Page 83 of 4500
NG: REPLACE REAR SPEED SENSOR
OK: REPLACE ABS & TRACTION ACTUATOR ASSY (SEE REPLACEMENT
)
CIRCUIT DESCRIPTION
<0037004b004c0056000300560052004f004800510052004c00470003005700580055005100560003005200510003005a004b0048005100030056004c004a00510044004f0056000300440055004800030055004800460048004c0059004800470003004900
550052005000030057004b0048000300280026003800030044[nd controls the pressure acting on the wheel
c
ylinders to control the braking force.
Page 102 of 4500
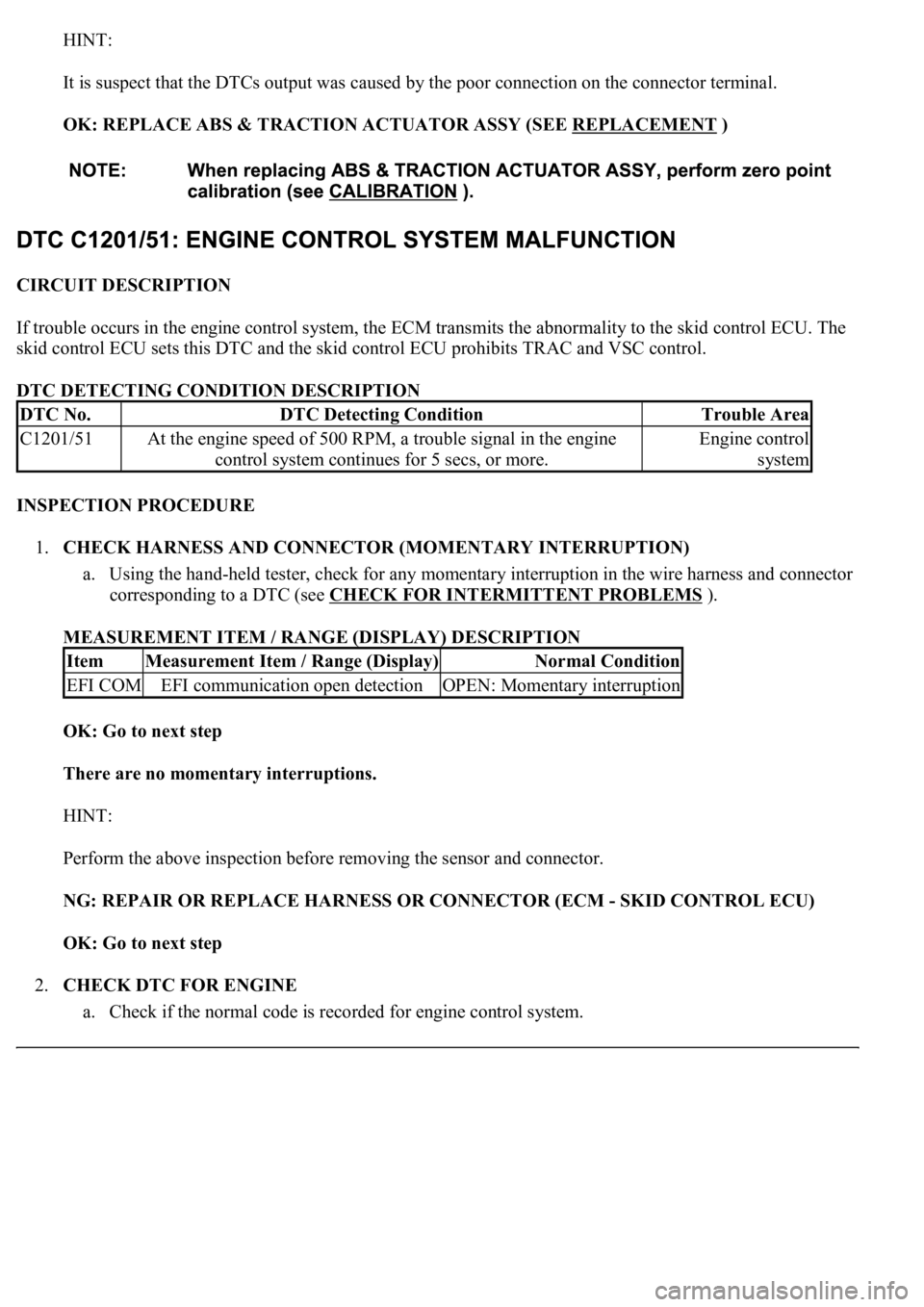
HINT:
It is suspect that the DTCs output was caused by the poor connection on the connector terminal.
OK: REPLACE ABS & TRACTION ACTUATOR ASSY (SEE REPLACEMENT
)
CIRCUIT DESCRIPTION
If trouble occurs in the engine control system, the ECM transmits the abnormality to the skid control ECU. The
skid control ECU sets this DTC and the skid control ECU prohibits TRAC and VSC control.
DTC DETECTING CONDITION DESCRIPTION
INSPECTION PROCEDURE
1.CHECK HARNESS AND CONNECTOR (MOMENTARY INTERRUPTION)
a. Using the hand-held tester, check for any momentary interruption in the wire harness and connector
corresponding to a DTC (see CHECK FOR INTERMITTENT PROBLEMS
).
MEASUREMENT ITEM / RANGE (DISPLAY) DESCRIPTION
OK: Go to next step
There are no momentary interruptions.
HINT:
Perform the above inspection before removing the sensor and connector.
NG: REPAIR OR REPLACE HARNESS OR CONNECTOR (ECM - SKID CONTROL ECU)
OK: Go to next step
2.CHECK DTC FOR ENGINE
a. Check if the normal code is recorded for en
gine control system.
DTC No.DTC Detecting ConditionTrouble Area
C1201/51At the engine speed of 500 RPM, a trouble signal in the engine
control system continues for 5 secs, or more.Engine control
system
ItemMeasurement Item / Range (Display)Normal Condition
EFI COMEFI communication open detectionOPEN: Momentary interruption
Page 103 of 4500
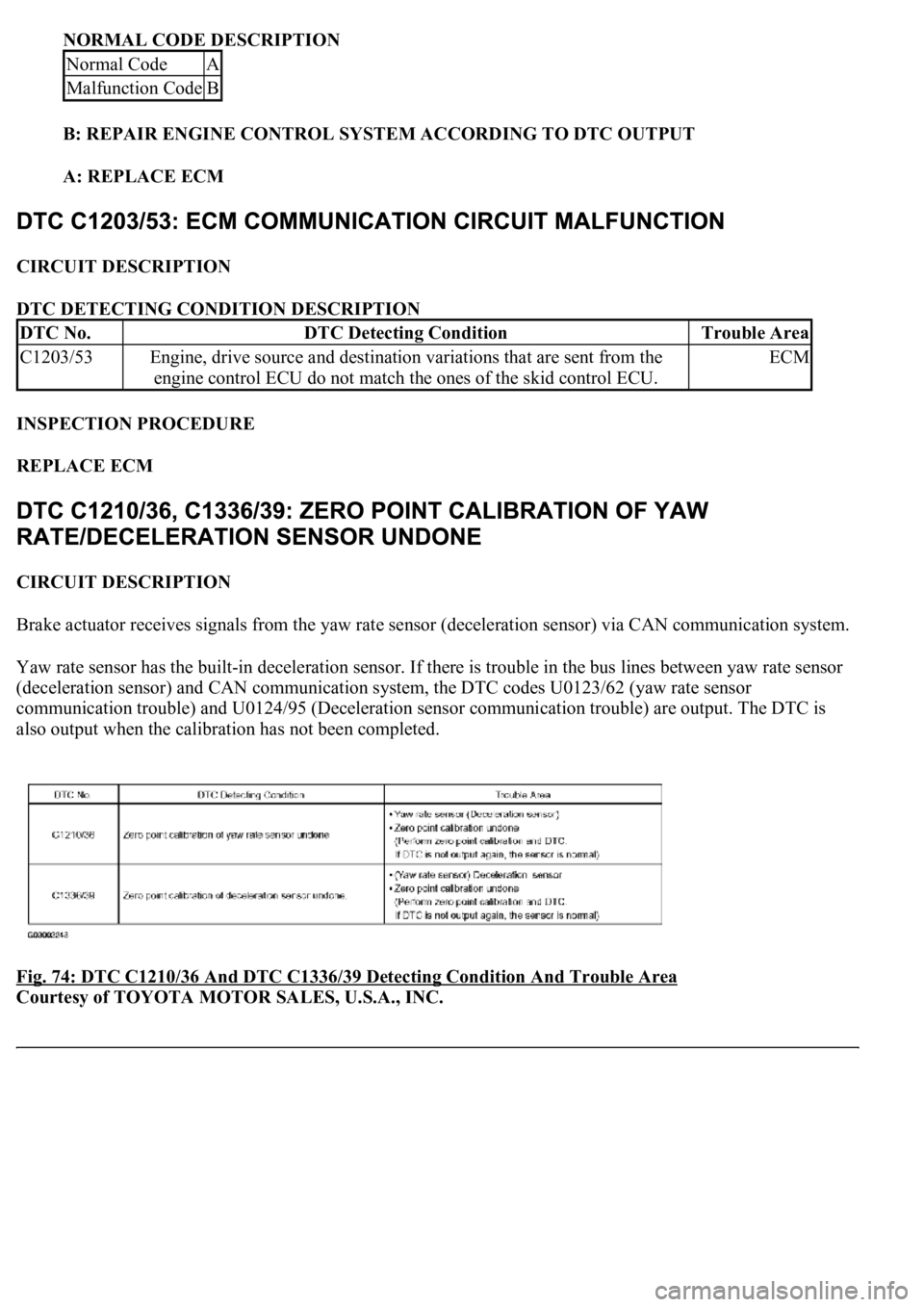
NORMAL CODE DESCRIPTION
B: REPAIR ENGINE CONTROL SYSTEM ACCORDING TO DTC OUTPUT
A: REPLACE ECM
CIRCUIT DESCRIPTION
DTC DETECTING CONDITION DESCRIPTION
INSPECTION PROCEDURE
REPLACE ECM
CIRCUIT DESCRIPTION
Brake actuator receives signals from the yaw rate sensor (deceleration sensor) via CAN communication system.
Yaw rate sensor has the built-in deceleration sensor. If there is trouble in the bus lines between yaw rate sensor
(deceleration sensor) and CAN communication system, the DTC codes U0123/62 (yaw rate sensor
communication trouble) and U0124/95 (Deceleration sensor communication trouble) are output. The DTC is
also output when the calibration has not been completed.
Fig. 74: DTC C1210/36 And DTC C1336/39 Detecting Condition And Trouble Area
Courtesy of TOYOTA MOTOR SALES, U.S.A., INC.
Normal CodeA
Malfunction CodeB
DTC No.DTC Detecting ConditionTrouble Area
C1203/53Engine, drive source and destination variations that are sent from the
engine control ECU do not match the ones of the skid control ECU.ECM
Page 104 of 4500
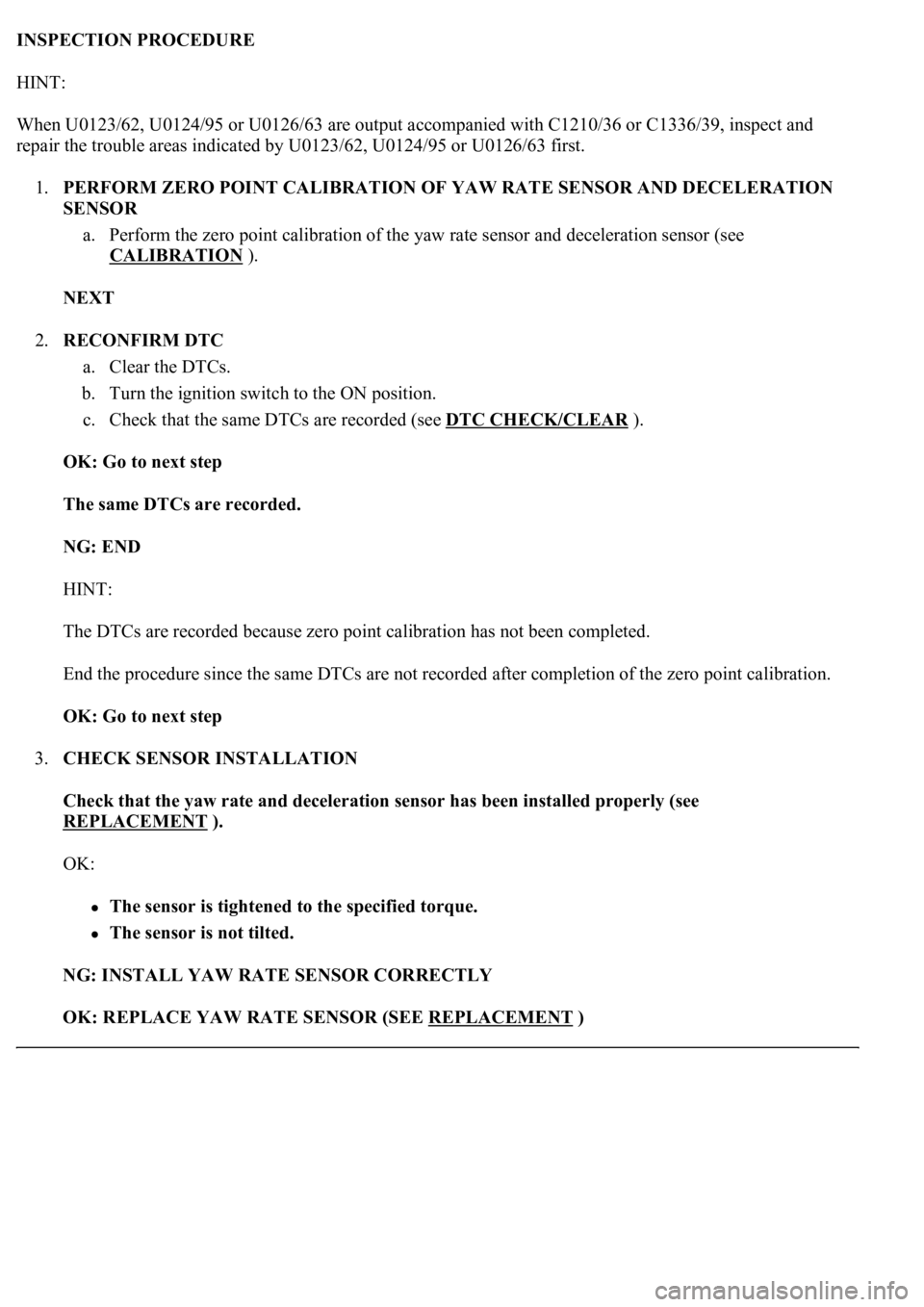
INSPECTION PROCEDURE
HINT:
<003a004b00480051000300380013001400150016001200190015000f0003003800130014001500170012001c001800030052005500030038001300140015001900120019001600030044005500480003005200580057005300580057000300440046004600
520050005300440051004c004800470003005a004c0057004b[ C1210/36 or C1336/39, inspect and
repair the trouble areas indicated by U0123/62, U0124/95 or U0126/63 first.
1.PERFORM ZERO POINT CALIBRATION OF YAW RATE SENSOR AND DECELERATION
SENSOR
a. Perform the zero point calibration of the yaw rate sensor and deceleration sensor (see
CALIBRATION
).
NEXT
2.RECONFIRM DTC
a. Clear the DTCs.
b. Turn the ignition switch to the ON position.
c. Check that the same DTCs are recorded (see DTC CHECK/CLEAR
).
OK: Go to next step
The same DTCs are recorded.
NG: END
HINT:
The DTCs are recorded because zero point calibration has not been completed.
End the procedure since the same DTCs are not recorded after completion of the zero point calibration.
OK: Go to next step
3.CHECK SENSOR INSTALLATION
Check that the yaw rate and deceleration sensor has been installed properly (see
REPLACEMENT
).
OK:
The sensor is tightened to the specified torque.
The sensor is not tilted.
NG: INSTALL YAW RATE SENSOR CORRECTLY
OK: REPLACE YAW RATE SENSOR (SEE REPLACEMENT
)
Page 105 of 4500
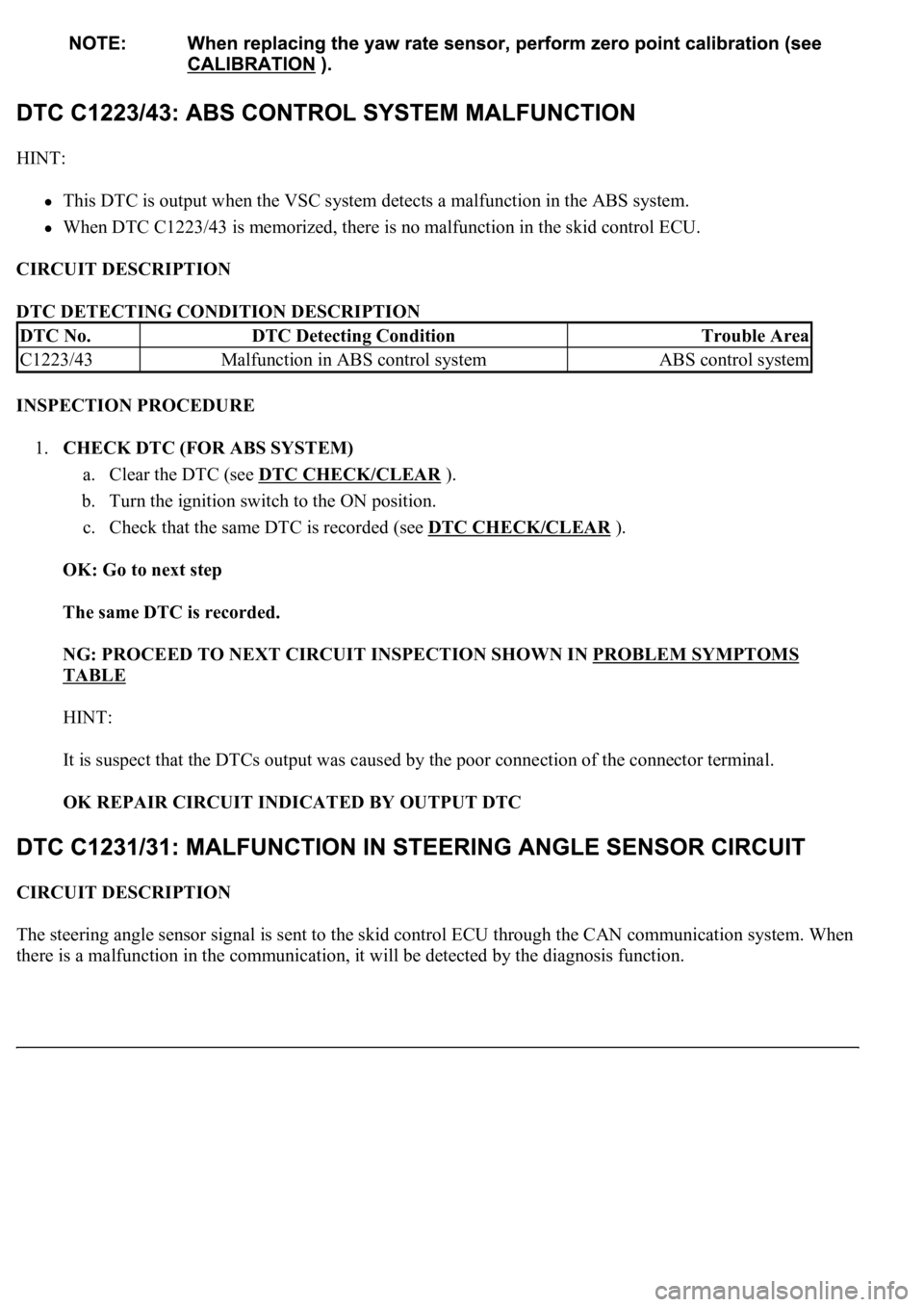
HINT:
This DTC is output when the VSC system detects a malfunction in the ABS system.
When DTC C1223/43 is memorized, there is no malfunction in the skid control ECU.
CIRCUIT DESCRIPTION
DTC DETECTING CONDITION DESCRIPTION
INSPECTION PROCEDURE
1.CHECK DTC (FOR ABS SYSTEM)
a. Clear the DTC (see DTC CHECK/CLEAR
).
b. Turn the ignition switch to the ON position.
c. Check that the same DTC is recorded (see DTC CHECK/CLEAR
).
OK: Go to next step
The same DTC is recorded.
NG: PROCEED TO NEXT CIRCUIT INSPECTION SHOWN IN PROBLEM SYMPTOMS
TABLE
HINT:
It is suspect that the DTCs output was caused by the poor connection of the connector terminal.
OK REPAIR CIRCUIT INDICATED BY OUTPUT DTC
CIRCUIT DESCRIPTION
The steering angle sensor signal is sent to the skid control ECU through the CAN communication system. When
there is a malfunction in the communication, it will be detected by the diagnosis function.
DTC No.DTC Detecting ConditionTrouble Area
C1223/43Malfunction in ABS control systemABS control system
Page 107 of 4500
Fig. 76: Steering Angle Sensor Wiring Diagram
Courtesy of TOYOTA MOTOR SALES, U.S.A., INC.
INSPECTION PROCEDURE
HINT:
Page 108 of 4500
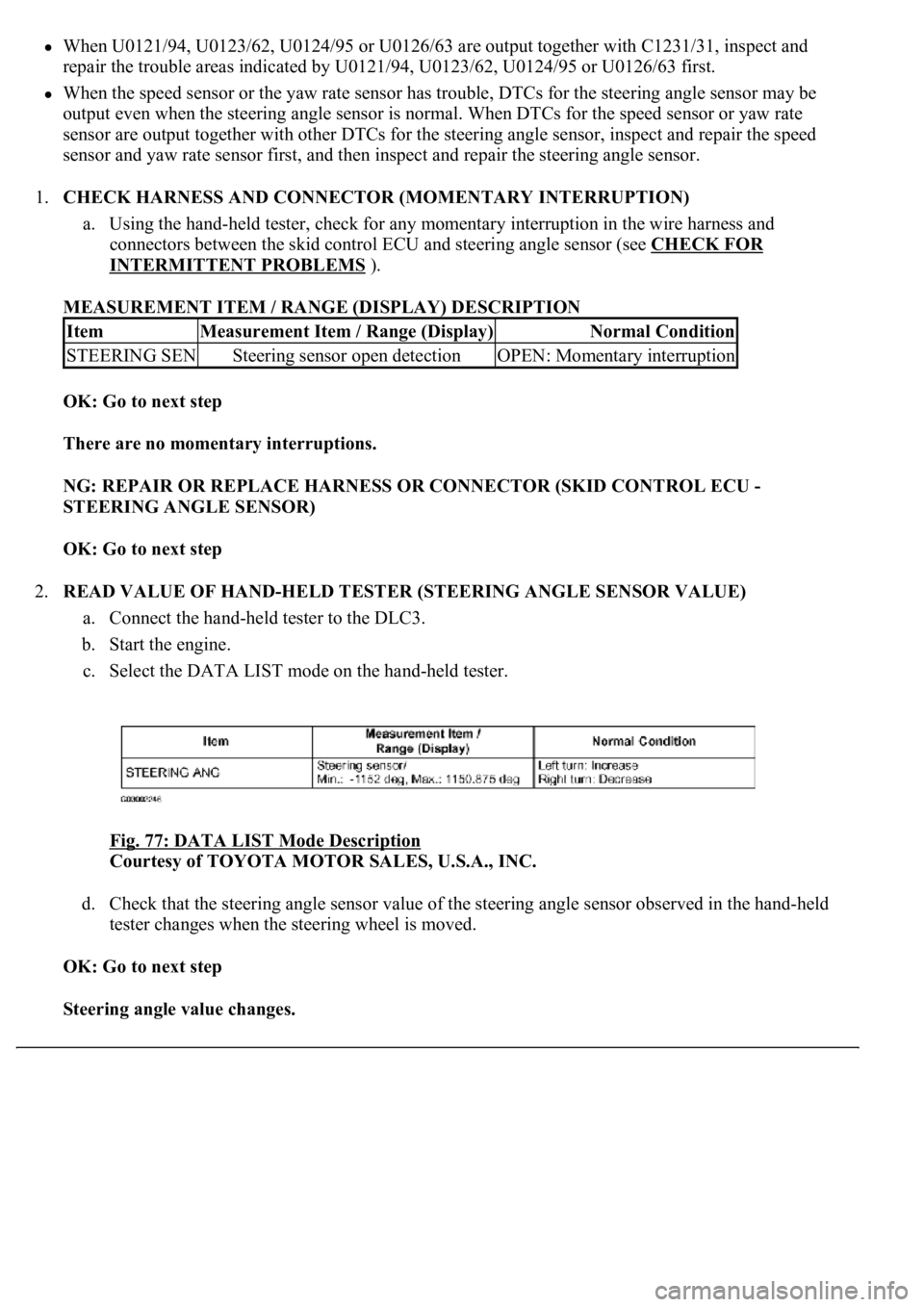
When U0121/94, U0123/62, U0124/95 or U0126/63 are output together with C1231/31, inspect and
repair the trouble areas indicated by U0121/94, U0123/62, U0124/95 or U0126/63 first.
When the speed sensor or the yaw rate sensor has trouble, DTCs for the steering angle sensor may be
output even when the steering angle sensor is normal. When DTCs for the speed sensor or yaw rate
sensor are output together with other DTCs for the steering angle sensor, inspect and repair the speed
sensor and yaw rate sensor first, and then inspect and repair the steering angle sensor.
1.CHECK HARNESS AND CONNECTOR (MOMENTARY INTERRUPTION)
a. Using the hand-held tester, check for any momentary interruption in the wire harness and
connectors between the skid control ECU and steering angle sensor (see CHECK FOR
INTERMITTENT PROBLEMS ).
MEASUREMENT ITEM / RANGE (DISPLAY) DESCRIPTION
OK: Go to next step
There are no momentary interruptions.
NG: REPAIR OR REPLACE HARNESS OR CONNECTOR (SKID CONTROL ECU -
STEERING ANGLE SENSOR)
OK: Go to next step
2.READ VALUE OF HAND-HELD TESTER (STEERING ANGLE SENSOR VALUE)
a. Connect the hand-held tester to the DLC3.
b. Start the engine.
c. Select the DATA LIST mode on the hand-held tester.
Fig. 77: DATA LIST Mode Description
Courtesy of TOYOTA MOTOR SALES, U.S.A., INC.
d. Check that the steering angle sensor value of the steering angle sensor observed in the hand-held
tester changes when the steering wheel is moved.
OK: Go to next step
Steering angle value changes.
ItemMeasurement Item / Range (Display)Normal Condition
STEERING SENSteering sensor open detectionOPEN: Momentary interruption
Page 109 of 4500
NG: Go to step 3
OK: REPLACE ABS & TRACTION ACTUATOR ASSY (SEE REPLACEMENT
)
3.CHECK TERMINAL VOLTAGE (STEERING ANGLE SENSOR CONNECTOR)
a. Remove the steering wheel and the column lower cover.
b. Disconnect the steering angle sensor connector.
c. Turn the ignition switch to the ON position.
d. Measure the voltage according to the value (s) in the table below.
Standard:
TESTER CONNECTION SPECIFIED CONDITION
e. Measure the voltage according to the value (s) in the table below.
Standard:
TESTER CONNECTION SPECIFIED CONDITION
Tester ConnectionSpecified Condition
S16-1 (IG1) - S16-2 (ESS)10 to 14V
Tester ConnectionSpecified Condition
S16-3 (BAT) -S16-2 (ESS)10 to 14V