Page 1816 of 3061
EM-46
< SERVICE INFORMATION >
CAMSHAFT
CAMSHAFT
Removal and InstallationINFOID:0000000003531534
NOTE:
Do not remove the engine assembly to perform this procedure.
REMOVAL
1. Remove the RH bank and LH bank rocker covers. Refer to EM-35, "Removal and Installation".
2. Obtain compression TDC of No. 1 cylinder as follows:
a. Turn the crankshaft pulley clockwise to align the TDC identifica- tion notch (without paint mark) with the timing indicator on the
front cover.
1. Cylinder head RH bank 2. Camshaft bracket (No. 2, 3, 4, 5) 3. Valve lifter
4. Camshaft bracket (No. 1) 5. Seal washer 6. Camshaft RH bank EXH
7. Camshaft RH bank INT 8. Camshaft LH bank INT 9. Camshaft LH bank EXH
10. Camshaft sprocket RH bank EXH 11. Camshaft sprocket RH bank INT 12. Camshaft sprocket LH bank INT
13. Camshaft sprocket LH bank EXH 14. Camshaft position sensor (PHASE) 15. O-ring
16. Cylinder head LH bank A. Follow installation procedure
WBIA0801E
KBIA2476E
Page 1835 of 3061
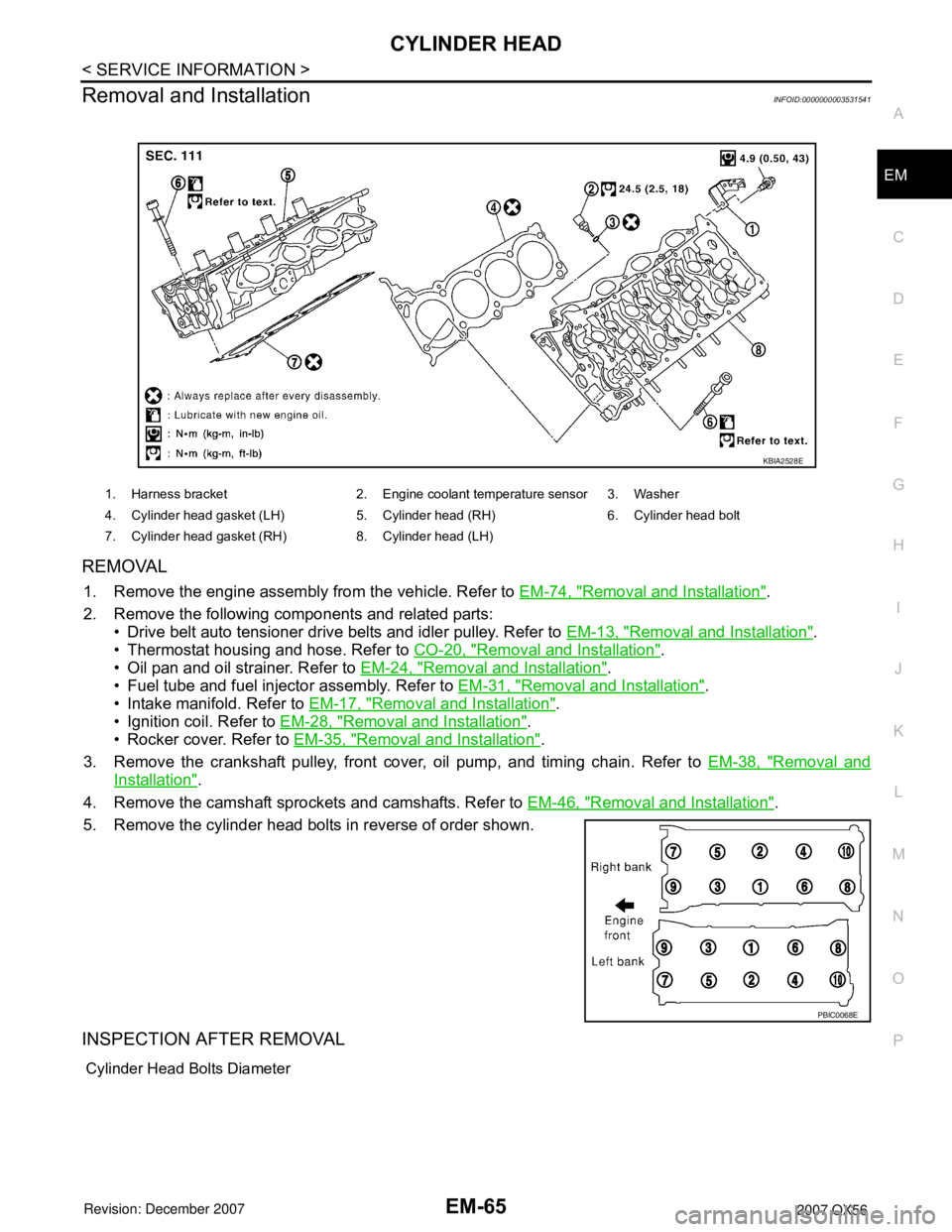
CYLINDER HEADEM-65
< SERVICE INFORMATION >
C
DE
F
G H
I
J
K L
M A
EM
NP
O
Removal and InstallationINFOID:0000000003531541
REMOVAL
1. Remove the engine assembly from the vehicle. Refer to
EM-74, "Removal and Installation".
2. Remove the following components and related parts: • Drive belt auto tensioner drive belts and idler pulley. Refer to EM-13, "
Removal and Installation".
• Thermostat housing and hose. Refer to CO-20, "
Removal and Installation".
• Oil pan and oil strainer. Refer to EM-24, "
Removal and Installation".
• Fuel tube and fuel injector assembly. Refer to EM-31, "
Removal and Installation".
• Intake manifold. Refer to EM-17, "
Removal and Installation".
• Ignition coil. Refer to EM-28, "
Removal and Installation".
• Rocker cover. Refer to EM-35, "
Removal and Installation".
3. Remove the crankshaft pulley, front cover, oil pump, and timing chain. Refer to EM-38, "
Removal and
Installation".
4. Remove the camshaft sprockets and camshafts. Refer to EM-46, "
Removal and Installation".
5. Remove the cylinder head bolts in reverse of order shown.
INSPECTION AFTER REMOVAL
Cylinder Head Bolts Diameter
1. Harness bracket 2. Engine coolant temperature sensor 3. Washer
4. Cylinder head gasket (LH) 5. Cylinder head (RH) 6. Cylinder head bolt
7. Cylinder head gasket (RH) 8. Cylinder head (LH)
KBIA2528E
PBIC0068E
Page 1848 of 3061
EM-78
< SERVICE INFORMATION >
CYLINDER BLOCK
CYLINDER BLOCK
Disassembly and AssemblyINFOID:0000000003531545
1. Knock sensor sub-harness 2. Knock sensor 3. Cylinder block
4. Main bearing upper 5. Top ring 6. Second ring
7. Oil ring 8. Crankshaft key 9. Piston
10. Connecting rod 11. Snap ring 12. Piston pin
13. Connecting rod bearing 14. Connecting rod bearing cap 15. Main bearing cap
16. Thrust bearing lower 17. Main bearing lower 18. Crankshaft
19. Pilot converter 20. Thrust bearing upper 21. Side bolt
WBIA0471E
Page 1849 of 3061
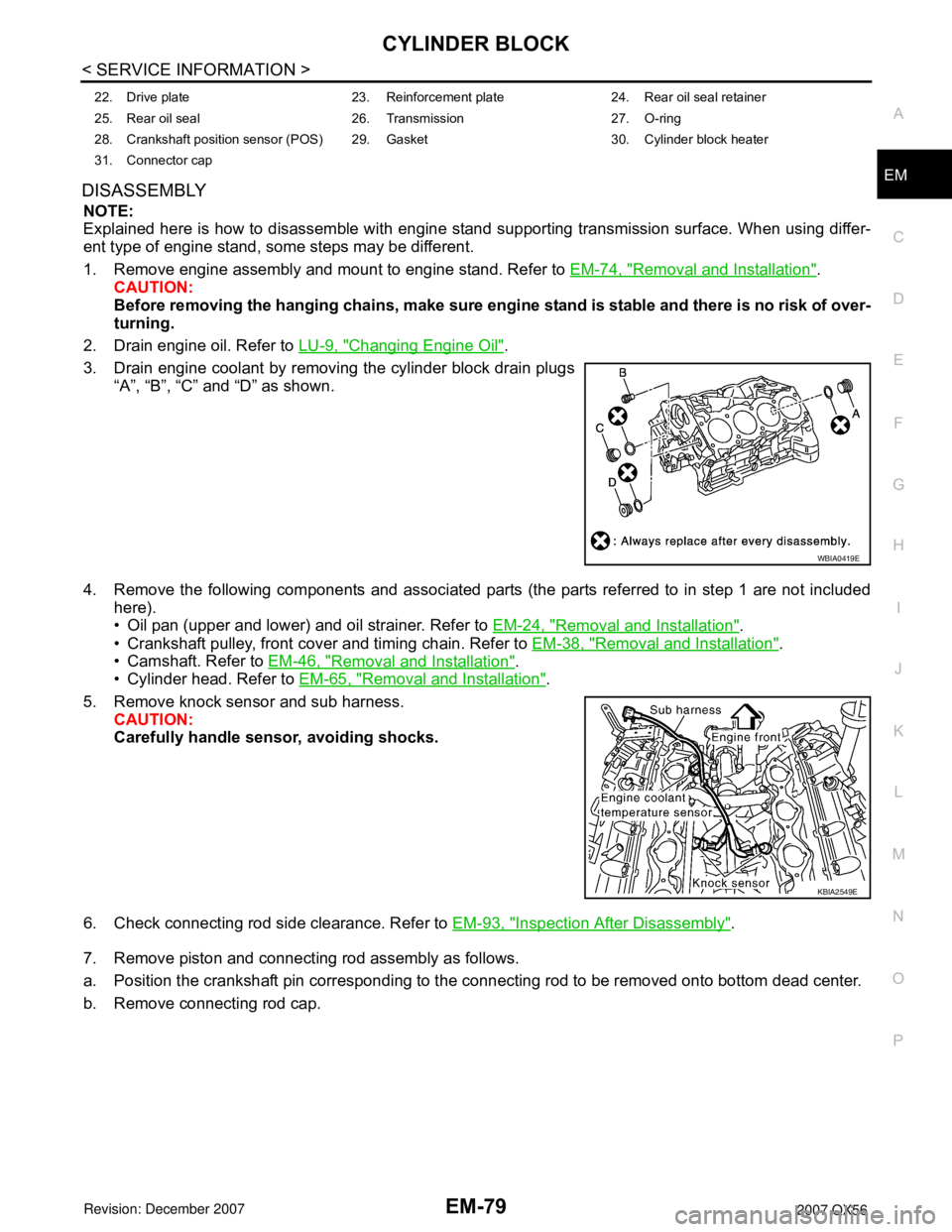
CYLINDER BLOCK
EM-79
< SERVICE INFORMATION >
C
D
E
F
G
H
I
J
K
L
MA
EM
N
P O
DISASSEMBLY
NOTE:
Explained here is how to disassemble with engine stand supporting transmission surface. When using differ-
ent type of engine stand, some steps may be different.
1. Remove engine assembly and mount to engine stand. Refer to EM-74, "
Removal and Installation".
CAUTION:
Before removing the hanging chains, make sure engine stand is stable and there is no risk of over-
turning.
2. Drain engine oil. Refer to LU-9, "
Changing Engine Oil".
3. Drain engine coolant by removing the cylinder block drain plugs
“A”, “B”, “C” and “D” as shown.
4. Remove the following components and associated parts (the parts referred to in step 1 are not included
here).
• Oil pan (upper and lower) and oil strainer. Refer to EM-24, "
Removal and Installation".
• Crankshaft pulley, front cover and timing chain. Refer to EM-38, "
Removal and Installation".
• Camshaft. Refer to EM-46, "
Removal and Installation".
• Cylinder head. Refer to EM-65, "
Removal and Installation".
5. Remove knock sensor and sub harness.
CAUTION:
Carefully handle sensor, avoiding shocks.
6. Check connecting rod side clearance. Refer to EM-93, "
Inspection After Disassembly".
7. Remove piston and connecting rod assembly as follows.
a. Position the crankshaft pin corresponding to the connecting rod to be removed onto bottom dead center.
b. Remove connecting rod cap.
22. Drive plate 23. Reinforcement plate 24. Rear oil seal retainer
25. Rear oil seal 26. Transmission 27. O-ring
28. Crankshaft position sensor (POS) 29. Gasket 30. Cylinder block heater
31. Connector cap
WBIA0419E
KBIA2549E
Page 1856 of 3061
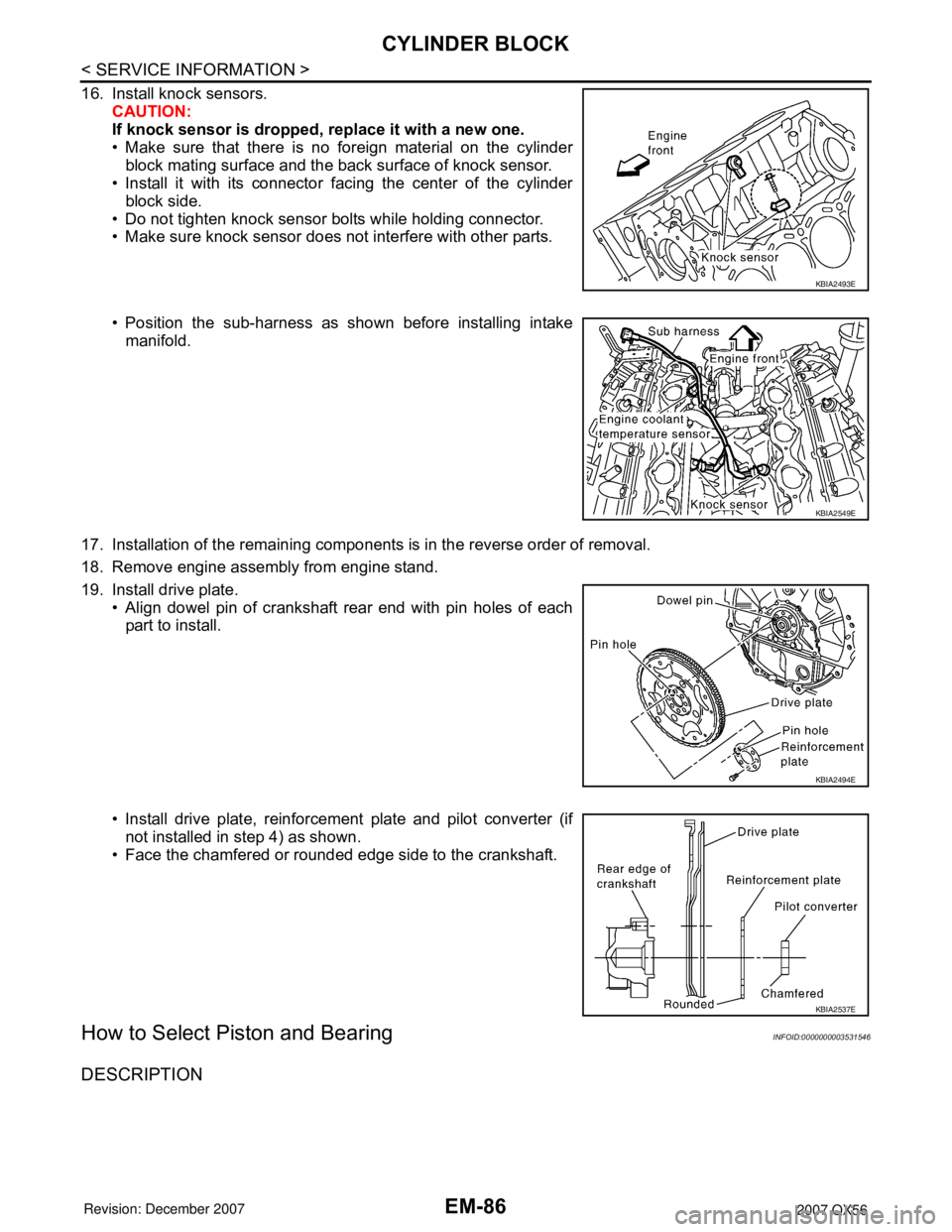
EM-86
< SERVICE INFORMATION >
CYLINDER BLOCK
16. Install knock sensors.
CAUTION:
If knock sensor is dropped, replace it with a new one.
• Make sure that there is no foreign material on the cylinder
block mating surface and the back surface of knock sensor.
• Install it with its connector facing the center of the cylinder
block side.
• Do not tighten knock sensor bolts while holding connector.
• Make sure knock sensor does not interfere with other parts.
• Position the sub-harness as shown before installing intake
manifold.
17. Installation of the remaining components is in the reverse order of removal.
18. Remove engine assembly from engine stand.
19. Install drive plate.
• Align dowel pin of crankshaft rear end with pin holes of each
part to install.
• Install drive plate, reinforcement plate and pilot converter (if
not installed in step 4) as shown.
• Face the chamfered or rounded edge side to the crankshaft.
How to Select Piston and BearingINFOID:0000000003531546
DESCRIPTION
KBIA2493E
KBIA2549E
KBIA2494E
KBIA2537E
Page 1884 of 3061
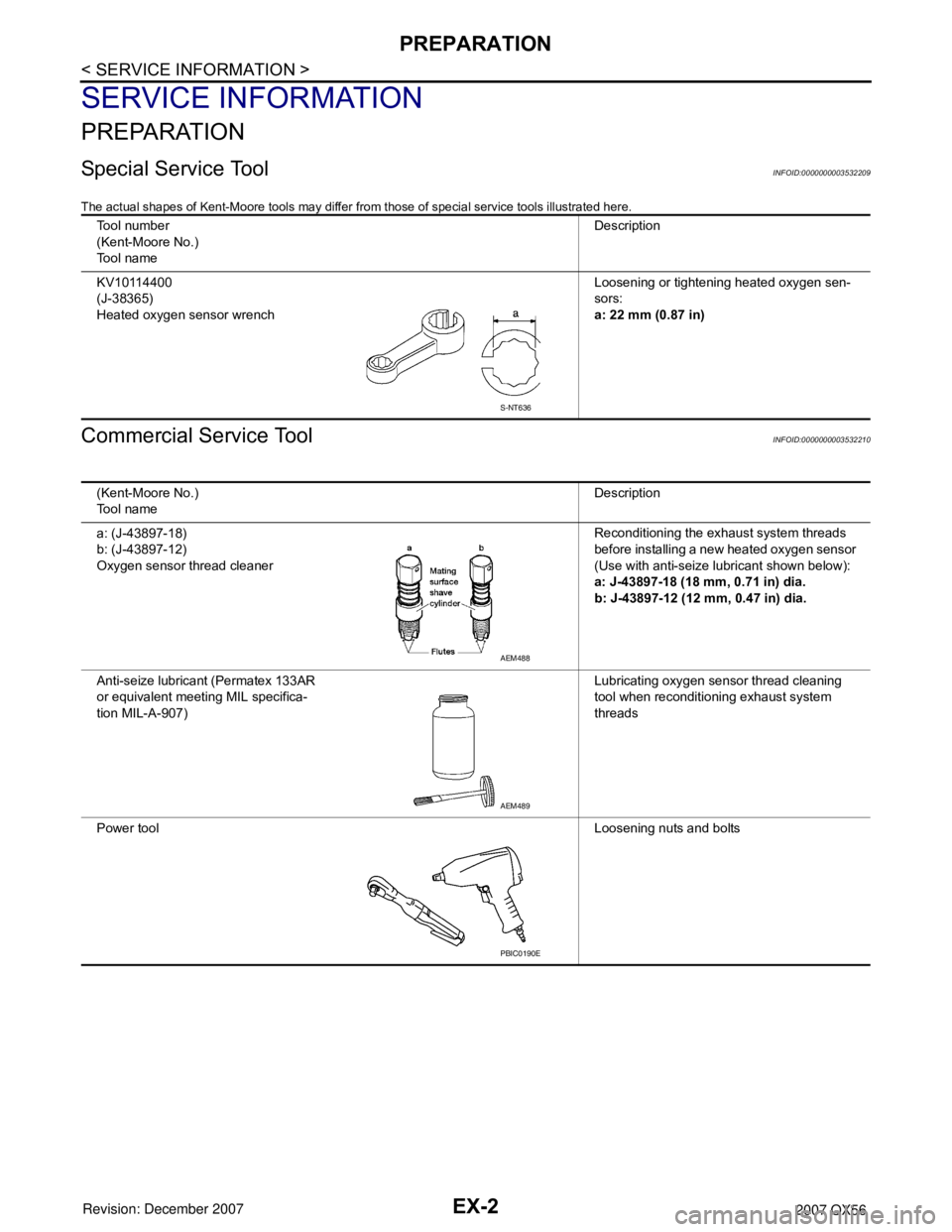
EX-2
< SERVICE INFORMATION >
PREPARATION
SERVICE INFORMATION
PREPARATION
Special Service ToolINFOID:0000000003532209
The actual shapes of Kent-Moore tools may differ from those of special service tools illustrated here.
Commercial Service ToolINFOID:0000000003532210
Tool number
(Kent-Moore No.)
Tool name Description
KV10114400
(J-38365)
Heated oxygen sensor wrench Loosening or tightening heated oxygen sen-
sors:
a: 22 mm (0.87 in)
S-NT636
(Kent-Moore No.)
Tool name
Description
a: (J-43897-18)
b: (J-43897-12)
Oxygen sensor thread cleaner Reconditioning the exhaust system threads
before installing a new heated oxygen sensor
(Use with anti-seize lubricant shown below):
a: J-43897-18 (18 mm, 0.71 in) dia.
b: J-43897-12 (12 mm, 0.47 in) dia.
Anti-seize lubricant (Permatex 133AR
or equivalent meeting MIL specifica-
tion MIL-A-907) Lubricating oxygen sensor thread cleaning
tool when reconditioning exhaust system
threads
Power tool Loosening nuts and bolts
AEM488
AEM489
PBIC0190E
Page 1885 of 3061
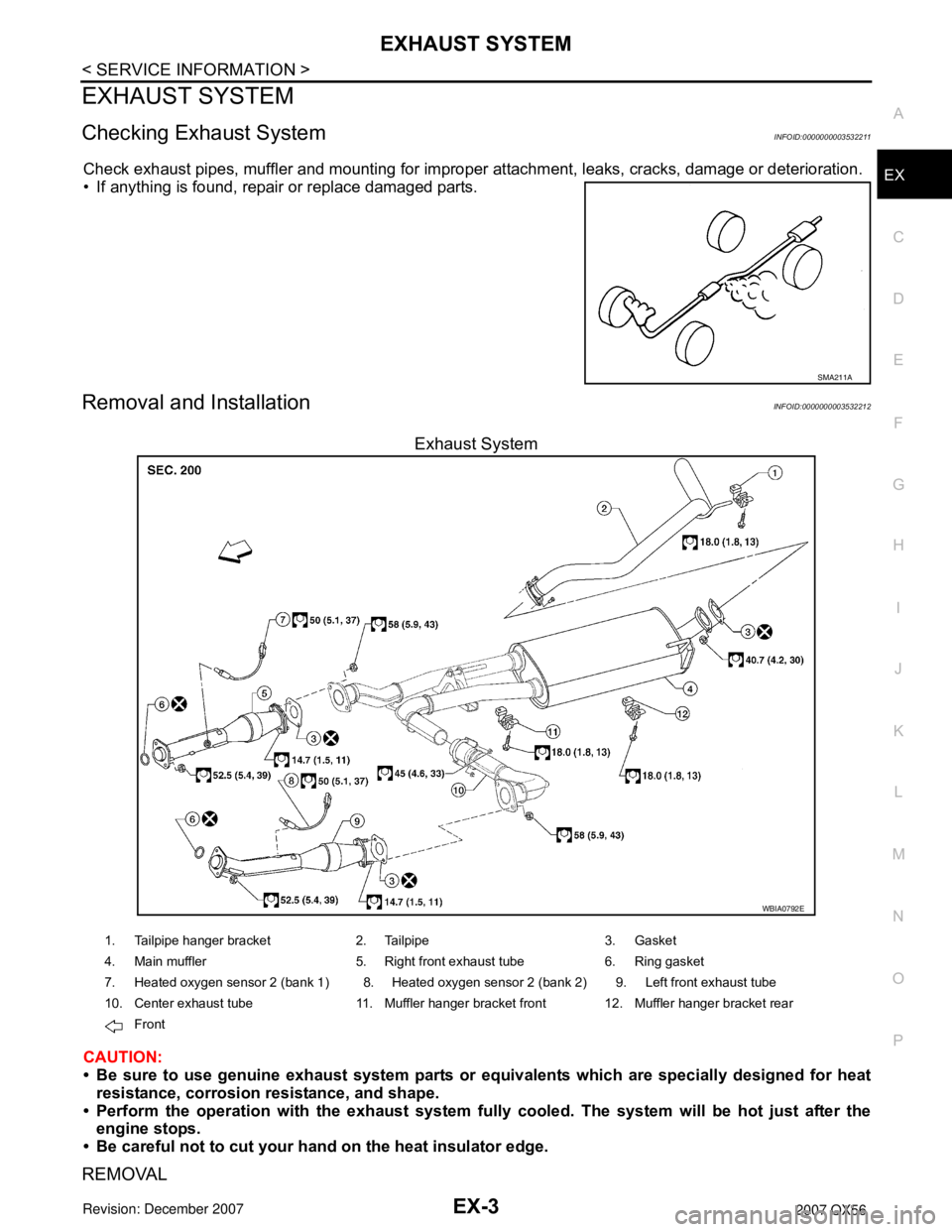
EXHAUST SYSTEMEX-3
< SERVICE INFORMATION >
C
DE
F
G H
I
J
K L
M A
EX
NP
O
EXHAUST SYSTEM
Checking Exhaust SystemINFOID:0000000003532211
Check exhaust pipes, muffler and mounting for improper
attachment, leaks, cracks, damage or deterioration.
• If anything is found, repair or replace damaged parts.
Removal and InstallationINFOID:0000000003532212
Exhaust System
CAUTION:
• Be sure to use genuine exhaust system parts or equivalents which are specially designed for heat
resistance, corrosion resistance, and shape.
• Perform the operation with the exhaust system full y cooled. The system will be hot just after the
engine stops.
• Be careful not to cut your hand on the heat insulator edge.
REMOVAL
SMA211A
WBIA0792E
1. Tailpipe hanger bracket 2. Tailpipe 3. Gasket
4. Main muffler 5. Right front exhaust tube 6. Ring gasket
7. Heated oxygen sensor 2 (bank 1) 8. Heated oxygen sensor 2 (bank 2) 9. Left front exhaust tube
10. Center exhaust tube 11. Muffler hanger bracket front 12. Muffler hanger bracket rear
Front
Page 1886 of 3061
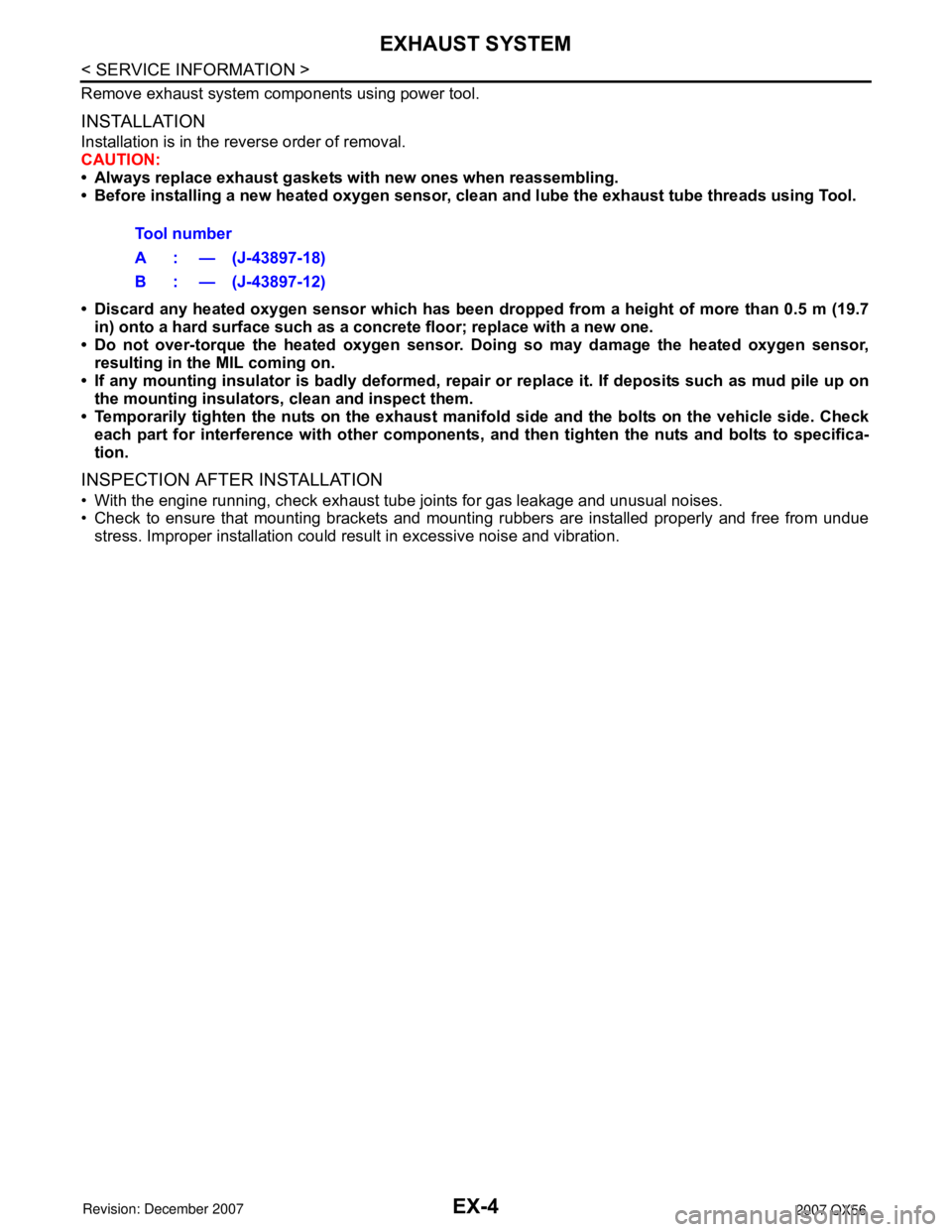
EX-4
< SERVICE INFORMATION >
EXHAUST SYSTEM
Remove exhaust system components using power tool.
INSTALLATION
Installation is in the reverse order of removal.
CAUTION:
• Always replace exhaust gaskets with new ones when reassembling.
• Before installing a new heated oxygen sensor, clean and lube the exhaust tube threads using Tool.
• Discard any heated oxygen sensor which has been dropped from a height of more than 0.5 m (19.7
in) onto a hard surface such as a concrete floor; replace with a new one.
• Do not over-torque the heated oxygen sensor. Doing so may damage the heated oxygen sensor,
resulting in the MIL coming on.
• If any mounting insulator is badly deformed, repair or replace it. If deposits such as mud pile up on
the mounting insulators, clean and inspect them.
• Temporarily tighten the nuts on the exhaust manifold side and the bolts on the vehicle side. Check
each part for interference with other components, and then tighten the nuts and bolts to specifica-
tion.
INSPECTION AFTER INSTALLATION
• With the engine running, check exhaust tube joints for gas leakage and unusual noises.
• Check to ensure that mounting brackets and mounting rubbers are installed properly and free from undue
stress. Improper installation could result in excessive noise and vibration. Tool number
A : — (J-43897-18)
B : — (J-43897-12)