Page 363 of 557
1. Cylinder block
2. Front oil seal:
Apply engine oil to contact part
of crankshaft with oil seal lip.
3. Main bearing:
Apply engine oil to bearing
inside surfaces.
4. Bearing cap
5. Cap bolt:
Apply engine oil to bolt and
bearing surfaces.
6. Timing pulley key7. Crankshaft:
Apply engine oil to crankshaft
journals.
8. Thrust bearing:
Set oil grooves of bearing to
crank weds.
Apply engine oil.
9. Rear oil seal:
Apply engine oil to contact part
of crankshaft with oil seal lip.10. Pin
11. Oil seal housing gasket
12. Oil seal housing
13. Housing bolt
14. Input shaft bearing
15. Flywheel
16. Flywheel bolt
: Do not reuse
: Tightening Torque
15 16
78 N.m (7.8 kg-m) for flywheel
95 N.m (9.5 kg-m) for drive plate
6A1-68 ENGINE MECHANICAL (G13B, 1-CAM 16-VALVES ENGINE)
MAIN BEARINGS, CRANKSHAFT AND CYLINDER BLOCK
Page 364 of 557
1. Flywheel bolt
2. Bolt
ENGINE MECHANICAL (G13B, 1-CAM 16-VALVES ENGINE) 6A1-69
REMOVAL
1) Remove engine assembly from body as previously outlined.
2) Remove clutch cover, clutch disc and flywheel (drive plate for
A / T).
Special Tool
(A): 09924-17810
3) Remove crankshaft pulley, timing belt and crankshaft timing
pulley.
4) Remove cylinder head assembly.
5) Remove oil pan and oil pump strainer.
6) Remove oil pump (1).
7) Remove oil seal housing.
8) Remove connecting rod bearing caps.
9) Loosen crankshaft bearing cap bolts in such order as indicated
in figure a little at a time and remove bearing caps.
10) Remove crankshaft from cylinder block.
Page 365 of 557
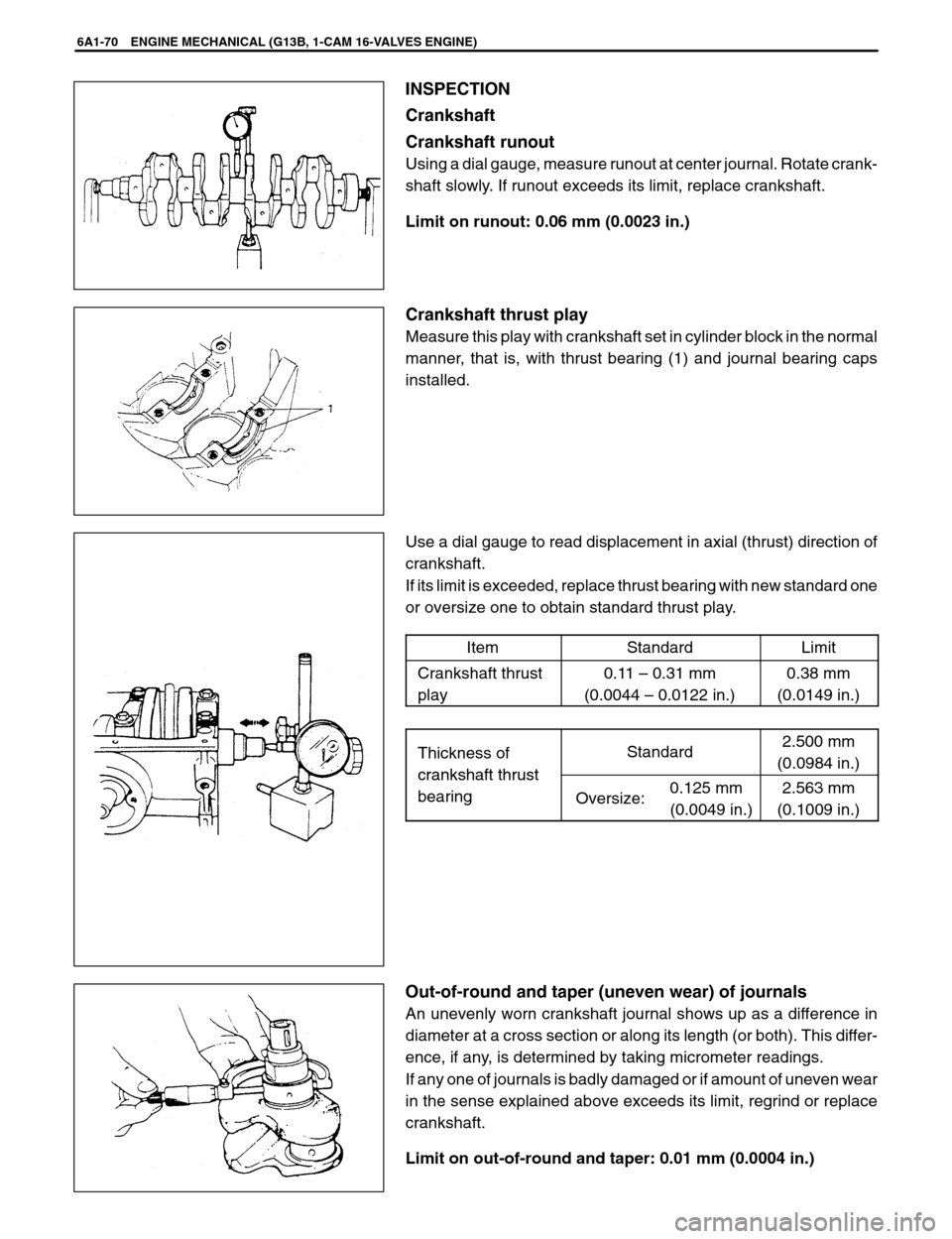
6A1-70 ENGINE MECHANICAL (G13B, 1-CAM 16-VALVES ENGINE)
INSPECTION
Crankshaft
Crankshaft runout
Using a dial gauge, measure runout at center journal. Rotate crank-
shaft slowly. If runout exceeds its limit, replace crankshaft.
Limit on runout: 0.06 mm (0.0023 in.)
Crankshaft thrust play
Measure this play with crankshaft set in cylinder block in the normal
manner, that is, with thrust bearing (1) and journal bearing caps
installed.
Use a dial gauge to read displacement in axial (thrust) direction of
crankshaft.
If its limit is exceeded, replace thrust bearing with new standard one
or oversize one to obtain standard thrust play.
Item
StandardLimit
Crankshaft thrust
play0.11 – 0.31 mm
(0.0044 – 0.0122 in.)0.38 mm
(0.0149 in.)
Thickness of
crankshaft thrust
Standard2.500 mm
(0.0984 in.)
crankshaft thrust
bearingOversize:0.125 mm
(0.0049 in.)2.563 mm
(0.1009 in.)
Out-of-round and taper (uneven wear) of journals
An unevenly worn crankshaft journal shows up as a difference in
diameter at a cross section or along its length (or both). This differ-
ence, if any, is determined by taking micrometer readings.
If any one of journals is badly damaged or if amount of uneven wear
in the sense explained above exceeds its limit, regrind or replace
crankshaft.
Limit on out-of-round and taper: 0.01 mm (0.0004 in.)
Page 366 of 557
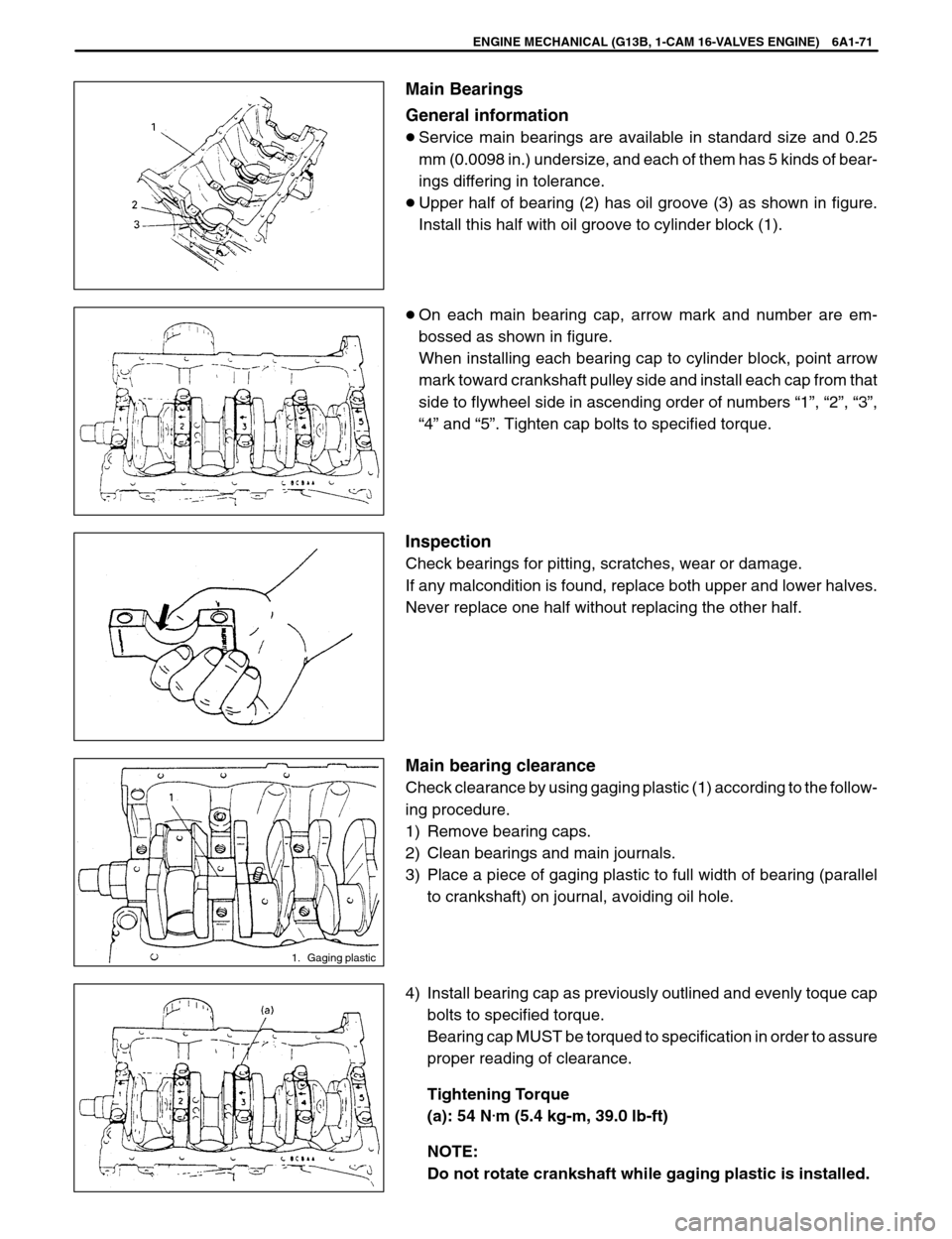
1. Gaging plastic
ENGINE MECHANICAL (G13B, 1-CAM 16-VALVES ENGINE) 6A1-71
Main Bearings
General information
Service main bearings are available in standard size and 0.25
mm (0.0098 in.) undersize, and each of them has 5 kinds of bear-
ings differing in tolerance.
Upper half of bearing (2) has oil groove (3) as shown in figure.
Install this half with oil groove to cylinder block (1).
On each main bearing cap, arrow mark and number are em-
bossed as shown in figure.
When installing each bearing cap to cylinder block, point arrow
mark toward crankshaft pulley side and install each cap from that
side to flywheel side in ascending order of numbers “1”, “2”, “3”,
“4” and “5”. Tighten cap bolts to specified torque.
Inspection
Check bearings for pitting, scratches, wear or damage.
If any malcondition is found, replace both upper and lower halves.
Never replace one half without replacing the other half.
Main bearing clearance
Check clearance by using gaging plastic (1) according to the follow-
ing procedure.
1) Remove bearing caps.
2) Clean bearings and main journals.
3) Place a piece of gaging plastic to full width of bearing (parallel
to crankshaft) on journal, avoiding oil hole.
4) Install bearing cap as previously outlined and evenly toque cap
bolts to specified torque.
Bearing cap MUST be torqued to specification in order to assure
proper reading of clearance.
Tightening Torque
(a): 54 N
.m (5.4 kg-m, 39.0 lb-ft)
NOTE:
Do not rotate crankshaft while gaging plastic is installed.
Page 368 of 557
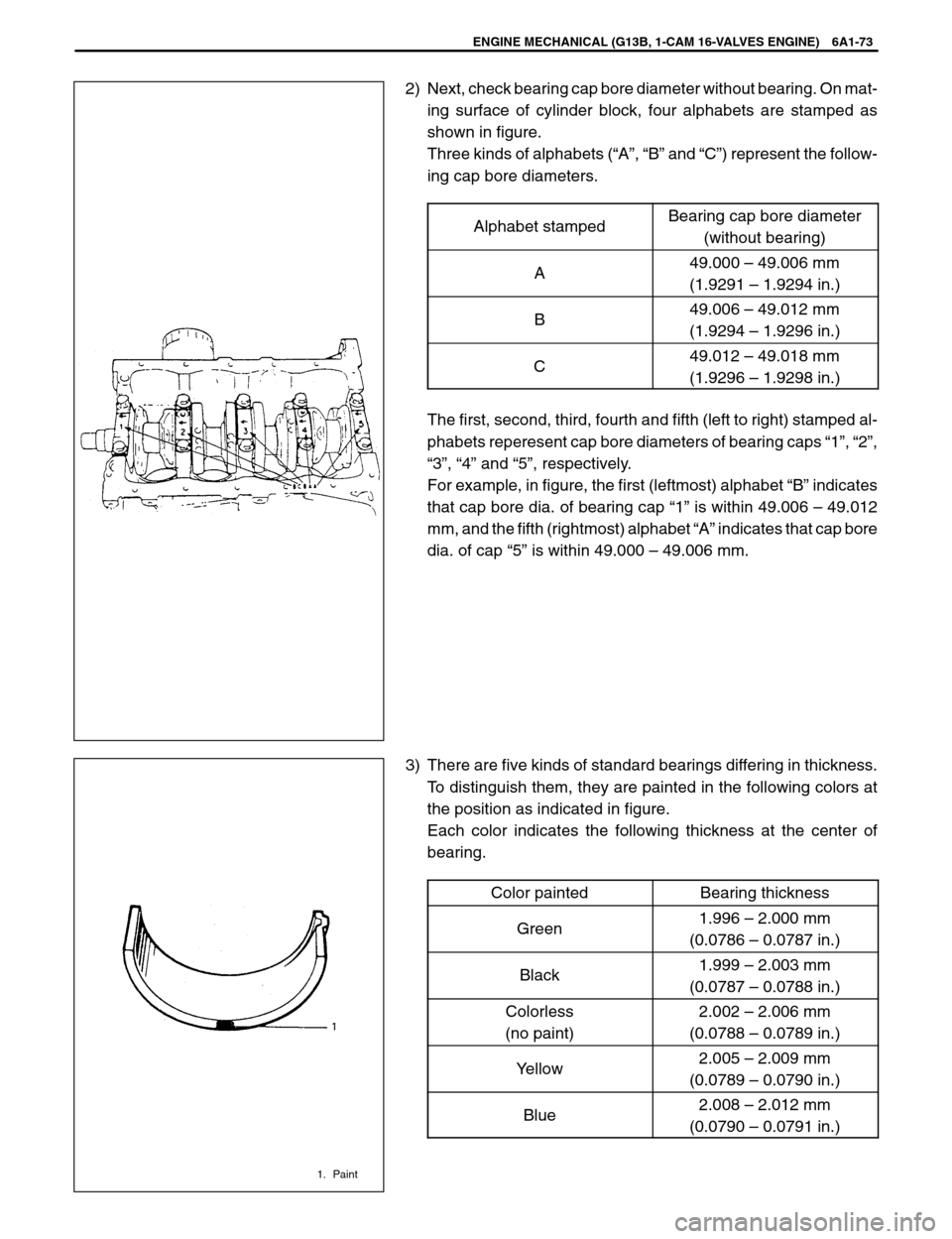
1. Paint
ENGINE MECHANICAL (G13B, 1-CAM 16-VALVES ENGINE) 6A1-73
2) Next, check bearing cap bore diameter without bearing. On mat-
ing surface of cylinder block, four alphabets are stamped as
shown in figure.
Three kinds of alphabets (“A”, “B” and “C”) represent the follow-
ing cap bore diameters.
Alphabet stamped
Bearing cap bore diameter
(without bearing)
A49.000 – 49.006 mm
(1.9291 – 1.9294 in.)
B49.006 – 49.012 mm
(1.9294 – 1.9296 in.)
C49.012 – 49.018 mm
(1.9296 – 1.9298 in.)
The first, second, third, fourth and fifth (left to right) stamped al-
phabets reperesent cap bore diameters of bearing caps “1”, “2”,
“3”, “4” and “5”, respectively.
For example, in figure, the first (leftmost) alphabet “B” indicates
that cap bore dia. of bearing cap “1” is within 49.006 – 49.012
mm, and the fifth (rightmost) alphabet “A” indicates that cap bore
dia. of cap “5” is within 49.000 – 49.006 mm.
3) There are five kinds of standard bearings differing in thickness.
To distinguish them, they are painted in the following colors at
the position as indicated in figure.
Each color indicates the following thickness at the center of
bearing.
Color painted
Bearing thickness
Green1.996 – 2.000 mm
(0.0786 – 0.0787 in.)
Black1.999 – 2.003 mm
(0.0787 – 0.0788 in.)
Colorless
(no paint)2.002 – 2.006 mm
(0.0788 – 0.0789 in.)
Yellow2.005 – 2.009 mm
(0.0789 – 0.0790 in.)
Blue2.008 – 2.012 mm
(0.0790 – 0.0791 in.)
Page 369 of 557
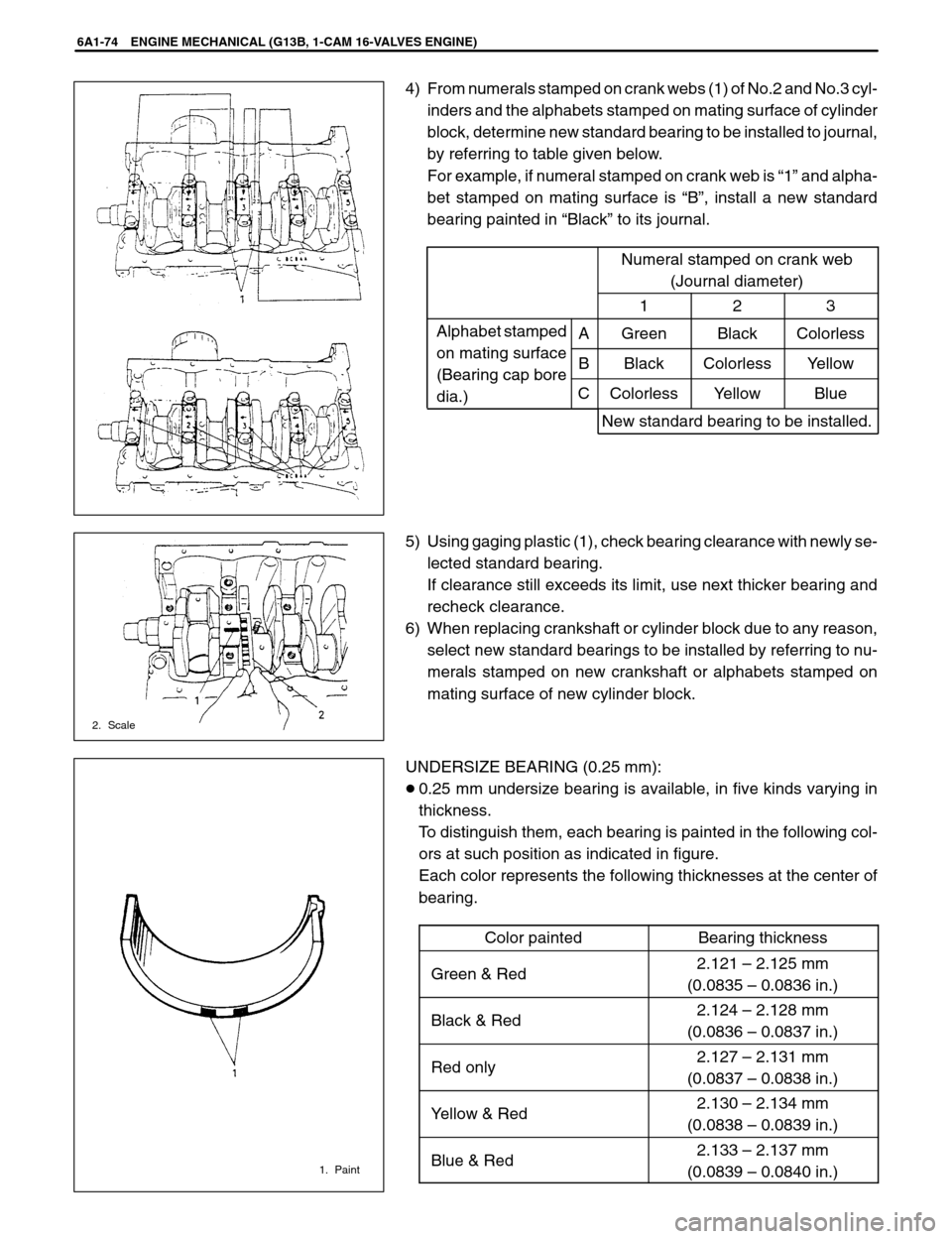
2. Scale
1. Paint
6A1-74 ENGINE MECHANICAL (G13B, 1-CAM 16-VALVES ENGINE)
4) From numerals stamped on crank webs (1) of No.2 and No.3 cyl-
inders and the alphabets stamped on mating surface of cylinder
block, determine new standard bearing to be installed to journal,
by referring to table given below.
For example, if numeral stamped on crank web is “1” and alpha-
bet stamped on mating surface is “B”, install a new standard
bearing painted in “Black” to its journal.
Numeral stamped on crank web
(Journal diameter)
123
Alphabet stamped
ti f
AGreenBlackColorless
on mating surface
(Bearing capboreBBlackColorlessYellow(Bearing ca bore
dia.)CColorlessYellowBlue
New standard bearing to be installed.
5) Using gaging plastic (1), check bearing clearance with newly se-
lected standard bearing.
If clearance still exceeds its limit, use next thicker bearing and
recheck clearance.
6) When replacing crankshaft or cylinder block due to any reason,
select new standard bearings to be installed by referring to nu-
merals stamped on new crankshaft or alphabets stamped on
mating surface of new cylinder block.
UNDERSIZE BEARING (0.25 mm):
0.25 mm undersize bearing is available, in five kinds varying in
thickness.
To distinguish them, each bearing is painted in the following col-
ors at such position as indicated in figure.
Each color represents the following thicknesses at the center of
bearing.
Color painted
Bearing thickness
Green & Red2.121 – 2.125 mm
(0.0835 – 0.0836 in.)
Black & Red2.124 – 2.128 mm
(0.0836 – 0.0837 in.)
Red only2.127 – 2.131 mm
(0.0837 – 0.0838 in.)
Yellow & Red2.130 – 2.134 mm
(0.0838 – 0.0839 in.)
Blue & Red2.133 – 2.137 mm
(0.0839 – 0.0840 in.)
Page 370 of 557
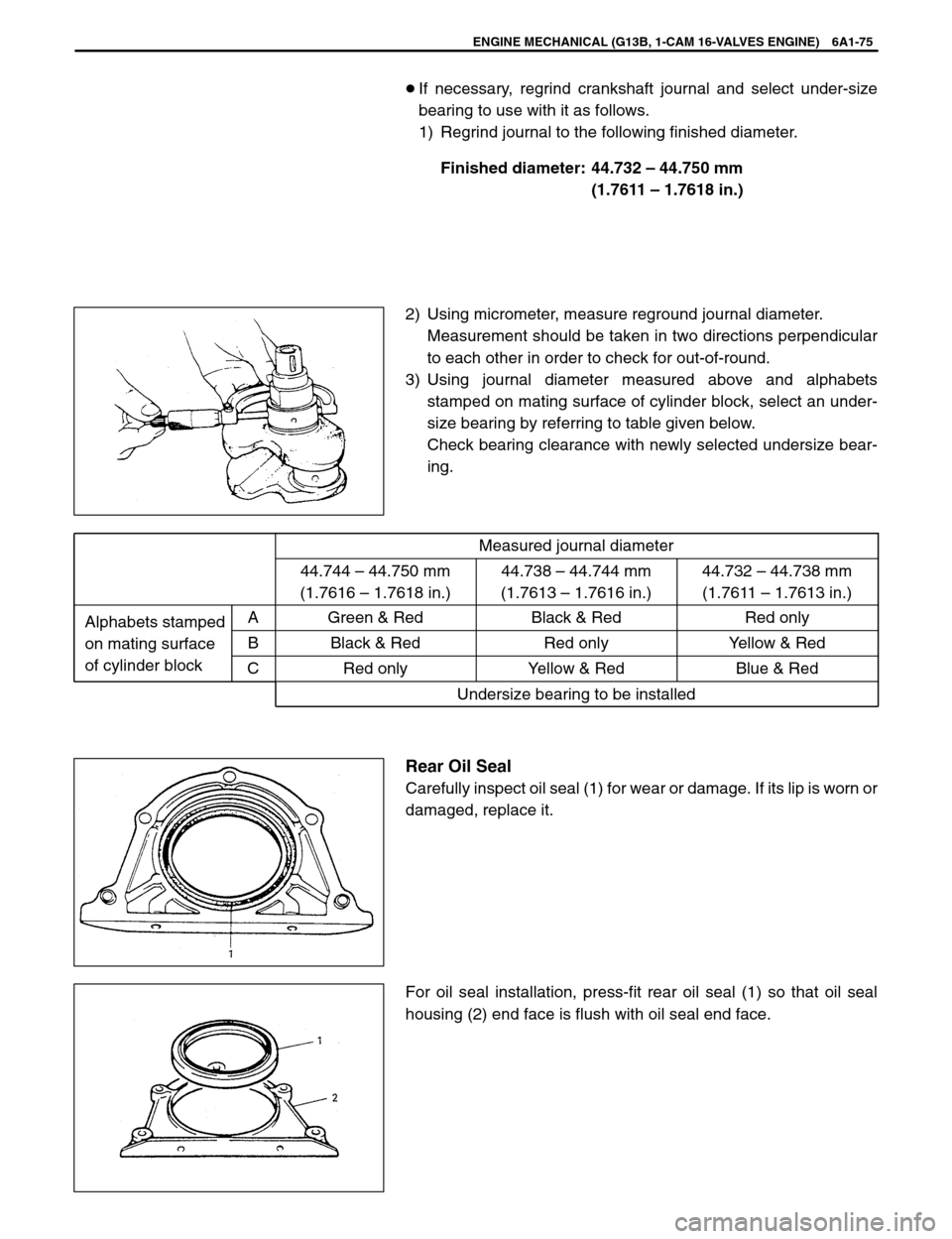
ENGINE MECHANICAL (G13B, 1-CAM 16-VALVES ENGINE) 6A1-75
If necessary, regrind crankshaft journal and select under-size
bearing to use with it as follows.
1) Regrind journal to the following finished diameter.
Finished diameter: 44.732 – 44.750 mm
(1.7611 – 1.7618 in.)
2) Using micrometer, measure reground journal diameter.
Measurement should be taken in two directions perpendicular
to each other in order to check for out-of-round.
3) Using journal diameter measured above and alphabets
stamped on mating surface of cylinder block, select an under-
size bearing by referring to table given below.
Check bearing clearance with newly selected undersize bear-
ing.
Measured journal diameter
44.744 – 44.750 mm
(1.7616 – 1.7618 in.)44.738 – 44.744 mm
(1.7613 – 1.7616 in.)44.732 – 44.738 mm
(1.7611 – 1.7613 in.)
Alphabets stampedAGreen & RedBlack & RedRed only
on mating surfaceBBlack & RedRed onlyYellow & Red
of cylinder block
CRed onlyYellow & RedBlue & Red
Undersize bearing to be installed
Rear Oil Seal
Carefully inspect oil seal (1) for wear or damage. If its lip is worn or
damaged, replace it.
For oil seal installation, press-fit rear oil seal (1) so that oil seal
housing (2) end face is flush with oil seal end face.
Page 371 of 557
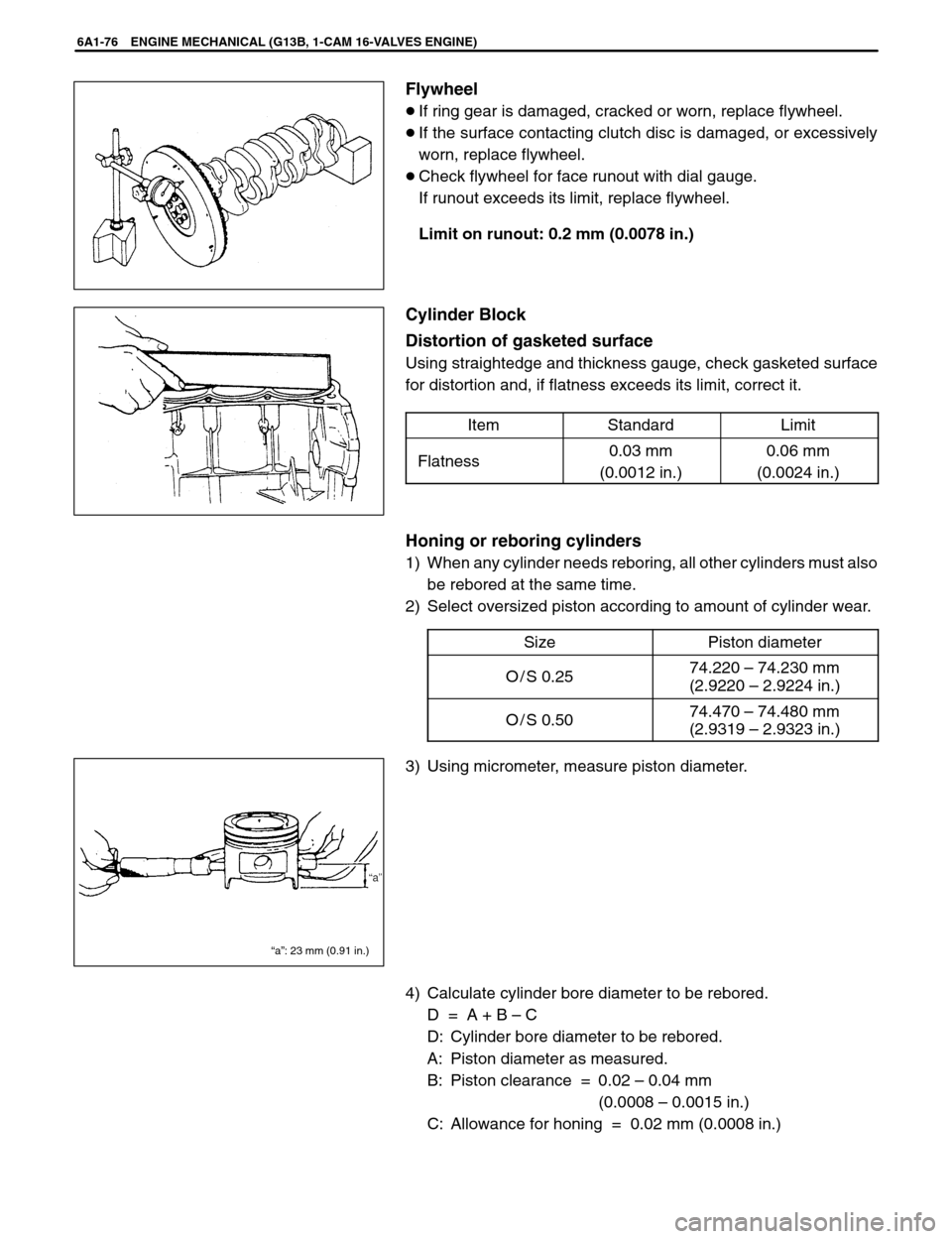
“a”: 23 mm (0.91 in.)
6A1-76 ENGINE MECHANICAL (G13B, 1-CAM 16-VALVES ENGINE)
Flywheel
If ring gear is damaged, cracked or worn, replace flywheel.
If the surface contacting clutch disc is damaged, or excessively
worn, replace flywheel.
Check flywheel for face runout with dial gauge.
If runout exceeds its limit, replace flywheel.
Limit on runout: 0.2 mm (0.0078 in.)
Cylinder Block
Distortion of gasketed surface
Using straightedge and thickness gauge, check gasketed surface
for distortion and, if flatness exceeds its limit, correct it.
Item
StandardLimit
Flatness0.03 mm
(0.0012 in.)0.06 mm
(0.0024 in.)
Honing or reboring cylinders
1) When any cylinder needs reboring, all other cylinders must also
be rebored at the same time.
2) Select oversized piston according to amount of cylinder wear.
Size
Piston diameter
O / S 0.2574.220 – 74.230 mm
(2.9220 – 2.9224 in.)
O / S 0.5074.470 – 74.480 mm
(2.9319 – 2.9323 in.)
3) Using micrometer, measure piston diameter.
4) Calculate cylinder bore diameter to be rebored.
D = A + B – C
D: Cylinder bore diameter to be rebored.
A: Piston diameter as measured.
B: Piston clearance = 0.02 – 0.04 mm
(0.0008 – 0.0015 in.)
C: Allowance for honing = 0.02 mm (0.0008 in.)