Page 9 of 557
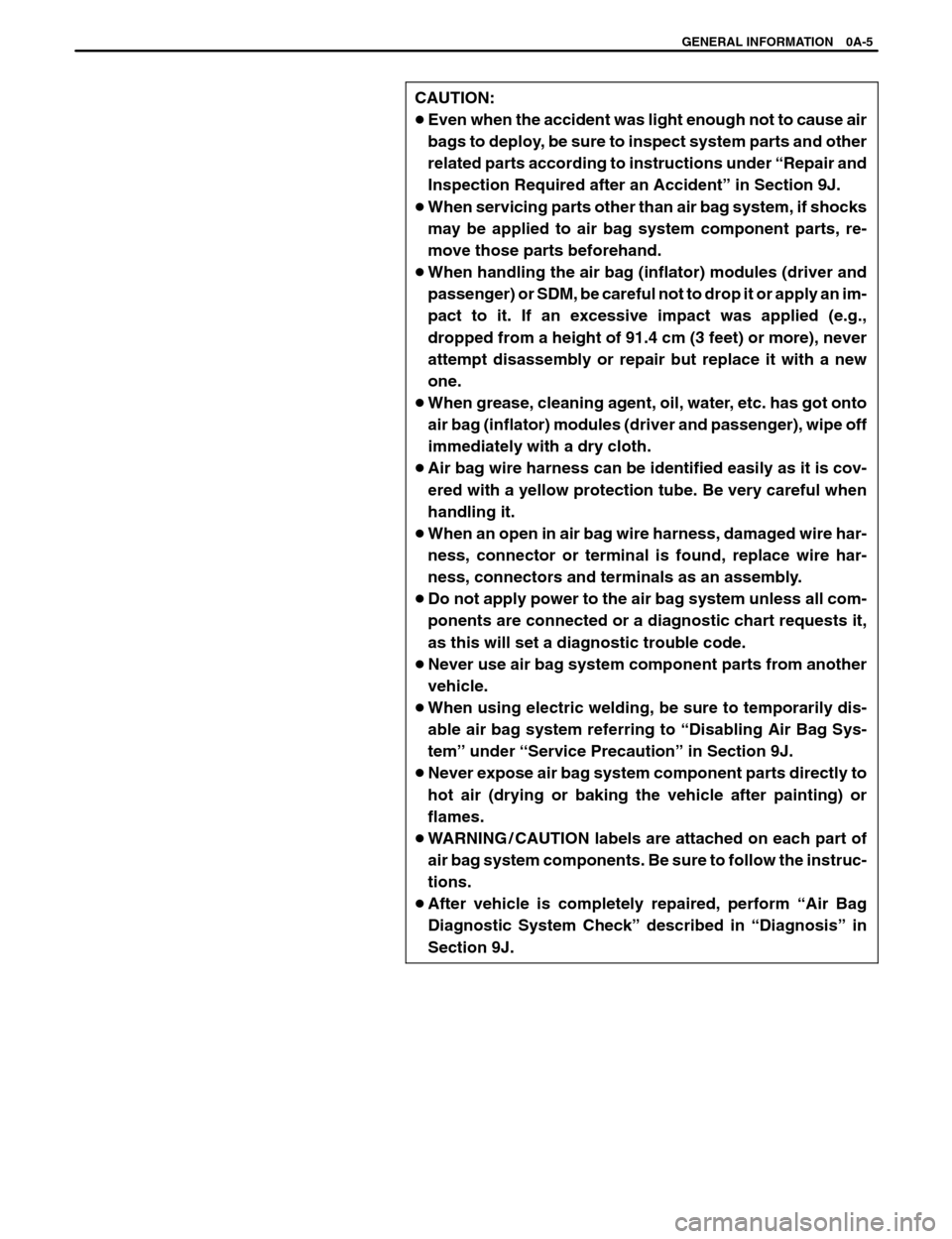
GENERAL INFORMATION 0A-5
CAUTION:
Even when the accident was light enough not to cause air
bags to deploy, be sure to inspect system parts and other
related parts according to instructions under “Repair and
Inspection Required after an Accident” in Section 9J.
When servicing parts other than air bag system, if shocks
may be applied to air bag system component parts, re-
move those parts beforehand.
When handling the air bag (inflator) modules (driver and
passenger) or SDM, be careful not to drop it or apply an im-
pact to it. If an excessive impact was applied (e.g.,
dropped from a height of 91.4 cm (3 feet) or more), never
attempt disassembly or repair but replace it with a new
one.
When grease, cleaning agent, oil, water, etc. has got onto
air bag (inflator) modules (driver and passenger), wipe off
immediately with a dry cloth.
Air bag wire harness can be identified easily as it is cov-
ered with a yellow protection tube. Be very careful when
handling it.
When an open in air bag wire harness, damaged wire har-
ness, connector or terminal is found, replace wire har-
ness, connectors and terminals as an assembly.
Do not apply power to the air bag system unless all com-
ponents are connected or a diagnostic chart requests it,
as this will set a diagnostic trouble code.
Never use air bag system component parts from another
vehicle.
When using electric welding, be sure to temporarily dis-
able air bag system referring to “Disabling Air Bag Sys-
tem” under “Service Precaution” in Section 9J.
Never expose air bag system component parts directly to
hot air (drying or baking the vehicle after painting) or
flames.
WARNING / CAUTION labels are attached on each part of
air bag system components. Be sure to follow the instruc-
tions.
After vehicle is completely repaired, perform “Air Bag
Diagnostic System Check” described in “Diagnosis” in
Section 9J.
Page 321 of 557
2. O-ring
6A1-26 ENGINE MECHANICAL (G13B, 1-CAM 16-VALVES ENGINE)
6) Remove oil pan (3) and then oil pump strainer (1).
CLEANING
Clean mating surfaces of oil pan and cylinder block.
Remove oil, old sealant, and dusts from mating surfaces and oil
pan inside.
Clean oil pump strainer screen.
INSTALLATION
1) Apply sealant to oil pan mating surface continuously as shown
in figure.
“A” Sealant: 99000-31150
Sealant amount
Width “a”: 4 mm, 0.16 in.
Height “b”: 2 mm, 0.08 in.
2) Install O-ring (2) into cylinder block securely as shown in figure.
Install oil pump strainer (1) to cylinder block.
Tighten strainer bolt first and then bracket bolt to specified
torque.
Tightening Torque
(a): 11 N
.m (1.1 kg-m, 8.0 lb-ft)
After fitting oil pan (3) to cylinder block, run in securing bolts and
start tightening at the center: move wrench outward, tightening
one bolt at a time.
Tighten bolts to specified torque.
Tightening Torque
(b): 11 N
.m (1.1 kg-m, 8.0 lb-ft)
Page 331 of 557

6A1-36 ENGINE MECHANICAL (G13B, 1-CAM 16-VALVES ENGINE)
Rocker Arm-to-Rocker Arm Shaft Clearance
Using a micrometer and a bore gauge, measure rocker shaft dia.
and rocker arm l.D.
Difference between two readings is arm-to-shaft clearance on
which a limit is specified.
If limit is exceeded, replace shaft or arm, or both.
Item
StandardLimit
Rocker arm l.D.15.996 – 16.014 mm
(0.629 – 0.630 in.)———
Rocker arm shaft dia.15.969 – 15.984 mm
(0.6287 – 0.6293 in.)———
Arm-to-shaft clearance0.012 – 0.045 mm
(0.0005 – 0.0018 in.)0.09 mm
(0.0035 in.)
Cam Wear
Using a micrometer, measured height of cam. If measured height
is below limit, replace camshaft.
Cam height
StandardLimit
Intake cam36.184 – 36.344 mm
(1.4246 – 1.4309 in.)36.084 mm
(1.4206 in.)
Exhaust cam35.900 – 36.060 mm
(1.4134 – 1.4197 in.)35.800 mm
(1.4094 in.)
Camshaft Runout
Hold camshaft between two “V” blocks, and measure runout by us-
ing a dial gauge.
If runout exceeds the limit, replace camshaft.
Runout limit: 0.10 mm (0.0039 in.)
Camshaft Journal Wear
Check camshaft journals and camshaft housings for pitting,
scratches, wear or damage.
If any malcondition is found, replace camshaft or cylinder head with
housing. Never replace cylinder head without replacing housing.
Page 399 of 557
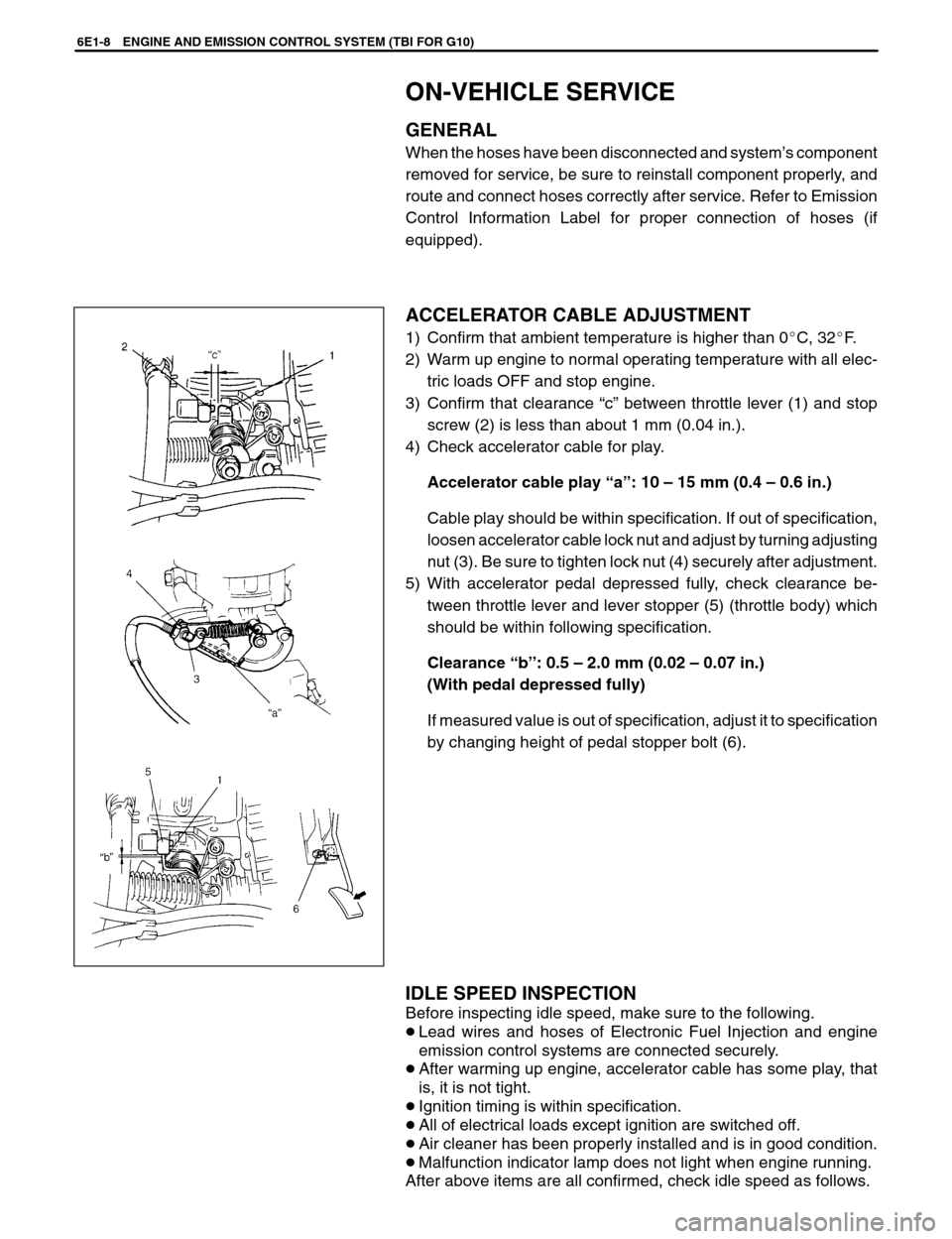
6E1-8 ENGINE AND EMISSION CONTROL SYSTEM (TBI FOR G10)
ON-VEHICLE SERVICE
GENERAL
When the hoses have been disconnected and system’s component
removed for service, be sure to reinstall component properly, and
route and connect hoses correctly after service. Refer to Emission
Control Information Label for proper connection of hoses (if
equipped).
ACCELERATOR CABLE ADJUSTMENT
1) Confirm that ambient temperature is higher than 0C, 32F.
2) Warm up engine to normal operating temperature with all elec-
tric loads OFF and stop engine.
3) Confirm that clearance “c” between throttle lever (1) and stop
screw (2) is less than about 1 mm (0.04 in.).
4) Check accelerator cable for play.
Accelerator cable play “a”: 10 – 15 mm (0.4 – 0.6 in.)
Cable play should be within specification. If out of specification,
loosen accelerator cable lock nut and adjust by turning adjusting
nut (3). Be sure to tighten lock nut (4) securely after adjustment.
5) With accelerator pedal depressed fully, check clearance be-
tween throttle lever and lever stopper (5) (throttle body) which
should be within following specification.
Clearance “b”: 0.5 – 2.0 mm (0.02 – 0.07 in.)
(With pedal depressed fully)
If measured value is out of specification, adjust it to specification
by changing height of pedal stopper bolt (6).
IDLE SPEED INSPECTION
Before inspecting idle speed, make sure to the following.
Lead wires and hoses of Electronic Fuel Injection and engine
emission control systems are connected securely.
After warming up engine, accelerator cable has some play, that
is, it is not tight.
Ignition timing is within specification.
All of electrical loads except ignition are switched off.
Air cleaner has been properly installed and is in good condition.
Malfunction indicator lamp does not light when engine running.
After above items are all confirmed, check idle speed as follows.