Page 278 of 557
6A-14 ENGINE MECHANICAL (G10, 1-CAM 6-VALVES ENGINE)
7) Install timing belt outside cover.
Before installing, make sure that rubber seal (1) is between wa-
ter pump and oil pump case and another between water pump
and cylinder head.
Tightening Torque
(c): 11 N
.m (1.1 kg-m, 8.0 lb-ft)
8) Install crankshaft pulley (2).
Tighten crankshaft pulley bolts (1).
Tightening Torque
(d): 16 N
.m (1.6 kg-m, 11.5 lb-ft)
9) Install water pump pulley and water pump belt.
Adjust the belt tension to the specification.
Refer to Section 6B for procedure to adjust the belt tension.
10) Install air cleaner assembly.
11) Install fender apron extension of right side.
12) Connect negative cable at battery.
Page 279 of 557
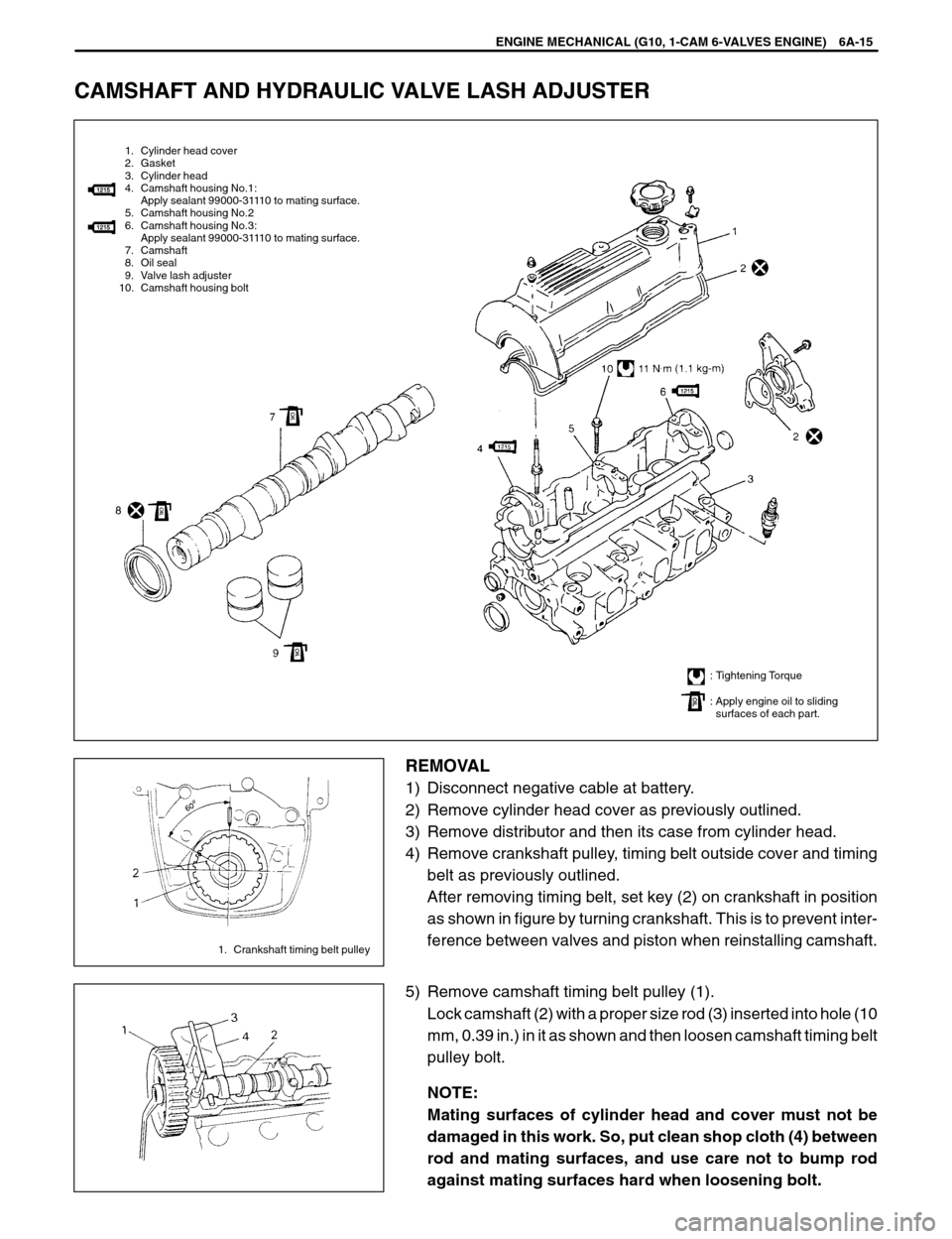
1. Cylinder head cover
2. Gasket
3. Cylinder head
4. Camshaft housing No.1:
Apply sealant 99000-31110 to mating surface.
5. Camshaft housing No.2
6. Camshaft housing No.3:
Apply sealant 99000-31110 to mating surface.
7. Camshaft
8. Oil seal
9. Valve lash adjuster
10. Camshaft housing bolt
1. Crankshaft timing belt pulley: Tightening Torque
: Apply engine oil to sliding
: surfaces of each part.
ENGINE MECHANICAL (G10, 1-CAM 6-VALVES ENGINE) 6A-15
CAMSHAFT AND HYDRAULIC VALVE LASH ADJUSTER
REMOVAL
1) Disconnect negative cable at battery.
2) Remove cylinder head cover as previously outlined.
3) Remove distributor and then its case from cylinder head.
4) Remove crankshaft pulley, timing belt outside cover and timing
belt as previously outlined.
After removing timing belt, set key (2) on crankshaft in position
as shown in figure by turning crankshaft. This is to prevent inter-
ference between valves and piston when reinstalling camshaft.
5) Remove camshaft timing belt pulley (1).
Lock camshaft (2) with a proper size rod (3) inserted into hole (10
mm, 0.39 in.) in it as shown and then loosen camshaft timing belt
pulley bolt.
NOTE:
Mating surfaces of cylinder head and cover must not be
damaged in this work. So, put clean shop cloth (4) between
rod and mating surfaces, and use care not to bump rod
against mating surfaces hard when loosening bolt.
Page 283 of 557
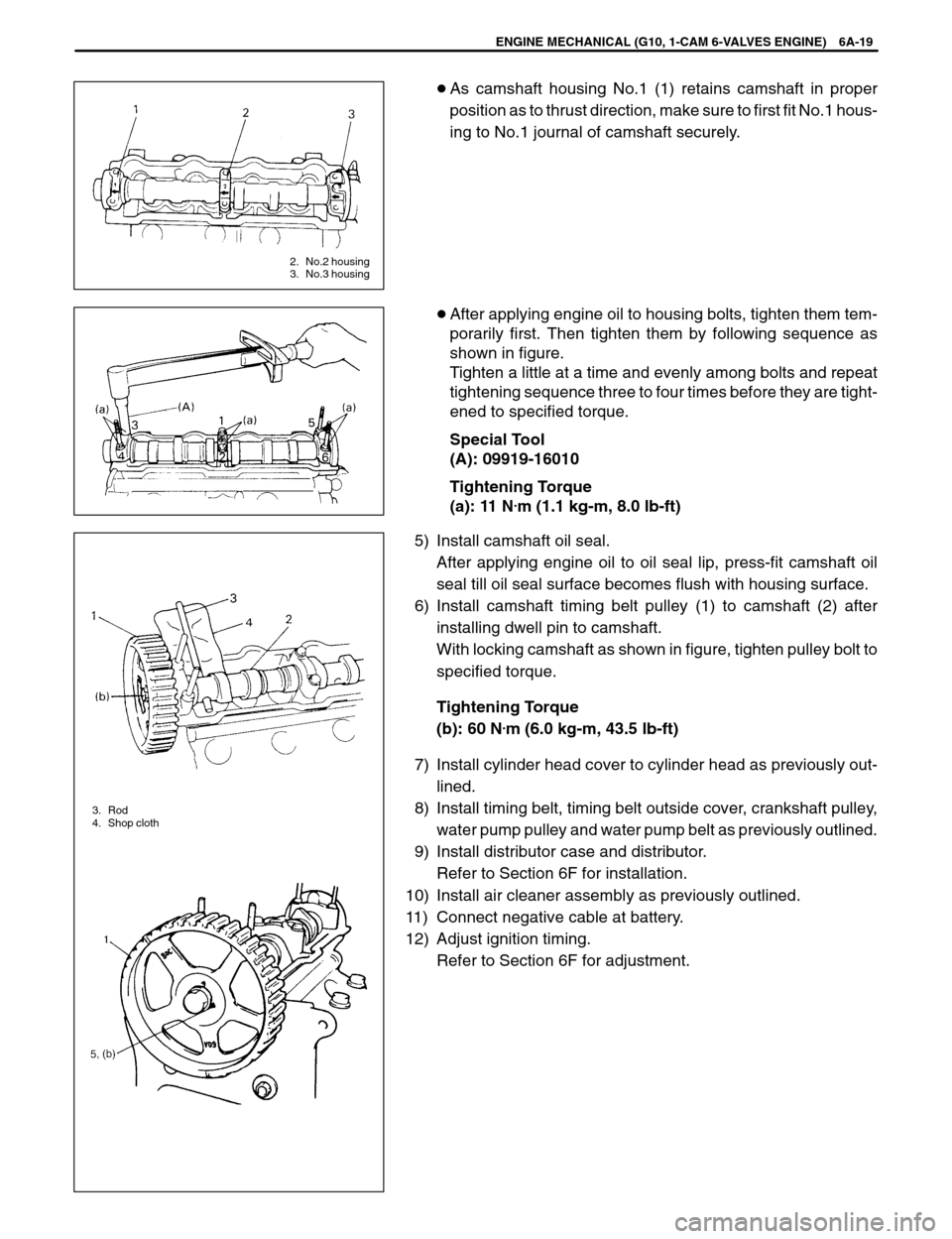
2. No.2 housing
3. No.3 housing
3. Rod
4. Shop cloth
ENGINE MECHANICAL (G10, 1-CAM 6-VALVES ENGINE) 6A-19
As camshaft housing No.1 (1) retains camshaft in proper
position as to thrust direction, make sure to first fit No.1 hous-
ing to No.1 journal of camshaft securely.
After applying engine oil to housing bolts, tighten them tem-
porarily first. Then tighten them by following sequence as
shown in figure.
Tighten a little at a time and evenly among bolts and repeat
tightening sequence three to four times before they are tight-
ened to specified torque.
Special Tool
(A): 09919-16010
Tightening Torque
(a): 11 N
.m (1.1 kg-m, 8.0 lb-ft)
5) Install camshaft oil seal.
After applying engine oil to oil seal lip, press-fit camshaft oil
seal till oil seal surface becomes flush with housing surface.
6) Install camshaft timing belt pulley (1) to camshaft (2) after
installing dwell pin to camshaft.
With locking camshaft as shown in figure, tighten pulley bolt to
specified torque.
Tightening Torque
(b): 60 N
.m (6.0 kg-m, 43.5 lb-ft)
7) Install cylinder head cover to cylinder head as previously out-
lined.
8) Install timing belt, timing belt outside cover, crankshaft pulley,
water pump pulley and water pump belt as previously outlined.
9) Install distributor case and distributor.
Refer to Section 6F for installation.
10) Install air cleaner assembly as previously outlined.
11) Connect negative cable at battery.
12) Adjust ignition timing.
Refer to Section 6F for adjustment.
Page 285 of 557
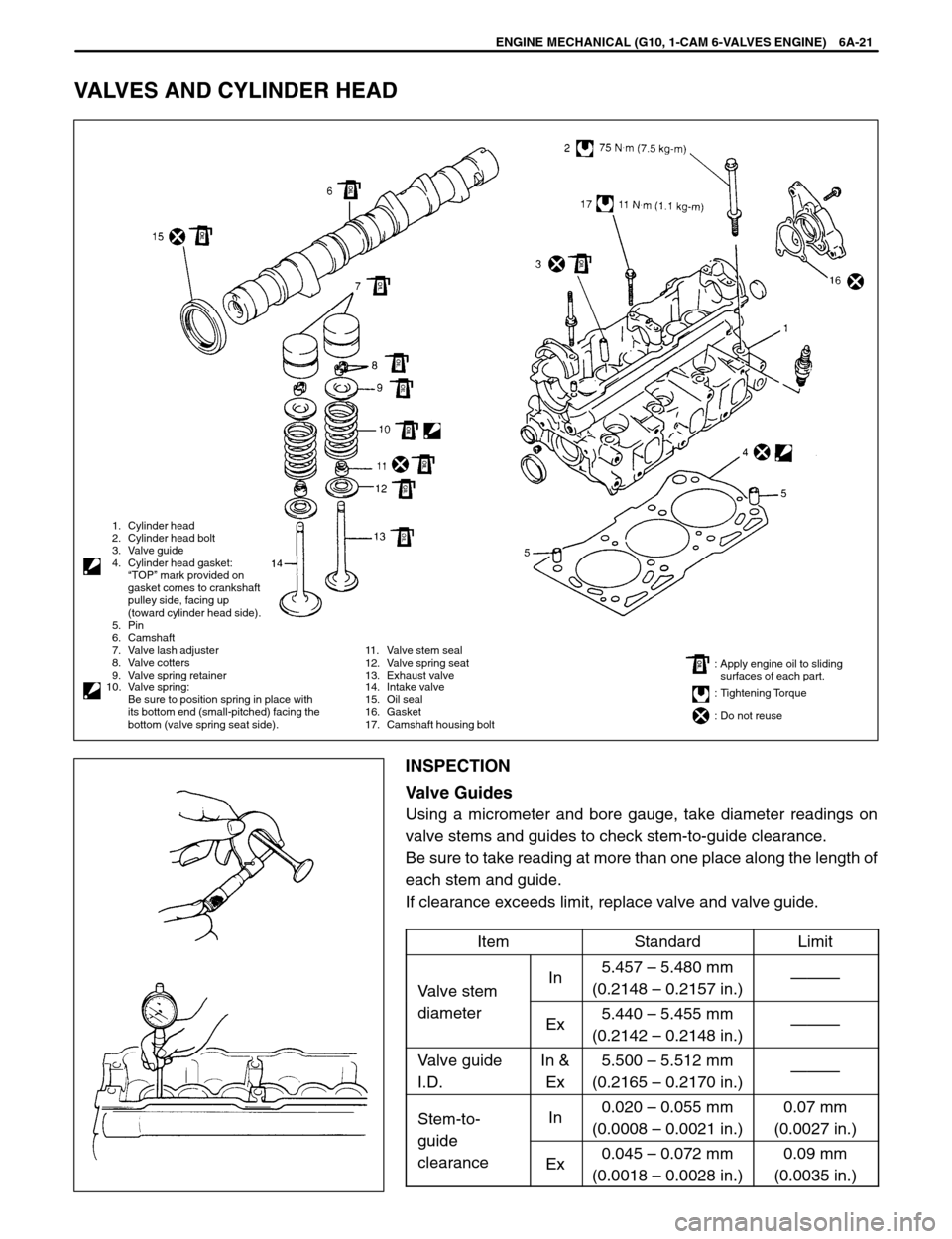
1. Cylinder head
2. Cylinder head bolt
3. Valve guide
4. Cylinder head gasket:
“TOP” mark provided on
gasket comes to crankshaft
pulley side, facing up
(toward cylinder head side).
5. Pin
6. Camshaft
7. Valve lash adjuster
8. Valve cotters
9. Valve spring retainer
10. Valve spring:
Be sure to position spring in place with
its bottom end (small-pitched) facing the
bottom (valve spring seat side).11. Valve stem seal
12. Valve spring seat
13. Exhaust valve
14. Intake valve
15. Oil seal
16. Gasket
17. Camshaft housing bolt: Tightening Torque
: Do not reuse
: Apply engine oil to sliding
: surfaces of each part.
ENGINE MECHANICAL (G10, 1-CAM 6-VALVES ENGINE) 6A-21
VALVES AND CYLINDER HEAD
INSPECTION
Valve Guides
Using a micrometer and bore gauge, take diameter readings on
valve stems and guides to check stem-to-guide clearance.
Be sure to take reading at more than one place along the length of
each stem and guide.
If clearance exceeds limit, replace valve and valve guide.
Item
StandardLimit
Valve stemIn5.457 – 5.480 mm
(0.2148 – 0.2157 in.)———
diameterEx5.440 – 5.455 mm
(0.2142 – 0.2148 in.)———
Valve guide
I.D.In &
Ex5.500 – 5.512 mm
(0.2165 – 0.2170 in.)———
Stem-to-
guide
In0.020 – 0.055 mm
(0.0008 – 0.0021 in.)0.07 mm
(0.0027 in.)
guide
clearanceEx0.045 – 0.072 mm
(0.0018 – 0.0028 in.)0.09 mm
(0.0035 in.)
Page 287 of 557
1. Cylinder block
2. Feeler gauge
3. Piston ring
4. 120 mm (4.72 in.)1. Top ring
2. 2nd ring
3. Oil ring
4. Piston
5. Connecting rod
6. Connecting rod bearing cap
7. Connecting rod bearing
8. Piston pin
9. Connecting rod nut : Tightening Torque
: Apply engine oil to sliding
: surfaces of each part.
ENGINE MECHANICAL (G10, 1-CAM 6-VALVES ENGINE) 6A-23
PISTONS, PISTON RINGS, CONNECTING RODS AND CYLINDERS
INSPECTION
Piston Rings
To measure end gap, insert piston ring into cylinder bore as shown
in figure and then measure gap by using thickness gauge.
If measured gap is out of specification, replace ring.
NOTE:
Decarbon and clean the top of cylinder bore before inserting
piston ring.
Item
StandardLimit
Piston
Top ring0.15 – 0.30 mm
(0.0059 – 0.0118 in.)0.7 mm
(0.0275 in.)
Piston
ring end
gap
2nd ring0.20 – 0.35 mm
(0.0079 – 0.0138 in.)0.7 mm
(0.0275 in.)
ga
Oil ring0.20 – 0.60 mm
(0.0079 – 0.0236 in.)1.8 mm
(0.0708 in.)
Page 290 of 557
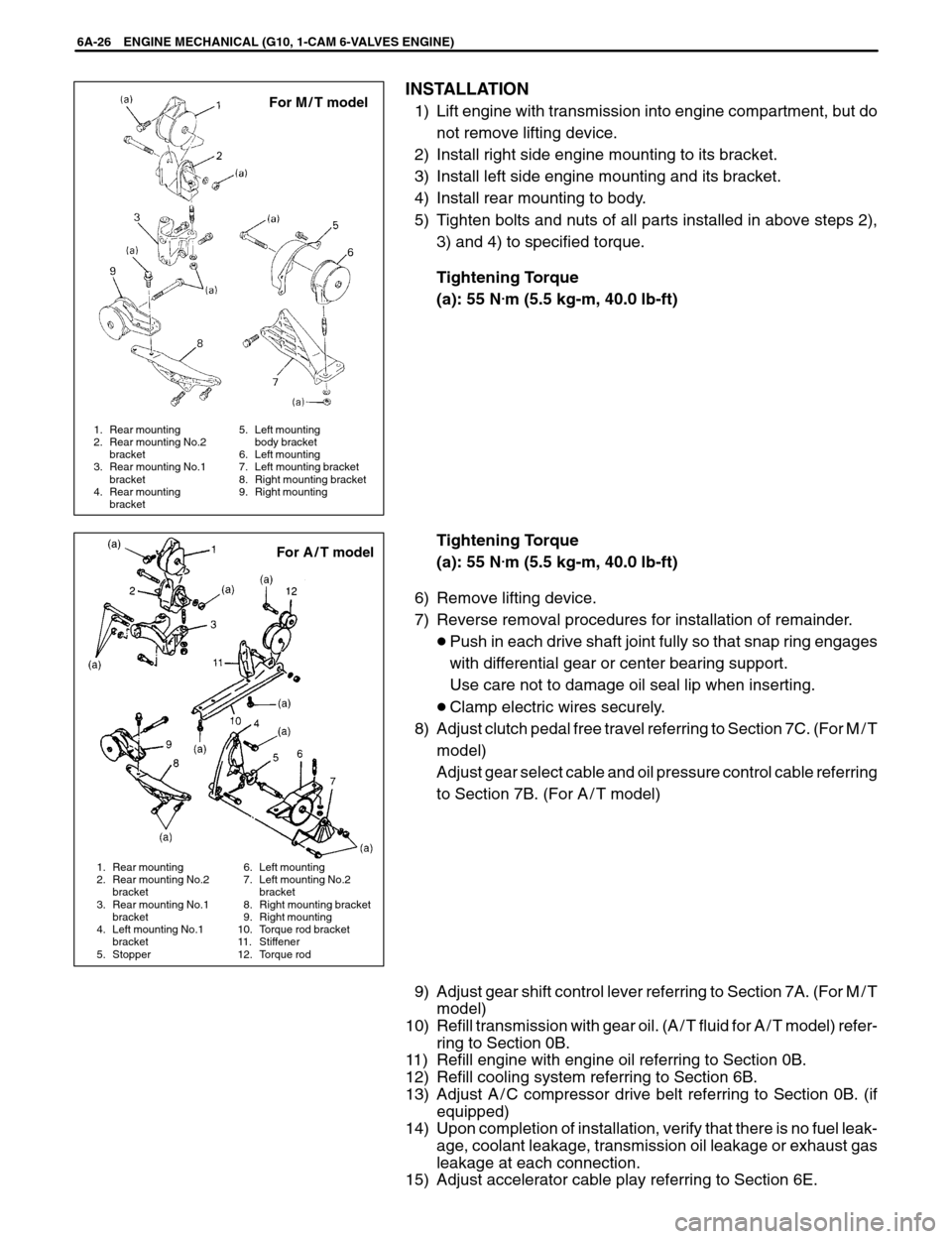
1. Rear mounting
2. Rear mounting No.2
bracket
3. Rear mounting No.1
bracket
4. Rear mounting
bracket5. Left mounting
body bracket
6. Left mounting
7. Left mounting bracket
8. Right mounting bracket
9. Right mounting
For M / T model
For A / T model
1. Rear mounting
2. Rear mounting No.2
bracket
3. Rear mounting No.1
bracket
4. Left mounting No.1
bracket
5. Stopper6. Left mounting
7. Left mounting No.2
bracket
8. Right mounting bracket
9. Right mounting
10. Torque rod bracket
11. Stiffener
12. Torque rod
6A-26 ENGINE MECHANICAL (G10, 1-CAM 6-VALVES ENGINE)
INSTALLATION
1) Lift engine with transmission into engine compartment, but do
not remove lifting device.
2) Install right side engine mounting to its bracket.
3) Install left side engine mounting and its bracket.
4) Install rear mounting to body.
5) Tighten bolts and nuts of all parts installed in above steps 2),
3) and 4) to specified torque.
Tightening Torque
(a): 55 N
.m (5.5 kg-m, 40.0 lb-ft)
Tightening Torque
(a): 55 N
.m (5.5 kg-m, 40.0 lb-ft)
6) Remove lifting device.
7) Reverse removal procedures for installation of remainder.
Push in each drive shaft joint fully so that snap ring engages
with differential gear or center bearing support.
Use care not to damage oil seal lip when inserting.
Clamp electric wires securely.
8) Adjust clutch pedal free travel referring to Section 7C. (For M / T
model)
Adjust gear select cable and oil pressure control cable referring
to Section 7B. (For A / T model)
9) Adjust gear shift control lever referring to Section 7A. (For M / T
model)
10) Refill transmission with gear oil. (A / T fluid for A / T model) refer-
ring to Section 0B.
11) Refill engine with engine oil referring to Section 0B.
12) Refill cooling system referring to Section 6B.
13) Adjust A / C compressor drive belt referring to Section 0B. (if
equipped)
14) Upon completion of installation, verify that there is no fuel leak-
age, coolant leakage, transmission oil leakage or exhaust gas
leakage at each connection.
15) Adjust accelerator cable play referring to Section 6E.
Page 291 of 557
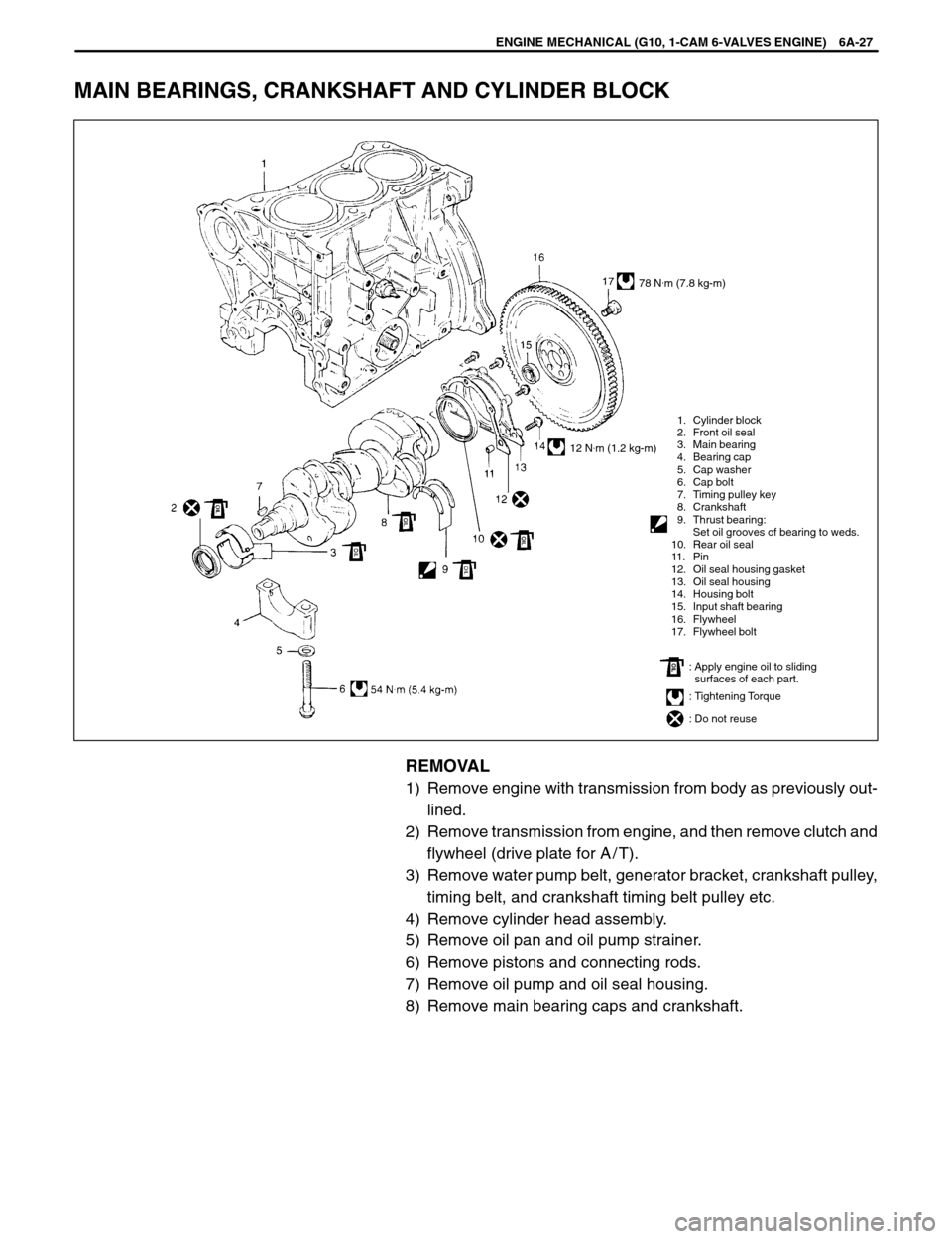
1. Cylinder block
2. Front oil seal
3. Main bearing
4. Bearing cap
5. Cap washer
6. Cap bolt
7. Timing pulley key
8. Crankshaft
9. Thrust bearing:
Set oil grooves of bearing to weds.
10. Rear oil seal
11. Pin
12. Oil seal housing gasket
13. Oil seal housing
14. Housing bolt
15. Input shaft bearing
16. Flywheel
17. Flywheel bolt
: Tightening Torque
: Do not reuse
: Apply engine oil to sliding
: surfaces of each part.
78 N.m (7.8 kg-m)
12 N
.m (1.2 kg-m)
ENGINE MECHANICAL (G10, 1-CAM 6-VALVES ENGINE) 6A-27
MAIN BEARINGS, CRANKSHAFT AND CYLINDER BLOCK
REMOVAL
1) Remove engine with transmission from body as previously out-
lined.
2) Remove transmission from engine, and then remove clutch and
flywheel (drive plate for A / T).
3) Remove water pump belt, generator bracket, crankshaft pulley,
timing belt, and crankshaft timing belt pulley etc.
4) Remove cylinder head assembly.
5) Remove oil pan and oil pump strainer.
6) Remove pistons and connecting rods.
7) Remove oil pump and oil seal housing.
8) Remove main bearing caps and crankshaft.
Page 292 of 557
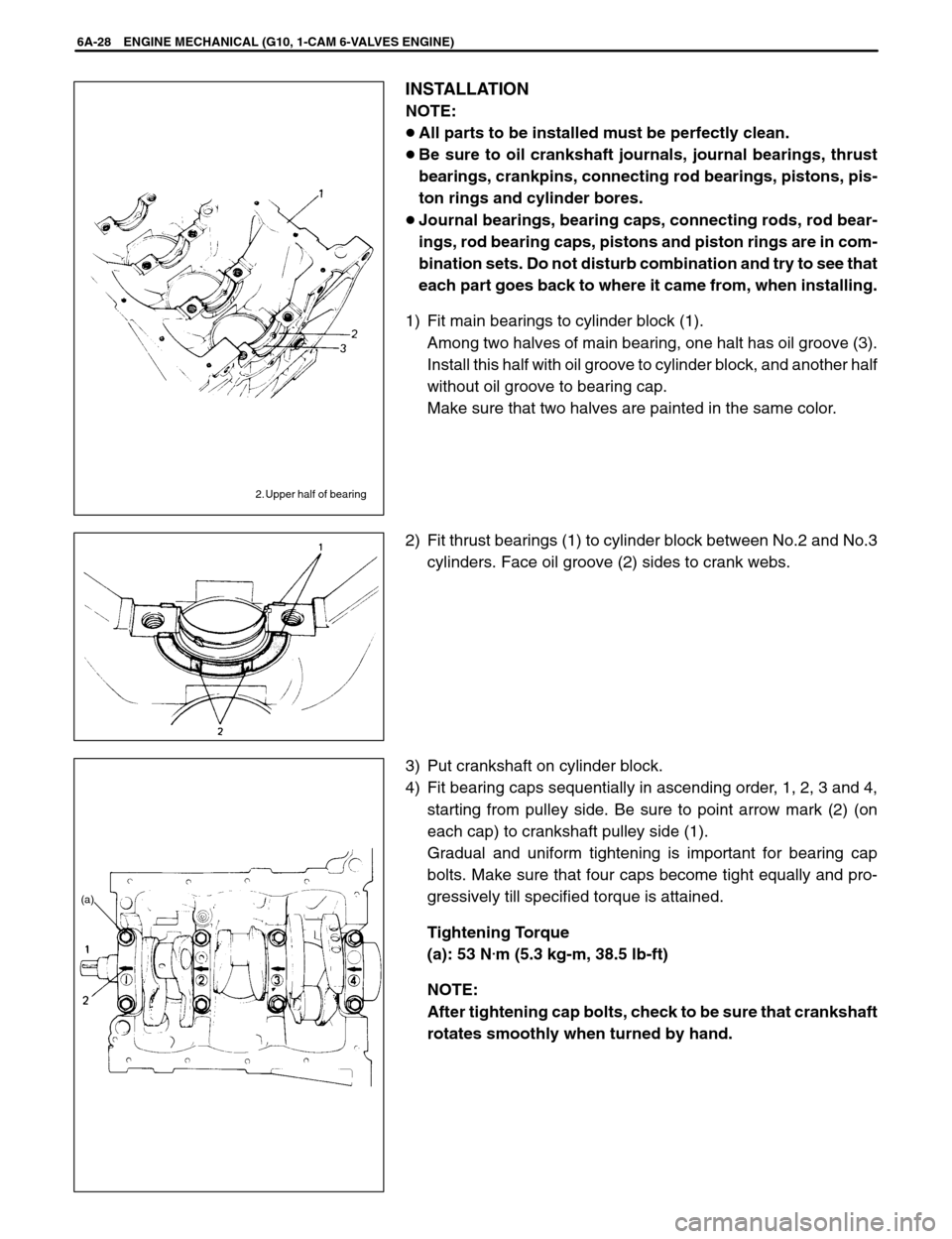
2. Upper half of bearing
(a)
6A-28 ENGINE MECHANICAL (G10, 1-CAM 6-VALVES ENGINE)
INSTALLATION
NOTE:
All parts to be installed must be perfectly clean.
Be sure to oil crankshaft journals, journal bearings, thrust
bearings, crankpins, connecting rod bearings, pistons, pis-
ton rings and cylinder bores.
Journal bearings, bearing caps, connecting rods, rod bear-
ings, rod bearing caps, pistons and piston rings are in com-
bination sets. Do not disturb combination and try to see that
each part goes back to where it came from, when installing.
1) Fit main bearings to cylinder block (1).
Among two halves of main bearing, one halt has oil groove (3).
Install this half with oil groove to cylinder block, and another half
without oil groove to bearing cap.
Make sure that two halves are painted in the same color.
2) Fit thrust bearings (1) to cylinder block between No.2 and No.3
cylinders. Face oil groove (2) sides to crank webs.
3) Put crankshaft on cylinder block.
4) Fit bearing caps sequentially in ascending order, 1, 2, 3 and 4,
starting from pulley side. Be sure to point arrow mark (2) (on
each cap) to crankshaft pulley side (1).
Gradual and uniform tightening is important for bearing cap
bolts. Make sure that four caps become tight equally and pro-
gressively till specified torque is attained.
Tightening Torque
(a): 53 N
.m (5.3 kg-m, 38.5 lb-ft)
NOTE:
After tightening cap bolts, check to be sure that crankshaft
rotates smoothly when turned by hand.