Page 1845 of 3383
EC-634Revision: November 2009
REFRIGERANT PRESSURE SENSOR
2006 QX56
7. CHECK REFRIGERANT PRESSURE SENSOR INPUT SIGNAL CIRCUIT FOR OPEN AND SHORT
1. Check harness continuity between ECM terminal 70 and refrigerant pressure sensor terminal 2. Refer to Wiring Diagram.
2. Also check harness for short to ground and short to power.
OK or NG
OK >> GO TO 9.
NG >> GO TO 8.
8. DETECT MALFUNCTIONING PART
Check the following.
Harness connectors E5, F14
Harness for open or short between ECM and refrigerant pressure sensor
>> Repair open circuit or short to ground or short to power in harness or connectors.
9. CHECK INTERMITTENT INCIDENT
Refer to EC-144, "
TROUBLE DIAGNOSIS FOR INTERMITTENT INCIDENT" .
OK or NG
OK >> Replace refrigerant pressure sensor.
NG >> Repair or replace.
Removal and InstallationUBS00HDK
REFRIGERANT PRESSURE SENSOR
Refer to ATC-182, "Removal and Installation for Refrigerant Pressure Sensor" .
Continuity should exist.
Page 1848 of 3383
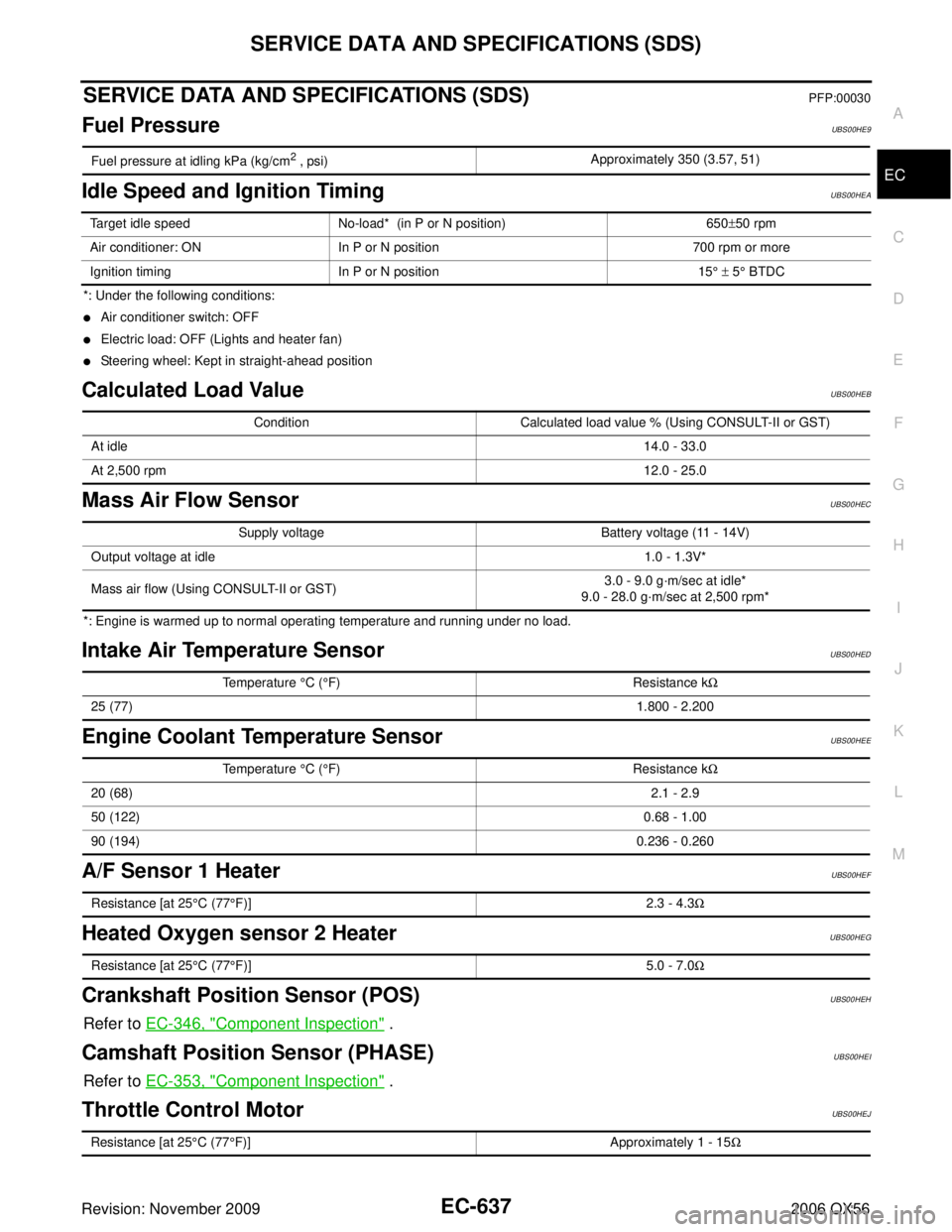
SERVICE DATA AND SPECIFICATIONS (SDS)EC-637
C
DE
F
G H
I
J
K L
M A
EC
Revision: November 2009 2006 QX56
SERVICE DATA AND SPECIFICATIONS (SDS)PFP:00030
Fuel PressureUBS00HE9
Idle Speed and Ignition TimingUBS00HEA
*: Under the following conditions:
Air conditioner switch: OFF
Electric load: OFF (Lights and heater fan)
Steering wheel: Kept in straight-ahead position
Calculated Load ValueUBS00HEB
Mass Air Flow SensorUBS00HEC
*: Engine is warmed up to normal operating temperature and running under no load.
Intake Air Temperature SensorUBS00HED
Engine Coolant Temperature SensorUBS00HEE
A/F Sensor 1 HeaterUBS00HEF
Heated Oxygen sensor 2 HeaterUBS00HEG
Crankshaft Position Sensor (POS)UBS00HEH
Refer to EC-346, "Component Inspection" .
Camshaft Position Sensor (PHASE)UBS00HEI
Refer to EC-353, "Component Inspection" .
Throttle Control MotorUBS00HEJ
Fuel pressure at idling kPa (kg/cm2 , psi) Approximately 350 (3.57, 51)
Target idle speed
No-load* (in P or N position) 650±50 rpm
Air conditioner: ON In P or N position 700 rpm or more
Ignition timing In P or N position 15° ± 5 ° BTDC
Condition Calculated load value % (Using CONSULT-II or GST)
At idle 14.0 - 33.0
At 2,500 rpm 12.0 - 25.0
Supply voltageBattery voltage (11 - 14V)
Output voltage at idle 1.0 - 1.3V*
Mass air flow (Using CONSULT-II or GST) 3.0 - 9.0 g
·m/sec at idle*
9.0 - 28.0 g· m/sec at 2,500 rpm*
Temperature °C (°F) Resistance kΩ
25 (77) 1.800 - 2.200
Temperature °C (°F) Resistance kΩ
20 (68) 2.1 - 2.9
50 (122) 0.68 - 1.00
90 (194) 0.236 - 0.260
Resistance [at 25°C (77 °F)] 2.3 - 4.3Ω
Resistance [at 25 °C (77 °F)] 5.0 - 7.0Ω
Resistance [at 25 °C (77 °F)] Approximately 1 - 15Ω
Page 1865 of 3383
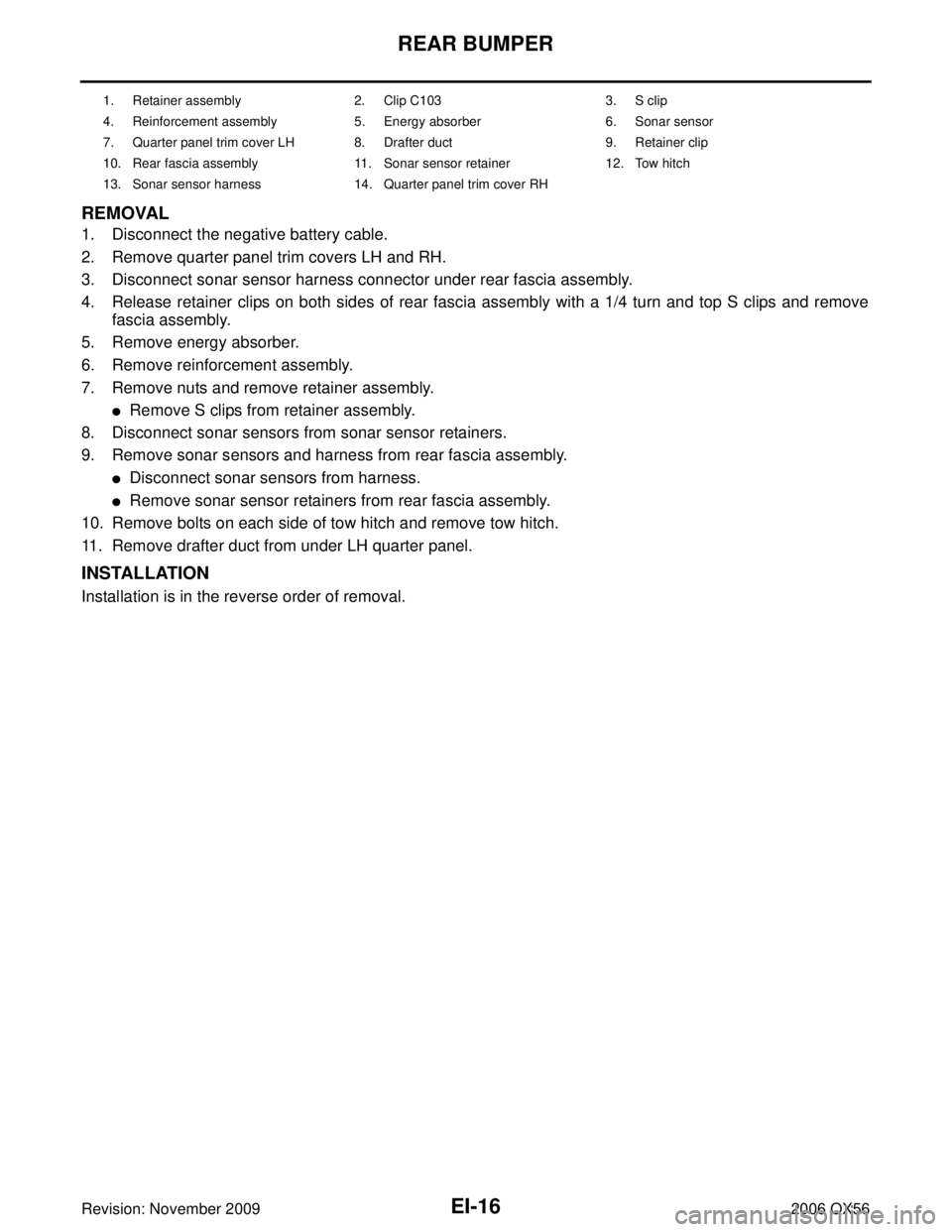
EI-16
REAR BUMPER
Revision: November 20092006 QX56
REMOVAL
1. Disconnect the negative battery cable.
2. Remove quarter panel trim covers LH and RH.
3. Disconnect sonar sensor harness connector under rear fascia assembly.
4. Release retainer clips on both sides of rear fascia assembly with a 1/4 turn and top S clips and remove
fascia assembly.
5. Remove energy absorber.
6. Remove reinforcement assembly.
7. Remove nuts and remove retainer assembly.
Remove S clips from retainer assembly.
8. Disconnect sonar sensors from sonar sensor retainers.
9. Remove sonar sensors and harness from rear fascia assembly.
Disconnect sonar sensors from harness.
Remove sonar sensor retainers from rear fascia assembly.
10. Remove bolts on each side of tow hitch and remove tow hitch.
11. Remove drafter duct from under LH quarter panel.
INSTALLATION
Installation is in the reverse order of removal.
1. Retainer assembly 2. Clip C103 3. S clip
4. Reinforcement assembly 5. Energy absorber 6. Sonar sensor
7. Quarter panel trim cover LH 8. Drafter duct 9. Retainer clip
10. Rear fascia assembly 11. Sonar sensor retainer 12. Tow hitch
13. Sonar sensor harness 14. Quarter panel trim cover RH
Page 1885 of 3383
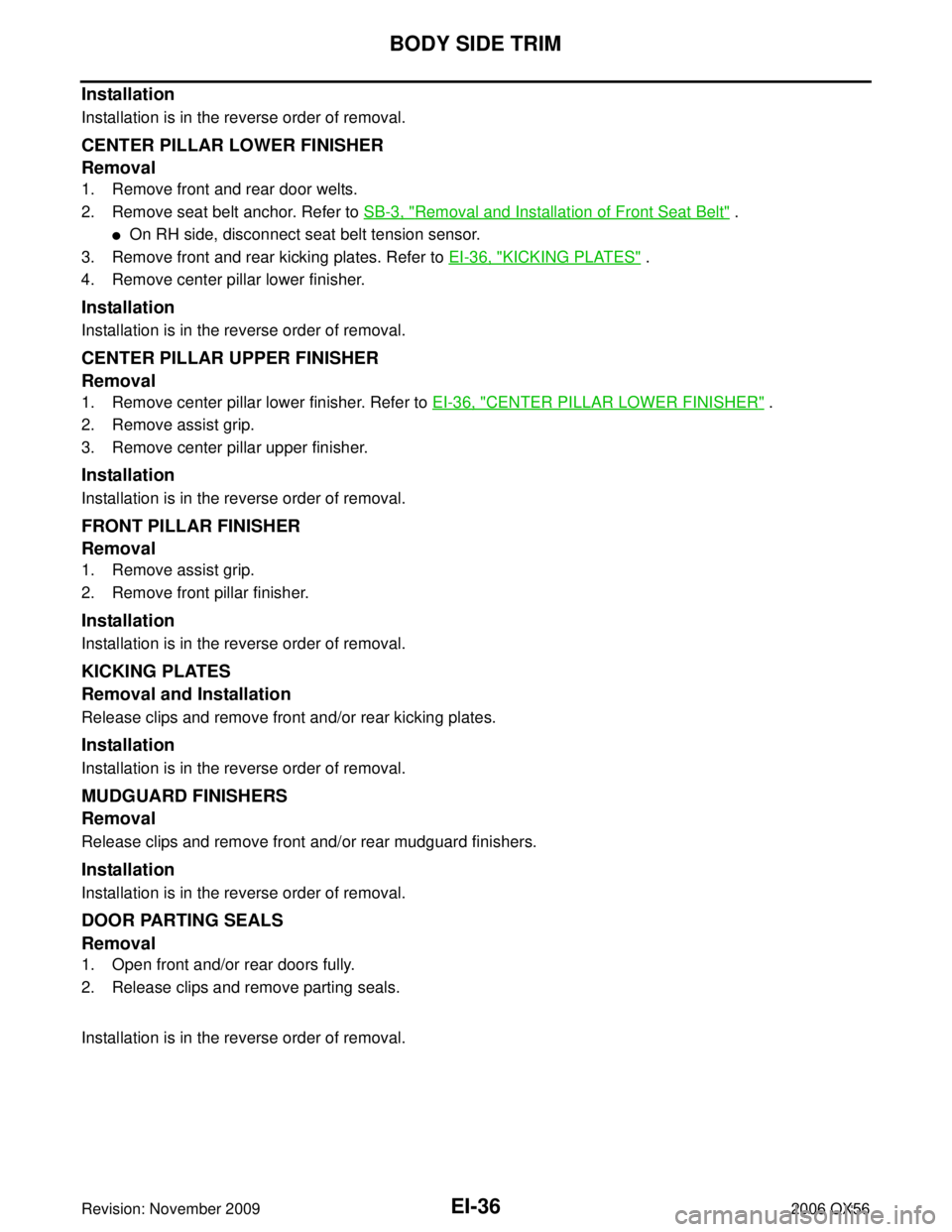
EI-36
BODY SIDE TRIM
Revision: November 20092006 QX56
Installation
Installation is in the reverse order of removal.
CENTER PILLAR LOWER FINISHER
Removal
1. Remove front and rear door welts.
2. Remove seat belt anchor. Refer to SB-3, "
Removal and Installation of Front Seat Belt" .
On RH side, disconnect seat belt tension sensor.
3. Remove front and rear kicking plates. Refer to EI-36, "
KICKING PLATES" .
4. Remove center pillar lower finisher.
Installation
Installation is in the reverse order of removal.
CENTER PILLAR UPPER FINISHER
Removal
1. Remove center pillar lower finisher. Refer to EI-36, "CENTER PILLAR LOWER FINISHER" .
2. Remove assist grip.
3. Remove center pillar upper finisher.
Installation
Installation is in the reverse order of removal.
FRONT PILLAR FINISHER
Removal
1. Remove assist grip.
2. Remove front pillar finisher.
Installation
Installation is in the reverse order of removal.
KICKING PLATES
Removal and Installation
Release clips and remove front and/or rear kicking plates.
Installation
Installation is in the reverse order of removal.
MUDGUARD FINISHERS
Removal
Release clips and remove front and/or rear mudguard finishers.
Installation
Installation is in the reverse order of removal.
DOOR PARTING SEALS
Removal
1. Open front and/or rear doors fully.
2. Release clips and remove parting seals.
Installation is in the reverse order of removal.
Page 1897 of 3383
EM-6Revision: November 2009
PREPARATION
2006 QX56
PREPARATIONPFP:00002
Special Service ToolsEBS00REQ
The actual shapes of Kent-Moore tools may differ from those of special service tools illustrated here.Tool number
(Kent-Moore No.)
Tool name Description
KV10111100
(J-37228)
Seal cutter Removing steel oil pan and rear timing chain
case
—
(J-44626)
Air fuel sensor Socket Loosening or tightening air fuel ratio A/F sen-
sor
a: 22 mm (0.87 in)
EG15050500
(J-45402)
Compression gauge adapter Inspecting compression pressure
KV10116200
(J-26336-A)
Valve spring compressor
1. KV10115900
(J-26336-20)
Attachment
2. KV10109220
( — )
Adapter Disassembling valve mechanism
Part (1) is a component of KV10116200 (J-
26336-A), but part (2) is not.
KV10112100
(BT-8653-A)
Angle wrench Tightening bolts for cylinder head, main bear-
ing cap and connecting rod cap
KV10107902
(J-38959)
Valve oil seal puller Removing valve oil seal
S-NT046
LBIA0444E
ZZA1225D
PBIC1650E
S-NT014
S-NT011
Page 1900 of 3383
PREPARATIONEM-9
C
DE
F
G H
I
J
K L
M A
EM
Revision: November 2009 2006 QX56
Valve guide reamer1: Reaming valve guide hole
2: Reaming hole for oversize valve guide
Intake & Exhaust:
d
1 : 6.0 mm (0.236 in) dia.
d
2 : 10.175 - 10.196 mm (0.4006 - 0.4014 in)
dia.
Front oil seal drift Installing front oil seal
Rear oil seal drift Installing rear oil seal
(J-43897-18)
(J-43897-12)
Oxygen sensor thread cleaner Reconditioning the exhaust system threads
before installing a new A/F sensor and heated
oxygen sensor (Use with anti-seize lubricant
shown below.)
a: J-43897-18 (18 mm dia.) (0.71 in) for zir-
conia heated oxygen sensor
b: J-43897-12 (12 mm dia.) (0.55 in) for tita-
nia heated oxygen sensor
Anti-seize lubricant (Permatex 133AR
or equivalent meeting MIL specifica-
tion MIL-A-907) Lubricating A/F sensors and heated oxygen
sensor thread cleaning tool when recondition-
ing exhaust system threads
(Kent-Moore No.)
Tool name
Description
S-NT016
ZZA0012D
ZZA0025D
AEM488
AEM489
Page 1912 of 3383
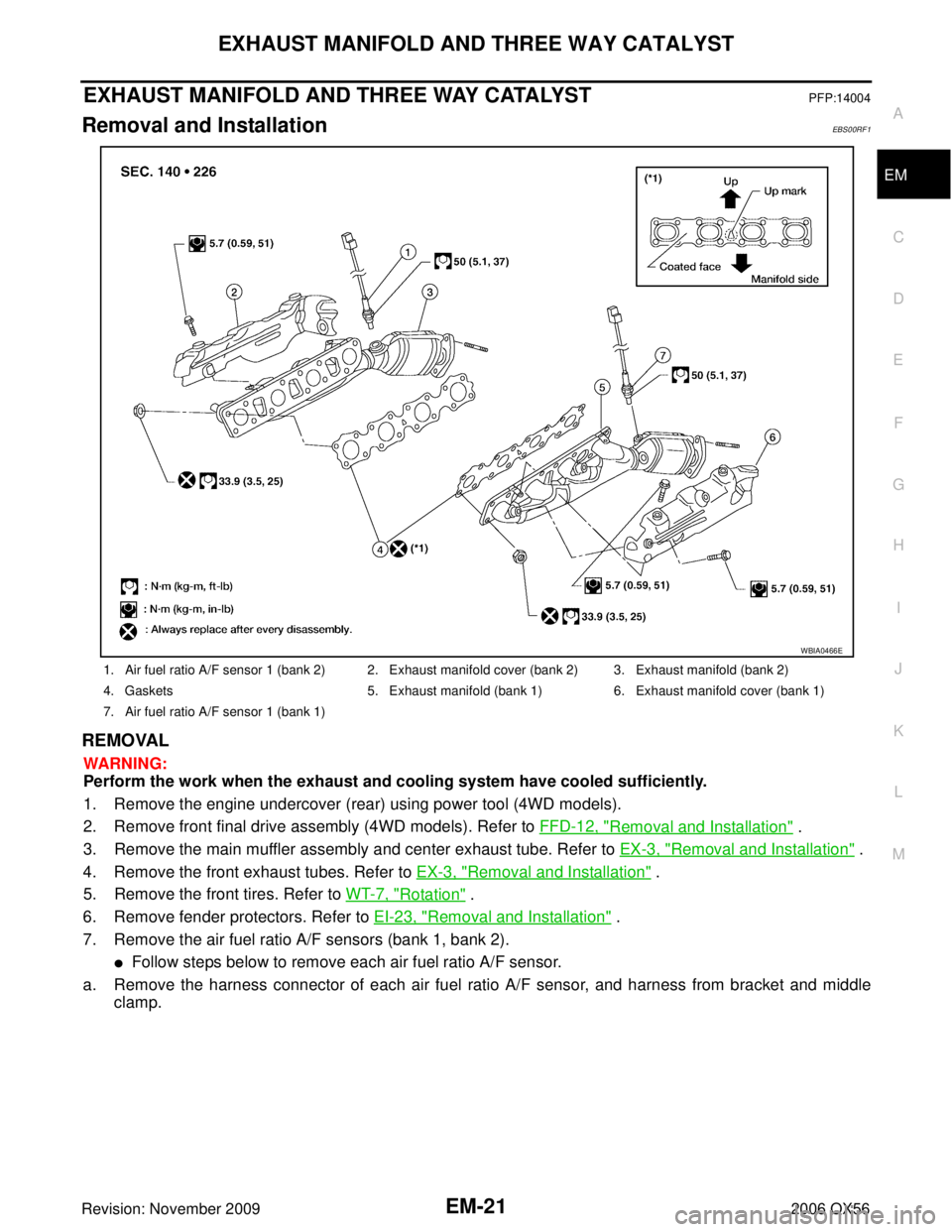
EXHAUST MANIFOLD AND THREE WAY CATALYSTEM-21
C
DE
F
G H
I
J
K L
M A
EM
Revision: November 2009 2006 QX56
EXHAUST MANIFOLD AND THREE WAY CATALYSTPFP:14004
Removal and InstallationEBS00RF1
REMOVAL
WARNING:
Perform the work when the exhaust and cooling system have cooled sufficiently.
1. Remove the engine undercover (rear) using power tool (4WD models).
2. Remove front final drive assembly (4WD models). Refer to FFD-12, "
Removal and Installation" .
3. Remove the main muffler assembly and center exhaust tube. Refer to EX-3, "
Removal and Installation" .
4. Remove the front exhaust tubes. Refer to EX-3, "
Removal and Installation" .
5. Remove the front tires. Refer to WT-7, "
Rotation" .
6. Remove fender protectors. Refer to EI-23, "
Removal and Installation" .
7. Remove the air fuel ratio A/F sensors (bank 1, bank 2).
Follow steps below to remove each air fuel ratio A/F sensor.
a. Remove the harness connector of each air fuel ratio A/F sensor, and harness from bracket and middle clamp.
1. Air fuel ratio A/F sensor 1 (bank 2) 2. Exhaust manifold cover (bank 2) 3. Exhaust manifold (bank 2)
4. Gaskets 5. Exhaust manifold (bank 1) 6. Exhaust manifold cover (bank 1)
7. Air fuel ratio A/F sensor 1 (bank 1)
WBIA0466E
Page 1913 of 3383
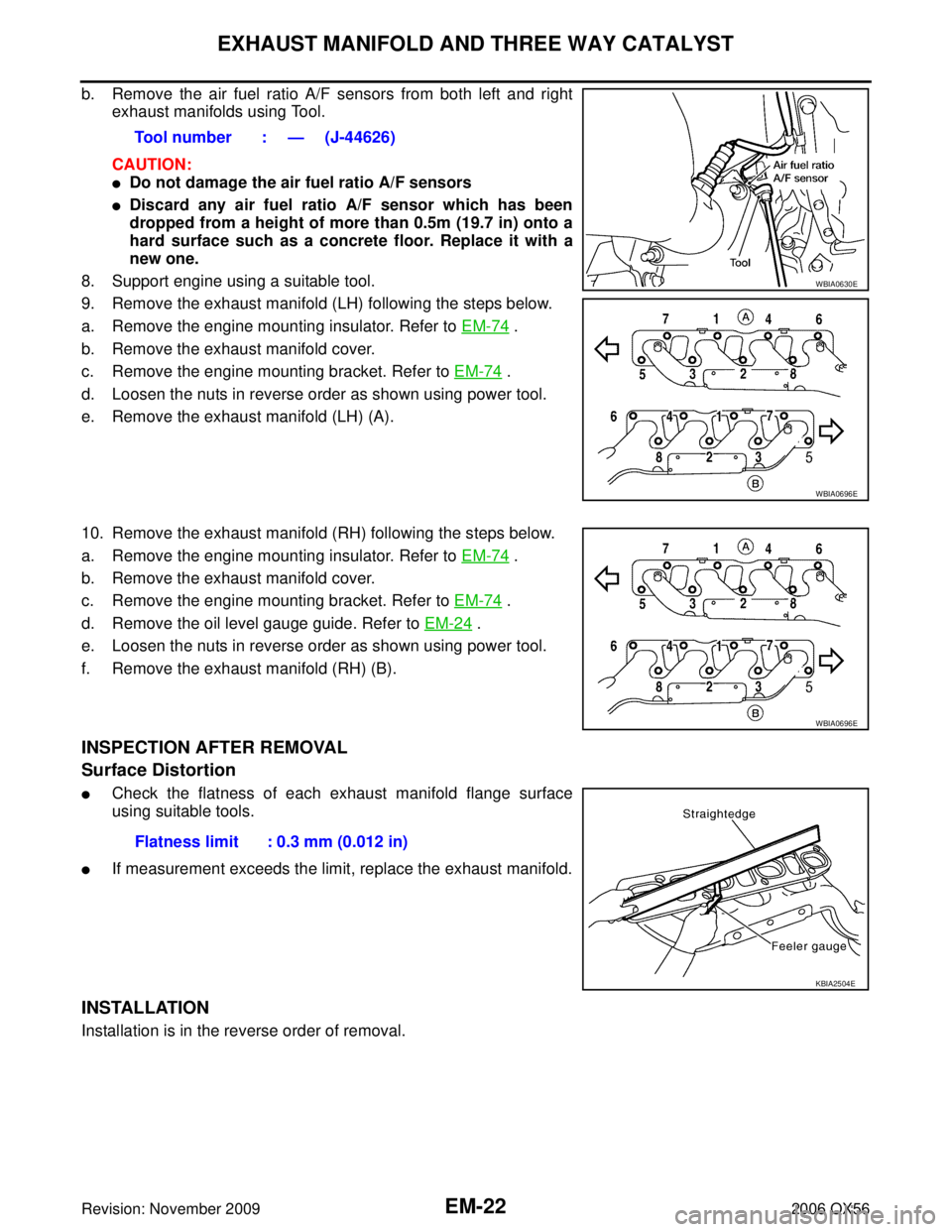
EM-22Revision: November 2009
EXHAUST MANIFOLD AND THREE WAY CATALYST
2006 QX56
b. Remove the air fuel ratio A/F sensors from both left and rightexhaust manifolds using Tool.
CAUTION:
Do not damage the air fuel ratio A/F sensors
Discard any air fuel ratio A/F sensor which has been
dropped from a height of more than 0.5m (19.7 in) onto a
hard surface such as a concrete floor. Replace it with a
new one.
8. Support engine using a suitable tool.
9. Remove the exhaust manifold (LH) following the steps below.
a. Remove the engine mounting insulator. Refer to EM-74
.
b. Remove the exhaust manifold cover.
c. Remove the engine mounting bracket. Refer to EM-74
.
d. Loosen the nuts in reverse order as shown using power tool.
e. Remove the exhaust manifold (LH) (A).
10. Remove the exhaust manifold (RH) following the steps below.
a. Remove the engine mounting insulator. Refer to EM-74
.
b. Remove the exhaust manifold cover.
c. Remove the engine mounting bracket. Refer to EM-74
.
d. Remove the oil level gauge guide. Refer to EM-24
.
e. Loosen the nuts in reverse order as shown using power tool.
f. Remove the exhaust manifold (RH) (B).
INSPECTION AFTER REMOVAL
Surface Distortion
Check the flatness of each exhaust manifold flange surface
using suitable tools.
If measurement exceeds the limit, replace the exhaust manifold.
INSTALLATION
Installation is in the reverse order of removal. Tool number : — (J-44626)
WBIA0630E
WBIA0696E
WBIA0696E
Flatness limit : 0.3 mm (0.012 in)
KBIA2504E