Page 2024 of 2490
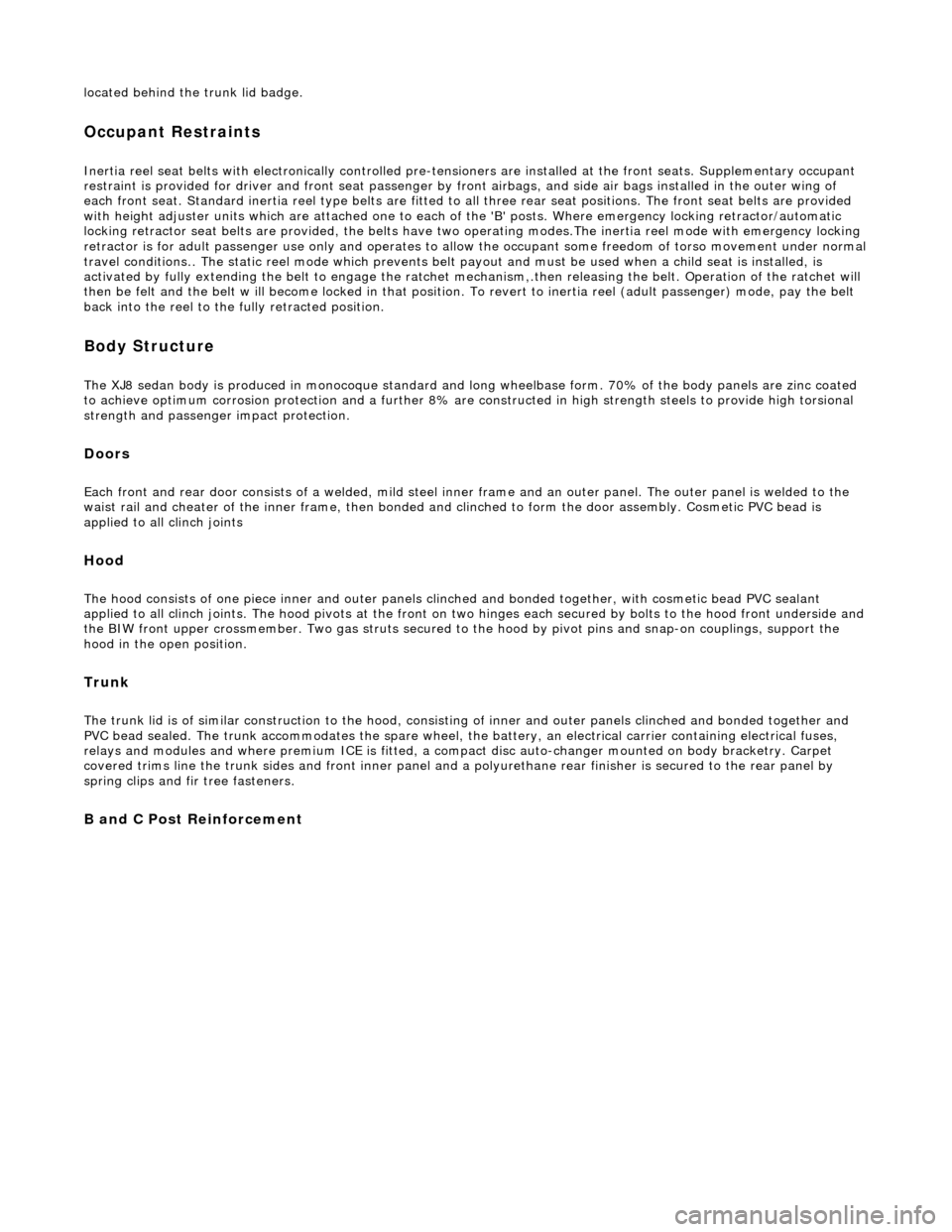
located behind the trunk lid badge.
Occupant Restraints
Inertia reel seat belts with electronically controlled pre-tensioners are installed at the front seats. Supplementary occupant
restraint is provided for driver and front seat passenger by front airbags, and side air bags installed in the outer wing of
each front seat. Standard inertia reel type belts are fitted to all three rear seat positions. The front seat belts are provide d
with height adjuster units which are attached one to each of the 'B' posts. Where emergency locking retractor/automatic
locking retractor seat belts are provided, the belts have two operating modes.The inertia reel mode with emergency locking
retractor is for adult passenge r use only and operates to allow the occupant some freedom of tors o movement under normal
travel conditions.. The static reel mode which prevents belt payout and must be used when a ch ild seat is installed, is
activated by fully extending the belt to engage the ratchet me chanism,.then releasing the belt. Operation of the ratchet will
then be felt and the belt w ill become locked in that position. To revert to in ertia reel (adult passenger) mode, pay the belt
back into the reel to th e fully retracted position.
Body Structure
The XJ8 sedan body is produced in monocoque standard and lo ng wheelbase form. 70% of the body panels are zinc coated
to achieve optimum corrosion protection and a further 8% are constructed in high st rength steels to provide high torsional
strength and passenger impact protection.
Doors
Each front and rear door consists of a we lded, mild steel inner frame and an outer panel. The outer panel is welded to the
waist rail and cheater of the inner frame, then bonded and clinched to fo rm the door assembly. Cosmetic PVC bead is
applied to all clinch joints
Hood
The hood consists of one piece inner an d outer panels clinched and bonded toge ther, with cosmetic bead PVC sealant
applied to all clinch joints. The hood pivo ts at the front on two hinges each secured by bolts to the hood front underside and
the BIW front upper crossmember. Two gas struts secured to the hood by pi vot pins and snap-on couplings, support the
hood in the open position.
Trunk
The trunk lid is of similar construction to the hood, consisting of inner and outer panels clinched and bonded together and
PVC bead sealed. The trunk accommodates the spare wheel, the battery, an electrical carrier containing electrical fuses,
relays and modules and where premium ICE is fitted, a compac t disc auto-changer mounted on body bracketry. Carpet
covered trims line the trunk sides and front inner panel and a po lyurethane rear finisher is secured to the rear panel by
spring clips and fir tree fasteners.
B and C Post Reinforcement
Page 2035 of 2490
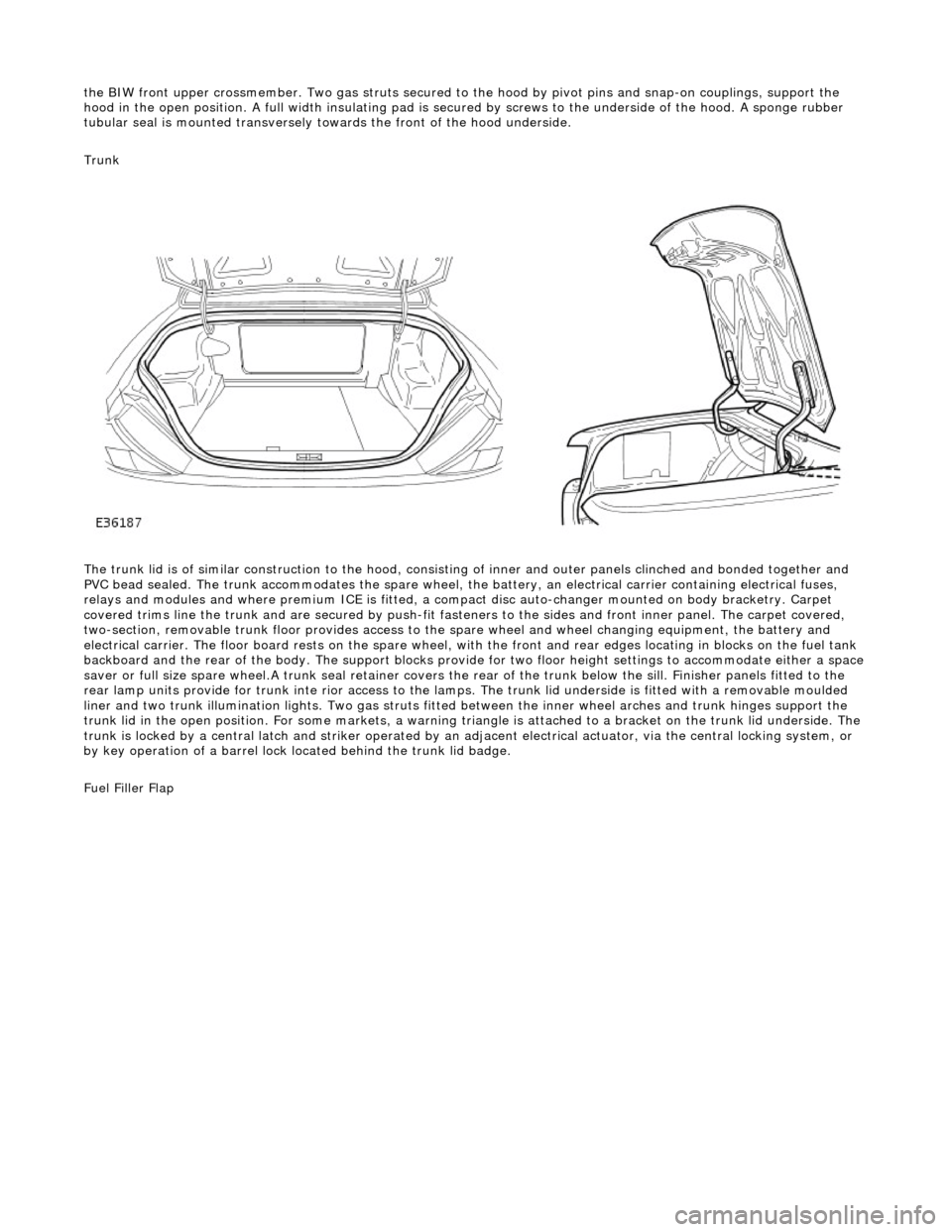
the BIW front upper crossmember. Two gas struts secured to the hood by pi vot pins and snap-on couplings, support the
hood in the open position. A full width insulating pad is secured by screws to the underside of the hood. A sponge rubber
tubular seal is mounted transversely to wards the front of the hood underside.
Trunk
The trunk lid is of similar construction to the hood, consisting of inner and outer panels clinched and bonded together and
PVC bead sealed. The trunk accommodates the spare wheel, the battery, an electrical carrier containing electrical fuses,
relays and modules and where premium ICE is fitted, a compac t disc auto-changer mounted on body bracketry. Carpet
covered trims line the trunk and are secured by push-fit fasten ers to the sides and front inner panel. The carpet covered,
two-section, removable trunk floor prov ides access to the spare wheel and wheel changing equipment, the battery and
electrical carrier. The floor board rests on the spare wheel, with the front and rear e dges locating in blocks on the fuel tank
backboard and the rear of the body. The support blocks provide for two floor height settings to accommodate either a space
saver or full size spare wheel.A trunk seal retainer covers the re ar of the trunk below the sill. Finisher panels fitted to the
rear lamp units provide for trunk inte rior access to the lamps. The trunk lid underside is fitted with a removable moulded
liner and two trunk illumination lights. Two gas struts fitted between the inner wheel arches and trunk hinges support the
trunk lid in the open position. For some markets, a warning triangle is attached to a bracket on the trunk lid underside. The
trunk is locked by a central latch and stri ker operated by an adjacent electrical actuator, via the central locking system, or
by key operation of a barrel lock located behind the trunk lid badge.
Fuel Filler Flap
Page 2036 of 2490
The hinged fuel filler flap which is attached to the rear saddle panel by two nuts, incorporates a rubber buffer, snap-in
striker, hinge spring and fuel cap stowage magnet. The rubber fuel bowl moulding at tached via a steel armature to the body reinforcement panel, is retained at the filler neck by a clip. A mating drain tube is fitted with an internal filter. The filler flap
latch mechanism which is secured by nuts to the fuel bowl armature, comprises a locking pin and actuator. The actuator,
driven directly by the security and lock ing control module, operates independently from the central locking system. Locking
of the fuel filler flap can only be achieved by operation of the key or the remote rf transmitter.
Page 2121 of 2490
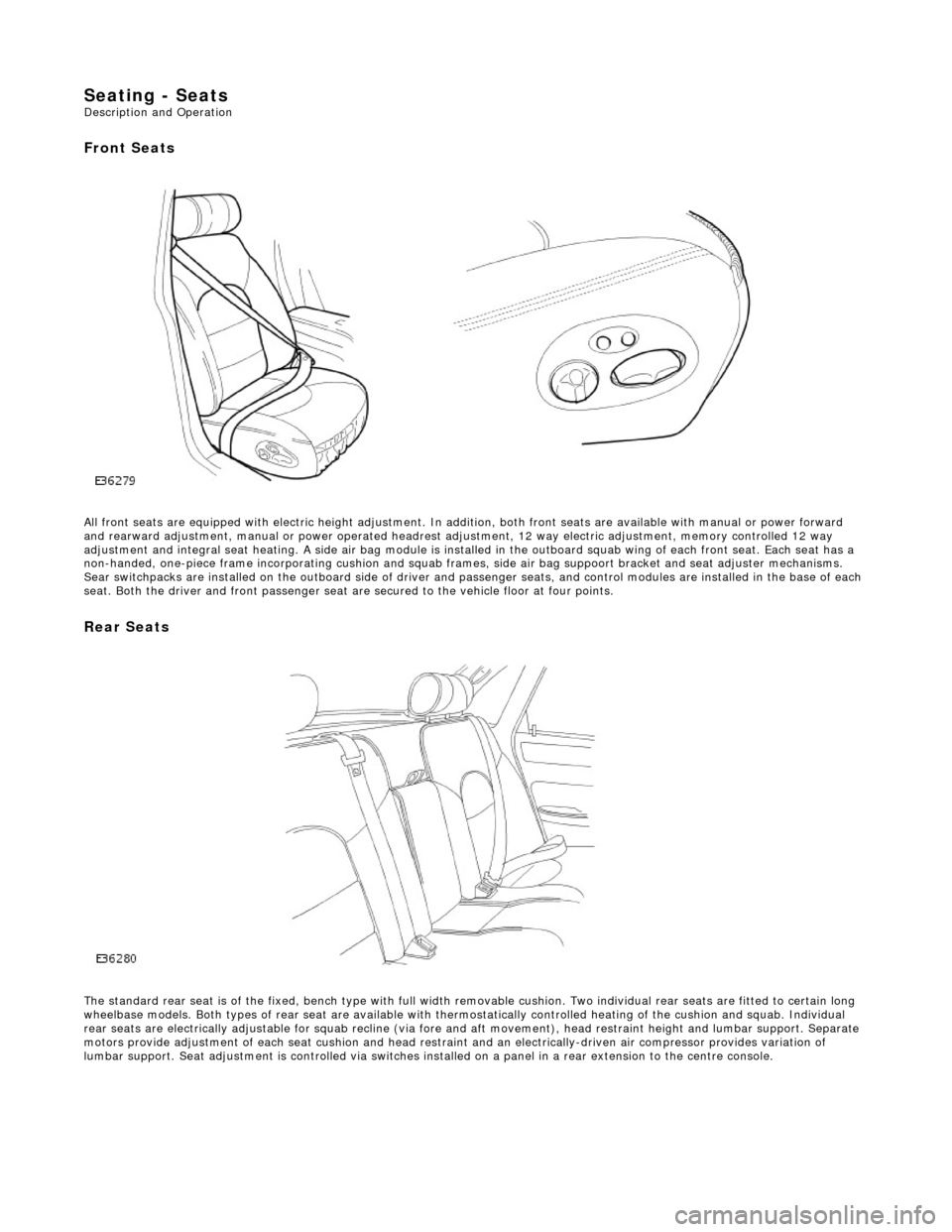
Seating - Seats Description and Operation
Front Seats
All front seats are equipped with electric height adjustment. In addition, both front seats are available with manual or power forward
and rearward adjustment, manual or powe r operated headrest adjustment, 12 way elec tric adjustment, memory controlled 12 way
adjustment and integral seat heating. A side air bag module is installed in the outboard squab wing of each front seat. Each se at has a
non-handed, one-piece frame incorporating cushion and squab frames , side air bag suppoort bracket and seat adjuster mechanisms.
Sear switchpacks are installed on the outboa rd side of driver and passenger seats, and control modules are installed in the bas e of each
seat. Both the driver and front passenger seat ar e secured to the vehicle floor at four points.
Rear Seats
The standard rear seat is of the fixed, bench type with full wi dth removable cushion. Two individual rear seats are fitted to certain long
wheelbase models. Both types of rear seat are available with thermostatically controlled heating of the cushion and squab. Indi vidual
rear seats are electrically adjustable for squab recline (via fore and aft moveme nt), head restraint height and lumbar support. Separate
motors provide adjustment of each seat cushion and head restraint and an electrica lly-driven air compressor provides variation of
lumbar support. Seat adjustment is controll ed via switches installed on a panel in a rear extension to the centre console.
Page 2122 of 2490
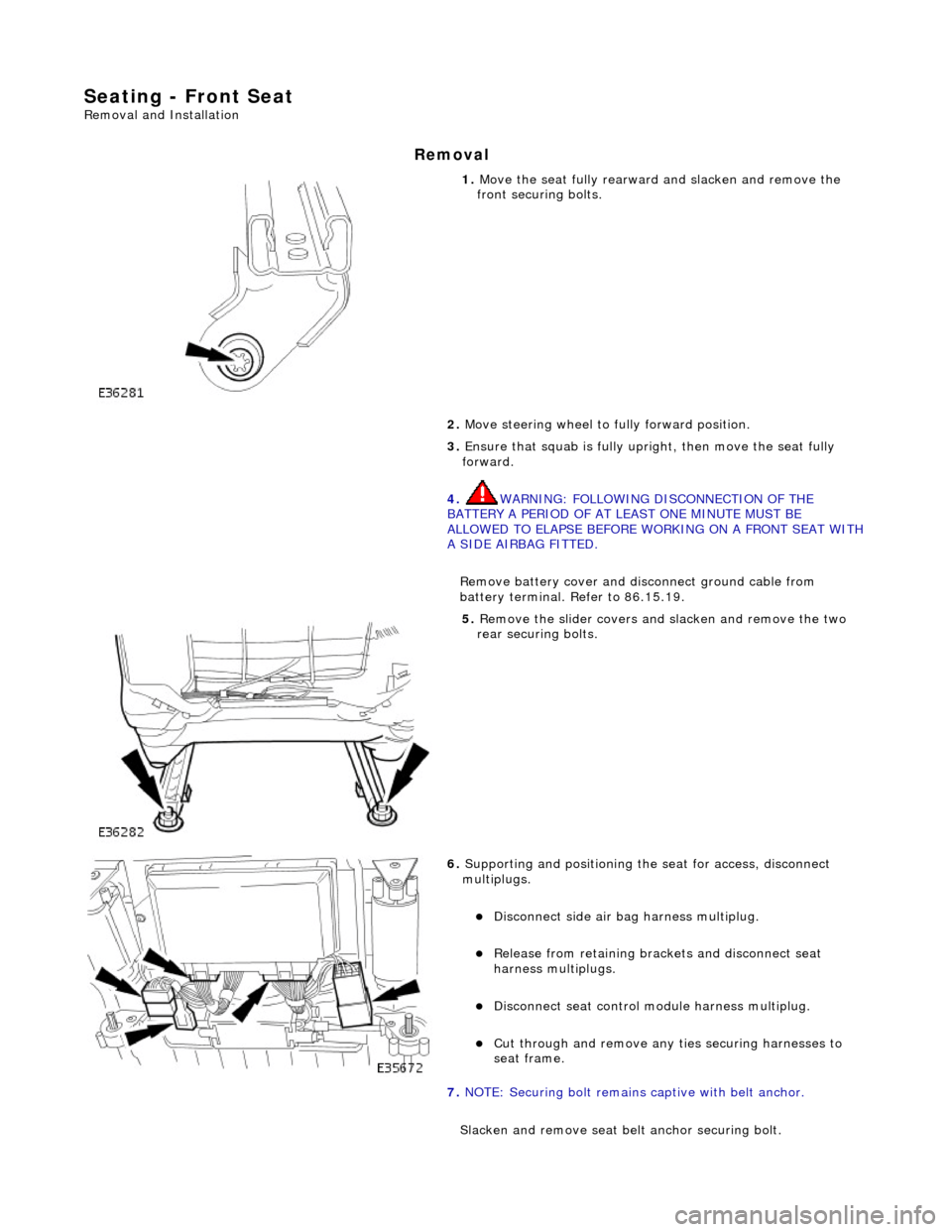
Seating - Front Seat
Removal and Installation
Removal
1. Move the seat fully rearward and slacken and remove the
front securing bolts.
2. Move steering wheel to fully forward position.
3. Ensure that squab is fully upright, then move the seat fully
forward.
4. WARNING: FOLLOWING DISCONNECTION OF THE
BATTERY A PERIOD OF AT LEAST ONE MINUTE MUST BE
ALLOWED TO ELAPSE BEFORE WORKING ON A FRONT SEAT WITH
A SIDE AIRBAG FITTED.
Remove battery cover and disc onnect ground cable from
battery terminal. Refer to 86.15.19.
5. Remove the slider covers an d slacken and remove the two
rear securing bolts.
6. Supporting and positioning the seat for access, disconnect
multiplugs.
Disconnect side air bag harness multiplug.
Release from retaining brackets and disconnect seat
harness multiplugs.
Disconnect seat control module harness multiplug.
Cut through and remove any ti es securing harnesses to
seat frame.
7. NOTE: Securing bolt remains captive with belt anchor.
Slacken and remove seat be lt anchor securing bolt.
Page 2149 of 2490
Seating - Front Seat Track Motor
Removal and Installation
Removal
1. WARNING: FOLLOWING DISCONNECTION OF THE
BATTERY A PERIOD OF AT LEAST ONE MINUTE MUST BE
ALLOWED TO ELAPSE BEFORE WORKING ON A FRONT SEAT WITH
A SIDE AIRBAG FITTED.
Remove battery cover and disc onnect ground cable from
battery terminal. Refer to 86.15.19.
2. Remove front seat from vehicle and place inverted on clean
work surface. Re fer to 76.70.01.
3. Release rearward (RH) tilt motor harness multiplug from
retaining bracket and di sconnect multiplug.
4. Release forward (LH) tilt motor harness multiplug from
retaining bracket and di sconnect multiplug.
5. Disconnect seat control module harness multiplugs.
6. Release heater relay (brown ) from retaining bracket.
Page 2153 of 2490
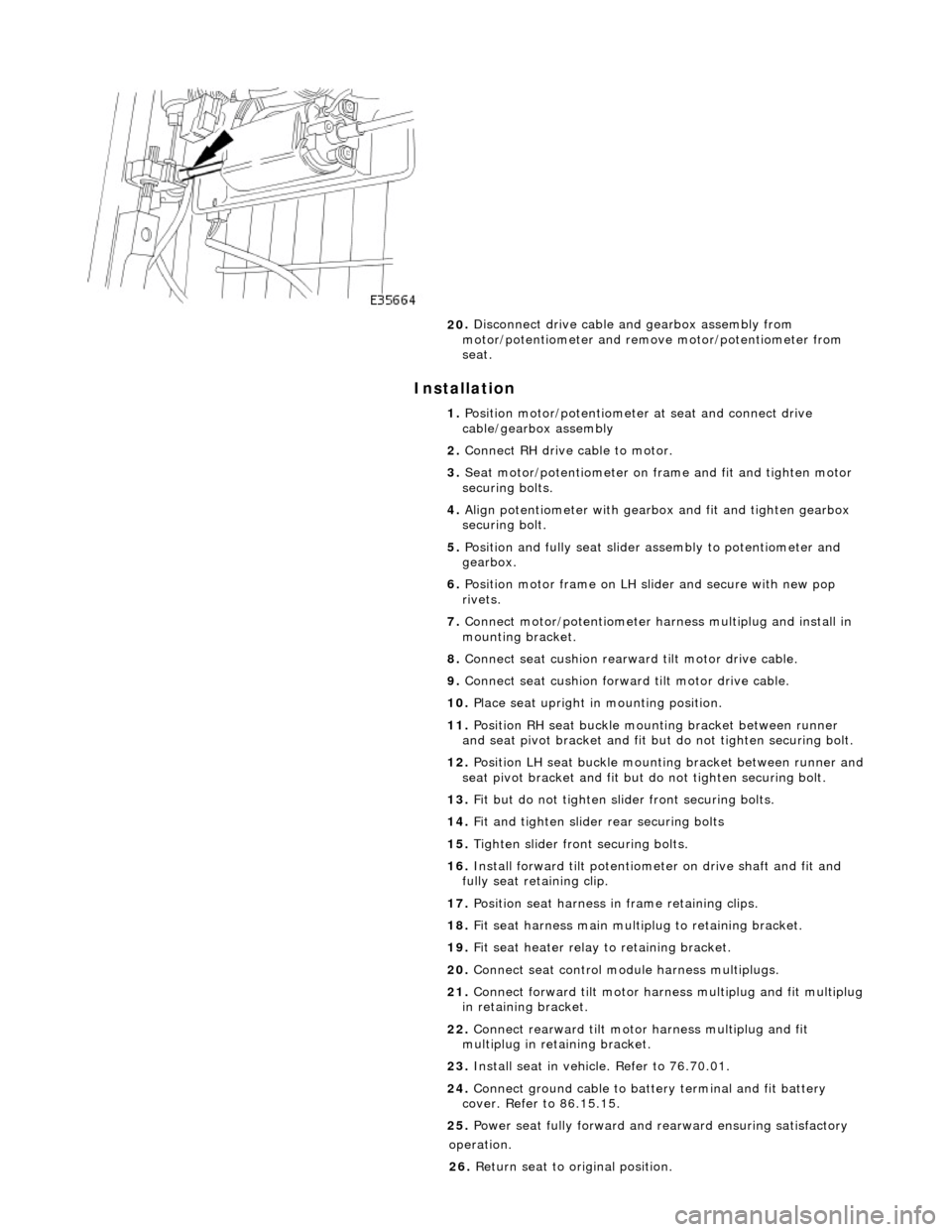
I
nstallation
20
.
Disconnect drive cable and gearbox assembly from
motor/potentiometer and remo ve motor/potentiometer from
seat.
1. Position motor/potentiometer at seat and connect drive
cable/gearbox assembly
2. Connect RH drive cable to motor.
3. Seat motor/potentiometer on fra me and fit and tighten motor
securing bolts.
4. Align potentiometer with gearbo x and fit and tighten gearbox
securing bolt.
5. Position and fully seat slider assembly to potentiometer and
gearbox.
6. Position motor frame on LH sl ider and secure with new pop
rivets.
7. Connect motor/potentiometer harness multiplug and install in
mounting bracket.
8. Connect seat cushion rearward tilt motor drive cable.
9. Connect seat cushion forwar d tilt motor drive cable.
10. Place seat upright in mounting position.
11. Position RH seat buckle mounting bracket between runner
and seat pivot bracket and fit but do not tighten securing bolt.
12. Position LH seat buckle mounting bracket between runner and
seat pivot bracket an d fit but do not tighten securing bolt.
13. Fit but do not tighten slider front securing bolts.
14. Fit and tighten slider rear securing bolts
15. Tighten slider front securing bolts.
16. Install forward tilt potentiome ter on drive shaft and fit and
fully seat retaining clip.
17. Position seat harness in frame retaining clips.
18. Fit seat harness main multiplug to retaining bracket.
19. Fit seat heater relay to retaining bracket.
20. Connect seat control module harness multiplugs.
21. Connect forward tilt motor harn ess multiplug and fit multiplug
in retaining bracket.
22. Connect rearward tilt motor harness multiplug and fit
multiplug in retaining bracket.
23. Install seat in vehicle. Refer to 76.70.01.
24. Connect ground cable to batt ery terminal and fit battery
cover. Refer to 86.15.15.
25. Power seat fully forward and rearward ensuring satisfactory
op
eration.
26. Return seat to original position.
Page 2184 of 2490
4.
Fully raise glass and using linen tape, secure to top of door
frame.
5. Fit door glass lift motor. Refer to 86.25.04.
6. Fit door module. Refer to 86.80.34.
7. Reposition PVC inne r weathershield.
8. Position water shedder and carefully pass harness multiplugs
through penetration.
9. Ensuring door mating surfaces ar e clean and dry, firmly seat
water shedder.
10. Fit door casing. Refer to 76.34.01.
11. Connect ground cable to batter y terminal and fit cover to
battery. Refer to 86.15.15.