Page 347 of 557
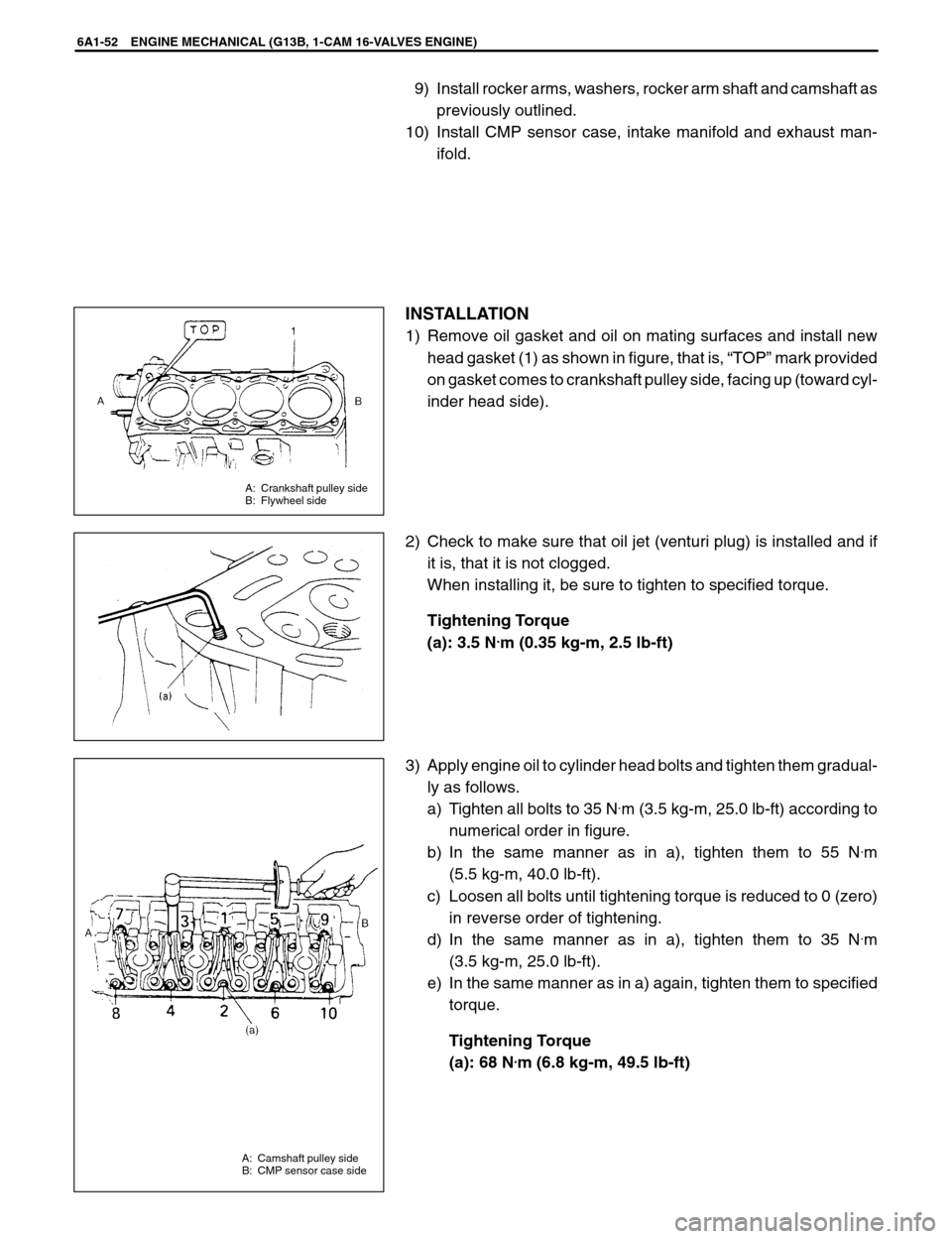
A: Crankshaft pulley side
B: Flywheel side
A: Camshaft pulley side
B: CMP sensor case side
6A1-52 ENGINE MECHANICAL (G13B, 1-CAM 16-VALVES ENGINE)
9) Install rocker arms, washers, rocker arm shaft and camshaft as
previously outlined.
10) Install CMP sensor case, intake manifold and exhaust man-
ifold.
INSTALLATION
1) Remove oil gasket and oil on mating surfaces and install new
head gasket (1) as shown in figure, that is, “TOP” mark provided
on gasket comes to crankshaft pulley side, facing up (toward cyl-
inder head side).
2) Check to make sure that oil jet (venturi plug) is installed and if
it is, that it is not clogged.
When installing it, be sure to tighten to specified torque.
Tightening Torque
(a): 3.5 N
.m (0.35 kg-m, 2.5 lb-ft)
3) Apply engine oil to cylinder head bolts and tighten them gradual-
ly as follows.
a) Tighten all bolts to 35 N
.m (3.5 kg-m, 25.0 lb-ft) according to
numerical order in figure.
b) In the same manner as in a), tighten them to 55 N
.m
(5.5 kg-m, 40.0 lb-ft).
c) Loosen all bolts until tightening torque is reduced to 0 (zero)
in reverse order of tightening.
d) In the same manner as in a), tighten them to 35 N
.m
(3.5 kg-m, 25.0 lb-ft).
e) In the same manner as in a) again, tighten them to specified
torque.
Tightening Torque
(a): 68 N
.m (6.8 kg-m, 49.5 lb-ft)
Page 349 of 557
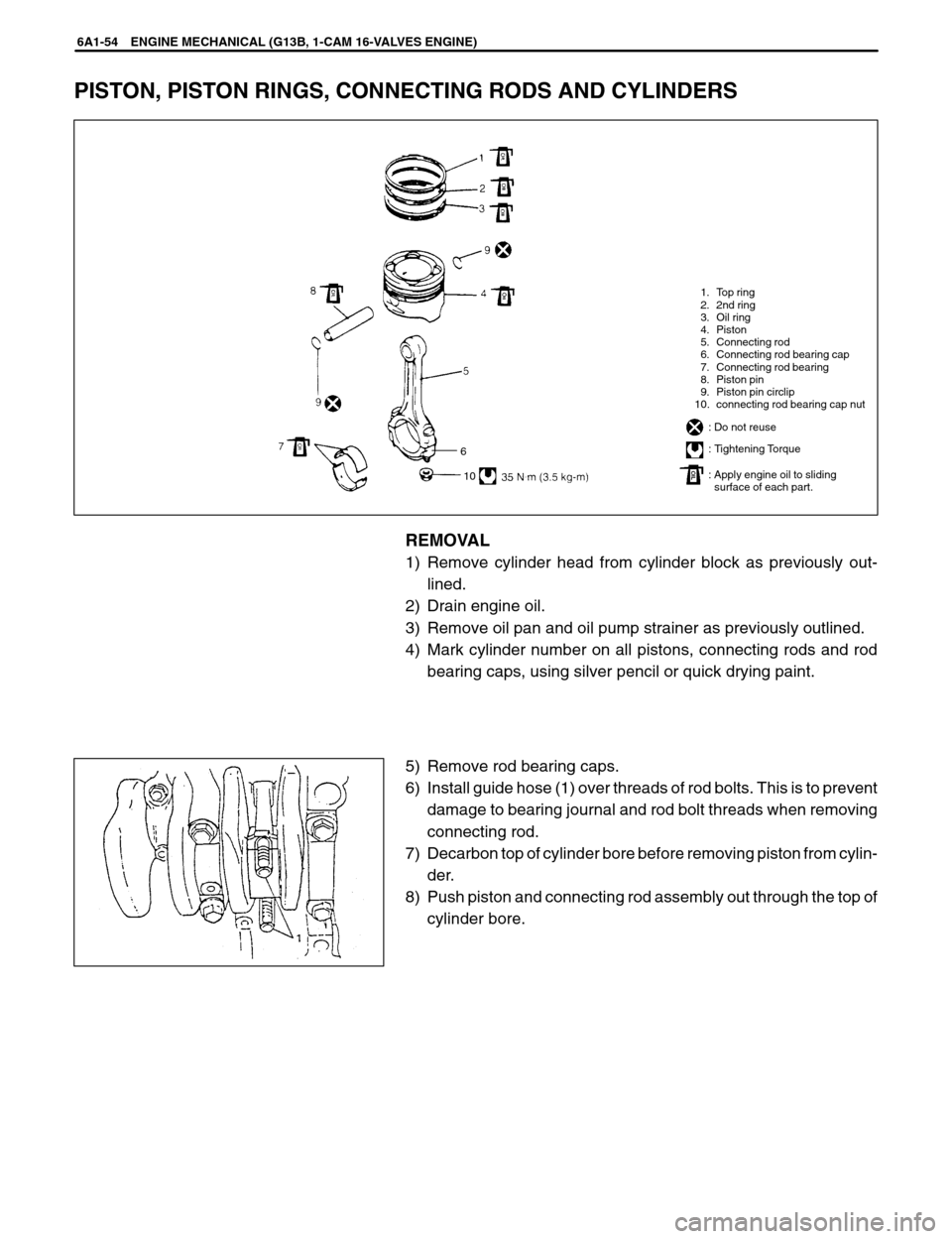
1. Top ring
2. 2nd ring
3. Oil ring
4. Piston
5. Connecting rod
6. Connecting rod bearing cap
7. Connecting rod bearing
8. Piston pin
9. Piston pin circlip
10. connecting rod bearing cap nut
: Do not reuse
: Tightening Torque
: Apply engine oil to sliding
: surface of each part.
6
10
6A1-54 ENGINE MECHANICAL (G13B, 1-CAM 16-VALVES ENGINE)
PISTON, PISTON RINGS, CONNECTING RODS AND CYLINDERS
REMOVAL
1) Remove cylinder head from cylinder block as previously out-
lined.
2) Drain engine oil.
3) Remove oil pan and oil pump strainer as previously outlined.
4) Mark cylinder number on all pistons, connecting rods and rod
bearing caps, using silver pencil or quick drying paint.
5) Remove rod bearing caps.
6) Install guide hose (1) over threads of rod bolts. This is to prevent
damage to bearing journal and rod bolt threads when removing
connecting rod.
7) Decarbon top of cylinder bore before removing piston from cylin-
der.
8) Push piston and connecting rod assembly out through the top of
cylinder bore.
Page 354 of 557
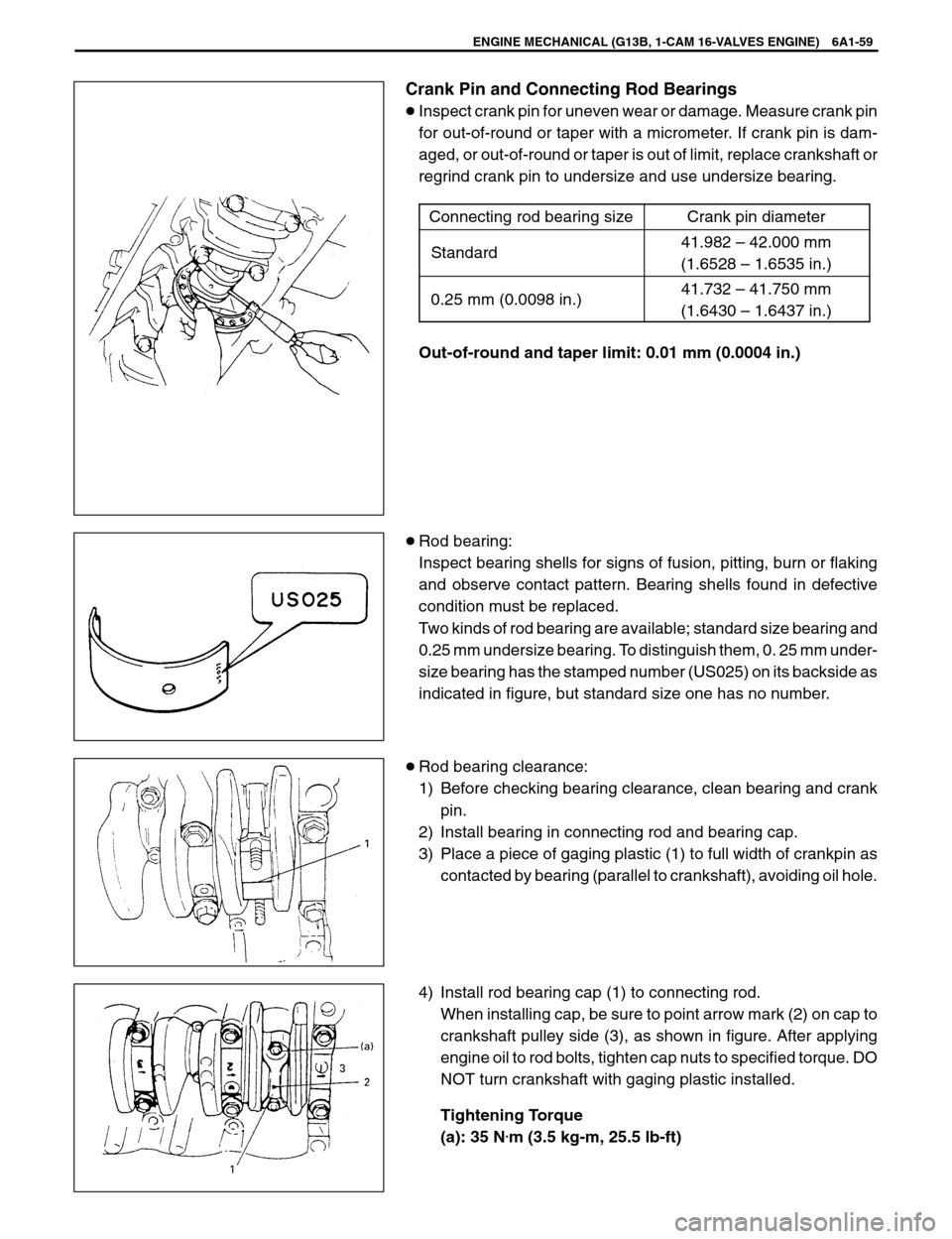
ENGINE MECHANICAL (G13B, 1-CAM 16-VALVES ENGINE) 6A1-59
Crank Pin and Connecting Rod Bearings
Inspect crank pin for uneven wear or damage. Measure crank pin
for out-of-round or taper with a micrometer. If crank pin is dam-
aged, or out-of-round or taper is out of limit, replace crankshaft or
regrind crank pin to undersize and use undersize bearing.
Connecting rod bearing size
Crank pin diameter
Standard41.982 – 42.000 mm
(1.6528 – 1.6535 in.)
0.25 mm (0.0098 in.)41.732 – 41.750 mm
(1.6430 – 1.6437 in.)
Out-of-round and taper limit: 0.01 mm (0.0004 in.)
Rod bearing:
Inspect bearing shells for signs of fusion, pitting, burn or flaking
and observe contact pattern. Bearing shells found in defective
condition must be replaced.
Two kinds of rod bearing are available; standard size bearing and
0.25 mm undersize bearing. To distinguish them, 0. 25 mm under-
size bearing has the stamped number (US025) on its backside as
indicated in figure, but standard size one has no number.
Rod bearing clearance:
1) Before checking bearing clearance, clean bearing and crank
pin.
2) Install bearing in connecting rod and bearing cap.
3) Place a piece of gaging plastic (1) to full width of crankpin as
contacted by bearing (parallel to crankshaft), avoiding oil hole.
4) Install rod bearing cap (1) to connecting rod.
When installing cap, be sure to point arrow mark (2) on cap to
crankshaft pulley side (3), as shown in figure. After applying
engine oil to rod bolts, tighten cap nuts to specified torque. DO
NOT turn crankshaft with gaging plastic installed.
Tightening Torque
(a): 35 N
.m (3.5 kg-m, 25.5 lb-ft)
Page 357 of 557
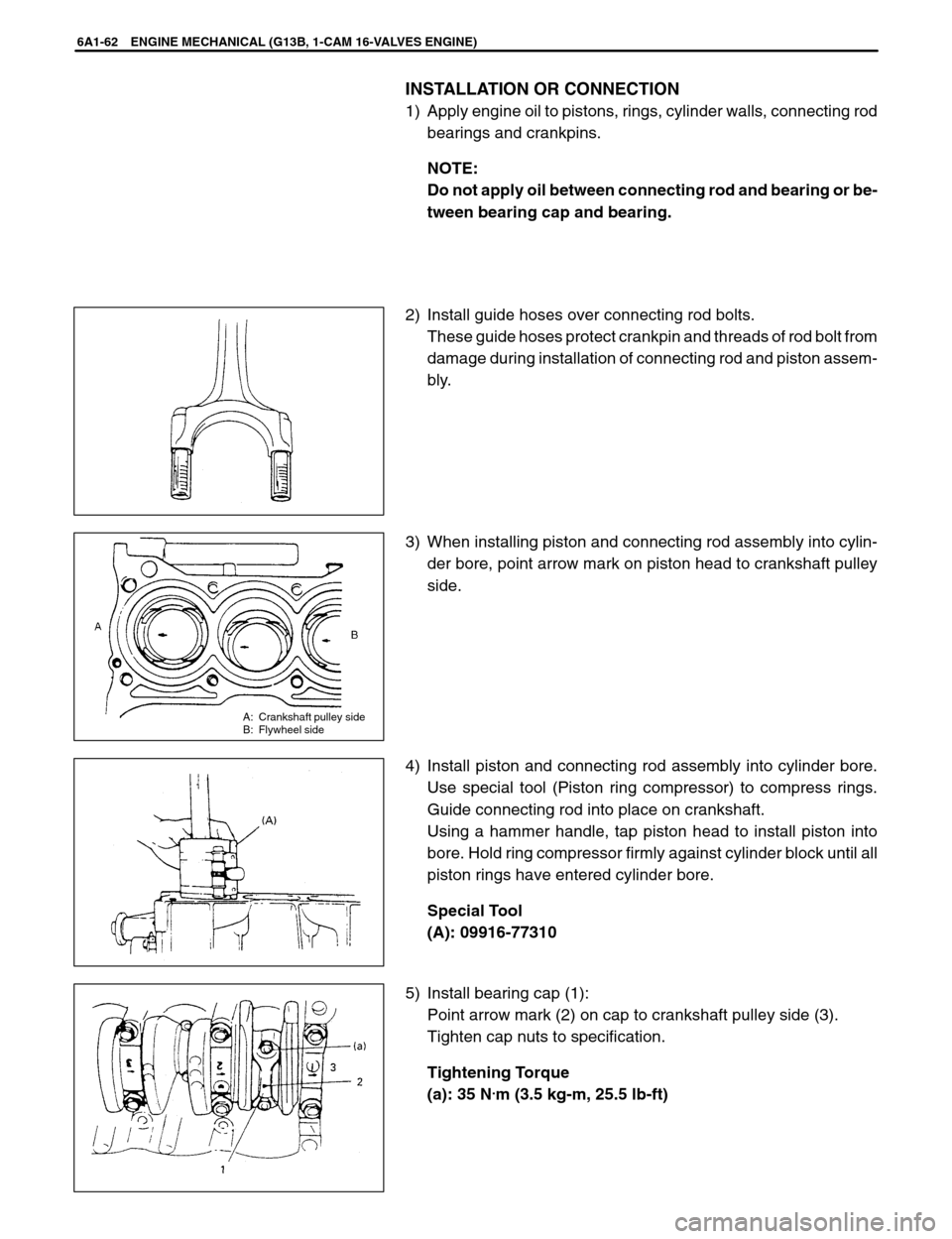
A: Crankshaft pulley side
B: Flywheel side
6A1-62 ENGINE MECHANICAL (G13B, 1-CAM 16-VALVES ENGINE)
INSTALLATION OR CONNECTION
1) Apply engine oil to pistons, rings, cylinder walls, connecting rod
bearings and crankpins.
NOTE:
Do not apply oil between connecting rod and bearing or be-
tween bearing cap and bearing.
2) Install guide hoses over connecting rod bolts.
These guide hoses protect crankpin and threads of rod bolt from
damage during installation of connecting rod and piston assem-
bly.
3) When installing piston and connecting rod assembly into cylin-
der bore, point arrow mark on piston head to crankshaft pulley
side.
4) Install piston and connecting rod assembly into cylinder bore.
Use special tool (Piston ring compressor) to compress rings.
Guide connecting rod into place on crankshaft.
Using a hammer handle, tap piston head to install piston into
bore. Hold ring compressor firmly against cylinder block until all
piston rings have entered cylinder bore.
Special Tool
(A): 09916-77310
5) Install bearing cap (1):
Point arrow mark (2) on cap to crankshaft pulley side (3).
Tighten cap nuts to specification.
Tightening Torque
(a): 35 N
.m (3.5 kg-m, 25.5 lb-ft)
Page 362 of 557
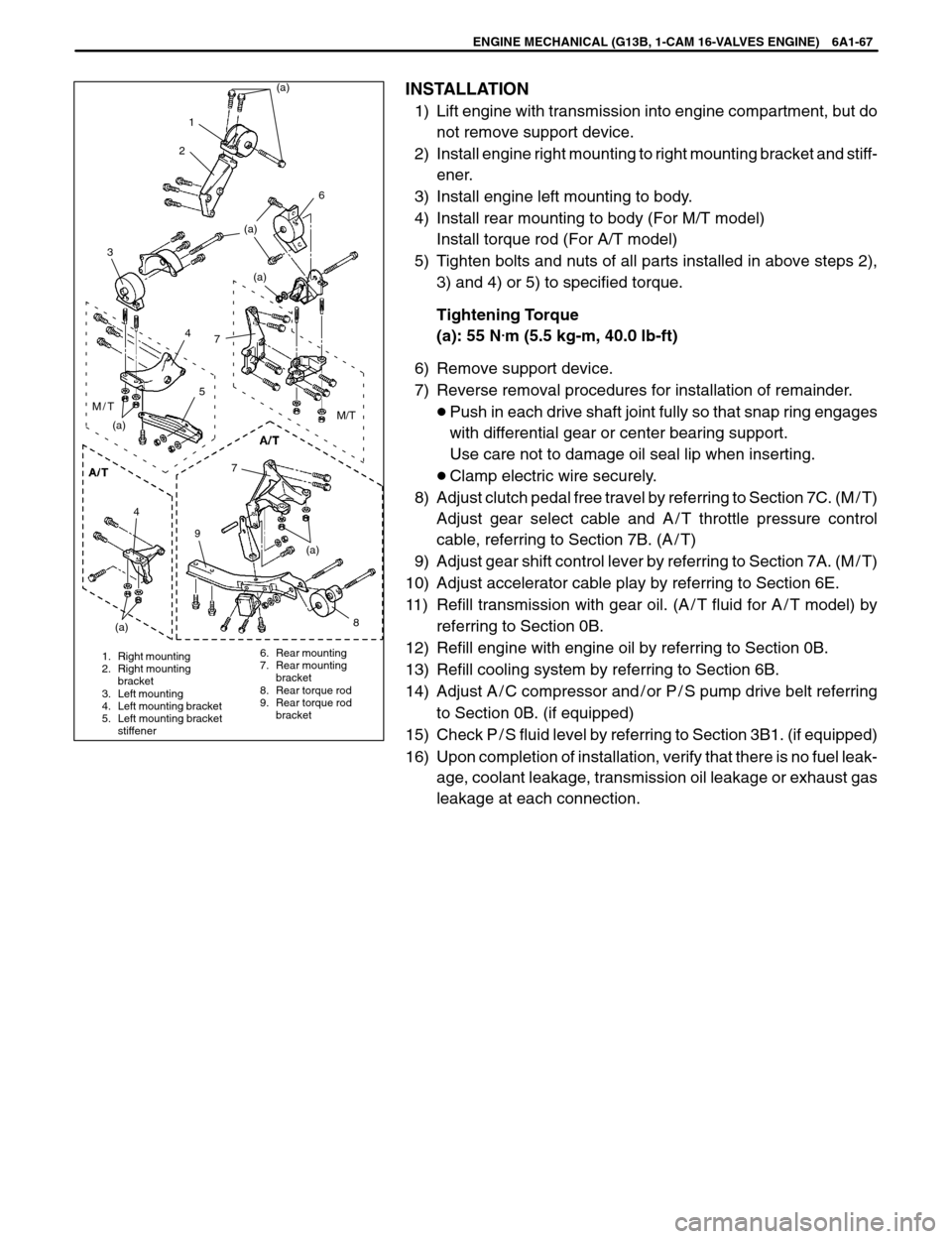
(a)
1
2
3
(a)
(a)
6
74
5
(a)
M/TM/T
9
(a)
4
7
(a)
8
1. Right mounting
2. Right mounting
bracket
3. Left mounting
4. Left mounting bracket
5. Left mounting bracket
stiffener6. Rear mounting
7. Rear mounting
bracket
8. Rear torque rod
9. Rear torque rod
bracket
ENGINE MECHANICAL (G13B, 1-CAM 16-VALVES ENGINE) 6A1-67
INSTALLATION
1) Lift engine with transmission into engine compartment, but do
not remove support device.
2) Install engine right mounting to right mounting bracket and stiff-
ener.
3) Install engine left mounting to body.
4) Install rear mounting to body (For M/T model)
Install torque rod (For A/T model)
5) Tighten bolts and nuts of all parts installed in above steps 2),
3) and 4) or 5) to specified torque.
Tightening Torque
(a): 55 N
.m (5.5 kg-m, 40.0 lb-ft)
6) Remove support device.
7) Reverse removal procedures for installation of remainder.
Push in each drive shaft joint fully so that snap ring engages
with differential gear or center bearing support.
Use care not to damage oil seal lip when inserting.
Clamp electric wire securely.
8) Adjust clutch pedal free travel by referring to Section 7C. (M / T)
Adjust gear select cable and A / T throttle pressure control
cable, referring to Section 7B. (A / T)
9) Adjust gear shift control lever by referring to Section 7A. (M / T)
10) Adjust accelerator cable play by referring to Section 6E.
11) Refill transmission with gear oil. (A / T fluid for A / T model) by
referring to Section 0B.
12) Refill engine with engine oil by referring to Section 0B.
13) Refill cooling system by referring to Section 6B.
14) Adjust A / C compressor and / or P / S pump drive belt referring
to Section 0B. (if equipped)
15) Check P / S fluid level by referring to Section 3B1. (if equipped)
16) Upon completion of installation, verify that there is no fuel leak-
age, coolant leakage, transmission oil leakage or exhaust gas
leakage at each connection.
Page 363 of 557
1. Cylinder block
2. Front oil seal:
Apply engine oil to contact part
of crankshaft with oil seal lip.
3. Main bearing:
Apply engine oil to bearing
inside surfaces.
4. Bearing cap
5. Cap bolt:
Apply engine oil to bolt and
bearing surfaces.
6. Timing pulley key7. Crankshaft:
Apply engine oil to crankshaft
journals.
8. Thrust bearing:
Set oil grooves of bearing to
crank weds.
Apply engine oil.
9. Rear oil seal:
Apply engine oil to contact part
of crankshaft with oil seal lip.10. Pin
11. Oil seal housing gasket
12. Oil seal housing
13. Housing bolt
14. Input shaft bearing
15. Flywheel
16. Flywheel bolt
: Do not reuse
: Tightening Torque
15 16
78 N.m (7.8 kg-m) for flywheel
95 N.m (9.5 kg-m) for drive plate
6A1-68 ENGINE MECHANICAL (G13B, 1-CAM 16-VALVES ENGINE)
MAIN BEARINGS, CRANKSHAFT AND CYLINDER BLOCK
Page 366 of 557
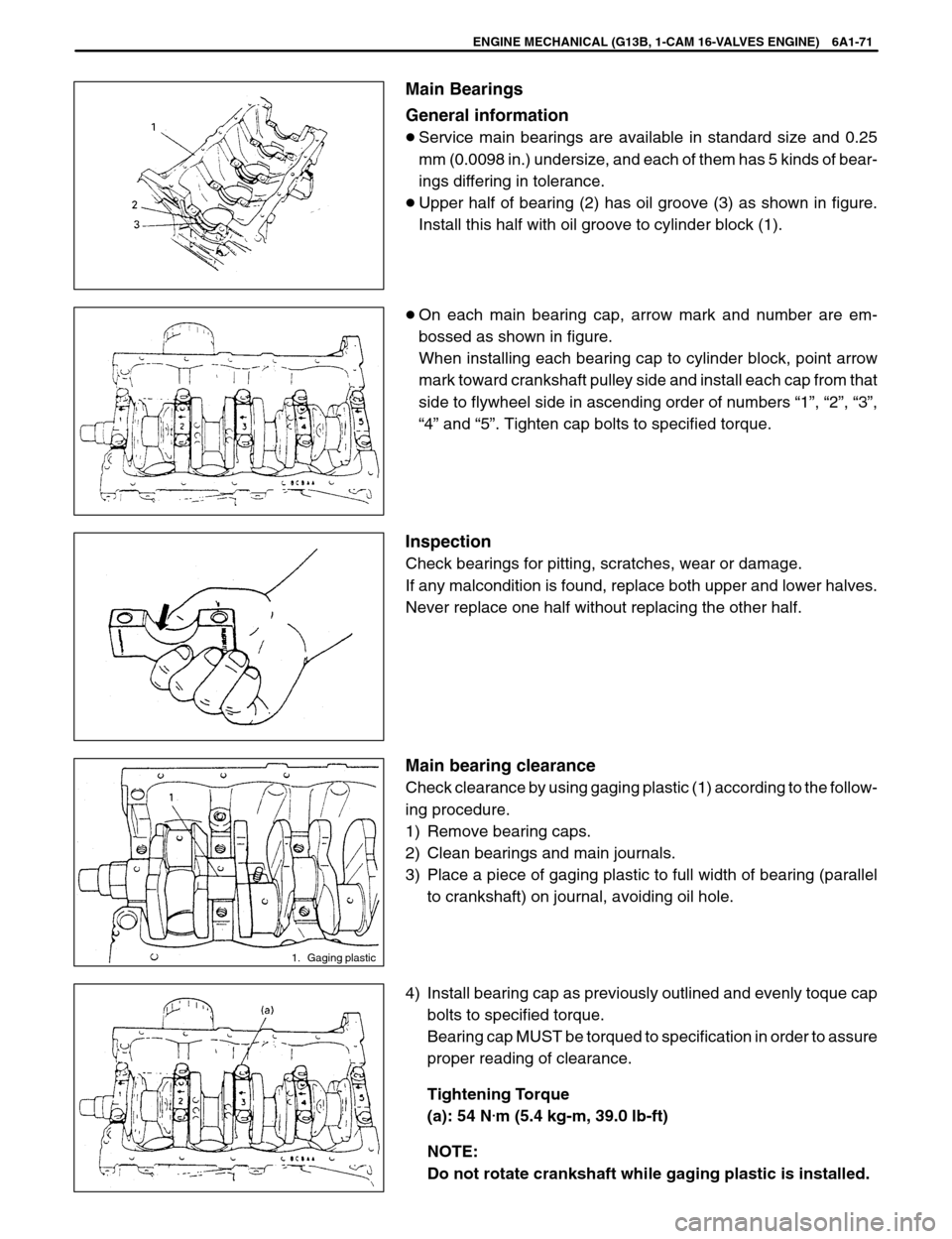
1. Gaging plastic
ENGINE MECHANICAL (G13B, 1-CAM 16-VALVES ENGINE) 6A1-71
Main Bearings
General information
Service main bearings are available in standard size and 0.25
mm (0.0098 in.) undersize, and each of them has 5 kinds of bear-
ings differing in tolerance.
Upper half of bearing (2) has oil groove (3) as shown in figure.
Install this half with oil groove to cylinder block (1).
On each main bearing cap, arrow mark and number are em-
bossed as shown in figure.
When installing each bearing cap to cylinder block, point arrow
mark toward crankshaft pulley side and install each cap from that
side to flywheel side in ascending order of numbers “1”, “2”, “3”,
“4” and “5”. Tighten cap bolts to specified torque.
Inspection
Check bearings for pitting, scratches, wear or damage.
If any malcondition is found, replace both upper and lower halves.
Never replace one half without replacing the other half.
Main bearing clearance
Check clearance by using gaging plastic (1) according to the follow-
ing procedure.
1) Remove bearing caps.
2) Clean bearings and main journals.
3) Place a piece of gaging plastic to full width of bearing (parallel
to crankshaft) on journal, avoiding oil hole.
4) Install bearing cap as previously outlined and evenly toque cap
bolts to specified torque.
Bearing cap MUST be torqued to specification in order to assure
proper reading of clearance.
Tightening Torque
(a): 54 N
.m (5.4 kg-m, 39.0 lb-ft)
NOTE:
Do not rotate crankshaft while gaging plastic is installed.
Page 373 of 557
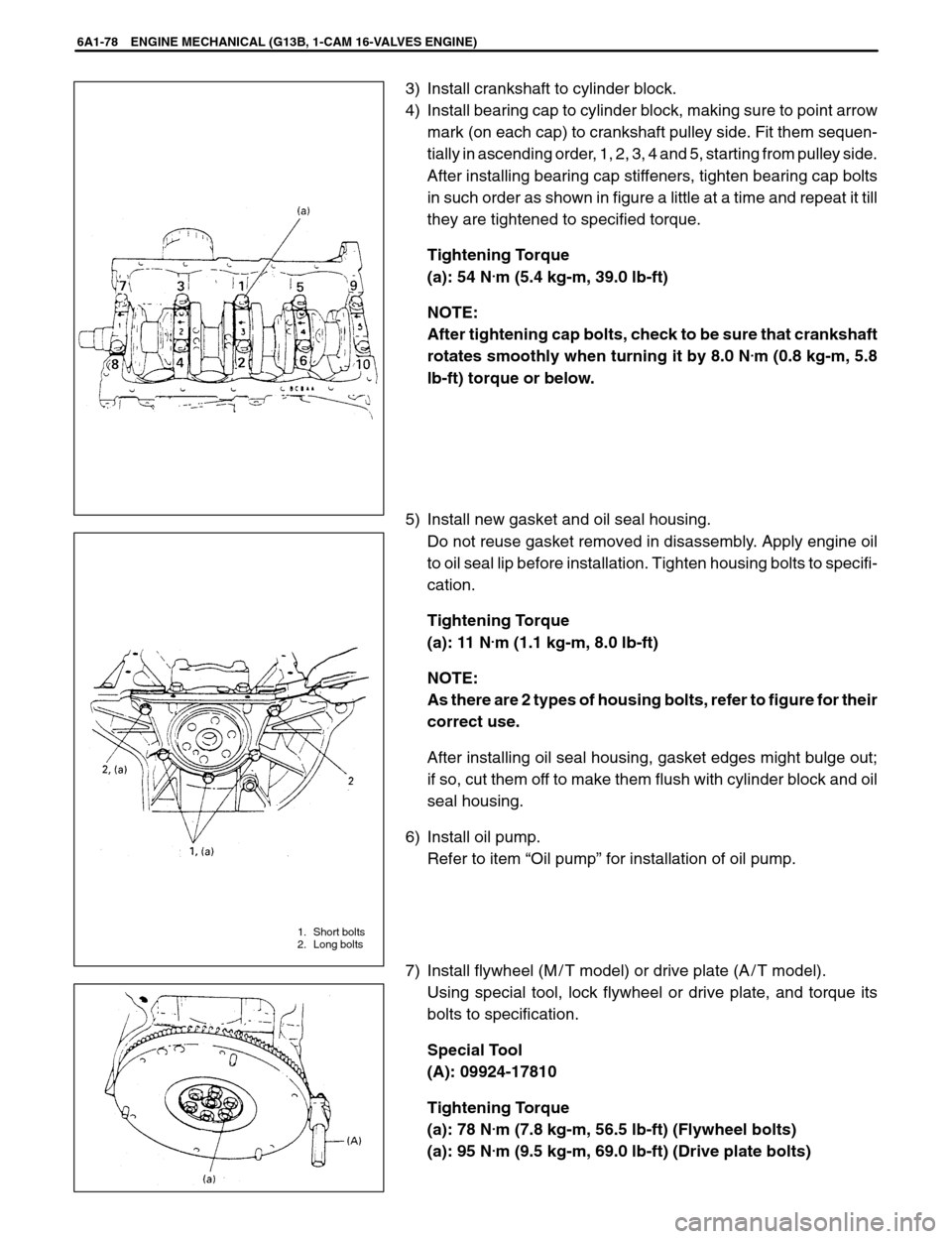
1. Short bolts
2. Long bolts
6A1-78 ENGINE MECHANICAL (G13B, 1-CAM 16-VALVES ENGINE)
3) Install crankshaft to cylinder block.
4) Install bearing cap to cylinder block, making sure to point arrow
mark (on each cap) to crankshaft pulley side. Fit them sequen-
tially in ascending order, 1, 2, 3, 4 and 5, starting from pulley side.
After installing bearing cap stiffeners, tighten bearing cap bolts
in such order as shown in figure a little at a time and repeat it till
they are tightened to specified torque.
Tightening Torque
(a): 54 N
.m (5.4 kg-m, 39.0 lb-ft)
NOTE:
After tightening cap bolts, check to be sure that crankshaft
rotates smoothly when turning it by 8.0 N
.m (0.8 kg-m, 5.8
lb-ft) torque or below.
5) Install new gasket and oil seal housing.
Do not reuse gasket removed in disassembly. Apply engine oil
to oil seal lip before installation. Tighten housing bolts to specifi-
cation.
Tightening Torque
(a): 11 N
.m (1.1 kg-m, 8.0 lb-ft)
NOTE:
As there are 2 types of housing bolts, refer to figure for their
correct use.
After installing oil seal housing, gasket edges might bulge out;
if so, cut them off to make them flush with cylinder block and oil
seal housing.
6) Install oil pump.
Refer to item “Oil pump” for installation of oil pump.
7) Install flywheel (M / T model) or drive plate (A / T model).
Using special tool, lock flywheel or drive plate, and torque its
bolts to specification.
Special Tool
(A): 09924-17810
Tightening Torque
(a): 78 N
.m (7.8 kg-m, 56.5 lb-ft) (Flywheel bolts)
(a): 95 N
.m (9.5 kg-m, 69.0 lb-ft) (Drive plate bolts)