Page 929 of 3383
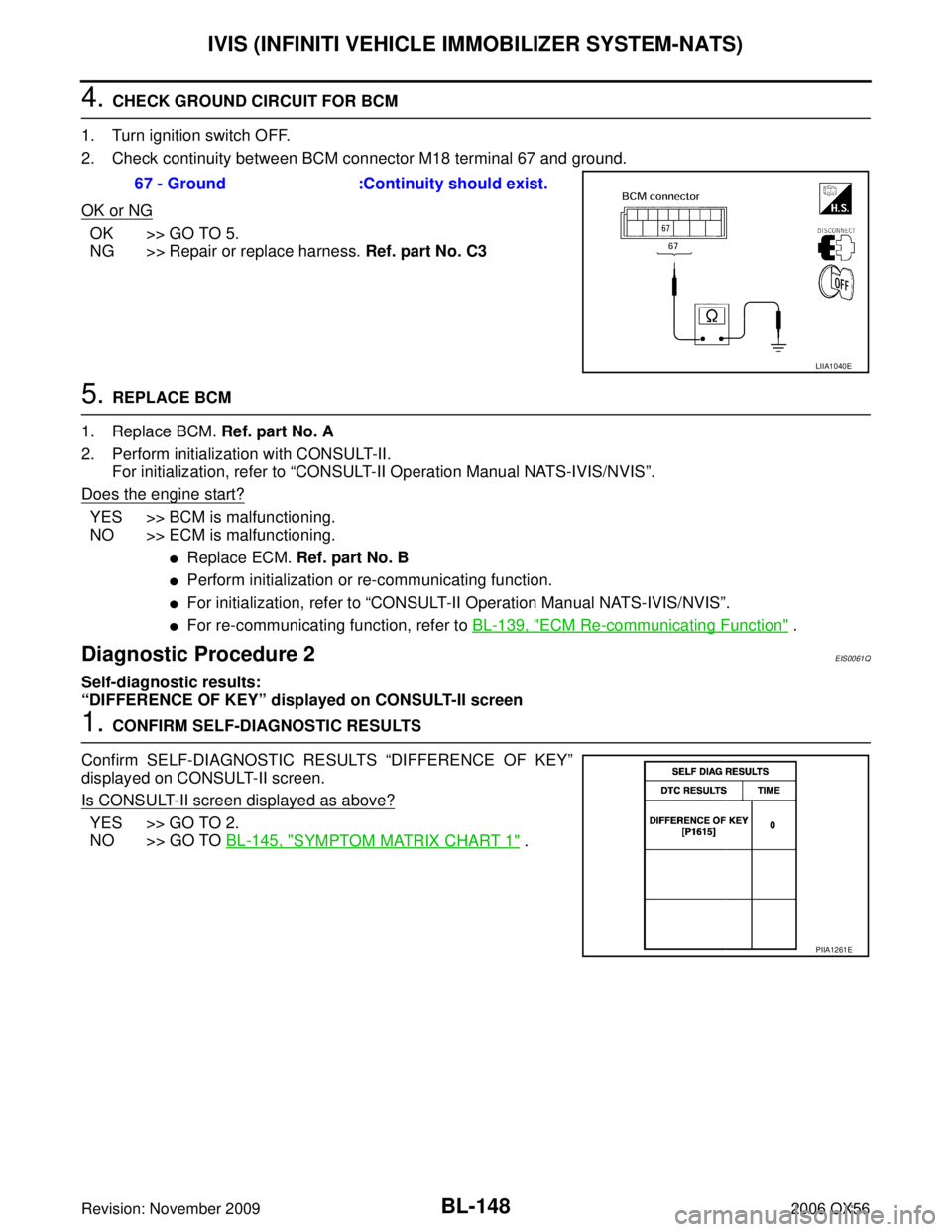
BL-148
IVIS (INFINITI VEHICLE IMMOBILIZER SYSTEM-NATS)
Revision: November 20092006 QX56
4. CHECK GROUND CIRCUIT FOR BCM
1. Turn ignition switch OFF.
2. Check continuity between BCM connector M18 terminal 67 and ground.
OK or NG
OK >> GO TO 5.
NG >> Repair or replace harness. Ref. part No. C3
5. REPLACE BCM
1. Replace BCM. Ref. part No. A
2. Perform initialization with CONSULT-II. For initialization, refer to “CONSULT-II Operation Manual NATS-IVIS/NVIS ”.
Does the engine start?
YES >> BCM is malfunctioning.
NO >> ECM is malfunctioning.
Replace ECM. Ref. part No. B
Perform initialization or re-communicating function.
For initialization, refer to “CONSULT-II Operation Manual NATS-IVIS/NVIS ”.
For re-communicating function, refer to BL-139, "ECM Re-communicating Function" .
Diagnostic Procedure 2EIS0061Q
Self-diagnostic results:
“DIFFERENCE OF KEY” displayed on CONSULT-II screen
1. CONFIRM SELF-DIAGNOSTIC RESULTS
Confirm SELF-DIAGNOSTIC RESULTS “DIFFERENCE OF KEY”
displayed on CONSULT-II screen.
Is CONSULT-II screen displayed as above?
YES >> GO TO 2.
NO >> GO TO BL-145, "
SYMPTOM MATRIX CHART 1" .
67 - Ground
:Continuity should exist.
LIIA1040E
PIIA1261E
Page 932 of 3383
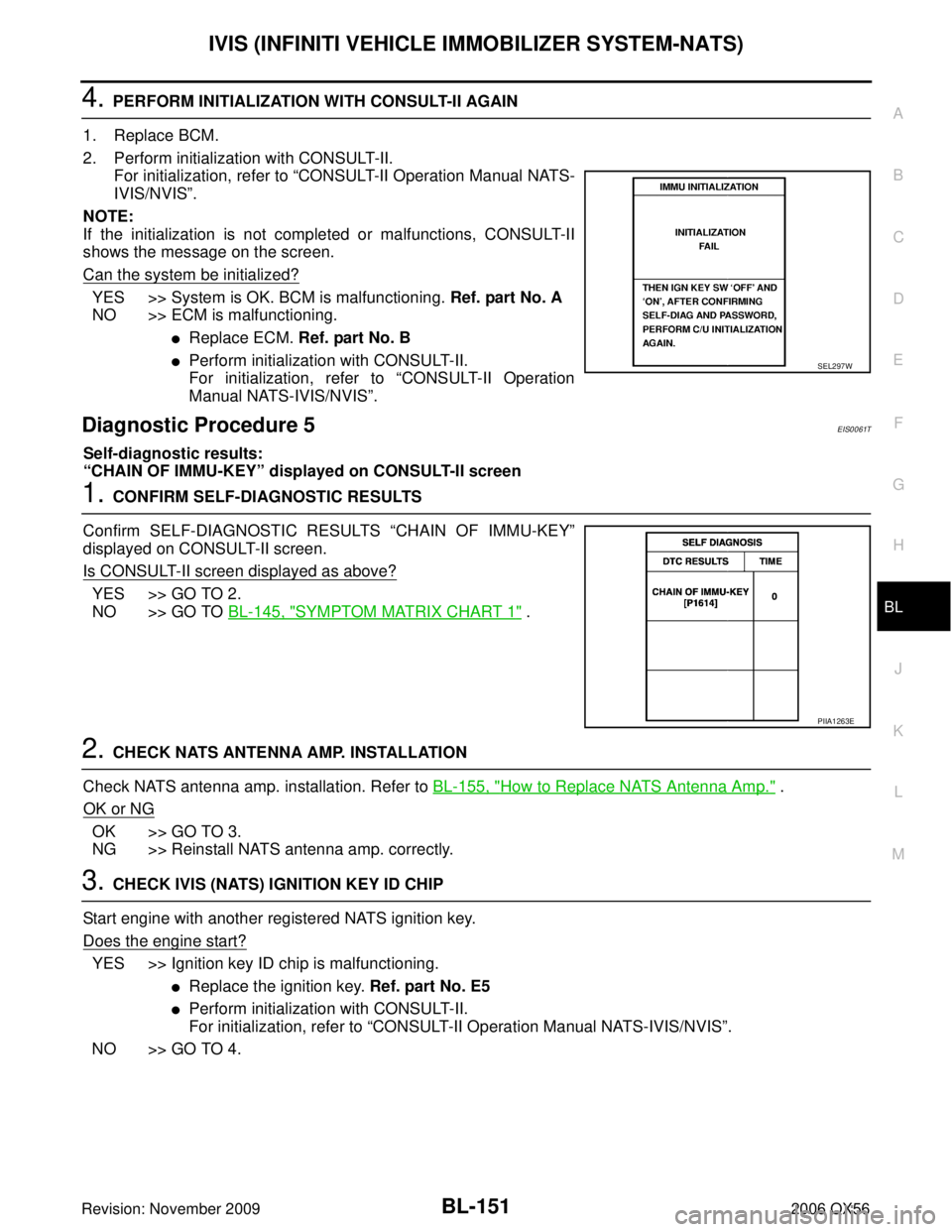
IVIS (INFINITI VEHICLE IMMOBILIZER SYSTEM-NATS)BL-151
C
DE
F
G H
J
K L
M A
B
BL
Revision: November 2009 2006 QX56
4. PERFORM INITIALIZATION WITH CONSULT-II AGAIN
1. Replace BCM.
2. Perform initialization with CONSULT-II. For initialization, refer to “CONSULT-II Operation Manual NATS-
IVIS/NVIS ”.
NOTE:
If the initialization is not completed or malfunctions, CONSULT-II
shows the message on the screen.
Can the system be initialized?
YES >> System is OK. BCM is malfunctioning. Ref. part No. A
NO >> ECM is malfunctioning.
Replace ECM. Ref. part No. B
Perform initialization with CONSULT-II.
For initialization, refer to “CONSULT-II Operation
Manual NATS-IVIS/NVIS ”.
Diagnostic Procedure 5EIS0061T
Self-diagnostic results:
“CHAIN OF IMMU-KEY” displayed on CONSULT-II screen
1. CONFIRM SELF-DIAGNOSTIC RESULTS
Confirm SELF-DIAGNOSTIC RESULTS “CHAIN OF IMMU-KEY ”
displayed on CONSULT-II screen.
Is CONSULT-II screen displayed as above?
YES >> GO TO 2.
NO >> GO TO BL-145, "
SYMPTOM MATRIX CHART 1" .
2. CHECK NATS ANTENNA AMP. INSTALLATION
Check NATS antenna amp. installation. Refer to BL-155, "
How to Replace NATS Antenna Amp." .
OK or NG
OK >> GO TO 3.
NG >> Reinstall NATS antenna amp. correctly.
3. CHECK IVIS (NATS) IGNITION KEY ID CHIP
Start engine with another registered NATS ignition key.
Does the engine start?
YES >> Ignition key ID chip is malfunctioning.
Replace the ignition key. Ref. part No. E5
Perform initialization with CONSULT-II.
For initialization, refer to “CONSULT-II Operation Manual NATS-IVIS/NVIS ”.
NO >> GO TO 4.
SEL297W
PIIA1263E
Page 935 of 3383
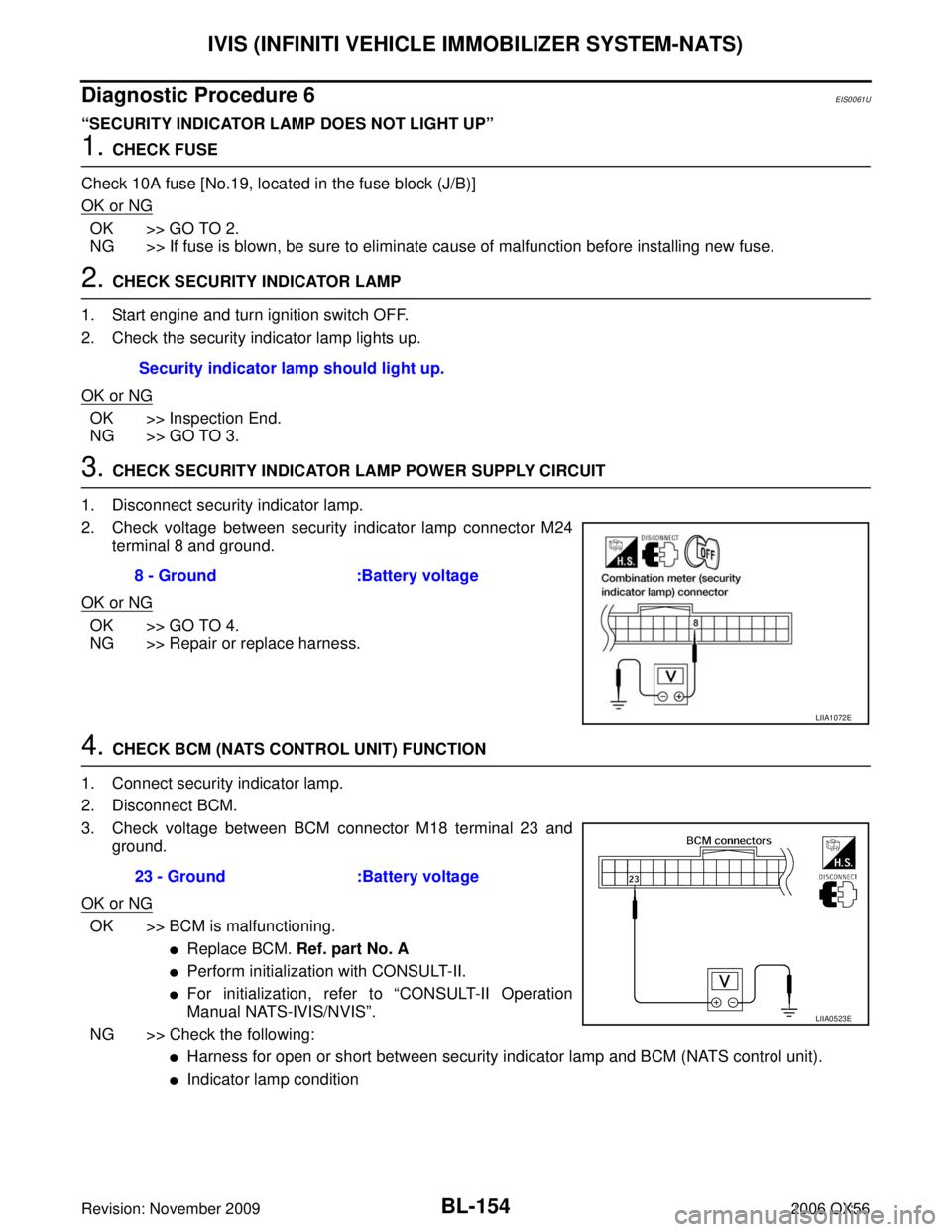
BL-154
IVIS (INFINITI VEHICLE IMMOBILIZER SYSTEM-NATS)
Revision: November 20092006 QX56
Diagnostic Procedure 6EIS0061U
“SECURITY INDICATOR LAMP DOES NOT LIGHT UP”
1. CHECK FUSE
Check 10A fuse [No.19, located in the fuse block (J/B)]
OK or NG
OK >> GO TO 2.
NG >> If fuse is blown, be sure to eliminate cause of malfunction before installing new fuse.
2. CHECK SECURITY INDICATOR LAMP
1. Start engine and turn ignition switch OFF.
2. Check the security indicator lamp lights up.
OK or NG
OK >> Inspection End.
NG >> GO TO 3.
3. CHECK SECURITY INDICATOR LAMP POWER SUPPLY CIRCUIT
1. Disconnect security indicator lamp.
2. Check voltage between security indicator lamp connector M24 terminal 8 and ground.
OK or NG
OK >> GO TO 4.
NG >> Repair or replace harness.
4. CHECK BCM (NATS CONTROL UNIT) FUNCTION
1. Connect security indicator lamp.
2. Disconnect BCM.
3. Check voltage between BCM connector M18 terminal 23 and ground.
OK or NG
OK >> BCM is malfunctioning.
Replace BCM. Ref. part No. A
Perform initialization with CONSULT-II.
For initialization, refer to “CONSULT-II Operation
Manual NATS-IVIS/NVIS ”.
NG >> Check the following:
Harness for open or short between security indicator lamp and BCM (NATS control unit).
Indicator lamp condition
Security indicator lamp should light up.
8 - Ground
:Battery voltage
LIIA1072E
23 - Ground :Battery voltage
LIIA0523E
Page 1000 of 3383
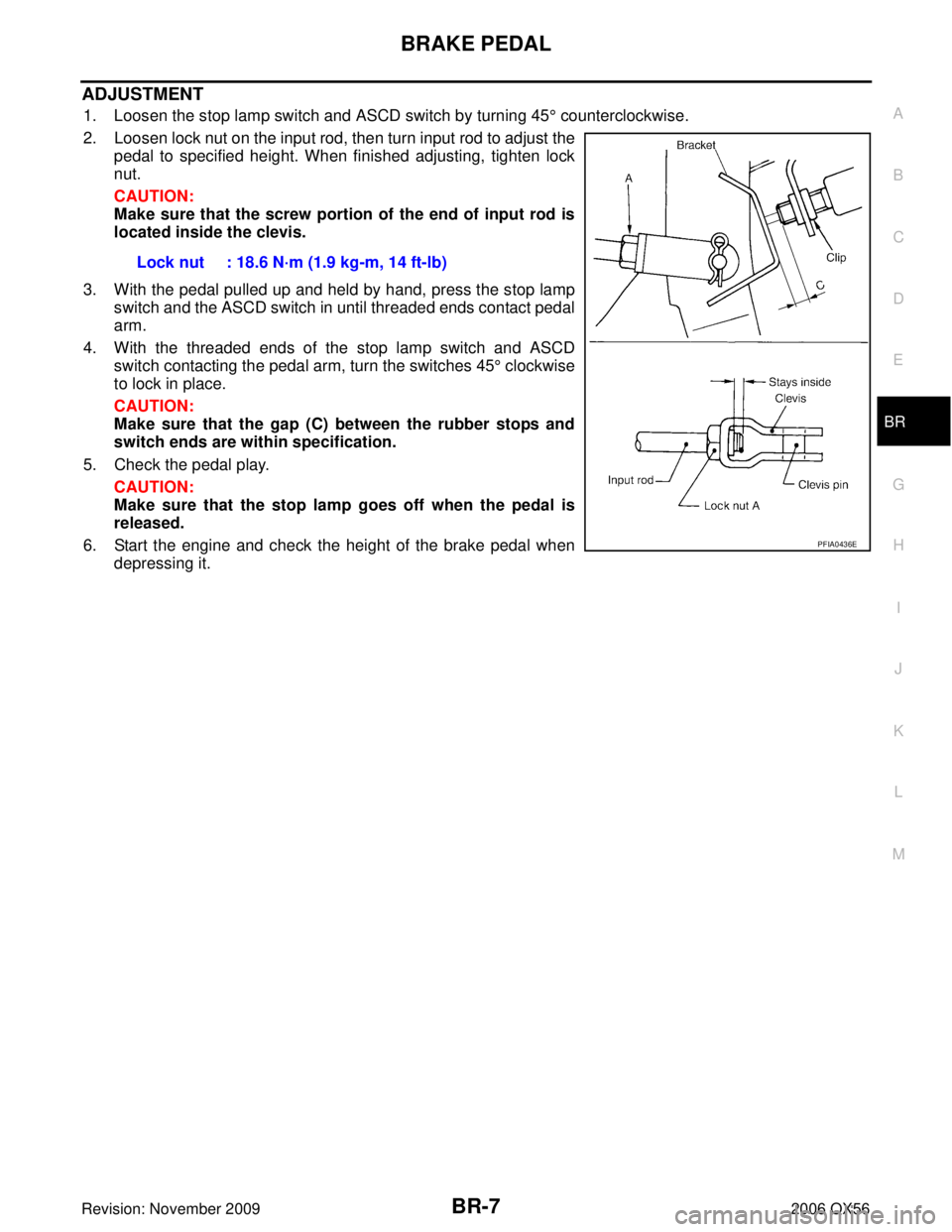
BRAKE PEDALBR-7
C
DE
G H
I
J
K L
M A
B
BR
Revision: November 2009 2006 QX56
ADJUSTMENT
1. Loosen the stop lamp switch and ASCD switch by turning 45° counterclockwise.
2. Loosen lock nut on the input rod, then turn input rod to adjust the pedal to specified height. When finished adjusting, tighten lock
nut.
CAUTION:
Make sure that the screw portion of the end of input rod is
located inside the clevis.
3. With the pedal pulled up and held by hand, press the stop lamp switch and the ASCD switch in until threaded ends contact pedal
arm.
4. With the threaded ends of the stop lamp switch and ASCD switch contacting the pedal arm, turn the switches 45 ° clockwise
to lock in place.
CAUTION:
Make sure that the gap (C) between the rubber stops and
switch ends are within specification.
5. Check the pedal play. CAUTION:
Make sure that the stop lamp goes off when the pedal is
released.
6. Start the engine and check the height of the brake pedal when depressing it.Lock nut : 18.6 N·m (1.9 kg-m, 14 ft-lb)
PFIA0436E
Page 1007 of 3383
BR-14
BRAKE PIPING AND HOSE
Revision: November 20092006 QX56
Inspection After InstallationEFS004W8
CAUTION:
If a leak is detected at the connections, retighten it or, if necessary, replace the damaged part.
1. Check brake tubes and hose connections for fluid leaks, damage, twist, deformation, contact with other
parts, and loose connections. Replace any damage parts.
2. While depressing brake pedal under a force of 785 N (80 kg-f, 177 lb-f) with engine running for approxi- mately 5 seconds, check for fluid leakage from each part.
Page 1010 of 3383
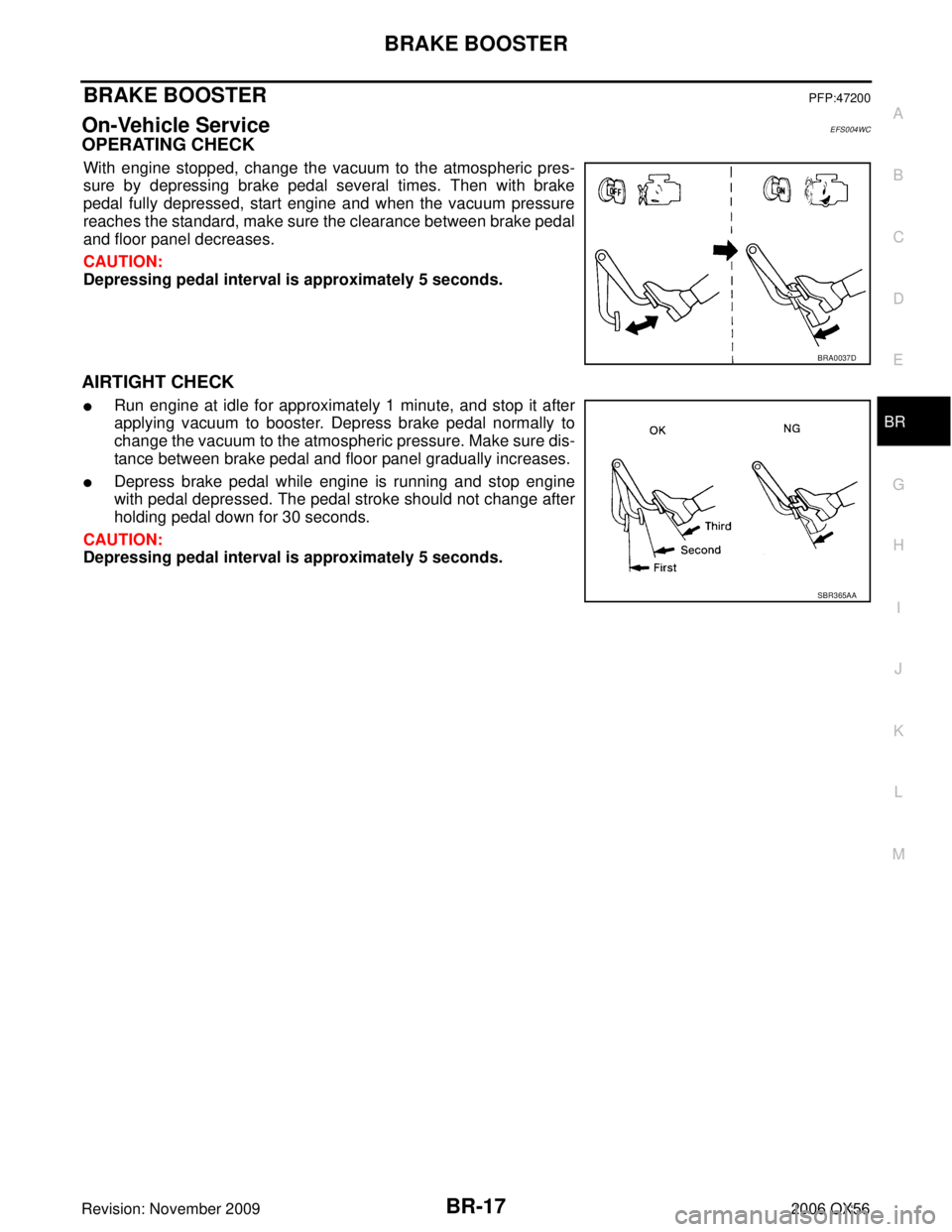
BRAKE BOOSTERBR-17
C
DE
G H
I
J
K L
M A
B
BR
Revision: November 2009 2006 QX56
BRAKE BOOSTERPFP:47200
On-Vehicle ServiceEFS004WC
OPERATING CHECK
With engine stopped, change the vacuum to the atmospheric pres-
sure by depressing brake pedal several times. Then with brake
pedal fully depressed, start engine and when the vacuum pressure
reaches the standard, make sure the clearance between brake pedal
and floor panel decreases.
CAUTION:
Depressing pedal interval is approximately 5 seconds.
AIRTIGHT CHECK
Run engine at idle for approximately 1 minute, and stop it after
applying vacuum to booster. Depress brake pedal normally to
change the vacuum to the atmospheric pressure. Make sure dis-
tance between brake pedal and floor panel gradually increases.
Depress brake pedal while engine is running and stop engine
with pedal depressed. The pedal stroke should not change after
holding pedal down for 30 seconds.
CAUTION:
Depressing pedal interval is approximately 5 seconds.
BRA0037D
SBR365AA
Page 1011 of 3383
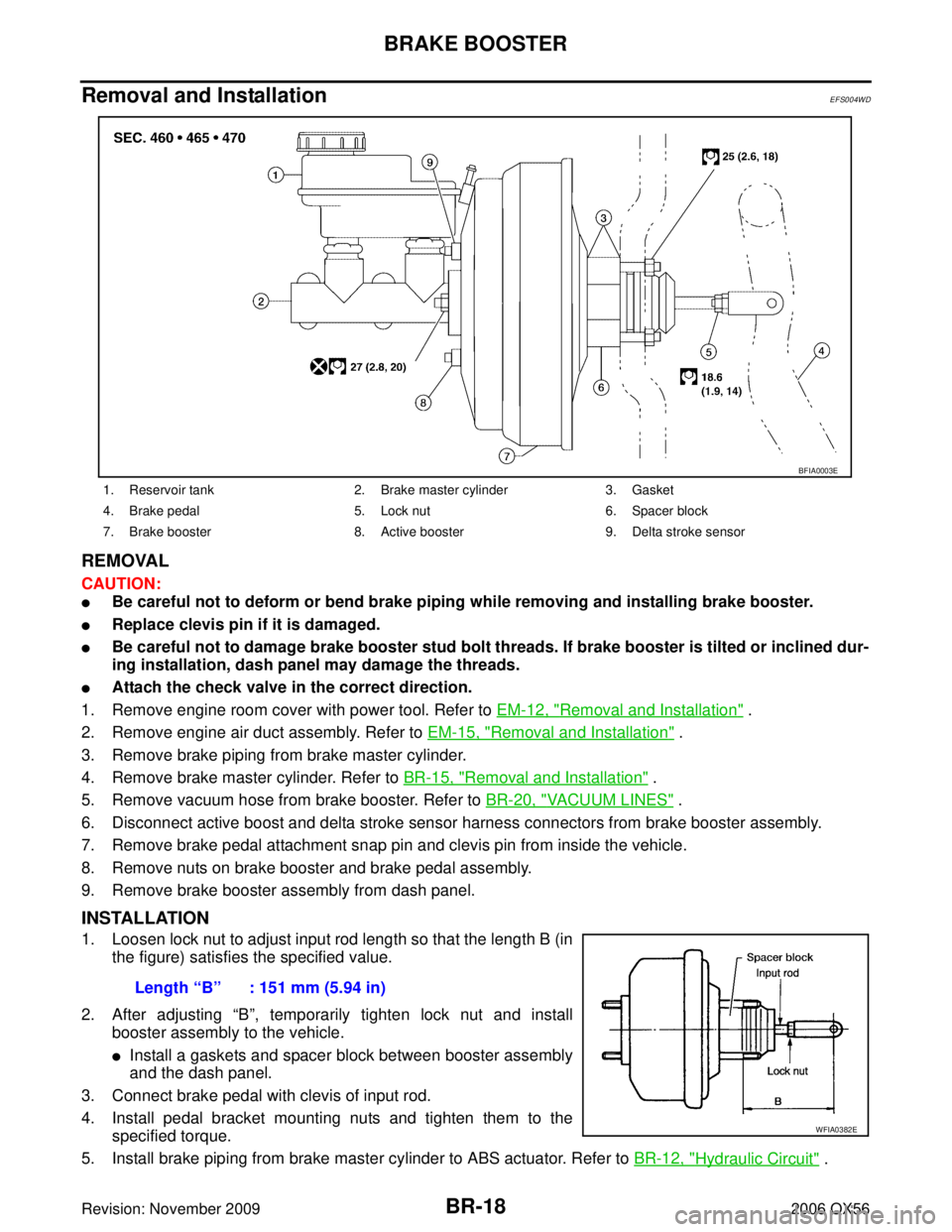
BR-18
BRAKE BOOSTER
Revision: November 20092006 QX56
Removal and InstallationEFS004WD
REMOVAL
CAUTION:
Be careful not to deform or bend brake piping while removing and installing brake booster.
Replace clevis pin if it is damaged.
Be careful not to damage brake booster stud bolt threads. If brake booster is tilted or inclined dur-
ing installation, dash panel may damage the threads.
Attach the check valve in the correct direction.
1. Remove engine room cover with power tool. Refer to EM-12, "
Removal and Installation" .
2. Remove engine air duct assembly. Refer to EM-15, "
Removal and Installation" .
3. Remove brake piping from brake master cylinder.
4. Remove brake master cylinder. Refer to BR-15, "
Removal and Installation" .
5. Remove vacuum hose from brake booster. Refer to BR-20, "
VACUUM LINES" .
6. Disconnect active boost and delta stroke sensor harness connectors from brake booster assembly.
7. Remove brake pedal attachment snap pin and clevis pin from inside the vehicle.
8. Remove nuts on brake booster and brake pedal assembly.
9. Remove brake booster assembly from dash panel.
INSTALLATION
1. Loosen lock nut to adjust input rod length so that the length B (in the figure) satisfies the specified value.
2. After adjusting “B”, temporarily tighten lock nut and install
booster assembly to the vehicle.
Install a gaskets and spacer block between booster assembly
and the dash panel.
3. Connect brake pedal with clevis of input rod.
4. Install pedal bracket mounting nuts and tighten them to the specified torque.
5. Install brake piping from brake master cylinder to ABS actuator. Refer to BR-12, "
Hydraulic Circuit" .
1. Reservoir tank 2. Brake master cylinder 3. Gasket
4. Brake pedal 5. Lock nut 6. Spacer block
7. Brake booster 8. Active booster 9. Delta stroke sensor
BFIA0003E
Length “B” : 151 mm (5.94 in)
WFIA0382E
Page 1025 of 3383
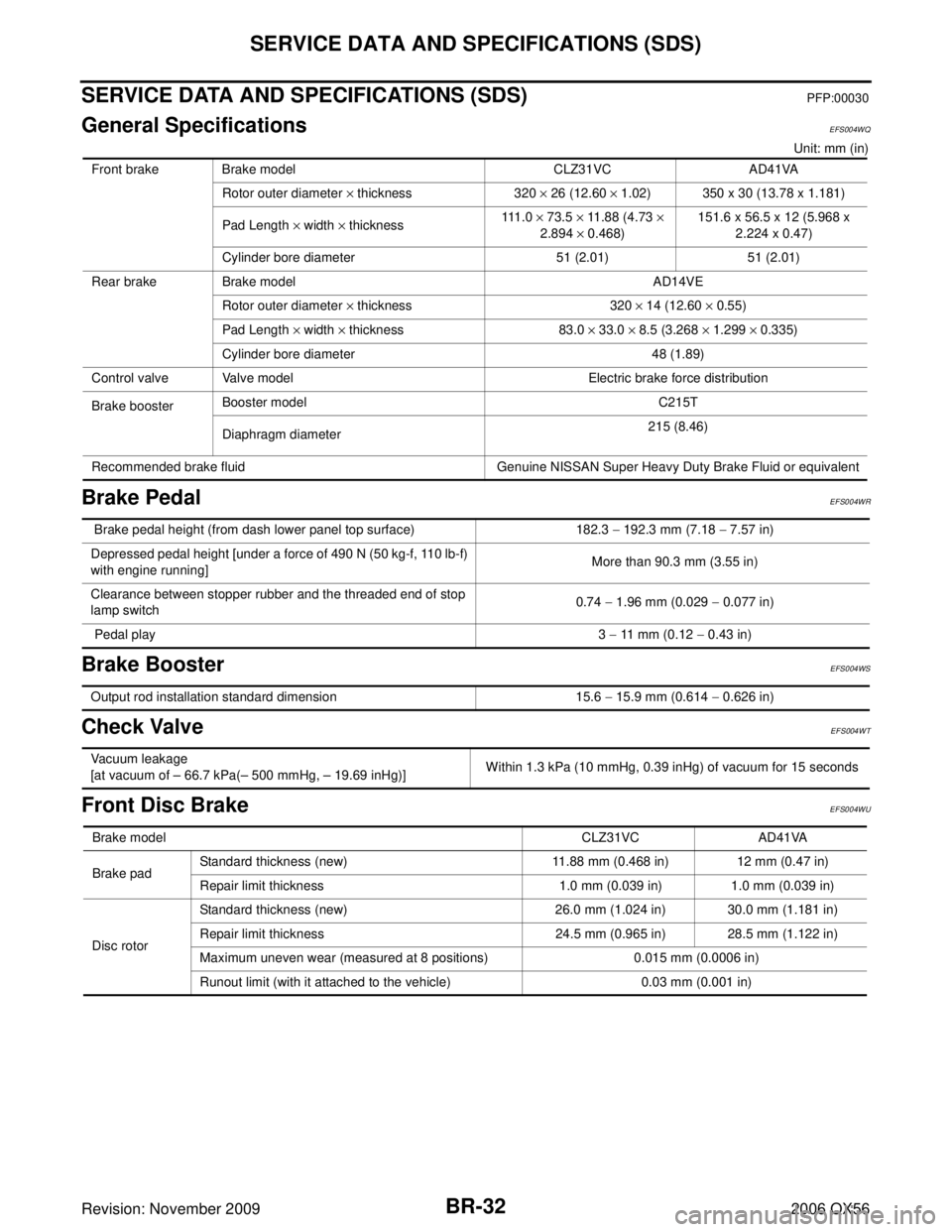
BR-32
SERVICE DATA AND SPECIFICATIONS (SDS)
Revision: November 20092006 QX56
SERVICE DATA AND SPECIFICATIONS (SDS)PFP:00030
General SpecificationsEFS004WQ
Unit: mm (in)
Brake PedalEFS004WR
Brake BoosterEFS004WS
Check ValveEFS004WT
Front Disc BrakeEFS004WU
Front brake Brake modelCLZ31VCAD41VA
Rotor outer diameter × thickness 320 × 26 (12.60 × 1.02) 350 x 30 (13.78 x 1.181)
Pad Length × width × thickness 111 . 0
× 73.5 × 11.88 (4.73 ×
2.894 × 0.468) 151.6 x 56.5 x 12 (5.968 x
2.224 x 0.47)
Cylinder bore diameter 51 (2.01)51 (2.01)
Rear brake Brake model AD14VE
Rotor outer diameter × thickness 320 × 14 (12.60 × 0.55)
Pad Length × width × thickness 83.0 × 33.0 × 8.5 (3.268 × 1.299 × 0.335)
Cylinder bore diameter 48 (1.89)
Control valve Valve model Electric brake force distribution
Brake booster Booster model
C215T
Diaphragm diameter 215 (8.46)
Recommended brake fluid Genuine NISSAN Super Heavy Duty Brake Fluid or equivalent
Brake pedal height (from dash lower panel top surface) 182.3 − 192.3 mm (7.18 − 7.57 in)
Depressed pedal height [under a force of 490 N (50 kg-f, 110 lb-f)
with engine running] More than 90.3 mm (3.55 in)
Clearance between stopper rubber and the threaded end of stop
lamp switch 0.74
− 1.96 mm (0.029 − 0.077 in)
Pedal play 3 − 11 mm (0.12 − 0.43 in)
Output rod installation standard dimension 15.6 − 15.9 mm (0.614 − 0.626 in)
Vacuum leakage
[at vacuum of – 66.7 kPa(– 500 mmHg, – 19.69 inHg)] Within 1.3 kPa (10 mmHg, 0.39 inHg) of vacuum for 15 seconds
Brake model
CLZ31VCAD41VA
Brake pad Standard thickness (new)
11.88 mm (0.468 in)12 mm (0.47 in)
Repair limit thickness 1.0 mm (0.039 in)1.0 mm (0.039 in)
Disc rotor Standard thickness (new)
26.0 mm (1.024 in) 30.0 mm (1.181 in)
Repair limit thickness 24.5 mm (0.965 in) 28.5 mm (1.122 in)
Maximum uneven wear (measured at 8 positions) 0.015 mm (0.0006 in)
Runout limit (with it attached to the vehicle) 0.03 mm (0.001 in)