Page 1777 of 2199
PLANETARY GEARTRAIN
DESCRIPTION
The planetary geartrain is located behind the 4C
retainer/bulkhead, toward the rear of the transmis-
sion. The planetary geartrain consists of three pri-
mary assemblies:
²Reaction (Fig. 102).
²Reverse (Fig. 103).
²Input (Fig. 103).
Fig. 102 Reaction Planetary Geartrain
1 - BEARING NUMBER 8 5 - BEARING NUMBER 7
2 - BEARING NUMBER 9 6 - THRUST PLATE (SELECT)
3 - REACTION PLANETARY CARRIER 7 - BEARING NUMBER 6
4 - REACTION SUN GEAR 8 - REACTION ANNULUS
21 - 258 AUTOMATIC TRANSMISSION - 545RFEWJ
Page 1778 of 2199
Fig. 103 Reverse/Input Planetary Geartrain
1 - SNAP-RING 5 - INPUT PLANETARY CARRIER
2 - BEARING NUMBER 10 6 - INPUT SUN GEAR
3 - BEARING NUMBER 11 7 - REVERSE PLANETARY CARRIER
4 - INPUT ANNULUS
WJAUTOMATIC TRANSMISSION - 545RFE 21 - 259
PLANETARY GEARTRAIN (Continued)
Page 1779 of 2199
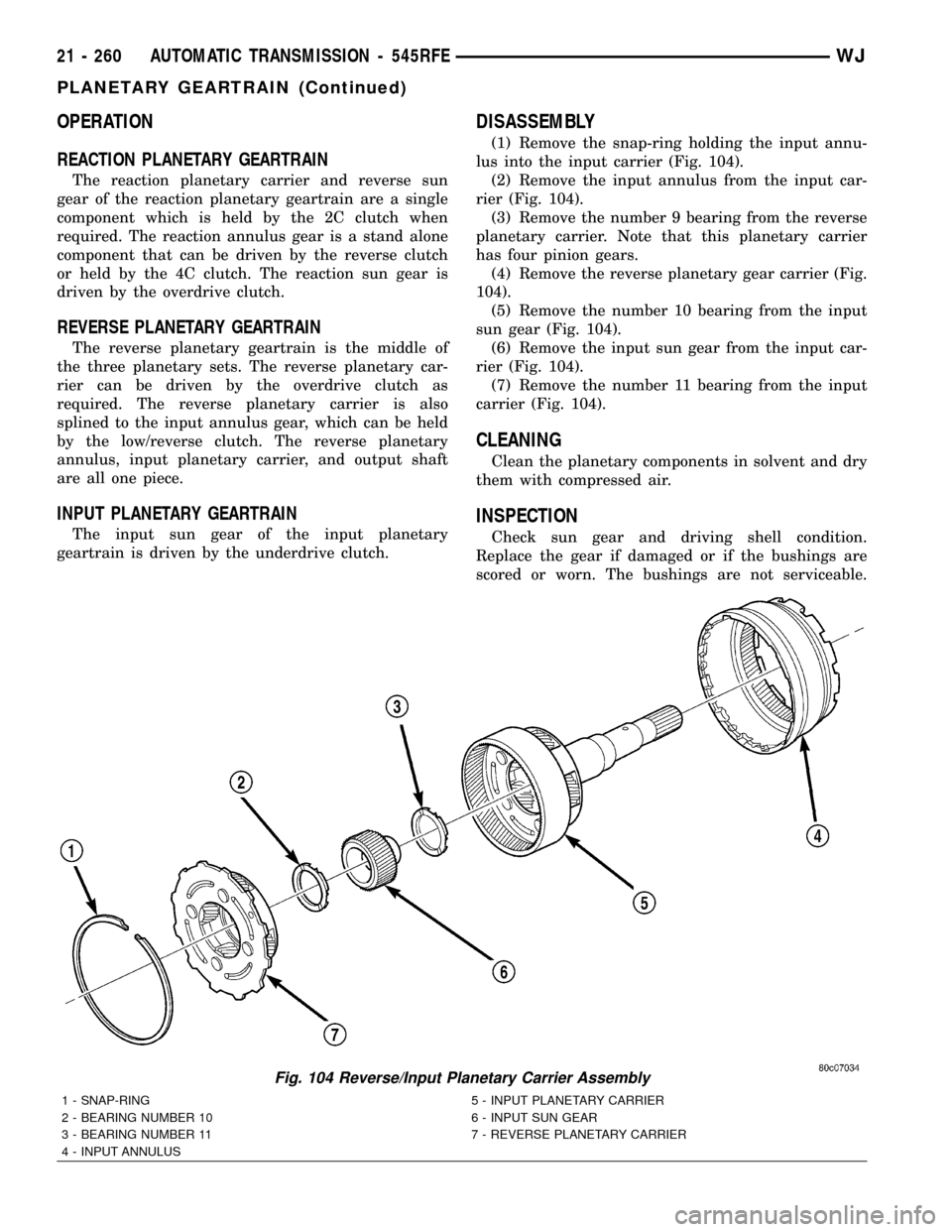
OPERATION
REACTION PLANETARY GEARTRAIN
The reaction planetary carrier and reverse sun
gear of the reaction planetary geartrain are a single
component which is held by the 2C clutch when
required. The reaction annulus gear is a stand alone
component that can be driven by the reverse clutch
or held by the 4C clutch. The reaction sun gear is
driven by the overdrive clutch.
REVERSE PLANETARY GEARTRAIN
The reverse planetary geartrain is the middle of
the three planetary sets. The reverse planetary car-
rier can be driven by the overdrive clutch as
required. The reverse planetary carrier is also
splined to the input annulus gear, which can be held
by the low/reverse clutch. The reverse planetary
annulus, input planetary carrier, and output shaft
are all one piece.
INPUT PLANETARY GEARTRAIN
The input sun gear of the input planetary
geartrain is driven by the underdrive clutch.
DISASSEMBLY
(1) Remove the snap-ring holding the input annu-
lus into the input carrier (Fig. 104).
(2) Remove the input annulus from the input car-
rier (Fig. 104).
(3) Remove the number 9 bearing from the reverse
planetary carrier. Note that this planetary carrier
has four pinion gears.
(4) Remove the reverse planetary gear carrier (Fig.
104).
(5) Remove the number 10 bearing from the input
sun gear (Fig. 104).
(6) Remove the input sun gear from the input car-
rier (Fig. 104).
(7) Remove the number 11 bearing from the input
carrier (Fig. 104).
CLEANING
Clean the planetary components in solvent and dry
them with compressed air.
INSPECTION
Check sun gear and driving shell condition.
Replace the gear if damaged or if the bushings are
scored or worn. The bushings are not serviceable.
Fig. 104 Reverse/Input Planetary Carrier Assembly
1 - SNAP-RING 5 - INPUT PLANETARY CARRIER
2 - BEARING NUMBER 10 6 - INPUT SUN GEAR
3 - BEARING NUMBER 11 7 - REVERSE PLANETARY CARRIER
4 - INPUT ANNULUS
21 - 260 AUTOMATIC TRANSMISSION - 545RFEWJ
PLANETARY GEARTRAIN (Continued)
Page 1780 of 2199
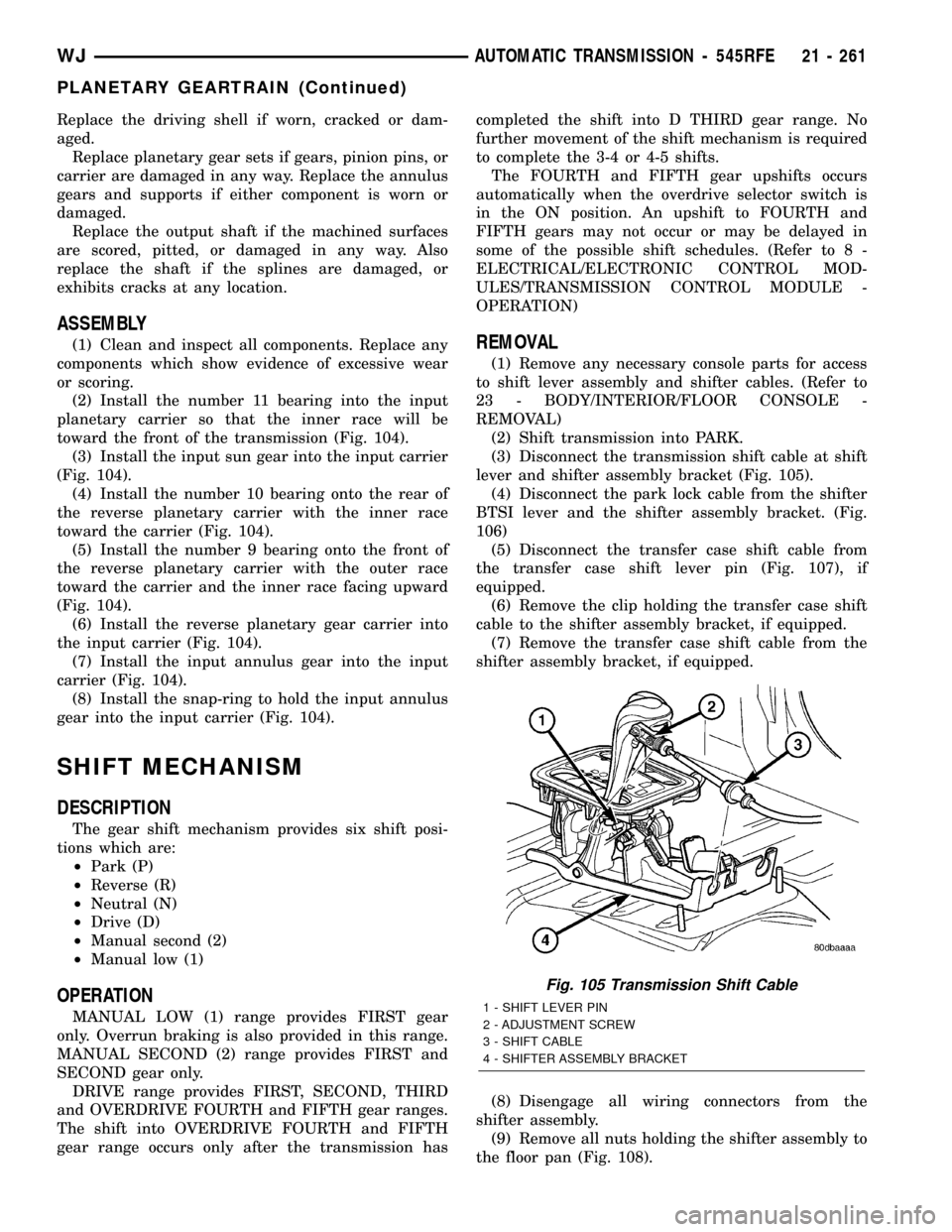
Replace the driving shell if worn, cracked or dam-
aged.
Replace planetary gear sets if gears, pinion pins, or
carrier are damaged in any way. Replace the annulus
gears and supports if either component is worn or
damaged.
Replace the output shaft if the machined surfaces
are scored, pitted, or damaged in any way. Also
replace the shaft if the splines are damaged, or
exhibits cracks at any location.
ASSEMBLY
(1) Clean and inspect all components. Replace any
components which show evidence of excessive wear
or scoring.
(2) Install the number 11 bearing into the input
planetary carrier so that the inner race will be
toward the front of the transmission (Fig. 104).
(3) Install the input sun gear into the input carrier
(Fig. 104).
(4) Install the number 10 bearing onto the rear of
the reverse planetary carrier with the inner race
toward the carrier (Fig. 104).
(5) Install the number 9 bearing onto the front of
the reverse planetary carrier with the outer race
toward the carrier and the inner race facing upward
(Fig. 104).
(6) Install the reverse planetary gear carrier into
the input carrier (Fig. 104).
(7) Install the input annulus gear into the input
carrier (Fig. 104).
(8) Install the snap-ring to hold the input annulus
gear into the input carrier (Fig. 104).
SHIFT MECHANISM
DESCRIPTION
The gear shift mechanism provides six shift posi-
tions which are:
²Park (P)
²Reverse (R)
²Neutral (N)
²Drive (D)
²Manual second (2)
²Manual low (1)
OPERATION
MANUAL LOW (1) range provides FIRST gear
only. Overrun braking is also provided in this range.
MANUAL SECOND (2) range provides FIRST and
SECOND gear only.
DRIVE range provides FIRST, SECOND, THIRD
and OVERDRIVE FOURTH and FIFTH gear ranges.
The shift into OVERDRIVE FOURTH and FIFTH
gear range occurs only after the transmission hascompleted the shift into D THIRD gear range. No
further movement of the shift mechanism is required
to complete the 3-4 or 4-5 shifts.
The FOURTH and FIFTH gear upshifts occurs
automatically when the overdrive selector switch is
in the ON position. An upshift to FOURTH and
FIFTH gears may not occur or may be delayed in
some of the possible shift schedules. (Refer to 8 -
ELECTRICAL/ELECTRONIC CONTROL MOD-
ULES/TRANSMISSION CONTROL MODULE -
OPERATION)
REMOVAL
(1) Remove any necessary console parts for access
to shift lever assembly and shifter cables. (Refer to
23 - BODY/INTERIOR/FLOOR CONSOLE -
REMOVAL)
(2) Shift transmission into PARK.
(3) Disconnect the transmission shift cable at shift
lever and shifter assembly bracket (Fig. 105).
(4) Disconnect the park lock cable from the shifter
BTSI lever and the shifter assembly bracket. (Fig.
106)
(5) Disconnect the transfer case shift cable from
the transfer case shift lever pin (Fig. 107), if
equipped.
(6) Remove the clip holding the transfer case shift
cable to the shifter assembly bracket, if equipped.
(7) Remove the transfer case shift cable from the
shifter assembly bracket, if equipped.
(8) Disengage all wiring connectors from the
shifter assembly.
(9) Remove all nuts holding the shifter assembly to
the floor pan (Fig. 108).
Fig. 105 Transmission Shift Cable
1 - SHIFT LEVER PIN
2 - ADJUSTMENT SCREW
3 - SHIFT CABLE
4 - SHIFTER ASSEMBLY BRACKET
WJAUTOMATIC TRANSMISSION - 545RFE 21 - 261
PLANETARY GEARTRAIN (Continued)
Page 1781 of 2199
(10) Remove the shifter assembly from the vehicle.
Fig. 106 Brake Transmission Interlock Cable
1 - SHIFT MECHANISM 4 - STEERING COLUMN ASSEMBLY
2 - SHIFTER BTSI LEVER 5 - INTERLOCK CABLE
3 - ADJUSTMENT CLIP
Fig. 107 Transfer Case Shift Cable
1 - CLIP
2 - SHIFTER
3 - TRANSFER CASE SHIFT LEVER PIN
4 - TRANSFER CASE SHIFT CABLE
Fig. 108 Shifter Assembly
1 - FLOOR PAN
2 - SHIFTER ASSEMBLY
21 - 262 AUTOMATIC TRANSMISSION - 545RFEWJ
SHIFT MECHANISM (Continued)
Page 1782 of 2199
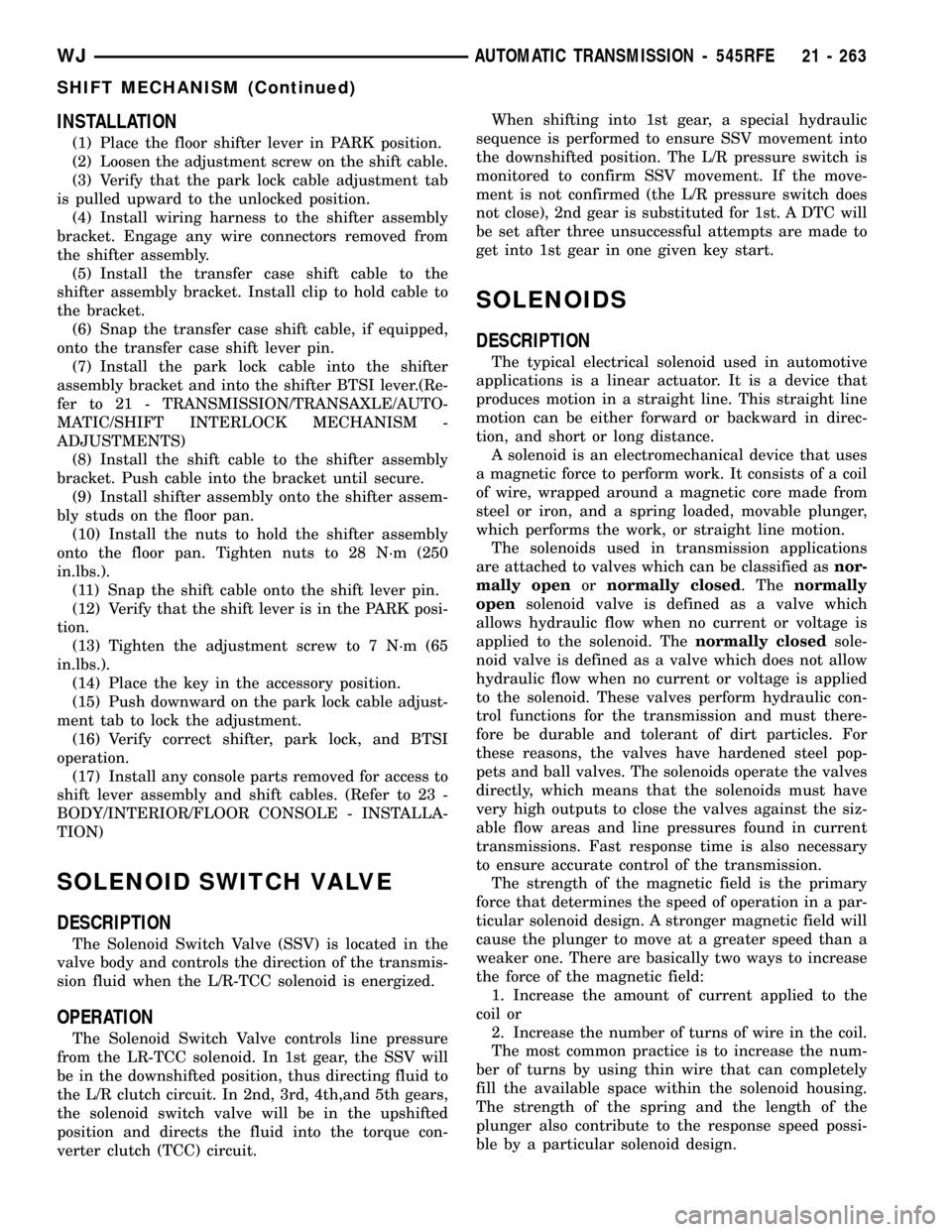
INSTALLATION
(1) Place the floor shifter lever in PARK position.
(2) Loosen the adjustment screw on the shift cable.
(3) Verify that the park lock cable adjustment tab
is pulled upward to the unlocked position.
(4) Install wiring harness to the shifter assembly
bracket. Engage any wire connectors removed from
the shifter assembly.
(5) Install the transfer case shift cable to the
shifter assembly bracket. Install clip to hold cable to
the bracket.
(6) Snap the transfer case shift cable, if equipped,
onto the transfer case shift lever pin.
(7) Install the park lock cable into the shifter
assembly bracket and into the shifter BTSI lever.(Re-
fer to 21 - TRANSMISSION/TRANSAXLE/AUTO-
MATIC/SHIFT INTERLOCK MECHANISM -
ADJUSTMENTS)
(8) Install the shift cable to the shifter assembly
bracket. Push cable into the bracket until secure.
(9) Install shifter assembly onto the shifter assem-
bly studs on the floor pan.
(10) Install the nuts to hold the shifter assembly
onto the floor pan. Tighten nuts to 28 N´m (250
in.lbs.).
(11) Snap the shift cable onto the shift lever pin.
(12) Verify that the shift lever is in the PARK posi-
tion.
(13) Tighten the adjustment screw to 7 N´m (65
in.lbs.).
(14) Place the key in the accessory position.
(15) Push downward on the park lock cable adjust-
ment tab to lock the adjustment.
(16) Verify correct shifter, park lock, and BTSI
operation.
(17) Install any console parts removed for access to
shift lever assembly and shift cables. (Refer to 23 -
BODY/INTERIOR/FLOOR CONSOLE - INSTALLA-
TION)
SOLENOID SWITCH VALVE
DESCRIPTION
The Solenoid Switch Valve (SSV) is located in the
valve body and controls the direction of the transmis-
sion fluid when the L/R-TCC solenoid is energized.
OPERATION
The Solenoid Switch Valve controls line pressure
from the LR-TCC solenoid. In 1st gear, the SSV will
be in the downshifted position, thus directing fluid to
the L/R clutch circuit. In 2nd, 3rd, 4th,and 5th gears,
the solenoid switch valve will be in the upshifted
position and directs the fluid into the torque con-
verter clutch (TCC) circuit.When shifting into 1st gear, a special hydraulic
sequence is performed to ensure SSV movement into
the downshifted position. The L/R pressure switch is
monitored to confirm SSV movement. If the move-
ment is not confirmed (the L/R pressure switch does
not close), 2nd gear is substituted for 1st. A DTC will
be set after three unsuccessful attempts are made to
get into 1st gear in one given key start.
SOLENOIDS
DESCRIPTION
The typical electrical solenoid used in automotive
applications is a linear actuator. It is a device that
produces motion in a straight line. This straight line
motion can be either forward or backward in direc-
tion, and short or long distance.
A solenoid is an electromechanical device that uses
a magnetic force to perform work. It consists of a coil
of wire, wrapped around a magnetic core made from
steel or iron, and a spring loaded, movable plunger,
which performs the work, or straight line motion.
The solenoids used in transmission applications
are attached to valves which can be classified asnor-
mally openornormally closed. Thenormally
opensolenoid valve is defined as a valve which
allows hydraulic flow when no current or voltage is
applied to the solenoid. Thenormally closedsole-
noid valve is defined as a valve which does not allow
hydraulic flow when no current or voltage is applied
to the solenoid. These valves perform hydraulic con-
trol functions for the transmission and must there-
fore be durable and tolerant of dirt particles. For
these reasons, the valves have hardened steel pop-
pets and ball valves. The solenoids operate the valves
directly, which means that the solenoids must have
very high outputs to close the valves against the siz-
able flow areas and line pressures found in current
transmissions. Fast response time is also necessary
to ensure accurate control of the transmission.
The strength of the magnetic field is the primary
force that determines the speed of operation in a par-
ticular solenoid design. A stronger magnetic field will
cause the plunger to move at a greater speed than a
weaker one. There are basically two ways to increase
the force of the magnetic field:
1. Increase the amount of current applied to the
coil or
2. Increase the number of turns of wire in the coil.
The most common practice is to increase the num-
ber of turns by using thin wire that can completely
fill the available space within the solenoid housing.
The strength of the spring and the length of the
plunger also contribute to the response speed possi-
ble by a particular solenoid design.
WJAUTOMATIC TRANSMISSION - 545RFE 21 - 263
SHIFT MECHANISM (Continued)
Page 1783 of 2199
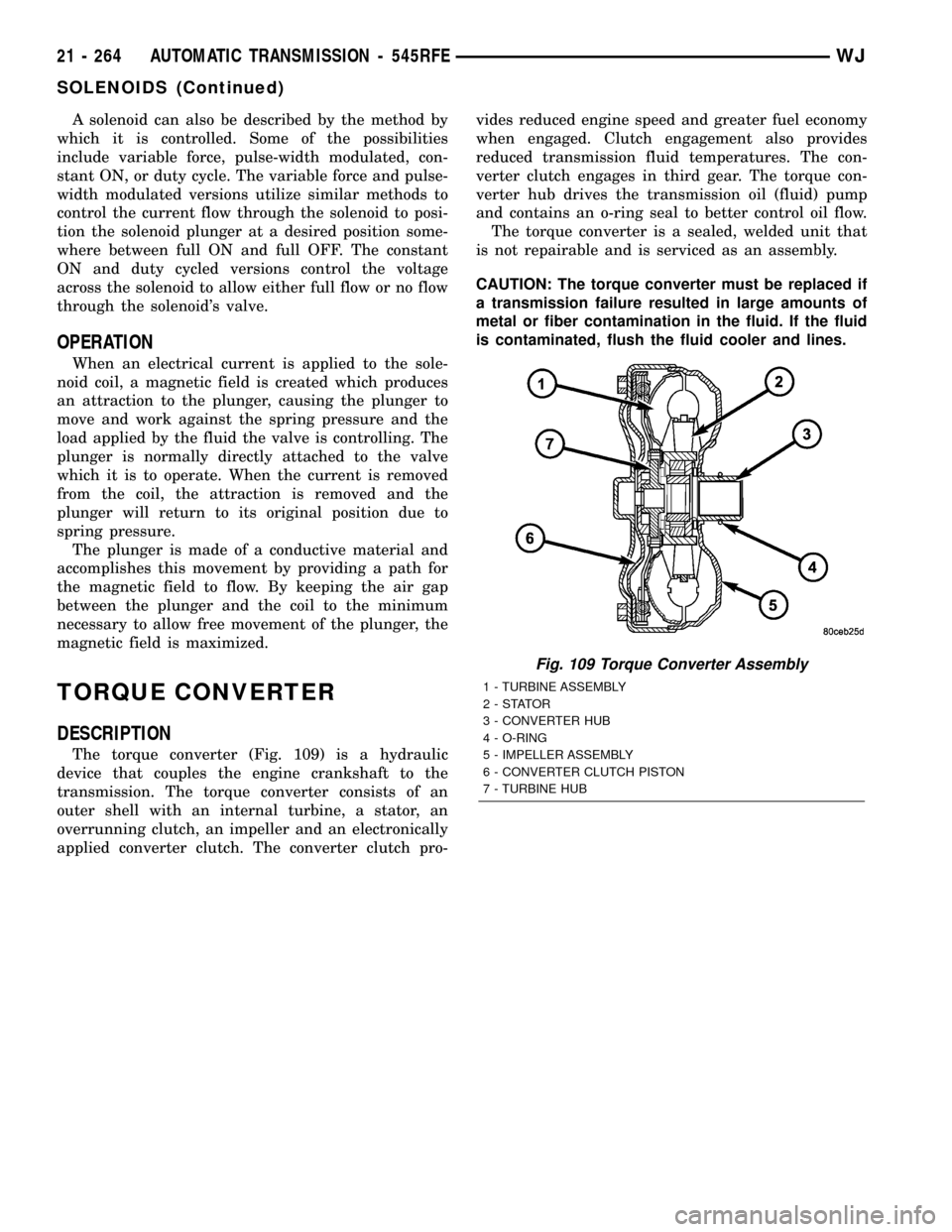
A solenoid can also be described by the method by
which it is controlled. Some of the possibilities
include variable force, pulse-width modulated, con-
stant ON, or duty cycle. The variable force and pulse-
width modulated versions utilize similar methods to
control the current flow through the solenoid to posi-
tion the solenoid plunger at a desired position some-
where between full ON and full OFF. The constant
ON and duty cycled versions control the voltage
across the solenoid to allow either full flow or no flow
through the solenoid's valve.
OPERATION
When an electrical current is applied to the sole-
noid coil, a magnetic field is created which produces
an attraction to the plunger, causing the plunger to
move and work against the spring pressure and the
load applied by the fluid the valve is controlling. The
plunger is normally directly attached to the valve
which it is to operate. When the current is removed
from the coil, the attraction is removed and the
plunger will return to its original position due to
spring pressure.
The plunger is made of a conductive material and
accomplishes this movement by providing a path for
the magnetic field to flow. By keeping the air gap
between the plunger and the coil to the minimum
necessary to allow free movement of the plunger, the
magnetic field is maximized.
TORQUE CONVERTER
DESCRIPTION
The torque converter (Fig. 109) is a hydraulic
device that couples the engine crankshaft to the
transmission. The torque converter consists of an
outer shell with an internal turbine, a stator, an
overrunning clutch, an impeller and an electronically
applied converter clutch. The converter clutch pro-vides reduced engine speed and greater fuel economy
when engaged. Clutch engagement also provides
reduced transmission fluid temperatures. The con-
verter clutch engages in third gear. The torque con-
verter hub drives the transmission oil (fluid) pump
and contains an o-ring seal to better control oil flow.
The torque converter is a sealed, welded unit that
is not repairable and is serviced as an assembly.
CAUTION: The torque converter must be replaced if
a transmission failure resulted in large amounts of
metal or fiber contamination in the fluid. If the fluid
is contaminated, flush the fluid cooler and lines.
Fig. 109 Torque Converter Assembly
1 - TURBINE ASSEMBLY
2-STATOR
3 - CONVERTER HUB
4 - O-RING
5 - IMPELLER ASSEMBLY
6 - CONVERTER CLUTCH PISTON
7 - TURBINE HUB
21 - 264 AUTOMATIC TRANSMISSION - 545RFEWJ
SOLENOIDS (Continued)
Page 1784 of 2199
IMPELLER
The impeller (Fig. 110) is an integral part of the
converter housing. The impeller consists of curved
blades placed radially along the inside of the housing
on the transmission side of the converter. As the con-
verter housing is rotated by the engine, so is the
impeller, because they are one and the same and are
the driving members of the system.
Fig. 110 Impeller
1 - ENGINE FLEXPLATE 4 - ENGINE ROTATION
2 - OIL FLOW FROM IMPELLER SECTION INTO TURBINE
SECTION5 - ENGINE ROTATION
3 - IMPELLER VANES AND COVER ARE INTEGRAL
WJAUTOMATIC TRANSMISSION - 545RFE 21 - 265
TORQUE CONVERTER (Continued)