Page 285 of 557
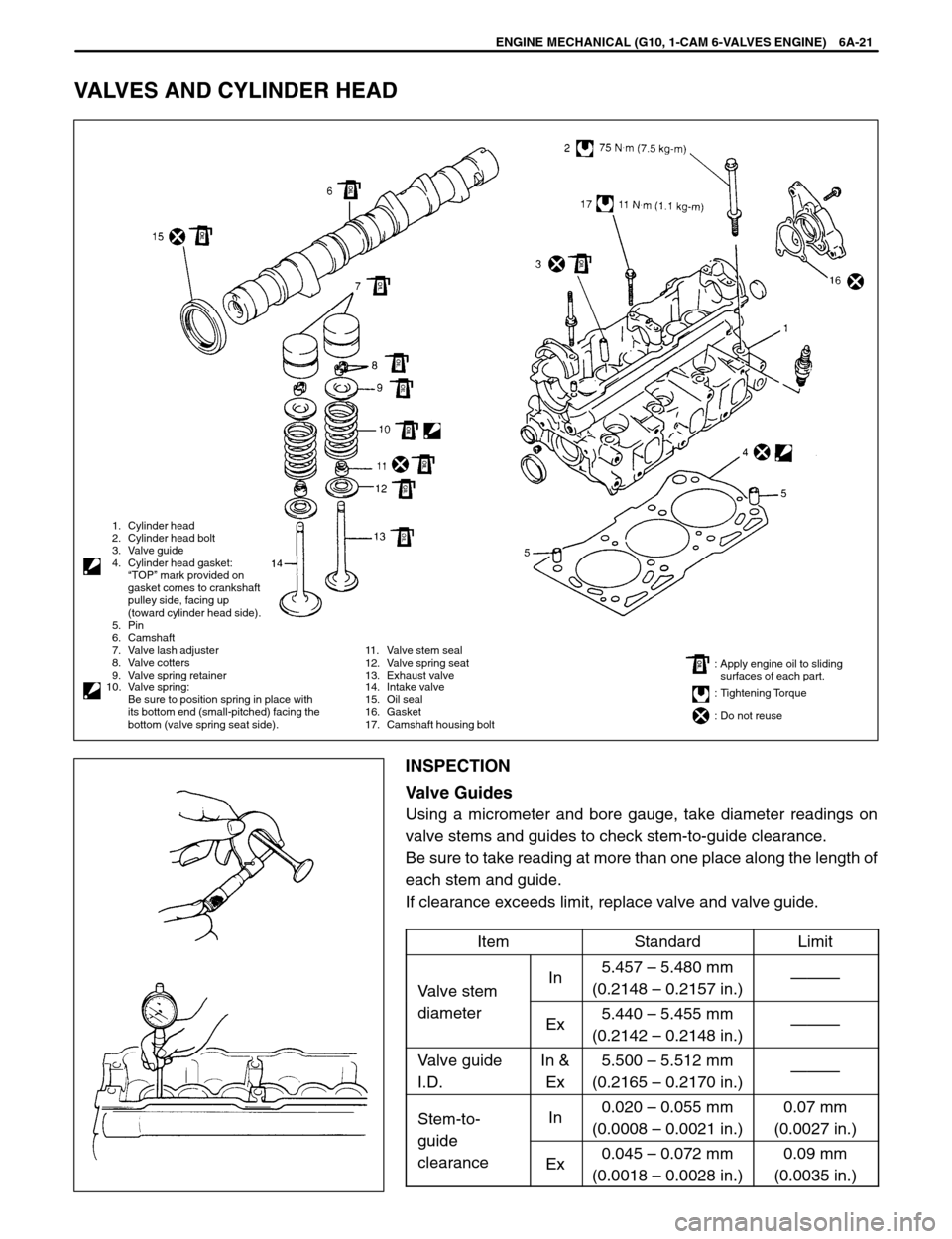
1. Cylinder head
2. Cylinder head bolt
3. Valve guide
4. Cylinder head gasket:
“TOP” mark provided on
gasket comes to crankshaft
pulley side, facing up
(toward cylinder head side).
5. Pin
6. Camshaft
7. Valve lash adjuster
8. Valve cotters
9. Valve spring retainer
10. Valve spring:
Be sure to position spring in place with
its bottom end (small-pitched) facing the
bottom (valve spring seat side).11. Valve stem seal
12. Valve spring seat
13. Exhaust valve
14. Intake valve
15. Oil seal
16. Gasket
17. Camshaft housing bolt: Tightening Torque
: Do not reuse
: Apply engine oil to sliding
: surfaces of each part.
ENGINE MECHANICAL (G10, 1-CAM 6-VALVES ENGINE) 6A-21
VALVES AND CYLINDER HEAD
INSPECTION
Valve Guides
Using a micrometer and bore gauge, take diameter readings on
valve stems and guides to check stem-to-guide clearance.
Be sure to take reading at more than one place along the length of
each stem and guide.
If clearance exceeds limit, replace valve and valve guide.
Item
StandardLimit
Valve stemIn5.457 – 5.480 mm
(0.2148 – 0.2157 in.)———
diameterEx5.440 – 5.455 mm
(0.2142 – 0.2148 in.)———
Valve guide
I.D.In &
Ex5.500 – 5.512 mm
(0.2165 – 0.2170 in.)———
Stem-to-
guide
In0.020 – 0.055 mm
(0.0008 – 0.0021 in.)0.07 mm
(0.0027 in.)
guide
clearanceEx0.045 – 0.072 mm
(0.0018 – 0.0028 in.)0.09 mm
(0.0035 in.)
Page 286 of 557
6A-22 ENGINE MECHANICAL (G10, 1-CAM 6-VALVES ENGINE)
Valve Springs
Referring to data given below, check to be sure that each spring
is in sound condition, free of any evidence of breakage or weak-
ening. Remember, weakened valve springs can cause chatter,
not to mention possibility of reducing power output due to gas
leakage caused by decreased seating pressure.
Item
StandardLimit
Valve spring
free length42.29 mm
(1.6649 in.)41.0 mm
1.6142 in.)
Valve spring
preload
209 – 235 N
(20.9 – 23.5 kg) at
32.6 mm (46.1 –
51.8 lb at 1.28 in.)187 N (18.7 kg)
at 32.6 mm
(41.2 lb at 1.28 in.)
Spring squareness:
Use a square and surface plate to check each spring for square-
ness in terms of clearance between end of valve spring and
square. Valve spring found to exhibit a larger clearance than limit
must be replaced.
Valve spring
2 0 mm (0 079 in )g
squareness limit.2.0 mm (0.079 in.)
Page 340 of 557
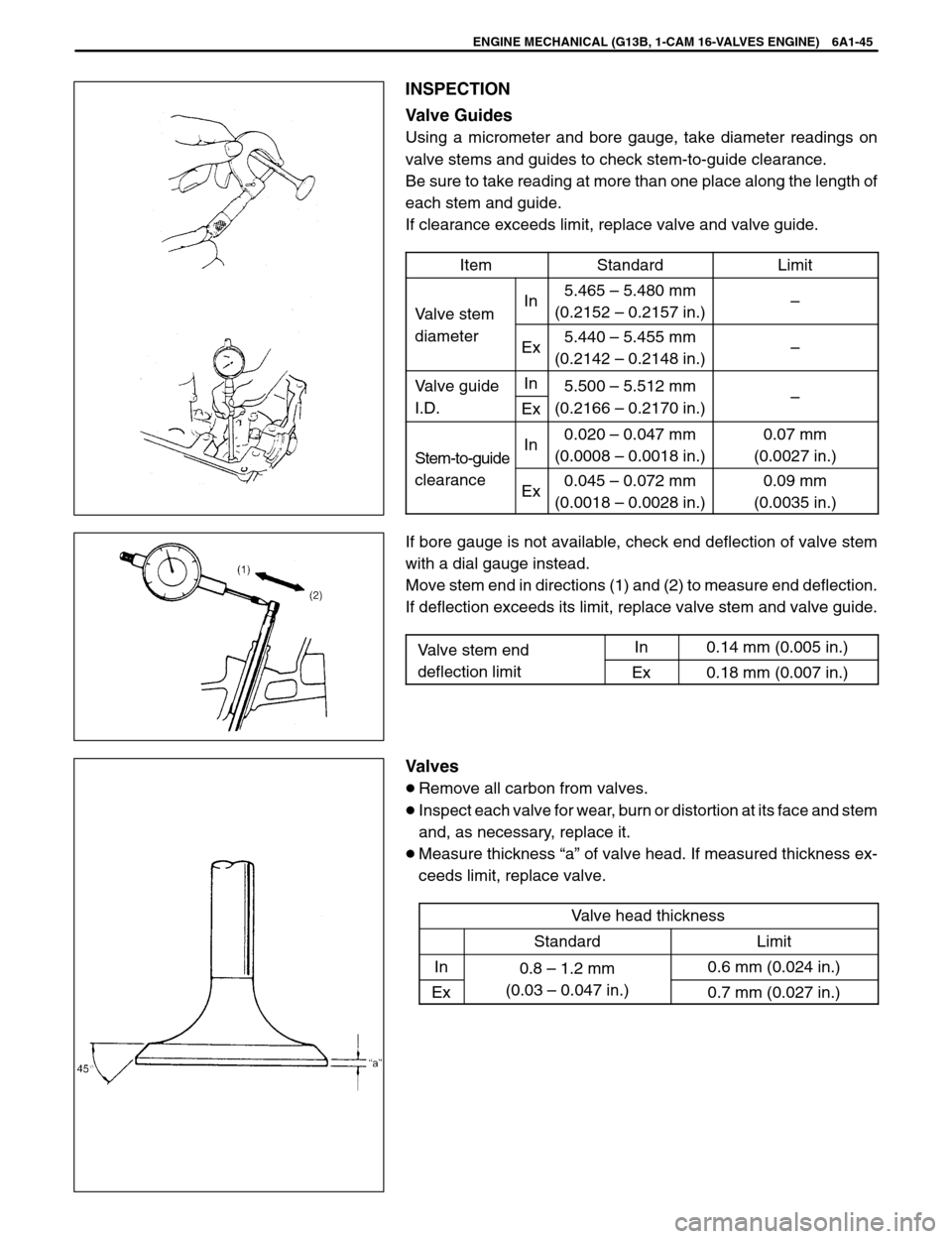
ENGINE MECHANICAL (G13B, 1-CAM 16-VALVES ENGINE) 6A1-45
INSPECTION
Valve Guides
Using a micrometer and bore gauge, take diameter readings on
valve stems and guides to check stem-to-guide clearance.
Be sure to take reading at more than one place along the length of
each stem and guide.
If clearance exceeds limit, replace valve and valve guide.
Item
StandardLimit
Valve stemIn5.465 – 5.480 mm
(0.2152 – 0.2157 in.)–
diameterEx5.440 – 5.455 mm
(0.2142 – 0.2148 in.)–
Valve guideIn5.500 – 5.512 mmg
I.D.Ex(0.2166 – 0.2170 in.)–
Stem-to-guideIn0.020 – 0.047 mm
(0.0008 – 0.0018 in.)0.07 mm
(0.0027 in.)
g
clearanceEx0.045 – 0.072 mm
(0.0018 – 0.0028 in.)0.09 mm
(0.0035 in.)
If bore gauge is not available, check end deflection of valve stem
with a dial gauge instead.
Move stem end in directions (1) and (2) to measure end deflection.
If deflection exceeds its limit, replace valve stem and valve guide.
Valve stem end
In0.14 mm (0.005 in.)
deflection limitEx0.18 mm (0.007 in.)
Valves
Remove all carbon from valves.
Inspect each valve for wear, burn or distortion at its face and stem
and, as necessary, replace it.
Measure thickness “a” of valve head. If measured thickness ex-
ceeds limit, replace valve.
Valve head thickness
StandardLimit
In0.8 – 1.2 mm0.6 mm (0.024 in.)
Ex(0.03 – 0.047 in.)0.7 mm (0.027 in.)
Page 344 of 557
ENGINE MECHANICAL (G13B, 1-CAM 16-VALVES ENGINE) 6A1-49
Valve Springs
Referring to data given below, check to be sure that each spring
is in sound condition, free of any evidence of breakage or weak-
ening. Remember, weakened valve springs can cause chatter,
not to mention possibility of reducing power output due to gas
leakage caused by decreased seating pressure.
Item
StandardLimit
Valve spring
free length36.83 mm
(1.4500 in.)35.67 mm
(1.4043 in.)
Valve spring
preload10.7 – 12.5 kg for
31.5 mm (23.6 –
27.5 lb / 1.24 in.)9.3 kg for 31.5 mm
(20.5 lb / 1.24 in.)
Spring squareness:
Use a square and surface plate to check each spring for square-
ness in terms of clearance between end of valve spring and
square. Valve springs found to exhibit a larger clearance than limit
given below must be replaced.
Valve spring squareness limit: 1.6 mm (0.063 in.)
Page 365 of 557
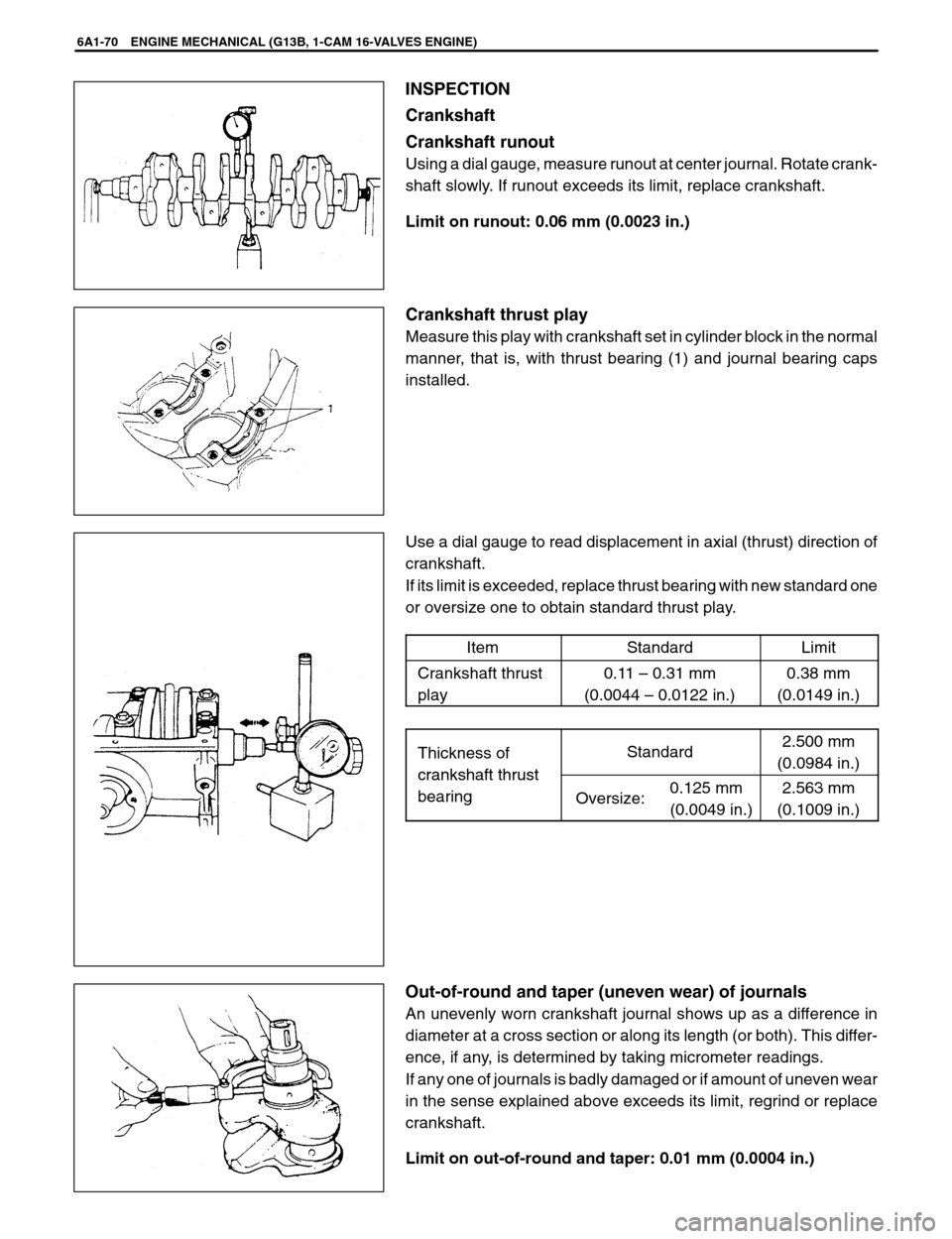
6A1-70 ENGINE MECHANICAL (G13B, 1-CAM 16-VALVES ENGINE)
INSPECTION
Crankshaft
Crankshaft runout
Using a dial gauge, measure runout at center journal. Rotate crank-
shaft slowly. If runout exceeds its limit, replace crankshaft.
Limit on runout: 0.06 mm (0.0023 in.)
Crankshaft thrust play
Measure this play with crankshaft set in cylinder block in the normal
manner, that is, with thrust bearing (1) and journal bearing caps
installed.
Use a dial gauge to read displacement in axial (thrust) direction of
crankshaft.
If its limit is exceeded, replace thrust bearing with new standard one
or oversize one to obtain standard thrust play.
Item
StandardLimit
Crankshaft thrust
play0.11 – 0.31 mm
(0.0044 – 0.0122 in.)0.38 mm
(0.0149 in.)
Thickness of
crankshaft thrust
Standard2.500 mm
(0.0984 in.)
crankshaft thrust
bearingOversize:0.125 mm
(0.0049 in.)2.563 mm
(0.1009 in.)
Out-of-round and taper (uneven wear) of journals
An unevenly worn crankshaft journal shows up as a difference in
diameter at a cross section or along its length (or both). This differ-
ence, if any, is determined by taking micrometer readings.
If any one of journals is badly damaged or if amount of uneven wear
in the sense explained above exceeds its limit, regrind or replace
crankshaft.
Limit on out-of-round and taper: 0.01 mm (0.0004 in.)