Page 179 of 557
![SUZUKI SWIFT 2000 1.G SF310 Service Workshop Manual ENGINE GENERAL INFORMATION AND DIAGNOSIS (SFI FOR G13) 6-1-23
ConditionPossible Cause]Referring Item
Low oil pressureImproper oil viscosity
Malfunctioning oil pressure switch
Clogged oil strainer
SUZUKI SWIFT 2000 1.G SF310 Service Workshop Manual ENGINE GENERAL INFORMATION AND DIAGNOSIS (SFI FOR G13) 6-1-23
ConditionPossible Cause]Referring Item
Low oil pressureImproper oil viscosity
Malfunctioning oil pressure switch
Clogged oil strainer
](/manual-img/20/7602/w960_7602-178.png)
ENGINE GENERAL INFORMATION AND DIAGNOSIS (SFI FOR G13) 6-1-23
ConditionPossible Cause]Referring Item
Low oil pressureImproper oil viscosity
Malfunctioning oil pressure switch
Clogged oil strainer
Functional deterioration of oil pump
Worn oil pump relief valve
Excessive clearance in various sliding partsEngine oil and oil filter change in
Section 0B
Oil pressure switch inspection in
Section 8
Oil pan and oil pump strainer
cleaning in Section 6A1
Oil pump in Section 6A1
Oil pump in Section 6A1
Engine noise
Note: Before
checking mechanical
noise, make sure
that:
Specified spark
plug in used.
Specified fuel is
used.Valve noise
Improper valve lash
Worn valve stem and guide
Weak or broken valve spring
Warped or bent valve
Piston, ring and cylinder noise
Worn piston, ring and cylinder bore
Connecting rod noise
Worn rod bearing
Worn crank pin
Loose connecting rod nuts
Low oil pressure
Crankshaft noise
Low oil pressure
Worn bearing
Worn crankshaft journal
Loose bearing cap bolts
Excessive crankshaft thrust play
Valve lash in Section 6A1
Valves inspection in Section 6A1
Valve springs inspection in
Section 6A1
Valves inspection in Section 6A1
Pistons and cylinders inspection
in Section 6A1
Crank pin and connecting rod
bearing inspection in Section 6A1
Crank pin and connecting rod
bearing inspection in Section 6A1
Connecting rod installation in
Section 6A1
Previously outlined
Previously outlined
Crankshaft and bearing
inspection in Section 6A1
Crankshaft and bearing
inspection in Section 6A1
Crankshaft inspection in
Section 6A1
Crankshaft thrust play inspection
in Section 6A1
Page 182 of 557
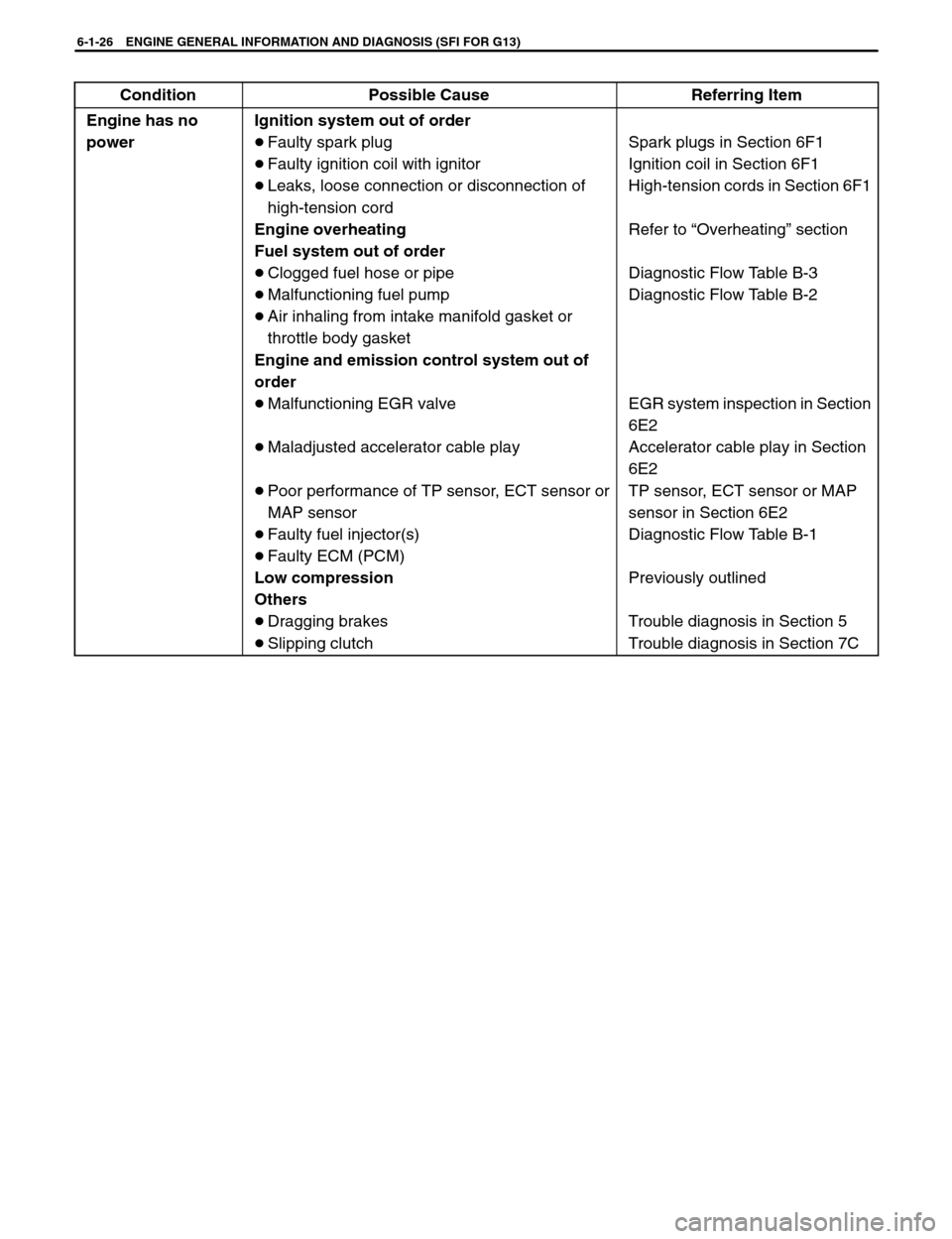
6-1-26 ENGINE GENERAL INFORMATION AND DIAGNOSIS (SFI FOR G13)
ConditionPossible CauseReferring Item
Engine has no
powerIgnition system out of order
Faulty spark plug
Faulty ignition coil with ignitor
Leaks, loose connection or disconnection of
high-tension cord
Engine overheating
Fuel system out of order
Clogged fuel hose or pipe
Malfunctioning fuel pump
Air inhaling from intake manifold gasket or
throttle body gasket
Engine and emission control system out of
order
Malfunctioning EGR valve
Maladjusted accelerator cable play
Poor performance of TP sensor, ECT sensor or
MAP sensor
Faulty fuel injector(s)
Faulty ECM (PCM)
Low compression
Others
Dragging brakes
Slipping clutch
Spark plugs in Section 6F1
Ignition coil in Section 6F1
High-tension cords in Section 6F1
Refer to “Overheating” section
Diagnostic Flow Table B-3
Diagnostic Flow Table B-2
EGR system inspection in Section
6E2
Accelerator cable play in Section
6E2
TP sensor, ECT sensor or MAP
sensor in Section 6E2
Diagnostic Flow Table B-1
Previously outlined
Trouble diagnosis in Section 5
Trouble diagnosis in Section 7C
Page 183 of 557
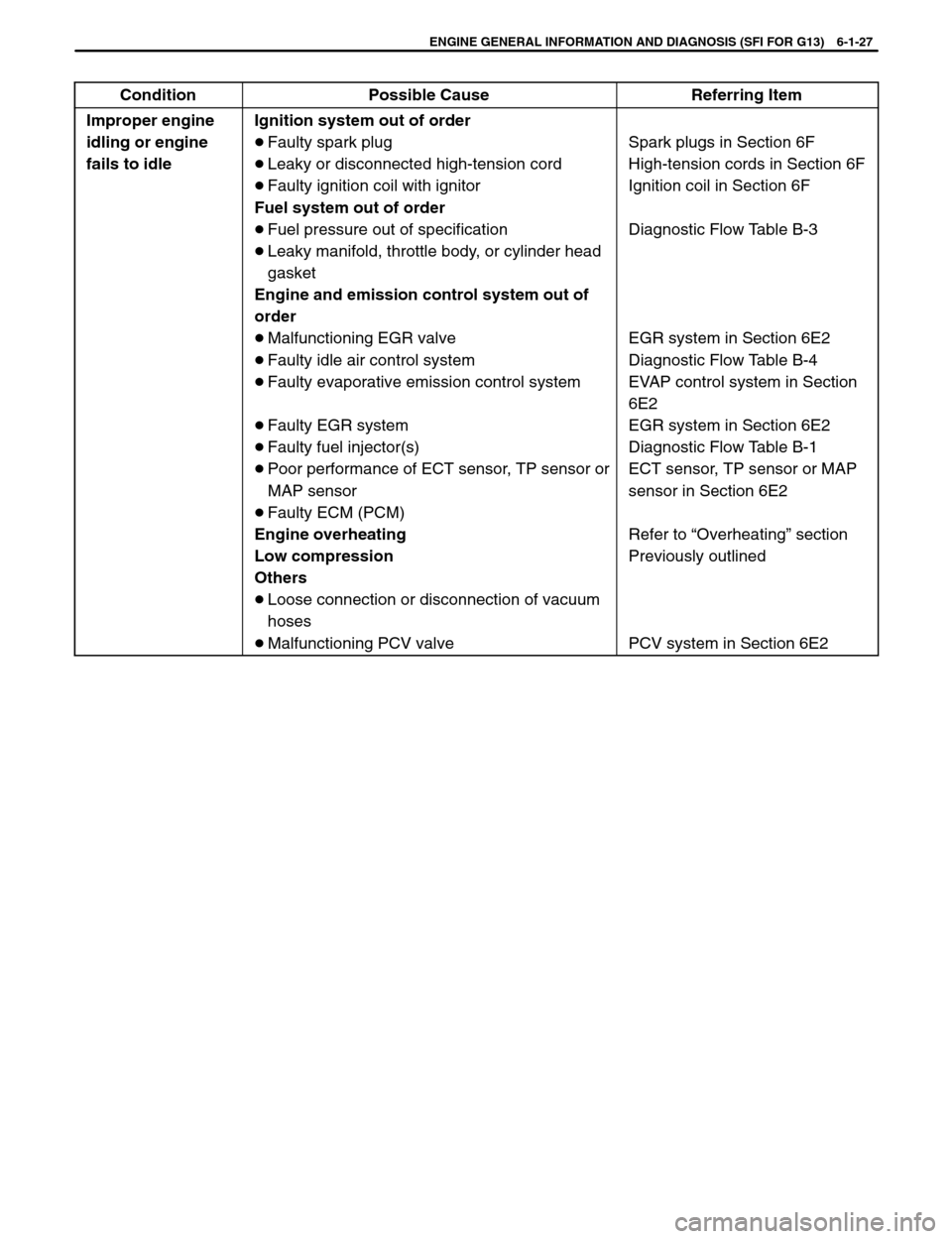
ENGINE GENERAL INFORMATION AND DIAGNOSIS (SFI FOR G13) 6-1-27
ConditionPossible CauseReferring Item
Improper engine
idling or engine
fails to idleIgnition system out of order
Faulty spark plug
Leaky or disconnected high-tension cord
Faulty ignition coil with ignitor
Fuel system out of order
Fuel pressure out of specification
Leaky manifold, throttle body, or cylinder head
gasket
Engine and emission control system out of
order
Malfunctioning EGR valve
Faulty idle air control system
Faulty evaporative emission control system
Faulty EGR system
Faulty fuel injector(s)
Poor performance of ECT sensor, TP sensor or
MAP sensor
Faulty ECM (PCM)
Engine overheating
Low compression
Others
Loose connection or disconnection of vacuum
hoses
Malfunctioning PCV valve
Spark plugs in Section 6F
High-tension cords in Section 6F
Ignition coil in Section 6F
Diagnostic Flow Table B-3
EGR system in Section 6E2
Diagnostic Flow Table B-4
EVAP control system in Section
6E2
EGR system in Section 6E2
Diagnostic Flow Table B-1
ECT sensor, TP sensor or MAP
sensor in Section 6E2
Refer to “Overheating” section
Previously outlined
PCV system in Section 6E2
Page 184 of 557
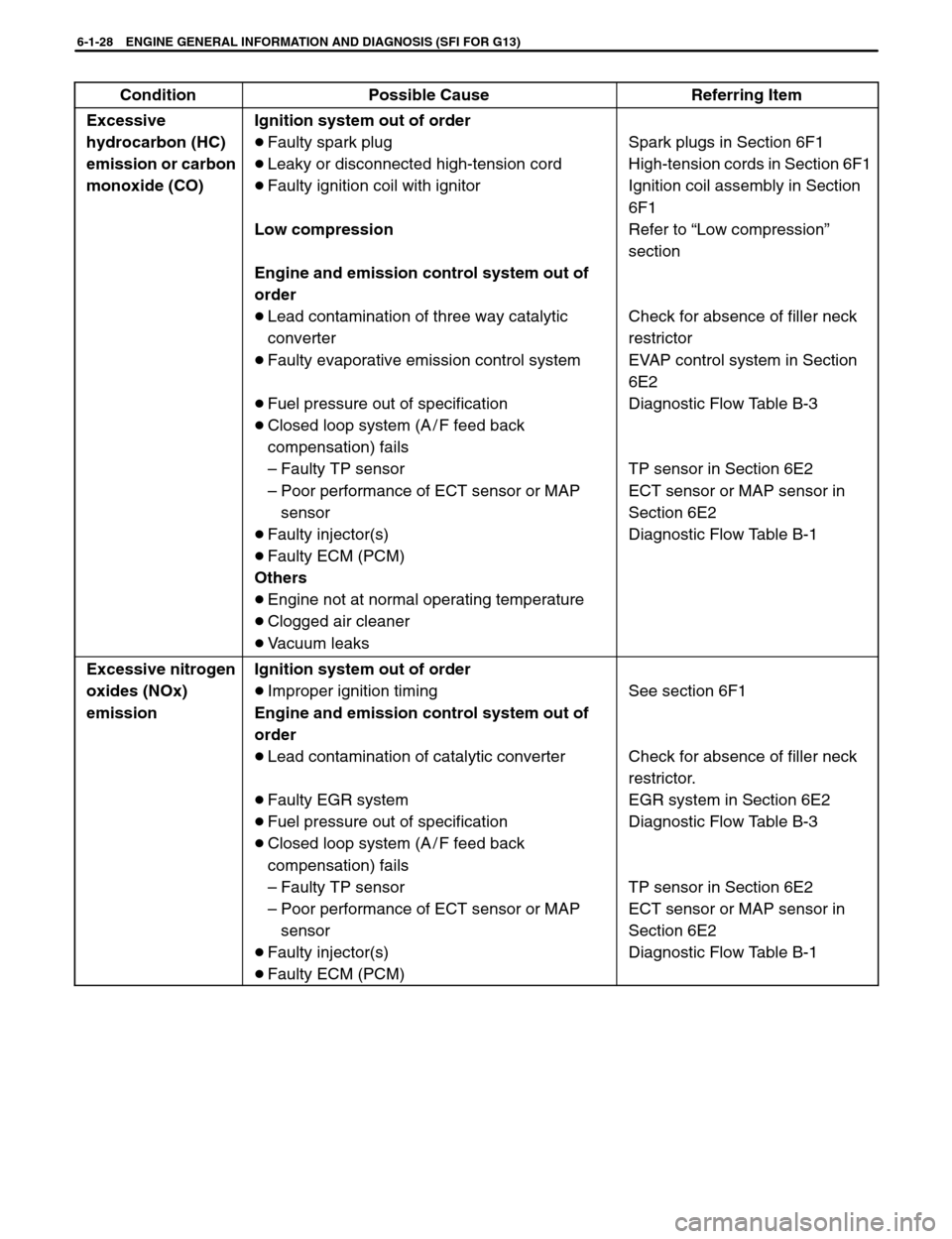
6-1-28 ENGINE GENERAL INFORMATION AND DIAGNOSIS (SFI FOR G13)
ConditionPossible CauseReferring Item
Excessive
hydrocarbon (HC)
emission or carbon
monoxide (CO)Ignition system out of order
Faulty spark plug
Leaky or disconnected high-tension cord
Faulty ignition coil with ignitor
Low compression
Engine and emission control system out of
order
Lead contamination of three way catalytic
converter
Faulty evaporative emission control system
Fuel pressure out of specification
Closed loop system (A / F feed back
compensation) fails
–Faulty TP sensor
–Poor performance of ECT sensor or MAP
sensor
Faulty injector(s)
Faulty ECM (PCM)
Others
Engine not at normal operating temperature
Clogged air cleaner
Vacuum leaks
Spark plugs in Section 6F1
High-tension cords in Section 6F1
Ignition coil assembly in Section
6F1
Refer to “Low compression”
section
Check for absence of filler neck
restrictor
EVAP control system in Section
6E2
Diagnostic Flow Table B-3
TP sensor in Section 6E2
ECT sensor or MAP sensor in
Section 6E2
Diagnostic Flow Table B-1
Excessive nitrogen
oxides (NOx)
emissionIgnition system out of order
Improper ignition timing
Engine and emission control system out of
order
Lead contamination of catalytic converter
Faulty EGR system
Fuel pressure out of specification
Closed loop system (A / F feed back
compensation) fails
–Faulty TP sensor
–Poor performance of ECT sensor or MAP
sensor
Faulty injector(s)
Faulty ECM (PCM)
See section 6F1
Check for absence of filler neck
restrictor.
EGR system in Section 6E2
Diagnostic Flow Table B-3
TP sensor in Section 6E2
ECT sensor or MAP sensor in
Section 6E2
Diagnostic Flow Table B-1
Page 189 of 557
ENGINE GENERAL INFORMATION AND DIAGNOSIS (SFI FOR G13) 6-1-33
1. ECM (PCM)
2. ECM (PCM) couplers
(Viewed from harness side)
INSPECTION OF ECM (PCM) AND ITS
CIRCUITS
ECM (PCM) and its circuits can be checked at ECM (PCM) wiring
couplers by measuring voltage and resistance.
CAUTION:
ECM (PCM) cannot be checked by itself. It is strictly prohib-
ited to connect voltmeter or ohmmeter to ECM (PCM) with
coupler disconnected from it.
Voltage Check
1) Remove ECM (PCM) (1) from body referring to Section 6E2.
2) Check voltage at each terminal of couplers (2) connected.
NOTE:
As each terminal voltage is affected by the battery voltage,
confirm that it is 11 V or more when ignition switch is ON.
Page 193 of 557
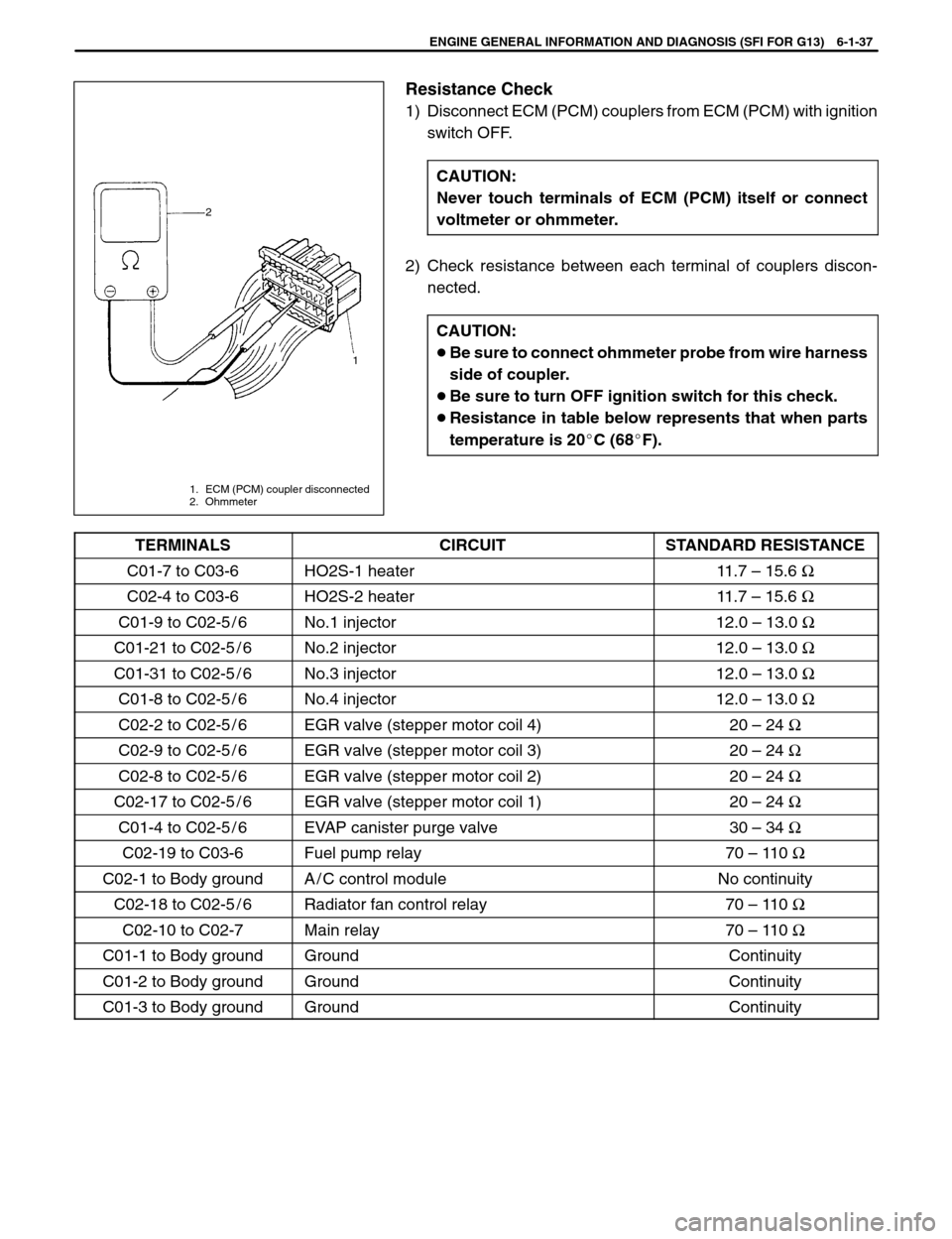
1 2
1. ECM (PCM) coupler disconnected
2. Ohmmeter
ENGINE GENERAL INFORMATION AND DIAGNOSIS (SFI FOR G13) 6-1-37
Resistance Check
1) Disconnect ECM (PCM) couplers from ECM (PCM) with ignition
switch OFF.
CAUTION:
Never touch terminals of ECM (PCM) itself or connect
voltmeter or ohmmeter.
2) Check resistance between each terminal of couplers discon-
nected.
CAUTION:
Be sure to connect ohmmeter probe from wire harness
side of coupler.
Be sure to turn OFF ignition switch for this check.
Resistance in table below represents that when parts
temperature is 20C (68F).
TERMINALSCIRCUITSTANDARD RESISTANCE
C01-7 to C03-6HO2S-1 heater11.7 – 15.6 Ω
C02-4 to C03-6HO2S-2 heater11.7 – 15.6 Ω
C01-9 to C02-5 / 6No.1 injector12.0 – 13.0 Ω
C01-21 to C02-5 / 6No.2 injector12.0 – 13.0 Ω
C01-31 to C02-5 / 6No.3 injector12.0 – 13.0 Ω
C01-8 to C02-5 / 6No.4 injector12.0 – 13.0 Ω
C02-2 to C02-5 / 6EGR valve (stepper motor coil 4)20 – 24 Ω
C02-9 to C02-5 / 6EGR valve (stepper motor coil 3)20 – 24 Ω
C02-8 to C02-5 / 6EGR valve (stepper motor coil 2)20 – 24 Ω
C02-17 to C02-5 / 6EGR valve (stepper motor coil 1)20 – 24 Ω
C01-4 to C02-5 / 6EVAP canister purge valve30 – 34 Ω
C02-19 to C03-6Fuel pump relay70 – 110 Ω
C02-1 to Body groundA / C control moduleNo continuity
C02-18 to C02-5 / 6Radiator fan control relay70 – 110 Ω
C02-10 to C02-7Main relay70 – 110 Ω
C01-1 to Body groundGroundContinuity
C01-2 to Body groundGroundContinuity
C01-3 to Body groundGroundContinuity
Page 195 of 557
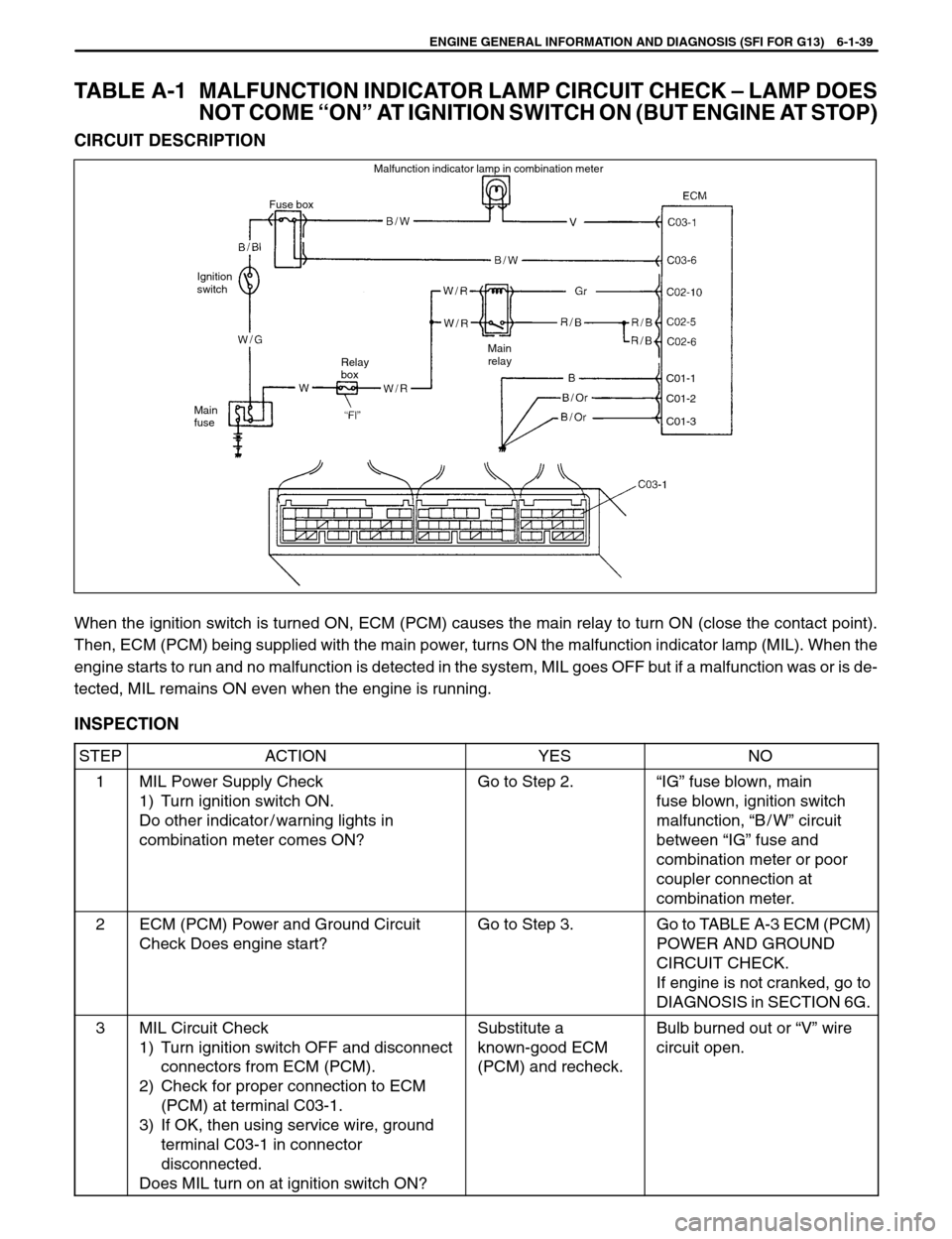
Main
fuseIgnition
switch
Main
relay Malfunction indicator lamp in combination meter
Relay
box Fuse box
C01-1
C01-2
C01-3
ENGINE GENERAL INFORMATION AND DIAGNOSIS (SFI FOR G13) 6-1-39
TABLE A-1 MALFUNCTION INDICATOR LAMP CIRCUIT CHECK – LAMP DOES
NOT COME “ON” AT IGNITION SWITCH ON (BUT ENGINE AT STOP)
CIRCUIT DESCRIPTION
When the ignition switch is turned ON, ECM (PCM) causes the main relay to turn ON (close the contact point).
Then, ECM (PCM) being supplied with the main power, turns ON the malfunction indicator lamp (MIL). When the
engine starts to run and no malfunction is detected in the system, MIL goes OFF but if a malfunction was or is de-
tected, MIL remains ON even when the engine is running.
INSPECTION
STEPACTIONYESNO
1MIL Power Supply Check
1) Turn ignition switch ON.
Do other indicator / warning lights in
combination meter comes ON?Go to Step 2.“IG” fuse blown, main
fuse blown, ignition switch
malfunction, “B/W” circuit
between “IG” fuse and
combination meter or poor
coupler connection at
combination meter.
2ECM (PCM) Power and Ground Circuit
Check Does engine start?Go to Step 3.Go to TABLE A-3 ECM (PCM)
POWER AND GROUND
CIRCUIT CHECK.
If engine is not cranked, go to
DIAGNOSIS in SECTION 6G.
3MIL Circuit Check
1) Turn ignition switch OFF and disconnect
connectors from ECM (PCM).
2) Check for proper connection to ECM
(PCM) at terminal C03-1.
3) If OK, then using service wire, ground
terminal C03-1 in connector
disconnected.
Does MIL turn on at ignition switch ON?Substitute a
known-good ECM
(PCM) and recheck.Bulb burned out or “V” wire
circuit open.
Page 196 of 557
6-1-40 ENGINE GENERAL INFORMATION AND DIAGNOSIS (SFI FOR G13)
TABLE A-2 MALFUNCTION INDICATOR LAMP CIRCUIT CHECK – LAMP
REMAINS “ON” AFTER ENGINE STARTS
WIRING DIAGRAM / CIRCUIT DESCRIPTION – Refer to table A-1.
INSPECTION
STEPACTIONYESNO
1Diagnostic Trouble Code (DTC) check
1) Check DTC referring to DTC CHECK section.
Is there any DTC(s)?Go to Step 2 of ENGINE
DIAG. FLOW TABLE.Go to Step 2.
2DTC check
Start engine and recheck DTC while engine
running.
Is there any DTC(s)?Go to Step 3.
3MIL Circuit check
1) Turn OFF ignition switch.
2) Disconnect connectors from ECM (PCM).
Does MIL turn ON at ignition switch ON?“V” wire circuit shorted to
ground.Substitute a known-good
ECM (PCM) and
recheck.