IVT CONTROL SOLENOID VALVE
2. Check resistance between intake valve timing control solenoid
valve terminals as follows.
If NG, replace intake valve timing control solenoid valve. Refer to
EC-184
.
If OK, go to next step.
3. Remove intake valve timing control solenoid valve. Refer to EC-
184.
4. Provide 12V DC between intake valve timing control solenoid
valve terminals and then interrupt it. Make sure that the plunger
moves as shown in the figure.
CAUTION:
Do not apply 12V DC continuously for 5 seconds or more.
Doing so may result in damage to the coil in intake valve
timing control solenoid valve.
If NG, replace intake valve timing control solenoid valve. Refer to
EC-184
.
NOTE:
Always replace O-ring when intake valve timing control
solenoid valve is removed.
Removal and InstallationINFOID:0000000003531679
INTAKE VALVE TIMING CONTROL SOLENOID VALVE (BANK 2)
Removal
1. Remove engine room cover using power tool. Refer to EM-12, "Removal and Installation".
2. Remove air duct and resonator assembly. Refer to EM-15, "
Removal and Installation".
3. Remove drive belt. Refer to EM-13, "
Removal and Installation".
4. Disconnect intake valve timing control solenoid valve (bank 2) connector.
5. Remove intake valve timing control solenoid valve (bank 2) (2)
from intake valve control solenoid cover (bank 2) (1).
Installation
Installation is in the reverse order of removal.
CAUTION:
Replace the O-ring (3) of the intake valve timing control solenoid valve with a new one, then lubricate
O-ring with engine oil before installing.
INTAKE VALVE TIMING CONTROL SOLENOID VALVE (BANK 1)
Removal
1. Remove drive belt. Refer to EM-13, "Removal and Installation".
Terminals Resistance
1 and 2 7.0 - 7.5Ω [at 20°C (68°F)]
1 or 2 and ground∞Ω
(Continuity should not exist)
PBIB0193E
PBIB2275E
LBIA0477E
Intake valve timing control solenoid valve bolt : 9.6 N·m (0.98 kg-m, 85 in-lb)
Page 1383 of 3061
EC-300
< SERVICE INFORMATION >
DTC P0171, P0174 FUEL INJECTION SYSTEM FUNCTION
3. Disconnect all fuel injector harness connectors.
4. Remove fuel injector gallery assembly. Refer to EM-31
.
Keep fuel hose and all fuel injectors connected to fuel injector gallery.
5. For DTC P0171, reconnect fuel injector harness connectors on bank 1.
For DTC P0174, reconnect fuel injector harness connectors on bank 2.
6. Disconnect all ignition coil harness connectors.
7. Prepare pans or saucers under each fuel injector.
8. Crank engine for about 3 seconds.
For DTC P0171, make sure that fuel sprays out from fuel injec-
tors on bank 1.
For DTC P0174, make sure that fuel sprays out from fuel injec-
tors on bank 2.
OK or NG
OK >> GO TO 9.
NG >> Replace fuel injectors from which fuel does not spray
out. Always replace O-ring with new ones.
9.CHECK INTERMITTENT INCIDENT
Refer to EC-138
.
>>INSPECTION END Fuel should be sprayed evenly for each fuel injector.
PBIB1726E
Page 1391 of 3061
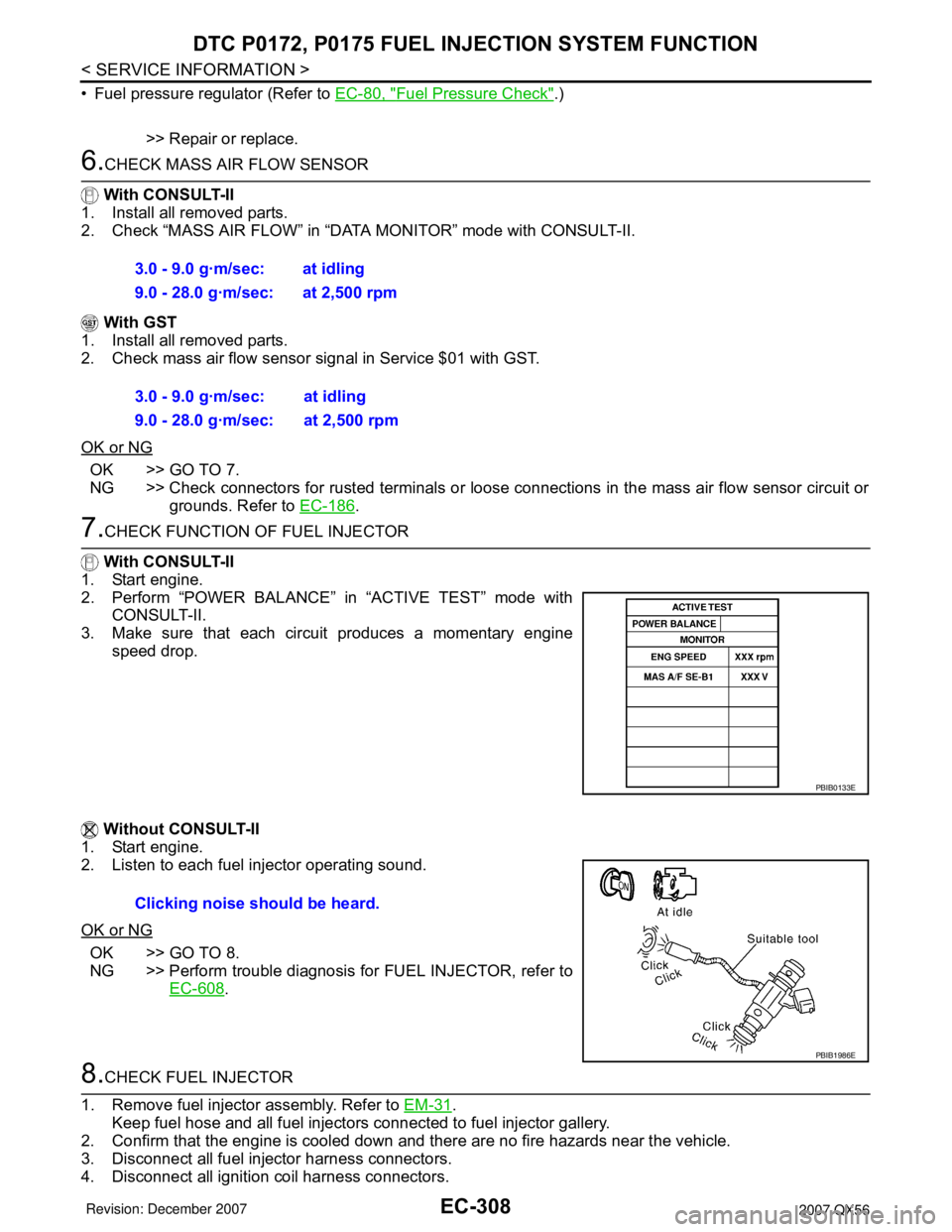
EC-308
< SERVICE INFORMATION >
DTC P0172, P0175 FUEL INJECTION SYSTEM FUNCTION
• Fuel pressure regulator (Refer to EC-80, "Fuel Pressure Check".)
>> Repair or replace.
6.CHECK MASS AIR FLOW SENSOR
With CONSULT-II
1. Install all removed parts.
2. Check “MASS AIR FLOW” in “DATA MONITOR” mode with CONSULT-II.
With GST
1. Install all removed parts.
2. Check mass air flow sensor signal in Service $01 with GST.
OK or NG
OK >> GO TO 7.
NG >> Check connectors for rusted terminals or loose connections in the mass air flow sensor circuit or
grounds. Refer to EC-186
.
7.CHECK FUNCTION OF FUEL INJECTOR
With CONSULT-II
1. Start engine.
2. Perform “POWER BALANCE” in “ACTIVE TEST” mode with
CONSULT-II.
3. Make sure that each circuit produces a momentary engine
speed drop.
Without CONSULT-II
1. Start engine.
2. Listen to each fuel injector operating sound.
OK or NG
OK >> GO TO 8.
NG >> Perform trouble diagnosis for FUEL INJECTOR, refer to
EC-608
.
8.CHECK FUEL INJECTOR
1. Remove fuel injector assembly. Refer to EM-31
.
Keep fuel hose and all fuel injectors connected to fuel injector gallery.
2. Confirm that the engine is cooled down and there are no fire hazards near the vehicle.
3. Disconnect all fuel injector harness connectors.
4. Disconnect all ignition coil harness connectors.3.0 - 9.0 g·m/sec: at idling
9.0 - 28.0 g·m/sec: at 2,500 rpm
3.0 - 9.0 g·m/sec: at idling
9.0 - 28.0 g·m/sec: at 2,500 rpm
PBIB0133E
Clicking noise should be heard.
PBIB1986E
Page 1410 of 3061
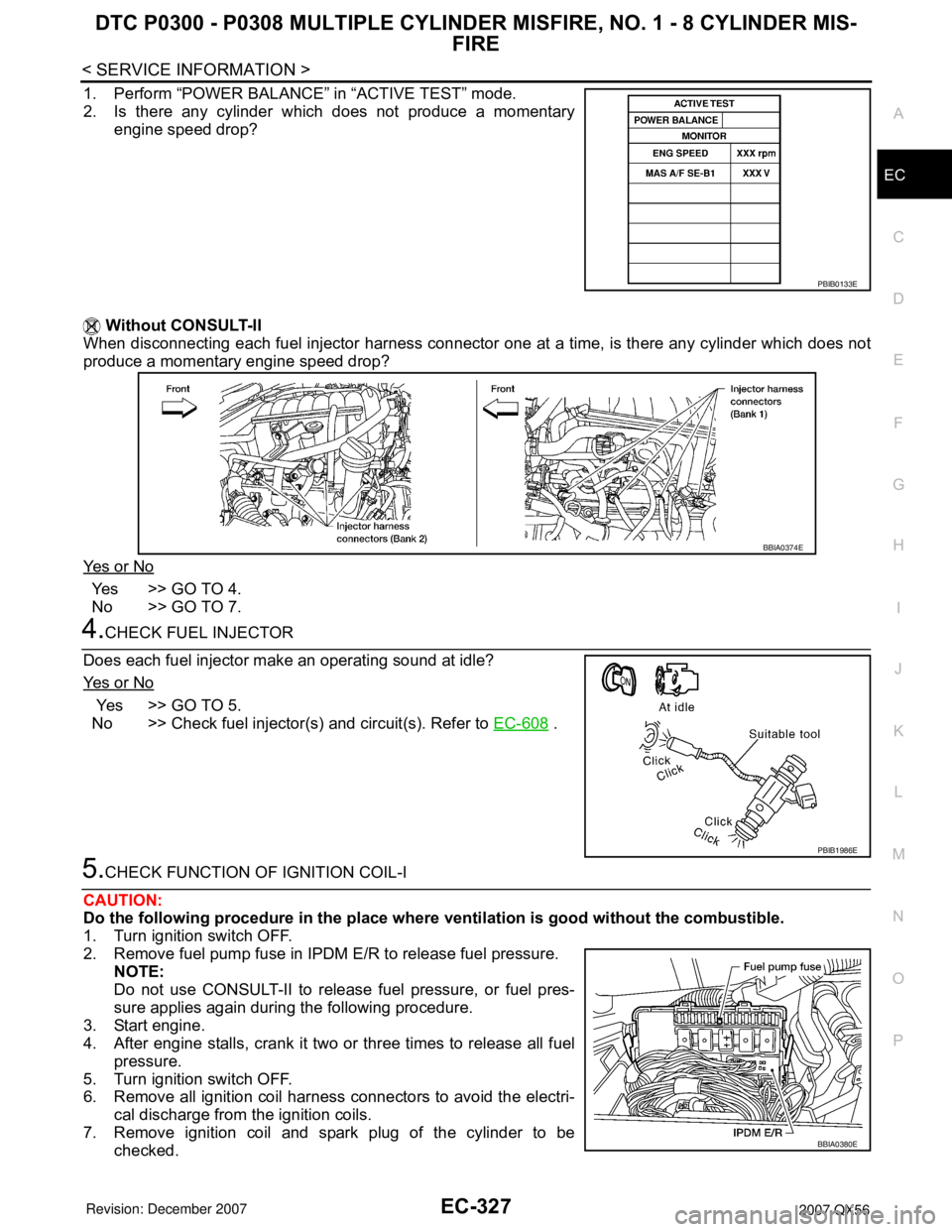
DTC P0300 - P0308 MULTIPLE CYLINDER MISFIRE, NO. 1 - 8 CYLINDER MIS-
FIRE
EC-327
< SERVICE INFORMATION >
C
D
E
F
G
H
I
J
K
L
MA
EC
N
P O
1. Perform “POWER BALANCE” in “ACTIVE TEST” mode.
2. Is there any cylinder which does not produce a momentary
engine speed drop?
Without CONSULT-II
When disconnecting each fuel injector harness connector one at a time, is there any cylinder which does not
produce a momentary engine speed drop?
Ye s o r N o
Yes >> GO TO 4.
No >> GO TO 7.
4.CHECK FUEL INJECTOR
Does each fuel injector make an operating sound at idle?
Ye s o r N o
Yes >> GO TO 5.
No >> Check fuel injector(s) and circuit(s). Refer to EC-608
.
5.CHECK FUNCTION OF IGNITION COIL-I
CAUTION:
Do the following procedure in the place where ventilation is good without the combustible.
1. Turn ignition switch OFF.
2. Remove fuel pump fuse in IPDM E/R to release fuel pressure.
NOTE:
Do not use CONSULT-II to release fuel pressure, or fuel pres-
sure applies again during the following procedure.
3. Start engine.
4. After engine stalls, crank it two or three times to release all fuel
pressure.
5. Turn ignition switch OFF.
6. Remove all ignition coil harness connectors to avoid the electri-
cal discharge from the ignition coils.
7. Remove ignition coil and spark plug of the cylinder to be
checked.
PBIB0133E
BBIA0374E
PBIB1986E
BBIA0380E
Page 1411 of 3061
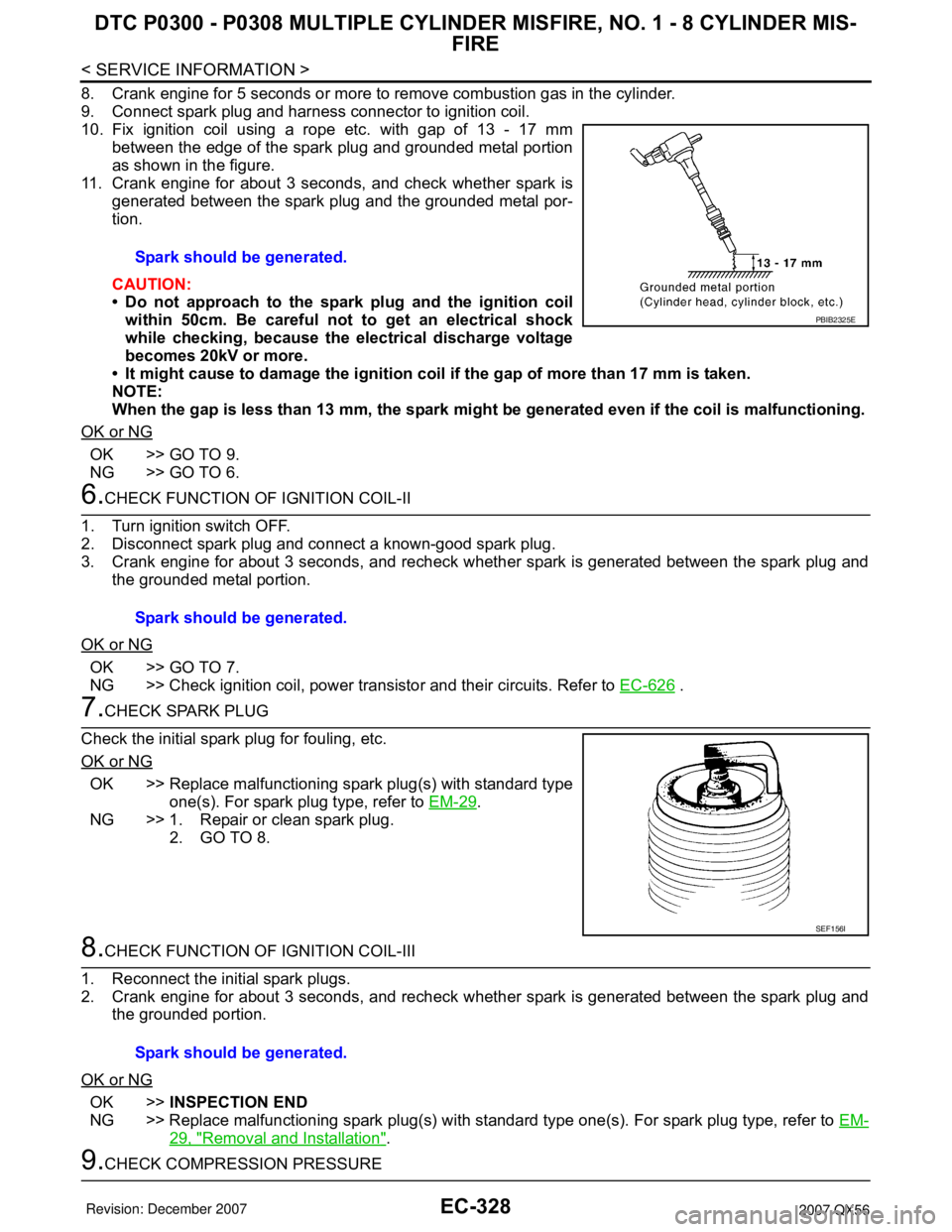
EC-328
< SERVICE INFORMATION >
DTC P0300 - P0308 MULTIPLE CYLINDER MISFIRE, NO. 1 - 8 CYLINDER MIS-
FIRE
8. Crank engine for 5 seconds or more to remove combustion gas in the cylinder.
9. Connect spark plug and harness connector to ignition coil.
10. Fix ignition coil using a rope etc. with gap of 13 - 17 mm
between the edge of the spark plug and grounded metal portion
as shown in the figure.
11. Crank engine for about 3 seconds, and check whether spark is
generated between the spark plug and the grounded metal por-
tion.
CAUTION:
• Do not approach to the spark plug and the ignition coil
within 50cm. Be careful not to get an electrical shock
while checking, because the electrical discharge voltage
becomes 20kV or more.
• It might cause to damage the ignition coil if the gap of more than 17 mm is taken.
NOTE:
When the gap is less than 13 mm, the spark might be generated even if the coil is malfunctioning.
OK or NG
OK >> GO TO 9.
NG >> GO TO 6.
6.CHECK FUNCTION OF IGNITION COIL-II
1. Turn ignition switch OFF.
2. Disconnect spark plug and connect a known-good spark plug.
3. Crank engine for about 3 seconds, and recheck whether spark is generated between the spark plug and
the grounded metal portion.
OK or NG
OK >> GO TO 7.
NG >> Check ignition coil, power transistor and their circuits. Refer to EC-626
.
7.CHECK SPARK PLUG
Check the initial spark plug for fouling, etc.
OK or NG
OK >> Replace malfunctioning spark plug(s) with standard type
one(s). For spark plug type, refer to EM-29
.
NG >> 1. Repair or clean spark plug.
2. GO TO 8.
8.CHECK FUNCTION OF IGNITION COIL-III
1. Reconnect the initial spark plugs.
2. Crank engine for about 3 seconds, and recheck whether spark is generated between the spark plug and
the grounded portion.
OK or NG
OK >>INSPECTION END
NG >> Replace malfunctioning spark plug(s) with standard type one(s). For spark plug type, refer to EM-
29, "Removal and Installation".
9.CHECK COMPRESSION PRESSURESpark should be generated.
PBIB2325E
Spark should be generated.
SEF156I
Spark should be generated.
Page 1431 of 3061
EC-348
< SERVICE INFORMATION >
DTC P0340 CMP SENSOR (PHASE)
5. Check resistance as shown in the figure.
Removal and InstallationINFOID:0000000003531846
CAMSHAFT POSITION SENSOR (PHASE)
Removal
1. Remove engine room cover using power tool. Refer to EM-12, "Removal and Installation".
2. Remove air duct and resonator assembly. Refer to EM-15, "
Removal and Installation".
3. Disconnect camshaft position sensor connector.
4. Remove camshaft position sensor (2) from intake valve timing
control solenoid valve cover (LH) (1).
Installation
Installation is in the reverse order of removal.
CAUTION:
Replace the O-ring (3) of the camshaft position sensor with a new one, then lubricate o-ring with
engine oil before installing.
Terminal No. (Polarity) Resistance Ω [at 25°C (77°F)]
3(+) - 1 (-)
Except 0 or ∞ 2 (+) - 1 (-)
3 (+) - 2 (-)
PBIB0564E
LBIA0479E
Camshaft position sensor : 9.6 N·m (0.98 kg-m, 5 in-bl)