Page 356 of 557
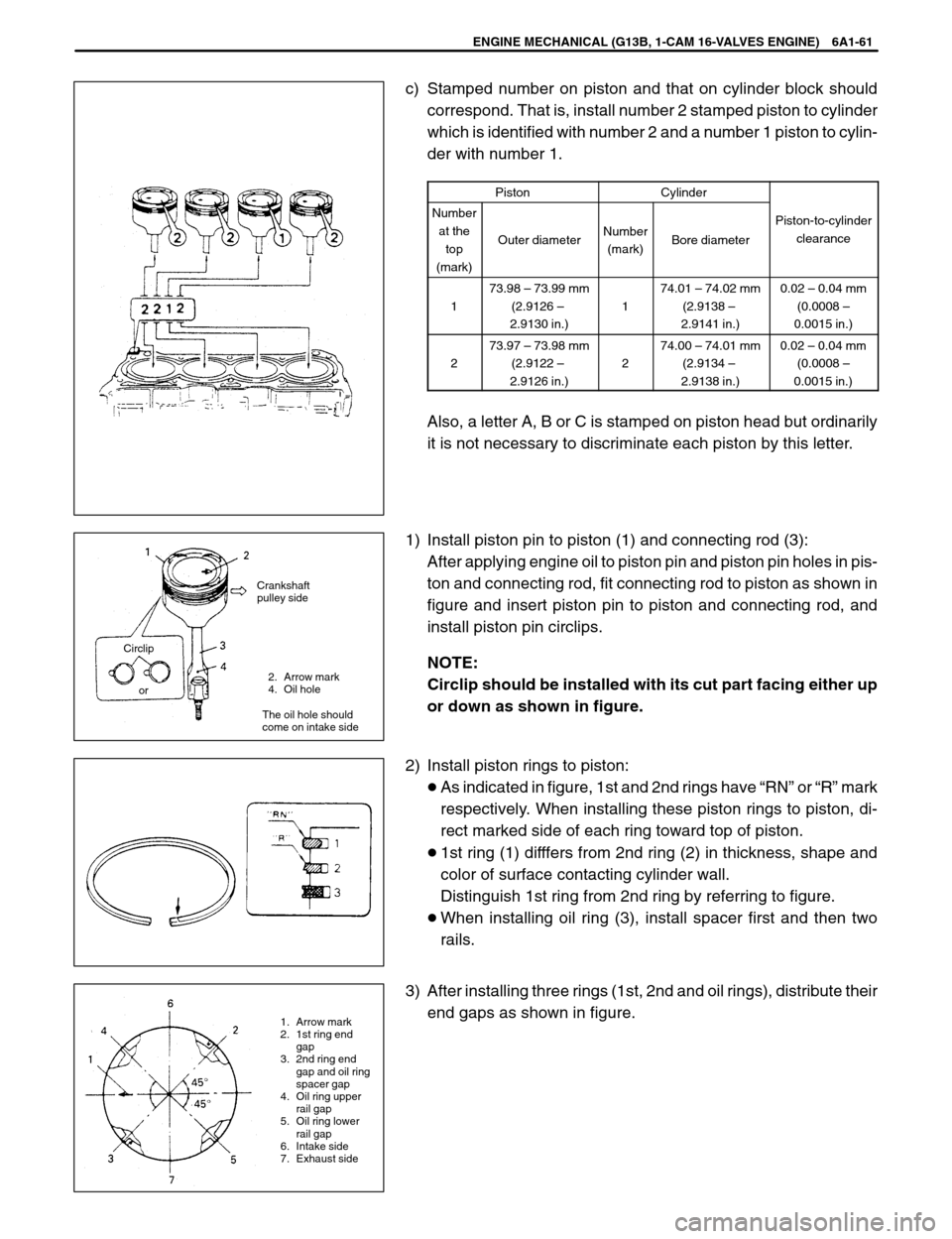
2. Arrow mark
4. Oil hole
The oil hole should
come on intake side
1. Arrow mark
2. 1st ring end
gap
3. 2nd ring end
gap and oil ring
spacer gap
4. Oil ring upper
rail gap
5. Oil ring lower
rail gap
6. Intake side
7. Exhaust side Crankshaft
pulley side
Circlip
or
ENGINE MECHANICAL (G13B, 1-CAM 16-VALVES ENGINE) 6A1-61
c) Stamped number on piston and that on cylinder block should
correspond. That is, install number 2 stamped piston to cylinder
which is identified with number 2 and a number 1 piston to cylin-
der with number 1.
PistonCylinder
Number
at the
top
(mark)
Outer diameterNumber
(mark)Bore diameter
Piston-to-cylinder
clearance
1
73.98 – 73.99 mm
(2.9126 –
2.9130 in.)
1
74.01 – 74.02 mm
(2.9138 –
2.9141 in.)0.02 – 0.04 mm
(0.0008 –
0.0015 in.)
2
73.97 – 73.98 mm
(2.9122 –
2.9126 in.)
2
74.00 – 74.01 mm
(2.9134 –
2.9138 in.)0.02 – 0.04 mm
(0.0008 –
0.0015 in.)
Also, a letter A, B or C is stamped on piston head but ordinarily
it is not necessary to discriminate each piston by this letter.
1) Install piston pin to piston (1) and connecting rod (3):
After applying engine oil to piston pin and piston pin holes in pis-
ton and connecting rod, fit connecting rod to piston as shown in
figure and insert piston pin to piston and connecting rod, and
install piston pin circlips.
NOTE:
Circlip should be installed with its cut part facing either up
or down as shown in figure.
2) Install piston rings to piston:
As indicated in figure, 1st and 2nd rings have “RN” or “R” mark
respectively. When installing these piston rings to piston, di-
rect marked side of each ring toward top of piston.
1st ring (1) difffers from 2nd ring (2) in thickness, shape and
color of surface contacting cylinder wall.
Distinguish 1st ring from 2nd ring by referring to figure.
When installing oil ring (3), install spacer first and then two
rails.
3) After installing three rings (1st, 2nd and oil rings), distribute their
end gaps as shown in figure.
Page 357 of 557
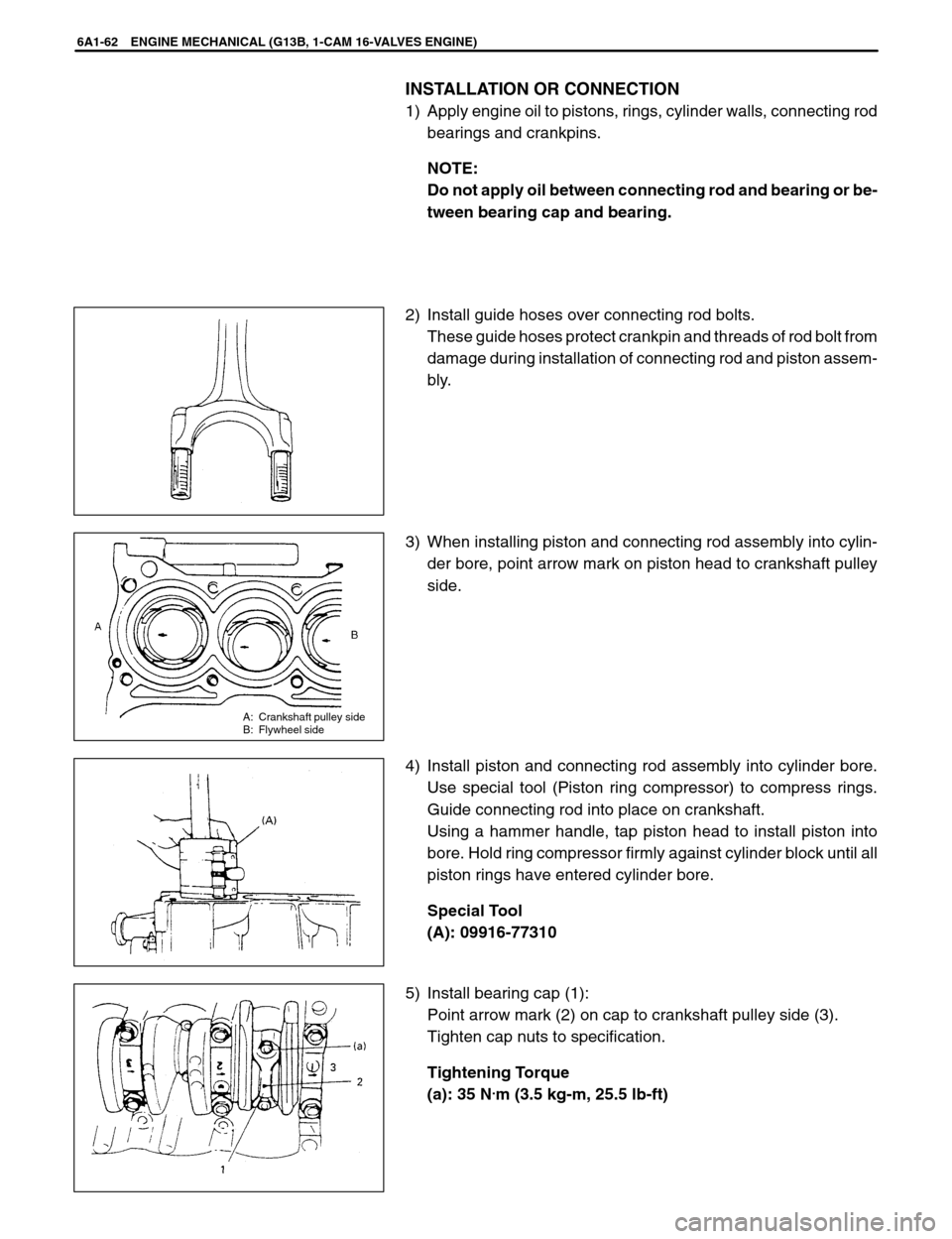
A: Crankshaft pulley side
B: Flywheel side
6A1-62 ENGINE MECHANICAL (G13B, 1-CAM 16-VALVES ENGINE)
INSTALLATION OR CONNECTION
1) Apply engine oil to pistons, rings, cylinder walls, connecting rod
bearings and crankpins.
NOTE:
Do not apply oil between connecting rod and bearing or be-
tween bearing cap and bearing.
2) Install guide hoses over connecting rod bolts.
These guide hoses protect crankpin and threads of rod bolt from
damage during installation of connecting rod and piston assem-
bly.
3) When installing piston and connecting rod assembly into cylin-
der bore, point arrow mark on piston head to crankshaft pulley
side.
4) Install piston and connecting rod assembly into cylinder bore.
Use special tool (Piston ring compressor) to compress rings.
Guide connecting rod into place on crankshaft.
Using a hammer handle, tap piston head to install piston into
bore. Hold ring compressor firmly against cylinder block until all
piston rings have entered cylinder bore.
Special Tool
(A): 09916-77310
5) Install bearing cap (1):
Point arrow mark (2) on cap to crankshaft pulley side (3).
Tighten cap nuts to specification.
Tightening Torque
(a): 35 N
.m (3.5 kg-m, 25.5 lb-ft)
Page 358 of 557
ENGINE MECHANICAL (G13B, 1-CAM 16-VALVES ENGINE) 6A1-63
6) Reverse removal procedure for installation, as previously out-
lined.
7) Adjust water pump drive belt tension referring to Section 6B.
8) Adjust power steering pump belt tension or A / C compressor
belt tension, if equipped.
Refer to Section 0B.
9) Adjust accelerator cable play.
Refer to Section 6E.
10) Check to ensure that all removed parts are back in place. Rein-
stall any necessary parts which have not been reinstalled.
11) Refill engine with engine oil by referring to item “ENGINE OIL
CHANGE” in Section 0B.
12) Refill cooling system referring to Section 6B.
13) Connect negative cable at battery.
14) Check ignition timing referring to Section 6F.
15) Verify that there is no fuel leakage, coolant leakage, oil leakage
and exhaust gas leakage at each connection.
Page 360 of 557
ENGINE MECHANICAL (G13B, 1-CAM 16-VALVES ENGINE) 6A1-65
12) Disconnect the following electric wires:
Ignition coil assembly
Ground wires from intake manifold
Engine oil pressure switch
EVAP canister purge valve (if equipped)
Engine coolant temp. sensor
Fuel injectors
Power steering pressure switch (if equipped)
Oxygen sensor-1
Back-up light switch (M / T)
Transmission range switch (A / T)
A/T vehicle speed sensor (A / T)
Solenoid coupler (A / T)
Generator
Starter
Battery negative cable from transmission
TP sensor
IAC valve
CMP sensor
MAP sensor
and then release wire harnesses from clamps.
13) Disconnect the following hoses:
Canister purge hose (2) from EVAP canister purge valve
Brake booster hose (1) from intake manifold
Radiator outlet hose from inlet pipe
Heater inlet and outlet hose from heater unit
14) Disconnect fuel feed (2) and return hoses (3) from fuel delivery
pipe (1).
Page 361 of 557
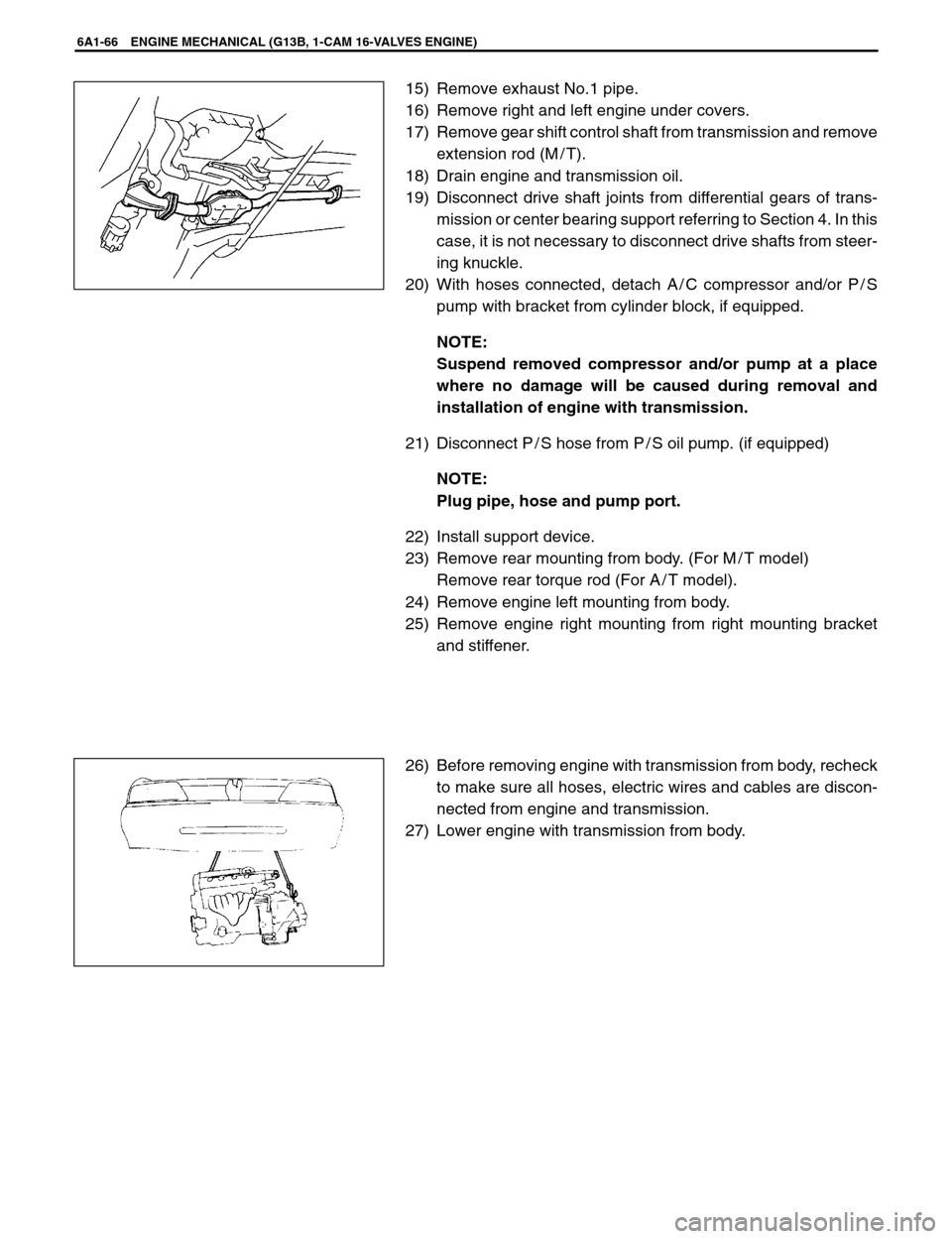
6A1-66 ENGINE MECHANICAL (G13B, 1-CAM 16-VALVES ENGINE)
15) Remove exhaust No.1 pipe.
16) Remove right and left engine under covers.
17) Remove gear shift control shaft from transmission and remove
extension rod (M / T).
18) Drain engine and transmission oil.
19) Disconnect drive shaft joints from differential gears of trans-
mission or center bearing support referring to Section 4. In this
case, it is not necessary to disconnect drive shafts from steer-
ing knuckle.
20) With hoses connected, detach A / C compressor and/or P / S
pump with bracket from cylinder block, if equipped.
NOTE:
Suspend removed compressor and/or pump at a place
where no damage will be caused during removal and
installation of engine with transmission.
21) Disconnect P / S hose from P / S oil pump. (if equipped)
NOTE:
Plug pipe, hose and pump port.
22) Install support device.
23) Remove rear mounting from body. (For M / T model)
Remove rear torque rod (For A / T model).
24) Remove engine left mounting from body.
25) Remove engine right mounting from right mounting bracket
and stiffener.
26) Before removing engine with transmission from body, recheck
to make sure all hoses, electric wires and cables are discon-
nected from engine and transmission.
27) Lower engine with transmission from body.
Page 362 of 557
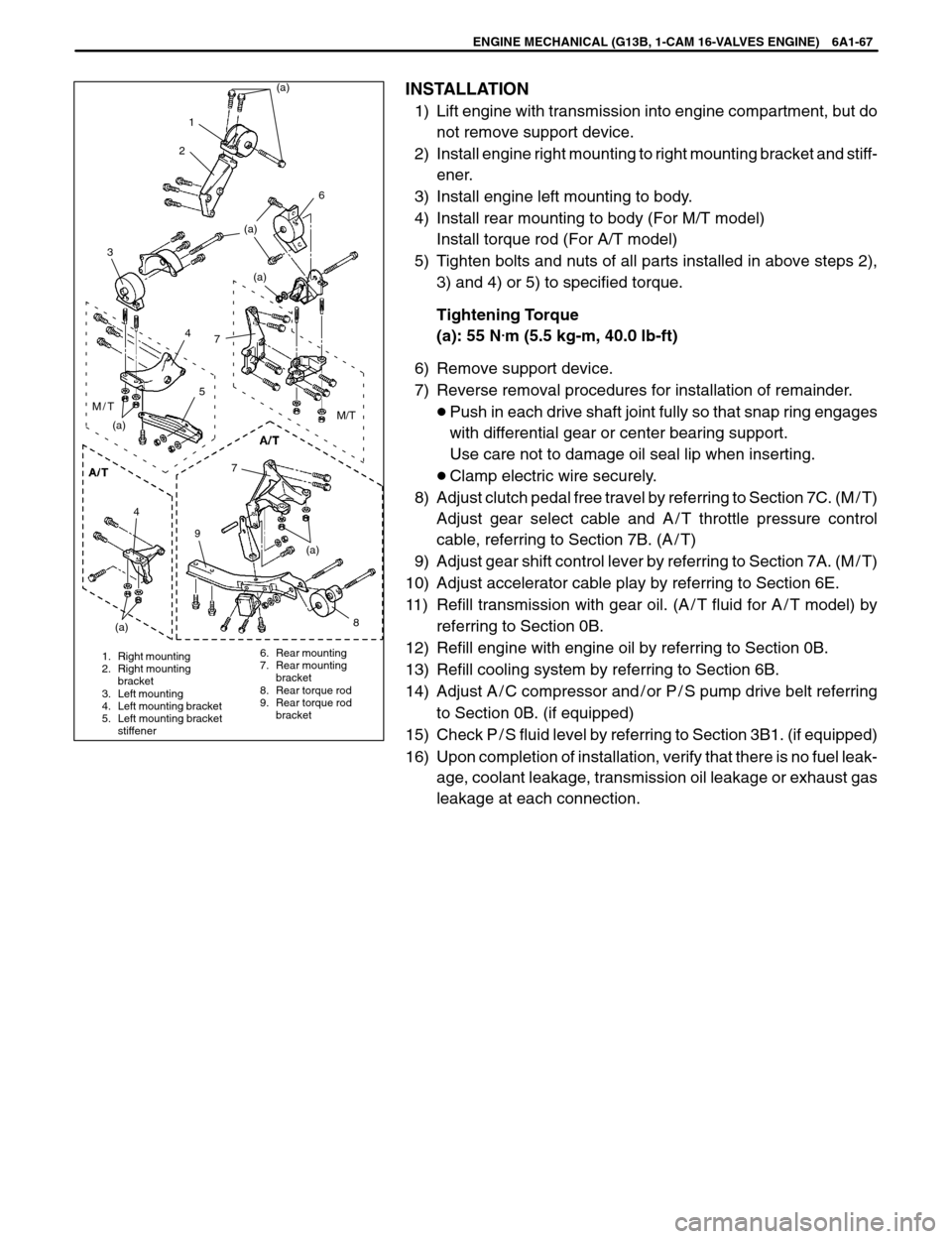
(a)
1
2
3
(a)
(a)
6
74
5
(a)
M/TM/T
9
(a)
4
7
(a)
8
1. Right mounting
2. Right mounting
bracket
3. Left mounting
4. Left mounting bracket
5. Left mounting bracket
stiffener6. Rear mounting
7. Rear mounting
bracket
8. Rear torque rod
9. Rear torque rod
bracket
ENGINE MECHANICAL (G13B, 1-CAM 16-VALVES ENGINE) 6A1-67
INSTALLATION
1) Lift engine with transmission into engine compartment, but do
not remove support device.
2) Install engine right mounting to right mounting bracket and stiff-
ener.
3) Install engine left mounting to body.
4) Install rear mounting to body (For M/T model)
Install torque rod (For A/T model)
5) Tighten bolts and nuts of all parts installed in above steps 2),
3) and 4) or 5) to specified torque.
Tightening Torque
(a): 55 N
.m (5.5 kg-m, 40.0 lb-ft)
6) Remove support device.
7) Reverse removal procedures for installation of remainder.
Push in each drive shaft joint fully so that snap ring engages
with differential gear or center bearing support.
Use care not to damage oil seal lip when inserting.
Clamp electric wire securely.
8) Adjust clutch pedal free travel by referring to Section 7C. (M / T)
Adjust gear select cable and A / T throttle pressure control
cable, referring to Section 7B. (A / T)
9) Adjust gear shift control lever by referring to Section 7A. (M / T)
10) Adjust accelerator cable play by referring to Section 6E.
11) Refill transmission with gear oil. (A / T fluid for A / T model) by
referring to Section 0B.
12) Refill engine with engine oil by referring to Section 0B.
13) Refill cooling system by referring to Section 6B.
14) Adjust A / C compressor and / or P / S pump drive belt referring
to Section 0B. (if equipped)
15) Check P / S fluid level by referring to Section 3B1. (if equipped)
16) Upon completion of installation, verify that there is no fuel leak-
age, coolant leakage, transmission oil leakage or exhaust gas
leakage at each connection.
Page 363 of 557
1. Cylinder block
2. Front oil seal:
Apply engine oil to contact part
of crankshaft with oil seal lip.
3. Main bearing:
Apply engine oil to bearing
inside surfaces.
4. Bearing cap
5. Cap bolt:
Apply engine oil to bolt and
bearing surfaces.
6. Timing pulley key7. Crankshaft:
Apply engine oil to crankshaft
journals.
8. Thrust bearing:
Set oil grooves of bearing to
crank weds.
Apply engine oil.
9. Rear oil seal:
Apply engine oil to contact part
of crankshaft with oil seal lip.10. Pin
11. Oil seal housing gasket
12. Oil seal housing
13. Housing bolt
14. Input shaft bearing
15. Flywheel
16. Flywheel bolt
: Do not reuse
: Tightening Torque
15 16
78 N.m (7.8 kg-m) for flywheel
95 N.m (9.5 kg-m) for drive plate
6A1-68 ENGINE MECHANICAL (G13B, 1-CAM 16-VALVES ENGINE)
MAIN BEARINGS, CRANKSHAFT AND CYLINDER BLOCK
Page 364 of 557
1. Flywheel bolt
2. Bolt
ENGINE MECHANICAL (G13B, 1-CAM 16-VALVES ENGINE) 6A1-69
REMOVAL
1) Remove engine assembly from body as previously outlined.
2) Remove clutch cover, clutch disc and flywheel (drive plate for
A / T).
Special Tool
(A): 09924-17810
3) Remove crankshaft pulley, timing belt and crankshaft timing
pulley.
4) Remove cylinder head assembly.
5) Remove oil pan and oil pump strainer.
6) Remove oil pump (1).
7) Remove oil seal housing.
8) Remove connecting rod bearing caps.
9) Loosen crankshaft bearing cap bolts in such order as indicated
in figure a little at a time and remove bearing caps.
10) Remove crankshaft from cylinder block.