Page 338 of 557
3
2. Breather hose
3. PCV valve4. High-tension cords
5. Ignition coil assembly
6. Ignition coil coupler
A: Camshaft pulley side
B: CMP sensor case side
ENGINE MECHANICAL (G13B, 1-CAM 16-VALVES ENGINE) 6A1-43
9) Remove cylinder head cover (1) as previously outlined.
Loosen all valve lash adjusting screws fully.
10) Remove timing belt and camshaft as previously outlined.
11) Disconnect exhaust pipe from exhaust manifold and remove
exhaust manifold stiffener (if equipped).
12) Loosen cylinder head bolts in such order as indicated in figure
and remove them.
13) Check all around cylinder head for any other parts required to
be removed or disconnected and remove or disconnect what-
ever necessary.
14) Remove cylinder head with intake manifold, exhaust manifold
CMP sensor case, using lifting device if necessary.
Page 339 of 557
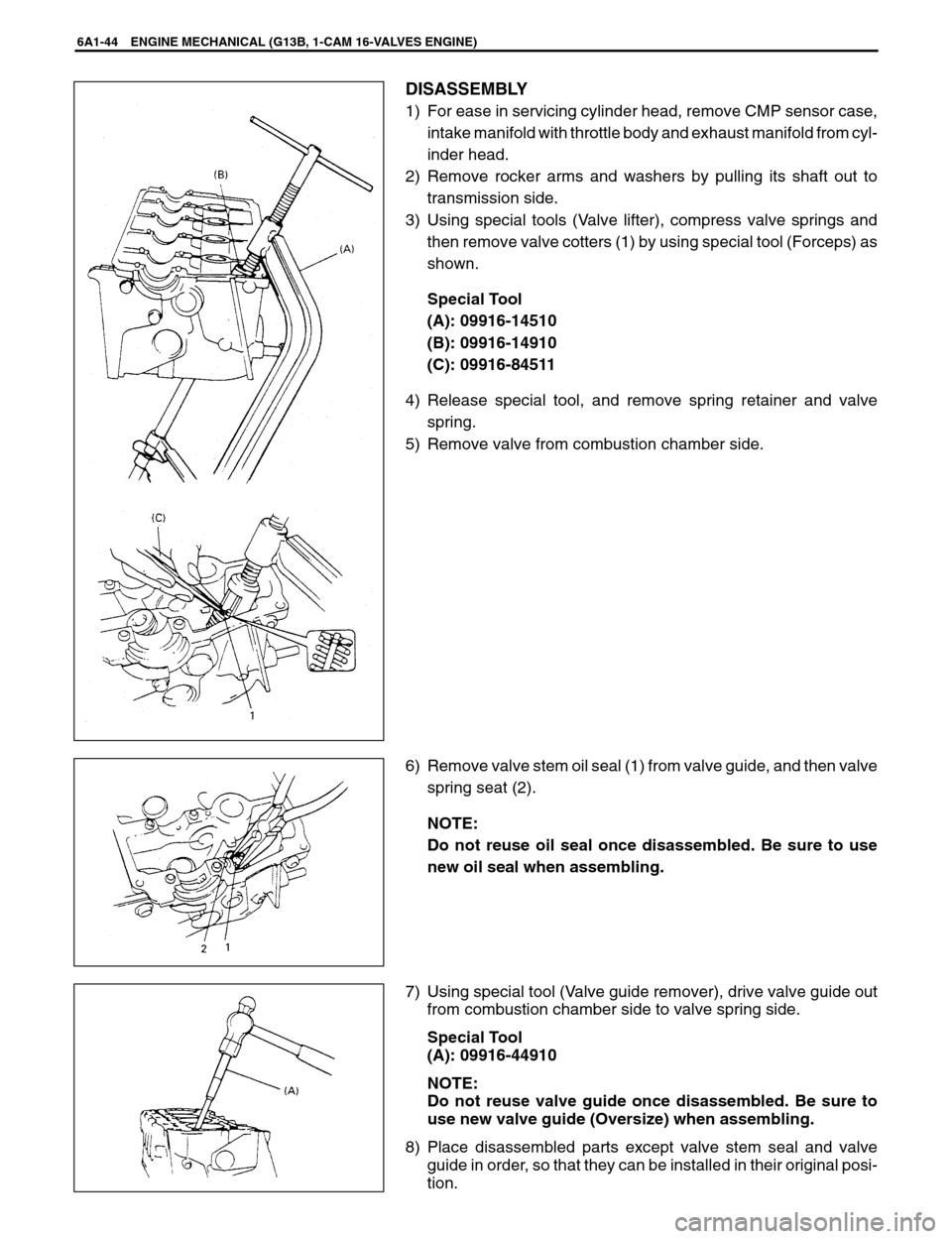
6A1-44 ENGINE MECHANICAL (G13B, 1-CAM 16-VALVES ENGINE)
DISASSEMBLY
1) For ease in servicing cylinder head, remove CMP sensor case,
intake manifold with throttle body and exhaust manifold from cyl-
inder head.
2) Remove rocker arms and washers by pulling its shaft out to
transmission side.
3) Using special tools (Valve lifter), compress valve springs and
then remove valve cotters (1) by using special tool (Forceps) as
shown.
Special Tool
(A): 09916-14510
(B): 09916-14910
(C): 09916-84511
4) Release special tool, and remove spring retainer and valve
spring.
5) Remove valve from combustion chamber side.
6) Remove valve stem oil seal (1) from valve guide, and then valve
spring seat (2).
NOTE:
Do not reuse oil seal once disassembled. Be sure to use
new oil seal when assembling.
7) Using special tool (Valve guide remover), drive valve guide out
from combustion chamber side to valve spring side.
Special Tool
(A): 09916-44910
NOTE:
Do not reuse valve guide once disassembled. Be sure to
use new valve guide (Oversize) when assembling.
8) Place disassembled parts except valve stem seal and valve
guide in order, so that they can be installed in their original posi-
tion.
Page 346 of 557
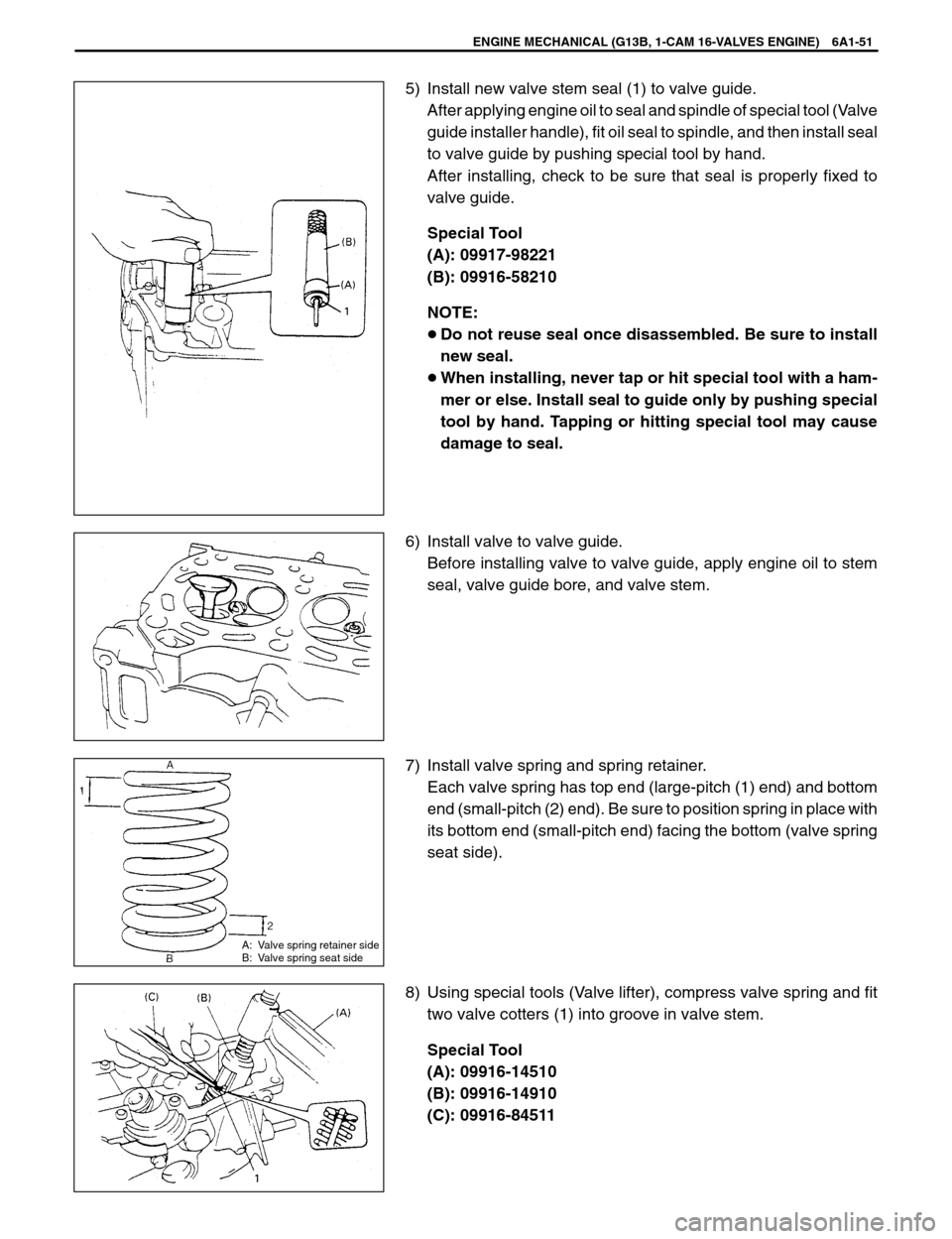
A: Valve spring retainer side
B: Valve spring seat side
ENGINE MECHANICAL (G13B, 1-CAM 16-VALVES ENGINE) 6A1-51
5) Install new valve stem seal (1) to valve guide.
After applying engine oil to seal and spindle of special tool (Valve
guide installer handle), fit oil seal to spindle, and then install seal
to valve guide by pushing special tool by hand.
After installing, check to be sure that seal is properly fixed to
valve guide.
Special Tool
(A): 09917-98221
(B): 09916-58210
NOTE:
Do not reuse seal once disassembled. Be sure to install
new seal.
When installing, never tap or hit special tool with a ham-
mer or else. Install seal to guide only by pushing special
tool by hand. Tapping or hitting special tool may cause
damage to seal.
6) Install valve to valve guide.
Before installing valve to valve guide, apply engine oil to stem
seal, valve guide bore, and valve stem.
7) Install valve spring and spring retainer.
Each valve spring has top end (large-pitch (1) end) and bottom
end (small-pitch (2) end). Be sure to position spring in place with
its bottom end (small-pitch end) facing the bottom (valve spring
seat side).
8) Using special tools (Valve lifter), compress valve spring and fit
two valve cotters (1) into groove in valve stem.
Special Tool
(A): 09916-14510
(B): 09916-14910
(C): 09916-84511
Page 347 of 557
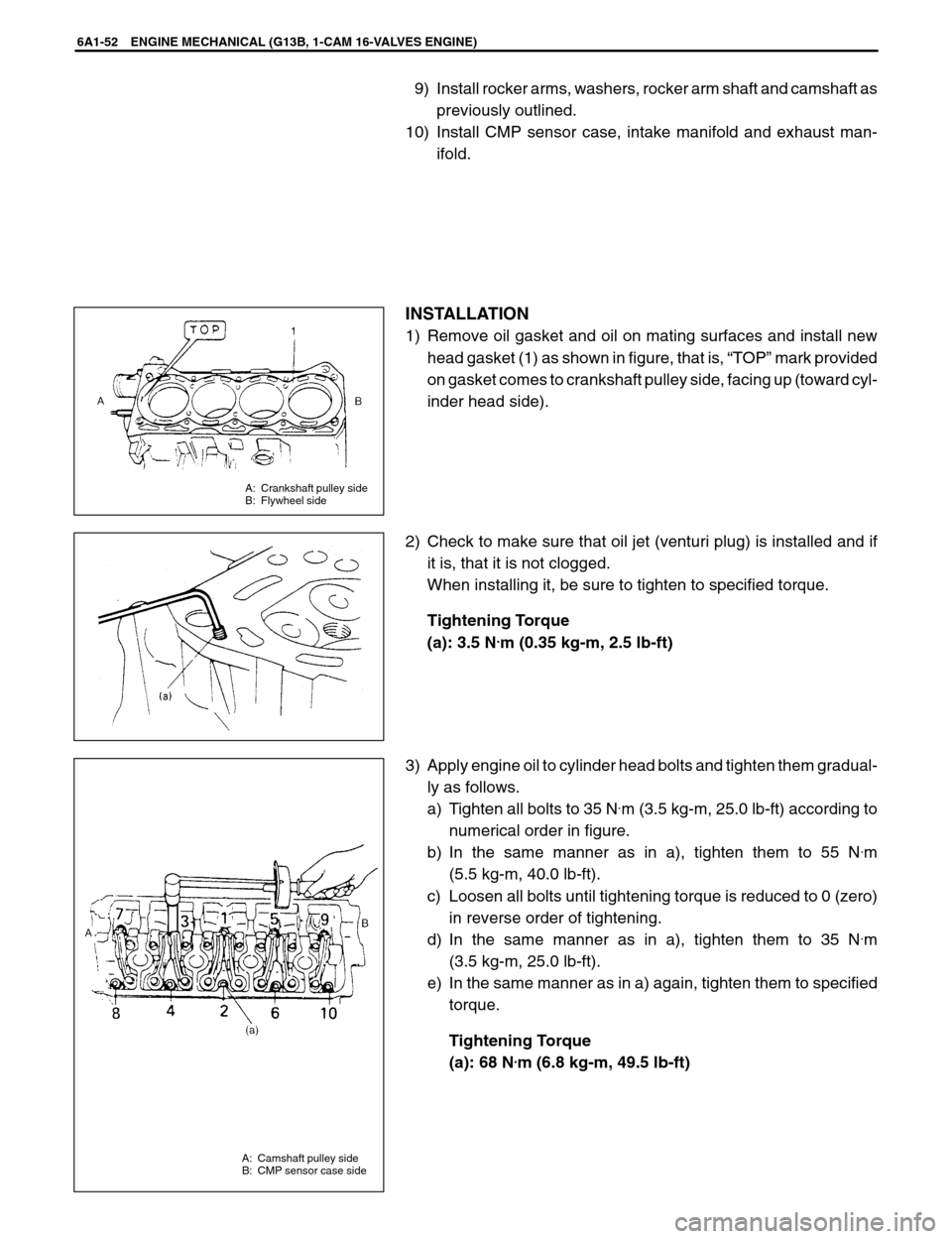
A: Crankshaft pulley side
B: Flywheel side
A: Camshaft pulley side
B: CMP sensor case side
6A1-52 ENGINE MECHANICAL (G13B, 1-CAM 16-VALVES ENGINE)
9) Install rocker arms, washers, rocker arm shaft and camshaft as
previously outlined.
10) Install CMP sensor case, intake manifold and exhaust man-
ifold.
INSTALLATION
1) Remove oil gasket and oil on mating surfaces and install new
head gasket (1) as shown in figure, that is, “TOP” mark provided
on gasket comes to crankshaft pulley side, facing up (toward cyl-
inder head side).
2) Check to make sure that oil jet (venturi plug) is installed and if
it is, that it is not clogged.
When installing it, be sure to tighten to specified torque.
Tightening Torque
(a): 3.5 N
.m (0.35 kg-m, 2.5 lb-ft)
3) Apply engine oil to cylinder head bolts and tighten them gradual-
ly as follows.
a) Tighten all bolts to 35 N
.m (3.5 kg-m, 25.0 lb-ft) according to
numerical order in figure.
b) In the same manner as in a), tighten them to 55 N
.m
(5.5 kg-m, 40.0 lb-ft).
c) Loosen all bolts until tightening torque is reduced to 0 (zero)
in reverse order of tightening.
d) In the same manner as in a), tighten them to 35 N
.m
(3.5 kg-m, 25.0 lb-ft).
e) In the same manner as in a) again, tighten them to specified
torque.
Tightening Torque
(a): 68 N
.m (6.8 kg-m, 49.5 lb-ft)
Page 349 of 557
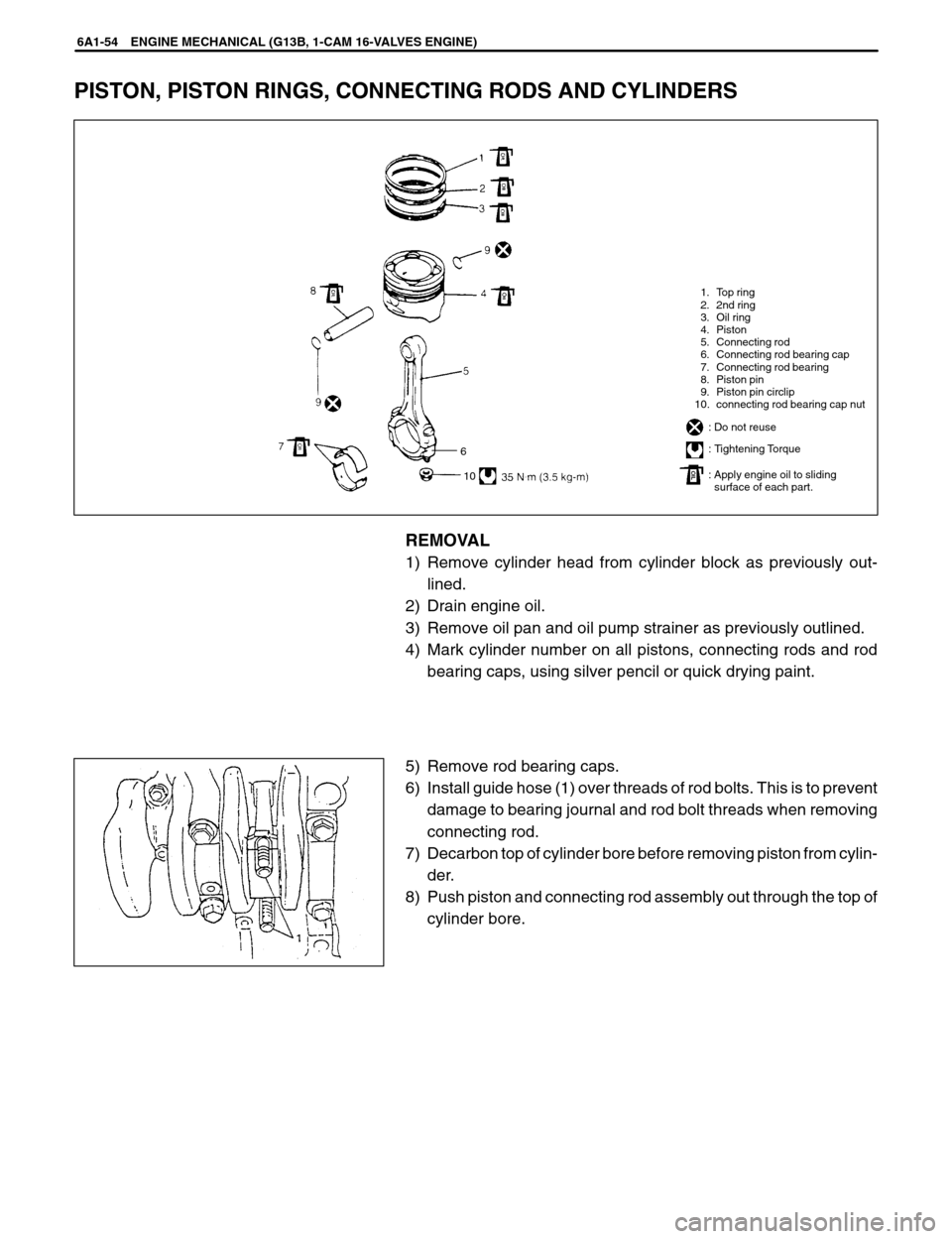
1. Top ring
2. 2nd ring
3. Oil ring
4. Piston
5. Connecting rod
6. Connecting rod bearing cap
7. Connecting rod bearing
8. Piston pin
9. Piston pin circlip
10. connecting rod bearing cap nut
: Do not reuse
: Tightening Torque
: Apply engine oil to sliding
: surface of each part.
6
10
6A1-54 ENGINE MECHANICAL (G13B, 1-CAM 16-VALVES ENGINE)
PISTON, PISTON RINGS, CONNECTING RODS AND CYLINDERS
REMOVAL
1) Remove cylinder head from cylinder block as previously out-
lined.
2) Drain engine oil.
3) Remove oil pan and oil pump strainer as previously outlined.
4) Mark cylinder number on all pistons, connecting rods and rod
bearing caps, using silver pencil or quick drying paint.
5) Remove rod bearing caps.
6) Install guide hose (1) over threads of rod bolts. This is to prevent
damage to bearing journal and rod bolt threads when removing
connecting rod.
7) Decarbon top of cylinder bore before removing piston from cylin-
der.
8) Push piston and connecting rod assembly out through the top of
cylinder bore.
Page 350 of 557
ENGINE MECHANICAL (G13B, 1-CAM 16-VALVES ENGINE) 6A1-55
DISASSEMBLY
1) Using piston ring expander, remove two compression rings (Top
and 2nd) and oil ring from piston.
2) Remove piston pin from connecting rod.
Ease out piston pin circlips (1), as shown.
Force piston pin out.
CLEANING
Clean carbon from piston head and ring grooves, using a suitable
tool.
Page 353 of 557
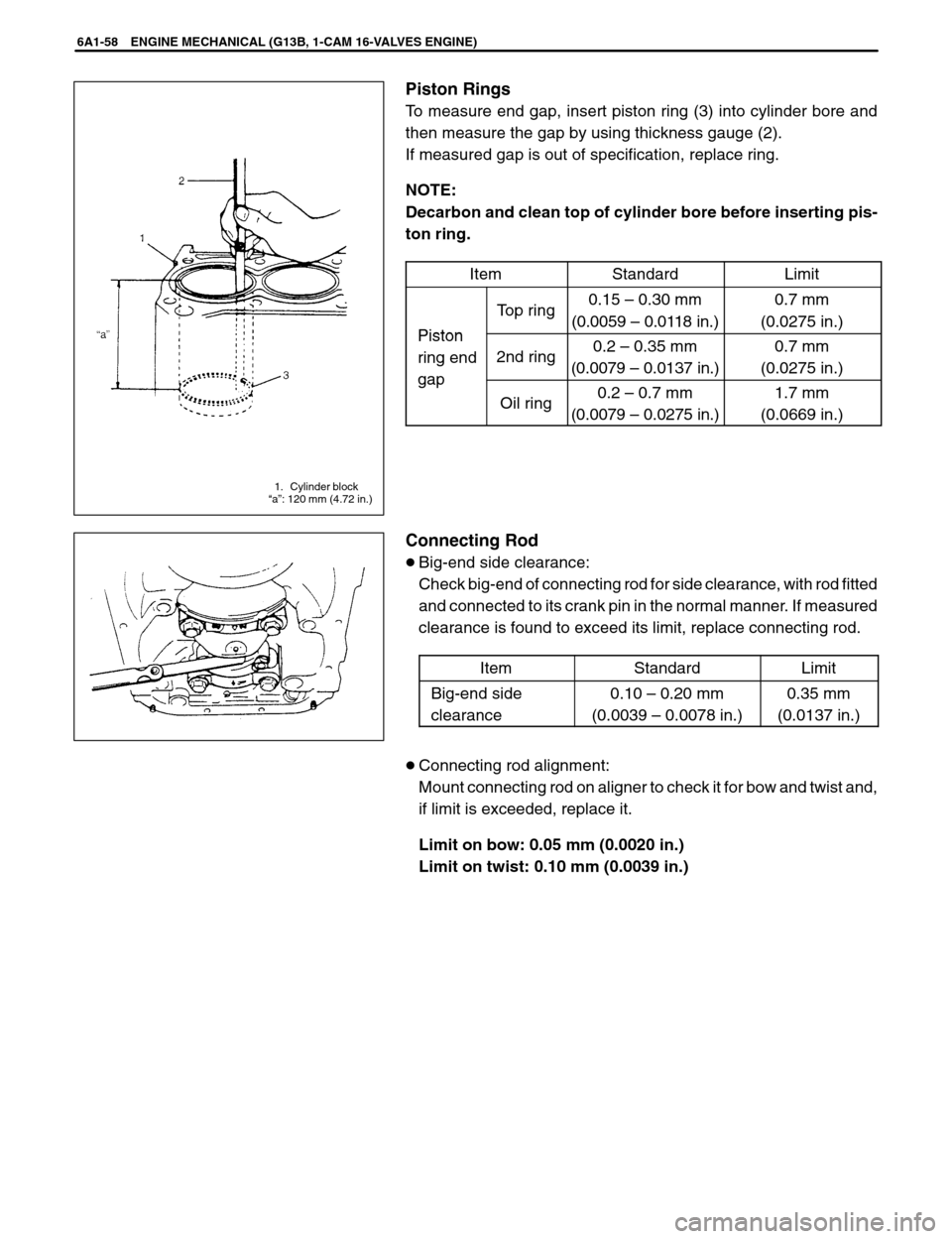
1. Cylinder block
“a”: 120 mm (4.72 in.)
6A1-58 ENGINE MECHANICAL (G13B, 1-CAM 16-VALVES ENGINE)
Piston Rings
To measure end gap, insert piston ring (3) into cylinder bore and
then measure the gap by using thickness gauge (2).
If measured gap is out of specification, replace ring.
NOTE:
Decarbon and clean top of cylinder bore before inserting pis-
ton ring.
Item
StandardLimit
Piston
Top ring0.15 – 0.30 mm
(0.0059 – 0.0118 in.)0.7 mm
(0.0275 in.)
Piston
ring end
gap
2nd ring0.2 – 0.35 mm
(0.0079 – 0.0137 in.)0.7 mm
(0.0275 in.)
ga
Oil ring0.2 – 0.7 mm
(0.0079 – 0.0275 in.)1.7 mm
(0.0669 in.)
Connecting Rod
Big-end side clearance:
Check big-end of connecting rod for side clearance, with rod fitted
and connected to its crank pin in the normal manner. If measured
clearance is found to exceed its limit, replace connecting rod.
Item
StandardLimit
Big-end side
clearance0.10 – 0.20 mm
(0.0039 – 0.0078 in.)0.35 mm
(0.0137 in.)
Connecting rod alignment:
Mount connecting rod on aligner to check it for bow and twist and,
if limit is exceeded, replace it.
Limit on bow: 0.05 mm (0.0020 in.)
Limit on twist: 0.10 mm (0.0039 in.)
Page 354 of 557
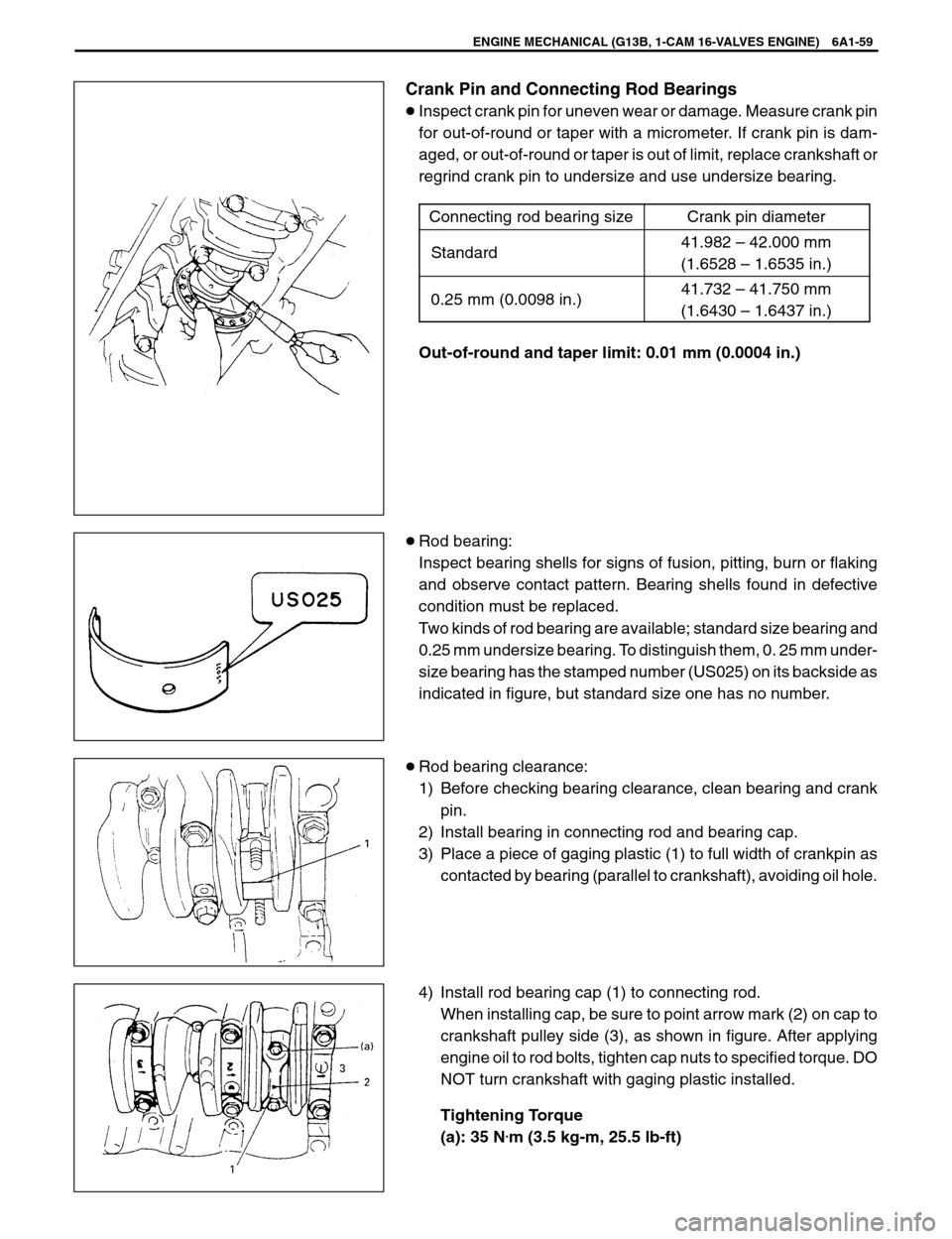
ENGINE MECHANICAL (G13B, 1-CAM 16-VALVES ENGINE) 6A1-59
Crank Pin and Connecting Rod Bearings
Inspect crank pin for uneven wear or damage. Measure crank pin
for out-of-round or taper with a micrometer. If crank pin is dam-
aged, or out-of-round or taper is out of limit, replace crankshaft or
regrind crank pin to undersize and use undersize bearing.
Connecting rod bearing size
Crank pin diameter
Standard41.982 – 42.000 mm
(1.6528 – 1.6535 in.)
0.25 mm (0.0098 in.)41.732 – 41.750 mm
(1.6430 – 1.6437 in.)
Out-of-round and taper limit: 0.01 mm (0.0004 in.)
Rod bearing:
Inspect bearing shells for signs of fusion, pitting, burn or flaking
and observe contact pattern. Bearing shells found in defective
condition must be replaced.
Two kinds of rod bearing are available; standard size bearing and
0.25 mm undersize bearing. To distinguish them, 0. 25 mm under-
size bearing has the stamped number (US025) on its backside as
indicated in figure, but standard size one has no number.
Rod bearing clearance:
1) Before checking bearing clearance, clean bearing and crank
pin.
2) Install bearing in connecting rod and bearing cap.
3) Place a piece of gaging plastic (1) to full width of crankpin as
contacted by bearing (parallel to crankshaft), avoiding oil hole.
4) Install rod bearing cap (1) to connecting rod.
When installing cap, be sure to point arrow mark (2) on cap to
crankshaft pulley side (3), as shown in figure. After applying
engine oil to rod bolts, tighten cap nuts to specified torque. DO
NOT turn crankshaft with gaging plastic installed.
Tightening Torque
(a): 35 N
.m (3.5 kg-m, 25.5 lb-ft)