Page 22 of 557
M/T A/T
G10 G13
[A] [A]
[B] [B]
0A-18 GENERAL INFORMATION
IDENTIFICATION INFORMATION
VEHICLE IDENTIFICATION NUMBER
The number is punched on the front dash panel in the engine room.
IDENTIFICATION WHETHER VEHICLE
EQUIPPED WITH WU-TWC OR NOT
It can be identified by the shape of exhaust manifold (1) and ex-
haust pipe (2).
[A]: Vehicle equipped with WU-TWC (3)
[B]: Vehicle not equipped with WU-TWC
ENGINE IDENTIFICATION NUMBER
The number is punched on the cylinder block.
TRANSMISSION IDENTIFICATION NUMBER
The number is punched on the transmission case.
Page 25 of 557
When using floor jack:
GENERAL INFORMATION 0A-21
In raising front or rear vehicle end off the floor by jacking, be sure
to put the jack against the center portion of front cross member (1)
or rear cross member (2).
WARNING:
Never apply jack against suspension parts (i.e., stabilizer,
etc.) or vehicle floor, or it may get deformed.
If the vehicle to be jacked up only at the front or rear end,
be sure to block the wheels on ground in order to ensure
safety.
After the vehicle is jacked up, be sure to support it on
stands. It is extremely dangerous to do any work on the
vehicle raised on jack alone.
To perform service with either front or rear vehicle end jacked up,
be sure to place safety stands under body so that body is securely
supported. And then check to ensure that body does not slide on
safety stands and the vehicle is held stable for safety’s sake.
Page 56 of 557
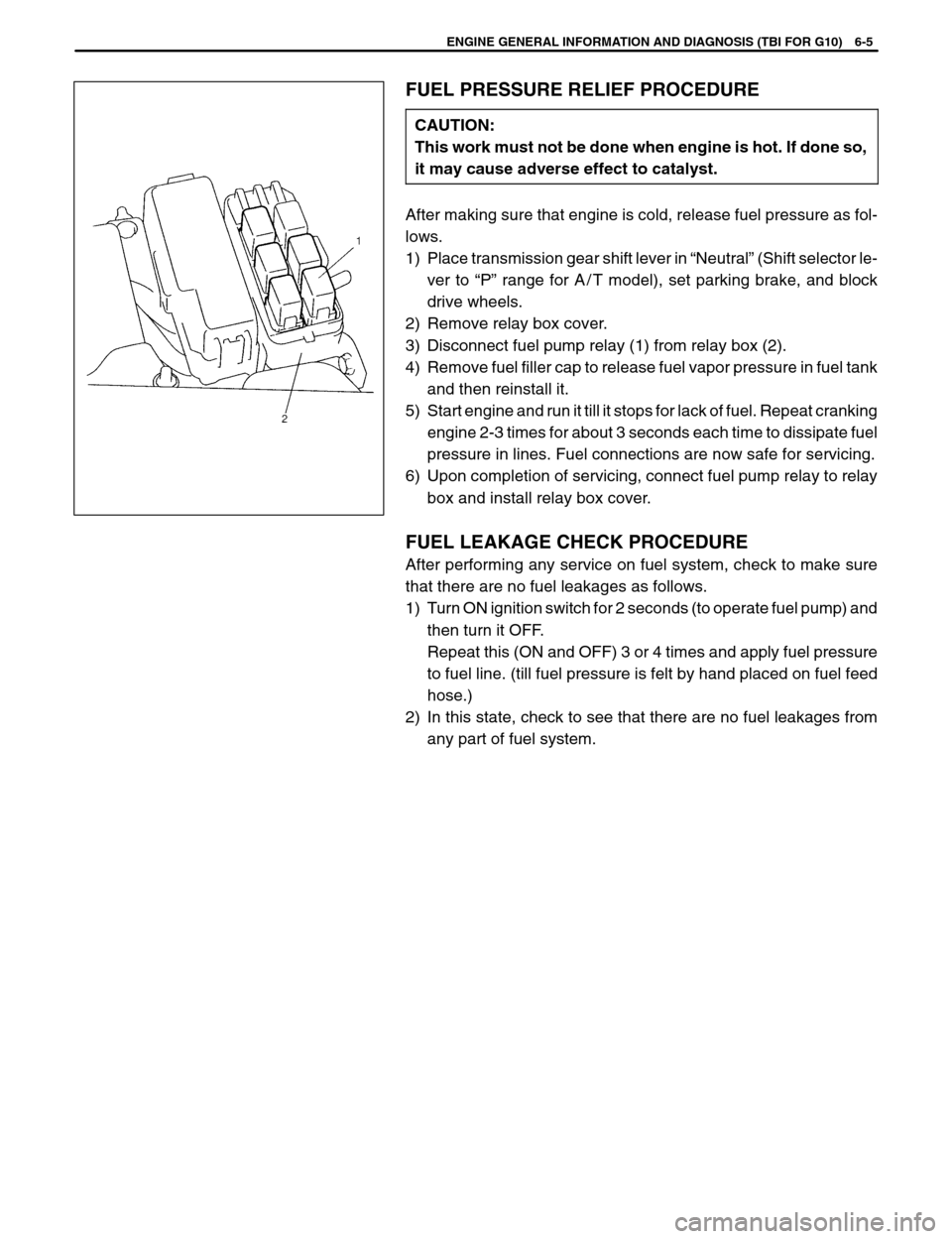
ENGINE GENERAL INFORMATION AND DIAGNOSIS (TBI FOR G10) 6-5
FUEL PRESSURE RELIEF PROCEDURE
CAUTION:
This work must not be done when engine is hot. If done so,
it may cause adverse effect to catalyst.
After making sure that engine is cold, release fuel pressure as fol-
lows.
1) Place transmission gear shift lever in “Neutral” (Shift selector le-
ver to “P” range for A / T model), set parking brake, and block
drive wheels.
2) Remove relay box cover.
3) Disconnect fuel pump relay (1) from relay box (2).
4) Remove fuel filler cap to release fuel vapor pressure in fuel tank
and then reinstall it.
5) Start engine and run it till it stops for lack of fuel. Repeat cranking
engine 2-3 times for about 3 seconds each time to dissipate fuel
pressure in lines. Fuel connections are now safe for servicing.
6) Upon completion of servicing, connect fuel pump relay to relay
box and install relay box cover.
FUEL LEAKAGE CHECK PROCEDURE
After performing any service on fuel system, check to make sure
that there are no fuel leakages as follows.
1) Turn ON ignition switch for 2 seconds (to operate fuel pump) and
then turn it OFF.
Repeat this (ON and OFF) 3 or 4 times and apply fuel pressure
to fuel line. (till fuel pressure is felt by hand placed on fuel feed
hose.)
2) In this state, check to see that there are no fuel leakages from
any part of fuel system.
Page 138 of 557
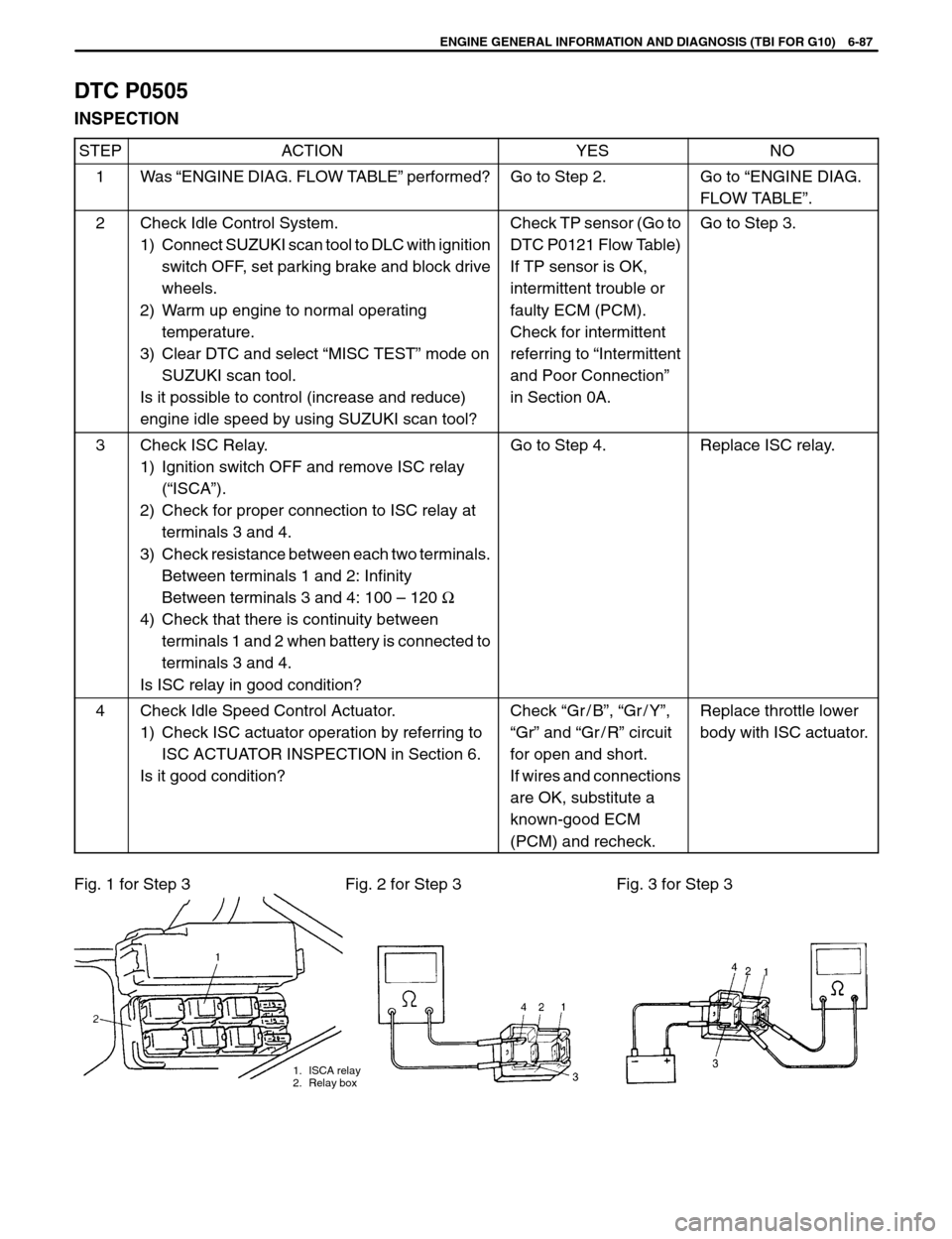
ENGINE GENERAL INFORMATION AND DIAGNOSIS (TBI FOR G10) 6-87
Fig. 1 for Step 3 Fig. 2 for Step 3 Fig. 3 for Step 3
1. ISCA relay
2. Relay box
DTC P0505
INSPECTION
STEPACTIONYESNO
1Was “ENGINE DIAG. FLOW TABLE” performed?Go to Step 2.Go to “ENGINE DIAG.
FLOW TABLE”.
2Check Idle Control System.
1) Connect SUZUKI scan tool to DLC with ignition
switch OFF, set parking brake and block drive
wheels.
2) Warm up engine to normal operating
temperature.
3) Clear DTC and select “MISC TEST” mode on
SUZUKI scan tool.
Is it possible to control (increase and reduce)
engine idle speed by using SUZUKI scan tool?Check TP sensor (Go to
DTC P0121 Flow Table)
If TP sensor is OK,
intermittent trouble or
faulty ECM (PCM).
Check for intermittent
referring to “Intermittent
and Poor Connection”
in Section 0A.Go to Step 3.
3Check ISC Relay.
1) Ignition switch OFF and remove ISC relay
(“ISCA”).
2) Check for proper connection to ISC relay at
terminals 3 and 4.
3) Check resistance between each two terminals.
Between terminals 1 and 2: Infinity
Between terminals 3 and 4: 100 – 120 Ω
4) Check that there is continuity between
terminals 1 and 2 when battery is connected to
terminals 3 and 4.
Is ISC relay in good condition?Go to Step 4.Replace ISC relay.
4Check Idle Speed Control Actuator.
1) Check ISC actuator operation by referring to
ISC ACTUATOR INSPECTION in Section 6.
Is it good condition?Check “Gr / B”, “Gr / Y”,
“Gr” and “Gr / R” circuit
for open and short.
If wires and connections
are OK, substitute a
known-good ECM
(PCM) and recheck.Replace throttle lower
body with ISC actuator.
Page 152 of 557
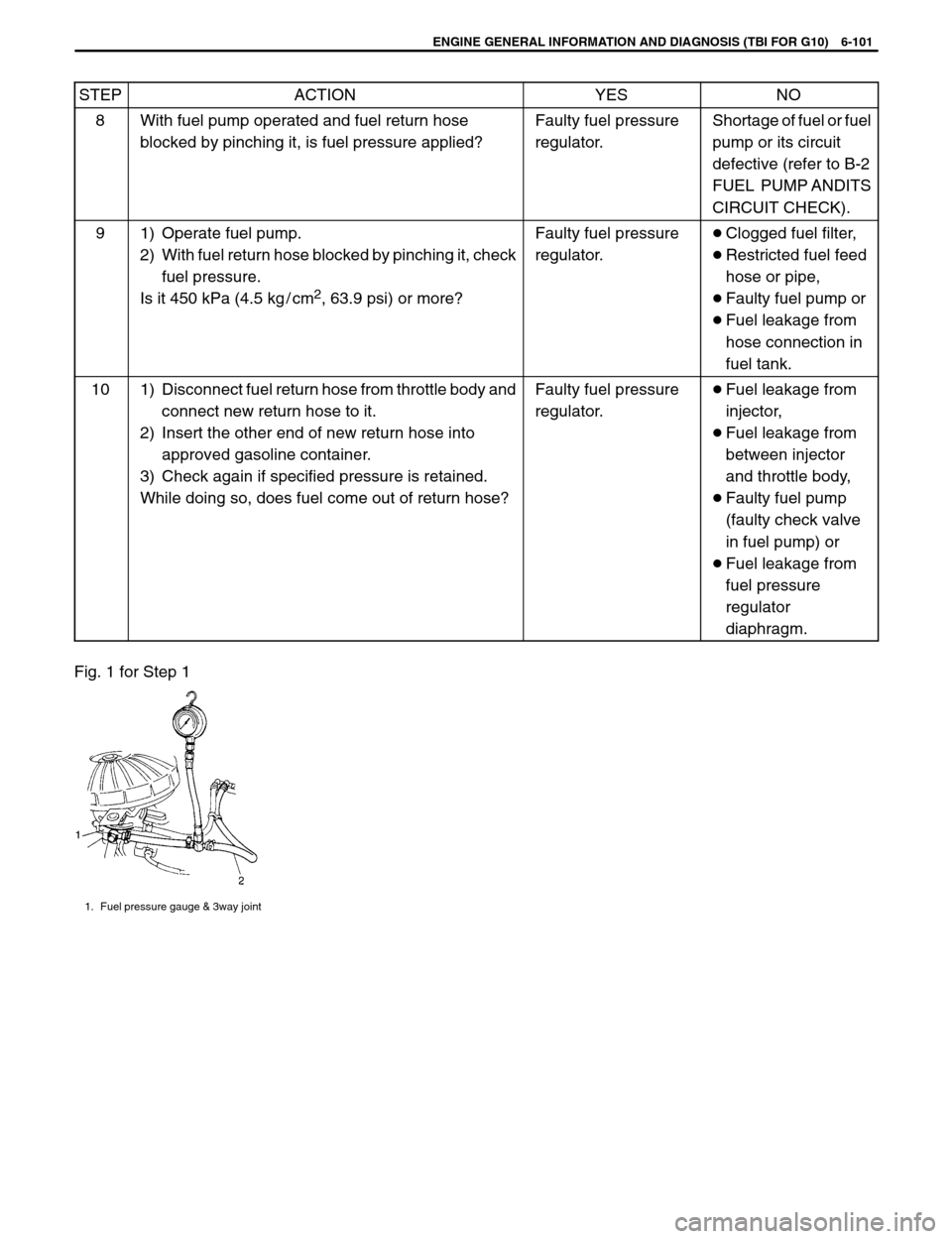
ENGINE GENERAL INFORMATION AND DIAGNOSIS (TBI FOR G10) 6-101
Fig. 1 for Step 1
1. Fuel pressure gauge & 3way joint
STEPACTIONYESNO
8With fuel pump operated and fuel return hose
blocked by pinching it, is fuel pressure applied?Faulty fuel pressure
regulator.Shortage of fuel or fuel
pump or its circuit
defective (refer to B-2
FUEL PUMP ANDITS
CIRCUIT CHECK).
91) Operate fuel pump.
2) With fuel return hose blocked by pinching it, check
fuel pressure.
Is it 450 kPa (4.5 kg / cm
2, 63.9 psi) or more?
Faulty fuel pressure
regulator.Clogged fuel filter,
Restricted fuel feed
hose or pipe,
Faulty fuel pump or
Fuel leakage from
hose connection in
fuel tank.
101) Disconnect fuel return hose from throttle body and
connect new return hose to it.
2) Insert the other end of new return hose into
approved gasoline container.
3) Check again if specified pressure is retained.
While doing so, does fuel come out of return hose?Faulty fuel pressure
regulator.Fuel leakage from
injector,
Fuel leakage from
between injector
and throttle body,
Faulty fuel pump
(faulty check valve
in fuel pump) or
Fuel leakage from
fuel pressure
regulator
diaphragm.
Page 161 of 557
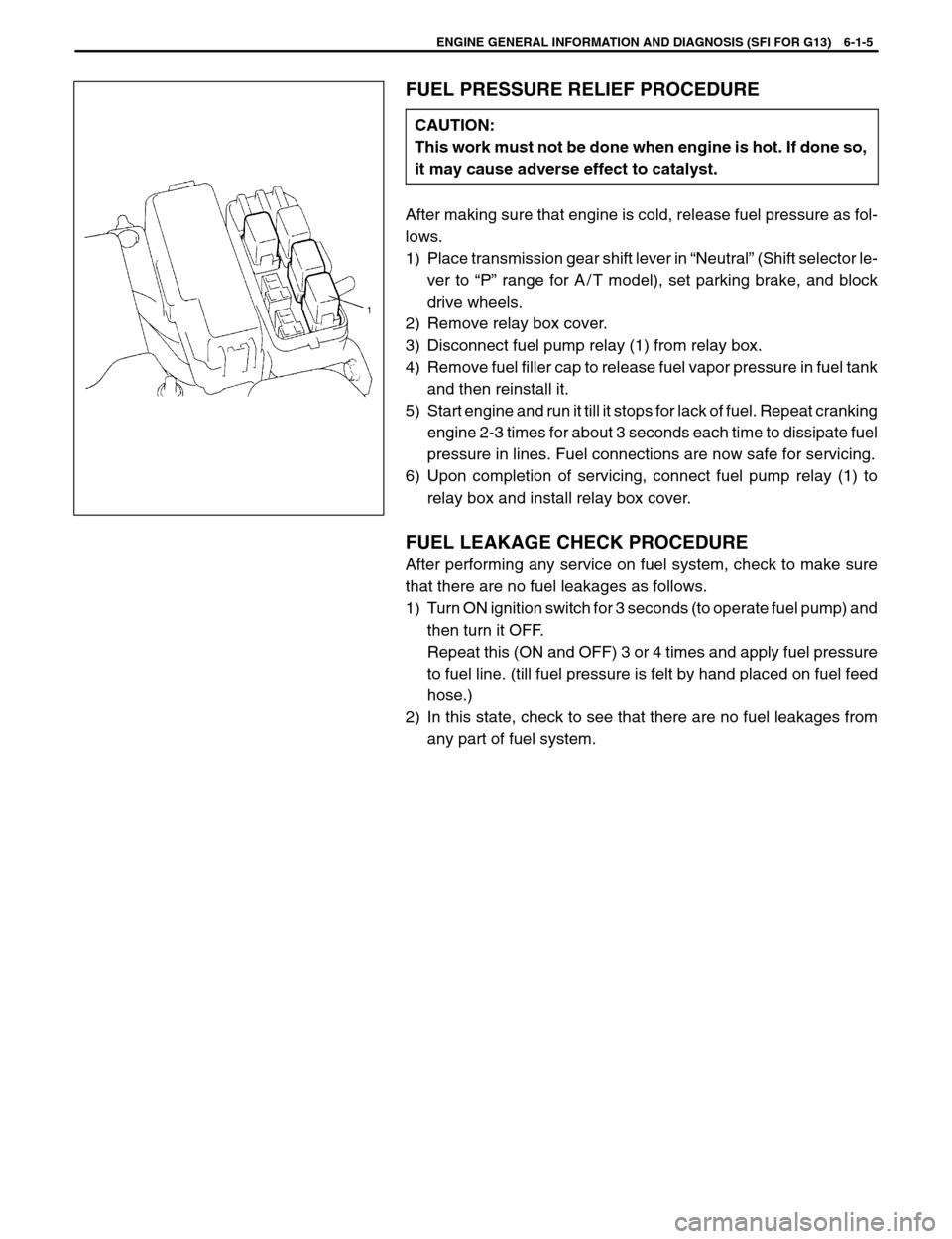
ENGINE GENERAL INFORMATION AND DIAGNOSIS (SFI FOR G13) 6-1-5
FUEL PRESSURE RELIEF PROCEDURE
CAUTION:
This work must not be done when engine is hot. If done so,
it may cause adverse effect to catalyst.
After making sure that engine is cold, release fuel pressure as fol-
lows.
1) Place transmission gear shift lever in “Neutral” (Shift selector le-
ver to “P” range for A / T model), set parking brake, and block
drive wheels.
2) Remove relay box cover.
3) Disconnect fuel pump relay (1) from relay box.
4) Remove fuel filler cap to release fuel vapor pressure in fuel tank
and then reinstall it.
5) Start engine and run it till it stops for lack of fuel. Repeat cranking
engine 2-3 times for about 3 seconds each time to dissipate fuel
pressure in lines. Fuel connections are now safe for servicing.
6) Upon completion of servicing, connect fuel pump relay (1) to
relay box and install relay box cover.
FUEL LEAKAGE CHECK PROCEDURE
After performing any service on fuel system, check to make sure
that there are no fuel leakages as follows.
1) Turn ON ignition switch for 3 seconds (to operate fuel pump) and
then turn it OFF.
Repeat this (ON and OFF) 3 or 4 times and apply fuel pressure
to fuel line. (till fuel pressure is felt by hand placed on fuel feed
hose.)
2) In this state, check to see that there are no fuel leakages from
any part of fuel system.
Page 248 of 557
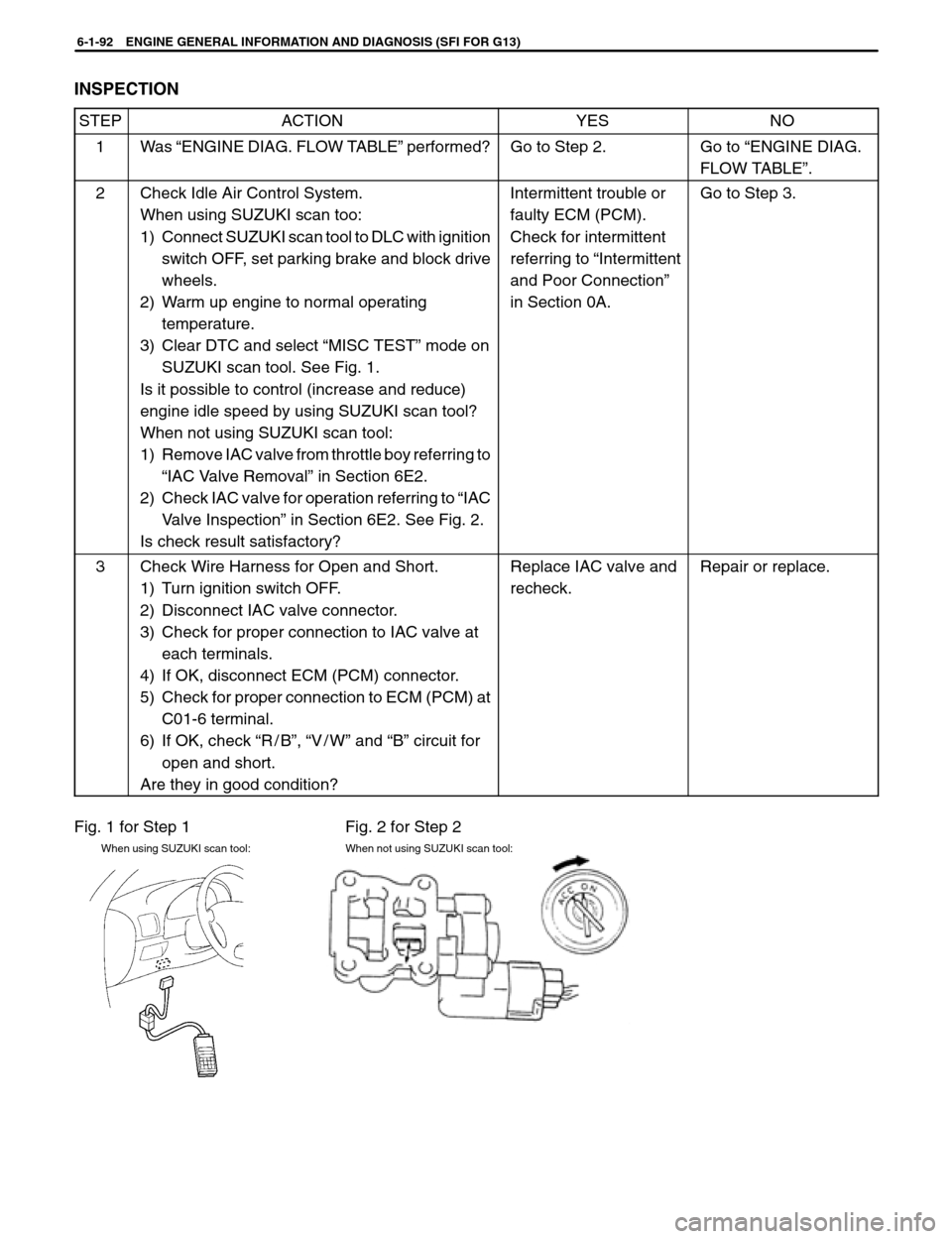
6-1-92 ENGINE GENERAL INFORMATION AND DIAGNOSIS (SFI FOR G13)
Fig. 1 for Step 1 Fig. 2 for Step 2
When using SUZUKI scan tool: When not using SUZUKI scan tool:
INSPECTION
STEPACTIONYESNO
1Was “ENGINE DIAG. FLOW TABLE” performed?Go to Step 2.Go to “ENGINE DIAG.
FLOW TABLE”.
2Check Idle Air Control System.
When using SUZUKI scan too:
1) Connect SUZUKI scan tool to DLC with ignition
switch OFF, set parking brake and block drive
wheels.
2) Warm up engine to normal operating
temperature.
3) Clear DTC and select “MISC TEST” mode on
SUZUKI scan tool. See Fig. 1.
Is it possible to control (increase and reduce)
engine idle speed by using SUZUKI scan tool?
When not using SUZUKI scan tool:
1) Remove IAC valve from throttle boy referring to
“IAC Valve Removal” in Section 6E2.
2) Check IAC valve for operation referring to “IAC
Valve Inspection” in Section 6E2. See Fig. 2.
Is check result satisfactory?Intermittent trouble or
faulty ECM (PCM).
Check for intermittent
referring to “Intermittent
and Poor Connection”
in Section 0A.Go to Step 3.
3Check Wire Harness for Open and Short.
1) Turn ignition switch OFF.
2) Disconnect IAC valve connector.
3) Check for proper connection to IAC valve at
each terminals.
4) If OK, disconnect ECM (PCM) connector.
5) Check for proper connection to ECM (PCM) at
C01-6 terminal.
6) If OK, check “R/B”, “V/W” and “B” circuit for
open and short.
Are they in good condition?Replace IAC valve and
recheck.Repair or replace.
Page 258 of 557
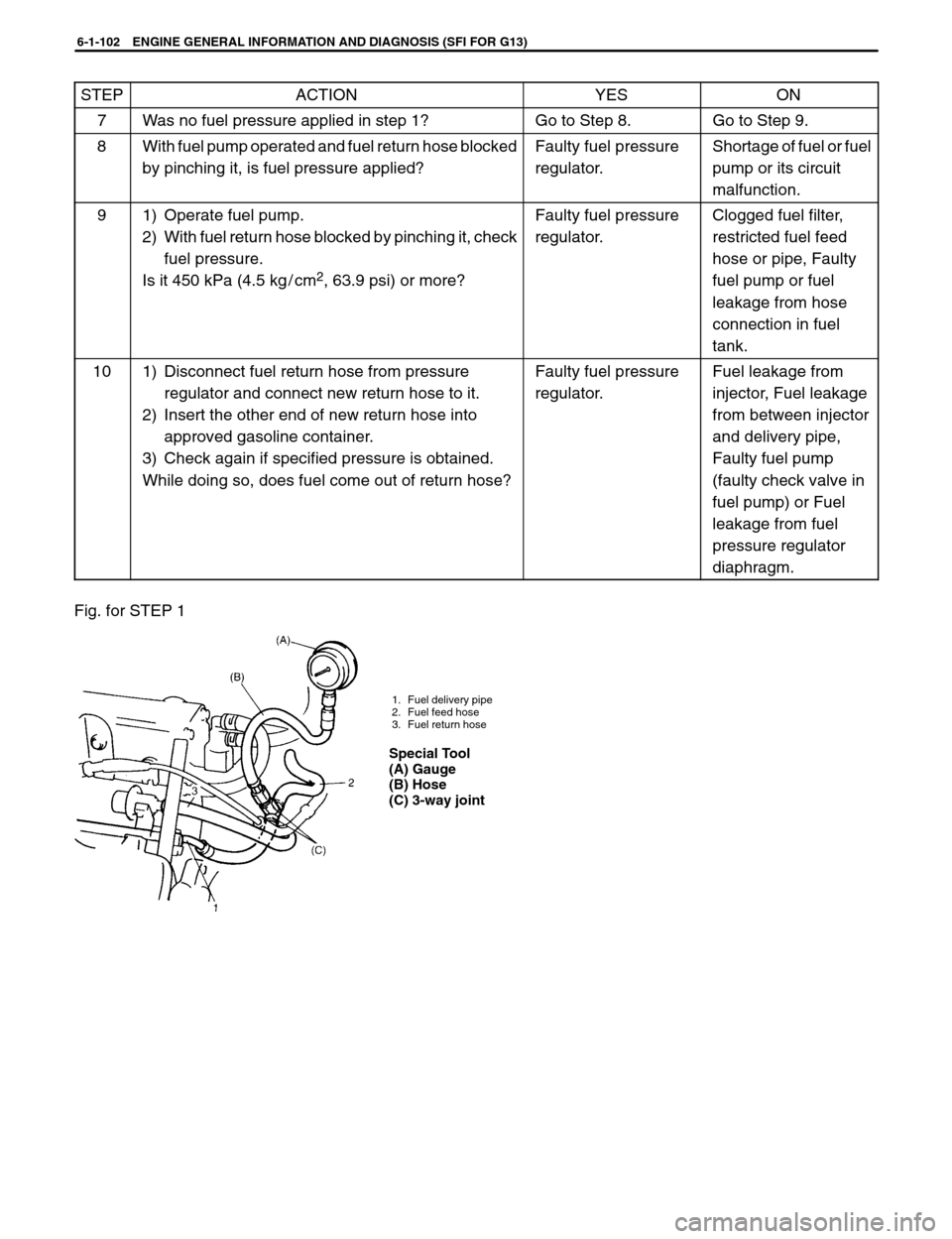
6-1-102 ENGINE GENERAL INFORMATION AND DIAGNOSIS (SFI FOR G13)
1. Fuel delivery pipe
2. Fuel feed hose
3. Fuel return hose
Special Tool
(A) Gauge
(B) Hose
(C) 3-way joint
STEPACTIONYESON
7Was no fuel pressure applied in step 1?Go to Step 8.Go to Step 9.
8With fuel pump operated and fuel return hose blocked
by pinching it, is fuel pressure applied?Faulty fuel pressure
regulator.Shortage of fuel or fuel
pump or its circuit
malfunction.
91) Operate fuel pump.
2) With fuel return hose blocked by pinching it, check
fuel pressure.
Is it 450 kPa (4.5 kg / cm
2, 63.9 psi) or more?
Faulty fuel pressure
regulator.Clogged fuel filter,
restricted fuel feed
hose or pipe, Faulty
fuel pump or fuel
leakage from hose
connection in fuel
tank.
101) Disconnect fuel return hose from pressure
regulator and connect new return hose to it.
2) Insert the other end of new return hose into
approved gasoline container.
3) Check again if specified pressure is obtained.
While doing so, does fuel come out of return hose?Faulty fuel pressure
regulator.Fuel leakage from
injector, Fuel leakage
from between injector
and delivery pipe,
Faulty fuel pump
(faulty check valve in
fuel pump) or Fuel
leakage from fuel
pressure regulator
diaphragm.
Fig. for STEP 1